文章编号:1004-0609(2013)S1-s0581-04
预成形设计对钛合金叶片热模锻造过程回弹的影响
马 龙,高 涛,彭孝国
(电子科技大学 机械电子工程学院,成都 611731)
摘 要:钛合金叶片的型面复杂,截面宽厚比大,且各截面之间有一定的转角,因而在叶片热模锻造后残余应力会使叶片产生回弹,从而影响叶片锻件的尺寸精度。采用不同的预成形毛坯,叶片终锻件的残余应力是不同的。因此,研究预成形设计对钛合金叶片热模锻造过程回弹的影响对提高叶片产品质量有重要意义。采用横截面为圆形和椭圆形的预成形毛坯,模拟和分析两种情况下叶片热模锻造过程,计算两种情况下叶片的回弹量。结果显示:采用椭圆形毛坯获得的叶片等效应变差值和温度差小,卸载后锻件的等效弹性应变较小,回弹量较小。
关键词:预成形设计;热模锻造;残余应力;回弹
中图分类号:TG146.2 文献标志码:A
Influence of preform design on spring-back in hot die forging of titanium blade
MA Long, GAO Tao, PENG Xiao-guo
(School of Mechanical, Electronic and Industrial Engineering, University of Electronic Science and Technology of China, Chengdu 611731, China)
Abstract: The titanium blade has characteristics of complex molding surface, very large ratio of cross-sectional width to thickness and a certain rotational angle between each cross-section. After the hot die forging, the existence of residual stress causes the spring-back of the blade, which reduces the dimension accuracy of the blade. Different preform design will affect the residual stress of the forged blade. Therefore, it is important to research the influence of the preform design on the spring-back in the hot die forging of the titanium blade. The circle cross-section and ellipse cross-section blank were designed. The blade forging processes with different blanks were simulated and analyzed, and then the blade spring-back was calculated. The result shows that the equivalent strain difference and the temperature difference of the blade which is forged from ellipse cross-section blank are little. The equivalent elastic strain after unloaded is little and the spring-back is little.
Key words: perform design; hot-die forging; residual stress; spring-back
钛合金叶片是锻造生产中最难成形的零件之一。叶片的型面复杂,截面宽厚比大,而且各截面之间有一定的转角[1-3]。叶片在热模锻造后,残余应力使其发生回弹。而不同形状的预成形毛坯在热模锻造后的残余应力不同,因此,研究预成形设计对钛合金叶片热模锻造过程回弹的影响对提高叶片产品质量有重要意义。
国内外学者对预成形及回弹进行了大量研究。KANG等[4]将叶片锻造过程作为二维平面应变问题处理,用二维有限元正向模拟与反向跟踪技术相结合的方法,采用库伦摩擦对叶片锻造过程进行了预成形设计,得到了充填良好的预成形毛坯的形状。AKIYASU等[5]采用有限元法对钛合金涡轮叶片等温锻进行二维刚塑性有限元模拟,确定预成形毛坯的最佳放置位置。WANG等[6]曾用有限元反向模拟技术确定了叶片预成形毛坯的形状。LU等[7]基于ESO法提出了一种预成形的拓扑优化方法,并对二维叶片叶身截面进行了预成形设计。上述研究都只考虑了预成形毛坯对材料充填的影响。LU等[8]采用ABAQUS对热模锻造航空涡轮叶片由温度引起的误差进行了二维有限元模拟,在一定的温度范围内,估计在卸载和冷却过程中,涡轮叶片所发生的变形,为改善叶片精度提供了基础。OU等[9]采用有限元模拟方法在压力模具变形量和叶片误差之间建立一种定量关系,有效地揭示压力模具变形量的变化对叶片误差的影响。
因此,本文作者以钛合金叶片为研究对象,采用不同的预成形毛坯,研究不同情况下叶片终锻件的等效应变差值和温度差对等效弹性应变的影响,进而研究对终锻叶片回弹量的影响。
1 有限元模型
本研究选用的两种典型的预成形毛坯如图1所示。图1(a)所示为圆形截面毛坯(毛坯A),图1(b)所示为椭圆形截面毛坯(毛坯B),均采用四节点的四面体单元划分单元。模具型腔采用有限元网格近似描述,如图2所示。上、下模具也采用四节点的四面体划分网格。
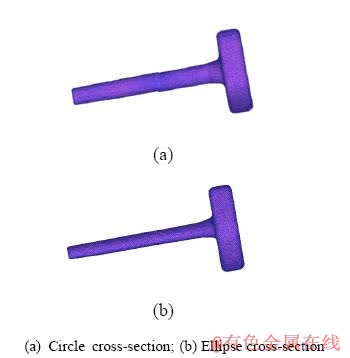
图1 预成形毛坯模型
Fig. 1 Model of preformed blank
叶片材料选用Ti-6Al-4V,初始温度均为950 ℃,采用弹塑性材料模型。叶片材料的泊松比取0.31,采用的流动应力—应变本构关系模型为
(1)
式中:
为等效应力;
为等效应变;
为等效应变速率;T为变形温度。
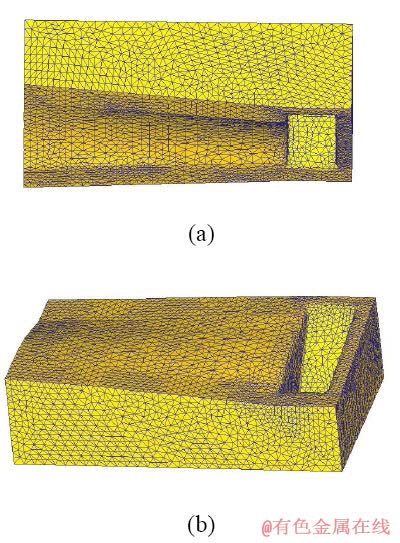
图2 模具模型
Fig. 2 Die model of upper die (a) and lower die (b)
模具采用H13中合金超高强度的热作模具钢。模具材料的泊松比取0.30。上模压下速度为20 mm/s,下模静止不动。上下模具初始温度分别为250 ℃,模具和叶片毛坯间的摩擦因数为0.1。
有限元仿真其他设置如下:1) 叶片毛坯与上下模具及外界空气环境间的热传递以热传导和热对流为主,热辐射所起的作用非常小,可以忽略不计;2) 在叶片热模锻造热力耦合过程中,由机械功转化为热量的效率设为90%;3) 叶片毛坯与外界环境之间的对流换热系数设为0.002 95 N/(S·mm·℃),叶片毛坯与模具接触处的热传导系数设为2 N/(S·mm·℃)[10];4) 仿真步长取0.05 mm。
2 仿真结果与分析
2.1 热模锻造叶片温度分析
叶片热模锻造过程是一个非线性的热—力耦合过程,涉及到工件与模具相接触位置处的热传导效应以及与周围环境空气间的对流传热效应,叶片热模锻造过程中的热能变化能够十分快速直观的表现在它们的温度变化情况上来。
不同压下量下工件的最高温度与最低温度差值如图3所示。从图3中可以看出,当压下量小于5 mm时,毛坯A与毛坯B获得的工件温度差基本相同。当压下量大于5 mm后,毛坯A获得工件的温度差大于毛坯B的温度差值的大小不同,将直接影响各部分金属的流动,致使工件内各部分变形抗力不均匀。由于温度高的部分塑性好变形抗力小,而温度低的部分塑性差变形抗力较大,因此,温度差值越大,意味着工件各部分变形越不均匀,叶片终锻件的残余应力越大,卸载后锻件的等效弹性应变越大,叶片的回弹量越大。
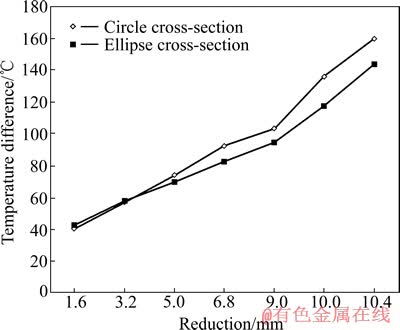
图3 不同压下量时工件温度的差值
Fig. 3 Temperature difference at different reductions
2.2 热模锻造叶片等效应变分析
应变状态对金属的塑性有很大的影响。等效应变上是指将连续介质上的应变“等效地”移植到离散介质的单元(节点)上而获得的应变。所以从模拟结果中选取等效应变来说明不同形状的预成形毛坯对叶片回弹的影响。图4所示为毛坯A获得的叶片终锻件(叶片A)和毛坯B获得的叶片终锻件(叶片B)的等效应变。
从图4中可以看出,叶片A的等效应变差值大于叶片B的等效应变差值。由于工件变形大的区域等效应变大,变形小的区域等效应变小,因此,等效应变的差值越大,则工件变形越不均匀,其内部金属受力也越不均匀,叶片终锻件的残余应力大。残余应力越大卸载后锻件的等效弹性应变越大,从而叶片的回弹量越大。
2.3 热模锻造叶片回弹分析
在叶片热模锻造过程中,由于热作用和不均匀塑性变形,由于在锻造过程中金属的不均匀流动,工件变形不均匀产生残余应力。叶片卸载后,由于塑性变形的不可恢复性,塑性变形部分限制了相邻部分变形的恢复,残余应力破坏了卸载后叶片内的力或力矩的平衡状态,使叶片发生了弹性变形。结合温度差及等效应变的分析,可以得到叶片A的残余应力大于叶片B的残余应力。叶片A和叶片B的等效弹性应变如图5所示。
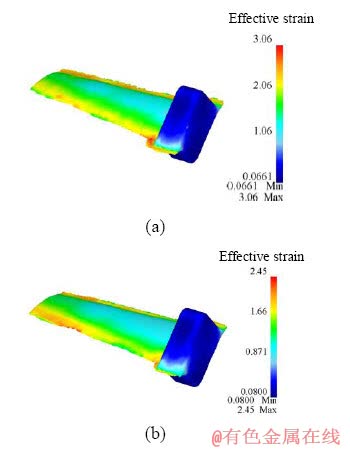
图4 叶片A和叶片B的等效应变
Fig. 4 Effective strain of blades A (a) and B (b)
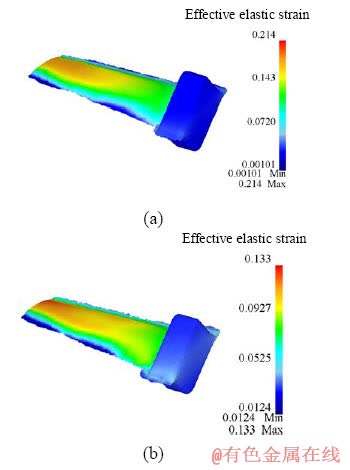
图5 叶片A和叶片B的等效弹性应变
Fig. 5 Equivalent elastic strain of blades A (a) and B (b)
从图5中可以得到,叶片A的最大等效弹性应变为0.214,叶片B的最大等效弹性应变为0.133。叶片叶身的最大厚度为1.5 mm。叶片的回弹量可以用等效弹性应变和叶身厚度的乘积来表示。所以,叶片A的最大回弹量为0.321 mm,叶片B的最大回弹量为 0.199 5 mm。比较叶片A与叶片B的回弹量,可见叶片B的回弹量小于叶片A的回弹量。所以,毛坯B较毛坯A对回弹量的影响小。
综上所述,在以上两种预成形毛坯中,椭圆形截面毛坯获得的叶片终锻件的残余应力小,卸载后锻件的等效弹性应变小。不仅有利于锻压时金属的均匀分布,而且叶片终锻件回弹的更小,其尺寸精度高于圆形截面毛坯获得的叶片尺寸精度。
3 结论
1) 随着压下量的增加,椭圆形截面锻件的温度差和等效应变差小于圆形截面锻件的温度差,获得的叶片终锻件的残余应力小,卸载后锻件的等效弹性应变小,回弹量小。
2) 叶片A的最大回弹量为0.321 mm,叶片B的最大回弹量为0.199 5 mm。可见,椭圆形截面毛坯获得的叶片尺寸精度高于圆形截面毛坯获得的叶片尺寸精度。
REFERENCES
[1] 盖 超, 陈 伟, 吕彦明. DEFORM-3D软件在叶片锻坯结构形式选取中的应用[J]. 热加工工艺, 2007, 36(1): 74-75.
GAI Chao, CHEN Wei, Lü Yan-ming. Application of DEFORM-3D software in optimizing forging stock shape of blade [J]. Hot Working Technology, 2007, 36(1): 74-75.
[2] 齐广霞, 闵慧娜, 陈小峰. TA11钛合金叶片制坯过程三维热力耦合数值模拟[J]. 锻压技术, 2009, 34(2): 124-128.
QI Guang-xia, MIN Hui-na, CHEN Xiao-feng. 3D thermal couple numerical simulation of TA11 titanium alloy blade blank making [J]. Forging & Stamping Technology, 2009, 34(2): 124-128.
[3] OU H, ARMSTRONG C G. Die shape compensation in hot forging of titanium aerofoil sections [J]. Journal of Materials Processing Technology, 2002, 125/126: 347-352
[4] KANG B S, KIM N S, KOBAYASHI S. Computer aided perform design in forging of an airfoil section blade [J]. Int J Mach Tools Manufact, 1990, 30(1): 43-52.
[5] AKIYASU M, SHIGEO H, TANI K, TAKEMURA A, ASHIDA Y. Near net shape forging of titanium alloy turbine blade [J]. ISTJ International, 1991, 31(8): 827-833.
[6] WANG Zhen, XUE Ke-min, LIU Ying-wei. Backward UBET simulation of the forging of a blade [J]. J Mater Process Technol, 1997, 65: 18-21.
[7] LU B, OU H,CUI Z S. Shape optimization of perform design for precision close-die forging [J]. Struct Mul-tidisc Optim, 2011, 44(6): 1-12.
[8] LU Xian, BALENDRA R. Temperature-related errors on aerofoil section of turbine blade [J]. Journal of Materials Processing Technology, 2001, 115(2): 240-244.
[9] OU H, ARMSTRONG C G. Evaluating the effect of press and die elasticity in forging of aerofoil sections using finite element simulation [J]. Finite Elements in Analysis and Design, 2006, 42(10): 856-867.
[10] HU Z M, BROOKS J W, DEAN T A. Three-dimensional finite element modeling of forging of a titanium alloy aerofoil sectioned blade [J]. Manufacturing science and Engineering Transaction ASME, 1999, 121: 366-371.
(编辑 李艳红)
基金项目:中央高校基本科研业务费项目(A030070203801073)
收稿日期:2013-07-28;修订日期:2013-10-10
通信作者:高 涛,副教授,博士;电话:028-61830242;E-mail: gaotao@uestc.edu.cn