
Oxidation mechanisms of C-SiC-TaC-C composites prepared by
chemical vapor infiltration
CHEN Zhao-ke(陈招科), XIONG Xiang(熊翔), HUANG Bai-yun(黄伯云), LI Guo-dong(李国栋),
XIAO Peng(肖鹏), WANG Ya-lei(王雅雷), WANG Qiong(王琼)
State Key Laboratory of Powder Metallurgy, Central South University, Changsha 410083, China
Received 15 July 2007; accepted 10 September 2007
Abstract: To improve the oxidation-resistance properties, SiC and TaC species were introduced in C/C composites by chemical vapor infiltration (CVI) methods. The oxidation-resistance properties of C-SiC-TaC-C composites were studied by X-Ray diffractometry (XRD), JEOL-6360LV scanning electronic microscopy (SEM) and AdventurerTM electronic balance with precision of 0.1 mg. The results show that, 1) the oxidation rate of the composites increases continuously with time at all experimental temperatures; 2) The oxidation rate increases with temperature within 700-1 100 ℃, slowly in 700-800 ℃, acutely in 800-1 100 ℃; it reaches a maximum value at 1 100 ℃, then decreases within 1 100-1 400 ℃; 3) The relationship curve of oxidation rate with temperature can be divided into three regions. The oxidation rate is controlled by reactivity in region Ⅰ, the mixed effects of reactivity and gas diffusion in region Ⅱ, gas phase diffusion in region Ⅲ; 4) The composites exhibit a higher oxidation onset temperature in low temperature region and a lower oxidation rate at high temperature due to the oxidation of TaC to (Ta, O) and the formation of the dense SiO2-Ta2O5 oxide layer respectively. With the addition of SiC/TaC species, the oxidation-resistant properties of C/C composites can be improved effectively.
Key words: C/C composites; TaC; chemical vapor infiltration; oxidation-resistance
1 Introduction
As aerospace technology develops continuously, there is a rapidly increasing demand for advanced materials with temperature capability of over 1 700 ℃ for ultra high temperature and aerospace applications, such as rocket engines and thermal protection systems for space vehicles [1-2]. Carbon-carbon (C/C) composites are leading candidates for ultra high temperature structural applications due to dimensional stability, high strength and modulus at high temperature, low coefficient of thermal expansion (CTE), high thermal conductivity and shock resistance, ease of machining and low density [3]. However, the use of carbon materials for high temperature application is limited due to their susceptibility to oxidation in air at temperature as low as 400 ℃[4]. Efforts have been made to inhibit the oxidation of carbon materials by coating C/C with refractory oxides, carbides[5] or by doping with boron and phosphorous compounds[6-7]. The former method has disadvantage of cracks in the protective coating due to mismatch of CTE between substrate and the coating material, while the doping technique can provide protection from oxidation only up to 700 ℃.
According to the results in Refs.[8-10], the oxidation of C/C composites first takes place at the fiber/matrix interface. Therefore, some materials must be introduced as a fiber coating or inhibitors to protect the interface from oxidation. However, little work was done to fiber coatings as a method of internal oxidation protection.
The characteristics of the fiber coating, which are necessary to protect C/C composites from internal oxidation efficiently, are as follows[8-10]: 1) be stable at 1 100 ℃ under low pressures (chemical vapor infiltration conditions); 2) can resist reaction with carbon fibers; 3) can oxidize faster than carbon and 4) can oxidize with a volume gain to prevent oxygen access to the interfacial zones. Previous results show that SiC is very efficient as external coating to protect C/C composites below 1 600 ℃[11], while refractory metal carbides are candidates for oxidation-resistant materials of C/C composites at ultra high temperature field[12-16]. To improve the oxidation-resistance properties of C/C composites, SiC and TaC species were introduced as interphases by chemical vapor infiltration (CVI) methods. And the oxidation behavior of C-SiC-TaC-C composites at 700- 1 400 ℃ were studied
2 Experimental
The preparation process of C-SiC-TaC-C composites is shown in Fig.1.
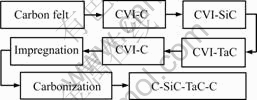
Fig.1 Preparation process of C-SiC-TaC-C composites
2.5 D PAN carbon fibers needle-punctured felt with original density of 0.56 g/cm3 was used as preforms. In order to reduce the damage of SiC or TaC ceramic coating to carbon fiber, a pyrolytic carbon layer was firstly deposited on carbon fiber as an interface material by CVI with N2-H2-C3H6 system. When the density of the preform reached 0.62 g/cm3, SiC and TaC interphases (or fiber coatings) were introduced in C/C composites successively by CVI methods with Ar-H2-CH3SiCl3 and Ar-C3H6-TaCl5 systems respectively. Then preforms were further densified with pyrocarbon (by CVI) and resin carbon (by impregnation and carbonization with 2-3 circles) to obtain composites finally. The densities of composites after each step of process and volume fraction of SiC and TaC are listed in Table 1.
All oxidation experiments are performed in natural convection air in an Al2O3 corundum tube (heated by MoSi2). The C-SiC-TaC-C composites with size of 10 mm×10 mm×4 mm were subjected to a series of five thermal cycles in air between oxidation temperature (700-1 400 ℃) and room temperature (25 ℃). The heating rates are about 300 ℃/s while cooling rates of sample are about 200 ℃/min. The oxidation time of each thermal cycle is 2, 3, 5, 10, 40 min. In these oxidation experiments, each sample was held at oxidation temperature for a total of 60 min. After oxidation, the macro shape of each sample was not destroyed and the composites were not noticeably affected by the thermal cycling.
The mass change of sample during oxidation process was measured using an AdventurerTM electronic balance with a precision of 0.1 mg. Phase composition of sample before and after oxidation was examined by a D/max 2550VB+18 kW rotating target XRD spectroscopy. Microstructure was analyzed by a JEOL-6360LV scanning electron microscopy (SEM).
3 Results and discussion
3.1 Oxidation rate
The oxidation rates were determined by calculating the mass loss per square centimeter of composites. The results are shown in Fig.2. The mass loss of the composites increases continuously with time at all temperatures. At relatively low temperature of 700 ℃ and 800 ℃ after 60 min, little mass losses of 4.7 mg/cm2 and 7.3 mg/cm2 are observed; while at 900 ℃, mass loss of 40.6 mg/cm2 was obtained. This suggests that the preliminary oxidation temperature of composites is improved to 900 ℃. In addition, the relationship between the mass loss and time is nearly linear under 700-800 ℃, parabolic with positive constant between 900-1 200 ℃,and finally parabolic with negative constant at 1 300- 1 400 ℃. The shape change of relationship curve indicates that the oxidation mechanism is changed with temperature.
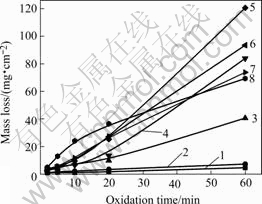
Fig.2 Mass loss of composites as function of oxidation time at 700-1 400 ℃: 1—700 ℃; 2—800 ℃; 3—900 ℃; 4—1 000 ℃; 5—1 100 ℃; 6—1 200 ℃; 7—1 300 ℃; 8—1 400 ℃
Table 1 Densities of composites after each step and volume fraction of SiC and TaC

The final mass loss of samples being oxidized for 60 min is plotted as function of temperature, as shown in Fig.3. The oxidation rate increases with temperature within 700-1 100 ℃, slowly from 4.7 mg/cm2 to 7.3 mg/cm2 in 700-800 ℃, acutely from 7.3 mg/cm2 to 120.7 mg/cm2 in 800-1 100 ℃; it reaches a maximum value of 120.7 mg/cm2 at 1 100 ℃, then decreases within 1 100-1 400 ℃; at 1 400 ℃ it is 69.4 mg/cm2.
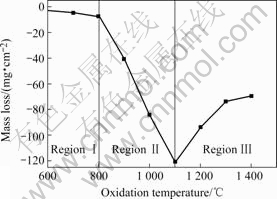
Fig.3 Oxidation rate curve of composites as function of temperature
As can be seen from Fig.3, the oxidation rates curve can be divided into three temperature regions. Region Ⅰ (low temperature zone at 700-800 ℃), Region Ⅱ(intermediate temperature zone at 800-1 100 ℃), and Region Ⅲ (high temperature zone above 1 100 ℃).
3.2 Oxidation mechanism
Compared with the oxidation of C/C composites[17], the composites exhibit a higher oxidation onset temperature in low temperature region and a lower oxidation rate at high temperature. In this case, the rate-limiting steps might involve diffusion across a boundary layer, diffusion through microcracks, diffusion through pores, diffusion through TaC, SiC interphases and chemical reactions. When reaction occurs, the step with the slowest rate will be the rate-limiting step. Based on this concept, detailed analyses of the oxidation mechanisms of C-SiC-TaC-C composites have been conducted with phase composition and microstructure of composites after oxidization.
A representative phase composition of composites before and after oxidation is listed in Table 2.
Phases enclosed by TaC, SiC interphase is not oxidized below 1 000 ℃. However, TaC interphase come into being at 700 ℃ and form (Ta, O) phases. The oxidation of TaC to (Ta, O) phase is a mass gain process,
Table 2 Phase constitution of composites before and after oxidation at different temperatures
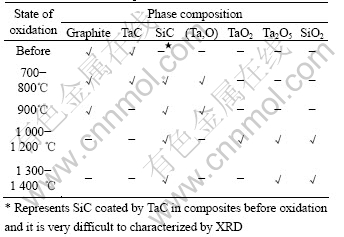
which can offset the mass loss of oxidation of C. This may be the main reason for the little mass loss of composites at low temperature. At 900 ℃, TaC interphase is oxidized completely (no TaC phase is found), but the oxidation of C phase is so faster that the mass loss can not be offset anymore. Therefore, the composites show an obvious mass loss after oxidation. Within 1 000-1 200 ℃, liquid SiO2 is formed, and TaC also turns to TaO2 and fluid Ta2O5 phases. TaO2 is not stabilized and can react with O2 to form Ta2O5 at increased temperature (1 300-1 400 ℃). The formation of liquid phases of SiO2 and Ta2O5 is contributed to the improvement of oxidation-resistance properties at high temperatures.
Microstructures of composites after oxidation at different temperatures are shown in Fig.4.
At 700-800 ℃, although the oxidation of TaC can offset the mass loss of composites, the deposits are oxidized slower than carbon. Oxidation progresses along with the carbon fibers and carbon matrices. As can be seen from Fig.4 (a), holes are formed at carbon fibers and carbon matrix. This gives an easy access of oxygen to the center of the composites. SiC-TaC interphases can not protect C/C composites from oxidation at low temperature.
At 900-1 100 ℃, TaC interphase is oxidized rapidly and form a porous (Ta, O) phase, while SiC is not completely oxidized. The oxidation of ceramic coating can not protect carbon phase from oxidation at outer zones of composites (see Fig.4(b)), however, O2 is exhausted rapidly by the oxidation of ceramic coating and can not diffuse to the center of composites. In Fig.4(c), it can be seen that the SiC-TaC interphases in the composites keep intact and are not oxidized.
Above 1 100 ℃, the TaC and SiC interphases are both completely oxidized and form Ta2O5 and SiO2 glass phases. In Fig.4(d), it can be seen that the glass phases enclose and seal the holes formed by the oxidation of carbon fiber. This layer effectively reduces the exposed surface and retards the oxidation of the composites. With the increase of temperature, more Ta2O5 and SiO2 are formed and less mass loss is obtained. However, the mass loss of composites with time is still observed up to 1 400 ℃, which indicates that pores are narrowed, but does not close up completely by liquid phases.
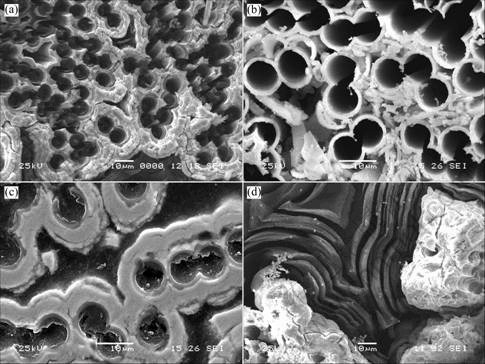
Fig.4 Microstructures of composites after oxidation at different temperatures: (a) 700-800 ℃; (b) 900-1 100 ℃, outer part of composites; (c) 900-1 100 ℃, inner part of composites; (d) 1 200-1 400 ℃
From the results of phase constitution and microstructure analyses of C-SiC-TaC-C composites oxidized at different temperatures, it can be concluded that the oxidation rate is controlled solely by the chemical reactivity of the solid in the low temperature region (Region Ⅰ), by the mixed effects of oxygen transported from the outer surface into the composites and the reaction of solids in the intermediate temperature region (Region II); by an obvious controlling mechanism of diffusion at temperatures up to 1 100 ℃ (Region Ⅲ). With the addition of SiC and TaC species, the oxidation-resistant properties of C/C composites can be improved effectively.
4 Conclusions
1) The oxidation rate of the composites increases continuously with time at all experimental temperatures.
2) The oxidation rate increases with temperature within 700-1 100 ℃, slowly from 4.7 mg/cm2 to 7.3 mg/cm2 in 700-800 ℃, acutely from 7.3 mg/cm2 to 120.7 mg/cm2 in 800-1 100 ℃; it reaches a maximum value of 120.7 mg/cm2 at 1 100 ℃; then decreases within 1 100-1 400 ℃; at 1 400 ℃ it is 69.4 mg/cm2.
3) The relationship curve of oxidation rate with temperature can be divided into three regions. The oxidation rate is controlled by reactivity in region Ⅰ, the mixed effects of reactivity and gas diffusion in region Ⅱ, gas phase diffusion in region Ⅲ.
4) The composites exhibit a higher oxidation onset temperature in low temperature region and a lower oxidation rate at high temperature due to the oxidation of TaC to (Ta, O) and the formation of the dense SiO2-Ta2O5 oxide layer respectively. With the addition of SiC and TaC species, the oxidation-resistant properties of C/C composites can be improved effectively.
References
[1] BANERJEE D. Structural materials in aerospace systems: Materials challenges for the next century[EB/OL]. [2007]. http://mrs.org/ publications/bulletin.
[2] RAMAN V, BHATIA G, MISHRA A, SENGUPTA P R, SAHA M, RASHMI. Development of carbon-ceramic composites[J]. Materials Science and Engineering A, 2005, 412(1/2): 31-36.
[3] VIRGIL’EV Y S, KALYAGINA I P. Carbon-carbon composite materials[J]. Inorganic Materials, 2004, 40(Suppl. 1): S33-S49.
[4] MANOCHA L M, MANOCHA S, PATEL K B, GLOGAR P. Oxidation behaviour of carbon/carbon composites impregnated with silica and silicon oxycarbide[J]. Carbon, 2000, 38(10): 1481-1491.
[5] WUNDER V, POPOVSKA N, WEGNER A, EMIG G., ARNOLD A. Multilayer coatings on CFC composites for high-temperature applications [J]. Surface and Coating Technology, 1998, 100-101(1/3): 329-332.
[6] ZHU Y C, OHTANI S, SATO Y, IWAMOTO N. Influence of boron ion implantation on the oxidation behavior of CVD-SiC coated carbon-carbon composites[J]. Carbon, 2000, 38(4): 501-507.
[7] CAIRO C A A, FLORIAN M, GRA?A M L A, BRESSIANI J C. Kinetic study by TGA of the effect of oxidation inhibitors for carbon/carbon composite[J]. Materials Science and Engineering A, 2003, 358(1/2): 298-303.
[8] NASLAIN R, GUETTE A, REBILLAT F, PAILLER R, LANGLAIS F, BOURRAT X. Boron-bearing species in ceramic matrix composites for long-term aerospace applications[J]. Journal of Solid State Chemistry, 2004, 177(2): 449-456.
[9] LABRUQU?RE S, BLANCHARD H, PAILLER R, NASLAIN R. Enhancement of the oxidation resistance of interfacial area in C/C composites. Part Ⅱ: oxidation resistance of B-C, Si-B-C and Si-C coated carbon preforms densified with carbon[J]. Journal of the European Ceramic Society, 2002, 22(7): 1011-1021.
[10] LABRUQU?RE S, PAILLER R, GUETTE A, NASLAIN R. Internal protection of C/C composites by boron-based compounds[J]. Journal of the European Ceramic Society, 2002, 22(7): 987-999.
[11] ZHU Q S, QIU X L, MA C W. Oxidation resistant SiC coating for graphite materials[J]. Carbon, 1999, 37(9): 1475-1484.
[12] SAYIR A. Carbon fiber reinforced hafnium carbide[J]. Journal of Materials Science, 2004, 39(19): 5995-6003.
[13] POPOVSKA N, GERHARD H, WURM D, POSCHER S, EMIG G, SINGER R F. Chemical vapor deposition of titanium nitride on carbon fibres as a protective layer in metal matrix composites [J]. Materials & Design, 1997, 18(4/6): 239-242.
[14] CHEN Z K, XIONG X, XIAO P, LI G D, ZHANG H B, HUANG B Y. Research of Cf/TaC composites prepared by low temperature chemical vapor infiltration (CVI) process[J]. Journal of Inorganic Materials, 2007, 22(2): 1195-1200. (in Chinese)
[15] LI Guo-dong, XIONG Xiang, HUANG Bai-yun. Effect of temperature on composition, surface morphology and microstructure of CVD-TaC coating[J]. The Chinese Journal of Nonferrous Metals, 2005, 15(4): 565-571. (in Chinese)
[16] LI Guo-dong, XIONG Xiang, HUANG Bai-yun. Microstructure characteristic and formation mechanism of crackfree TaC coating on C/C composite[J]. Trans Nonferrous Met Soc China, 2005, 15(6): 1206-1213.
[17] LUO R Y, CHENG J W, WANG T M. Oxidation behavior and protection of carbon/carbon composites prepared using rapid directional diffused CVI techniques[J]. Carbon, 2002, 40(11): 1965-1972.
Foundation item: Project (2006CB600908) supported by National Basic Research Program of China
Corresponding author: XIONG Xiang; Tel: +86-731-8836864; E-mail: Xiong228@sina.com; pallettechen@163.com
(Edited by CHEN Can-hua)