
Preparation of nanometer δ- and β-bismuth trioxide by
vacuum vapor-phase oxidation
HU Han-xiang(胡汉祥)1, 2, QIU Ke-qiang(丘克强)1, XU Guo-fu(徐国富)3
1. School of Chemistry and Chemical Engineering, Central South University, Changsha 410083, China;
2. Department of Chemistry and Chemical Engineering, Hunan Building Materials College,
Hengyang 421008, China;
3. School of Materials Science and Engineering, Central South University, Changsha 410083, China
Received 19 September 2005; accepted 14 October 2005
Key words: δ- bismuth trioxide; β-bismuth trioxide; vacuum vapor-phase oxidation; nanometer particles
1 Introduction
Bismuth trioxide is an important function material. It exits in four polymorphs[1-4], i.e. the monoclinic α-phase, the tetragonal β-phase, the body-centered cubic(bcc) γ-phase and the face-centered cubic(fcc) δ-phase. Below 730 ℃, bismuth trioxide exits as the monoclinic α-phase, and above this temperature, it exits as the fcc δ-phase[5]. Because phase transformation lags behind temperature changing, when cooled from temperatures above 730 ℃, fcc δ-phase of bismuth trioxide will undergo a transformation into one of the two metastable phases, the tetragonal β-phase or bcc γ-phase, before reverting to the monoclinic form[6].
δ-Bi2O3 has a fluorite-type structure with one quarter of the oxygen ions missing in an ordered oxygen lattice. The oxygen lattice sites are occupied randomly by oxide ions which can move from site to site through the bismuth sub-lattice. So δ-Bi2O3 has high ionic conductivity[7]. At the same time, its conductivity is about 2 orders of magnitude higher than zirconia-system electrolytes widely used at present. Therefore, it is an extremely promising solid electrolyte material and can be used as solid oxide fuel cells and oxygen sensors. However, a significant limitation is that it exists stably only between 730 ℃ and 825 ℃[8].
With the development of the studies for nanometer materials, scientists found that nanometer size of crystal can stabilize metastable materials such as ZrO2[9, 10]. This rule was applied in the preparation of pure δ-Bi2O3 and β-Bi2O3. BOHANNAN et al[11] prepared nanocrystalline films of δ-Bi2O3 by electrodepositing at 65 ℃ directly from alkaline solutions of tartrate- complexed Bi(Ⅲ).The author proposed that the high temperature form of the oxide was stable due to the nanocrystalline (70 nm) size of the particles in the film. Monnerau et al[12] prepared stable β-Bi2O3 at room temperature with the decomposition of different bismuth(Ⅲ) oxalate precursors by controlled transformation rate thermal analysis, which were obtained from the reaction of Bi(NO3)?5H2O and H2C2O4?2H2O.
Some processes of forementioned preparing methods are operated in the solution, in which some components may be adsorbed at the interface of nanometer bismuth trioxide. In general, it is more difficult that the components are completely eliminated by washing, and the remains may influence the conductivity of bismuth trioxide. Additionally, the chemical processing methods have disadvantages of environmental protection. In this paper, an alternative, environmentally benign preparing method was presented—vacuum vapor-phase oxidation that was used for preparing bismuth trioxide. And how to control the size and the polymorph of particles were also dis- cussed.
2 Experimental
2.1 Apparatus
Fig.1 shows the apparatus for preparation of bismuth trioxide which was made by ourselves. The middle section of a porcelain pipe (length 1 000 mm, inner diameter 36 mm) was heated to the desired temperature by an electric-tubular furnace to evaporate bismuth from a porcelain boat. The furnace temperature was controlled by a temperature controller connected with a thermocouple. Air or oxygen (industrial pure gas from Changsha supply-gas Ltd) was introduced through the pipe inlet (feed side) to the system using a 6 mm copper tube in length. The outlets of the porcelain pipe on the other side were connected with the collecting system and vacuum pump. Two model mechanical vacuum pumps were used under different experimental conditions, model ZXQ-2 and 2XZ-1, respectively. All tube connections were spread with vacuum flanges to allow gas-tight operation at subatmospheric pressure.
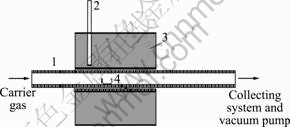
Fig.1 Schematic of apparatus for preparation of bismuth trioxide porcelain pipe: 1 Porcelain pipe; 2 Thermocouple; 3 Furnace; 4 Porcelain boat containing bismuth melt
2.2 Experiment
The apparatus was connected as described in Fig.1, firstly. After the set temperature was reached, the rubber plug was taken down, and the porcelain boat loaded with about 5 g bismuth granules which was crushed from bulk bismuth (industrial grade, from Zhuzhou Metallurgy Co) and 0.3 g adding agent (preventing bismuth melt from oxidation) was placed at the appropriate position in the porcelain pipe. Next, closed tightly the feed side of the pipe with the rubber plug, switched on the vacuum pump and adjusted carrier flow rates to the operating conditions with needle valves. Experiments were carried out from 1 005 ℃ to 1 140 ℃, at carrier flow rates of 40-200 L/h, the two different model mechanical vacuum pumps were used for changing drag force. The apparatus should be slowly cooled down to room temperature after all experiments were performed.
2.3 Characterization
Morphology of bismuth trioxide was analyzed by a Sirion200 (FEI Co) scanning electron microscope (5 kV accelerating voltage). The powder was stuck on the surface of an electric double-faced stickiness film and blown off the redundant powder on the surface. In addition, the samples were sputter coated with about 100 ? Pd to improve its conductivity.
The structure of the sample was characterized by Japan Rigaku D/Max-2500 X-ray diffractometer (Cu Kα radiation, 1.540 65 ?, 40 kV, 300 mA). X-ray diffrac- tion analysis was performed over an angle of 10°≤θ≤90° in steps of 0.02°. The average crystal size of the powder was calculated according to Scherrer’s equation D=0.89λ/βcosθ, where λ is the X-ray wavelength, β is the line with at half maximum height and θ is the diffraction angle. The (400) diffraction peak was selected for calculation of the average crystal size so that the size of bismuth trioxide with different polymorphs was comparable.
The granularity distribution of powders was determined by Laser Particle Sizers (Mastersizer 2000, Malvern Instrument Ltd). The powder was suspended in water before measurement. The detecting size range was 0.02 μm to 2 000 μm. The d(0.5) value was the mea- surement results analyzed with Mastersizer 2000 soft- ware(version 5.0). GSD was calculated with commercially available Matlab 6.0 software using the following equation[13]:
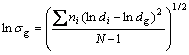
where ni is the number of particles with diameter of di, dg is the geometric mean diameter, and N is the total number of particles.
3 Results and discussion
The preparing processes of bismuth oxide by vacuum vapor-phase oxidation include evaporation of bismuth, formation of gaseous molecules of bismuth oxide by chemical reaction of bismuth and oxygen, nucleation, condensation and coagulation. The average size and granularity distribution of particles strongly depend on the process conditions mentioned above. Different size and different polymorphs of bismuth oxide were prepared by controlling the experimental conditions, shown in Table 1.
3.1 Polymorph of bismuth trioxide
Table 1 shows that when carrier gas is air, the products prepared at different evaporation tempera- tures(No.1, 2, 3 in Table 1) or different carrier flow rates (No.4, 5, 6, 7 in Table 1) exhibit the same XRD patterns (Fig.2), which correspond exactly with the PDF#27- 0050, indicating that bismuth trioxide powders are tetragonal β-Bi2O3. And when the vacuum pump with larger dragging rates is used (No.9 in Table 1), all diffraction peaks are assigned to the face-centered cubic phase bismuth trioxide (Fig.3) as reported in PDF#16-0654, indicating that the bismuth trioxide powders are fcc δ-Bi2O3.
In the processes, the bismuth vapors reacted with oxygen in the carrier gas to form the bismuth oxide. When the temperature of bismuth oxide decreased because of heat exchange, it began to solidify and subsequently, the transition of cubic δ-phase to monoclinic α-phase occurred. The decreasing temperature rates of bismuth oxide were very rapid because of large temperature gradient between evaporation region and collecting region and very small size of particles. Consequently, phase transition could not keep with the temperature change in the particles so that metastable δ-Bi2O3 and β-Bi2O3 were formed. According to the Laplace equation, the additive pressure of the liquid droplets with the nanometer grade could reach MPa grade. After such liquid droplets solidified, a higher inner pressure could exist in the particle, which was in favor of the stability of metastable phases[14]. And when the dragging rates of large vacuum pump
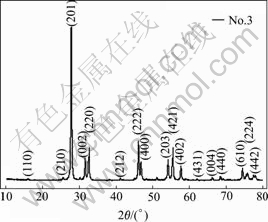
Fig.2 XRD pattern of β-Bi2O3
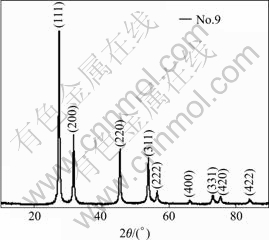
Fig.3 XRD pattern of δ-Bi2O3
were rising, the quenching rates were quickened correspondingly. Then δ-Bi2O3 was formed. And β-Bi2O3 was formed at lower quenching rates. Both polymorphs of bismuth trioxide were stable at room temperature because their sizes were nanometer magnitude order.
Table 1 Polymorphs and size of bismuth oxide prepared under different experimental conditions
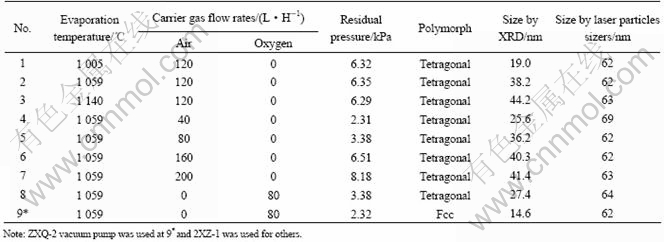
3.2 Size of bismuth trioxide
3.2.1 Influence of process conditions on size of bismuth trioxide
In our experimental temperature range (from 1 005 ℃ to 1 140 ℃), the saturated vapor pressure of bismuth oxide obtained from the gaseous reaction was very low. Such systems were known as constant rate aerosol reactors[15], in which the initial homogeneous nucleation finished in a limited duration. Subsequently, the nucleation and growth of the particles will simultaneously occur, which leads to the content decreasing of the gaseous bismuth oxide. The systems reached the balance if the rate of bismuth oxide formed from the gaseous reaction was equal to its rate lost from the nucleation and growth. According to the nucleation theory, the number of nuclei was constant at balance state[16]. Therefore, the size of final products was determined by the initial nucleating number, the growing rate and duration of the particles at balance state. The growing duration of the particles was inversely proportional to the quenching rate.
The rise of temperature enhances formation of the bismuth oxide, leads to high supersaturation degree and increases the number of the initial nucleation, which consequently decreases the particle size. However, after the constant state of the system is reached, the rise of the temperature promotes the growth of grains and leads to the greater size of particles. In our experiments, the size of the grain becomes greater as temperature rises (Fig.4).
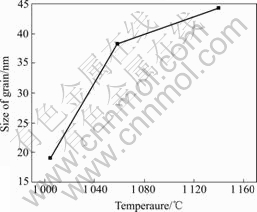
Fig.4 Effect of temperature on bismuth trioxide grain
The increase of the carrier gas flow rate increases the residual pressure of the system, which enhances the eddy flow of gas in the system because the gas stream is obstructed by the poreclain boat in the reaction pipe, increase residence time of the particle, prolongs growing duration of the particle and leads to larger particles. Therefore the size of grains increases with the carrier flow rate or the residual pressure of the system (Fig.5).
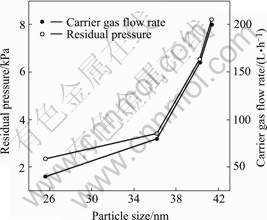
Fig.5 Effect of air flow rate on system residual pressure and bismuth trioxide size
The size of grains decreases with the increase of the drag force (No.8 and No.9 in Table 1) which can raise the carrier flow velocity and quenching rate, reduce the growing duration of grains.
3.2.2 Size distribution of particles
To estimate the size distribution of the particles, the products were measured by the Laser Particle Sizers listed in Table 1. The size of particles was estimated to be from 62 nm to 69 nm, geometric standard deviation(GSD) is from 1.42 to 1.64. These results show that the size of particles is small and size distribution is narrow.
3.3 Morphologies of bismuth trioxide
Fig.6 shows the SEM images of representative products. It can be seen that all the particles are near spherical shape, and do not change their shape with process conditions. But process conditions affect the size of grains substantially. The maximum size of grains is respectively 113.4 nm at 1 140 ℃ under 6.29 kPa of residual pressure (No.3 in Fig.6), 69.19 nm at 1 059 ℃ and 6.35 kPa of residual pressure (No.2 in Fig.6), 40.36 nm at 1 059 ℃ under 3.38 kPa of residual pressure (No.8 in Fig.6) and 28.82 nm at 1 059 ℃ under 2.32 kPa of residual pressure (No.9 in Fig.6). This changing tendency is consistent with the results obtained by XRD.
4 Conclusions
1) The apparatus of bismuth oxide prepared by vacuum vapor oxidation in this paper creates a quenching circumstance in which phase transition of bismuth oxide lagged behind the temperature changing so as to produce nonequilibrium δ-Bi2O3 and β-Bi2O3. The larger inner pressure exists in the nanoparticles stabilized δ-Bi2O3 and β-Bi2O3 at room temperature.
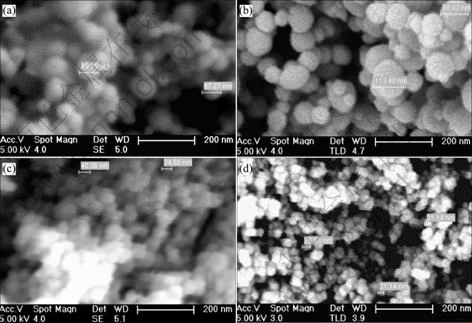
Fig.6 SEM images of No.2, 3, 8, 9 in Table 1: (a) No.2; (b) No.3; (c) No.8; (d) No.9
2) The average size of the minimal grain prepared in our experiments is 14.6 nm(measured by XRD). The d(0.5) value of the products determined by the Laser Particle Sizers is from 62 nm to 69 nm, and by GSD is from 1.42 to 1.64. These results show that the size of particles is small and the size distribution is narrow.
3) The size of the product is influenced by some factors such as temperature, flow rate of carrier gas as well as residence time. The size of grains prepared by vacuum vapor-phase oxidation increases with the increasing reaction temperature, growing time of grains, flow rate of carrier gas and residual pressure of system.
References
[1] SHUK P, Wiemhofer H D, Guth U, Gopel W, GREENBLATT M. Oxide ion conducting solid electrolytes based on Bi2O3 [J]. Solid State Ionics, 1996, 89: 179-196.
[2] Aurivillius B, Sillen L G. Polymorphy of bismuth trioxide[J]. Nature(London), 1945, 155: 305-306.
[3] RAO C N R, SUBBA RAO G V, Ramdas S. Phase transformations and electrical properties of bismuth sesquioxide[J]. Journal of Physical Chemistry, 1969, 73: 672-675.
[4] Levin E M, McDaniel C L. Heat of transformation in Bi oxide determined by differential thermal analysis(DTA)[J]. Journal of Research National Bureau of Standards Section A, 1965, 69(3): 237-243.
[5] Sammes N M, Tompsett G A, Nafe H, ALDINGER F. Bismuth based oxide electrolytes-structure and ionic conductivity[J]. Journal of the European Ceramic Society, 1999, 19: 1801-1826.
[6] Matsuzaki R, Masumizu H, Saeki Y. Phase transition of bismuth(Ⅲ) oxide prepared by the thermal decomposition of bismuth sulfate[J]. Bulletin of the Chemical Society of Japan, 1975, 48(11): 3397-3384.
[7] Battle P D, Catlow C R A, Drennan J, MURRY A D. The structural properties of the oxygen conducting δ phase of Bi2O3[J]. J Phys C: Solid State Phys, 1983, 16: L561-L566.
[8] Harwig H A, Gerards A.G. The polymorphism of bismuth sesquioxide[J]. Thermochimica Acta, 1979, 28: 121-131.
[9] Mitsuhashi T, Ichihara M, Tatsuke U. Characterization and stabilization of metastable tetragonal ZrO2[J]. J Am Ceram Soc, 1974, 57(2): 97-101.
[10] Switzer J A, Phillips R J. Electrochemical synthesis of zirconia[J]. Mat Res Soc Symp Proc, 1988, 121: 111-114.
[11] Bohannan E W, Jaynes C C, Shumsky M C, BARTON J K, SWITZER J A. Low-temperature electrodeposition of the high- temperature cubic polymorph of bismuth(III) oxide[J]. Solid State Ionics, 2000, 131: 97-107.
[12] Monnereau O, Tortet L, Llewellyn P, ROUQUEROL F, VACQUIER G. Synthesis of Bi2O3 by controlled transformation rate thermal analysis: a new route for this oxide?[J]. Solid State Ionics, 2003, 157: 163-169.
[13] Hinds W C. Aerosol Technology Properties, Behavior, and Measurement of Airborne Particles[M]. 2nd ed. New York: John Wiley & Sons, Inc, 1999. 93.
[14] Krauss W, Birringer R. Metastable phases synthesized by inert-gas condensation[J]. Nanostructured Materials, 1997, 9: 109-112.
[15] Rao N P, McMurry P H. Nucleation and growth of aerosol in chemically reacting systems─a theoretical study of the near-collision- controlled regime[J]. Aerosol Science and Technology, 1989, 11: 120-132.
[16] Friedlander S K. Dynamics of aerosol formation by chemical reaction[J]. Annals New York Academy of Sciences, 1983, 404: 354-364.
Foundation item: Project(03SSY4056) supported by the Bureau of Science and Technology of Hunan Province, China; Project(04C034) supported by the Bureau of Education of Hunan Province, China
Corresponding author: HU Han-xiang; Tel: +86-734-8432456,+86-731-6696582; E-mail: hanxianghu_62@hotmail.com
(Edited by LI Xiang-qun)