J. Cent. South Univ. Technol. (2007)01-0047-04
DOI: 10.1007/s11771-007-0010-7

Preparation and electrochemical properties of polymer Li-ion battery reinforced by non-woven fabric
HU Yong-jun(胡拥军)1,2, CHEN Bai-zhen(陈白珍)1, YUAN Yan(袁 艳)1
(1. School of Metallurgical Science and Engineering, Central South University, Changsha 410083, China;
2. Department of Chemistry, Hunan City University, Yiyang 413049, China)
Abstract: A polymer electrolyte based on poly(vinylidene) fluoride-hexafluoropropylene was prepared by evaporating the solvent of dimethyl formamide, and non-woven fabric was used to reinforce the mechanical strength of polymer electrolyte and maintain a good interfacial property between the polymer electrolyte and electrodes. Polymer lithium batteries were assembled by using LiCoO2 as cathode material and lithium foil as anode material. Scanning electron microscopy, alternating current impedance, linear sweep voltammetry and charge-discharge tests were used to study the properties of polymer membrane and polymer Li-ion batteries. The results show that the technics of preparing polymer electrolyte by directly evaporating solvent is simple. The polymer membrane has rich micro-porous structure on both sides and exhibits 280% uptake of electrolyte solution. The electrochemical stability window of this polymer electrolyte is about 5.5 V, and its ionic conductivity at room temperature reaches 0.151 S/m. The polymer lithium battery displays an initial discharge capacity of 138 mA?h/g and discharge plateau of about 3.9 V at 0.2 current rate. After 30 cycles, its loss of discharge capacity is only 2%. When the battery discharges at 0.5 current rate, the voltage plateau is still 3.7 V. The discharge capacities of 0.5 and 1.0 current rates are 96% and 93% of that of 0.1 current rate, respectively.
Key words: polymer electrolyte; Li-ion battery; poly(vinylidene) fluoride-hexafluoropropylene; ionic conductivity
1 Introduction
Solid polymer electrolyte has been received great interest in recent years due to its applications in various electrochemical devices. In the past decades, a large number of studies have been carried out on this kind of polymer electrolyte[1-5], and great progress has been achieved. However, because of their complicated preparing technology and poor mechanical strength, gel polymer electrolyte still can not be used in commercial production. To simplify the procedure of preparation and to improve the properties of polymer electrolyte, some organic and inorganic materials were added to the polymer[6-10]. In 1994, researchers of Bellcore developed a new technology to prepare micro-porous gel polymer electrolyte based on poly(vinylidene) fluoride-co- hexafluoropropylene (PVDF-HFP) by plasticization/ extraction procedure[11], and successfully used this gel polymer electrolyte in commercial batteries. But the extraction step increases the production cost, and the mechanical strength of this PVDF-HFP polymer electrolyte is still not strong enough to produce excellent batteries.
In this study, a novel method was used to prepare polymer electrolyte. By directly evaporating the solvent of dimethyl formamide (DMF), we can prepare a micro-porous PVDF-HFP polymer electrolyte without extraction step and without using any organic or inorganic additives, so the preparation technology is simplified and the cost is reduced. By choosing non-woven fabric to support the polymer membrane, the polymer electrolyte’s mechanical strength can be greatly reinforced, and the interfacial property between electrolyte and electrodes can be improved.
2 Experimental
2.1 Preparation and characterization of polymer electrolyte
The preparation of polymer electrolyte included a two-step procedure. The first step was to form a micro- porous membrane, then the polymer electrolyte was obtained by absorbing the electrolyte solution into the membrane. For the preparation of micro-porous polymer membrane, PVDF-HFP(Elf Atochem, Kynar 2801, USA) was first dissolved in DMF to form a homogeneous solution. The resulting viscous solution was cast on to the non-woven fabric (Tiert, Xiamen, China) which was spread out on a glass plate. The solution was evaporated in atmosphere environment for 24 h to form a white polymer membrane, and the polymer membrane was dried in a vacuum oven at 80 ℃ for 6 h to remove the moisture, then the polymer membrane was transferred to an argon-filled glove-box and soaked in an electrolyte solution containing 1 mol/L LiPF6 dissolved in EC/DEC/ DMC (m(EC)?m(DEC)?m(DMC)=1?1?1) for 10 min.
The morphologies of polymer membrane were observed by using Japan JSM-6360LV scanning electron microscopy (SEM). The liquid electrolyte uptake(U) was evaluated according to the following formula:
U=[(m-m0)/m0]×100% (1)
where m and m0 are the masses of wet and dry membrane, respectively.
The ionic conductivity (σ) was calculated by
σ=d/(SR) (2)
where d and S are the thickness and area of polymer membrane, respectively; R is the bulk resistance from alternating current(AC) impedance test by using blocking cell of stainless steel/polymer electrolyte/stainless steel at 1-105 Hz. The electrochemical stability window of polymer electrolyte was determined from linear sweep voltammetry using a three-electrode cell with a stainless steel work electrode, lithium reference electrode and counter electrode on Chi660B electrochemical working- station.
2.2 Electrochemical measurement of polymer lithium
batteries
The polymer lithium batteries were assembled by sandwiching the polymer electrolyte between lithium foil and LiCoO2 cathode mixture (m(LiCoO2)?m(PVDF)? m(C)=8?1?1) in a glove-box filled with argon, and the type was 2032 button cell. The charge-discharge experiment was carried out at 2.75-4.20 V by using Neware battery testing system. AC impedance tests were measured on Chi660B electrochemical working-station at 10-2-105 Hz.
3 Results and discussion
3.1 Morphologies of polymer membrane
Fig.1 shows the SEM images of the PVDF-HFP membrane. It can be seen that this polymer membrane has a rich micro-porous structure, and the pores on both sides are like honeycomb. The pore’s diameter of the obverse surface is 4-10 μm. On the back surface of the polymer membrane, because the evaporation speed of DMF is resisted by glass, the diameter of pore is smaller than that of the obverse surface. In Fig.1(c), there is a large number of tiny non-woven fabric in the inside of polymer. This fabric reinforces the polymer membrane, so it has strong mechanical strength and can meet the requirement of polymer electrolyte used in commercial lithium batteries. After absorbing LiPF6 liquid electrolyte, the solution uptake of this polymer membrane is up to 280%.
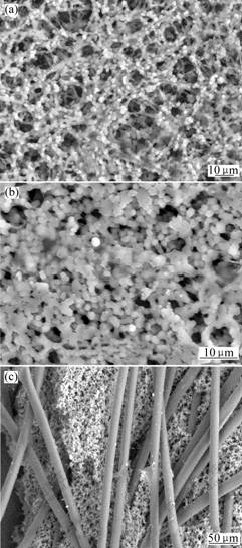
Fig.1 SEM images of polymer membrane
(a) Obversed surface; (b) Back surface; (c) Cross-section
3.2 Electrochemical properties of polymer electrolyte
Ionic conductivity was obtained by AC impedance test. The thickness and surface area of polymer electrolyte are 0.025 cm and 2.01 cm2, respectively. Fig. 2 shows the relationship between the ionic conductivities and temperature for polymer electrolyte reinforced by non-woven fabric. It is found that over the whole temperature, the ionic conductivity dependence on temperature fits the Arrhenius plot, and its ionic conductivity which reaches 0.151 S/m at room temperature and remains 0.122 S/m even at 283 K is as good as that of the polymer electrolytes prepared by the other methods[5,10-11]. This high conductivity should ascribe to the micro-porous structure and high uptake of liquid electrolyte of the polymer membrane.
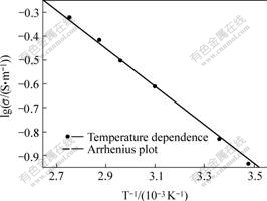
Fig.2 Relationship between temperature and ionic conductivity of polymer electrolyte
Fig.3 shows the current-voltage response of stainless steel working electrode by the linear sweep voltammetry experiment. It can be seen that there is no obvious current through the working electrode from open circuit potential to 5.5 V, and the current that is related to the decomposition of polymer electrolyte increases suddenly when the electrode potential is higher than 6.0 V. This shows that the PVDF-HFP polymer electrolyte reinforced by non-woven fabric is electrochemical stable at least 5.5 V, and the addition of non-fabric into polymer does not debase the electrochemical window of polymer electrolyte[3,5,9-10]. so this polymer electrolyte reinforced by non-fabric can be safely used for polymer lithium batteries.
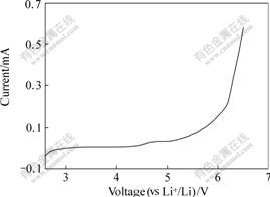
Fig.3 Current—voltage response of Li/polymer electrolyte/stainless steel block cell
3.3 Performance of polymer battery
Fig.4 shows the cycling performance of different batteries at 0.2 current rate between 2.75-4.20 V, of which the reinforced polymer battery uses the non-woven fabric reinforced polymer electrolyte, free-standing polymer battery uses only PVDF-HFP polymer electrolyte obtained also by evaporating the DMF, while the liquid electrolyte battery using LiPF6 solution without any polymer materials.
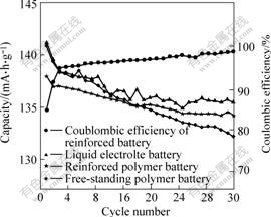
Fig.4 Cycling performance of different batteries at 0.2 current rate
From Fig.4, it can be seen that liquid electrolyte battery and the reinforced polymer electrolyte battery have excellent retention capacity. After 30 cycles, the discharge capacity of the reinforced polymer lithium battery is still above 135 mA?h/g, exhibiting only 2% loss of its initial discharge capacity. At the same time, the charge- discharge efficiency of the reinforced polymer battery goes up from 85% to 98.5% because the anode and the cathode of this polymer battery are gradually wetted by its polymer electrolyte. For the free-standing polymer battery, although it can discharge 140.8 mA?h/g at its first cycle, its discharge capacity wanes quickly, after 30 cycles its loss of capacity is about 6%.
Impedance can affect the capacity of battery[12]. The larger the impedance is, the more quickly the capacity declines. Fig.5 shows the AC impedance of different batteries. Among them, samples 1, 3 and 5 are the impedance plot of liquid electrolyte battery, polymer battery reinforced by non-fabric and free-standing polymer battery at their open circuit potential, respectively, while samples 2, 4 and 6 are their impedance at 3.9 V after 30 cycles.
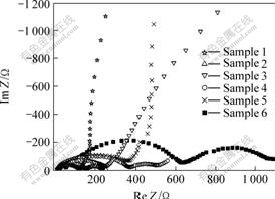
Fig.5 Impedance spectra of different batteries
The first semicircle of impedance plot is the total impedance of solid electrolyte interface film and interfacial impedance between electrolyte and electrodes. During the cycling, polymer electrolyte membrane gradually dents, micro-pores decrease and the absorbed electrolyte solution is squeezed out, so the impedance of free-standing polymer battery increases quickly. Compared with polymer electrolyte, the impedance of reinforced polymer battery only goes up slowly from 260 Ω to 350 Ω, this is a convincing indication that the non-woven fabric can resist the dent of polymer membrane and retain its micro-porous structure, thus keep a good interfacial property between electrodes and polymer electrolyte, and this maybe the reason why the cycling performance of reinforced polymer battery is better than that of the free-standing polymer battery.
Fig.6 shows the rate performance of polymer batteries at 2.75-4.20 V. It can be seen that the discharge voltage plateau of fabric-reinforced polymer battery at 0.1 current rate is about 3.9 V, showing low impedance of polymer battery, and the discharge plateau at 0.5 current rate is still 3.7 V. Assuming the discharge capacity at 0.1 current rate is 100%, this polymer battery can discharge 96% of its capacity at 0.5 current rate and still retains 93% at 1.0 current rate. This good performance at high current rates may be ascribed to the efficient ionic conduction in the polymer electrolyte and the favorable interfacial charge transport between electrodes and electrolyte in the battery. Compared with fabric-reinforced polymer battery, the discharge plateau of free-standing polymer battery at different rates is lower. When the battery discharges at 1.0 current rate, its capacity is only 89% of its discharge capacity at 0.1 current rate.
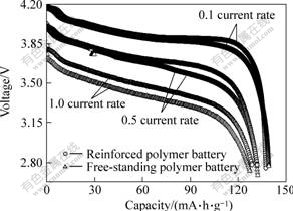
Fig.6 Rate performance of polymer batteries prepared by different polymer electrolytes
4 Conclusions
1) By directly evaporating the solvent of DMF, micro-porous PVDF-HFP polymer membrane reinforced by non-woven fabric is prepared. Compared with phase inversion or plasticization/extraction procedure, this technics is simple, and the cost is low. Non-woven fabric not only reinforces the mechanical strength of polymer electrolyte, but also keeps a good interfacial property between polymer electrolyte and electrodes.
2) The reinforced polymer membrane has a electrolyte solution uptake up to 280%, its electrochemical stability window is about 5.5 V, and its ionic conductivity at room temperature is 0.151 S/m.
3) This reinforced polymer battery exhibits only 2% loss of its initial discharge capacity after 30 cycles at 0.2 current rate, and can remain 96% and 93% of the discharge capacity of 0.5 and 1.0 current rates, respectively.
References
[1] ZHANG S S, ERVIN M H, XU K, et al. Microporous P(AN-MMA) membrane as a separator of rechargeable lithium battery[J]. Electrochimica Acta, 2004, 49(20): 3339-3345.
[2] KIM H S, KUN K S, CHO B W, et al. Electrochemical and physical properties of composites polymer electrolyte of PMMA and PEGDA[J]. Journal of Power Sources, 2003, 124(1): 221-224.
[3] KIM K M, KO J M, PARK N G, et al. Characterization of P(VDF-HFP)-based polymer electrolyte filled with rutile TiO2 nanoparticles[J]. Solid State Ionics, 2003, 161(1): 121-131.
[4] KIM D W, KIM Y R, PARK J K, et al. Electrical properties of the plasticized polymer electrolytes based on acrylonitrile-methacrylate copolymers[J]. Solid State Ionics, 1998, 106(2): 329-337.
[5] DONG D Y, DAEJON Y. Cycling performances of Li/LiCoO2 cell with polymer-coated separator[J]. Electrochimica Acta, 2004, 50(2/3): 323-326.
[6] SONG M K, KIM Y T, CHO J Y, et al. Composed polymer electrolytes reinforced by non-won fabric[J]. Journal of Power Sources, 2004, 125(1): 10-16.
[7] XI J Y, TANG X Z. Enhanced lithium ion transference number and ionic conductivity of composite polymer electrolyte doped with organic-inorganic hybrid P123@SBA-15[J]. Chemical Physics Letters, 2004, 400(1): 68-73.
[8] LIU G, KEINHOUT M, BAKER G L. Nanoscale lithium ion conducting polyethylene oxide with self-attached insulating layers[J]. Solid State Ionics, 2005, 175(4): 721-724.
[9] WU C G, LU M I, CHUANG H J. PVDF-HFP/P123 hybrid with mesopores: a new matrix for high-conducting, low-leakage porous polymer electrolyte[J]. Polymer 2005, 46(20): 5929-5938.
[10] WANG Z L, TANG Z Y. Characterization of the polymer electrolyte based on the blend of PVDF-HFP and PVP for lithium battery[J]. Materials Chemistry and Physics, 2003, 82(1): 16-20.
[11] SONG J Y, WANG Y Y, WANG C C. Review of gel-type polymer electrolytes for lithium batteries[J]. Journal of Power Sources, 1999, 77(2): 183-197.
[12] KUM K, SONG M, KIM Y T, et al. The effect of mixed salts in gel-coated polymer electrolyte for advanced lithium battery[J]. Electrochimica Acta, 2004, 50(2/3): 285-288.
(Edited by YANG You-ping)
Foundation item: Project (2003AA32X010) supported by the National High Technology Research and Development Program of China
Received date: 2006-04-19; Accepted date: 2006-06-28
Corresponding author: HU Yong-jun, Doctoral candidate; Tel: +86-731-8876621; E-mail: hyjwsg@163.com