Article ID: 1003-6326(2005)06-1361-06
Preparation of hyperthermal lithium complex grease
MAO Da-heng(毛大恒), FENG Hao(俸 颢), SUN Xiao-ya(孙晓亚)
(School of Mechanical and Electrical Engineering, Central South University,
Changsha 410083, China)
Abstract: Using 12-hydroxystearate, nonan-edioic acid and lithium hydroxide as thickener, refined mineral oil and synthetic oil as base oil, along with some structure improver, antioxidant and anti-wear extreme pressure additive, lithium complex grease was developed. The dropping point of the grease is 331℃, friction factor is 0.025-0.026 under 1.0kN, especially above 220℃, its friction factor is 2/3 of those of urea-based greases and other high temperature greases. At the same time, it has good waterproof, anti-oxidation effect and anti-corrosion properties. The results of the field experiment proves that its working temperature is higher than 600℃, and it has reasonable working life in 800℃.
Key words: lithium complex grease; structure improver; anti-wear agent CLC
number: TG580.21 Document code: A
1 INTRODUCTION
Along with the development of metallurgy, mine, material process, mechanism, chemical industry, communications and transport, more and more equipments run at high or extraordinarily high temperature, and the equipment need elevated temperature property of grease. The development and production of high-temperature grease in our country is behindhand to developed country. At present, absolute majority of high temperature grease is import, so, it is essential to develop a high temperature grease with excellent performance[1, 2].
In 1962, the first lithium grease passed field experiment in America[3]. From 1970s, lithium complex grease developed rapidly, and lithium complex grease with dibasic acid, stearinic acid and ortho-hydroxybenzoic are called new generation lithium grease[4, 5]. In China, there are a lot of research to lithium complex grease[6-12], but it is not in a creative way and is based on the formulation and technology, so we have great gap to foreign advanced technology. This research work is on the base lithium complex grease, its major factor which impacts the high-temperature behavior was discussed, a new extraordinarily high temperature grease was developed. The developed grease have high dropping point, low friction factor, with working temperature higher than 600℃, and reasonable working life in 800℃.
2 EXPERIMENTAL
2.1 Prescription mode
The properties of grease are affected by thickener, base oil and addition agent. At present, lithium complex grease, urea-based grease and aluminum complex grease are very popular in use, especially lithium complex grease and urea-based grease, their dropping point is 250-270℃, the highest working temperature is about 240℃[13, 14]. To get a complex grease with dropping point over 310℃ and working temperature above 600℃, the batch formula was improved on the base of lithium complex grease. The prescription mode is as follows.
1) Thickener
12-hydroxystearate, nonan-edioic acid and lithium hydroxide were used as leading materials, a small quantity of organic polymer and inorganic matter were added as structure improver.
2) Base oil
Base oil is the basis of grease, about 70%-80% in all. In grease, base oil is fastened in structure frame created by the thickener, affecting the lubricant performance of grease greatly. The base oil should have property of low freezing point and vapor ability, high viscosity-temperature and flash point, and good oxidation stability, The formulation adopts unit system of refined mineral oil which has high flash point and synthetic oil. The performance parameter is listed in Table 1.
3) Anti-wear extreme pressure additive and bulking agent
To improve the abrasion-resistance and extreme pressure performance, and gain low friction factor, some borate, WS2 colloidal powder and anti-wear extreme pressure additive were added to
Table 1 Chief performance parameters of base oil
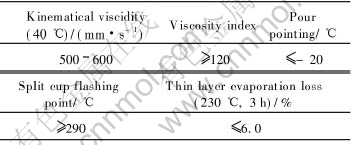
this novel grease.
2.2 Preparation process
One-step technology was used to prepare the grease. Added 12-hydroxystearate, nonan-edioic acid, water solution of lithium hydroxide into reactor in suitable proportion, then added partial base oil, controled the heating velocity and degree of intermix, the first saponification proceeded. And added the residual base oil, raised the temperature to 220-230℃. When the grease was cooled down to 130℃, added WS2 colloidal powder, structure improver and extreme pressure additive, finally homogenized and milled.
To compare the contribution of structure improver and WS2 colloidal powder to the performance of grease, in the preparation process the greases were divided to two groups, one group (MW-01) is only added extreme pressure additive, another group (MW-02) is added WS2 colloidal powder, structure improver and extreme pressure additive.
3 RESULTS AND DISCUSSION
3.1 Influence of structure improver and WS2 colloidal powder bulking agent on dropping point
Dropping point test was carried out in SYD—4929 dropping point apparatus according to the standards of GB/T4929—85. The dropping point of grease which is not added with structure improver and WS2 colloidal powder is 282℃, while that is added structure improver and WS2 colloidal powder is 331℃, which is higher than other high temperature greases by 50-110℃(Table 2). This result proves that structure improver and WS2 colloidal powder bulking agent have remarkable effect on dropping point.
Table 2 Dropping point of some high temperature grease(℃)
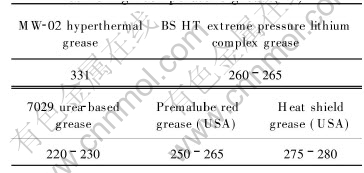
3.2 Infection of WS2 colloidal powder bulking agent on oil film strength and friction factor
The oil film strength and friction factor of MW-01 and MW-02 were tested on MRC—10A four-ball extreme pressure tester at 30, 50, 100, 150, 200 and 220℃, the results are shown in Figs.1-3.
Friction factor of MW-02 grease which is added with WS2 colloidal powder is lower than that of MW-01. This anti-attrition effect is obvious especially when working temperature is at 150℃. Friction factors of MW-02 are 2/3 as that of MW-01 at 150 and 200℃, respectively. For example, the friction factor of MW-02 is 0.027 at load of 1.0kN and 150℃, while that of MW-01 is 0.039. At 200℃, the friction factor of MW-02 is 0.027,
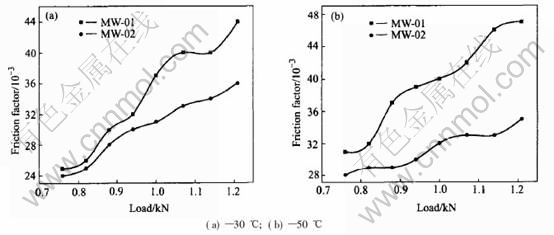
Fig.1 Comparison of oil film strength and friction factor between MW-01 and MW-02 at different temperatures
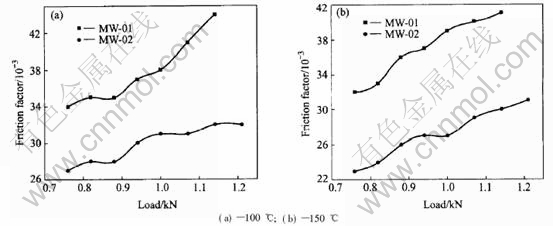
Fig.2 Comparison of oil film strength and friction factor between MW-01 and MW-02 at different temperatures
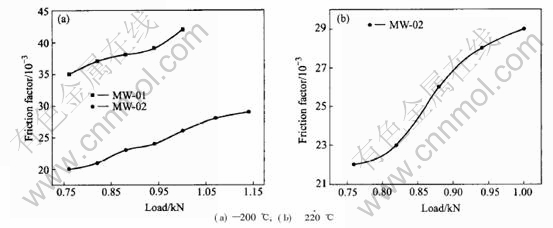
Fig.3 Comparison of oil film strength and friction factor between MW-01 and MW-02 at different temperatures
that of MW-01 is 0.042. At 220℃, the friction factor of MW-02 is 0.029, while MW-01 is seized.
At high temperature the oil film strength of MW-02 grease that is added with WS2 colloidal powder has significant advantages over MW-01 grease that is added with nothing. At 150℃, the oil film strength of MW-01 grease is 1.21kN, while that of MW-02 is 1.14kN. At 200℃, oil film strength of MW-01 grease is 1.14kN, while that of MW-02 is 1.0kN. At 220℃, oil film strength of MW-01 grease is still 1.0kN, but MW-02 has lost its lubricating ability.
3.3 Contrast of MW-02 grease to other high-temperature grease in oil film strength and friction factor
In order to prove the performance of MW-02 grease, we select urea-based grease, high temperature lithium grease, import high temperature grease (NCH Premalube heat shield grease) in the current market as reference objects. The result are shown in Figs.4-6.
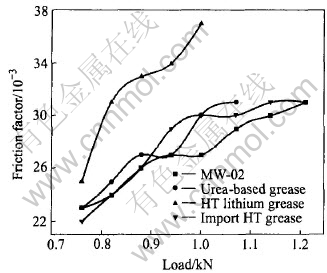
Fig.4 Comparison of oil film strength and friction factor between four greases at 150℃
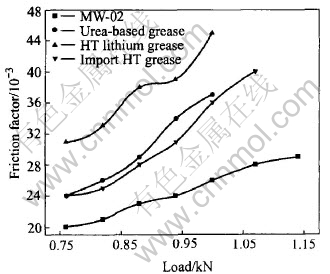
Fig.5 Comparison of oil film strength and friction factor between four greases at 200℃
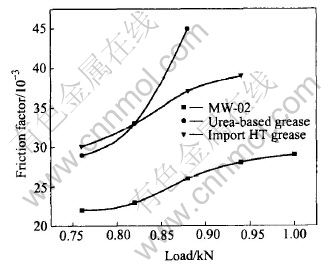
Fig.6 Comparison of oil film strength and friction factor between four greases at 220℃
The measurement results indicate that when working temperature is over 150℃, the oil film strength of MW-02 grease is higher than those of urea-based grease, high temperature lithium complex grease and import high temperature grease, and the friction factor of MW-02 grease is the lowest. Especially when the working temperature is over 200℃, the friction factor of MW-02 grease is only 2/3 of other high temperature greases. So, MW-02 grease has well anti-attrition capability both at normal atmospheric temperature and high temperature.
4 MICROSTRUCTURE ANALYSIS AND LUBRICANT MECHANICS RESEARCH
Fig.7 shows the stereoscan photograph by JSM-5600LV scanning electronic microscopy(SEM), sample 1 is MW-01 grease, sample 2 is MW-02 grease. It can be seen from Fig.7 that the soap fiber of MW-01 is thin filament, but that of MW-02 is thick filament, which is obviously furcated. At the same time, filament fibrous tissue of MW-02 is in higher proportion, which can confine the base oil in fiber framework better. The result proves that MW-02 grease has better framework construction than MW-01 grease.
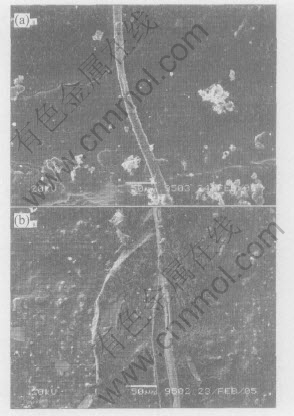
Fig.7 SEM images of MW-01 grease(a) and MW-02 grease(b)
In grease, base oil is fixed in the thicker framework construction, whose strength and high temperature stability partly determinate the dropping point of grease. It is the base reason why the dropping point of MW-02 grease is obviously higher than that of MW-01 grease, which can prove that the structure improver has good effect, too.
The microstructure of WS2 crystal is layered hollow sphere with hexagonal, its surface form hexagonal network with S—W—S molecular, layers are connected by van de waals force. This weak binding force is easy to be sheared on the middle of layers, put up low friction factor[15]. Because WS2 crystal is so stable at high temperature, even above 400℃, WS2 can create compact WO3 covering layer by retarded oxidation which can stop further oxidation, and WO3 has low friction factor, too, which stop glue on metal surface.
The microstructure of WS2 colloidal powder by JSM-5600LV scanning electronic microscope is lamellar structure, bedding surface is very smooth, and the length and width are much greater than thickness (Fig.8). After multiple milling, under scanning electronic microscope(SEM) we can see that there are a large number of micro grains whose length and width are resemble to thickness at platelet (Fig.9). These micro grains and base grease form plentiful oil micro-pools that are locally sealed. So, the antifriction of WS2 colloidal powder in lubrication is not rolling bearing effect but shearing effect along weak-bonded bedding-plane and oil micro-pool effect.
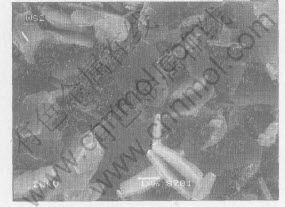
Fig.8 Microstructure of WS2 powder
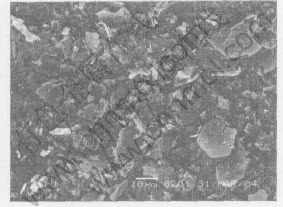
Fig.9 Microstructure of WS2 powder after repetitious milling
The result proves that the grain size of WS2 powder greatly affects the friction factor. At the grain size of 0.3-7.6μm, the friction factor decrease with decreasing grain size (Table 3). When WS2 powder and MoS2 powder whose grain sizes are similar are mixed with kerosene oil in the same proportion, their friction factors were measured. The results show that the friction factor of WS2 is lower than that of MoS2(Table 4). So, WS2 colloidal powder is a stable and low-loss lubricant system, it can make MW-02 grease has low friction factor, good anti-high temperature and extreme pressure performance when added as extreme-pressure additive.
Table 3 Infection of different grain sizes of WS2 powder on friction factor at different loads
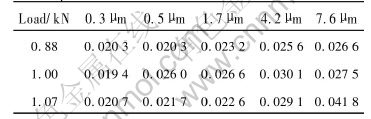
Table 4 Comparison of friction factors between WS2 and MoS2

5 CONCLUSION
1) WS2 colloidal powder is a stable and low-loss lubricant system, it can make MW-02 grease has low friction factor and good anti-high-temperature and extreme pressure performance when added as extreme-pressure additive.
2) This kind of structure improver can obviously improve the microstructure of soap fiber in lithium complex grease, turn thin filament to thick filament, and obviously increase the proportion of filament fibrous tissue.
3) Using WS2 colloidal powder as bulking agent, the dropping point of MW-02 hyperthermal grease is 331℃. MW-02 hyperthermal grease has anti-high temperature and extreme pressure performance, and can work long-time at above 600℃.
4) Above 150℃, the oil film strength of MW-02 grease is higher than those of urea-based grease, high temperature lithium grease and imported high temperature grease, while the friction factor is the lowest. Especially at over 200℃, the friction factor of MW-02 grease is 2/3 of those of urea-based grease and other high temperature lithium greases.
REFERENCES
[1]LI Xue-jing, PAN Yuan-qing, ZHOU Hui-juan. General situation of grease [J]. Lubricant and Fuel, 2003, 13(4): 10-14. (in Chinese)
[2]LUO Rui-bin. Update prospect for global lubricating grease industry [J]. Lubrication Engineering, 1994(2): 63-68. (in Chinese)
[3]Compell I D, Harting G I. A new generation of lithium complex grease [J]. NLGI Spokesman, 1976, 40(6): 193-200.
[4]Ehrlish M, Musili T G. The development of lithium complex grease [J]. NLGI Spokesman, 1980, 12(6): 87-100.
[5]Hissa R, Brasil T. Lithium complex grease with an unusually high dropping point [J]. NLGI Spokesman, 1995, 59(1): 19-20.
[6]YI Jian-guo, YANG Shu-hong. Performance and application of lithium complex grease [J]. Synthetic Lubricant Material, 2003, 13(4): 15-18. (in Chinese)
[7]YUAN Jun, JIANG Chao-hui. Performance and application of decanedioic acid extreme pressure lithium complex grease [J]. Lubricant, 2003, 30(1): 4-6. (in Chinese)
[8]CUI Jing-jie, LI Yan-qiu. Application of PAO and ester oil in synthetic lubricant [J]. Lubricant, 2004, 19(1): 7-12. (in Chinese)
[9]CHEN Hui-qin. Application of MoS2 in grease [J]. Synthetic Lubricant Material, 2002, 29(1): 13-19. (in Chinese)
[10]XU Jian-ping. Sense of technology movement of grease [J]. Synthetic Lubricant Material, 2004, 31(1): 27-30. (in Chinese)
[11]JIANG Ming-jun, GUO Xiao-chuan, CHEN Guo-xu. Research of lithium complex grease [J]. Lubrication and Seal, 2000(5): 25-28. (in Chinese)
[12]JIANG Ming-jun, GUO Xiao-chuan, CHEN Guo-xu. Application of additive in lithium complex grease [J]. Lubrication and Seal, 2000(3): 1-7. (in Chinese)
[13]ZHANG Cheng-qing. Grease Making [M]. Beijing: China Petrochemical Press, 2003. (in Chinese)
[14]YANG Zheng-yu. A survey on the recently research about the grease making in America, Europe and Asia [A]. Memoir of National Ninth Grease Technical Exchange Meeting [C]. Beijing: Petroleum Processing and Petrochemicals, 1997, 11-16.
[15]SUN Ke-hui, WEI Qin, LUO Wen-dong. Preparation and microstructure analysis of nano WS2 solid lubricating material[J]. Mining & Metallurgy, 2001(1): 46-48. (in Chinese)
(Edited by LONG Huai-zhong)
Received date: 2005-03-03; Accepted date: 2005-05-30
Correspondence: MAO Da-heng, Professor; Tel: +86-731-8876350; E-mail: mdh@mail.csu.edu.cn