A356.2合金半固态浆料的在线制备技术
冯鹏发, 唐靖林, 李双寿, 曾大本
(清华大学 机械工程系, 北京 100084)
摘 要: 利用自行研制的双向多级速电磁搅拌装置, 研究“熔体处理+双向电磁搅拌”半固态浆料复合制备技术。 结果表明: 该技术制备浆料效率较高, 可实现A356.2合金半固态浆料的在线制备。 在冷速较快的情况下, 降低浇注温度可以大大缩短半固态浆料的制备时间; 在冷却速度较快、 搅拌速度较低的情况下, 提高搅拌频率不但有助于改善晶粒形貌, 而且具有相当的晶粒细化作用。 选取如下技术参数: 加入0.03%Ti(Al-5Ti-B)(质量分数)和0.04%Sr(Al-10Sr)进行熔体处理、 正-反无间歇双向搅拌、 浇注温度640℃、 搅拌频率25~30Hz、 输出电压220V、 单向搅拌时间5s、 搅拌时间67s, 可获得形状系数大于0.8、 初生晶粒尺寸在80~90μm之间的A356.2半固态浆料。
关键词: A356.2合金; 在线制备; 熔体处理; 双向电磁搅拌; 流变成形 中图分类号: TG146.2; TG115.9
文献标识码: A
On-line preparation technology of semi-solid slurry of A356.2 alloy
FENG Peng-fa, TANG Jing-lin, LI Shuang-shou, ZENG Da-ben
(Department of Mechanical Engineering, Tsinghua University, Beijing 100084, China)
Abstract: Using the self-developed reversible multilevel-speed electromagnetic stirrer, the multiple semi-solid preparation technology of melt treatment and reversible electromagnetic stirring was studied. The results show that the technology, with high preparation efficiency, can realize the on-line preparation of semi-solid slurry of A356.2 alloy, i.e. the preparation efficiency fits the subsequent die casting procedure. With the faster cooling rate, the slurry preparation time can be largely reduced by decreasing pouring temperature. Under the condition of the faster cooling rate and smaller stirring speed, elevated stirring frequency not only strongly promotes to modify the morphologies of α(Al) grains, but also has considerable effects on grain refinement. Following the processing parameters below, the A356.2 alloy slurry with grain diameter of 80-90μm and shape factor of 0.8 or more can be obtained: melt treatment with the additions of 0.03%Ti(Al-5Ti-B) (mass fraction) and 0.04%Sr(Al-10Sr), reversible two-way stirring without interval, pouring temperature of 640℃, stirring frequency of 25-30Hz, output voltage of 220V, one-way stirring time of 5s, total stirring time of 67s.
Key words: A356.2 alloy; on-line preparation; melt treatment; reversible electromagnetic stirring; rheoforming
半固态触变成形技术存在工艺流程长、 制坯成本高(坯料成本占零件成本约40%)、 重熔能耗高、 坯料表面氧化严重、 加热过程坯料流失严重(流失高达10%)、 生产废料无法在生产现场回收等诸多问题[1]。 从20世纪90年代以来, 流变成形技术逐渐成为国内外半固态成形技术的重点发展方向。
目前, 在主要流变成形技术中, 机械搅拌式流变射铸技术[1-3]存在浆料易污染、 搅拌强度低等问题。 射室制备浆料式流变铸造技术[4-6]虽然可以保证半固态浆料的质量, 但存在电磁搅拌的效率较低、 压铸机压室机构改造复杂以及对工艺调控精度要求较高等不足。 液相线铸造(模锻)[7-11]通过低过热度浇注和整体加压效应, 使整个合金液同时进入过冷状态, 实现了同时形核和同时长大, 但只能用于简单结构件的成形, 且生产效率较低。 这三类方法属于制浆-成形一体化技术, 虽然避免了浆料从制备系统到成形系统的转移过程, 但各自具有很大的局限性。
以日本UBE公司UBE New Rheocasting (UNRC)工艺为代表的在线制备半固态浆料的流变铸造技术[7,12]和Flemings等[13-15]开发出的Semi-Solid Rheocasting (SSRTM)技术, 实现了浆料制备系统与零件成形系统分离, 无须对成形机构进行大的改造, 并分别于1999年和2002年实现实际试生产, 但其具体技术细节没有公开。
本文作者的前期研究表明, 如果保证半固态浆料在转移过程中温度下降不超过5℃, 则不会对其流变性能、 显微组织和工件的力学性能产生太大的影响, 因此, 在传统热成形技术的基础上, 研制制浆-成形分离的流变成形系统是完全可行的, 从而可以实现与传统压铸或模锻技术的融合。 本文作者探索的“熔体处理+双向电磁搅拌”复合制备技术, 是整个新型铝合金流变成形技术的关键环节之一。
1 实验
实验材料为A356.2铝合金, 通过差热分析确定其固相率与温度的对应关系, 见表1。
表1 实验用A356.2合金温度与固相率的关系
Table 1 Relations between mass fraction of solid (ws) and temperature (θ)

为获得最佳熔体处理工艺, 首先在电阻炉中进行熔体处理优化实验。 中间合金采用轧制态Al-5Ti-B合金和挤压态Al-10Sr合金。 熔体处理过程如下: 合金在720~750℃熔化保温后, 首先加入Al-5Ti-B合金, 然后通氮气精炼, 接着加入Al-10Sr合金, 随后静置30min。 Al-5Ti-B和Al-10Sr分别选取5个加入量, 通过显微组织分析, 确定最佳熔体处理工艺。
将按照最佳工艺进行熔体处理后的铝液, 转移至自主研发的双向多级速电磁搅拌装置(图1)中进行电磁搅拌。 双向多级速电磁搅拌装置的主要技术参数有: 1)电磁搅拌频率在5~30Hz间可调; 2)电磁搅拌功率为15kW; 3)搅拌方式可采用正转、 反转或交替运行; 4)搅拌换向时间可在0~10s间调节; 5)铝合金半固态浆料最大制备量为2kg。 该装置采用耐火纤维保温, 无加热保温系统。 本研究采用“正-反无间歇转向”方式, 单向搅拌时间设定为5s。
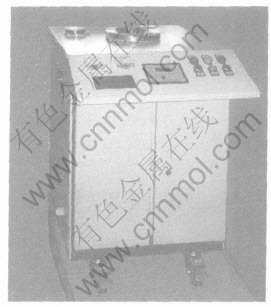
图1 双向多极速电磁搅拌装置照片
Fig.1 Photo of reversible multilevel-speed electromagnetic stirrer
为找到最佳电磁搅拌工艺参数, 依次考察了不同浇注温度(720、 700、 680、 660、 640℃)、 搅拌时间和搅拌频率(5、 10、 15、 20、 25、 30Hz)等3个变量对半固态组织的影响。
熔体处理过程和电磁搅拌过程的温度变化, 采用热电偶和温度采集系统进行记录。 熔体处理实验采用水冷取样, 电磁搅拌实验采用空冷取样。 试样的显微组织分析采用SEM法和定量金相分析法。
2 结果与讨论
初生α(Al)相的形貌采用形状系数Fc描述[16]: Fc=[SX(]4πS[]P2[SX)](其中, S、 P分别为α(Al)晶粒的截面积和截面周长)。 Fc值介于0~1之间, Fc值越趋近1, 表明α(Al)相枝晶退化效果越显著。
2.1 熔体处理工艺对半固态显微组织的影响
2.1.1 Al-5Ti-B加入量对初生α(Al)相形貌的影响
图2所示为Al-5Ti-B加入量对A356.2合金α(Al)相的形貌照片和形状系数的影响。 可以看出, 当细化剂加入量较少(≤0.03%Ti)时, 随着加入量的增大, α(Al)晶粒在尺寸逐渐减小的同时, 形貌也逐渐由发达树枝状退化为花朵状(相应地, 形状系数Fc从0.14增大到0.264); 当细化剂的加入量超过一定程度(>0.03%Ti)后, α(Al)相的形貌变化明显减缓。 这是由于: 加入量较少时, Al-5Ti-B带入铝液中的异相粒子(TiAl3和TiB2)除极少量沉淀外, 绝大部分起到了形核基底的作用, α(Al)相形核率显著增大, 因而晶粒细化和枝晶退化效果显著; 而当铝液中的异相粒子超过一定数量后, 其中一部分异相粒子形核时所释放的热量使整个熔体的温度高于铝的非自发形核温度, 抑制了其余异相粒子发挥形核作用, 致使α(Al)相的细化和枝晶退化效果减缓。
2.1.2 Al-10Sr对初生α(Al)相形貌的影响
通过观察不同Al-10Sr加入量下α(Al)相的形貌(图3)可以看出, 加入0.04%Sr时, α(Al)晶粒形貌最佳。 这表明, 适当加入Sr元素(0.04%Sr)对 α(Al)具有一定的细化和枝晶退化作用(但效果较小); 而当Sr加入量过大(0.05%Sr)时, 就失去了对α(Al)相的细化效果。 这可能是由于Sr的加入促使初生α(Al)的一次枝晶臂间距和二次枝晶臂间距缩短, 激发更多的形核核心, 促进α(Al)成核, 抑制枝晶生长, 使晶粒细化和圆整化[17, 18]。 加入过多的Sr则可能产生局部富集, 导致细化和枝晶退化作用减弱。
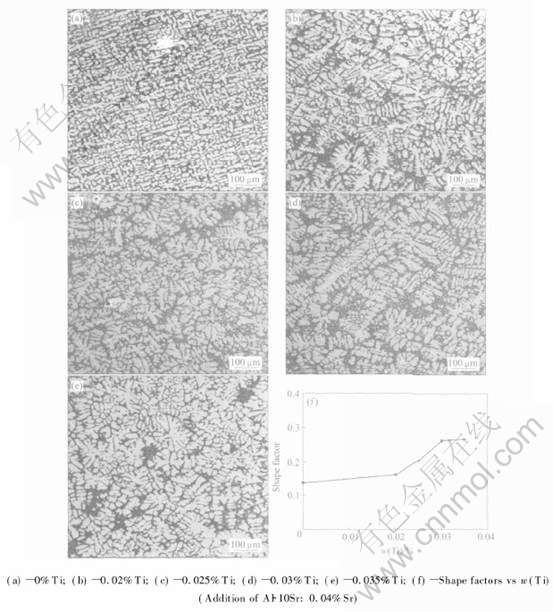
图2 不同Al-5Ti-B加入量下α(Al)相的SEM照片和形状因子
Fig.2 SEM micrographs and shape factors of α(Al) phase with differernt additions of Al-5Ti-B
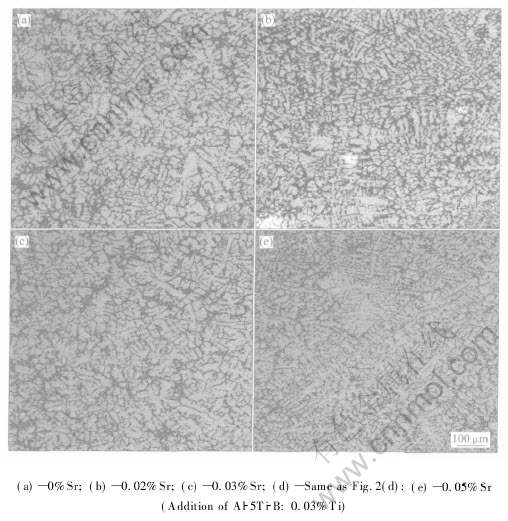
图3 不同Al-10Sr加入量下α(Al)相的SEM照片
Fig.3 SEM micrographs of α(Al) phase with differernt additions of Al-10Sr
通过这一组实验可知, A356.2合金浆料制备时中间合金的最佳加入量为0.03%Ti(Al-5Ti-B)和0.04%Sr(Al-10Sr)。
2.2 制备方式对半固态显微组织的影响
图4和图5所示分别为双向电磁搅拌工艺和“熔体处理+双向电磁搅拌”工艺制备的半固态A356.2合金显微组织。 比较图4和图5(a)可以看出, 在其它条件(搅拌频率f=20Hz, 输出电压U=200V, 浇注温度θ0=720℃, 搅拌时间t=160s, 单向搅拌时间Δt=5s和正-反无间歇双向搅拌)完全相同的情况下, “熔体处理+双向电磁搅拌”工艺制备的半固态组织远优于单纯双向电磁搅拌工艺。
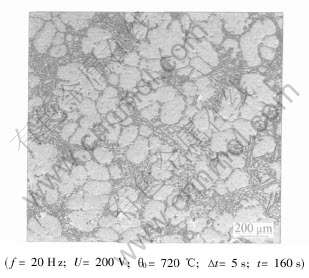
图4 双向电磁搅拌工艺下α(Al)相的SEM照片
Fig.4 SEM micrograph of α(Al) phase prepared by reversible electromagnetic stirring (Fc=0.52)
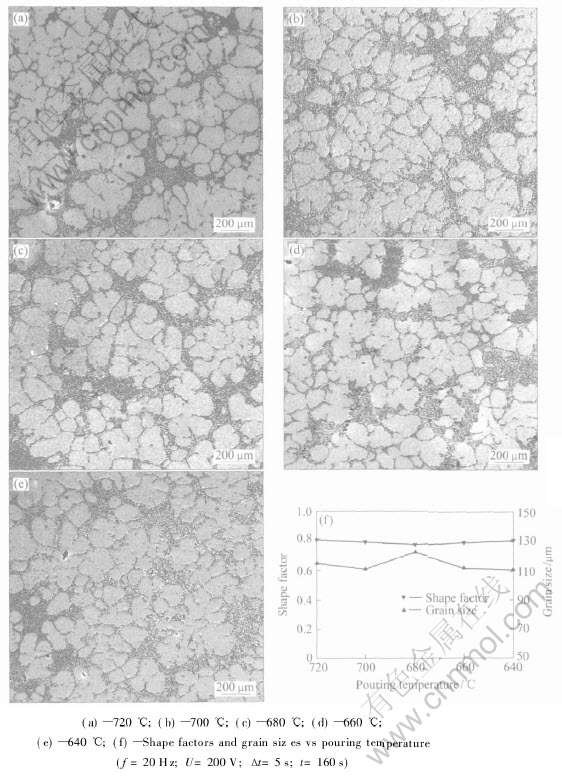
图5 “熔体处理+双向电磁搅拌”工艺下浇注温度对α(Al)形貌和尺寸的影响
Fig.5 Effects of pouring temperature on morphologies and sizes of α(Al) by multiple processing of melt treatment and reversibe electromagnetic stirring
电磁搅拌使熔体产生强烈的对流, 从而处于同一温度或极小温度梯度状态下, 保证整个熔体同时进入过冷状态, 实现同时形核。 即电磁搅拌的作用是获得等轴晶形核的动力学条件。 熔体处理使合金在结晶前形成大量的有效形核核心(TiAl3+L→α(Al), 665℃), 并在电磁搅拌作用下均匀分布于整个熔体中, 因此在较小的过冷度下就可实现整个熔体同时形核。 在以后的长大过程中, 受到相邻晶核长大阻力的影响, 不可能(或极少)形成发达的枝晶, 从而得到理想的球状晶粒结构。 而在单纯的电磁搅拌工艺中, 由于大量形核是在较大过冷度条件下进行的, 如果搅拌时间较短, 搅拌结束温度较高(过冷度不够), 就将有一部分晶粒是在电磁搅拌结束以后才形核的, 因此仍然按发达枝晶方式结晶, 最终形成等轴晶和树枝晶并存的半固态组织。
2.3 搅拌方式对半固态显微组织的影响
比较“熔体处理+双向电磁搅拌”工艺(图5(a))和“熔体处理+单向电磁搅拌”工艺(图6)制备的半固态A356.2合金的显微组织可见, 在熔体处理工艺和其它搅拌参数(0.03%Ti, 0.04%Sr, f=20Hz, U=200V, θ0=720℃, t=160s)完全相同的情况下, 后者的α(Al)相晶粒不仅形貌较差, 而且卷液现象(图6中白点)严重。 这是由于单向电磁搅拌的搅拌力不足所致。 电磁搅拌力跟磁场转速与熔体流速之间的速度差密切相关。 单向电磁搅拌时, 磁场与熔体同向运动, 二者的速度差有限; 而双向电磁搅拌利用熔体的运动惯性产生很大的速度差和惯性冲击, 从而使搅拌效率大为提高。

图6 “熔体处理+单向电磁搅拌”工艺制备α(Al)相的SEM照片
Fig.6 SEM micrograph of α(Al) phase prepared by multiple processing of melt treatment and unilateral electromagnetic stirring (Fc=0.63)
2.4 浇注温度和制备时间对半固态显微组织的影响
采用搅拌结束温度来控制浆料制备时间, 即从浇注温度到达5%固相率(即607℃)时所需的时间, 作为浆料制备时间。 从A356.2合金在本电[CM(22]磁搅拌装置中的热分析曲线(图7)可知, 熔体从720、700、 680、 660、 640℃降温至607℃时, 所需时间依次约为160、 140、 115、 92、 67s。
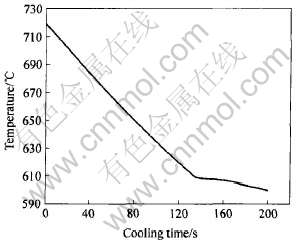
图7 A356.2合金的热分析曲线
Fig.7 Thermal analysis curve of A356.2 alloy
分析图5(a)~(e)可以看出, 在其它参数(0.03%Ti, 0.04%Sr, f=20Hz, U=200V, Δt=5s)相同的条件下, 浇注温度θ0从720℃降至640℃(相应地, 搅拌时间t从160s减至67s)时, α(Al)晶粒的形貌和尺寸变化不大(Fc=0.78~0.81, Dc=111~122.6μm)。 这表明, 在冷速较快(本装置没有专门的加热保温措施, 冷速为0.7K/s)的情况下, 可以采取较低的浇注温度来缩短半固态浆料的制备时间。 其原因分析如下: 制备非枝晶浆料的关键是, 在合金冷却经过液相线时, 形成快速冷却与对流的复合作用, 保证整个熔体均处于形核和凝固中; 形成大量的超过临界尺寸的初生晶核后, 搅拌就失去了作用, 即可停止搅拌, 初生晶粒就会自发长大成球状晶粒。 Flemings等[13-15]研究表明, 当固相率达到3%~7%时, 搅拌作用不再对最终的显微组织产生影响或影响甚微。
需要说明的是, 至于640℃是不是最低的许可浇注温度(即最佳的浇注温度), 以及是否可以采取适当强冷措施来进一步缩短制备时间, 尚有待进一步研究。
2.5 搅拌频率对半固态显微组织的影响
图8所示为不同搅拌频率下A356.2合金半固态的显微组织和定量分析结果。 可以看出, 在本搅拌过程(冷速为0.7K/s, 搅拌速度≤1000r/min)中, 搅拌频率对α(Al)的影响可分为3个阶段: 当搅拌频率较低(5Hz)时, 搅拌强度较低, 不足以使外来形核基底完全均布于整个熔体, 故仍有部分晶粒按发达枝晶方式结晶(Fc=0.68, Dc=138.1μm, 图8(a)); 当搅拌频率达到一定值(15~20Hz)时, 搅拌强度足以使晶粒按照等轴晶方式结晶, 但对晶核周围的溶质偏析层的均匀化程度不够, 与较薄的溶质偏析层邻近的晶粒可能产生合并长大, 故球状结构晶粒的尺寸较大((Fc=0.75~0.81, Dc=118.4~120μm, 图8(c)和(d)); 当搅拌频率足够高(25~30Hz)时, 搅拌强度不但可以保证等轴晶方式结晶, 而且使晶核周围的溶质偏析层均匀化良好, 因而球状结构晶粒的尺寸大大减小((Fc=0.81~0.84, Dc=83~84.4μm, 图8(e)和(f))。 因此, 在冷却速度较快、 搅拌速度较低的情况下, 提高搅拌频率不但有助于优化晶粒形貌, 而且具有相当的晶粒细化作用。

图8 “熔体处理+双向电磁搅拌”工艺下搅拌频率对α(Al)相形貌和尺寸的影响
Fig.8 Effect of stirring frequency on morphologies and sizes of α(Al) phase by multiple processing of melt treatment and reversible electromagnetic stirring
3 结论
1) 研制的双向多级速电磁搅拌装置与“熔体处理+双向电磁搅拌”复合技术, 具有较高的浆料制备效率, 可实现A356.2合金半固态浆料的在线制备, 从而为新型流变成形技术的实现提供了可能。
2) 采用如下参数: 0.03%Ti(Al-5Ti-B)和0.04%Sr(Al-10Sr)、 正-反无间歇双向搅拌、 浇注温度θ0=640℃、 搅拌频率f=25~30Hz、 输出电压U=220V、 单向搅拌时间Δt=5s、 搅拌时间t=67s, 可获得形状系数大于0.8、 初晶尺寸在80~90μm之间的A356.2半固态浆料。
3) 如果没有适当的辅助工艺, 仅仅依靠常规细化剂和变质剂的物理化学作用来实现半固态浆料的制备, 是十分困难的。
4) 在冷速较快(≥0.7K/s)时, 采取较低的浇注温度可较大缩短半固态浆料制备时间。
5) 在冷速较快(≥0.7K/s)、 搅拌速度较低(≤1000r/min)的情况下, 提高搅拌频率不但有助于优化晶粒形貌, 而且具有相当的晶粒细化作用。
REFERENCES
[1]冯鹏发, 唐靖林, 李双寿, 等. 半固态合金流变成形技术的研究现状与发展[J]. 铸造, 2004, 53(12): 963-967.
FENG Peng-fa, TANG Jing-lin, LI Shuang-shou, et al. Progress and prospect of research and application of semi-solid alloy rheoforming processes[J]. Foundry, 2004, 53(12): 963-967.
[2]Wang K K, Hsuan P, Wang N, et al. Method and Apparatus for Injection Molding of Semi-Solid Metals[P]. US 5501266, 1996-03-26.
[3]Ji S, Fan Z, Bevis M J. Semi-solid processing of engineering alloys by a twin-screw rheomoulding process[J]. Materials Science and Engineering A, 2001, A299: 210-217.
[4]Shibata R, Kaneuchi T, Soda T, et al. Formation of spherical solid phase in die casting shot sleeve without any agitation[A]. Proceedings of the 5th International Conference on Semi-Solid Processing of Alloys and Composites [C]. Golden, Colorado: Colorado School of Mines, 1998. 465-470.
[5]洪俊杓, 金宰民, 金玟秀, 等. 用于流变铸造的模铸法和设备[P]. CN 1485170A, 2004-03-31.
HONG Jun-shao, JIN Zai-min, JIN Wen-xiu, et al. The Method and Equipment of Die Casting for Rheocasting[P]. CN 1485170A, 2004-03-31.
[6]毛卫民, 赵爱民. 球状初晶半固态金属或合金浆料直接成型方法及装置[P]. CN 1411932A, 2003-04-23.
MAO Wei-min, ZHAO Ai-min. The Method and Equipment of Direct Moulding of Semi-Solid Slurry of Metals or Alloys with Spherical Primary Crystal[P]. CN 1485170A, 2004-04-23.
[7]Toshio H, Kapranos P. Simple rheocasting processes [J]. Journal of Materials Processing Technology, 2002, 130-131: 594-598.
[8]乐启炽, 崔建忠, 路贵民, 等. 两相区铸造AZ91D半固态坯料的部分重熔工艺与组织演变[J]. 中国有色金属学报, 2003, 13(6): 1488-1493.
LE Qi-chi, CUI Jian-zhong, LU Gui-min, et al. Microstructure evolution and partially remelting processing of two-phase-region casting AZ91D semisolid slurry ingot [J]. The Chinese Journal of Nonferrous Metals, 2003, 13(6): 1488-1493.
[9]路贵民, 董杰, 崔建忠. 7075合金液相线半连续铸造与二次加热的合金组织[J]. 中国有色金属学报, 2001, 11(2): 211-215.
LU Gui-min , DONG Jie, CUI Jian-zhong. Casting and remelted microstructures of 7075 alloy cast by liquidus semi-continuous casting[J]. The Chinese Journal of Nonferrous Metals, 2001, 11(2): 211-215.
[10]崔建忠, 乐启炽, 路贵民. 镁合金超低温铸造制取半固态浆方法[P]. CN 1460566A, 2003-12-10.
CUI Jian-zhong, LE Qi-chi, LU Gui-min. The Method of Ultra-Low Temperature Casting for Semi-Solid Slurry Making of Magnesium Alloys[P]. CN 1460566A, 2003-12-10.
[11]LUO Shou-jing, JIANG Ju-fu, WANG Ying, et al. Mechanics and forming theory of liquid metal forging[J]. Trans Nonferrous Met Soc China, 2003, 13(2): 369-375.
[12]Uchida M. Feature of UBE squeeze process and UNRC process (semi-solid casting)[A]. 李荣德. 第三届中国国际压铸会议论文集[C]. 沈阳: 东北大学出版社, 2002. 207-219.
Uchida M. Feature of UBE squeeze process and UNRC process (semi-solid casting)[A]. LI Rong-de. Proceedings of the 3rd China International Conference on Die Casting[C]. Shenyang: Northeastern University Press, 2002. 207-219.
[13]Yurko J A, Martinez R A, Flemings M C. Commercial development of the semisolid rheocasting (SSRTM) process[J]. Metallurgical Science and Technology, 2003, 21(1): 10-15.
[14]Flemings M C, Martinez R A, de Figueredo A M. Metal Alloy Compositions and Process[P]. US 20020096231, 2002-07-25.
[15]Yurko J. Semi-solid rheocasting—increasing the capabilities of die casting[J]. Die Casting Engineer, 2004(1): 50-52.
[16]唐靖林, 殷雅俊, 范钦珊, 等. 液固温区不同初生α相形态A356合金的流变行为[J]. 中国有色金属学报, 2002, 12(3): 430-435.
TANG Jing-lin, YIN Ya-jun, FAN Qin-shan, et al. Rheological behavior of semisolid A356 alloy with different morphology of primary α phases [J]. The Chinese Journal of Nonferrous Metals, 2002, 12(3): 430-435.
[17]Kori S A, Murty B S, Chakraborty M. Development of an efficient grain refiner for Al-7Si alloy and its modification with strontium[J]. Materials Science and Engineering A, 2000, 283A: 94-104.
[18]汪沛雨, 徐淑清, 张新颖. Al-Si-Cu合金加入Sr复合变质剂的变质效果[J]. 特种铸造及有色合金, 1995(2): 6-8.
WANG Pei-yu, XU Shu-qing, ZHANG Xin-ying. The modification effect of strontium-containing composite modifier on Al-Si-Cu alloy[J]. Special Casting and Nonferrous Alloys, 1995(2): 6-8.
(编辑陈爱华)
基金项目: 航天支撑技术基金资助项目(2002-HT-QHDX)
收稿日期: 2005-05-31; 修订日期: 2005-10-17
作者简介: 冯鹏发(1972-), 男, 博士研究生
通讯作者: 唐靖林, 副教授; 电话: 010-62772502; E-mail: tangjl@mail.tsinghua.edu.cn