
Microstructure and interface reaction of investment casting TiAl alloys
CHEN Yu-yong(陈玉勇), XIAO Shu-long(肖树龙), KONG Fan-tao(孔凡涛), WANG Xue(王 雪)
National Key Laboratory for Precision Hot Processing of Metals,
School of Materials Science and Engineering, Harbin Institute of Technology, Harbin 150001, China
Received 28 July 2006; accepted 15 September 2006
Abstract: In order to research the microstructure of TiAl alloy and TiAl-mould reaction between TiAl and ceramic mould shells prepared with the low cost binder in investment casting, the ceramic mould shells were prepared with low cost binder and refractory materials. Using two kinds of casting methods (gravity casting and centrifugal casting), the titanium aluminum alloys with rare earth element (Ti-47.5Al-2Cr-2Nb-0.3Y and Ti-45Al-5Nb-0.3Y) were cast into the mould shells. The microstructures of investment casting titanium aluminum alloys were observed by optical microscope (OM). The distributions of elements of topping investment on the surfaces of titanium aluminum alloys castings were analyzed by the means of electron probe micro-analysis (EPMA), and the mechanical properties were studied. The results show that the microstructures of two kinds of titanium aluminum alloys are both lamella shape, and lamella is thin. The thickness of reaction and diffusing layer of Ti-47.5Al-2Cr-2Nb-0.3Y alloy is about 80 μm, and that of Ti-45Al-5Nb-0.3Y is less than 30 μm.
Key words: titanium aluminum; investment casting; microstructure; reaction
1 Introduction
TiAl alloys have been researched for quite some time because of their attractive combination of high melting point, low density, high specific yield strength, good oxidation resistance and excellent creep properties at high temperatures[1-5].
In the early stage, the development of TiAl alloys was focused on the defense industry, so that the performance was important than the cost. But in the emerging market especially automotive industry, not only the performance but also the cost is very important factors[6-7]. Because highly reactive in a molten state and low ductility, TiAl alloys applied for commerce are limited. In order to utilize TiAl alloy, the development of net-shape technologies must be studied. The investment casting can be regarded as an economic net-shape technology for TiAl alloys because of higher utilization rate of materials, reliability and so on. In recent years the extensive research has been undertaken on the technology of TiAl investment casting[8-15].
In this study, a kind of new low cost material was chosen for investment binder, mechanical properties of TiAl-based alloys and surface reaction layer between TiAl-based alloys and ceramic mould shells were studied.
2 Experimental
2.1 Materials
The content of alloying elements, especially Al element, has a large effect on properties of TiAl based alloys. During solidification of TiAl alloys, after being added alloying elements, the γ-phase area changes, the content of Al element in γ-phase and value of γ/α2 and γ/L are influenced, so that the properties of the alloys are different.
Ti-47.5Al-2Cr-2Nb and Ti-45Al-5Nb are mature TiAl alloys and to the former, the addition of element of Y can improve the structures and properties of these alloys, especially with content of 0.3%(actomic fraction)[16]. So in the experiment, TiAl alloys of Ti-47.5Al-2Cr-2Nb-0.3Y and Ti-45Al-5Nb-0.3Y were chosen.
2.2 Materials preparation and experimental
The TiAl alloys were melted in vacuum inducting furnace and cast into different mould shells. Ti-47.5Al-2Cr-2Nb-0.3Y alloy was cast by means of gravity casting and Ti-45Al-5Nb-0.3Y alloy was cast by centrifugal casting. In each type of casting alumina based and zirconia based mould shells were chosen. The experiment scheme is as follows:
Test 1: gravity casting and alumina based mould shell;
Test 2: gravity casting and zirconia based mould shell;
Test 3: centrifugal casting and alumina based mould shell;
Test 4: centrifugal casting and zirconia based mould shell.
The samples were cut from the casts in the reaction interface. The size of the samples was 5 mm×5 mm×5 mm. After being burnised, polished and corroded, the samples were observed by OLYMPUS BH2-UMA light microscope. The line scan analysis of the samples without being corroded was carried out by X-650 scan electron microscope. The samples with size of 3 mm×5 mm cutting from cast were prepared for the experiment of compressibility of TiAl alloy, the test machine was INSTRON-5500 compression testing machine, and the loading velocity was 2 mm/min.
3 Results and discussion
3.1 Microstructure of investment casting TiAl alloys
The microstructures of Ti-47.5Al-2Cr-2Nb-0.3Y and Ti-45Al-5Nb-0.3Y cast in the condition of gravity casting and centrifugal casting are shown in Figs.1 and 2. The metallograph of the TiAl based alloys are all near lamella or full lamella structure. And there are some white massive phases that may be α2 phase.
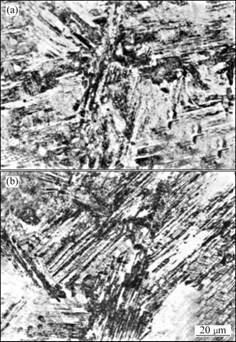
Fig.1 Metallographs of Ti-47.5Al-2Cr-2Nb-0.3Y cast by gravity casting: (a) Al2O3 based mould shell; (b) ZrO2 based mould shell
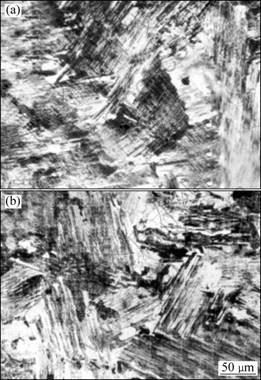
Fig.2 Metallographs of Ti-45Al-5Nb-0.3Y cast by centrifugal casting: (a) Al2O3 based mould shell; (b) ZrO2 based mould shell
3.2 Surface reaction of investment casting TiAl alloy with mould shell
The line scan photographs of the interface between Ti-47.5Al-2Cr-2Nb-0.3Y alloy and mould shell are shown in Fig. 3. The basal body and interface layer of the alloys can be observed from interfaces of alloys and mould shells, and the thickness of reaction layers are about 80 μm. The layer thickness of Test 2 is smaller than that of Test 1. The content of Ti, Al and Cr decreases gradually on the direction of alloys to interface, the content of O increases and that of Si doesn’t obviously change, so the results can be gotten that the reaction layers are mainly caused by reaction and diffusion of element of O. The source of O can be melting atmosphere and mould shell materials.
Fig.4 shows the line scan photographs of Ti-45Al-5Nb-0.3Y alloy. The content of element of mould shell materials changes with the change of content of Ti-47.5Al-2Cr-2Nb-0.3Y alloy, and the thickness of reaction layers is about 30 μm.
At the same time, the white grains distributed in crystal and grain boundary can be found in Figs.3 and 4. Line scan photographs show that at the grains the content of Y segregates on normal way and that of Ti, Al segregates on inverse way, so the white grains are Y-rich phase.
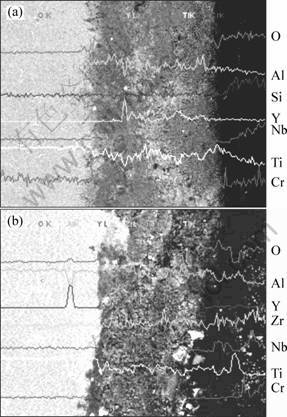
Fig.3 Line scanning analysis of Ti-47.5Al-2Cr-2Nb- 0.3Y alloy: (a) Al2O3 based mould shell; (b) ZrO2 based mould shell
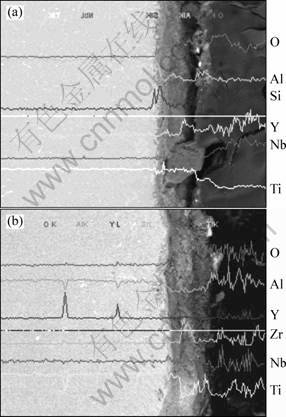
Fig.4 Line scanning analysis of Ti-45Al-5Nb-0.3Y alloy: (a) Al2O3 based mould shell; (b) ZrO2 based mould shell
Fig.5(a) shows the compressibility curve of alloys of Tests 1 and 2. The results show that the compression ratio and compressive strength of Test 2 are better than those of Test 1 because the mould shell materials are different, which indicates that the properties of alloy cast with zirconia based mould shell are bigger than that of alumina. The same conclusion can be gotten in Tests 3 and 4, and the difference of the compressibility is marked, the results is shown in Fig.5(b).
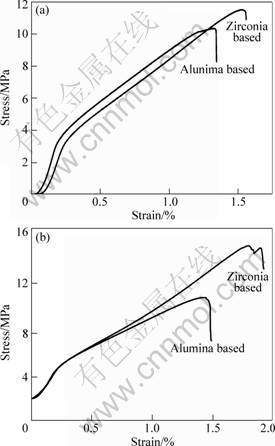
Fig.5 Compression curves of TiAl based alloy: (a) Ti-47.5Al- 2Cr-2Nb-0.3Y alloy; (b) Ti-45Al-5Nb-0.3Y alloy
Figs.6(a) and (b) show the compressing rupture of Ti-47.5Al-2Cr-2Nb-0.3Y alloy cast by gravity casting. The form of fracture is cleavage fracture, the ruptures contain some cleavage planes, cracks expand along the parallel plants with the same crystal indices and there appears split but no dimple. The fracture of Test 2 is cleavage fracture with the character of ductile fracture. The fracture ruptures of Ti-45Al-5Nb-0.3Y are shown in Figs.6(c) and (d). Many dimples can be found in the ruptures. The ruptures of alloy cast with zirconia based mould shell are more than that of alumina based and the ruptures show the shape of parabola, and the alloy has bigger toughness. The former analysis result indicates that compressive properties of alloy cast into zirconia based mould shell is better than that of alumina based, and the property of centrifugal casting is better than that of gravity casting.
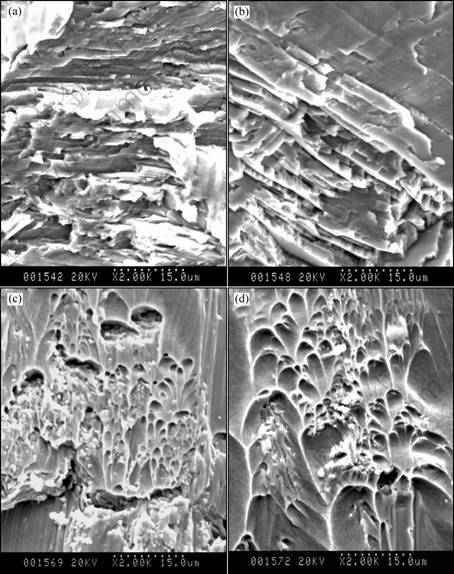
Fig.6 Compressive fracture photographs of TiAl based alloys: (a) Gravity casting into alumina based mould shell; (b) Gravity casting into zirconia based mould shell; (c) Centrifugal casting into alumina based mould shell; (d) Centrifugal casting into zirconia based mould shell
4 Conclusions
1) The microstructures of Ti-47.5Al-2Cr-2Nb-0.3Y and Ti-45Al-5Nb-0.3Y alloys both tend to form near lamella or full lamella structure.
2) The basal body and interface layer of the alloys can be observed from interfaces of alloys and mould shells. The thickness of interface layers between Ti-47.5Al-2Cr-2Nb-0.3Y alloy and mould shell are about 80 μm, and the layers are mainly caused by reaction and diffusion of O. The reaction layers of Ti-45Al-5Nb-0.3Y alloy are smaller and thinner than that of Ti-47.5Al- 2Cr-2Nb-0.3Y and the thickness is about 30 μm.
3) The results from the compression experiments show that the different mould shell materials cause the different properties of materials, the properties of alloys cast into zirconia based mould shell are better than those of alumina based.
References
[1] LORIA E A. Quo vadis gamma titanium aluminide[J]. Intermetallics, 2001, 9(12): 997-1001.
[2] YAMAGUCHI M. High-temperature structural intermetalics[J]. Acta Materialia, 2000, 48 (1): 307-322.
[3] ZHANG Y G, HAN Y F, CHEN G L, GUO J T, WANG X J. Structural Intermetallics[M]. Beijing: National Defence Industry Press, 2001.(in Chinese)
[4] CLEMENS H, KESTLER H. Processing and applications of intermetallic γ-TiAl-based alloys[J]. Advanced Engineering Materials, 2000, 2(9): 551-570.
[5] APPEL F, BROSSMANN U, CHRISTOPH U, EGGERT S, JANSCHEK P, LORENZ U, MULLAUER J, OEHRING M, PAUL J. Recent progress in the development of gamma titanium aluminide alloys[J]. Advanced Engineering Materials, 2000, 2(11): 699-720.
[6] EYLON D, KELLER M M, JONES P E. Development of permanent-mold cast TiAl automotive valves[J]. Intermetallics, 1998, 6(7-8): 703-708.
[7] TETSUI T. Application of TiAl in a turbocharger for passenger vehicles[J]. Advanced Engineering Materials, 2001, 3(5): 307-310.
[8] WANGER R, APPEL F, BILAL D. Investment casting of γ-TiAl based alloys: Microstructure and data base for gas turbine application[C]//KIM Y W, WAGNER R, YAMAGUCHI M. Gamma titanium aluminides. New York: The Minerals, Metal and Materials Society, 1995: 387.
[9] LIU Bing, FAN Run-hua, SUN Jia-tao, MA Lai-peng. Development of TiAl-base Alloy and its application on automotives[J]. Automobile Technology, 2005(3): 29-33.
[10] KUANG J P, HARDING R A, CAMPBELL J. Examination of defects in gamma titanium aluminide investment casting[J]. Int J cast Metal Res, 2000, 13(3): 125-134.
[11] APPEL F, BROSSMANN U, CHRISTOPH U. Recent progress in the development of gamma titanium aluminide alloys[J]. Advanced Engineering Materials, 2000, 2(11): 699-720.
[12] LIN Fan, WANG Jia-fang, GENG Rui-shan. Casting of TiAl turbine wheels [J]. Hot Working Technology, 2001(5): 33-34.(in Chinese)
[13] CHEN Yu-yong, XIAO Shu-long, KONG Fan-tao. Application and investment casting of high temperature titanium alloys and tial intermetallics[J]. Acta Metallurgica Sinica, 2002, 38(Z1): 39-44.(in Chinese)
[14] SU Yan-qing, GUO Jing-jie, JIA Jun, DING Hong-sheng, CUI Hong-bao, LIU Song-qing. Centrifugal investment casting of a TiAl-based turbine blade[J]. Rare metal Materials and Engineering, 2002, 31(4): 296-299.(in Chinese)
[15] LIANG Zhu-jian, XU Qing-yan, LI Jun-tao, LI Shi-qiong, ZHANG Ji, LIU Bai-cheng, ZHONG Zeng-yong. Experimental research on the near net shape casting process of gamma titanium aluminide turbochargers[J]. Rare Metal Materials and Engineering, 2002, 31(5): 354-359.(in Chinese)
[16] KONG Fan-tao, CHEN Zi-yong, TIAN Jing, CHEN Yu-yong, JIA Jun. Effect of rare earth on microstructure of γ-TiAl intermetallics[J]. Journal of Rare Earths, 2003, 21(2): 163-167.(in Chinese)
(Edited by CHEN Can-hua)
Corresponding author: XIAO Shu-long; Tel: +86-451-86418802; E-mail: xiaoshulong@hit.edu.cn