
J. Cent. South Univ. (2018) 25: 754-763
DOI: https://doi.org/10.1007/s11771-018-3780-1

Effect of additives on anode passivation in direct electrolysis process of copper–nickel based alloy scraps
LI Lei(李磊), LI Hong-juan(李红娟), QIU Shi-wei(邱士伟), WANG Hua(王华)
State Key Laboratory of Complex Non-ferrous Metal Resources Clean Utilization, Engineering Research Center of Metallurgical Energy Conservation and Emission Reduction of Ministry of Education, Faculty of Metallurgical and Energy Engineering, Kunming University of Science and Technology, Kunming 650093, China
Central South University Press and Springer-Verlag GmbH Germany, part of Springer Nature 2018
Abstract: Effects of nickel component, thiourea, glue and chloride ions and their interactions on the passivation of copper–nickel based alloy scrap anodes were investigated by combining conventional electrochemical techniques. Results obtained from chronopotentiometry and linear voltammetry curves showed that the Ni component made electrochemical stability of the anode strong and difficult to be corroded, caused by the adsorption of generated Cu2O, NiO or copper powder to the anode surface. The Ni2+ reducing Cu2+ to Cu+ or copper powder aggravated the anode passivation. In a certain range of the glue concentration ≤8×10–6 or thiourea concentration ≤4×10–6, the increase of glue or thiourea concentration increases the anode passivation time. Over this range, glue and thiourea played an adverse effect. The increase of chloride ions concentration led to the increase in passivation time.
Key words: copper–nickel based alloy scrap; direct electrolysis; nickel component; anode passivation; additive
Cite this article as: LI Lei, LI Hong-juan, QIU Shi-wei, WANG Hua. Effect of additives on anode passivation in direct electrolysis process of copper-nickel based alloy scraps [J]. Journal of Central South University, 2018, 25(4): 754–763. DOI: https://doi.org/10.1007/s11771-018-3780-1.
1 Introduction
Copper-based alloys are widely used in different industries such as electric, building materials, and mechanical industry because of their good electrical conductivity, high strength, and corrosion resistance [1–3]. With the increasing concurrent requirement of copper-based alloys, an increasing emphasis has been placed on the recovery of copper and nickel from the secondary sources [4, 5]. Various secondary sources and wastes containing copper-based alloy scraps are generated in industries, waste residues of electric arc furnace, and automobile shredder etc [6]. These wastes represent currently a serious resource of valuable materials, but also a requirement of environmental protection [7].
There are many studies about the separating and recovering treatment of nickel and copper from some copper-based alloy scraps through conventional pyrometallurgical or hydrometallurgical process. Currently, most of the waste is recycled pyrometallurgically in the copper smelters [7, 8], where the scraps are used as a part of copper concentrate batch. The equipment used in pyrometallurgical process always includes reverberatory furnace, fuming furnace and converter. However, the associated elements are hard to be recycled. Hydrometallurgical treatment of waste materials is proposed as an alternative low-cost and more environmental friendly technology [9, 10]. However, it has drawbacks such as complex processes, high consumption of chemical reagents, high cost in operation and secondary environmental pollution. In addition, leaching and extraction- electrowinning processes are inevitable for obtaining pure copper or nickel in the process of traditional hydrometallurgical treatment, which causes energy consumption increase. Biological leaching of metals using bacteria or fungi as a cost effective method was also studied recently in a laboratory scale [11]. WANG et al [12] reported that the separation of copper from copper–nickel based alloy scraps (90% Cu, 9% Ni) using a direct electrolysis method was feasible, in which the alloy scraps were used as anode and the copper was recovered in the form of pure copper. It solves the problem of high energy consumption and long flow path for recovering copper from copper–nickel based alloy scraps. The impurities in the anode, especially noticeable amounts of Ni, affect the anode passivation seriously. However, few studies researched the anodic passivation phenomenon during the direct electrolysis process of copper– nickel based alloy scraps.
The anode passivation has received increasing attention and the factors influencing it have been extensively studied. The electrolyte composition, current density, thermal treatment and temperature play important roles in passivation phenomenon [13–16], and ABE et al [17] concluded that passivation time decreased with nickel contents for the formation of nickel sulfate. In addition, several recent studies have focused on effects of additives on passivation in a laboratory scale [13, 18]. This paper focuses on the anodic passivation phenomenon during the direct electrolysis process of copper–nickel based alloy scraps, which do not contain noticeable amounts like Se, Bi, and As etc. Some experiments were carried out to detect effects of additives and their interactions on the passivation of the anode. In this work, linear voltammetry and chronopotentiometry were employed to investigate the passivation effect.
2 Experimental
2.1 Materials and methods
Mixtures of copper–nickel based alloy scraps from a mechanical industry were collected, and then were cut into rectangular samples (2 cm×4 cm). A synthetic electrolyte was utilized for all electrochemical tests, and it was prepared by using sulfuric acid (Analytically pure), copper sulfate (analytically pure) and deionized water. The additives (glue and thiourea) were supplied by the Yunnan Copper Complex, China. Chloride ions were added in the form of hydrochloric acid (analytically pure). An electrolyte composition of 50 g/L Cu2+ (0.79 mol/L) and 160 g/L H2SO4(1.63 mol/L) was used at a temperature of 50 °C. Glue and thiourea were added just prior to heating the electrolyte. The electrolyte was heated by a flow of thermostated water in the double wall of a cell, and was magnetically stirred at 80 r/min during the experiments.
Chronopotentiogram and linear voltammetry curves were performed with Princeton 2273 electrochemical workstation using a three-electrode system. In the electrode system, the copper–nickel based alloy scraps were used as the working electrode (Rectangular, 2 cm×4 cm), copper electrode as the counter electrode, and saturated calomel electrode (SCE 0.24V versus SHE) as the reference electrode. Exposed areas of 1 cm2 of working electrode surface and 10 cm2 of counter electrode surface were ground using abrasive papers through 400–1000 grades, rinsed using acetone, degreased with de-ionized water and dried in air. The distance of working and counter electrodes was fixed at 2 cm. Table 1 gives main chemical compositions of three kinds of copper–nickel based alloy scraps analyzed by titrimetric method and ICP-AES.
Table 1 Chemical compositions of copper-nickel based alloy scraps used in experiments
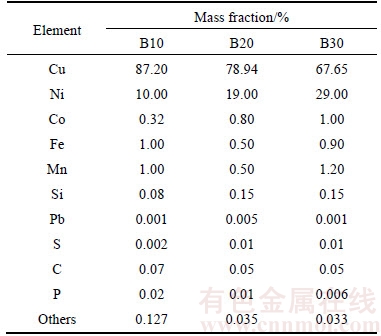
2.2 Instrumentation
Chronopotentiometry and linear voltammetry curves were used to research the effects of Ni component and additives on the passivation response during anodic dissolution. Based on previous works by other researchers [13], a constant current density of 4800 A/m2 was applied in the experiments. The surface morphology and elemental composition of the electrolytic product were examined using scanning electron microscope (SEM, Philip-XL30ESEM) together with energy dispersive X-ray (EDX) analysis.
3 Results and discussion
3.1 Effect of Ni content of anodes
No additives were added to the electrolyte in this series of experiments. Effects of Ni content on linear voltammetry curves are given in Figure 1, where B10, B20 and B30 are represented by three kinds of anodes (Table 1), respectively. With Ni content of the anode increasing, a shift toward a more positive potential takes place in the anodic peak (A). The ascending current peak OA in the anodic branch from a stationary potential to the peak potential is due to the formation of Cu2O (Cu+) and NiO (Ni2+). On the descending part of the anodic branch AB, a shoulder appears due to the formation of CuO (Cu2+) from the reaction of Cu2O (Cu+) and H2O. The second ascending BD part in the anodic branch is associated with the formation of CuSO4 and NiSO4 by Reactions (1) and (2) [19].
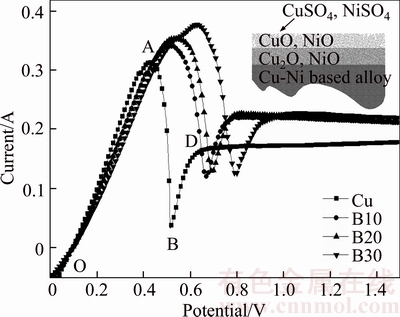
Figure 1 Linear voltammetry curves of pure copper and different copper–nickel-based alloy scrap anodes in electrolyte
CuO+H2SO4→CuSO4+H2O (1)
NiO+H2SO4→NiSO4+H2O (2)
A more positive peak potential as seen in Figure 1 is an indication that the Ni component makes electrochemical stability of the anode stronger and more difficult to be corroded. The reason could be ascribed to the more formation of NiO, Cu2O (Reaction (3)) and copper powder (Reaction (4)) with the increase of Ni content [13, 19–21], and they cover the anode surface as a layer of anodic slime (Figure 2) and hinder the diffusion of copper ions. Thus, the anode potential increases and more cuprous ions could be formed. As a result, the slime layer thickens rapidly and forms a barrier hindering the cupric ions diffusing into the bulk electrolyte. This leads to the precipitation of copper sulphate crystals on the anode and further to the formation of cuprous oxide, and finally to the anode passivation.
2CuO(2Cu2+)+2NiO(Ni2+)=Cu2O(2Cu+)+Ni2O3(2Ni3+) (3)
CuO(Cu2+)+2NiO(Ni2+)=Cu(powder)(Cu0)+Ni2O3(2Ni3+) (4)

Figure 2 SEM image of surface of B20 anode passivated for 600 s
LAFRONTA et al [15] also reported that the dissolution of copper occurred by passing through two mono-electron transfers (Reactions (5) and (6)):
Cu→Cu++e (5)
Cu+→Cu2++e (6)
Consequently, the concentration of Cu+ increases near the anode surface and the disproportionation of these ions (Reaction. (7)) produces copper powder and Cu2+ ions [13, 21]:
2Cu+(sol)→Cu2+(sol)+Cu0 (7)
The generated copper powder can make a diffusion barrier for the copper ions. Figure 3 shows chronopotentiograms of different tested anodes in electrolyte. The chronopotentiogram for pure copper shows a potential jump from the 1020th second indicating passivation of the anode, which is caused by the generation of copper powder and Cu2O [13]. Nickel contents in excess of 0.3wt% will result in the formation of NiO upon anode solidification, and it does not dissolve in the electrolyte and ends up in the anode slimes [19]. The slimes will either settle to the bottom of the cell or remain attached to the anode forming a relatively thick porous layer, and the attached slimes will make a diffusion barrier for the copper ions, causing passivation time of the anode decreases with Ni content (Figure 3). In addition, more copper powder or Cu2O could be formed through the reduction of CuO (Cu2+) by NiO (Ni2+) (Reactions (3) and (4)), which also aggravates the anodes passivation.
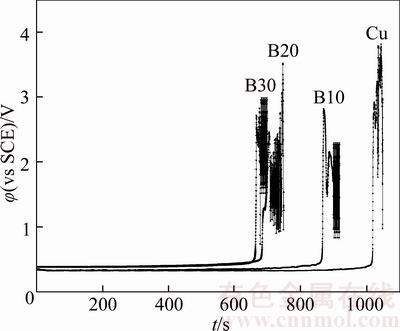
Figure 3 Chronopotentiometry curves of pure copper and different copper–nickel based alloy scrap anodes in electrolyte
3.2 Effect of glue
Detecting effects of additives and their interactions on the passivation of anodes, Ni content of the anode should be set at a fixed value. Any kind of the B10, B20 and B30 anodes could be selected for carrying this study, and the B20 was selected as the material to be researched in this paper.
Figures 4–9 illustrate chronopotentiogram curves of the tested anode in electrolyte containing 0, 2×10–6, 4×10–6, 8×10–6, 16×10–6 and 32×10–6 glue, respectively. Based on the results, the increase of glue concentration from 0 (with no additives) to 8×10–6 leads to increasing in passivation time. Further, the passivation time decreases by increasing glue concentration to ≥8×10–6 level. Figure 10 shows a passivation delay action of glue at a low concentration, and an advance effect at a higher concentration. Glue is an animal protein, which is composed of amino acids. At a low concentration, complexations of Cu+ and Ni2+ ions with amino acids occur [13], and they will weak the occurrence of Reactions (3), (4) and (7), causing formation amounts of Cu2O and copper powder decrease and passivation time increase with glue concentration. However, glue can also be adsorbed on the anode surface at a higher concentration, and the adsorption layer thickens with an increment in the glue concentration and forms a barrier hindering the complexing effect. It accelerates the anode passivation and decreases passivation time. The glue concentration corresponding to the inflection point in Figure 10 is 8×10–6. It is much higher than that of 5×10–6 in the study of ILKHCHI et al [13], in which the working electrode was made of high purity copper. It shows that the nickel component in the anode has a significant effect on the passivation. The increase of nickel content from 0.0084 wt% (Ref. [13]) to 19.00wt% (The B20 in Table 1) leads to an increase of glue consumption through the complexation with Ni2+ and Cu+ generated from the reduction of Cu2+ by Ni2+ (Reaction (3)), and the glue concentration corresponding to the inflection point increases.

Figure 4 Chronopotentiogram of B20 anode in electrolyte with no additives
3.3 Effect of thiourea
Figures 4 and 11–15 illustrate chronopotentiogram curves of the tested B20 anode in electrolyte containing 0, 1×10–6, 2×10–6, 4×10–6,8×10–6 and 16×10–6 thiourea, respectively. It is noticed that the passivation time increases with thiourea concentration from 0 to 4×10–6, and decreases by increasing thiourea concentration to ≥4×10–6 level. It can be seen from Figure 16 that the thiourea appears to have a positive effect at a low concentration and an adverse effect at a higher concentration on the passivation.
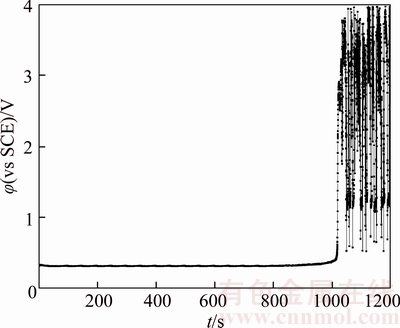
Figure 5 Chronopotentiogram of B20 anode in electrolyte containing 2×10–6 glue
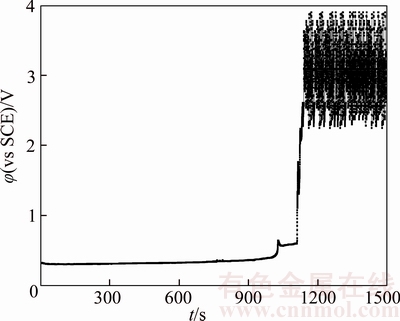
Figure 6 Chronopotentiogram of B20 anode in electrolyte containing 4×10–6 glue
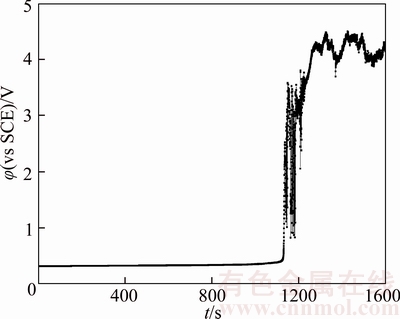
Figure 7 Chronopotentiogram of B20 anode in electrolyte containing 8×10–6 glue
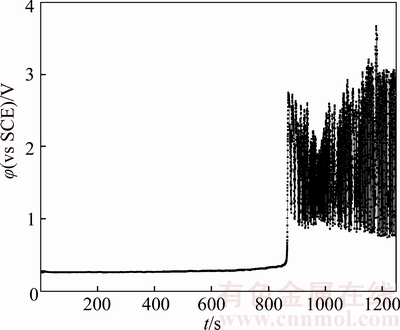
Figure 8 Chronopotentiogram of B20 anode in electrolyte containing 16×10–6 glue
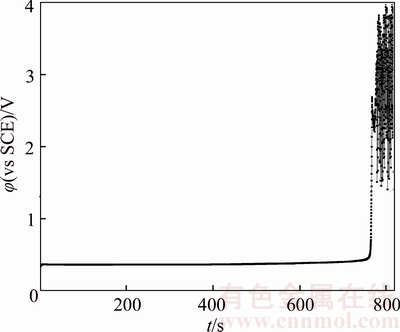
Figure 9 Chronopotentiogram of B20 anode in electrolyte containing 32×10–6 glue
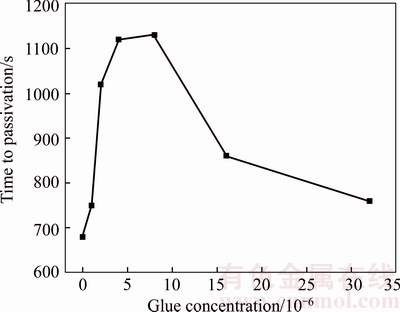
Figure 10 Passivation time of B20 anode against glue concentration
During the process of electrolysis, the thiourea (TU) can be directly oxidized on the electrode surface, and then reacted with electrolyte components (complexation, hydrolysis, and other reactions), in which the generated complexes are mainly in the form of [Cu(TU)4]+ and [Ni(TU)4]2+ [13, 18]. Meanwhile, TU and its decomposition products could be adsorbed on the metallic electrodes surface via theirs sulfur atoms, which consequently affects the interfacial electrochemical process [18]. At a low concentration of thiourea, the complexing effect plays a major role compared to the adsorption, as a result of which concentrations of Cu+ and Ni2+ ions in free forms decrease and their detrimental effects on the anode passivation are decreased (Figure 16). When the thiourea concentration is over 4×10–6 level, the adsorption will appear in advance and the adsorbed compounds will cover the active surface area of the anode, which makes a diffusion barrier for the copper ions and causes the passivation time decrease.
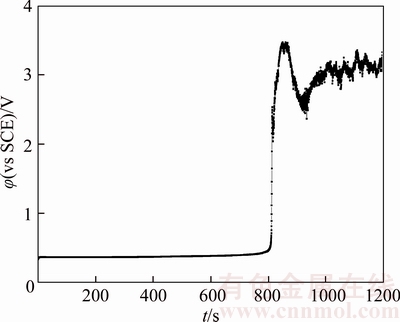
Figure 11 Chronopotentiogram of B20 anode in electrolyte containing 1×10–6 thiourea
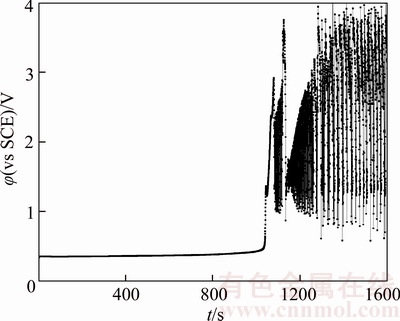
Figure 12 Chronopotentiogram of B20 anode in electrolyte containing 2×10–6 thiourea
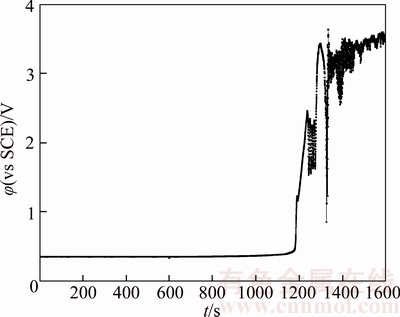
Figure 13 Chronopotentiogram of B20 anode in electrolyte containing 4×10–6 thiourea
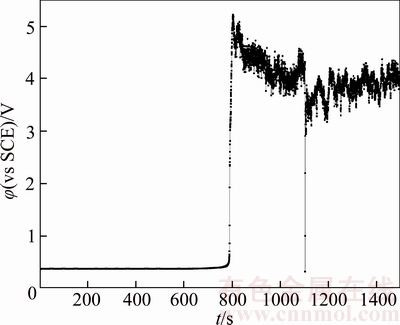
Figure 14 Chronopotentiogram of B20 anode in electrolyte containing 8×10–6 thiourea

Figure 15 Chronopotentiogram of B20 anode in electrolyte containing 16×10–6 thiourea
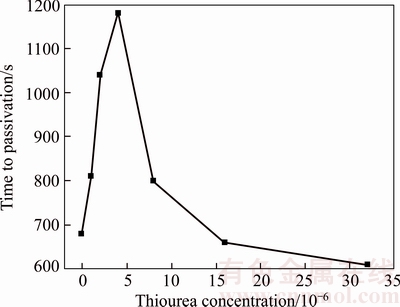
Figure 16 Passivation time of B20 anode against thiourea concentration
3.4 Effect of chloride ions
In an acidic solution without chloride ions, the passivation layer mainly contains Cu2O with a certain amount of Ni2+ and Ni3+ [20]. Figures 4 and 17–21 illustrate chronopotentiogram curves of the tested anode in electrolyte containing (0, 20×10–6, 40×10–6, 60×10–6, 80×10–6 and 100×10–6 Cl–, respectively. It is obvious that the passivation time increases with Cl– concentration from Figure 22, meaning the Cl– appears to have a positive effect for the passivation. The mechanism could be ascribed to part of the Cu2O layer dissolves and forms soluble (CuCl2)– complexes through the pitting effect of chloride ions. During the process of the tested anodic electrodissolution, the cations move away from the electrode while cation vacancies travel towards it [20],
CuCu(M)+V′Cu(ox)→CuCu(ox)+VCu(M)+e (8)
NiNi(M)+VCu(M)→NiCu(ox)+2e (9)
where CuCu (M) and NiNi (M) are the cationic sites in the alloy; V′Cu (ox) is the vacancy of copper ions; VCu (M) is the vacancy created by the copper cation in the alloy; CuCu (ox) is a monovalent copper ion site inside the film; NiCu (ox) is the site where nickel divalent cation occupies the vacancy created by copper in the oxide. As time goes on, the external diffusion of nickel ions occurs from the Cu2O passivation layer to the inside of the layer, and the additional cation vacancies will be generated (Figure 23). Because of the solubility of the generated NiCl2 is better than that of (CuCl2)–, nickel ions leave faster from the oxide layer, which in turn generates further vacancies in the layer (Reaction. (10)). As a result, the anodic electrodissolution can be carried further.
NiCuVCu→Ni2+(aq.)+V′Cu(ox) (10)
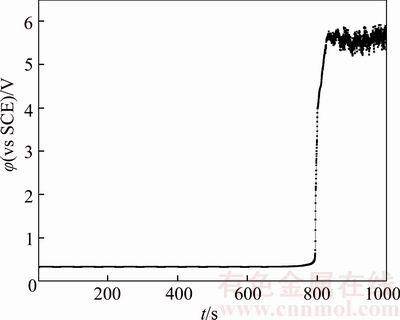
Figure 17 Chronopotentiogram of B20 anode in electrolyte containing 20×10–6 Cl–

Figure 18 Chronopotentiogram of B20 anode in electrolyte containing 40×10–6 Cl–
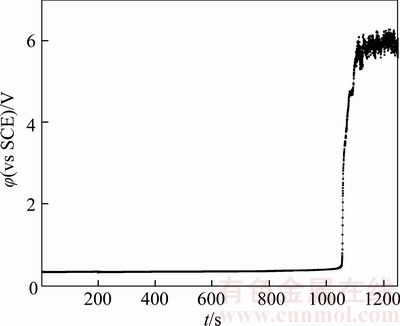
Figure 19 Chronopotentiogram of B20 anode in electrolyte containing 60×10–6 Cl–
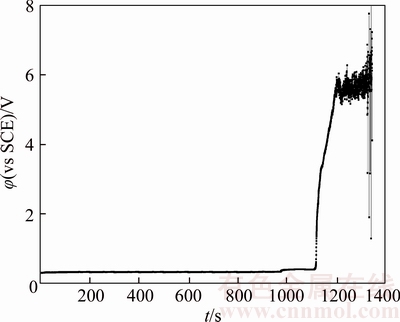
Figure 20 Chronopotentiogram of B20 anode in electrolyte containing 80×10–6 Cl–
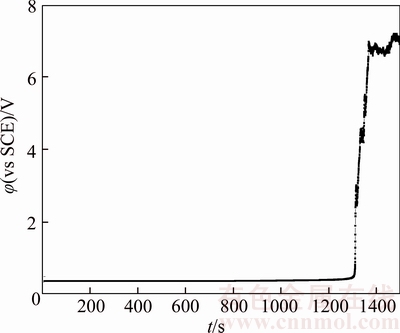
Figure 21 Chronopotentiogram of B20 anode in electrolyte containing 100×10–6 Cl–
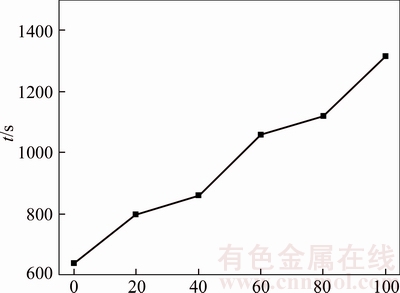
Figure 22 Passivation time of B20 anode against Cl– concentration

Figure 23 Schematic diagram of pitting mechanism of B20 anode by chloride ions
3.5 Effects of simultaneous addition of three different additives
The combined addition of glue, thiourea and chloride ions in the copper electrolyte has become quite usual to obtain a uniform deposit with a high throwing power and a weak roughness. In addition, they have obvious effect on the anode passivation [22]. The chronopotentiogram of the tested anode in the electrolyte containing 4×10–6 glue, 2×10–6 thiourea, and 40×10–6 chloride ions is shown in Figure 24. It is evident that the anode is passivated after 865 s, which shows that there is a delay in the passivation comparing to that of with no additives. By comparing this timeframe with the passivation time in the electrolytes containing equal contents of each additive individually (Figures 6, 12 and 18), it can be seen that the passivation time in Figure 24 is in advance. The reason may be that the addition of chloride ions weakens the effect of thiourea and glue, caused by the formation of a complex compound through the reaction of thiourea and glue with chloride ions [13]. The amino was composed in glue at its molecular structure, and it could be reacted with Cu+ by a complexation [13, 18]. Meanwhile, the thiourea and chloride ions could also be reacted with Cu+ forming [Cu(TU)4]+ and (CuCl2)– respectively. The complexation among thiourea, glue and chloride ions might be carried out through centering at Cu+. After the complex compound being formed, the complexations of thiourea or glue with Cu+ and Ni2+, and the pitting effect of chloride ions, will be hindered. As a result, the passivation time in Figure 24 appears in advance compared with that in Figures 6, 12 and 18.

Figure 24 Chronopotentiogram of B20 anode in electrolyte containing 4×10–6 glue, 2×10–6 thiourea, and 40×10–6 chloride ions
4 Conclusions
Among the studied parameters, it was determined that the Ni component in the anode, glue, thiourea and chloride ions all had profound effects on the anodic passivation during the direct electrolysis process of copper-nickel based alloy scraps.
An increase of Ni content causes passivation time of the anodes decreases, the reason for which could be ascribed to the more formation of NiO, Cu2O and copper powder and they cover the anode surface as layer of anodic slime hindering the diffusion of copper ions. Adding (0–8)×10–6 of glue or (0–4)×10–6 of thiourea to the electrolyte individually increases passivation time of the anode, whereas increasing their concentrations more accelerates the passivation. The chloride ions appear to have a positive effect on the passivation, and the mechanism could be ascribed to part of the Cu2O layer dissolving and forming soluble (CuCl2)– complexes through the pitting effect of it.
References
[1] ZHU An-yi, CHEN Jing-lin, LI Zhou, LUO Li-yang, LEI Qian, ZHANG Liang, ZHANG Wan. Hot deformation behavior of novel imitation-gold copper alloy [J]. Transactions of Nonferrous Metals Society of China, 2013, 23 (5): 1349–1355.
[2] LIU Jun, YANG Shuai, XIA Wei-sheng, JIANG Xin, GUI Chi-bin. Microstructure and wear resistance performance of Cu-Ni-Mn alloy based hardfacing coatings reinforced by WC particles [J]. Journal of Alloys and Compounds, 2016, 654: 63–70.
[3] GORSSE S, OUVRARD B, GOUNE M, POULON- QUINTIN A. Microstructural design of new high conductivity-high strength Cu-based alloy[J]. Journal of Alloys and Compounds, 2015, 633(23): 42–47.
[4] LI Lei, WANG Hua, HU Jian-hang. Smelting chlorination method applied to removal of copper from copper slag [J]. Journal of Central south University, 2015, 22: 59–65.
[5] YANG Hong-ying, MA Zhi-yuan, HUANG Song-tao, LV Yang, XIONG Liu. Intensification of pretreatment and pressure leaching of copper anode slime by microwave radiation [J]. Journal of Central south University, 2015, 22: 4536–4544.
[6] BABA A A, ADEKOLA A F, BALE R B. Development of a combined pyro- and hydro-metallurgical route to treat spent zinc-carbon batteries [J]. Journal of Hazardous Materials, 2009, 171 (1–3): 838–844.
[7] MA Yun-jian, QIU Ke-qiang. Separation and recovery of zinc from copper-based alloy scraps under vacuum conditions [J]. Vacuum, 2014, 106(6): 5–10.
[8] KHALIG A, RHAMDHANI M A, BROOKS G, MASOOD S. Metal extraction process for electronic waste and existing industrial routes: A review and Australian perspective [J]. Resources, 2014, 3(1): 152–179.
[9] TUNCUK A, STAZI V, AKCIL A, YAZICI E Y, DEVECI H. Aqueous metal recovery techniques from e-scrap: Hydrometallurgy in recycling [J]. Minerals Engineering, 2012, 25(1): 28–37.
[10] RUDNIK E, BAYARAA E. Electrochemical dissolution of smelted low-grade electronic scraps in acid sulfate-chloride solutions [J]. Hydrometallurgy, 2016, 159: 110–119.
[11] PANT D, JOSHI D, UPRETI M K, KOTNALA R K. Chemical and biological extraction of metals present in E waste: A hybrid technology [J]. Waste Management, 2012, 32(5): 979–990.
[12] WANG Fei, LI Hong-juan, LI Lei, XIE Xiao-feng, QIU Shi-wei, YU Jun-qiang. Recovery of copper from cupronickel alloy waste by low current density electrolysis [J]. The Chinese Journal of Process Engineering, 2016, 16(2): 266–271. (in Chinese)
[13] ILKHCHI M O, YOOZBASHIZADEH H, SAFARZADEH M S. The effect of additives on anode passivation in electrorefining of copper [J]. Chemical Engineering and Processing, 2007, 46(8): 757–763.
[14] LANZANI G, KANGAS T, LAASONEN K. Copper passivation by metal doping [J]. Journal of Alloys and Compounds, 2009, 482: 33–42.
[15] LAFRONTA A M, SAFIZADEHA F, GHALIA E, HOULACHIB G. Study of the copper anode passivation by electrochemical noise analysis using spectral and wavelet transforms [J]. Electrochemical Acta, 2010, 55(7): 2505–2512.
[16] OWAIS A, GEPREEL M A H, AHMED E. Effect of thermal treatment of copper anodes on electrorefining process [J]. Hydrometallurgy, 2015, 152(3): 55–60.
[17] ABE S, BURROWS B W, ETTEL V A. Anode passivation in copper refining [J]. Canadian Metallurgical Quarterly, 1980, 19(3): 289–296.
[18] JIN S, GHALI E. Effect of some aromatic nitro compounds on the passivation of copper anodes during electrorefining [J]. Journal of Applied Electrochemistry, 1991, 21(3): 247–254.
[19] JARJOURA G, KIPOUROS G J. Cycle voltametric studies of the effect of nickel on copper anode passivation in a copper sulfate solution [J]. Canadian Metallurgical Quarterly, 2013, 44(4): 469–482.
[20] MATHIYARASU J, PALANISWAMY N, MURALIDHARAN V S. Electrochemical behavior of copper-nickel alloy in chloride [J]. Proc Indian Acad Sci (Chem. Sci.), 1999, 111(2): 377–386.
[21] KUCHARAKA-GIZIEWICZ E A, MACKINNON D J. Factors affecting the electrochemical behaviorof copper anodes under simulated electrorefining conditions [J]. Journal of Applied Electrochemistry, 1994, 24: 953–964.
[22] BONOU L, EYRAUD M, DENOYEL R, MASSIANI Y. Influence of additives on Cu electrodeposition mechanisms in acid solution: direct current study supported by non- electro chemical measurements [J]. Electrochemical Acta, 2002, 47(26): 4139–4148.
(Edited by HE Yun-bin)
中文导读
铜镍基合金废料直接电解过程中添加剂对阳极钝化现象的影响
摘要:采用传统电化学技术探讨了镍组分、明胶、硫脲、氯离子及他们交互作用下铜镍基合金废料阳极腐蚀过程中的钝化特征。计时电位曲线和线性伏安曲线表征结果显示阳极中镍组分会增加其自身电化学稳定性使其受腐蚀难度增加,原因是阳极活性表面吸附了生成的Cu2O, NiO或金属Cu粉。同时,Ni2+可将Cu2+还原成Cu+或金属Cu粉,也加剧了阳极钝化过程。一定范围内,明胶浓度≤8×10–6或硫脲浓度≤4×10–6时,增加明胶或硫脲浓度将会延长铜镍基合金废料阳极达到钝化的时间,缓解钝化现象的产生。超过此浓度时,将会促进阳极钝化。提高溶液中氯离子浓度,铜镍基合金废料阳极达到钝化的时间明显延长。
关键词:铜镍基合金废料;直接电解;镍组分;阳极钝化;添加剂
Foundation item: Project(51574135) supported by the National Natural Science Foundation of China; Project(KKPT201563022) supported by the Collaborative Innovation Center of Kunming University of Science and Technology, China
Received date: 2016-09-10; Accepted date: 2016-12-15
Corresponding author: LI Lei, PhD, Professor; Tel: +86–871–65153405; E-mail: tianxiametal1008@163.com; ORCID: 0000-0003- 1205-3989