J. Cent. South Univ. Technol. (2008) 15: 779-785
DOI: 10.1007/s11771-008-0144-2
Flame retardancy effect of surface-modified metal hydroxides On
linear low density polyethylene
KONG Xiang-jian(孔祥建)1, LIU Shu-mei(刘述梅)1, 2, ZHAO Jian-qing(赵建青)1, 2
(1. College of Materials Science and Engineering, South China University of Technology,
Guangzhou 510640, China;
2. The Key Laboratory of Polymer Processing Engineering of Ministry of Education,
South China University of Technology, Guangzhou 510640, China)
Abstract: Metal hydroxides (MAH) consisting of magnesium hydroxide and aluminum hydroxide with a mass ratio of 1?2 were surface-modified by γ-diethoxyphosphorous ester propyldiethoxymethylsilane, boric acid and diphenylsilanediol in xylene under dibutyl tin dilaurate catalyst at 140 ℃. Phosphorus, silicon and boron elements covalently bonded to metal hydroxide particles were detected by X-ray photoelectron spectroscopy. The degradation behavior of the surface-modified MAH was characterized by thermogravimetric analysis. The results show that linear low density polyethylene (LLDPE) composite, filled with 50% (mass fraction) of MAH modified by 5.0% (mass fraction) of modifiers, passes the V-0 rating of UL-94 test and shows the limited oxygen index of 34%, and its heat release rate and average effective heat combustion in a cone calorimeter measurement decrease obviously; The mechanical properties of MAH can be improved by surface-modification. The uniform dispersion of particles and strong interfacial bonding between particles and matrix are obtained.
Key words: metal hydroxides; linear low density polyethylene (LLDPE); synergistic flame retardancy effect; surface-modification
1 Introduction
Linear low density polyethylene (LLDPE) is a kind of widely used, easy to be burned material[1-2]. Flame retardants, such as halogenated flame retardants, phosphorus-containing flame retardants and metal hydroxides, are added to improve its flame-retarded property. Though halogenated flame retardants are effective, a world-wide innovation of substituting for halogenated flame retardants to avoid the persistent and bioaccumulative toxicity in the environment is an important trend in the plastics products[3-5]. Metal hydroxides, notably magnesium hydroxide (MH) and aluminum hydroxide (ATH), are extensively used as halogen-free flame retardants in polyethylene[6]. The thermal decomposition of metal hydroxides releases water, which subtracts energy from substrate, dilutes the combustible pyrolystate in the gas phase and thus retards the fire. Furthermore, their thermal degradation products, refractory metal oxides, act as a protective layer preventing oxygen from feeding the fire[7-8]. However, metal hydroxides are not effective flame retardants and incompatible with non-polar LLDPE. High loadings (approximate 60%, mass fraction) of metal hydroxides are always necessary for adequate flame retardancy, which leads to the deterioration of mechanical and processing properties of LLDPE material.
Improving interfacial structure is important for good dispersion of metal hydroxides in polymer matrix, which enhances mechanical properties and lowers melt viscosity[9-10]. The surface-modification of coupling agents can improve their interfacial structure[11-13]. Typical coupling agents for metal hydroxide filler contain organosilane coupling agents[14], titanate coupling agents, etc, which can react with the polar functional groups of metal hydroxides and form an organic coating[15]. However, the purpose of surface-modification of the fillers mainly aimed at the improvement of mechanical properties, seldom at the synergistic flame retardancy effect. In order to decrease high loadings of metal hydroxides, the combined use of metal hydroxides with other flame retardants has been performed on many investigations[16-17]. Many halogen- free flame retardants, such as red phosphorus, phosphate esters and zinc borate, have been found to be synergistic effect[5, 18]. However, the synergistic flame retardants are mostly incompatible with polymer matrix and incapable of improving the interfacial structure of metal hydroxides.
Their addition causes further deterioration of mechanical and processing properties of material.
Above all, the improvement of interfacial structure and synergistic effect are both important to the flame retardant system of metal hydroxides[5, 19-20]. In this work, metal hydroxides were surface-modified by γ- diethoxyphosphorous ester propyldiethoxymethylsilane (γ-PSi), boric acid and diphenylsilanediol. The surface-modified metal hydroxides (SMAH) were expected to coat organic layer containing phosphorus, silicon and boron elements and exhibit simultaneously improved flame retardancy due to synergistic effect with phosphorus, silicon and boron and improved interfacial adhesion with LLDPE matrix. Considering the decomposition temperature of MH at approximately 380 ℃ and ATH at 220 ℃, the mixture exhibiting flame retardancy effect in both high temperature and low temperature was used. The LLDPE composite filled by 50% SMAH passed the V-0 rating of UL-94 test, presented 34% limited oxygen index (LOI) value, and its mechanical properties were improved. Compared with the surface-modification of traditional coupling agents, the modification in the work introduced synergistic flame retardancy elements into organic coating layer to elevate the flame retardancy efficiency of metal hydroxides.
2 Experimental
2.1 Materials
MH (MARTIFIN H-5, d90=2.4-4.4 μm) and ATH (MARTINAL OL-107LE, d90=1.5-3.5 μm) were supplied by Martinswerk GmbH, Germany. LLDPE (trade name: 7042) with melt flow rate (MFR) of 2.0 g/10 min (2.16 kg, 190 ℃) was provided by Sinopec Maoming Refining & Chemical Co. Ltd, China. Boric acid (analytical reagent) was obtained from Tianjin Jingu Company, China. Diphenylsilanediol was provided by Bluestar New Chemical Material Co. Ltd, Jiangxi Xinghuo Organicsilcone Plant, China. γ-PSi was synthesized according to Ref.[21]. Dibutyl tin dilaurate (solution) was supplied by Shanghai Chemical Reagent Co. Ltd, China. Methanol and xylene were obtained from Tianjin Fuyu Chemical Company, China. N, N-dimethyl- formamide (DMF) was purified to obtain anhydrous solvent by vacuum distillation.
2.2 Surface-modification of MAH
The mixture of MH and ATH with a mass ratio of 1:2 (MAH) was dispersed in xylene under mechanical agitation to give slurry with solid content of 30% (mass fraction). When the system was heated to 140 ℃,γ-PSi, boric acid and diphenylsilanediol at mass ratio of 17?1?2 were charged in one batch, then small amount of dibutyl tin dilaurate was followed. After 6 h, xylene was vacuum-distilled off, and the residue was washed with methanol several times and dried at 60 ℃ under vacuum to give white powder product of constant mass. When the addition amounts of the modifiers were 0.5%, 1.0%, 3.0% and 5.0% (mass fraction), four kinds of surface- modified MAH named as SMAH-1, SMAH-2, SMAH-3 and SMAH-4 in turn were obtained.
2.3 Composite preparation
The mixture of LLDPE and MAH (or SMAH series) at mass ratio of 1?1 was melt-kneaded and extruded into pellets by using a 30 mm twin-screw extruder at a cylinder temperature of 175-200 ℃ and screw speed of 100 r/min. The resulting pellets were dried at 80 ℃ to constant mass and then injection-molded at an injection temperature of 180-205 ℃ into test pieces for measure- ment of the flame retardancy and mechanical properties.
2.4 Characterization
X-ray photoelectron spectroscope (XPS, AXIS ULTRA DLD) was used to determine surface element of SMAH at the survey pass energy of 160 eV (8 mA, 15 kV) using Al Kα ray. Thermogravimetric analysis (TGA) was performed on a NETZSCH TG 209 F1 thermogravimetric analyzer from 100 to 800 ℃ at a heating rate of 20 ℃/min under the flow of anhydrous air.
The LOI was tested using an Oxygen Index/FTA instrument (Fire Testing Technology Co. Ltd, England) on sheets of 150 mm×10 mm×4 mm according to the ISO 4589-1984. The vertical burning tests were carried out using a UL94 flammability meter (Fire Testing Technology Co. Ltd, England) on the sheets of 127 mm×12.7 mm×3 mm according to the UL-94 classification. The fire performance was characterized by the cone calorimeter (Fire Test Technology Co. Ltd, England) according to the ISO5660-1 (2000) under an external heat flux of 35 W/m2. The dimensions of the samples were 100 mm×100 mm×6 mm. Heat release rate (HRR), mass loss rate (MLR), average effective heat combustion (av-EHC) were recorded simultaneously. According to the standard of ASTM D638-98, the tensile strength of specimens was determined by using a Shimadzu (AG-1) universal electronic tensile testing machine at a crosshead speed of 50 mm/min. Izod impact strength of notched specimen with dimensions of 4 mm×10 mm×80 mm was determined with a Zwick 5102 pendulum type testing machine according to the ISO 180?1993. The impacting fracture surface of the specimens coated with gold by spraying ultrathin sections of the composite was observed on a JSM-6380 scanning electron microscope (SEM) at an accelerating voltage of 10 kV.
3 Results and discussion
3.1 Characterization of surface-modified MAH
XPS was employed for examining the composition of organic coating layer. Since all modifiers were not anchored to the surface of MAH particles, a 48 h extraction of SMAH-4 in DMF was performed[22], washed with methanol again, and dried at 60 ℃ under vacuum for 20 h. The obtained residues were conducted by XPS analysis. The result is shown in Fig.1. The appearance of phosphorus, silicon and boron elements in addition to Al and Mg suggests that three flame-retarded elements have been covalently bonded to the surface of metal hydroxide particles. Relative atomic mass fractions of phosphorus, silicon and boron are 1.00%, 1.81% and 3.23%, respectively, higher than their nominal percents calculated by the addition amounts. The results are consistent with the surface distribution of phosphorus, silicon and boron on the particles.
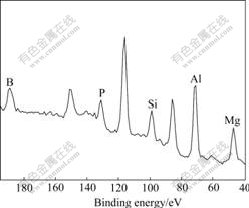
Fig.1 XPS pattern of SMAH-4 after extraction by DMF
TGA and DTG thermograms of MAH and SMAH series are shown in Fig.2. No mass loss occurs below 220 ℃,then MAH exhibits a two-stage thermooxidative degradation in air atmosphere. The first step is associated principally with the degradation of ATH with evidence for the substantial amounts of water release and the second stage is dominated by the degradation of MH. Two separate degradation peaks occur at 281 ℃ and 395 ℃ in DTG curve. The residue amount of the thermal degradation at 800 ℃ is 67.6%. SMAH series have a similar thermal stability as MAH. The onset temperature of the main degradation and two temperatures of the maximum mass loss rate are almost the same as those of MAH. The residue amounts of SMAH-1, SMAH-2, SMAH-3 and SMAH-4 at 800 ℃ are 67.2%, 67.0%, 65.9% and 65.3%, respectively, and tend to decrease with increasing addition amounts of the modifiers in the surface-modified process of MAH. This is possibly due to the introduction of organic substituents in γ-PSi and diphenylsilanediol.
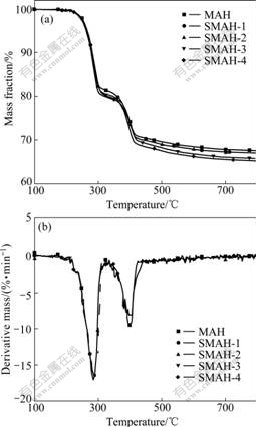
Fig.2 TGA (a) and DTG (b) thermograms of MAH and SMAH series
The above results show further that the surface- modified approach can anchor an organic coating layer containing synergistic flame-retarded element to metal hydroxide particles.
3.2 Flame retardancy of LLDPE/SMAH composites
The LOI, UL-94 and the cone calorimeter tests are widely used to evaluate flame retardancy of materials. For investigating the flame retardancy effect of surface- modified MAH, four kinds SMAH were employed for flame-retarding LLDPE with 50% loadings. The LOI values and UL-94 rating of the corresponding composites are listed in Table 1. It can be seen from Table 1 that the LOI values of LLDPE/SMAH composites are higher than that of LLDPE/MAH composite and increase with increasing addition amounts of the modifiers in the surface-modified process of MAH. The LOI of LLDPE/MAH composite is 27% and that of LLDPE/SMAH-4 composite increases to 34%. A large increase is obtained by the use of 5% modifiers. The UL-94 tests show that the flame retardancy rating of LLDPE/SMAH series composites increases with the addition amounts of the modifiers. LLDPE/MAH composite fails to V-2 rating, while LLDPE/SMAH-1 composite passes V-2 rating. With an increase of the amounts to 5.0%, LLDPE/SMAH-4 composite can pass V-0 rating. This means that the surface-modification of MAH by γ-PSi, boric acid and diphenylsilanediol improves the flame-retarded efficiency of MAH, which is probably attributed to the generation of synergistic flame retardancy effect of phosphorus, silicon and boron elements with metal hydroxides.
Table 1 LOI values and UL-94 rating of LLDPE and composites
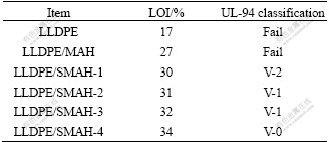
Measurements were performed to evaluate the flammability of LLDPE composites by a cone calorimeter. The data of peak heat release rate (pk-HRR), average heat release rate (av-HRR), av-EHC and average mass loss rate (av-MLR) of the samples are listed in Table 2. The HRR curves of LLDPE and the composites as a function of time are shown in Fig.3. The pk-HRR of neat LLDPE is as high as 866.9 kW/m2, and an addition of 50% MAH decreases pk-HRR of LLDPE composite to 228.6 kW/m2. LLDPE/SMAH series composites show smaller HRR, which decrease with addition amounts of the modifiers in the surface-modification process of MAH. The pk-HRR of LLDPE/SMAH-1 composite is 210.2 kW/m2 and a decrease occurs on the basis of LLDPE/MAH composite, indicating that the use of small amounts of modifiers produces obviously synergistic flame retardancy effect. Usually, pk-HRR is used to determine the intensity of a fire, EHC reflects the burning degree of the combustible and volatile gas in the gas phase[23]. MLR reflects the degree of thermal decomposition, volatile gas generation and burn. With the use of small amounts of modifiers, pk-HRR, EHC and MLR of LLDPE/SMAH-1 composites decrease in the same time. This shows that the modifiers increase not only the condensed phase but the gas phase flame retardancy of the composites. The pk-HRR of LLDPE/ SMAH-4 composite decreases to 204.6 kW/m2 and a small decrease extent compared with 206.5 kW/m2 of LLDPE/SMAH-3 composite indicates that the effect of addition amounts on HRR gets smaller after the addition amounts attain 2.5%. The variation of av-HRR and av-EHC of the composites presents the similar trend as pk-HRR. A small difference of LLDPE/SMAH-4 with LLDPE/SMAH-3 composite in HRR and av-EHC values indicates that 2.5% is the saturation addition amount of the modifiers, due to the organic substituents of modifiers. The parameter MLR in combustion is primarily responsible for the decrease of HRR of a material. The av-MLR of LLDPE/SMAH-4 composite reduces from 0.022 g/s of LLDPE/MAH composite to 0.020 g/s. A decrease degree of 10% is considerable based on the same 50% filled amounts of MAH. The above results confirm that the surface-modified MAH perform higher flame retardancy efficiency.
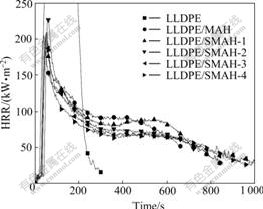
Fig.3 HRR of LLDPE and composites
3.3 Mechanical properties of LLDPE/SMAH com- posites
As previously pointed out, high MAH loadings for achieving adequate flame retardant properties of the composites will induce a large decrease of mechanical properties. The tensile strength of the composites is examined and the results are shown in Fig.4. It can be seen that the contribution of surface-modification to the improvement of tensile strength is obvious and the tensile strength of LLDPE/SMAH series composites is remarkably higher than that of LLDPE/MAH composite. The tensile strength of LLDPE/SMAH-2 composite among the four SMAH series composites is the maximum, which is about 1.24 times greater than that of LLDPE/MAH composite. After the addition amounts of the modifiers are greater than 1.0%, a slightly decrease trend in tensile strength is detected. The phenomena are presumably due to the formation of a monomolecular organic layer on the surface of inorganic particles, leading to an improvement of the dispersion of metal hydroxide particles in LLDPE matrix. The monomolecular organic layer acts just as a molecular bridge between the interfaces and as an internal lubricant, which improves the miscibility and interface adhesion enabling a more efficient load transfer. Excess amounts of modifiers, however, will form multilayers on the base of the first layer by van der Waal’s attraction, which is not tightly bound to the particles and tends to decrease the interfacial adhesion force at the boundary between the filler and polymer matrix, resulting in the deterioration of tensile strength[24].
Table 2 Cone calorimetric data for LLDPE and its composites at heat flux of 35 kW/m2

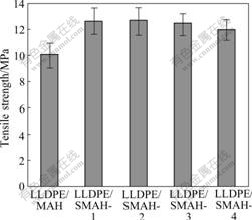
Fig.4 Tensile strength of LLDPE/MAH and LLDPE/SMAH series composites
Fig.5 shows elongation at break of LLDPE/MAH and LLDPE/SMAH series composites. The addition amounts of the modifiers influence the elongation at break of the composites to some degree. The elongation at break of LLDPE/SMAH-1 composite is 46%, smaller than that of LLDPE/MAH composite (65%). This might be due to that small amounts of modifiers tend to form strong interaction between filler particles and polymer matrix, which restrains the motion of LLDPE molecule and decreases the elongation at break. The elongation at break of LLDPE/SMAH series composites increases as the addition amounts of the modifiers increase. The elongation at break with 2.5% addition amounts is 70%, greater slightly than that of LLDPE/MAH composite. The elongation at break with 5.0% addition amounts reaches 87% and is about 1.34 times greater than that of LLDPE/MAH composite. This might be due to that the elongation at break is mainly dependent on the interfacial lubrication. Excess amounts of modifiers tend to form more lubricative interfaces between rigid particles and polymer matrix, which enhances stress relaxation during stretching, and then increases elongation at break of the composites.
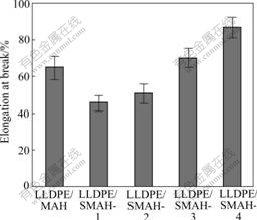
Fig.5 Elongation at break of LLDPE/MAH and LLDPE/SMAH series composites
Fig.6 shows the notched impact strength of the LLDPE/MAH and LLDPE/SMAH series composites. The impact strength increases with increasing addition amounts of modifiers. The impact strength at 5.0% addition amounts reaches 32.4 kJ/m2 and is about 1.62 times of that of the LLDPE/MAH composite (20.5 kJ/m2). That is to say, the impact strength of composites mainly depends on the dispersion of filler particles, for the increasing amounts of the modifiers help to improve the dispersion. Thus the surface- modification of MAH also ensures the interfacial structure to provide the improved mechanical properties.
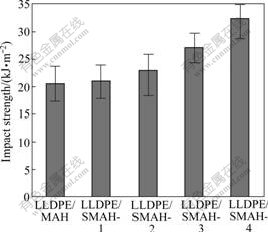
Fig.6 Notched impact strength of LLDPE/MAH and LLDPE/SMAH series composites
3.4 Dispersion of SMAH in LLDPE composites
Dispersion status of SMAH-4 in LLDPE matrix was examined by SEM images of the notched impact fracture surface in comparison with MAH in LLDPE (Fig.7). It can be seen that metal hydroxide particles are dispersed poorly in the polymer matrix with aggregation in Figs.7(a) and (b), while the surface-modified particles are dispersed uniformly with the disappearance of aggregates in Figs.7(c) and (d), where a kind of fiber drawing and network bonding metal hydroxides particles to the matrix can be obviously observed, indicating that the adhesion between the particles and matrix is so strong that the fiber drawing reticulate structure occurs around the particles during the impact process[25]. The strong interfacial bonding between the rigid metal hydroxide particles and LLDPE matrix should be arise from the entanglement of LLDPE molecular chains and organic layer shell of metal hydroxides. The uniform dispersion of particles and strong interfacial bonding between particles and matrix help to improve the overall properties of the composites.
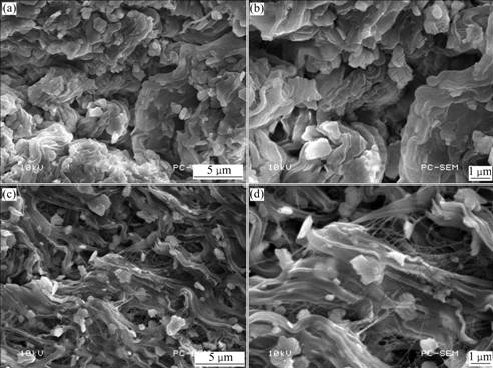
Fig.7 SEM images of LLDPE/MAH (a), (b) and LLDPE/SMAH-4 composite (c), (d)
4 Conclusions
1) Phosphorus, silicon and boron elements can be covalently bonded to the surface of metal hydroxides.
2) Increasing the content of modifiers within 1% to 5%, the flammability properties of LLDPE/SMAH-4 are greatly improved. It can be concluded that modifiers have good synergistic effect with metal hydroxides.
3) The LLDPE/SMAH-4 composite modified by 5.0% modifiers passes the V-0 rating of UL-94 test and shows 34% limited oxygen index, and its heat release rate and average effective heat combustion in a cone calorimeter measurement decrease obviously. The impact strength of LLDPE/SMAH-4 composite is about 1.62 times and the elongation at break is about 1.34 times greater than those of LLDPE/metal hydroxides composite.
References
[1] HAMEED T, HUSSEIN I A. Melt miscibility and solid-state properties of metallocene LLDPE blends with HDPE: Influence of MM of LLDPE [J]. Journal of Central South University of Technology, 2007, 14(s1): 183-187.
[2] LIANG Rui-feng. Processing flow behavior and modeling of polyethylene melts [J]. Journal of Central South University of Technology, 2007, 14(s1): 178-182.
[3] KIERKEGAARD A, BJORKLUND J, FRIDEN U. Identification of the flame retardant decabromodiphenyl ethane in the environment [J]. Environment Science & Technology, 2004, 38(12): 3247-3253.
[4] THOMSEN C, LUNDANES E, BECHER G. Brominated flame retardants in archived serum samples from Norway: A study on temporal trends and the role of age [J]. Environment Science & Technology, 2002, 36(7): 1414-1418.
[5] LU Shui-yu, HAMERTON I. Recent developments in the chemistry of halogen-free flame retardant polymers [J]. Progress in Polymer Science, 2002, 27(8): 1661-1712.
[6] FU Mou-zheng, QU Bao-jun, Synergistic flame retardant mechanism of fumed silica in ethylene-vinyl acetate/magnesium hydroxide blends [J]. Polymer Degradation and Stability, 2004, 85(1): 633-639.
[7] XIAO Jin, WAN Ye, DENG Hua, LI Jie, LIU Ye-xiang. Effects of drying method on preparation of nanometer α-Al2O3 [J]. Journal of Central South University of Technology, 2007, 14(3): 330-335.
[8] LIU Guan-jun, LI Wen-fang, PENG Ji-hua, DU Jun. Micro-yield behaviors of Al2O3-SiO2(sf)/Al-Si metal matrix composites [J]. Trans of Nonferrous Metal Soc China, 2007, 17(1): 307-312.
[9] HIPPI U, MATTILA J, KORHONEN M, SEPPALA J. Compatibilization of polyethylene/aluminum hydroxide (PE/ATH) and polyethylene/magnesium hydroxide (PE/MH) composites with functionalized polyethylenes [J]. Polymer, 2003, 44(4): 1193-1201.
[10] ZHANG Ling, LI Chun-zhong, ZHOU Qiu-ling, SHAO Wei. Aluminum hydroxide filled ethylene vinyl acetate (EVA) composites: Effect of the interfacial compatibilizer and the particle size [J]. Journal of Materials Science, 2007, 42(12): 4227-4232.
[11] CHEN Xiao-lang, YU Jie, GUO Shao-yun. Structure and properties of polypropylene composites filled with magnesium hydroxide [J]. Journal of Applied Polymer Science, 2006, 102(5): 4943-4951.
[12] NACHTIGALL S M B, MIOTTO M, SCHNEIDER E E, MAULER R S, FORTE M M C. Macromolecular coupling agents for flame retardant materials [J]. European Polymer Journal, 2006, 42(5): 990-999.
[13] PLENTZ R S, MIOTTO M, SCHNEIDER E E, FORTE M S M C, MAULER R S, NACHTIGALL S M B. Effect of a macromolecular coupling agent on the properties of aluminum hydroxide/PP composites [J]. Journal of Applied Polymer Science, 2006, 101(3): 1799-1805.
[14] LI Zhi-hua, LI Bo, ZHENG Zi-qiao. Special epoxy silicone adhesive for inertial confinement fusion experiment [J]. Journal of Central South University of Technology, 2007, 14(2): 153-156.
[15] LIAUW C M, LEES G C, HURST S J, ROTHON R N, ALI S. Effect of silane-based filler surface treatment formulation on the interfacial properties of impact modified polypropylene/magnesium hydroxide composites [J]. Composites Part A, 1998, 29(9/10): 1313-1318.
[16] DU Long-chao, QU Bao-jun, XU Zhen-jin. Flammability characteristics and synergistic effect of hydrotalcite with microencapsulated red phosphorus in halogen-free flame retardant EVA composite [J]. Polymer Degradation and Stability, 2006, 91(5): 995-1001.
[17] BRAUN U, SCHARTEL B. Flame retardant mechanisms of red phosphorus and magnesium hydroxide in high impact polystyrene [J]. Macromolecular Chemistry and Physics, 2004, 205(16): 2185-2196.
[18] BOURBIGOT S, DUQUESNE S. Fire retardant polymers: Recent developments and opportunities [J]. Journal of Materials Chemistry, 2007, 17(22): 2283-2300.
[19] CARPENTIER F, BOURBIGOT S, LE B M, DELOBEL R, FOULON M. Charring of fire retarded ethylene vinyl acetate copolymer-magnesium hydroxide/zinc borate formulations [J]. Polymer Degradation and Stability, 2000, 69(1): 83-92.
[20] BOURBIGOT S, DUQUESENE S, SEBIH Z, SEGURA S, DELOBEL R. Synergistic aspects of the combination of magnesium hydroxide and ammonium polyphosphate in flame retardancy of ethylene-vinyl acetate copolymer [J]. Fire and Polymers IV: Materials and Concepts for Hazard Prevention ACS Symposium Series, 2006, 922: 200-212.
[21] OLIVER S, LUCKAS H J, SANDRA R. Method for producing phosphonate-modified silicones: US, 20070049718 [P]. 2007-03-01.
[22] ZHANG Yong, ZHANG Zhi-jie, WANG Qian, XIE Ze-min. Synthesis of well-defined difunctional polydimethylsiloxane with an efficient dianionic initiator for ABA triblock copolymer [J]. Journal of Applied Polymer Science, 2007, 103(1): 153-159.
[23] ZUO Jian-dong, LI Rong-xun, FENG Shao-hua, LI Guang-ye, ZHAO Jian-qing. Flame retardancy and its mechanism of polymers flame retarded by DBDPE/Sb2O3 [J]. Journal of Central South University of Technology, 2008, 15(1): 64-68.
[24] HE Ji-hui, MA Wen-shi, TAN Shao-zao, ZHAO Jian-qing. Study on surface modification of ultrafine inorganic antibacterial particles [J]. Applied Surface Science, 2005, 241(3/4): 279-286.
[25] RUAN Ying, YANG Ming-shan, LIANG Tong-xiang, YAN Qin, LIU De-shan, JIN Ri-guang. Effects of the reinforcement and toughening of acrylate resin/CaCO3 nanoparticles on rigid poly(vinyl chloride) [J]. Journal of Applied Polymer Science, 2007, 103(6): 3940-3949.
Foundation item: Project(20574020) supported by the National Natural Science Foundation of China; Project(20061001) supported by the Opening Project of the Key Laboratory of Polymer Processing Engineering, Ministry of Education, China; Project (20060106-2) supported by Guangdong Key Projects
Received date: 2008-03-19; Accepted date: 2008-05-27
Corresponding author: ZHAO Jian-qing, Professor; Tel/Fax: +86-20-87113576; E-mail: psjqzhao@scut.edu.cn
(Edited by YANG Hua)