Trans. Nonferrous Met. Soc. China 24(2014) 1737-1743
Microstructure and mechanical properties of (TiB+La2O3)/Ti composites heat treated at different temperatures
Xiang-long GUO, Li-qiang WANG, Ji-ning QIN, Wei-jie
, Di ZHANG
State Key Laboratory of Metal Matrix Composites, Shanghai Jiao Tong University, Shanghai 200240, China
Received 11 March 2013; accepted 8 March 2014
Abstract: Near-α titanium matrix composites reinforced with TiB and La2O3 were synthesized by common casting and hot-working technology. The effects of β heat treatment temperature on the microstructure and the tensile properties of the in situ synthesized (TiB+La2O3)/Ti were studied. Microstructure was studied by OM and TEM, and tensile tests were carried out at room temperature and 923 K, respectively. Results show that with the increase of β heat treatment temperature, prior β phase grain size increases and α colony size decreases. Room temperature tensile strength increases with the increase of β heat treatment temperature, which can be attributed to the decrease of α colony size with the increase of β heat treatment temperature. However, high-temperature tensile strength decreases with the increase of β heat treatment temperature and the decrease of the high-temperature tensile strength is due to the increase of the prior β phase grain size.
Key words: titanium matrix composites; microstructure; mechanical properties
1 Introduction
As a result of the increasingly severe requirement for high-performance structural material in the aero industry, titanium matrix composites have been extensively studied due to the low density, high strength, high modulus and corrosion resistance [1-3]. Moreover, conventional techniques, such as powder metallurgy, common casting and mechanical alloying, can be applied to the in situ synthesis of whiskers and particles reinforced titanium matrix composites, which greatly reduces the cost of titanium matrix composites [4-6]. Among the various kinds of reinforcements that can be used to reinforce the titanium matrix composites, TiB is believed to be a good one because of its high strength, high thermal stability and similar thermal expansion coefficient to titanium. Rare earth oxide is proved to be useful in the high-temperature titanium matrix composites, which can increase the mechanical properties and thermal stability of the titanium matrix composites [7,8].
In the past years, β heat treatment for titanium alloys has been extensively studied. Compared with traditional (α+β) heat treatment, β heat treatment offers a fully lamellar microstructure, which improves the creep resistance, high-temperature tensile strength, oxidation resistance and fracture toughness properties of the titanium alloy. ZHANG et al [9] reported that β heat treatment method can greatly change the microstructure and mechanical properties of Ti-6Al-2Cr-2Mo-2Sn-2Zr alloy. FILIP et al [10] demonstrated that β heat treatment leads to higher fracture toughness property of Ti-6Al-2Mo-2Cr alloy and IVASISHIN et al [11] studied the influence of β heat treatment on the grain growth and texture evolution of Ti-6Al-4V alloy. However, the β heat treatment of titanium matrix composites has been rarely studied. In the present research, the influence of β heat treatment temperature on the microstructure, room and high temperature tensile properties of titanium matrix composites is studied.
2 Experimental
The titanium matrix composite was prepared with gradeⅠsponge titanium, LaB6 powder (>99%) and materials for synthesizing matrix Ti-Al-Sn-Zr-Mo-Si alloy such as AlMo (50% Mo), TiSn (65% Sn), AlNb (50%), Zr, Al, and Si. Stoichiometric amounts of grade I sponge titanium, LaB6, and alloying elements were blended and melt in a vacuum consumable arc-melting furnace. The ingot was melted three times to ensure the homogeneity of the composite. The α+β→β transus temperature was 1313 K.
TiB and La2O3 particles were synthesized in the melts according to the following reaction:
12Ti+2LaB6+3[O]=12TiB+La2O3
The volume fractions of TiB whiskers and La2O3 particles were 1.82% and 0.58% respectively. The titanium matrix composites slabs were cut from the received material and then hot-rolled unidirectionally at 1283 K with deformation degree of 40%. The heat treatment methods are shown in Table 1.
Table 1 Heat treatment methods for titanium matrix composites
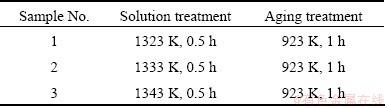
Microstructures of the composites were investigated by metallurgical microscopy, and the samples were cut directly from the plate, grinded, polished and etched by the conventional techniques. About 200 measurements were carried out to obtain the average aspect ratio of the TiB whisker, the average diameter of La2O3 particle and α colony size for each microstructural condition. The specimens for tensile test were machined from the heat treated plate with the specimen axis parallel to the rolling direction, and the gauge sections of the tensile specimens were 15 mm×4 mm×1.5 mm. Room and high temperature (923 K) tensile tests were carried out on a ZwickT1FR020TN-A50 and CSS-3950 at a strain rate of 10-3 s-1, respectively. JSM-6460 was used for studying the fracture surfaces as well as the morphology of the TiB reinforcement along the load sections. Reinforcement observations were carried out on a JEM-2000 EX transmission electron microscope.
3 Results and discussion
3.1 Matrix microstructure analysis
Figure 1 shows the microstructure of titanium matrix composites before and after β heat treatment. The microstructure of titanium matrix composites before heat treatment (Fig. 1(a)) consists of near equiaxed and elongated α phase grains. The forming of the specific microstructure results from the hot rolling process. When temperature dropped during rolling in the α+β phase, β phase transformed to α phase that grew into equiaxed α phase grains. Primary α phase was deformed during rolling and resulted in the elongated α phase grain. The allotropic transformation occurred when near-α titanium matrix composites were cooled from β phase district during the heat treatment and laminar α phase precipitated at the same time, so full lamellar structures were formed when titanium matrix composites were cooled from β phase district, as shown in Figs. 1(b), (c), and (d).
The variations of α colony size, d, with β heat treatment temperature is displayed in Fig. 2. It can be found that with the increase of β heat treatment temperature, α colony size decreases.
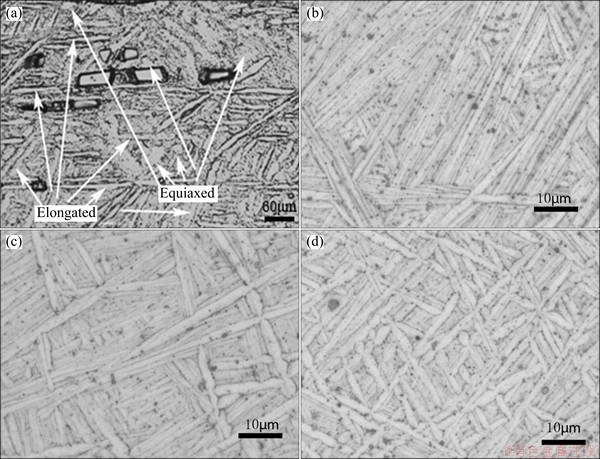
Fig. 1 Optical images of titanium matrix composites before (a) and after heat treatment at 1323 K (b), 1333 K (c), and 1343 K (d)
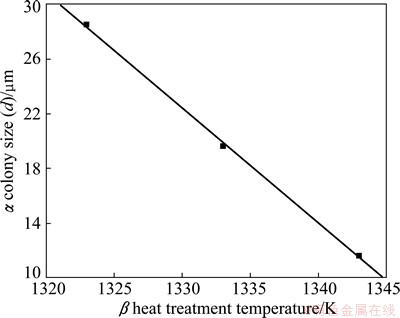
Fig. 2 Variation of α colony size with β heat treatment temperature
For isothermal grain growth, previous efforts [12-14] revealed the kinetics of grain growth as follows:
(1)
where Q is the activation energy; D and D0 denote final and initial β phase grain size, respectively; t is the annealing time; R is the mole gas constant; T is the heat treatment temperature; n is the grain-growth exponent; K is the rate constant. According to Eq. (1), in the present research, the grain size of prior β phase grain is determined by β heat treatment temperature T, and time t. So, if the β heat treatment time is the same, it can be easily concluded that prior β phase grain size increases with the increase of β heat treatment temperature.
In the present study, the α colony size does not coincide with the trend of the prior β phase grain size. Actually, the α colony size and the prior β phase grain size change inversely with the improvement of heat treatment temperature. The reasons for this may be that the cooling rate plays a key role in determining α colony size and the prior β phase grain size is in a subordinate position [9,15]. According to Newton’s law of cooling:
dT/dt=-k(T-TS) (2)
where T is the temperature of the object; t is the time, k is a positive constant; TS is the temperature of the surrounding; the cooling rate (dT/dt) is determined by the temperature difference between the object and the surroundings. In the present research, the titanium matrix composites are all air-cooled after heat treatment, so cooling rate is higher for titanium matrix composites with a higher β heat treatment temperature because of the larger temperature difference between the titanium matrix composites and the air. Besides, with the increase of the prior β phase grain size, the nucleation point of α colony increases, which results in the smaller α colony size. Thus, smaller α colonies are got in the titanium matrix composites with a higher β heat treatment temperature, as shown in Fig. 2.
3.2 Reinforcements after heat treatment
Figure 3 shows the morphology of the reinforcements after β heat treatment. It can be seen that the interface between reinforcements and titanium matrix is clean, and no interface pollution is detected, which indicates that TiB whiskers and La2O3 particles can effectively strengthen the titanium matrix composites. Statistical analysis [16] reveals that the average aspect ratios of TiB whiskers and average diameter of La2O3 particles are 6.57 and 200 nm, respectively. The morphologies of TiB whiskers and La2O3 particles are stable in the heat treatment process, and β heat treatment has no effect on the reinforcement formed during the solidification process [17].
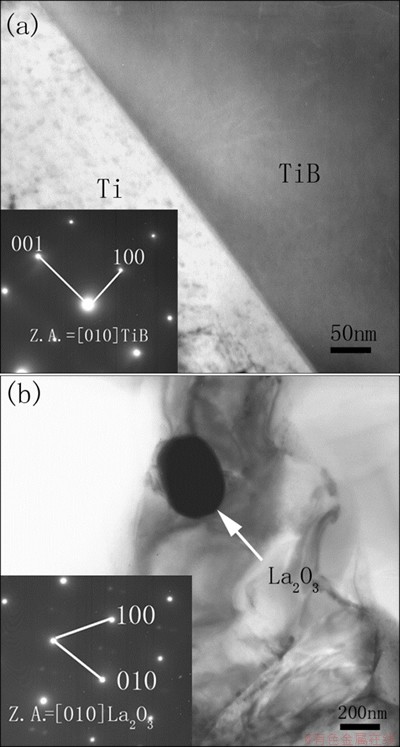
Fig. 3 TEM images of TiB whisker (a) and La2O3 particles (b) after heat treatment
3.3 Room temperature mechanical properties
Figure 4 shows the typical strength-strain responses of the titanium matrix composites heat treated at different temperatures. Strength of titanium matrix composites increases with the enhancement of β heat treatment temperature, while the elongation acts inversely.
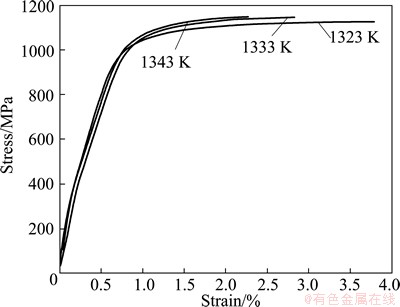
Fig. 4 Room temperature tensile properties of titanium matrix composites heat treated at different temperatures
It can be seen that the room temperature tensile strength of titanium matrix composites increases with the enhancement of β heat treatment temperature.
[15] reported that the most influential factor on the mechanical properties of fully lamellar structure is α colony size, because it determines the effective slip length. The smaller the α colony size, the higher the room temperature tensile strength, so the room temperature tensile strength of the titanium matrix composites increases with the improvement of heat treatment temperature. However, in the present research, the elongation of sample 3 decreases a lot compared with sample 1, and the great decrease in ductility may attribute to two reasons. Firstly, there is a “critical point” [15] for the α colony size in various titanium alloys. When the α colony size is bigger than the critical α colony size, the elongation increases with the reduction of α colony size. However, if α colony size is smaller than the critical size, further refinement of α colony leads to the decrease of elongation. The α colony sizes acquired in the present study are very small (<30 μm), which may be lower than the critical α colony size for the titanium matrix composites, so the decrease of the α colony size results in the decrease of elongations. Secondly, the influence of prior β phase grain size can not be neglected. The room temperature ductility of titanium alloys and titanium matrix composites is very sensitive to the changing of prior β phase grain size and the increase of prior β phase grain size can reduce the ductility of the titanium matrix composites greatly [18]. However, further researches are necessary to distinguish which factor plays the main role in determining the strain of titanium matrix composites.
Figure 5 shows the fracture surfaces of titanium matrix composites heat treated at different temperatures. It is observed that few dimples appear on the surface of the 1333 K and 1343 K heat treated samples, and the fracture surfaces are composed of cleavage planes, which suggests a brittle cleavage fracture. However, some big dimples are detected on the fracture surface of the sample heat treated at 1323 K, which means that the sample owns better ductility.
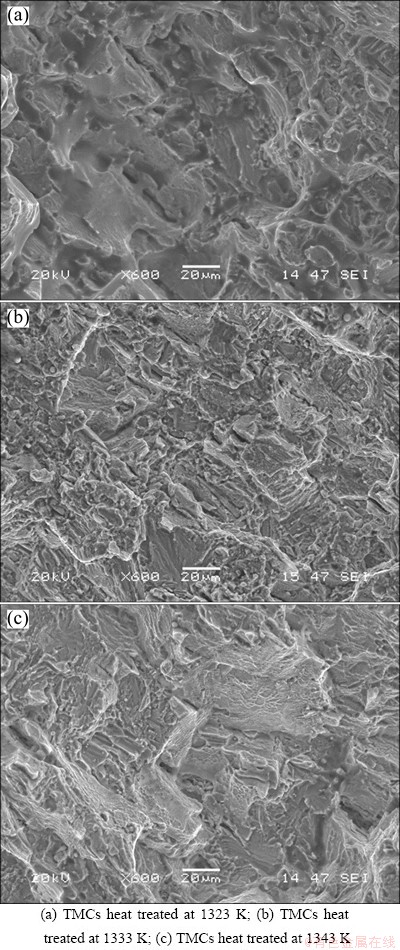
Fig. 5 Fracture surfaces of specimens after room temperature tensile test
3.4 High-temperature mechanical properties
High-temperature mechanical properties of the titanium matrix composites were tested at 923 K, and the results are shown in Table 2. It is found that with the rising of β heat treatment temperature, the elevated temperature tensile strength of the composites decreases, and the high temperature tensile strain increases. XIAO et al [19] reported that the “equicohesive temperature” of the matrix alloy is approximately 873 K at a tensile strain rate of 10-3 s-1, so when the testing temperature is higher than 873 K, the inner grain strength of α laths is higher than the grain boundary strength, and coarse α phase grains can effectively hinder the grain boundary sliding, so composites with smaller α colony size show inferior strength. However, ZHANG et al [20] reported that at a testing temperature higher than the “equicohesive temperature”, titanium matrix composites with a finer α colony owned higher tensile strength. The reason that XIAO et al [19] and ZHANG et al [20] got controversial conclusions might be that they both did not consider the influence of prior β phase grain size on the high temperature tensile strength of the titanium matrix composites. For the fully lamellar structure, the high temperature tensile strength is also sensitive to the prior β phase grain size, and bigger prior β phase grains result in a lower high temperature tensile strength [18]. So in the present research, the decrease of the α colony size and the increase of the prior β phase grain size both result in the decrease of high-temperature tensile strength. According to research of ZHANG et al [20], titanium matrix composites with smaller prior β phase grain and finer α colony have higher strength, which suggests that prior β phase grain size plays the main role in determining the high-temperature tensile strength.
Figure 6 shows the SEM images of TMCs after the high-temperature tensile test. From Figs. 6(a), (b) and (c), lots of dimples can be detected on the fracture surface, which suggests toughness fracture for the samples. It can also be found that dimples appearing in Fig. 6(c) are more than those appearing in Figs. 6(a) and (b), which indicates that sample 3 owns better tensile strain at elevated temperatures. Figures 6(d)-(f) show that lots of TiB whiskers are broken along the tensile direction. Prior study [21] revealed that the flow stress of IMI834 at 1273 K ranges from about 10 to 60 MPa at different strain rates. In this study, the titanium matrix composites were deformed at 1283 K, and at this temperature, the strength of ceramic TiB whisker decreased little, which is much higher than that of the matrix at 1283 K. So, most of the TiB whiskers will not break during the rolling process. The broken TiB whiskers that appearing in Figs. 6(d), (e) and (f) are attributed to the tensile process. Besides TiB whiskers, La2O3 particles can also increase the strength of the titanium matrix composites by dispersion strengthening effect [18].
Table 2 High temperature tensile properties of titanium matrix composites
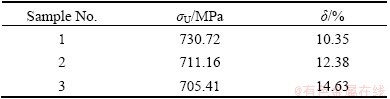
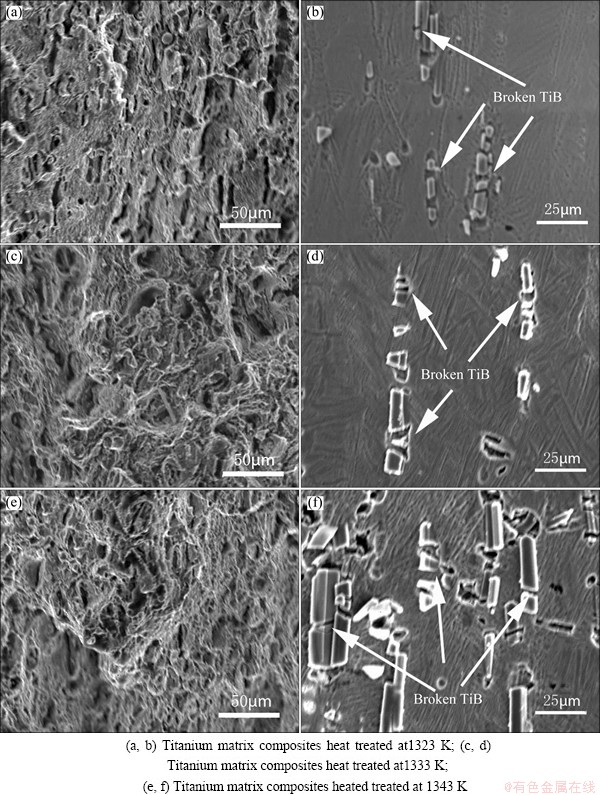
Fig. 6 SEM images obtained from high-temperature tensile test
4 Conclusions
1) Matrix microstructure of titanium matrix composites is very sensitive to β heat treatment temperature. With the increase of β heat treatment temperature, prior β phase grain size increases and α colony size decreases. The decrease of α colony size is due to the higher cooling rate and increasing nucleation points in the big prior β phase grain.
2) The room temperature tensile strength of titanium matrix composites is mainly determined by α colony size, and the decrease of tensile strain with the increasing of β heat treatment temperature can be attributed to the increase of prior β phase grain size and decrease of the too small α colony size. Elevated temperature strength decreases with the increase of β heat treatment temperature, which is mainly due to the increase of prior β phase grain size.
References
[1] Abkowitz S, Abkowitz SM, Fisher H, Schwartz P J. Cermt@Ti
discontinuously reinforced Ti-matrix composites: Manufacturing, properties, and applications [J]. JOM, 2004, 56: 37-41.
[2] Larsen J M, Russ S M, Jones J W. An evaluation of fiber reinforced titanium matrix composites for advanced high temperature aerospace applications [J]. Metallurgical Materials Transactions A, 1995, 26: 3211-3223.
[3] Tjong S C, Ma Z Y. Microstructure and mechanical characteristics of in situ metal matrix composites [J]. Material Science and Engineering A, 2000, 29: 49-113.
[4] Chandran K S R, Panda K B, Sahay S S. TiBw-reinforced Ti composites: Processing, properties, application prospects, and research needs [J]. JOM, 2004, 56: 42-48.
[5] Suryanarayana S. Mechanical alloying and milling [J]. Progress in Materials Science, 2001, 46: 1-184.
[6] Ranganath S, Vijayakumar M, Subrahmanyan J. Combustion-assisted synthesis of Ti-TiB-TiC composite via the casting [J]. Materials Science and Engineering A, 1992, 149: 253-357.
[7] Lu W J, Zhang D, Zhang X N, Wu R J. HREM study of TiB/Ti interfaces in a Ti-TiB-TiC in situ composite [J]. Scripta Materialia, 2001, 44: 1069-1075.
[8] de Castro V, Leguey T, Munoz A, Monge MA, Pareja R. Microstructure and tensile properties of Y2O3-dispersed titanium produced by arc melting [J]. Materials Science and Engineering A, 2006, 422: 189-197.
[9] Zhang X D, Bonniwell P, Fraser H L, Baeslack III W A, Evans D J, Ginter T, Bayha T, Cornell B. Effect of heat treatment and silicon addition on the microstructure development of Ti-6Al-2Cr-2Mo-2Sn-2Zr alloy [J]. Materials Science and Engineering A, 2003, 343: 210-226.
[10] Filip R, Kubiak K, Ziaja W, Sieniawski J. The effect of microstructure on the mechanical properties of two phases titanium alloys [J]. Journal of Materials Processing Technology, 2003, 133: 84-89.
[11] Ivasishin O M, Semiatin S L, Markovsky P E, Shevchenko S V, Ulshin S V. Grain growth and texture evolution in Ti6Al4V during beta annealing under continuous heating conditions [J]. Materials Science and Engineering A, 2002, 337: 88-96.
[12] Higgins G T. Grain-boundary migration and grain growth [J]. Metal Science, 1974, 8: 143-150.
[13] Greenwood G W. The growth of dispersed precipitates in solution [J]. Acta Materialia, 1956, 4: 243-248.
[14] Hillert M. The growth of dispersed precipitates in solution [J]. Acta Materialia, 1965, 13: 227-238.
[15]
G. Influence of processing on microstructure and mechanical properties of (α+β) titanium alloys [J]. Materials Science and Engineering A, 1998, 243: 32-45.
[16] GUO Xiang-long, WANG Li-qiang, WANG Min-min, QIN Ji-ning, ZHANG Di, LU Wei-jie. Effects of degree of deformation on the microstructure, mechanical properties and texture of hybrid-reinforced titanium matrix composites [J]. Acta Materialia, 2012, 60: 2656-2667.
[17] Fan Z, Chandrasekaran L, Ward-Close C M, Miodownik A P. The effect of pre-consolidation heat treatment on TiB morphology and mechanical properties of rapidly solidified Ti-6Al-4V-xB alloys [J]. Scripta Materialia, 1995, 32: 833-838.
[18] WANG Jin-you, GE Zhi-ming. Aeronautical titanium alloys [M]. Shanghai: Shanghai Science and Technology Press, 1985. (in Chinese)
[19] XIAO
,
Wei-jie, QIN Ji-ning, ZHANG Di. High temperature tensile properties of in-situ synthesized titanium matrix composites with strong dependence on strain rates [J]. Journal of Materials Research, 2008, 23: 3066-3074.
[20] ZHANG Zhen-gui, QIN Ji-ning, ZHANG Zhi-wei, CHEN Yi-fei,
Wei-jie, ZHANG Di. Effect of β heat treatment temperature on microstructure and mechanical properties of in situ titanium matrix composites [J]. Materials and Design, 2010, 31: 4269-4273.
[21] Donachie M J. Titanium: A technical guide [M]. Metals Park, OH: ASM International, 1988.
热处理温度对(TiB+La2O3)/Ti复合材料的显微组织和力学性能的影响
郭相龙,王立强,覃继宁,吕维洁,张 获
上海交通大学 金属基复合材料国家重点实验室,上海 200240
摘 要:采用熔铸法制备TiB短纤维和La2O3颗粒混杂增强的近α型钛基复合材料,并采用合适的热加工工艺将其加工成板材。研究β热处理温度对原位自生(TiB+La2O3)/Ti复合材料的微观组织和力学性能的影响规律。采用OM和TEM研究钛基复合材料的微观组织,同时测试钛基复合材料的室温以及高温(923 K)拉伸性能。结果表明:随着β热处理温度的升高,原始β晶粒尺寸增大但是α集束的尺寸变小;室温拉伸强度随着β热处理温度的升高而提高,这主要是因为α集束尺寸随着β热处理温度的升高而降低;而高温拉伸强度则随着β热处理温度的升高而降低,这主要是由于原始β晶粒随着β热处理温度的升高而增大。
关键词:钛基复合材料;微观组织;力学性能
(Edited by Hua YANG)
Foundation item: Project (2012CB619600) supported by the National Basic Research Program of China; Project (51371114) supported by the National Natural Science Foundation of China; Project (12XD1402800) supported by Excellent Academic Leaders Program of Shanghai, China
Corresponding author: Wei-jie
; Tel: +86-21-34202641; E-mail: luweijie@ sjtu.edu.cn
DOI: 10.1016/S1003-6326(14)63247-7