DOI:10.19476/j.ysxb.1004.0609.2018.02.02
AZ61镁合金降温多向压缩中的动态析出及其对晶粒细化和力学性能的影响
方正午1,肖振宇1,张笃秀1,尹 勇1,杨续跃1, 2, 3
(1. 中南大学 材料科学与工程学院,长沙 410083;
2. 中南大学 有色金属先进结构材料与制造协同创新中心,长沙 410083;
3. 中南大学 有色金属学材料科学与工程教育部重点实验室,长沙 410083)
摘 要:对AZ61镁合金进行降温多向压缩变形,利用OM,SEM/EBSD及TEM技术对其晶粒细化和析出相变化进行了观察和分析。结果表明:在623~483 K温度范围内降温多向压缩时AZ61镁合金晶粒急剧细化,低角晶界通过吸收位错转变成高角晶界,而降温变形会明显抑制晶粒长大和晶界高角化,5道次变形后还存在大量中低角晶界,平均晶粒尺寸约为0.8 μm。变形初期析出的第二相尺寸较大,随着变形道次的增加,第二相细化的同时数量明显增多。降温变形可促进动态析出,使得析出相分布更加细小、弥散。动态析出使得AZ61相对AZ31镁合金具有更高的硬度。AZ61镁合金经降温变形后强度和延性得到同步提升,尤其是5道次变形后伸长率显著提高,这是细小第二相在中低角晶界上动态析出造成的。
关键词:镁合金;多向压缩;中低角度晶界;动态析出
文章编号:1004-0609(2018)-02-0223-10 中图分类号:TG146.2 文献标志码:A
镁合金具有密度低、比强度高和减震性能优异等特点,常作为结构材料应用于汽车制造、航空航天工业等领域,符合当前发展需要减量增效、节能减排的要求,具有极大的发展潜力[1]。其中变形镁合金可通过变形与热处理相结合的方法来调控材料的组织结构,从而获得更加优异的力学性能。AZ31、AZ61镁合金是最常用的变形镁合金,AZ31镁合金中Al含量低,基体中基本不存在第二相,而AZ61和AZ91镁合金中的Al除固溶于基体中之外,还会形成Mg17Al12相[2]。合金中第二相的大小、形态与分布都可能影响其变形行为与力学性能[3],调控第二相是获取优异性能的主要方法之一[4]。通常钢和铝合金能通过变形过程中的动态析出调控第二相的大小及分布,从而取得较好的合金强化效果[5-6]。近来刘六法等[7]发现,AZ91镁合金在挤压过程中也有大量的Mg17Al12相动态析出,析出相特征与温度和变形量有关。在Mg15Al合金等径角挤压(EACP)过程中,由于高温与高应力的共同作用,基体内部出现大量尺寸在小于200 nm的粒状Mg17Al12动态析出相[8]。同时GUO等[9]在Mg-8Al合金大应变热轧板中也观察到了动态析出现象:动态再结晶晶粒内部析出大量纳米级Mg17Al12相,变形量越大,析出相含量越高,合金强度得到显著提升。然而热轧等变形时温度难以保持恒定,且动态析出与温度密切相关。因此,本研究中采用炉内变形以保证温度的恒定,变形完成后迅速冷却,并通过多向多道次变形来累积应变,便于对变形过程中动态析出相变化进行研究,还能获得不同道次变形时的真应力-累积应变曲线,从而对合金的变形行为进行研究。
多向变形作为镁合金常用的开坯工艺,工业应用前景广阔。本文作者课题组[10-12]采用降温多向压缩研究了Mg-Al-Zn系合金变形中的晶粒细化,所制备出的超细晶AZ61镁合金抗拉强度均高于400 MPa,室温伸长率都在15%以上,强度与伸长率的同步提升可能与动态析出有关。JIANG等[13]发现在AZ61镁合金多向高速锻造(MDIF)初期,细小椭圆的Mg17Al12相会动态析出在原始晶界上,随着锻造道次的增加,晶粒内部也会发生动态析出。SOMJEET等[14]对Mg-Al-Mn合金进行降温多向压缩变形后,使其室温伸长率高达55%,降温变形能有效改善镁合金延性。在此,本文作者通过光学显微镜(OM)、电子背散射衍射(EBSD) 及透射电子显微镜(TEM)技术观察分析AZ61合金降温多向压缩变形时组织和析出相变化,探讨动态析出对组织演变、力学性能尤其是室温拉伸伸长率的影响,为开发低成本高强高延性镁合金提供了理论指导。
1 实验
本实验中采用热挤压态AZ61镁合金,经773 K下退火2 h后得到晶粒平均尺寸约为56 μm的组织。样品规格为31 mm×21 mm×14 mm的长方体,最长轴方向与挤压方向平行。实验在附有保温炉的万能试验机(WDW-100A型)上进行,变形沿着X、Y和Z方向循环进行(见图1(a)),变形速率设定为3×10-3 s-1,每道次变形量设定为Δε=0.8,总共进行5道次(∑Δε=4)变形。变形前将样品放入保温炉中(炉温设定为实验温度)保温10 min,变形完成后在1.5 s内取出样品进行水淬。第1道次变形温度为623 K,随后各道次变形温度依次降低,图1(b)给出了具体工艺曲线。
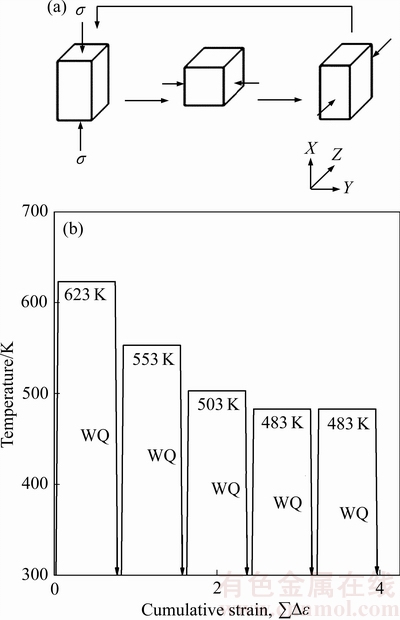
图1 镁合金降温多向压缩示意图和工艺曲线
Fig. 1 Schematic diagram of multi directional forging (MDF) (Each pass strain is Δε=0.8, once pass strain is finished, forging axis is changed by 90°, WQ is water quenching) (a) and continuous decreasing temperature processing (b)
将水淬样品沿最终道次压缩方向切开,对垂直压缩方面进行研磨、抛光处理后利用腐蚀液进行浸蚀,成分为4.2 g苦味酸(C6H3N3O7)、10 mL冰醋酸(CH3COOH)、10 mL蒸馏水(H2O)和70 mL酒精(C2H5OH)。随后利用OLYMPUS光学显微镜(OM)进行显微组织观察。通过电解抛光制取EBSD样品后,采用Sirion 200型场发射扫描电子显微镜(SEM)及其配备的OIM Data Collection 5.3和OIM Analysis 5.3对其微观织构进行分析。透射电镜试样在Tenupol-3型双喷电解设备上进行双喷穿孔(电解液成分为体积比1:2的硝酸和甲醇混合溶液),然后使用Tecnai G2 20型TEM进行显微组织观测。拉伸试验在室温下进行,拉伸试样的计量尺寸为3 mm×6 mm×0.7 mm。
2 结果与讨论
2.1 降温多向压缩的真应力-真应变曲线
图2所示为AZ61镁合金与AZ31镁合金[15]降温多向压缩的真应力-累积应变(σ-∑Δε) 曲线。2组曲线所对应工艺均为优选工艺,能在避免变形中样品发生开裂的同时显著细化晶粒,有效提高合金力学性能。可以看出,2种合金第1道次变形时温度相同,变形曲线均为典型的动态再结晶型,应力达到峰值后都出现明显的加工软化。不同的是,AZ31镁合金在后续4道次变形中仍存在明显的加工软化,各道次软化程度相差不大,变形温度对其影响甚小。而AZ61镁合金的加工软化现象随着变形温度的降低明显减弱,甚至在483 K下第5道次变形时不再发生加工软化,应力随着累积应变的增加始终增加。此外,从图2还可看出,AZ31镁合金第3、4道次变形温度相同,两者的屈服强度相差不大,第4道次变形时仍出现加工软化。而AZ61镁合金第4、5道次变形温度同样相同,但其第5道次变形时已不再出现加工软化,屈服强度相对第4道次有明显提升。上述差异应该与动态析出有关,AZ61镁合金比AZ31镁合金的Al元素含量更高,变形时第二相更容易析出。此外,低温高应变变形也会造成大量的动态析出[16],所以降温变形时变形温度的降 低、累积应变的增加促进了AZ61镁合金的动态析出,其晶粒内较高的动态析出相密度会阻碍位错运动,从而提高合金的屈服强度与变形抗力,导致加工软化现象消失。
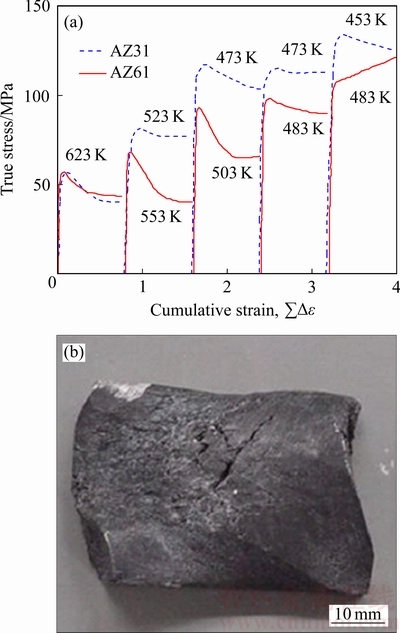
图2 AZ61和AZ31镁合金[15]降温多向压缩过程中的真应力-累积应变曲线及AZ61镁合金经5道次变形后的宏观图像
Fig. 2 True stress-cumulative strain curves of AZ61 and AZ31 Mg alloys[15] during MDF decreasing temperature condition from 623 K to 483 K(423 K) at strain rate of 3×10-3 s-1(a) and macrograph of AZ61 alloy after five passes MDF(b)
2.2 组织观察
图3所示为AZ61镁合金不同道次变形后的OM像。可以看出,初始退火态(见图3(a))为等轴状组织,晶粒清晰可辨,基本观察不到析出相分布。而经过1道次变形后(见图3(b)),组织内出现大量尺寸不一的动态再结晶晶粒,晶粒急剧细化,此时晶粒内部仍较为清晰,但部分晶界已难以分辨,这应该是动态析出所造成。2道次变形完成后(见图3(c)),晶粒发生进一步细化,晶界模糊区域也进一步增多。随着累积应变量的增加与变形温度的降低(见图2),发生动态析出的区域逐渐扩大。5道次变形后的OM像已难以分辨出晶粒,动态析出基本覆盖整个区域(见图3(d))。
2.3 第1道次变形的EBSD分析
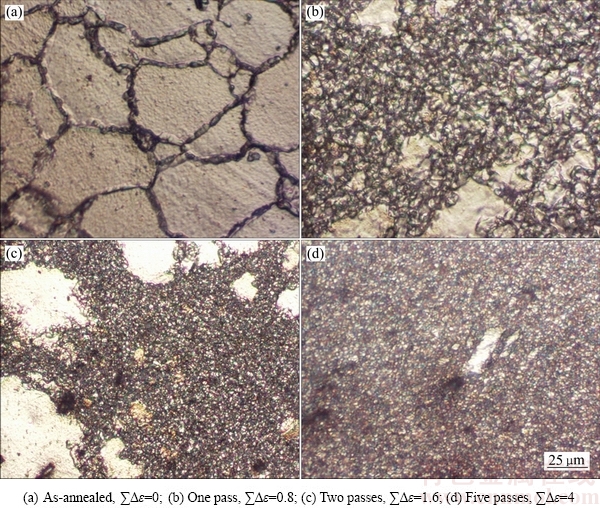
图3 AZ61镁合金降温多向压缩后的OM像
Fig. 3 OM images of AZ61 Mg alloy before and after MDF under continuous decreasing temperature
AZ61镁合金第1道次变形进行至∑Δε=0.1时达到应力峰值,随后出现加工软化现象,约在∑Δε=0.4时进入稳态变形阶段(见图2)。利用高分辨EBSD技术对变形前(∑Δε=0)、软化刚发生(∑Δε=0.2)以及软化结束(∑Δε=0.4)阶段的样品组织进行分析,结果如图4所示。图4(a)~(c)所示分别为各状态的晶粒取向图,图中不同取向的晶粒用不同颜色来表示。黑实线代表高角度晶界(取向差大于15°),红实线和黄实线分别代表中角度晶界(取向差大于5°)和低角度晶界(取向差介于2°~5°之间)。从图4(a)可以看出,初始态晶粒为等轴状,晶界几乎都为高角度晶界,而在软化刚发生(∑Δε=0.2)阶段,原始晶界凸出处有细小的晶粒出现,这是典型的动态再结晶晶粒[17],其附近区域还形成了低角度晶界和中角度晶界,这些中低角晶界即扭折带,是一种位错界面,由基面位错堆积导致晶格弯曲所致[18],它能松弛局部应力集中,协调变形,并在变形过程中不断吸收周围位错[18],转变成高角晶界。同时其数量也逐渐增多,有助于分割细化原始晶粒(见图4(b)中A1晶粒内)。随着变形量的增大,新形成的晶粒内部也会出现新的中低角晶界(见图4(c)中A2晶粒内),进一步分割细化原始晶粒;变形进入稳态阶段(∑Δε=0.4)时,再结晶程度得到进一步提升,晶粒细化显著,组织更加均匀,晶粒内部仍存在大量中低角晶界(见图4(c))。
图4(d)~(f)所示为各状态对应的衬度图,依据Kikuch带绘制而成,可直观地反映出变形组织的形貌。从图4(d)可以看出,初始退火态组织边界清晰,图像质量高。而第1道次变形开始后(∑Δε=0.2),部分区域表现出凹凸不平的形貌(见图4(e)),反映出在SEM下对该类区域进行数据采集时存在强度差异,这种差异应该是组织中分布的第二相造成的,说明在第1道次变形初期就发生了动态析出。同样,图4(f)的图像质量也受到了第二相的影响。
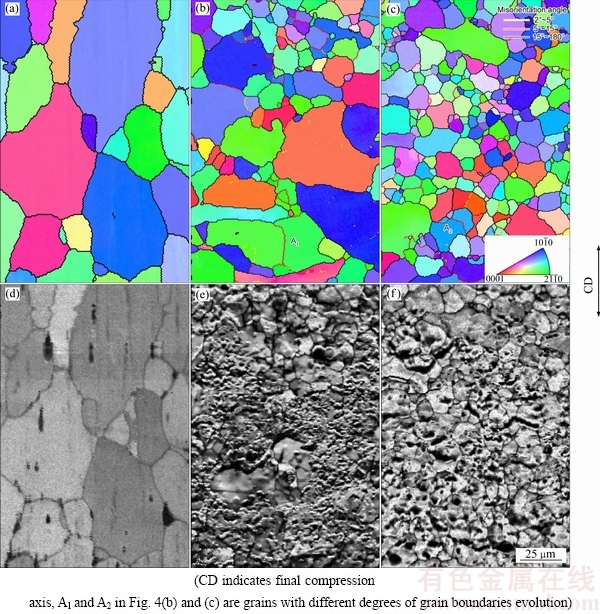
图4 AZ61镁合金第1道次变形的EBSD取向图及图像质量图
Fig. 4 EBSD-orientation maps ((a), (b), (c)) and their corresponding imaging quality maps ((d), (e), (f)) of AZ61 Mg alloy as annealed ((a), (d)) and 1st pass deformation to cumulative strains of 0.2 ((b), (e)) and 0.4 ((c), (f))
2.4 降温多向压缩过程中动态析出相及组织变化
为进一步了解AZ61镁合金多向压缩变形中的动态析出行为与组织演变,利用透射电镜(TEM)对其进行观察。图5所示为初始态和2、3道次变形态的TEM像。从图5(a)可以看出,初始态组织中不存在第二相,原始晶粒边界与内部都极为清晰,位错密度极低。经过2道次变形后(见图5(b)),晶界附近出现了尺寸较大的椭圆状析出相。此时原始晶粒已得到显著细化,平均晶粒尺寸约为3.8 μm。晶粒边界与晶粒内部依旧清晰,位错密度仍然很低,其选区衍射花样(SAED)为一系列同心圆环(见图5(b)中插图),这说明晶粒间均为高角度晶界,晶粒取向呈现出随机化。随着变形量的增加,3道次变形后(见图5(c))晶粒进一步细化至2.0 μm,此时晶粒边界与位错密度无明显变化,但尺寸较大的第二相明显减少,晶粒内部开始出现细小的第二相(见图5(d)),其SAED谱(见图5(d)中插图)证明其为BCC结构的Mg17Al12相。
这是因为1、2道次的变形温度较高,过饱和的Al原子容易在原始晶界高密度位错堆积处析出第二相[19],这些析出相尺寸较大,对位错运动的阻碍作用很小,变形初期形成的位错堆积及扭折带等低角度位错界面在后续变形中易吸收可动位错,取向差不断增大,从而转变成高角度晶界,有效分割细化原始晶粒[18],并最终形成动态再结晶晶粒,导致晶粒内部位错密度较低。第3道次变形时,随着应变量的增加,部分先前道次变形中析出的尺寸较大的第二相发生破碎细化,阻碍位错运动,同时变形温度的降低会使位错运动的驱动力减小,中低角晶界难以吸收位错,导致位错密度变高,高密度位错缠结处增多,并向晶粒内部扩展,而Al原子在该位置过饱和度更高[20],因此第二相粒子的形核位置增多,再结晶晶粒内部开始析出细小的第二相。
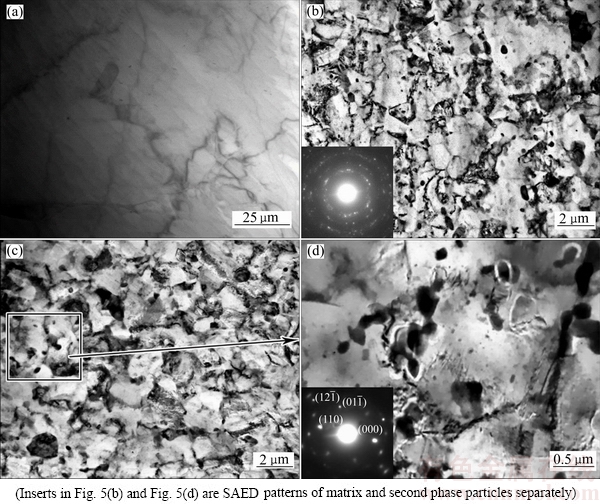
图5 AZ61镁合金降温多向压缩前3道次变形的TEM像
Fig. 5 TEM images of AZ61 Mg alloy before and after prior three passes MDF under continuous decreasing temperature (a) as-annealed, ∑Δε=0, (b) ∑Δε=1.6, (c) ∑Δε=2.4 and local image for zone in Fig. 5(c), (d)
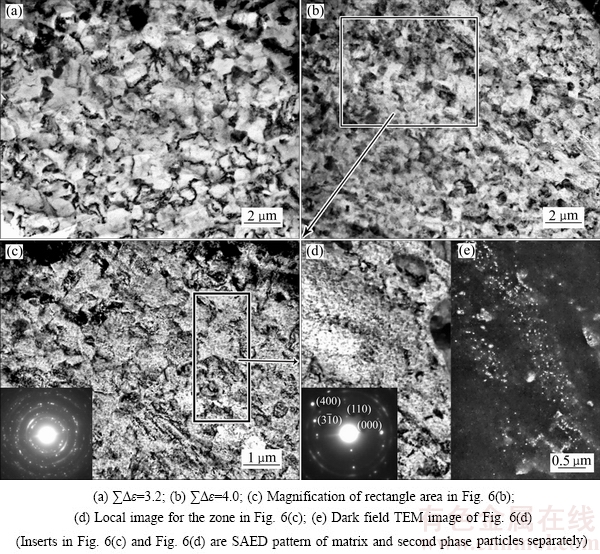
图6 AZ61镁合金降温多向压缩4、5道次变形的TEM像和SAED谱
Fig. 6 Bright field ((a)-(d)) and dark field (e) TEM images of AZ61 Mg alloy after four and five passes MDF under continuous decreasing temperature
图6所示为AZ61镁合金经4、5道次变形后的TEM像和第二相的SAED像。从图6(a)可以看出,相对前3道次变形(见图5),4道次变形后再结晶晶粒发生进一步细化,平均晶粒尺寸约为1.2 μm。此时部分区域晶粒边界不再清晰,组织内位错密度较高,同时尺寸较大的第二相粒子几乎消失,大量细小第二相分布其中。 变形进行到5道次后(见图6(b)),晶粒进一步细化至约0.8 μm,此时大部分区域晶粒边界不再清晰。图6(c)所示为图6(b)的高倍率图像,可以看出,细小的第二相粒子弥散分布于晶粒内部,晶粒边界十分模糊,晶粒内部表现出极高位错密度。其SAED除一系列圆环外,还有许多强度不一的衍射斑点分布在圆环周围(见图6(c)中插图),这说明组织中存在大量中低角晶界。图6(d)和(e)所示为图6(c)中某区域的明暗场像,可以看出,基体中分布着大量细小、弥散的第二相。图6(d)中插图所示为该相的SAED谱,该套斑点为BCC晶体[001]晶带轴的电子衍射花样。查阅Mg-Al合金中可能存在相的PDF卡片,初步确定该套衍射斑点由Mg17Al12产生。通过计算得出该SAED谱对应的点阵常数为a=b=c=10.55 nm,与BCC结构的Mg17Al12的点阵常数(a=b=c=10.5438 nm)极为接近。可以确定细小的动态析出相也为BCC结构的Mg17Al12相。
第4、5道次的变形温度相同,其变形过程中的组织演变和第二相变化与累积应变有关。随着累积应变量的增加,晶粒得到进一步细化,原有的第二相继续破碎,同时晶粒内部也析出更多细小、弥散分布的第二相,这些细密的第二相极大地阻碍了位错的运动,造成位错堆积,同时阻碍扭折带等低角度晶界在变形过程中进一步吸收其他可动位错而转变成高角度晶界,因此变形组织内存在着大量中低角晶界,晶粒边界不再清晰。这也是图2中第4、5道次变形中加工软化现象减弱甚至消失的主要原因。随着变形温度的降低(与第3道次变形温度相比)和应变量的增加,位错密度不断提高,位错运动驱动力反而下降,同时晶粒内部析出的越来越细小、弥散的第二相对位错的钉扎作用也大大增强,进一步阻碍了位错运动,使得变形抗力不断提高。
2.5 动态析出对合金力学性能的影响
AZ61镁合金与AZ31镁合金硬度与累积应变的关系如图7所示。由图7可以看出,两合金的硬度均与累积应变量成线性关系。通常变形温度越高,越容易发生回复与动态再结晶,会造成合金硬度下降。但是尽管降温多向压缩过程中AZ61镁合金各道次变形温度更高(见图2),其硬度及增长速率反而明显高于AZ31镁合金,经5道次变形后超过了975 MPa,后者仅为785 MPa。原因在于AZ61镁合金在降温多向压缩过程中发生了动态析出,且随着变形量的累积,析出相变得细小弥散,对位错钉扎作用不断增强,导致两合金硬度差值不断增大。此外,晶粒细化也会提升合金硬度,因此图8将结合晶粒尺寸与室温硬度的关系来进一步探究动态析出对合金硬度的影响。
图8所示为AZ61镁合金和AZ31镁合金[15]室温硬度与平均晶粒尺寸(D)的关系曲线。可以看出,两类合金室温硬度均与D-1/2的值成正比,但AZ61镁合金比AZ31镁合金曲线斜率更高。AZ31镁合金中基本不存在第二相,而AZ61镁合金在降温多向压缩过程中会发生动态析出,两者主要强化机制存在差异。AZ31 镁合金主要强化机制是固溶强化与细晶强化,而由图3可看出,AZ61镁合金经降温多向压缩变形后,除细晶组织外还存在第二相分布(见图5),晶粒内部位错密度较高(见图6)。因此该合金的主要强化机制还有第二相强化和位错强化。
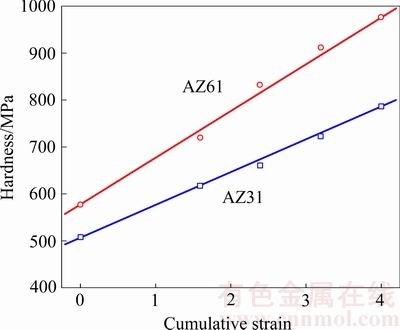
图7 AZ61镁合金与AZ31[15]镁合金硬度与累积应变曲线
Fig. 7 Hardness change depending on cumulative strain of AZ61 and AZ31[15] Mg alloys
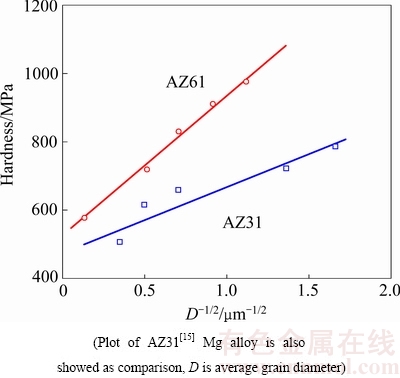
图8 降温多向压缩变形AZ61镁合金和AZ31镁合金[15]的Hall-Petch曲线
Fig. 8 Hall-Petch plot of MDFed AZ61 Mg alloy under decreasing temperature
对于Mg-Al系合金的固溶强化,相关研究表明[21-22],其屈服强度增量
可用下列公式描述:
(1)
式中:C为常数;X为溶质摩尔浓度。
对于细晶强化,根据Hall-Petch关系,其屈服强度增量
可用下列公式描述[23]:
(2)
式中:
为Hall-Petch系数;d为平均晶粒尺寸。
对于第二相强化,其强化方式主要有两种:切割机制和绕过机制(即Orowan机制)。AZ61合金中第二相强化机制为Orowan机制。对于Orowan机制,位错线绕过第二相粒子所引起的屈服强度增量
可用下列公式描述[24]:
(3)
式中:M为基体的Taylor因子;G为基体的剪切模量;b为基体位错的柏氏矢量大小;
为球状第二相粒子随机横截面的平均半径;ν为泊松比;r为第二相粒子的平均半径;λ为滑移面上粒子间的平均距离[24]:
(4)
式中:f为第二相的体积分数。
对于位错强化,其屈服强度增量
可用下列公式描述[20]:
(5)
式中:
为常数;
为位错密度。
假设上述各强化效果可以线性叠加[23],则AZ61镁合金的屈服强度
可以表示为:
(6)
式中:
为Mg-Al合金的晶格摩擦应力。
合金2的曲线差异主要由固溶强化、第二相强化以及位错强化造成。相同晶粒尺寸的AZ61镁合金与AZ31镁合金相比,由于溶质摩尔浓度更高和动态析出相的存在而具有更高的硬度。此外,随着累积变形量的增加,AZ61镁合金中的细小动态析出相不断增多(见图5(d)和图6(e)),滑移面上粒子间的平均距离不断减小,因此第二相强化带来的屈服强度增量
会不断增大。同时,细小弥散的第二相还会钉扎位错,阻碍中低角晶界吸收位错进行高角化,使得组织内位错密度得到提高,其带来的屈服强度增量
也不断增大。故AZ61镁合金Hall-Petch曲线斜率高于AZ31镁合金的。
图9所示为AZ61镁合金初始态和经2、4和5道次降温多向压缩变形后的室温拉伸应力-应变曲线。可以看出,经2道次变形后,合金的抗拉强度和伸长率得到了同步提升,4道次变形后合金强度得到进一步提升,伸长率没有太大变化,而全部5道次变形完成后,合金强度继续提升的同时伸长率出现显著提高。与低道次变形相比(见图3),4、5道次变形后晶粒尺寸相差不大(见图6),晶粒尺寸应该不是第5道次变形后合金抗拉强度和伸长率出现显著提升的主要原因。从图6(c)~(e)可以看出,5道次变形后组织内存在大量中低角晶界和细小的动态析出相。5道次变形后合金伸长率的显著提高应该与细小第二相在中低角晶界上动态析出有关。
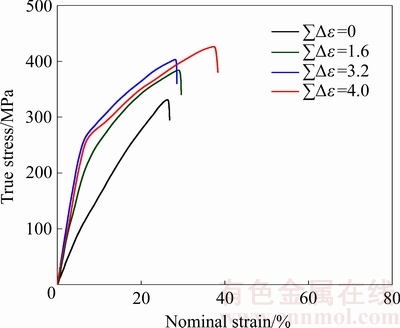
图9 AZ61镁合金不同道次变形后的室温拉伸应力-应变曲线
Fig. 9 Tensile true stress-strain curves of AZ61 Mg alloy at room temperature
3 结论
1) AZ61镁合金在623~483 K下降温多向压缩时晶粒急剧细化,低角晶界通过吸收位错转变成高角晶界,而降温变形会明显抑制晶粒长大和晶界高角化, 5道次变形后还存在大量中低角晶界,平均晶粒尺寸约为0.8 μm。
2) 变形初期析出的第二相尺寸较大,随着变形道次的增加,第二相细化的同时数量明显增多。降温变形可促进动态析出,使得析出相分布更加细小、弥散。
3) AZ61镁合金经降温变形后强度与伸长率得到同步提升,尤其是5道次变形后伸长率提高显著,这与细小第二相在中低角晶界上动态析出密切相关。
REFERENCES
[1] 吴国华, 肖 寒, 周慧子, 王瑞雪, 程 明, 张士宏. 挤压态AZ31镁合金温热拉伸性能的各向异性[J]. 中国有色金属学报, 2017, 27(1): 57-63.
WU Guo-hua, XIAO Han, ZHOU Hui-zi, WANG Rui-xue, CHEN Ming, ZHANG Shi-hong. Anisotropy of warm- temperature tensile properties of extruded AZ31 magnesium alloy[J]. The Chinese Journal of Nonferrous Metals, 2017, 27(1): 57-63.
[2] THIRUMURUGAN M, KUMARAN S. Extrusion and precipitation hardening behavior of AZ91 magnesium alloy[J]. The Chinese Journal of Nonferrous Metals, 2013, 23(6): 1595-1601.
[3] 余 琨, 黎文献, 王日初, 马正青. 变形镁合金的研究, 开发及应用[J]. 中国有色金属学报, 2003, 13(2): 277-288.
YU Kun, LI Wen-xian, WANG Ru-chu, MA Zheng-qing. Research, development and application of wrought magnesium alloys[J]. The Chinese Journal of Nonferrous Metals, 2003, 13(2): 277-288.
[4] 张笃秀, 李 祎, 叶友雄, 沈阳志, 杨续跃. 微量Fe对冷轧超细晶Cu-30Zn-0.15Fe合金等温退火组织演化的影响[J]. 金属学报, 2016, 52(3): 369-377.
ZHANG Du-xiu, LI Yi, YE You-xiong, XHEN Yang-zhi, YANG Xu-yue. Effect of minor Fe addition on microstructure evolution of ultrafine grained cold rolling Cu-30Zn-0.15Fe alloy subjected to isothermal annealing[J]. Acta Metall Sin, 2016, 52(3): 369-377.
[5] MILITZER M, SUN W P, JONAS J J. Modelling the effect of deformation-induced vacancies on segregation and precipitation[J]. Acta Metall, 1994, 42(1): 133-141.
[6] ZHAO S T, MENG C L, MAO F X, HU W, GOTTSTEIN G. Influence of severe plastic deformation on dynamic strain aging of untrafine grained Al-Mg alloys[J]. Acta Mater, 2014, 76(2): 54-67.
[7] 刘六法, 丁汉林, 丁文江. AZ91镁合金挤压过程中β相的动态析出及其对组织和拉伸性能的影响[J]. 稀有金属材料与工程, 2009, 38(1): 104-109.
LIU Liu-fa, DING Han-ling, DING Wen-jiang. Dynamic precipitation of β phase during extrusion process and its effects on the microstructures and tensile properties of AZ91 magnesium alloy[J]. Rare Metal Materials and Engineering, 2009, 38(1): 104-109.
[8] 王红霞, 周康康, 梁 伟, 龚家林, 曹晓卿, 赵兴国. Mg15Al镁合金ECAP变形过程中β相的碎化机理及动态析出行为[J]. 中国有色金属学报, 2011, 21(9): 1794-1800.
WANG Hong-xia, ZHOU Kang-kang, LIANG Wei, GONG Jia-lin, CAO Xiao-qing, ZHAO Xing-guo. Fragmentation mechanism and dynamic precipitation behavior of β phase in Mg15Al magnesium alloy during ECAP[J]. The Chinese Journal of Nonferrous Metals, 2011, 21(9): 1794-1800.
[9] GUO F, ZHANG D F, YANG X S, JIANG L Y, PAN F S. Strain-induced precipitation of Mg17Al12 phase in Mg-8Al alloys sheets rolled at 748 K[J]. Mater Sci Eng A, 2015, 636: 516-521.
[10] 杨续跃, 孙 欢, 吴新星, 马继军, 秦 佳, 霍庆欢. AZ21镁合金降温多向压缩过程中的组织和微观织构演化[J]. 金属学报, 2012, 48(1): 129-134.
YANG Xu-yue, SUN Huan, WU Xin-xing, MA Ji-jun, QIN Jia, HUO Qing-huan. Evolutions of microstructure and microtexture in AZ21 Mg alloy during multi-directional forging under decreasing temperature conditions[J]. Acta Metall Sin, 2012, 48(1): 129-134.
[11] YANG X Y, SUN Z Y, XING J, HIROMI M, TAKU S. Grain size and texture changes of magnesium alloy AZ31 during multi-directional forging[J]. The Chinese Journal of Nonferrous Metals, 2008, 18(2): 200-204.
[12] MIURA H, YU G, YANG X. Multi-directional forging of AZ61 Mg alloy under decreasing temperature conditions and improvement of its mechanical properties[J]. Mater Sci Eng A, 2011, 528: 6981-6992.
[13] JIANG M G, YAN H, CHEN R S. Twinning, recrystallization and texture development during multi-directional impact forging in an AZ61 Mg alloy[J]. J Alloys Compd, 2015, 650: 399-409.
[14] SOMJEET B, SATYAM S. Evolution of sub-micron grain size and weak texture in magnesium alloy Mg-3Al-0.4Mn by a modified multi-axial forging process[J]. Scr Mater, 2012, 66(2): 89-92.
[15] MIURA H, YANG X, SAKAI T. Evolution of ultra-fine grains in AZ31 and AZ61 Mg alloys during multi-directional forging and their properties[J]. Mater Trans, 2008, 49(5): 1015-1020.
[16] YU H, PARK S H, YOU B S. Development of extraoridinary high-strength Mg-8Al-0.5Zn alloy via a low temperature and slow speed extrusion[J]. Mater Sci Eng A, 2014, 610: 445-449.
[17] YANG X Y, MIURA H, SAKAI T. Dynamic evolution of new grains in magnesium alloy AZ31 during hot deformation[J]. Mater Trans, 2003, 44(1): 197-203.
[18] 杨续跃, 姜育培. 镁合金热变形下变形带的形貌和晶体学特征[J]. 金属学报, 2010, 46(4): 451-457.
YANG Xu-yue, JIANG Yu-pei. Morphology and crystallographic characteristics of deformation bands in Mg alloy under hot deformation[J]. Acta Metall Sin, 2010, 46(4): 451-457.
[19] CLARK J B. Age hardening in Mg-9wt.% Al alloy[J]. Acta Metall, 1968, 16(2): 141-152.
[20] MATHIS K, GUBICZA J, NAM N H. Microstructure and mechanical behavior of AZ91 Mg alloy processed by equal channel angular pressing[J]. J Alloys Compd, 2005, 394: 194-199.
[21] CACERES C H, ROVERA D M. Solid solution strengthening in concentrated Mg-Al alloys[J]. J Light Met, 2001, 1(3): 151-156.
[22] HUTCHINSON C R, NIE J F, GORSSE S. Modeling the precipitation processes and strengthening mechanisms in a Mg-Al-(Zn) AZ91 alloy[J]. Metall Mater Trans A, 2004, 36(8): 2093-2015.
[23] YE Y X, YANG X Y, LIU C Z, SHEN Y Z, ZHANG X K, SAKAI T. Enhancement of strength and ductility of Cu-Sn-Zn alloy by iron addition[J]. Mater Sci Eng A, 2014, 612: 246-252.
[24] YANG Qiang, BU Fan-qiang, QIU Xin, LI Yang-de, LI Wei-rong, SUN Wei, LIU Xiao-juan, MENG Jiang. Strengthening effect of nano-scale precipitates in a die-cast Mg-4Al-5.6Sm-0.3Mn alloy[J]. J Alloys Compd, 2016, 665: 240-250.
Dynamic precipitation and its effect on grain refinement and mechanical properties in AZ61 Mg alloy during multi-directional forging under decreasing temperature conditions
FANG Zheng-wu1, XIAO Zhen-yu1, ZHANG Du-xiu1, YING Yong1, YANG Xu-yue1, 2, 3
(1. School of Materials Science and Engineering, Central South University, Changsha 410083, China;
2. Nonferrous Metal Oriented Advanced Structural Materials and Manufacturing Cooperative Innovation Center, Central South University, Changsha 410083, China;
3. Key Laboratory of Nonferrous Metal Materials Science and Engineering, Ministry of Education, Central South University, Changsha 410083, China)
Abstract: Dynamic precipitation and its effect on grain refinement and mechanical properties of AZ61 Mg alloy during multi-directional forging in temperature range from 623 K to 483 K were investigated by OM, SEM/EBSD and TEM techniques. Dynamic precipitation of Mg17Al12 phase does happen at the early stage of multi-directional forging and grain size is significantly refined to 0.8 μm after five passes deformation. The initial size of precipitates is relatively big, and then precipitates become dispersed and are refined to nanometer scale. The nanometer dispersed precipitation retards the dislocation movement, along with the temperature decreasing, resulting in the high density of dislocations and low medium angle grain boundaries inside the grain. The strength and ductility of AZ61 Mg alloy are simultaneously improved after multi-directional forging under decreasing temperature. The dramatic improvement of ductility is found after the whole five passes deformation finished, which can be attributed to the dynamic precipitation occurring on the low or medium angle grain boundary.
Key words: magnesium alloy; multi-directional forging; low-medium angle grain boundary; dynamic precipitation
Foundation item: Projects(51474241, 51771230) supported by the National Natural Science Foundation of China; Project(2013CB632204) supported by the National Key Basic Research Program of China; Project (2016WK2018) supported by the Key Research Program of Hunan Province, China
Received date: 2017-01-03; Accepted date: 2017-06-05
Corresponding author: YANG Xu-yue; Tel: +86-13873133470; E-mail: yangxuyue@csu.edu.cn
(编辑 龙怀中)
基金项目:国家自然科学基金资助项目(51474241,51771230);国家重点基础研究发展计划资助项目(2013CB632204);湖南省重点研发项目(2016WK2018)
收稿日期:2017-01-03;修订日期:2017-06-05
通信作者:杨续跃,教授,博士;电话:13873133470;E-mail: yangxuyue@csu.edu.cn