
Effect of nanoclay on properties of porous PVdF membranes
Hae-Young HWANG1, Deuk-Ju KIM1, Hyung-Jun KIM2, Young-Taik HONG3, Sang-Yong NAM1
1. School of Materials Science and Engineering, Engineering Research Institute, i-Cube Center,
Gyeongsang National University, Jinju 660-701, Korea;
2. Fuel Cell Research Center, Korea Institute of Science and Technology, Seoul 136-791, Korea;
3. Energy Material Research Center, Korea Research Institute of Chemical Technology, Daejeon 305-600, Korea
Received 21 April 2010; accepted 10 September 2010
Abstract: The main requirements for battery separators are high porosity which can serve pathways of lithium ion and space for gel electrolytes to impregnate in a membrane and mechanical strength to allow easy handling for battery assembly. Generally, it appears the trade-off relationship between the porosity and mechanical strength of the membrane. PVdF composite membranes containing nano-size clays were used to improve the mechanical strength of the membrane without affecting the membrane porosity. The composite membranes were prepared by phase inversion method controlling the membrane preparation conditions such as retention time. The resultant membranes show increased mechanical properties with similar membrane porosity around 80 % compared to the pristine PVdF membrane. Incorporation of nonoclay can be considered as an effective method to improve the mechanical strength in porous membrane supports, especially in a separator.
Key words: Li-ion battery; separator; poly(vinylidene fluoride); nanocomposite
1 Introduction
The past decade has seen significant advances in the ambient temperature lithium battery technology. Lithium-ion batteries are the preferred power source for most portable electronics because of their higher energy density, longer cycle life and higher operational voltage. Separators used in commercial Li-ion batteries are nearly exclusively semi-crystalline polyolefine membranes, including polyethylene (PE)[1-2], polypropylene (PP)[3-5], and their blends such as PE-PP[6-7]. Although PE-based separators have good mechanical properties, chemical stability and acceptable cost, they cause safety problems in lithium-polymer batteries at temperatures above 140 °C[8-9]. At these temperatures, the separator melts and internal short-circuits could be observed, if the melt does not perfectly cover the electrodes.
Generally, the separator should have sufficient porosity to absorb liquid electrolyte for the high ionic conductivity. However, the presence of the separator adds electrical resistance and takes up limited space inside the battery, which adversely affects the battery performance. Therefore, the selection of an appropriate separator is critical to the battery performance, including the energy density, power density, cycle life and safety. For high energy and power densities, the separator is required to be very thin (less than 30 ?m) and highly porous while still remaining mechanically stable. For battery safety, the separator should be able to shut the battery down when overheating occurs, such as the occasional short circuit, so that thermal runaway can be avoided.
Poly(vinylidene fluoride) (PVdF) is well known to have good compatibility with liquid electrolyte and poor mechanical properties compared to the normal PE separator. In this study, we adopted nanoclay particles in porous polymeric membrane based on PVdF for a separator to improve the critical properties. PVdF based composite membrane was prepared by a phase inversion method under different preparation conditions and examined to apply for lithium rechargeable battery.
2 Experimental
2.1 Membrane preparation
The PVdF used in this study was supplied by Solvay Chemicals under the trade mark Solef 6008. N,N-dimethylformamide (DMF) was purchased from Samchen chemical, Korea and used as received. Natural and organic clay were provided by Southern Clay Product. Co. which has been commercially on the market under trade name of Closite? Na+, Closite? 15A, Closite? 20A, and Closite? 30B. The structure and properties of layered silicates are presented in Fig.1 and Table 1. Where HT is hydrogenated tallow (about 65% C18; about 30% C16; about 5% C14)
Table 1 Properties of various clay species
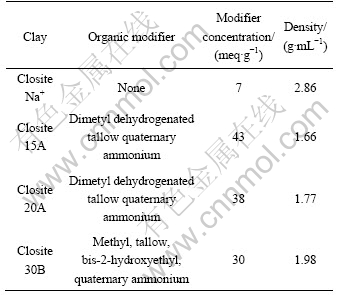
Polymer solutions were prepared by stirring a mixture of PVdF and a solvent with mass ratio of 1?4 in a round bottom flask at 70 °C for 6 h. After complete dissolution, various kinds of clay suspensions were added into the polymer solution and mixed completely. The clay suspensions were prepared by mixing an appropriate amount of clay and DMF solvent. The clay concentration was controlled to 1% (mass fraction) per polymer contents. The prepared solutions were cast on a glass plate with doctor blade. The cast membranes were kept under air atmosphere for controlled time of 30 s and 60 s. Then, the membranes were immersed into water coagulation bath to generate micro-pores. After 6 h, the membranes were washed with methanol and dried at room temperature to remove the residual solvent. The thickness of the obtained membranes was in the range of 20-30 ?m.
2.2 Characterization
The polymer solution viscosity was measured using a viscometer (Brookfiled HBDV-1, USA). The specimens for observing the SEM images of the cross- section, top side and bottom side of the films were prepared by fracturing the films in liquid nitrogen. The SEM images of the polymer films were taken by using a JEOL 6380 (Japan). The membrane porosity was examined using liquid absorption methods according to American Society for Testing and Materials (ASTM) D-2873. The X-ray diffraction (XRD) patterns were determined by a Miniflex X-ray diffractometer (Rigaku Corp., Japan), using Cu Kα radiation (λ=0.154 2 nm), at a scanning rate of 5 (°)/min over 2θ intervals from 1.5° to 15°. The d-spacing values were calculated from the Bragg equation: nλ=2dsinθ, where n is an integer determined by the order given, λ is the wavelength of X-rays, and moving electrons, protons and neutrons, d is the spacing between the planes in the atomic lattice, and θ is the angle between the incident ray and the scattering planes.
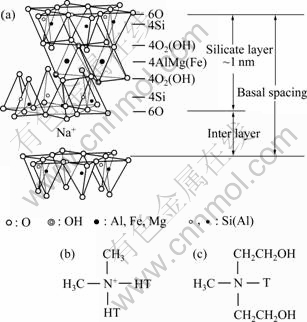
Fig.1 Structural formula of various clay species: (a) Closite? Na+; (b) Closite? 15A, Closite? 20A; (c) Closite? 30B
The mechanical properties of PVdF and PVdF nanocomposite membranes were measured using a universal tensile machine (Instron model 5565, Lloyd, UK) with a constant cross-head speed of 10 mm/min according to the ASTM 638 method. The specimen dimensions were 50 mm×5 mm. The produced membranes were kept in the oven at 135 °C for 1d to examine thermal shrinkage and the change of membrane dimension were measured along the machine direction (MD) and transverse direction (TD).
3 Results and discussion
The viscosity of 20% (mass fraction) PVdF/DMF solution was around 0.7 Pa?s and all PVdF nanocomposite solution also showed similar viscosity with the pristine PVdF solution. The solution viscosity was suitable to prepare porous polymeric membranes. Figs.2 and 3 present the morphology of cross-section, top side and bottom side of the membranes prepared with different retention times.
The cross-section morphologies of the membranes show sponge-like micro-pores in the lower side and finger-like macro-pores in the upper side of the membrane. The increase of finger-like macro-pores was observed at the membrane prepared with longer retention time. This represented that the evaporated solvents were trapped at the upper side of the membrane with increasing retention time[10].
An appropriate porosity is necessary to hold sufficient liquid electrolyte for the ionic conductivity between the electrodes. However, too high porosity will adversely impact the shutdown performance because in this case the pores cannot be closed effectively and the membrane tends to shrink as it melts or soft. Therefore, high porous membranes with good mechanical and thermal stability were required for Li-ion battery separators[11]. Fig.4 shows the membrane porosities of PVdF and PVdF nanocomposite membranes prepared with retention time of 30 s and 60 s. All membranes exhibit high porosities over than 75% independent of the presence or absence of clay particles and clay species.
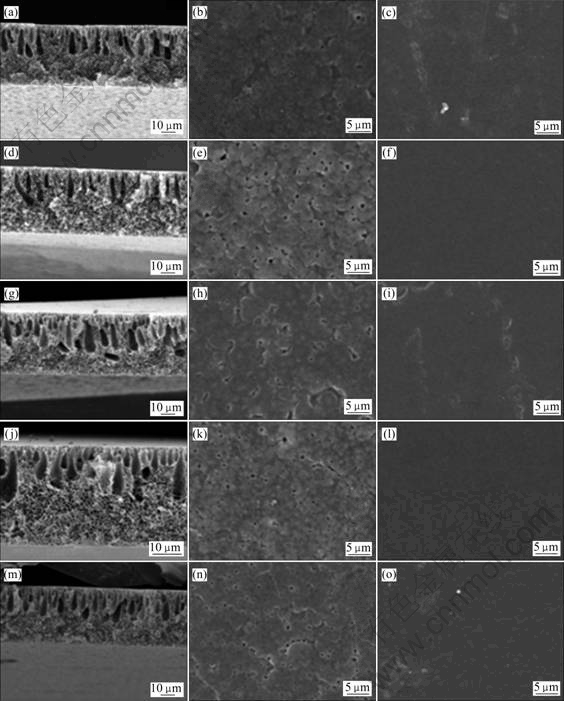
Fig.2 SEM images of porous PVdF and PVdF nanocomposite membranes prepared with retention time of 30 s: (a), (b), (c) PVdF; (d), (e), (f) PVdF/Na+; (g), (h), (i) PVdF/15A; (j), (k), (l) PVdF/20A; (m), (n), (o) PVdF/30B
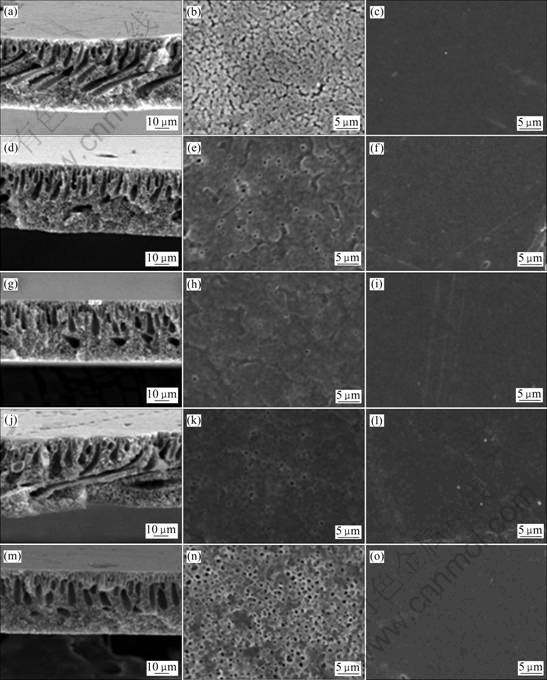
Fig.3 SEM images of porous PVdF and PVdF nanocomposite membranes prepared with retention time of 60 s: (a), (b), (c) PVdF; (d), (e), (f) PVdF/Na+; (g), (h), (i) PVdF/15A; (j), (k), (l) PVdF/20A; (m), (n), (o) PVdF/30B
Intercalation of clay particles into PVdF matrix using solution casting method is based on the DMF solvent system in which the PVdF is soluble and the clay particles are swellable. The clay particle is first swollen or dispersed in the DMF solvent. When the PVdF solution and clay suspensions are mixed, the polymer chains intercalate and displace the solvent within the interlayer of the clay. Upon solvent removal, the intercalated structure remains, resulting in PVdF/clay nanocomposite. This method is good for the intercalation of polymers and facilitates production of thin films with polymer-oriented clay intercalated layers. XRD was used to identify the structure of PVdF/clay nanocomposite membranes. The intercalation of the polymer chains usually increases the interlayer spacing of clays, compared with that of the pristine one. As far as the exfoliated structure is concerned, no more diffraction peaks are visible in the X-ray diffractograms either because of too large spacing between the layers or because the nanocomposite does not present ordering anymore[12-13]. Fig.5 shows XRD patterns of the PVdF/clay composite membranes containing different clay species and the original clay. The characteristic peaks were observed at 2θ=7.5° (d001=11.9 ?) for Closite? Na+, 2θ=3° (d001=28.6 ?) for Closite? 15A, 2θ=3.5° (d001=24.9 ?) for Closite? 20A, and 2θ=5.3° (d001=16.7 ?) for Closite? 30B, respectively.
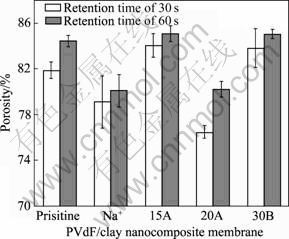
Fig.4 Membrane porosities of PVdF and PVdF nanocomposite membranes prepared with retention times of 30 s and 60 s
After complete intercalation, no diffraction peaks appeared in the XRD pattern of PVdF/clay nanocomposite membranes excepting PVdF/Na+ nanocomposite. As shown in Fig.5(c), the diffraction peaks of Closite? Na+ were moved to the left side from 2θ=7.5° (d001=11.9 ?) to 2θ=6.4° (d001=13.8 ?), indicating partially intercalated structure and the reduced intensity of the diffraction peak present a disordered exfoliated structure of clay gallery[14-16]. This partial intercalation may result from the poor affinity between the hydrophobic PVdF and hydrophilic Closite? Na+.
The separator must be mechanically strong and enough to withstand the tension of the winding operation during battery assembly. Generally, it is believed that clay is an effective material to improve the mechanical properties if it disperses well in polymer matrix[17-18]. The mechanical properties of PVdF and PVdF/clay nanocomposite membranes are shown in Fig.6. As confirmed in the XRD results, all clay particles are completely or partially intercalated into PVdF matrix, resulting in the improvement of mechanical properties. The maximum tensile strength was observed at PVdF/15A nanocomposite membrane prepared with retention time of 30 s. The high hydrophobicity of Closite? 15A may give good affinity to PVdF matrix, resulting in tensile strength increasing from 15 to 54 MPa.
To evaluate the heat-resisting properties of PVdF and PVdF/clay nanocomposite membranes, we measured the film shrinkage along the MD and TD after heat treatment at 105 and 135 °C. Fig.7 shows the thermal shrinkage of PVdF and PVdF/clay nanocomposite membranes. They exhibit reasonable stability of less than 2% in both MD and TD. In case of polyethylene, it can shrink as much as 10% when it was exposed to a temperature of 120 °C for only 10 min[19]. However, PVdF used in this study has high melting point of 174 °C and provides low values of shrinkage up to 135 °C.
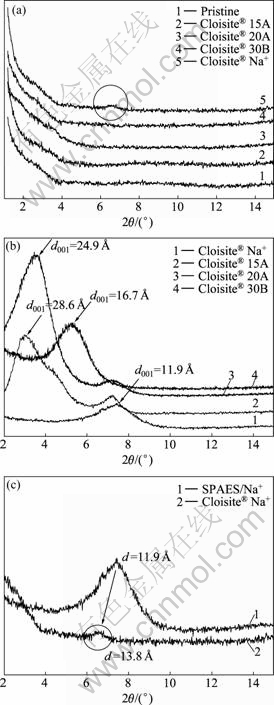
Fig.5 XRD patterns of PVdF/clay composite membranes containing different clay species and original clay: (a) PVdF/clay nanocomposite membranes; (b) Clay particles used in this study; (c) Diffraction peak shift in PVdF/Na+ nanocomposite membrane
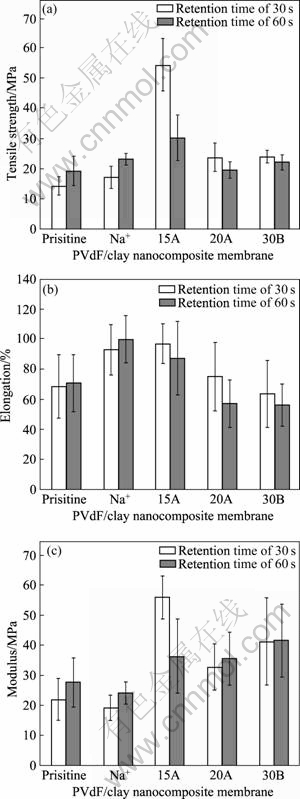
Fig.6 Mechanical properties of PVdF and PVdF/clay nanocomposite membranes prepared with retention time of 30 s and 60 s
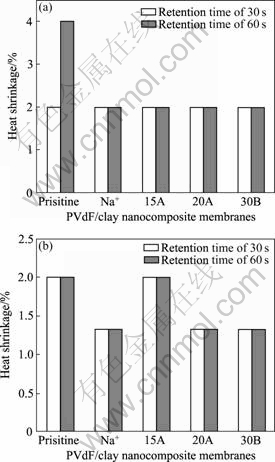
Fig.7 Heat shrinkages of PVdF and PVdF/clay nanocomposite membranes prepared with different retention time of 30 s and 60 s: (a) Machine direction; (b) Transverse direction
4 Conclusions
1) Various kinds of clay particles were incorporated into PVdF by solution mixing and PVdF/clay nanocomposite membranes were prepared by phase inversion methods controlling retention time.
2) High porous morphologies were confirmed by SEM analysis and all prepared membranes show high porosity over than 75%.
3) XRD results showed that clay particles were well-dispersed in PVdF matrix and partially intercalated in case of the PVdF/Na+ nanocomposite membrane.
4) Improved mechanical properties and thermal stability against to shrinkage were obtained by incorporating clay particles in PVdF matrix.
Acknowledgement
Hae-young HWANG is grateful to the second stage of Brain Korea (BK) 21 Project for supporting a fellowship. This work was funded by Fundamental R&D Program for Core Technology of Materials of Korean Ministry of Knowledge Economy.
References
[1] HASHIMOTO A, YAGI K, MANTOKU H. Porous film of high molecular weight polyolefin and process for producing same. US 6048607 [P]. 2000.
[2] KAIMAI N, TAKITA K, KONO K, FUNAOKA H. Method of producing highly permeable microporous polyolefin membrane. US 6153133 [P]. 2000.
[3] CHU F, YAMAOKA T, KIMURA Y. Crystal transformation and micropore formation during uniaxial drawing of β-form polypropylene film [J]. Polymer, 1995, 36(13): 2523-2530.
[4] FISHER H M, WENSLEY C G. Polypropylene microporous membrane for battery separator. US 09/105516 [P]. 1998.
[5] LEE S Y, AHN B I, IM S G, PARK S Y, SONG H S, KYUNG Y J. High crystalline polypropylene microporous membrane, multi- component microporous membrane and methods for preparing the same. US 6830849 [P]. 2004.
[6] HIGUCHI H, MATSUSHITA K, EZOE M, SHINOMURA T. Porous film, process for producing the same, and use of the same. US 5385777 [P]. 1995.
[7] SOGO H. Separator for a battery using an organic electrolytic solution and method for preparing the same. US 5641565 [P]. 1997.
[8] UCHIDA I, ISHIKAWA H, MOHAMEDI M, UMEDA M. AC-impedance measurements during thermal runaway process in several lithium/polymer batteries [J]. Journal of Power Sources, 2003, 119: 821-825.
[9] WU M S, CHIANG P C J, LIN J C, JAN Y S. Correlation between electrochemical characteristics and thermal stability of advanced lithium-ion batteries in abuse tests-short-circuit tests [J]. Electrochimica Acta, 2004, 49(11): 1803-1812.
[10] SEOL W H, LEE Y M, PARK J K. Preparation and characterization of new microporous stretched membrane for lithium rechargeable battery [J]. Journal of Power Sources, 2006, 163(1): 247-251.
[11] ZHANG S S. A review on the separators of liquid electrolyte Li-ion batteries [J]. Journal of Power Sources, 2007, 164(1): 351-364.
[12] SONG M K, PARK S B, KIM Y T, KIM K H, MIN S K, RHEE H W. Characterization of polymer-layered silicate nanocomposite membranes for direct methanol fuel cells [J]. Electrochimica Acta, 2004, 50(2/3): 639-643.
[13] CHISHOLM B J, MOORE R B, BARBER G, KHOURI F, HEMPSTEAD A, LARSEN M, OLSON E, KELLEY J, BALCH G, CARAHER J. Nanocomposites derived from sulfonated poly (butylene terephthalate) [J]. Macromolecules, 2002, 35(14): 5508-5516.
[14] KIM K M, PARK N G, RYU K S, CHANG S H. Characteristics of PVdF-HFP/TiO2 composite membrane electrolytes prepared by phase inversion and conventional casting methods [J]. Electrochimica Acta, 2006, 51(26): 5636-5644.
[15] WANG Y, ZHANG L, TANG C, YU D. Preparation and characterization of rubber-clay nanocomposites [J]. Journal of Applied Polymer Science, 2000, 78(11): 1879-1883.
[16] RAY S. Polymer/layered silicate nanocomposites: a review from preparation to processing [J]. Progress in Polymer Science, 2003, 28(11): 1539-1641.
[17] USUKI A, KOJIMA Y, KAWASUMI M, OKADA A, FUKUSHIMA Y, KURAUCHI T, KAMIGAITO O. Synthesis of nylon 6-clay hybrid [J]. Journal of Materials Research (USA), 1993, 8(5): 1179-1184.
[18] KOJIMA Y, USUKI A, KAWASUMI M, OKADA A, FUKUSHIMA Y, KURAUCHI T, KAMIGAITO O. Mechanical properties of nylon 6-clay hybrid [J]. Journal of Materials Research (USA), 1993, 8(5): 1185-1189.
[19] KRITZER P. Nonwoven support material for improved separators in Li-polymer batteries [J]. Journal of Power Sources, 2006, 161(2): 1335-1340.
(Edited by LONG Huai-zhong)
Foundation item: Project supported by the Fundamental R&D Program for Core Technology of Materials of Korean, Ministry of Knowledge Economy; Project supported by the second stage of Brain Korea (BK) 21
Corresponding author: Sang-Yong NAM; Tel: +82-55-7515301; E-mail: walden@gnu.ac.kr