DOI: 10.11817/j.issn.1672-7207.2019.02.002
湿法炼锌厂针铁矿渣的表征
李玉虎1,高禄鹏2,刘志宏2
(1. 江西理工大学 冶金与化学工程学院,江西 赣州,341000;
2. 中南大学 冶金与环境学院,湖南 长沙,410083)
摘要:针对湿法炼锌厂针铁矿渣中铁和锌质量分数波动大、过滤性不佳的问题,通过采集不同锌厂的针铁矿渣样,对其展开系统的表征分析,研究铁、锌在针铁矿渣样中的赋存特征以及形成原因。研究结果表明:尽管不同厂家的针铁矿渣成分相差较大,但颗粒粒径及铁、锌分布特征相似;铁渣样品中粒径小于38 μm的颗粒占多数,且这部分颗粒渣中铁质量分数较高,锌质量分数较低,而对于粒径大于80 μm的颗粒,锌质量分数约为30%,铁质量分数仅为15%左右,这说明除酸洗外还可采用分级的方法降低针铁矿渣中锌质量分数;在针铁矿样品中,大部分铁存在明显的富集相,而锌除了存在富集相外,还有一部分呈分散分布;因此,为了获得理想的针铁矿渣、除调控沉铁工艺条件外,还需严格控制中和剂品质。
关键词:针铁矿渣;锌;除铁;湿法炼锌;赋存特征
中图分类号:TF813;TF803.25 文献标志码:A 文章编号:1672-7207(2019)02-0257-07
Characterization analysis of goethite residue from zinc hydrometallurgy plants
LI Yuhu1, GAO Lupeng2, LIU Zhihong2
(1. School of Metallurgy and Chemical Engineering,
Jiangxi University of Science and Technology, Ganzhou 341000, China;
2. School of Metallurgy and Environment, Central South University, Changsha 410083, China)
Abstract: Considering the great variation of iron and zinc mass fraction and poor filtration performance in the goethite residue from zinc hydrometallurgy plants, the goethite residue samples from different zinc plants were collected and characterized systematically. The occurrence characteristics of zinc and iron in goethite residue and its formation causes were revealed. The results show that although there is great difference in the mass fractions of zinc and iron in these samples, the characterization of particle size and distribution of Fe and Zn are similar. Particles smaller than 38 μm in diameter in the sample account for vast majority, and contain high mass fraction of iron and low mass fraction of zinc. While particles of greater than 80 μm in diameter contain up to 30% zinc, but only 15% iron. In other words, besides acid washing process, size classification can also reduce the mass fraction of zinc in the goethite residue. Most of the iron in the goethite samples exists as enrichment phase. For zinc, in addition to zinc rich phase, some zinc is widely scattered in the sample. For obtaining ideal iron removed goethite residue, the quality of neutralizer also need to be strictly controlled in addition to improvement of iron precipitation parameters.
Key words: goethite residue; zinc; iron removal; zinc hydrometallurgy; occurrence characteristics
针铁矿法除铁工艺由比利时老山公司于20世纪60年代末开发[1-2],由于该工艺具有物料适应性强、工艺简单,且所得铁渣中铁质量分数较高、过滤性能较好[3],同时除铁过程还可脱除砷、锑、氟和氯等有害杂质[4],因此,被广泛应用于锌、铜、镍、锰等有价金属的湿法冶金工艺中[5-6]。针铁矿法被认为是未来湿法冶金除铁技术的主流工艺和发展方向[7]。随着热酸浸出和硫化锌精矿氧压直接浸出技术的广泛应用,针铁矿法作为一种高效且低成本的除铁方法,越来越受到国内外研究者的重视[8-12]。按照操作方法,可将针铁矿法分为还原-氧化法和稀释法[13]。还原-氧化法首先将Fe3+还原为Fe2+,然后用空气(或氧气)在适当的pH条件下,将Fe2+缓慢氧化为Fe3+,使得Fe3+以针铁矿形式沉淀。稀释法则是将高质量浓度Fe3+溶液均匀缓慢地加入至不含铁或铁质量分数较低的溶液中,通过控制加料速度,保持沉铁溶液中Fe3+质量浓度<1 g/L,使得Fe3+在适当pH下以针铁矿形式沉淀。稀释法省去了Fe3+的还原工序,工艺流程简单,但稀散金属进入铁渣,不利于稀散金属的综合回收[14]。在稀释法的基础上,人们先后开发了仲针铁矿(paragoethite)法[15-17]和Zincor法除铁工艺[18-19]。然而,尽管针对针铁矿工艺的应用和优化研究取得了较大进展,但针铁矿除铁渣中铁和锌质量分数波动较大,锌质量分数为8%~17%[20-21],普遍高于黄钾铁矾法和赤铁矿法中的锌质量分数,增加了不必要的锌损失,使得针铁矿法的经济效益受到了影响。此外,不同针铁矿渣过滤性能也存在较大差异,为此,不得不借助絮凝剂提升过滤性能,这使得湿法炼锌系统面临有机杂质引入的问题。对于针铁矿铁渣铁、锌质量分数和过滤性差异的研究,暂未见相关报道。为此,本文通过采集具有代表性锌厂的针铁矿渣样,开展系统表征分析,研究针铁矿渣中锌和铁的分布、物相组成和微观形貌特征,揭示针铁矿铁渣锌、铁的赋存规律和物相形成机制,以便为后续优化针铁矿沉铁工艺提供参考。
1 试验
1.1 原料
试验所用针铁矿渣样采集自国内2家大型炼锌企业生产现场,共3个批次样品,其中1号和2号样品为同一厂家样品,1号为原渣,2号为酸洗后渣样,颜色均呈褐红色;3号为另一厂家针铁矿原渣,颜色呈暗红色。1号、2号和3号针铁矿渣样的铁质量分数分别为45.09%,44.31%和33.43%;锌质量分数分别为11.20%,8.50%和9.30%。
1.2 试验设备
8411型电动振筛机;孔径为38~250 μm的分样筛;鼓风干燥箱(SFG-01B);METTLER TOLEDO ME204E电子分析天平;JP-060超声波清洗机;DB-XAB电热恒温数显加热板。
1.3 试验方法
1) 湿筛分析。分别称取2 kg针铁矿渣(1号、2号和3号)于5 L烧杯中,加入3.5 L水后超声搅拌分散20 min,然后,将分散好的料浆缓慢倒入筛分机进样口,使得料浆依次通过孔径为250,150,109,80,66,58,48和38 μm的分样筛。进料结束后,继续加入1.5 L水冲洗筛网,然后停止筛分,收集不同筛网上的渣样。将收集的渣样在鼓风干燥箱中于105 ℃干燥24 h。干燥完成后,收集渣样,封装编号并送样检测。
2) 表征分析。取200 g 1号、2号、3号针铁矿样品于表面皿中,在鼓风干燥箱中于105 ℃干燥24 h,然后,磨细封装,送成分和物相表征。
采用扫描电子显微镜(SEM,型号为JSM-6360LV)观测针铁矿渣样微观形貌和粒径分布特征;采用X线衍射仪(XRD,型号为Rigaku-TTRⅢ,Cu/Kα,波长λ=0.154 06 nm)表征渣样物相组成;采用电感耦合等离子发射光谱仪(ICP-AES,IRIS Intrepid Ⅱ XSP型)测定针铁矿渣样中锌、铁等元素的质量分数;采用X线荧光光谱仪(S4 PIONEER型)分析样品中主要元素的分布特征;采用JEOL JXA-8230型电子探针观测固体产物微区结构和成分特征。
2 结果与讨论
2.1 针铁矿渣粒径和锌铁分布特征
1号、2号和3号针铁矿渣样品经湿筛分级后的粒径及锌、铁质量分数分布特征如图1所示。
由图1可知:试验所采集的3个样品的颗粒粒径均较小,大多数颗粒粒径小于38 μm,其中1号渣和2号渣中粒径小于38 μm的颗粒占比高达90%以上,3号渣中颗粒占比为76%左右。这些粒径小于38 μm的颗粒中铁质量分数较高,而锌质量分数较低,1号和3号样中粒径小于38 μm的颗粒中铁质量分数分别为48.3%和35.2%,远高于粒径大于38 μm颗粒中的铁质量分数;而锌质量分数分别为9.44%和5.30%;3号样中锌质量分数最低。其次,对于1号和3号矿渣样品,随着颗粒粒径增大,矿渣铁质量分数逐步降低,而锌质量分数呈增加趋势。2号渣样中粒径小于38 μm的颗粒由酸洗前的90.2%(见图1(a))增加到97.2%,且酸洗使得2号铁渣中粒径小于38 μm的颗粒渣锌质量分数由9.44%降至8.21%。此外,由图1(b)还可以发现:经过酸洗后,2号样中粒径大于80 μm的颗粒显著减少,同时,这部分颗粒的渣中锌质量分数也迅速降低。可见,对铁渣进行酸洗处理可有效地降低针铁矿渣的锌质量分数,且酸洗对大颗粒的作用最为明显。

图1 针铁矿渣样的粒径及锌、铁质量分数分布
Fig. 1 Distribution of particle sizes and mass fractions of zinc and iron in goethite residue samples
2.2 针铁矿渣成分和物相表征
表1所示为针铁矿渣的X线衍射(XRF)分析结果,其中1"样品、2"样品和3"样品分别为1号、2号和3号针铁矿渣样经湿筛处理后,粒径小于38 μm的样品。
从表1可知:1号和2号渣样主要含有Fe,Zn和Si等元素,还含有少量的Pb,Cu,Al,Ca和Mn,其中Fe质量分数最高,为50.00%以上,1号渣样的Zn质量分数为15.33%;经过酸洗得到的2号渣样,其锌质量分数可降至12.86%;3号渣样中Fe和Zn质量分数分别为43.31%和12.56%,与1号和2号渣样相比偏低,这可能是由于中和剂的品质较差,可溶锌质量分数较低,使得渣中铁质量分数较低,渣中锌质量分数较高。值得注意的是,3号渣中Si,Pb和Cu等质量分数较高,且K质量分数明显较高,这意味着在3号渣中,部分铁可能以铁矾形式存在,这也是造成3号渣中铁质量分数不高的主要原因之一。此外,由1号和3号样品经过分级得到1"号和3"号样品,其锌质量分数分别为12.69%和9.53%,与分级前相比明显降低,这说明除了采用酸洗处理外,通过分级措施脱除渣样中的粗颗粒,也可降低针铁矿渣中锌质量分数。对比2号和2"号样品可以发现:这2个样品各元素质量分数差异较小,这表明酸洗处理和分级处理的效果是一致的。这是因为渣样中锌质量分数较高的颗粒,其粒径也较大,而酸洗和分级主要对这些颗粒起作用。虽然采用酸洗和分级的效果一致,但考虑到酸洗易导致炼锌系统水膨胀,同时可能会导致部分吸附于铁渣上的氟、氯杂质解吸进入系统,因而,采用分级的方法处理针铁矿渣更可行。
表1 针铁矿渣XRF分析结果(质量分数)
Table 1 Results of XRF analysis of goethite residue samples %

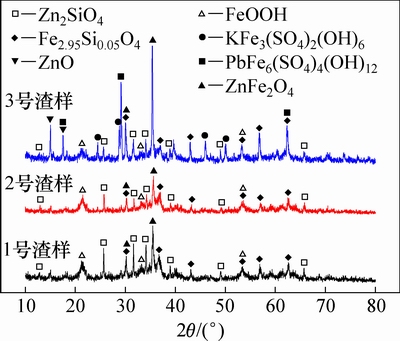
图2 针铁矿渣的XRD图谱
Fig. 2 XRD patterns of goethite residue samples
图2所示分别为1号、2号和3号针铁矿渣样的XRD分析结果。由图2可知:3种渣的物相均较复杂,由多种物相组成;1号渣样中除了针铁矿外,还含有一定质量的硅酸锌、硅酸铁、铁酸锌,这些主要由中和剂焙砂带入,其在沉铁过程中基本未参与反应;1号和2号渣物相一致,表明酸洗过程未对铁渣物相产生影响;3号渣样中除上述物相外,还含有一定量的未反应完全的氧化锌,以及一定量的钾铁矾和铅铁矾。这些铁矾在沉铁过程中形成,这是导数3号中渣铁质量分数较低、锌质量分数较高的主要原因。由此可见:对于1号和2号铁渣生成条件的优化,应控制中和剂的成分,尽量提高可溶锌的质量分数,降低硅酸锌、铁酸锌等难溶相。而对于3号渣,除了控制中和剂用量和品位外,还应降低氧化速度、并尽量降低溶液碱金属离子浓度,以避免铁以铁矾形式沉淀。
2.3 微观形貌表征
图3所示为针铁矿渣样的SEM照片。由图3可知:3种针铁矿渣样微观形貌相似,均呈不规则球形或团聚体,但颗粒表面形态相差较大。1号渣颗粒表面存在一些针状物质,2号颗粒表面更为光洁,这表明酸洗后,针状物质消失,由此推断这些针状物质可能为碱式硫酸锌;3号渣颗粒表面为片状结构,这些片状物质可能仍为碱式硫酸锌,但由于其质量分数较高,导致其形貌与1号渣样形貌有一定差异。此外,3个渣样均存在粒径分布范围较宽的特征,但相对来说,3号渣粒径分布范围最宽,除了粒径为30~50 μm的大颗粒外,还出现了大量亚微米级的小颗粒,而1号和2号针铁矿渣样粒径分布相对较窄,且大颗粒数量相对较少。同时,对比1号和2号渣样可以发现:酸洗处理后,2号渣样中粗颗粒数量有所减小,但小颗粒数量未有明显变化,这是因为酸洗处理除溶解碱式硫酸锌外,还使得部分铁酸锌和硅酸锌大颗粒溶解,这再次证实了酸洗主要对富锌大颗粒起作用。
2.4 针铁矿渣样电子显微探针分析
图4所示为1号针铁矿渣的电子显微探针分析(EPMA)面扫描结果。由图4可以看出:Fe主要存在于灰色衬度的颗粒,而Zn则富集于灰白色的颗粒中,且大多数铁存在于富铁区域,少量铁与锌呈共存分布特征;此外,Zn存在少量的单独富锌颗粒,但其几乎弥散于所有区域。结合图2的物相分析结果,可以推断这些富锌颗粒主要是铁酸锌、硅酸锌。锌的分布特征表明1号针铁矿渣在形成过程中,中和剂氧化锌的利用率较高,几乎不存在未反应的单独ZnO颗粒。而锌的弥散分布可能是由于在针铁矿形成过程中,针铁矿晶格在构建过程易夹带锌离子,使其嵌入晶格。另外,由于针铁矿比表面积大,具有强烈的吸附特性[22-23],这种吸附特性也会夹杂一部分锌,最终使得锌既有分散分布,又有集中分布。根据XRD分析结果可知呈铁、锌共存分布特征的颗粒可能是不参与反应的铁酸锌。
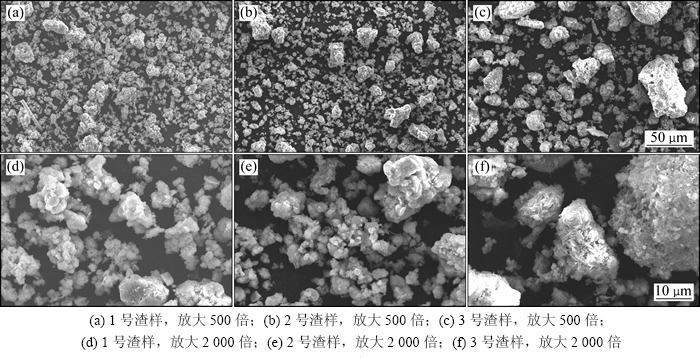
图3 针铁矿渣SEM照片
Fig. 3 SEM images of goethite residue samples
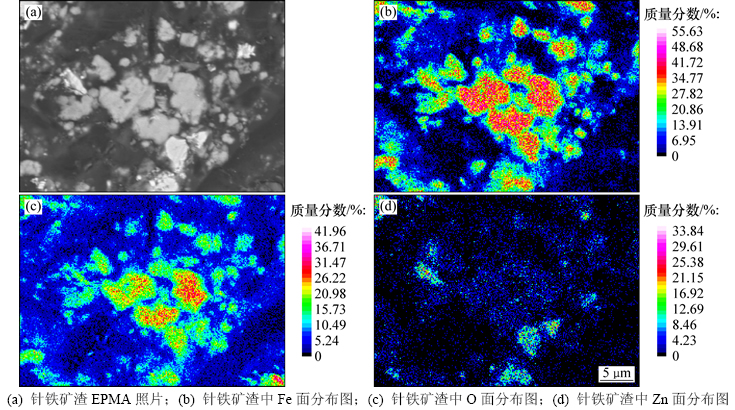
图4 1号针铁矿渣中Fe,O和Zn元素面扫描图
Fig. 4 Area scan images of Fe, Zn, S and O in No.1 goethite residue
根据1号样品EPMA照片中颗粒粒径和区域位置不同,选择有代表性的5个点进行分析。图5所示为1号针铁矿渣EMPA点分析结果;表2所示为针铁矿渣EPMA点分析结果。由图5及表2可知:点Ⅰ和点Ⅳ所属颗粒衬度较亮,属于锌原子数分数较高区域,其锌原子数分数分别为14.62%和32.79%,但点Ⅰ所属颗粒中铁原子数分数明显较高,为21.13%,由此推测点Ⅰ所属区域应为铁酸锌颗粒。点Ⅳ铁原子数分数较低,仅为1.59%,锌原子数分数较高,且锌、氧原子数分数之比接近1:2,表明点Ⅳ所属区域可能为硅酸锌颗粒。点Ⅱ,Ⅲ和Ⅴ中Fe原子数分数均较高,锌原子数分数均低于5.00%,但点Ⅴ中Fe原子数分数明显比点Ⅱ和点Ⅲ中的高,表明点Ⅴ所属区域可能为针铁矿颗粒,而点Ⅱ和点Ⅲ所属颗粒可能为氢氧化铁或水铁矿颗粒。此外,从图5(b)可见:存在针铁矿对硅酸锌物相的包裹现象。由于硅酸锌颗粒粒径较大,性质较稳定,加之存在包裹问题,使得硅酸锌更加难以参与反应,导致其主要进入渣中,这可能也是针铁矿渣中锌质量分数高的原因之一。
表2 针铁矿渣EPMA点分析结果
Table 2 Point analysis results of goethite residue by EPMA
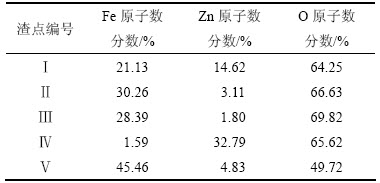
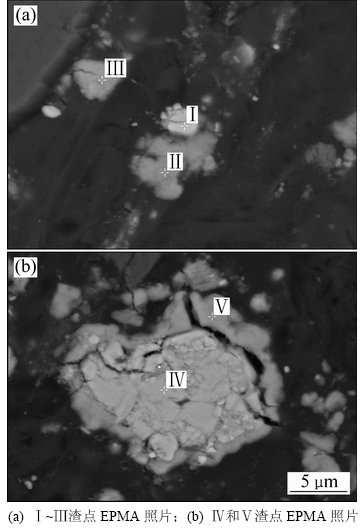
图5 1号针铁矿渣点扫描照片
Fig. 5 Point scan images of No. 1 goethite residue
3 结论
1) 尽管不同厂家的针铁矿渣成分差别较大,但其粒径及铁、锌分布特征相似;矿渣中粒径小于38 μm的颗粒占多数,且这部分颗粒渣铁质量分数较高、而锌质量分数较低。
2) 铁渣中锌质量分数较高的颗粒,其粒径也较大,特别是粒径超过80 μm的颗粒,锌质量分数为30%左右,因而,采用酸洗或分级处理均可有效降低针铁矿渣中锌质量分数。
3) 针铁矿渣样物相较为复杂,杂相除了由中和剂带入的硅酸锌、硅酸铁、铁酸锌外,还可能出现钾铁矾、铅铁矾新生物相。
4) 大部分铁在针铁矿样品中存在明显的富集相,而锌除了存在富集相外,还有部分呈分散分布;锌富集相主要由中和剂带入的铁酸锌、硅酸锌及未反应完全的大颗粒氧化锌构成,而锌的分散分布则可能是由于被吸附和嵌入针铁矿晶格而造成的。
5) 要获得理想的针铁矿渣,除了优化沉铁工艺条件外,还需考虑中和剂品质。
参考文献:
[1] DAVEY P T, SCOTT T R. Removal of iron from leach liquors by the goethite process[J]. Hydrometallurgy, 1976, 2(1): 25-33.
[2] CHANG Yongfeng, ZHAI Xiujing, LI Binchuan, et al. Removal of iron from acidic leach liquor of lateritic nickel ore by goethite precipitate[J]. Hydrometallurgy, 2010, 101(1): 84-87.
[3] XIE Yongfang, XIE Shiwen, LI Yonggang, et al. Dynamic modeling and optimal control of goethite process based on the rate-controlling step[J]. Control Engineering Practice, 2017, 58: 54-65.
[4] 周桂英, 刘美荣. 湿法冶金过程净化除铁的研究进展[C]//中国矿业科技大会. 北京冶金工业出版社, 2012: 69-76.
ZHOU Guiying, LIU Meirong. Research progress of iron removal for purification in hydrometallurgical process[C]//China Mining Science and Technology Conference. Beijing: Metallurgical Industry Press, 2012: 69-76.
[5] YUE Tong, HAN Haisheng, SUN Wei, et al. Low-pH mediated goethite precipitation and nickel loss in nickel hydrometallurgy[J]. Hydrometallurgy, 2016, 165: 238-243.
[6] HAN Haisheng, SUN Wei, HU Yuehua, et al. Induced crystallization of goethite precipitate from nickel sulfate solution by limonite seeding[J]. Hydrometallurgy, 2017, 174: 253-257.
[7] GULER E, SEYRANKAYA A. Precipitation of impurity ions from zinc leach solutions with high iron contents—a special emphasis on cobalt precipitation[J]. Hydrometallurgy, 2016, 164: 118-124.
[8] 吴远桂, 谈定生, 丁伟中, 等. 针铁矿法除铁及其在湿法冶金中的应用[J]. 湿法冶金, 2014, 42(2): 86-89.
WU Yuangui, TAN Dingsheng, DING Weizhong, et al. Goethite process for removing iron in hydrometallurgy[J]. Hydrometallurgy of China, 2014, 42(2): 86-89.
[9] 邓永贵, 陈启元, 尹周澜, 等. 湿法炼锌浸出液针铁矿法除铁晶种的制备[J]. 中国有色金属学报, 2008, 18(增刊1): 27-31.
DENG Yonggui, CHEN Qiyuan, YIN Zhoulan, et al. Preparation of goethite seeds for removal of ferrous/ferric ions from leaching solution of zinc in hydrometallurgy process[J]. The Chinese Journal of Nonferrous Metals, 2008, 18(S1): 27-31.
[10] 熊富强, 桂卫华, 阳春华, 等. 基于针铁矿法的沉铁过程动态建模[J]. 中南大学学报(自然科学版), 2012, 43(2): 541-547.
XIONG Fuqiang, GUI Weihua, YANG Chunhua, et al. Dynamic modeling for process of iron precipitation based on goethite method[J]. Journal of Central South University (Science and Technology), 2012, 43(2): 541-547.
[11] 李海军, 杨洪英, 陈国宝, 等. 中心复合设计针铁矿法从含钴生物浸出液中除铁[J]. 中国有色金属学报, 2013, 23(7): 2040-2046.
LI Haijun, YANG Hongying, CHEN Guobao, et al. Goethite deironization process for cobaltiferous bioleaching solution by central composite design[J]. The Chinese Journal of Nonferrous Metals, 2013, 23(7): 2040-2046.
[12] 陈宁, 范勇, 桂卫华, 等. 针铁矿法沉铁过程的混杂建模与控制[J]. 中国有色金属学报, 2014, 24(1): 254-261.
CHEN Ning, FAN Yong, GUI Weihua, et al. Hybrid modeling and control of iron precipitation by goethite process[J]. The Chinese Journal of Nonferrous Metals, 2014, 24(1): 254-261.
[13] WANG K, LI J, MCDONALD R G, et al. The effect of iron precipitation upon nickel losses from synthetic atmospheric nickel laterite leach solutions: Statistical analysis and modelling[J]. Hydrometallurgy, 2011, 109(1/2): 140-152.
[14] 张文山, 石朝军, 梅光贵. 湿法冶金(包括Zn、Mn、Cu、Ni、Co等)除铁的几种主要方法[J]. 中国锰业, 2006, 24(2): 42.
ZHANG Wenshan, SHI Chaojun, MEI Guanggui. Studies on several important methods of Fe removal from (Zn, Mn, Cu, Ni and Co) hydrometallurgy[J]. China’s Manganese Industry, 2006, 24(2): 42.
[15] CUBEDDU F, PIASENTIN M, REILLY F, et al. The paragoethite process at the Enirisorse-Porto Vesme Plant[C]//DUTRIZAC J E, HARRIS G B. Iron control and disposal. Montreal, Canada: Canadian Institute of Mining, Metallurgy and Petroleum, 1996: 147-161.
[16] DYER L G, RICHMOND W R, FAWELL P D. Simulation of iron oxide/silica precipitation in the paragoethite process for the removal of iron from acidic zinc leach solutions[J]. Hydrometallurgy, 2012, 119/120: 47-54.
[17] LOAN M, NEWMAN O M G, COOPER R M G, et al. Defining the paragoethite process for iron removal in zinc hydrometallurgy[J]. Hydrometallurgy, 2006, 81(2): 104-129.
[18] CLAASSEN J O, MEYER E H O, RENNIE J, et al. Iron precipitation from zinc-rich solutions: defining the Zincor Process[J]. Hydrometallurgy, 2002, 67(1/2/3): 87-108.
[19] HAN Haisheng, SUN Wei, HU Yuehua, et al. Magnetite precipitation for iron removal from nickel-rich solutions in hydrometallurgy process[J]. Hydrometallurgy, 2016, 165(24): 318-322.
[20] 骆昌运. 针铁矿除铁工艺在丹霞冶炼厂的应用实践[J]. 有色金属工程, 2011, 1(1): 44-46.
LUO Changyun. Application of goethite deironization process in Danxia Smelter[J]. Nonferrous Metals Engineering, 2011, 1(1): 44-46.
[21] ROMERO M, RINCON J M. Microstructural characterization of a goethite waste from zinc hydrometallurgical process[J]. Materials Letters, 1997, 31(1/2): 67-73.
[22] 邹雪华, 陈天虎, 张萍, 等. 天然针铁矿热处理产物的结构特征[J]. 硅酸盐学报, 2013, 41(10): 1442-1446.
ZOU Xuehua, CHEN Tianhu, ZHANG Ping, et al. Structural characteristic of natural goethite by thermal treatment[J]. Journal of the Chinese Ceramic Society, 2013, 41(10): 1442-1446.
[23] MOHAMED R, EL-MAGHRABI H H, RIAD M, et al. Environmental friendly FeOOH adsorbent materials preparation, characterization and mathematical kinetics adsorption data[J]. Journal of Water Process Engineering, 2017, 16: 212-222.
(编辑 伍锦花)
收稿日期:2018-03-01;修回日期:2018-05-07
基金项目(Foundation item):国家科技支撑计划项目(2015BAB02B02);国家自然科学基金资助项目(51864019)(Project(2015BAB02B02) supported by the National Science and Technology Support Program; Project(51864019) supported by the National Natural Science Foundation of China)
通信作者:李玉虎,博士,副教授,从事湿法冶金新工艺和新方法研究;E-mail:lyh_csu@163.com