Trans. Nonferrous Met. Soc. China 24(2014) 3886-3893
Novel method of screw extrusion for fabricating Al/Mg (macro-) composites from aluminum alloy 6063 and magnesium granules
Kristian
SKORPEN1, Eirik MAULAND1, Oddvin REISO1,2, Hans
ROVEN1,3
1. Department of Materials Science and Engineering, Norwegian University of Science and Technology, Trondheim N-7491, Norway;
2. R&D Materials Technology, Hydro Aluminium AS, Sunndalsora 6600, Norway;
3. Center for Advanced Materials, Qatar University, Doha 2713, Qatar
Received 17 October 2013; accepted 17 November 2014
Abstract: A novel method of screw extrusion was used for producing a bimetal composite Al/Mg from granules containing aluminium alloy 6063 (AA6063) and commercial pure magnesium. Up to 12.5% (mass fraction) pure magnesium was added to the aluminium alloy. In general, the material consisted of a fine grained microstructure. In addition to the phases originating from the input materials, intermetallic phases were observed as islands consisting of the Al2Mg3 phase surrounded by γ-Mg17Al12, throughout the microstructure. The mechanical properties of the extruded material showed a gradual increase in strength with increasing the addition of Mg. The highest registered UTS, well above 350 MPa, was observed for the material containing 10% Mg. Examinations of the fracture surfaces indicated that increasing the magnesium content led to a higher degree of brittle fracture and a gradual change of the fracture micro-mechanisms. The optimization of the post-extrusion processing conditions is still ongoing.
Key words: Al/Mg composites; extrusion; microstructure; mechanical properties
1 Introduction
A bimetal is a material consisting of two dissimilar metals joined together through solid state bonding mechanisms. The motivation behind the development of bimetals is that, by combining two dissimilar metals it is possible to obtain an optimal combination of the desired properties, while at the same time to minimize the restrictive properties of the metals involved.
Magnesium has a hexagonal crystal structure and is normally more difficult to deform than FCC aluminium, and thus, has a limited formability. It is therefore expected that magnesium fragments in a matrix of an aluminium alloy might contribute to the enhanced strength. Furthermore, the use of magnesium in different engineering applications might be restricted by the high reactivity of the metal.
By combining the AA6063 with pure magnesium, it may be possible to obtain a light mass metallic composite that exhibits a high corrosion resistance and a relatively high specific strength combined with significant ductility.
Previous work on bimetals has focused on utilizing the process of accumulated roll bonding (ARB) to generate a continuous composite of fine fragments of reinforcing fibers of the harder material fully integrated in the softer matrix [1,2]. Various processes, which generate preforms of bimetals that can be suitable for further deformation, have been investigated at length, e.g. continuous casting [3], other casting and various deposition and surfacing methods [4].
A method of screw-extrusion was utilized in this work to produce a complete bimetallic composite. Previous work on ARB of Al and Mg sheets [5] gave promising result, and hence screw extrusion could be an alternative and a more direct method of forming a similar material. Also, previous work on the extrusion of bimetallic preforms acted as a motivation [6,7].
2 Experimental
2.1 Materials
The materials used in this work were prepared from a cast block of commercial pure magnesium (CP-Mg) and a cold drawn wire of aluminium alloy 6063 (AA6063). The cold drawn wire (d 3 mm) was cut into approximately 10 mm in length by feeding it onto a rotating knife. The CP-Mg was cut by a water jet saw and with mechanical scissors to assimilate the size of the aluminium granules, ending up with square prisms of 3 mm×3 mm×(~10 mm). An image of these starting materials is given in Fig. 1.
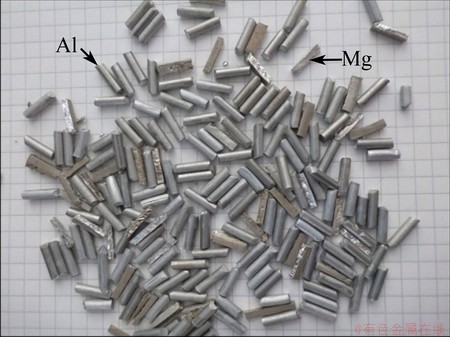
Fig. 1 Granules of CP-Mg (rectangular, matte-brown surface) and AA6063 (round, metallic-grey surface) used as starting materials
The chemical compositions given on the certificate from the providers of these materials are given in Table 1.
Table 1 Nominal compositions of CP-Mg and AA6063 starting materials

The granules were rinsed in acetone and thermally degreased prior to the extrusion. The thermal degreasing was conducted in a resistance furnace at 360 °C for 1 h. This degreasing method was chosen based on the results of an investigation of degreasing methods for aluminium intended for solid state recycling [8].
2.2 Methods
The bimetals were produced by the method of screw extrusion. A schematic presentation of this process is given in Fig. 2 [9]. The system utilizes an Archimedes screw to feed and consolidate the material, and then force it through an extrusion die, hence producing a bimetallic composite in one single processing step.
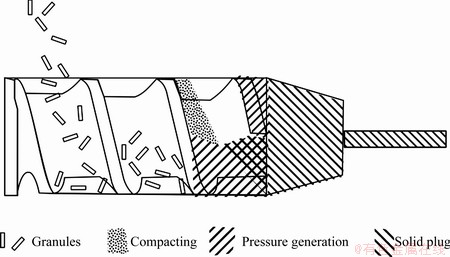
Fig. 2 Schematic sketch of production process [9]
The process setup is controlled by a Labview software, and has the possibility of manually adjusting several parameters in real time. The software also gives live feedback on critical parameters, such as rotational torque and various temperatures. The extrusion die is preheated using an induction coil in front of the die, and the effect of the coil can be adjusted during the process. Further, the extrusion chamber can also be cooled by passing air through embedding cooling ribs in this region. The temperature measured at the extrusion die is considered the most critical process parameter, as this is the highest temperature that is measured while extruding with this setup.
The granules enter the screw at ambient temperature from a feed hopper. Round rod-like profiles with a diameter of 20 mm are extruded in the experiments.
Furthermore, Figure 3 shows the binary phase diagram of the Al-Mg system [10]. Here, the relatively low melting point of the intermetallic components should be kept in mind while extruding a mixture of Al and Mg constituents.
By mixing the constituents at elevated temperatures, intermetallic phases can be formed through diffusion. An overview of the relevant phases is included in Table 2 [10].
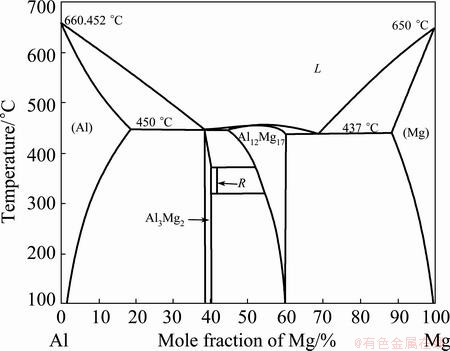
Fig. 3 Al-Mg binary phase diagram including critical temperatures [10]
Table 2 Crystal structure data of equilibrium solid phases in Al-Mg system [10]
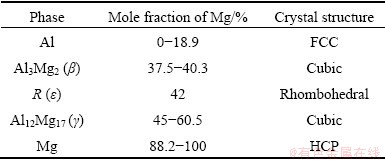
The experiments were conducted at temperatures in the extrusion chamber high enough for generating satisfactory friction between the parts in the extruder set-up and the input materials, but at the same time low enough to avoid local melting in the material. The temperatures utilized were selected based on prior initial experiments. The temperature at the die was maintained at (410±10) °C during the extrusion trials by adjusting the heating from induction, the screw rotation speed (i.e. indirect heating from friction and plastic deformation) and the forced cooling (engaged by passing air through cooling ribs around the extrusion chamber).
The extruded samples with increasing amount of Mg granules were produced under these conditions.
Different parallels are given in Table 3. The material was weighed and successively well mixed in a container prior to putting it onto the feed hopper of the extrusion setup.
Table 3 Experimental trial compositions
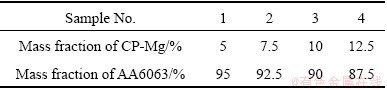
3 Results and discussion
3.1 Microstructure
The microstructures of the materials were studied on different size scales. The samples were prepared for optical microscopy by anodizing to obtain an overview of the grain structure. This method gave only an indication of the structure in the material as anodizing did not give a good representation of the structure of the Mg-rich regions. Images obtained from optical microscopy of the extruded profiles in the longitudinal- and transverse-cross sections are shown in Figs. 4 and 5, respectively.
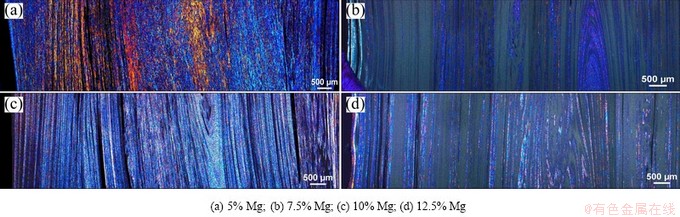
Fig. 4 Optical micrographs of longitudinal-cross sections of anodized extruded samples investigated by polarized light
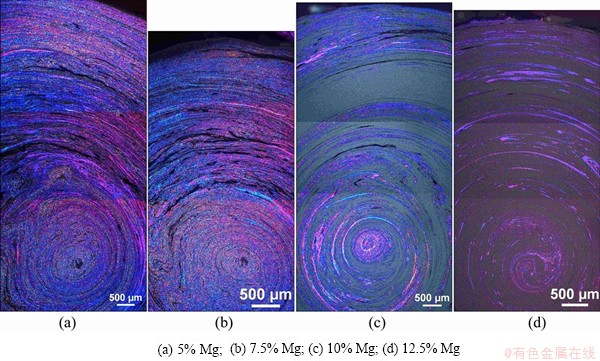
Fig. 5 Optical micrographs of transverse-cross sections of anodized samples investigated by polarized light
A layered structure is clearly visible in these sections. It can be observed that by increasing addition of Mg, less Al grains are visible, as anodizing affects the intermetallic and Mg-rich phases differently. The most Mg-rich phase is believed to be heavily corroded and can be seen as black stripes in the materials. This was further confirmed by investigations in the scanning electron microscope (SEM), as illustrated by the low- magnification SEM micrographs in Fig. 6, where no similar porosity can be observed. The intermetallics, or heavily alloyed phases, are believed to be the dark grey-blue regions in images obtained by optical microscopy, as can be observed in regions between black stripes representing the heavily corroded Mg-rich region and the anodized grains representing the Al-rich phase (Fig. 7).
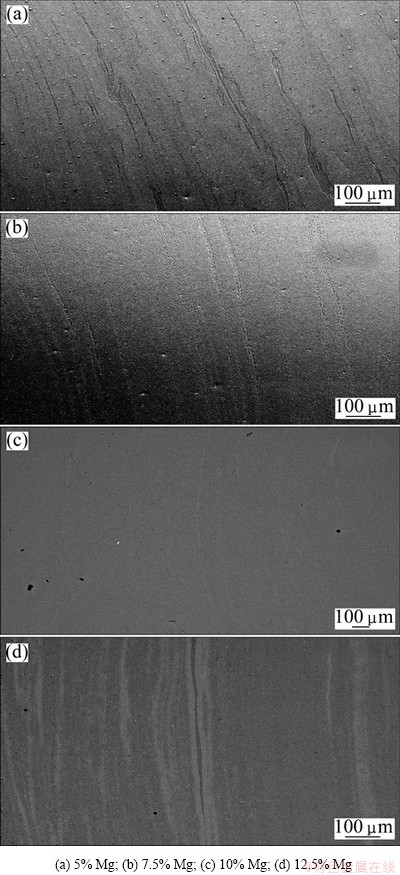
Fig. 6 SEM images of cross sections of extruded profiles
Moreover, the optical microscopy images confirm a well-mixed structure of the constituent materials and the obtained phases, indicating that the present method of screw extrusion is promising for the production of bimetallic materials. However, the properties might be anisotropic, as the regions of different phases are ordered in twirls or helixes along the extrusion direction. This kind of structure is also reported in earlier reports on screw extrusion [11].
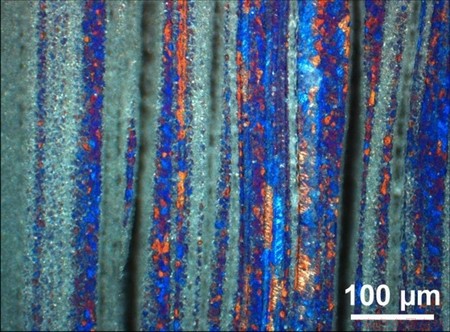
Fig. 7 Optical micrograph of longitudinal section of 10% Mg extruded sample
Because of this mixed structure, further deformation steps may be beneficial as to obtain a more random orientation distribution of microstructure constituents and phases. It can therefore be believed that the screw extrusion can be a suitable method for generating bimetallic preforms. Thus, in the future, less deformation may be introduced to the material at this production step (e.g. by applying a smaller extrusion reduction ratio), as the screw extrusion can be used as the initial stage of forming a bimetallic material. This may be beneficial in terms of reducing the heat generated from friction, thus giving an easier control of the temperatures present during the extrusion.
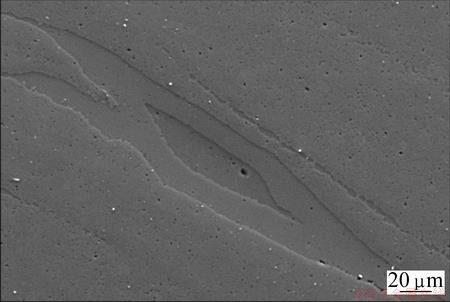
Fig. 8 SEM secondary image of sample containing 7.5% Mg showing intermetallic phases and characteristic of “island structure”, i.e., rich in Mg in center region
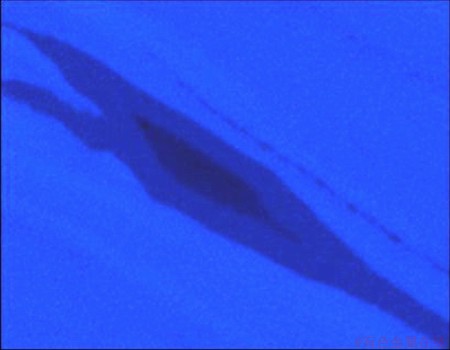
Fig. 9 EDS-mapping of Al in area displayed in Fig. 8
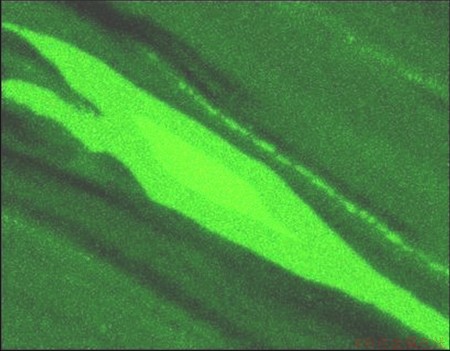
Fig. 10 EDS-mapping of Mg in area displayed in Fig. 8
In the regions with high Al content, equiaxed grains in the range of a couple of microns in size can be observed.
The material was further investigated with SEM, and EDS analysis was conducted over the selected representative regions. Figure 8 shows a secondary image of a region of such a structure. The Al content map is shown in Fig. 9, where a brighter intensity of blue indicates a higher content of Al. Similarly, Fig. 10 shows the corresponding Mg content map, where a brighter intensity of green indicates a higher content of Mg. Such islands, which are actually seen throughout the material, are believed to originate from the Mg constituents.
Another “island structure region” is illustrated by the SEM image in Fig. 11. Here, the superimposed line-scan confirms the rise of the Mg content in steps towards the center of the Mg-island. However, point analysis gives a more quantitative indication of the composition in these regions and the line-scan confirms that there is a consistency in content within each region.
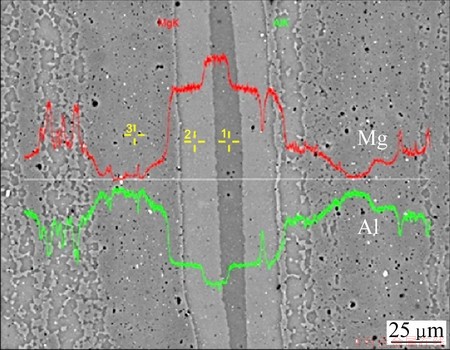
Fig. 11 Line-scan (red for Mg and green for Al) and point analysis (yellow) by EDS in SEM showing typical Mg-rich island
The results of the point analysis illustrated in Fig. 11 are given in Table 4. Here, the highest content of Mg is found in point 1, which is located in the middle of this island.
Table 4 Results of point scan indicated in Fig. 11
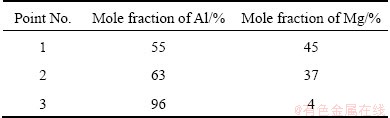
Compared the result in Table 4 with Table 2, it can be concluded that the composition at point 1 is within the range of the Al12Mg17 (γ) phase, and the composition at point 2 is consistent with the Al3Mg2 (β) phase, and the material at point 3 is the original AA6063 alloy with some additional Mg in solid solution.
The fact that no high-content Mg region (or regions closer in chemistry to the CP-Mg constituent) is observed, indicates a fast diffusion of the constituents during the production of these materials. This is in consistency with the relative high temperature during the extrusion trials. For an ARB equivalent (ARB of Al and Mg at 400 °C), a coarse Mg/Al intermetallic was observed in the material after the final rolling step, in addition to the constituent phases [5]. In the latter case, the starting materials were below 1 mm in thickness, and were rolled to 50% thickness reduction followed by air cooling. The applied temperature and cooling rate are not very dissimilar to the conditions prevailing during the present extrusion trials, indicating that the deformation conditions, or the thermal influence, on the material prior to entering the extrusion die contributes significantly to the formation of the mentioned intermetallic phases.
The recorded temperature in the extrusion die was just below the melting point of the intermetallic phases, and the extrusion was performed with characteristic parameters (high screw-rotation speed and low extrusion speed) to gain significant deformation of the material through the experiment. Hence, the initial size of the feedstock granule materials does not represent the diffusion length for the complete generation of the intermetallic phases observed. However, it may be that the total width of the intermetallic islands (Figs. 8-11) represents original Mg-granules that have been deformed during the extrusion at high temperature (e.g. close to the local melting point). Thus, a well mixed material was obtained, and no regions of the starting material granules were observed.
Further, in the regions outside these islands an inhomogeneous phase distribution can be observed. Here, dendrite-like structures are visible. These regions may indicate that during the extrusion, in a region of high deformation where no temperature measurements are possible, the temperature due to deformation heat is high enough to produce local melting. The line scan in such regions has peaks that are in the range of the β-phase, and the low Mg composition end of the line could indicate an aluminium phase, which is a mixture consistent with the phase diagram.
In future experiments, conditions may be altered to gain a more bi-metallic mixture of bonded original Al and Mg “granule islands”. This might be achieved by increasing the extrusion speed so that the material is moved through the screw extruder without so much deformation at shorter times and the highest temperatures. This is also in accordance with the above uttered statement that the screw extrusion process may be used as an initial step to generate a bi-metallic preform that can be subjected to further deformation steps.
3.2 Mechanical properties
The mechanical properties were investigated by performing tensile testing and hardness measurements. A total of 5 parallel samples of the extruded rods containing 5% Mg, 7% Mg and 10% Mg and 3 parallel samples of the extruded rods containing 12.5% Mg were subjected to tensile testing. The characteristic values extracted from these tests are given in Figs. 12-14.
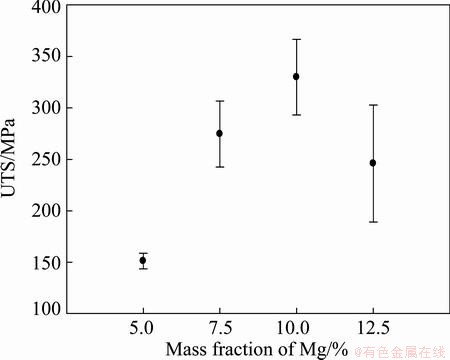
Fig. 12 Ultimate tensile strength (UTS) for as-extruded rods
An almost linear increase in strength and the corresponding decrease in ductility can be observed for the three samples containing the lowest content of Mg (i.e. up to 10% Mg). This trend cannot be extrapolated to materials containing 12.5% Mg and the latter has also a higher variation in strength properties. By increasing the content of Mg, it is hard to maintain constant extrusion speeds as the material accumulates in the extrusion chamber and feeding zone after some time. This is particularly observed when extruding the 12.5% Mg bimetal, and the samples may be deemed incomparable to the three other bimetals. Nevertheless, by tuning the process, it is believed that bimetals with that high Mg content (and even higher contents) can be produced by screw extrusion. Then, a continued increase in strength may be observed, e.g. resulting in extraordinary high specific strength levels.
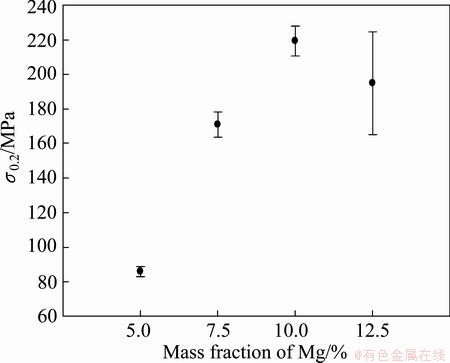
Fig. 13 Offset yield strength (σ0.2) for as-extruded rods
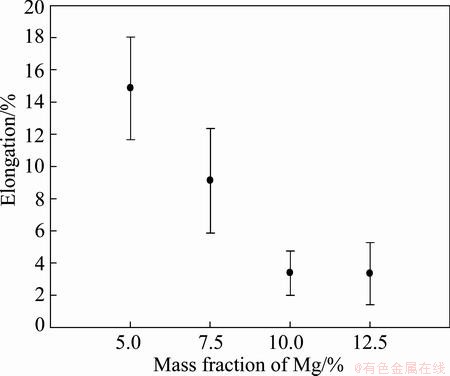
Fig. 14 Elongation at fracture for as-extruded rods
By comparison, the extrusion of profile with 10 mm in diameter at a measured die temperature of 560 °C with mono-granules of AA6060 that were thermally degreased in the same way as in the current work, an UTS of (175±3.1) MPa , an offset yield strength of (79±2.2) MPa and an elongation of (12.9±0.64)% was observed [12].
The results of randomly set hardness indentations on the cross sections of different extruded profiles are shown in Fig. 15. The same trend as for the tensile strength is confirmed by the average hardness.
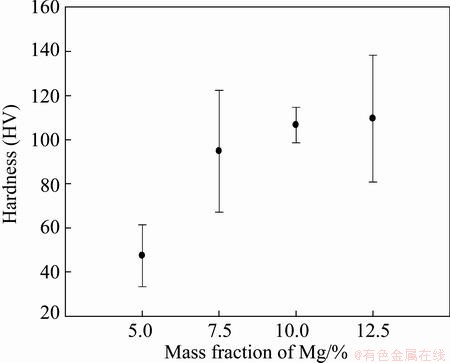
Fig. 15 Results of hardness measurements of extruded materials
Compared to the screw-extruded mono-material AA6060 with an average hardness of about HV 47 [12], a substantial average hardness increase across profiles can be observed for the sample with addition of 7.5% Mg and more. This is most probably due to the addition of Mg, but it should here be noticed that the observed hardness of HV 47 is for the material extruded at 560 °C, i.e., in contrast to ~410 °C for the current material.
3.3 Fractograph
Fractographs of selected tensile samples are included to support the statement that the properties may be anisotropic and with poor internal bonding. However, no mechanical tests have been conducted to support this up to now, but the fracture surfaces indicate supporting evidence. Two fractographs with the most extreme features have been included. For example, Fig. 16 shows a delaminated ridge going along what appears as a helical plane on the fracture surface of a sample containing 5% Mg. This phenomenon was observed in several investigated samples, independent of the amount of Mg added. Further, Fig. 17 shows a fracture surface with less macroscopic topography, and the circular twirl is here much less prominent as is also the tendency to form delaminations.
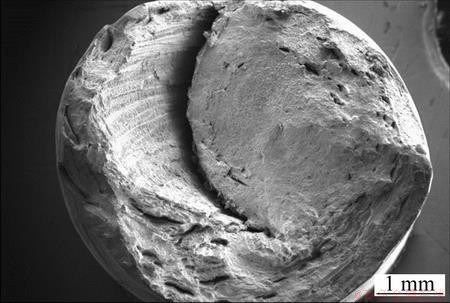
Fig. 16 SEM fractograph of sample containing 5% Mg subjected to tensile testing
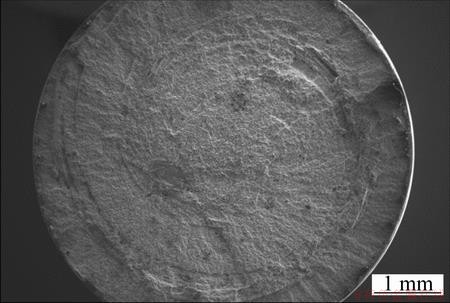
Fig. 17 SEM fractograph of sample containing 10% Mg subjected to tensile testing
Moreover, the fracture surfaces contain regions with characteristics of ductile as well as brittle failure. From Fig. 16 it can be observed that the delamination crack has propagated along an interphase on the left hand side of the image, and the interphase regions that lay in twirls on the cross sections can be observed in both Figs. 16 and 17. Thus, a more homogenous distribution of the interphases and improved interphase bonding may be beneficial to the material properties.
4 Conclusions
1) The production of bimetals through screw extrusion is possible.
2) A well-mixed Al/Mg material was produced. Running extrusion at high screw rotation speed and relative high temperatures yielded a material with a quite homogeneous structure, and regions of dendrite-like structures may indicate local melting.
3) The present results show that there are several convincing arguments for conducting further deformation steps, using screw extrusion as an initial compaction step.
4) Increasing the content of Mg to an Al alloy gives promising results in regard to mechanical properties, and motivates further investigations with this novel method.
References
[1] DEHSORKHI R N, QODS F, TAJALLY M. Investigation on microstructure and mechanical properties of Al-Zn composite during accumulative roll bonding (ARB) process [J]. Materials Science and Engineering A, 2011, 530: 63-72.
[2] EIZADJOU M, KAZEMI TALACHI A, DANESH MANESH H, SHAKUR SHAHABI H, JOANGHORBAN K. Investigation of structure and mechanical properties of multi-layered Al/Cu composite produced by accumulative roll bonding (ARB) process [J]. Composites Science and Technology, 2008, 68: 2003-2009.
[3] SUN J, SONG X, WANG T, YU Y, SUN M, CAO Z, LI T. The microstructure and property of Al-Si alloy and Al-Mn alloy bimetal prepared by continuous casting [J]. Materials Letters, 2012, 67: 21-23.
[4] BYKOV A. Bimetal production and applications [J]. Steel in Translation, 2011, 41: 778-786.
[5] WU K, CHANG H, MAAWAD E, GAN W M, BROKMEIER H G, ZHENG M Y. Microstructure and mechanical properties of the Mg/Al laminated composite fabricated by accumulative roll bonding (ARB) [J]. Materials Science and Engineering A, 2010, 527: 3073-3078.
[6] PARAMSOTHY M, GUPTA M, SRIKANTH N. Processing, microstructure, and properties of a Mg/Al bimetal macrocomposite [J]. Journal of Composite Materials, 2008, 42: 2567-2584.
[7] PARAMSOTHY M, HASSAN S F, SRIKANTH N, GUPTA M. Enhancing the performance of magnesium alloy AZ31 by integration with millimeter length scale aluminium-based cores [J]. Journal of Composite Materials, 2010, 44: 1099-1117.
[8] CUI J. Solid state recycling of aluminium scrap and dross characterization [D]. Trondheim: Norwegian University of Science and Technology, 2011.
[9] WERENSKIOLD J C, AURAN L, ROVEN H J, RYUM N REISO O. Screw extruder for continuous extrusion of materials with high viscosity: US 20100285165 A1 [P]. 2010.
[10] MURRAY J. The Al-Mg (aluminum-magnesium) system [J]. Bulletin of Alloy Phase Diagrams, 1982, 3: 60-74.
[11]
F, WELO T. Using contrast material techniques to determine metal flow in screw extrusion of aluminium [J]. Journal of Materials Processing Technology, 2013, 213: 1007-1018.
[12] BILSBAK A. Mikrostruktur og mekaniske egenskaper for skrueekstrudert aluminium: Karakterisering av skrueekstrudert aluminium etter ulike rensmetoder av
[D]. Trondheim: Norwegian University of Science and Technology, 2012.
一种新螺杆挤压法从6063铝合金和Mg混合颗粒制备Al/Mg复合材料
Kristian
SKORPEN1, Eirik MAULAND1, Oddvin REISO1,2, Hans
ROVEN1,3
1. Department of Materials Science and Engineering, Norwegian University of Science and Technology, Trondheim N-7491, Norway;
2. R&D Materials Technology, Hydro Aluminium AS, Sunndalsora 6600, Norway;
3. Center for Advanced Materials, Qatar University, Doha 2713, Qatar
摘 要:采用一种新的螺杆挤压法以AA6063合金和工业纯Mg混合颗粒为原料制备Al/Mg双金属复合材料。加入铝合金中的镁合量最高可达到12.5%(质量分数)。所制备复合材料由细小晶粒组织组成。其显微组织中除有原料中的物相外,还观察到由γ-Mg17Al12包围的岛状Al2Mg3金属间合物。复合材料的强度随Mg含量的增加逐渐增高。含Mg为10%复合材料的极限抗拉强度最高,超过350 MPa。断裂表面分析结果表明,增加Mg含量导致材料发生较严重的脆性断裂及断裂机制的较小变化。因此,应对挤压工艺条件进行进一步优化。
关键词:Al/Mg复合材料;挤压;显微组织;力学性能
(Edited by Wei-ping CHEN)
Corresponding author: Kristian
SKORPEN; Tel: +47-73-594045; +47-99-464669; E-mail: kristian.g.skorpen@ntnu.no
DOI: 10.1016/S1003-6326(14)63547-0