J. Cent. South Univ. (2012) 19: 2073-2080
DOI: 10.1007/s11771-012-1247-3
Hot-compression behavior of Al alloy 5182
TANG Jian-guo(唐建国), HUANG Xing-xing(黄星星), ZHANG Xin-ming(张新明)
School of Materials Science and Engineering, Central South University, Changsha 410083, China
? Central South University Press and Springer-Verlag Berlin Heidelberg 2012
Abstract: Hot-compression of aluminum alloy 5182 was carried out on a Gleeble-1500 thermo-simulator at deformation temperature ranging from 350 ℃ to 500 ℃ and at strain rate from 0.01 s-1 to 10 s-1 with strain range from 0.7 to 1.9. The microstructures and macro-textures evolution under different conditions were investigated by polarized optical microscopy and X-ray diffraction analysis, respectively. The basic trend is that the hot-compression stress increases with the decrease of temperature and increase of strain rate, which is revealed and elucidated in terms of Zener-Hollomon parameter in the hyperbolic sine equation with the hot-deformation activation energy of 143.5 kJ/mol. An empirical constitutive equation is proposed to predict the hot-deformation behavior under different conditions. As deformation temperature increases up to 400 ℃, at strain rate over 1 s-1, dynamic recrystallization (DRX) occurs. Cube orientation {100}á001? is detected in the recrystallized sample after hot-compression.
Key words: aluminum alloy 5182; hot-compression; texture; microstructure
1 Introduction
Aluminum alloy 5182 containing magnesium as a basic alloying addition is widely used for beverage can closure and complex components needed by the transportation industry to reduce vehicle weight. However, one of the most recognized problems for the industrial processing, e.g. deep drawing, is the occurrence of “earing” which is caused by the plastic anisotropy of the sheets. Extensive research work has been done both theoretically and experimentally to find the mechanisms of complex texture evolution during hot deformation and the subsequent heat-treatment in the hot tandem rolled sheets. Obtaining a strong cube texture before cold rolling is a widely accepted method to solve this problem, which leads to a relatively homogeneous deformation, then earing can be prevented.
Unlike steels whose structure can be changed by phase transformation, recrystallization is the only way to manipulate the microstructure of aluminum. For the purpose of energy saving, full recrystallization is expected to occur during cooling of the hot-rolled strip after hot-rolling, which is called self-annealing, afterwards a strong cube texture can be developed. According to the results of ENGLER et al [1], a high recrystallization rate has been observed in Al-Mg alloy due to addition of element Mg. However, recrystallization during self-annealing is largely influenced by the softening process during hot tandem rolling, including dynamic recovery, dynamic recrystallization (DRX) and inter-stand static recrystallization [2]. It is well known that dynamic softening processes which decrease the driving force of recrystallization during self-annealing are closely associated with the deformation parameters. So a detailed understanding of hot deformation behavior of AA5182 aluminum alloy is desired. A lot of works have been performed to investigate the hot deformation process of aluminum alloys, for instance, LIN et al [3] have studied dynamic recrystallization during hot torsion of Al-4Mg alloy and dynamic recrystallization occurred in a certain range of Z parameter, i.e. 19.3≤ln Z≤24.8. IHARA et al [4] believed that DRX was more frequent in Al-3Mg alloy after 0.2%Sc was added. A model of microstructural and texture evolution during the hot tandem rolling process of 5××× aluminum has been developed by WELLS et al [5-7]. Based on the investigation of stress relaxation of AA5182 during hot deformation, a new method to model the recovery process in the aluminum alloy has been provided by BANGE [8].
Due to the requirement of high quality, AA5182 aluminum sheets are usually produced by high-speed hot tandem rolling. Meanwhile, as aluminum alloy 5182 belongs to high strength aluminum alloy compared to 1××× and 3××× aluminum alloys, it has a high deformation resistance, resulting in a metal strip steering problem during rolling process. Therefore, a further study of the force in the rolling process associated with a constitutive equation for aluminum alloy 5182 deformed at elevated temperatures is needed. However, up to date, few studies have been reported about AA5182 aluminum alloy on the microstructural and texture evolution during hot-rolling process. Therefore, it is necessary to investigate the hot-compression behavior of aluminum alloy 5182 in order to optimize the deforming parameters for controlling the manufacture procedure and the final properties of the products.
In this work, an empirical constitutive equation of aluminum alloy 5182 compressed at elevated temperatures is proposed, and the microstructure and texture evolution during hot-compression are investigated as well. Finally, the deformation conditions under which the DRX takes place are analyzed.
2 Experimental
2.1 Materials processing
The material used in this work was industrially produced AA5182 aluminum by Southwest Aluminum Group Co. Ltd, which was fully recrystallized after breakdown-rolled. The chemical composition is listed in Table 1.
Table 1 Main chemical composition of AA5182 aluminum alloy (mass fraction, %)

The dimensions of plain strain compression (PSC) specimens are 20 mm in length, 10 mm in width and 6 mm in thickness. They were machined from the slab sheet whose surface was removed. The specimen width was parallel to the rolling direction to get rid of the effect of initial texture. The experiments were undertaken using Gleeble-1500 thermo-simulator in different conditions. The actual deformation parameters were decided by the measured data. In order to measure the real compression temperature, a thermocouple was affixed at the top of the specimen. Lubricant with 70% graphite was placed between the specimen and platen on the contact surface. All specimens were heated to the desired deformation temperature in 1 min, and held for 3 min at the temperature before compression. Then the specimens were water-quenched within 1-2 s after compression, so as to maintain the deformed microstructure at end of deformation. Figure 1 shows the schematic diagram of the deformed sample of PSC.
2.2 Analysis of microstructure and texture
Optical microscope with the polarized light was used to observe the microstructure of the hot deformed samples which underwent electro-polishing and anodic oxidation. Micrograph was taken from the longitudinal section, i.e., the elongation direction (ED) and the normal direction (ND) of the samples.
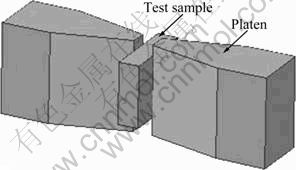
Fig. 1 Schematic diagram of deformed sample
One third of the material from the surface of the samples for texture measurement was removed so as to maintain the plane strain deformation region. X-ray diffractometry instrument with the applied voltage of 40 kV and current of 40 mA was used to measure the incomplete pole figure. The incomplete pole figures of {111}, {200}, {220} and {311} were measured. Orientation distribution functions (ODFs) were computed from these incomplete pole figures with series expansion method. And two dimensional ODFs were plotted in the constant φ2 sections with the method proposed by TANG et al [9].
3 Results and discussion
3.1 Flow stress analysis
Figure 2 shows the true stress-true strain curves of hot compression of aluminum alloy 5182 under different deformation conditions. The maximum flow stress increases with increasing the strain rate and decreases with increasing the deformation temperature. Generally, the flow stress changes very little when the strain exceeds a certain value. However, under some deformation conditions, it decreases with the increase of strain.
It is widely accepted that the relationship between flow stress and dislocation density can be described by σ=σ0+
where σ is the true stress, ρ is the dislocation density. The annihilation and rearrangement of dislocation is accelerated by the high deformation temperature and plenty time for this dislocation behavior is provided by small strain rate, then a relative lower dislocation density will be attained which indicates a lower flow stress according to the formula.
From Fig. 2, it also can be seen that under a certain deformation condition (except for the curve of 10 s-1 in Fig. 2(d)), the true stress increases gradually with strain, then reaches a plateau, which is finally followed by a steady state of flow stress. Generally, the true stress-true strain curves presented in Fig. 2, in which dynamic recovery is expected to occur, can be divided into three parts involving work hardening, transition stage and steady flow stage. During the initial stage of the deformation, there is an increase in the flow stress as dislocations multiply and interact. However, as the dislocation density increases, the driving force accumulates so as to accelerate the rate of recovery. At a certain strain, the rates of work hardening and recovery reach a dynamic equilibrium, the dislocation density remains constant and a steady-state flow stress is reached [10]. It should be noted that when the compression test was carried out under 500 ℃ with the strain rate up to 10 s-1, the true stress-true strain curve exhibits a obvious peak, which is the characteristic of dynamic recrystallization.
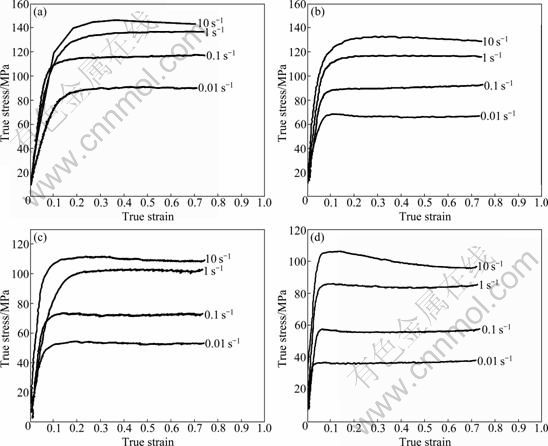
Fig. 2 True stress-true strain curves of hot-compression of aluminum alloy 5182 under different conditions: (a) 350 ℃; (b) 400 ℃; (c) 450 ℃; (d) 500 ℃
During hot deformation of aluminum, it is commonly accepted that the relationship between the steady-state stress, strain rate and deformation temperature can be expressed as follows [11]:
Z=A[sinh(ασ)]n (1)
Z=A1σn (2)
Z=A2exp(βσ) (3)
where Z is the Zener-Hollomon parameter defined by ZENER and HOLLOMON [12]:
(4)
Equation (1) is used for all stress level, while Eq. (2) and Eq. (3) are used for low stress level and high stress level, respectively. Substituting Z of Eqs. (2) and (3) with Eq. (4), and taking nature logarithm of both sides of the developed equations, we have
(5)
(6)
where Q is the apparent activation energy for hot deformation; R is the universal gas constant;
σ and T are strain rate, stress and deformation temperature, respectively; A1, A2, n and β are the material constants.
The steady stresses under different deformation conditions are given in Table 2. The parameters in Eqs. (5) and (6) can be derived by the mean of linear regression. The slopes of the line for ln
-ln σ and ln
- σ represent n and β, respectively (Fig. 3). The average values of n=9.13 and β=0.108 with the relative standard deviation of 34.6% and 9.5%, are obtained, respectively (Table 3). Therefore, the constitutive relationship for high stress level is chosen to describe the flow stress behavior of the hot-compression of aluminum alloy 5182 because of the relatively lower standard deviation.
Table 2 Steady stress under different deformation conditions
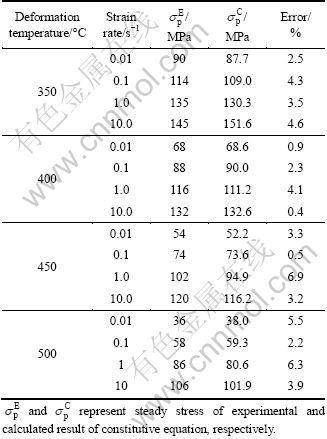
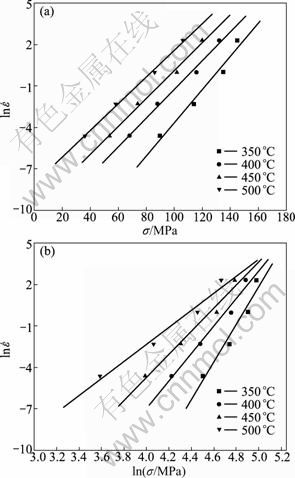
Fig. 3 Variation of flow stress of hot-compression of aluminum alloy 5182 with strain rates at critical strain and different temperatures: (a) ln
-σ; (b) ln
-ln σ
The values of Z parameter under different deformation conditions are given in Table 4. The apparent activation energy Q=143.5 kJ/mol can be derived from σ-1/T plot (Fig. 4) as the slope and the material constant A2=8.14×105 can be derived from ln Z-σ plot (Fig. 5) as the intercept, respectively. Consequently, the constitutive equation of hot-compression of aluminum alloy 5182 is given as follows:
ln
=13.61-
×0.108σ (7)
3.2 Microstructure and texture observation
Figure 6 shows the optical microstructures of the hot compressed aluminum alloy 5182 in ND-RD plane under different compression conditions. It can be seen that all the pictures are characterized by fibrous microstructure, in which the grains elongate along rolling direction. Some new recrystallized grains can be found among the primary elongated grains, when strain rate reaches 1 s-1 and deformation temperature is above 400 ℃ (some optical microstructures are not shown in Fig. 6). These indicate that dynamic recrystallization may occur under such deformation conditions. Especially, from Fig. 6(f), a large amount of new grains are observed, which means that the extent of dynamic recrystallization is very large. Similar results were reported by ZHANG et al [13] and WANG et al [14]. A dynamic recrystallization during hot torsion of Al-4Mg by LIN et al [3] showed that the occurrence of dynamic recrystallization was accelerated with increasing the strain rate at high deformation temperature. This is in agreement with the large amount of new grains in Fig. 6(f) and the peak of strain-stress curve of 10 s-1 in Fig. 2(d). But, it should be pointed out that there is no visible peak in true stress-true strain curves (except for the curve of 10 s-1 in Fig. 2(d)) which is the characteristic of discontinuous dynamic recrystallization. The reason accounted for this phenomenon is that the softening caused by dynamic recrystallization is so little that it cannot be reflected by flow stress. When the extent of dynamic recrystallization increases, the visible peak in true stress-true strain curve is observed (the curve of 10 s-1 in Fig. 2(d)).
Table 3 Results of linear regression analysis of n and β
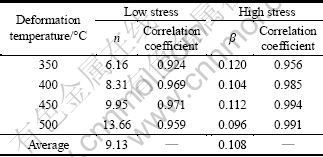
Table 4 Values of Z parameter under different deformation conditions
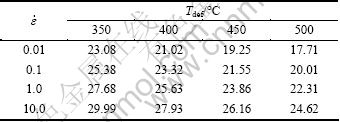
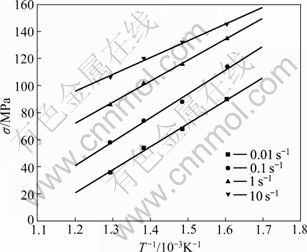
Fig. 4 Variation of flow stress of hot-compression of aluminum alloy 5182 with reciprocal of deformation temperature at different strain rates
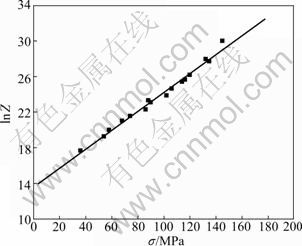
Fig. 5 Relationship of flow stress and ln Z
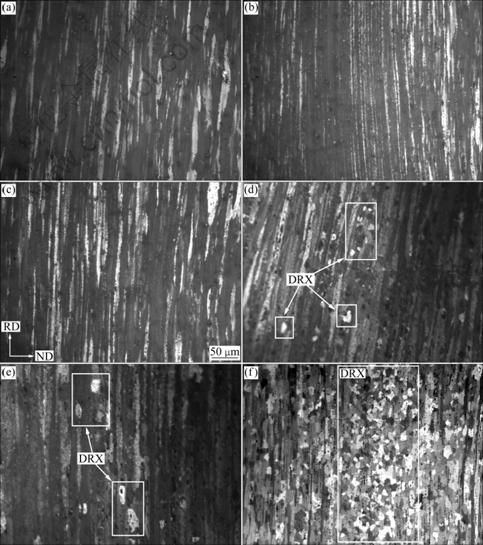
Fig. 6 Polarized optical microstructures of aluminum alloy 5182 under different hot deformation conditions: (a) Tdef=350 ℃,
= 0.1 s-1, ε=0.7; (b) Tdef=350 ℃,
=0.01 s-1, ε=1.9; (c) Tdef=400 ℃,
=0.1 s-1, ε=0.7; (d) Tdef=400 ℃,
=1 s-1, ε=1.2; (e) Tdef=450 ℃,
=1 s-1, ε=1.2; (f) Tdef=500 ℃,
=10 s-1, ε=1.9
The ODFs of AA5182 alloy sample hot compressed under different deformation conditions are shown in Fig. 7.
Typical rolling deformation textures, including the brass {011}á211?, copper {112}á111? and S {123}á634? components, can be found in Fig. 7(b). However, in Figs. 7(c) and (d), the cube texture {100}á001? is found and the orientation density of cube texture in Fig. 7(d) is higher than that in Fig. 7(c). Cube texture is considered as a main recrystallization texture in aluminum. Then, another evidence of dynamic recrystallization under the deformation condition is provided by the occurrence of cube texture. The more the dynamic recrystallization happened, the higher the orientation density of cube texture is. But it can also be seen that the cube texture is very weak, which indicates that very few new recrystallized grains with cube orientation have formed during dynamic recrystallization (DRX). Even though, these new cube oriented grains may be the sets of recrystallization during self-annealing.
Figure 8 shows the orientation density f(g) along β fiber at different deformation temperatures and strain rates, respectively. The maximum density along β fiber is located at an orientation near the Bs position, and the minimum density is located at C position. Similar results were found in other works [15-16]. One possible explanation is that the cross slip is obstructed because of the greatly reduced stacking fault energy in aluminum alloy 5182 due to the much high content of Mg element [17]. Furthermore, the orientation densities along β fiber decrease by increasing either deformation temperature or strain rate, which is consistent with the conclusion of microstructure observation. However, contrary conclusion, i.e. with the increase of deformation temperature the texture can sharpen significantly, was made by some other researchers [18-19]. According to DUCKHAM’s argument, the general sharpening of texture with deformation temperature increasing is attributed to the healing out of dislocation within the subgrains. But in the present work, the dynamic recovery is replaced by the dynamic recrystallization at high deformation temperature; therefore, a part of deformation texture is consumed, which leads to the reduction of the orientation densities along β fiber. Besides, Fig. 8 indicates that the deformation temperature affects Brass component most dramatically. However, C component decreases rapidly as strain rate increases. It also should be noted that the overall texture intensity of hot-rolled AA5182 sheet in Fig. 7 and Fig. 8 are relatively low, which may be due to the nearly random orientation distribution of the initial microstructure (Fig. 7(a)).
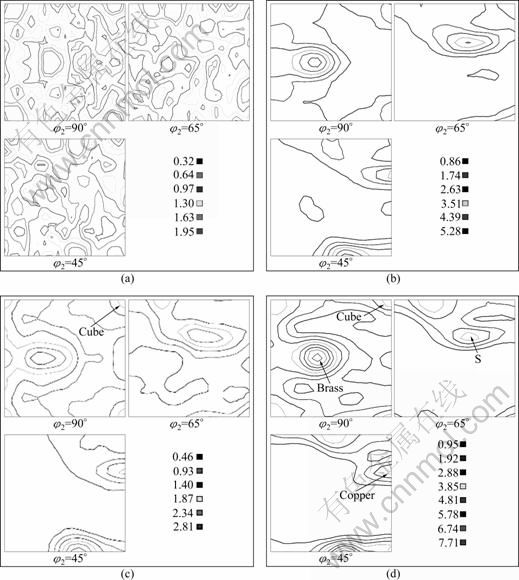
Fig. 7 Crystallographic textures of aluminum alloy 5182 sample under hot-compression under different deformation conditions: (a) Initial texture; (b) Tdef=350 ℃,
=1 s-1, ε=1.2; (c) Tdef=450 ℃,
=1 s-1, ε=1.2; (d) Tdef=500 ℃,
=10 s-1, ε=1.9
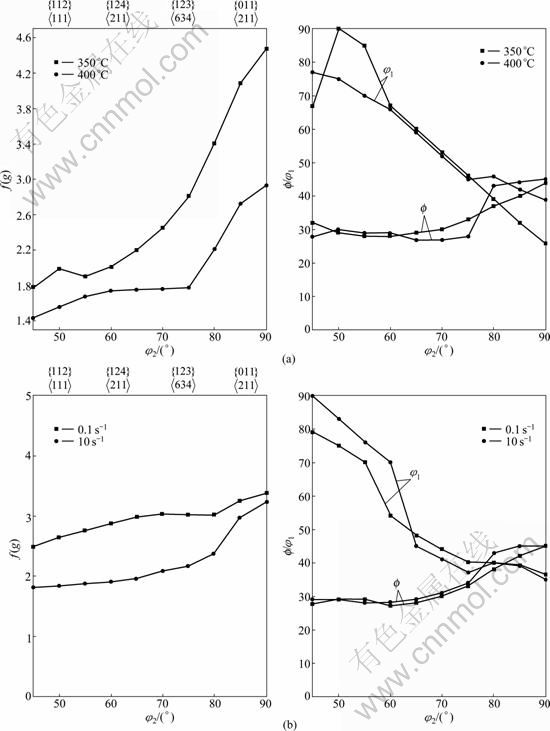
Fig. 8 Orientation density along β fibers for hot-compression of aluminum alloy 5182 at different deformation temperatures and strain rates: (a)
=1.0 s-1, ε=0.7; (b) Tdef=450 ℃, ε=1.9
4 Conclusions
1) The hot deformation behavior of aluminum alloy 5182 can be described by the constitutive relationship for high stress level, and the constitutive equation is derived
as ln
=13.61-
×0.108σ.
2) When deformation temperature reaches 400 ℃ and strain rate reaches 1 s-1, DRX (dynamic recrystallization) takes place.
3) The hot-compression textures are distributed along β fiber with the strongest orientation density located nearly at Bs position. The orientation densities along β fiber decrease by increasing either deformation temperature or strain rate
4) Cube texture is observed in the sample undergoing DRX during hot-compression.
References
[1] ENGLER O, LOCHTE L, HIRSCH J. Through-process simulation of texture and properties during the thermomechanical propecessing of aluminium sheets [J]. Acta Materialia, 2007, 55(16): 5449-5463.
[2] DOHERTY R D, HUGHES D A, HUMPHREYS F J, JONAS J J, JUUL JENSEN D, KASSNER M E, KING W E, MCNELLEY T R, McQUEEN H J, ROLLETT A D. Current issues in recrystallization: A review [J]. Materials Science and Engineering A, 1997, 238(2): 219-274.
[3] LIN Jun-pin, WANG Yan-li, ZHI Lin, CHEN Guo-liang. Dynamic recrystallization during hot torsion of Al-4Mg alloy [J]. Journal of University of Science and Technology Beijing, 2003, 10(2): 45-50.
[4] IHARA K, MIURA Y. Dynamic recrystallization in Al-Mg-Sc alloys [J]. Materials Science and Engineering A, 2004, 387/388/389(1): 647-650.
[5] WELLS M A, LLOYD D J, SAMARASEKERA I V, BRIMACOMBE J K, HAWBOLT E B. Modeling the microstructural changes during hot tandem rolling of AA5xxx aluminum alloys: Part I. Microstructural evolution [J]. Metallurgical and Materials Transaction B, 1998, 29B(3): 611-620.
[6] WELLS M A, LLOYD D J, SAMARASEKERA I V, BRIMACOMBE J K, HAWBOLT E B. Modeling the microstructural changes during hot tandem rolling of AA5xxx aluminum alloys: Part II. Texture evolution [J]. Metallurgical and Materials Transaction B, 1998, 29B(3): 621-633.
[7] WELLS M A, LLOYD D J, SAMARASEKERA I V, BRIMACOMBE J K, HAWBOLT E B. Modeling the microstructural changes during hot tandem rolling of AA5xxx aluminum alloys: Part III. Texture evolution [J]. Metallurgical and Materials Transaction B, 1998, 29B(3): 709-719.
[8] BANGE M E. Stress relaxation of AA5182 during hot deformation [D]. Urbana-Champaign: University of Illinois, 2003.
[9] TANG Jian-guo, ZHANG Xin-ming, DENG Yun-lai. Texture decomposition with particle swarm optimization method [J]. Computer Material Science, 2006, 38(2): 395-399.
[10] HUMPHREYS F J, HATHERLY M. Recrystallization and related annealing phenomena [M]. Elsevier, 2004: 416.
[11] McQUEEN H J, RYAN N D. Constitutive analysis in hot working [J]. Materials Science and Engineering A, 2002, 322(1/2): 43-63.
[12] ZENER C, HOLLOMON J H. Effect of strain-rate upon the plastic flow of steel [J]. Journal of Applied Physics, 1944, 15(1): 22-32.
[13] ZHANG Xin-ming, XU Min, TANG Jian-guo, OU Jun. Hot-compression behavior of Al-1Mn-1Mg alloy [J]. Journal of Central South University of Technology, 2010, 17(3): 425-430.
[14] WANG Y, SHAO W Z, ZHEN L, YANG L, ZHANG X M. Flow behavior and microstructures of superalloy 718 during high temperature deformation [J]. Materials Science and Engineering A, 2008, 497(1/2): 479-486.
[15] DUCKHAM A, KNUTSEN R D, ENGLER O. Influence of deformation variables on the formation of copper-type shear bands in Al-1Mg [J]. Acta Materialia, 2001, 49(14): 2739-2749.
[16] PANCHANADEESWARAN S, FIELD D P. Texture evolution during plane strain deformation of aluminum [J]. Acta Metallurgica et Materialia, 1995, 43(4): 1683-1692.
[17] MAO Wei-min, ZHANG Xin-ming. Quantitative texture analysis of crystalline materials [M]. Beijing: Metallurgical Industry Press, 1995: 110-112.
[18] LIU W C, MORRIS J G. Effect of hot and cold deformation on the β fiber rolling texture in continuous cast AA5052 aluminum alloy [J]. Scripta Materialia, 2005, 52(12): 1317-1321.
[19] JUUL J D, SHI H, BOLINGBROKE R K. Texture development in Al 3003 during hot plane strain compression [J]. Materials Science Forum, 1994, 157-162(1): 745-752.
(Edited by HE Yun-bin)
Foundation item: Project(50905188) supported by the National Natural Science Foundation; Project(2012CB619500) supported by Key Basic Research Program of China
Received date: 2011-05-31; Accepted date: 2011-10-24
Corresponding author: TANG Jian-guo, Professor; Tel: +86-731-88830265; E-mail: jgtang@csu.edu.cn