文章编号:1004-0609(2009)03-0411-07
高能球磨制备纳米WC-MgO粉末的反应模式及判据
吴彩霞1, 2,朱世根1, 2,马 俊1, 2,张梅琳1
(1. 东华大学 机械工程学院,上海 201620;
2. 东华大学 材料科学与工程学院,上海 201620)
摘 要:以WO3、Mg和石墨粉为原材料,通过XRD、SEM 和TEM对粉末的结构特征进行表征。结合Magini模型和杨君友模型界定扩散反应和自蔓延反应两种高能球磨合成WC-MgO反应模式的能量区域,并通过球磨能量图阐明球磨速度、球料比和球磨时间等工艺参数对不同反应模式的影响。结果表明:在一定球磨条件下,当有效强度因子大于38.24 kJ/(g·s)时,合成WC-MgO的反应模式为自蔓延反应,所需的球磨总能量介于21.51×109 J/g和61.82×109 J/g之间;当有效强度因子为22.12~38.24 kJ/(g·s)时,合成WC-MgO的反应模式为扩散反应,所需的最小球磨总能量为112.83×109 J/g。
关键词:WC-MgO;纳米复合粉末;高能球磨;反应模式
中图分类号:TF 123.7 文献标识码:A
Reaction mode and criterion of nanocomposite WC-MgO powders prepared by high-energy ball milling
WU Cai-xia1, 2, ZHU Shi-gen1, 2, MA Jun1, 2, ZHANG Mei-lin1
(1. College of Mechanical Engineering, Donghua University, Shanghai 201620, China;
2. College of Materials Science and Engineering, Donghua University, Shanghai 201620, China)
Abstract: The synthesis of nanocomposite WC-MgO powders was investigated by high-energy ball milling of the mixture powders WO3, graphite and Mg at the mole ratio of 1?1?3. The energy region of diffusion and self-propagation reaction (SHS) was defined using a refined model based on Magini model and YANG Jun-you model. The effects of milling parameters conditions (including milling speed, ball to powder mass ratio and milling time) on the reaction mode were illuminated by the obtained milling energy map. The results show that the formation mechanism of WC-MgO is SHS when the effective extensive factor is above 38.24 kJ/(g·s), and it can be diffusion providing that effective extensive factor is 22.12?38.24 kJ/(g·s). As the energy map demonstration, the total energy for fabricating WC-MgO required for SHS is 21.51×109?61.82×109 J/g, while more than 112.83×109 J/g is necessary for diffusion mode.
Key words: WC-MgO; nanocomposite powders; high-energy ball milling; reaction mode
机械合金化(MA)方法由于成本低、工艺设备简单,已成为制备各种纳米复合粉体材料的一种重要制备方法[1?8]。EL-ESKANDARAY[7?8]最先采用该技术对WO3、Mg和C粉末进行球磨,利用球磨引起原始粉末间的化学反应,在室温下合成纳米WC-MgO复合粉末,并对获得的粉末通过等离子活化烧结得到块体材料。研究表明,晶粒细小、粒径分布均匀的WC-MgO粉末经过烧结后不仅具有较高的硬度,同时还具备很好的韧性。这种材料由于具有优异的性能、简便的制备方法和低廉的制备成本,可以应用于制造切削刀具、挖掘工具以及耐磨零件等,是一种极具工业应用前景的纳米复合材料。
一般认为,机械合金化高能球磨方法的反应模式有两种,即通过原子扩散反应逐渐实现合金化和自蔓延反应实现合金化[9?12]。扩散型反应球磨中粉末被反复破碎和焊合,产生大量新的结合界面,形成细化的多层状复合颗粒,继续球磨,随着塑性变形、内部缺陷(空位、位错等)增加,导致晶粒进一步细化,组元间发生固态扩散反应,这是一个逐渐反应过程,需要时间较长。而自蔓延型反应球磨中,球磨造成的剧烈碰撞和局部温升,都有可能点燃反应,反应一旦开始将会放出大量的燃烧热,这些燃烧热又激活邻近区域粉末间的放热反应,所有反应在极短的时间内完成,但是放出的大量燃烧热常常会引起爆炸现象。高能球磨中反应采用哪种模式进行取决于很多因素,如原始粉末的热力学性能、原子扩散能力及其力学性能等,其中最重要的因素是球磨速度、球料比、磨球直径等影响球磨过程中磨球转移给粉末的能量的工艺参数。SURYANARAYANA[13]认为,如果粉末获得的能量较低则以扩散反应机理进行合金化反应,相反,如果能量较高则以自蔓延反应机理进行合金化反应。
高能球磨合成WC-MgO纳米复合粉末的反应模式与球磨过程中的能量转移有关。根据最近研究结 果[14?19],球磨能量图是研究球磨工艺与球磨能量的关系和球磨能量与反应模式之间的关系最有效的方法之一。BURGIO等[14?15]首先用一组动力学方程估算单次碰撞过程中磨球传递给粉末的能量。MAGINI等[16]在此基础上进一步进行研究,用每次碰撞能和填充系数建立球磨图,并应用于Pd-Si、Fe-Zr 和Ti-Al系统的球磨过程分析。MURTY等[17]和ROJAC等[18]也分别给出了能量图,阐明Ti50Ni50和NaNbO3材料的高能球磨过程。然而,球磨能量图在高能球磨制备WC-MgO纳米复合粉末中的应用几乎没有。在本研究中,主要涉及球磨工艺条件和合成WC-MgO的反应模式之间的关系,并结合Magini-Iasonna和杨君友模型[19]界定扩散反应和自蔓延反应两种反应机理的能量区域,使获得的能量图有助于更好地理解高能球磨法制备WC-MgO纳米复合粉末的球磨过程,为工艺过程的控制及优化提供依据。
1 实验
本研究中采用WO3(纯度99.9%、平均粒径1.3 μm),石墨(纯度99.9%、平均粒径1 μm)和Mg(纯度为99.5%、平均粒径50 μm)为原材料,利用南京大学仪器厂生产的QM?1SP4型行星式球磨机,在氩气保护下进行球磨。球磨罐和磨球材质为硬质合金,磨球直径为10 mm,每个磨球质量为6.67 g,球磨机球磨试验的转速为100、150和200 r/min。在每个转速下都进行了球料比为5?1、10?1、15?1和20?1的球磨试验。为了确定粉末的反应情况,在球磨过程中间歇地取出部分产物,采用X射线衍射仪(RIGAKU, D/Max? 2550PC, Japan)、扫描电子显微镜(JEOL, JSM?5600LV, Japan)和透射电子显微镜(JEM?2010, Japan)对粉末进行表征和分析。粉末的晶粒尺寸根据XRD衍射谱采用Scherrer公式估算:

式中 β为经仪器宽度校正的衍射峰的半高宽(FWHM,以弧度计算);λ为X射线波长(0.154 20 nm);k为Scherrer常数,取0.89。
2 结果与分析
图1(a)所示为球磨速度200 r/min,球料比15?1条件下球磨不同时间后粉末的XRD谱。从图可看出,球磨4 h,只有原始粉末WO3、Mg和C的衍射峰,继续球磨0.5 h后,原始粉末经过反应生成WC和MgO。这种合成过程类似于自蔓延反应,即WC-MgO在较短的时间内生成。此外,随着球磨时间的延长,衍射峰逐渐宽化,说明球磨使粉末晶粒细化。图2(b)所示为球磨速度100 r/min,球料比15?1条件下球磨不同时间后的XRD谱。在球磨初期,也只有WO3、Mg和C的衍射峰,球磨40 h后,出现了少量WC和MgO相的衍射峰与之共存,球磨时间延长,原始粉末的衍射峰逐渐减弱直至消失,最终合成WC-MgO复合粉末。这种合成过程是一种扩散反应,即需经过较长时间的反应逐渐合成WC-MgO。在其它球磨速度和球料比条件下球磨不同时间后得到的XRD谱中,可以得到类似于图1(a)和(b)所示的结果,但是在不同球磨条件下合成WC-MgO所需的时间不同。另外,在球磨速度为100 r/min,球料比为10?1的条件下球磨100 h,无法合成WC-MgO复合粉末,如图1(c)所示。这可能是由于在球磨强度较低的情况下,粉末获得的能量太低,不足以使粉末间发生扩散反应。由图1(d)可见,合成WC-MgO复合粉末所需的时间一般是随着球磨速度和球料比的增加而缩短(根据XRD谱),说明在一定的球磨强度下,可以在较长时间的球磨过程中通过扩散反应合成WC-MgO。根据衍射峰的半高宽,用Scherrer公式计算得到晶粒的平均尺寸约为25 nm。
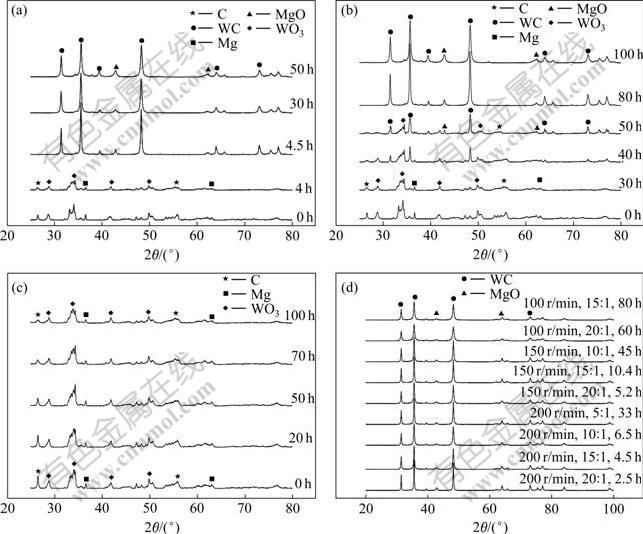
图1 球磨不同时间后粉末的XRD谱
Fig. 1 XRD patterns of powders as function of milling time under 200 r/min, 15?1(a), 100 r/min, 15?1(b), 100 r/min, 10?1(c) and different milling conditions(d)
图2所示为球磨速度和球料比与合成纳米WC- MgO复合粉末所需要时间之间的关系。由图2可见,合成WC-MgO复合粉末所需的时间一般是随着球磨速度和球料比的增加而缩短,与XRD分析结果(见图1(d))一致。同时,在较低的球磨强度下,即在较低的球磨速度和较低的球料比下,球磨较长一段时间,也能合成WC-MgO复合粉末。
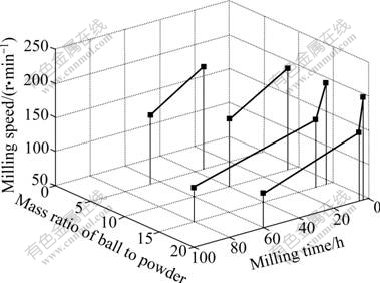
图2 高能球磨合成WC-MgO复合粉末的工艺参数关系图
Fig.2 Relationship of milling parameters during synthesis of WC-MgO powders by high-energy ball milling
图3所示为未球磨之前及在球磨速度100 r/min、球料比15?1的条件下球磨不同时间得到的粉末的SEM像,作为通过扩散反应合成纳米WC-MgO复合粉末的一个例子。由于球磨过程中的反复破碎和冷焊作用,球磨时间从0 h到80 h,粉末的尺寸明显减小。从图3(b)、(c)中可发现球磨粉末中有少量大颗粒,而且分布不均匀,这可能是球磨过程中过冷焊造成的。需要指出的是,粉末的实际晶粒尺寸是纳米级的,SEM像中看到的大颗粒是纳米晶的团聚体。在TEM的高能电子束下这些团聚体可以被分散开。图4所示为分散开的纳米WC-MgO颗粒的TEM明场像和选区衍射图(SADP)。图4中深黑色颗粒为WC,浅灰色颗粒为MgO。从明场像还可以看出,不规则形状的WC和MgO颗粒分布较均匀,而且大部分颗粒的尺寸为20~30 nm,与XRD分析的结果基本一致。选区衍射图表明球磨所得的粉末为WC-MgO复合粉末,如图4(b)所示。因此,用扩散反应可以获得纳米级的WC-MgO复合粉末。
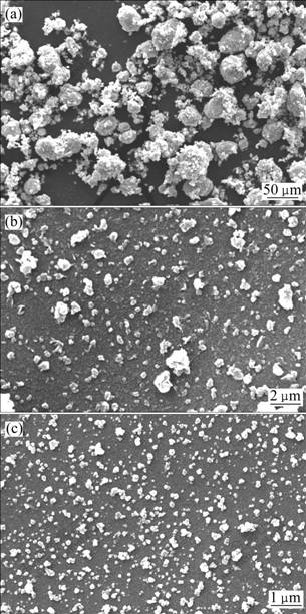
图3 球磨不同时间后粉末的SEM像(100 r/min, 15:1)
Fig.3 SEM micrographs of as-milled powders at milling speed of 100 r/min and mass ratio of ball to power of 15?1 after different time of milling: (a) 0 h; (b) 50 h; (c) 80 h
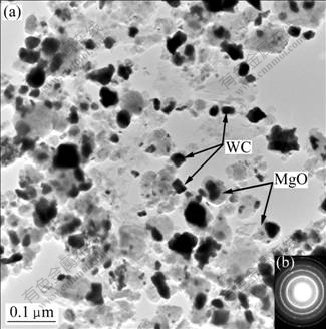
图4 球磨80 h后粉末的明场像和选区衍射图(100 r/min, 1:5)
Fig.4 BFI(a) and corresponding SADP(b) of as-milled powders at milling speed of 100 r/min and mass ratio of ball to power of 15?1 after milling 80 h
3 讨论
由上述实验结果可知,球磨速度、球料比和球磨时间等工艺参数可以影响高能球磨制备WC-MgO复合粉末的过程。合成WC-MgO复合粉末所需的时间随着球磨速度和球料比的增加而缩短,而且在不同球磨条件下其反应模式也不同。通过分析球磨过程中的能量转移,可以更好地解释这些结果。MAGINI等[16]、MURTY等[17]和杨君友等[19]都分别对行星球磨过程中的能量转移进行过研究,并都提出了各自的理论模型。本文作者在这些理论模型基础上,结合QM-1SP4行星球磨机的各个参数,对高能球磨法制备WC-MgO复合粉末的过程进行能量分析。
球磨过程中磨球运动的平均线速度(vb)和平均自由程(S)分别表示为[19]


式中 ωp为球磨速度,r0、VG分别为罐子的半径和容积,rb为磨球的半径,Rbp为球料比,mp为每次实验装入罐子的粉末质量。本实验中r0=0.038 m,VG= 250 mL,rb=0.005 m,mp=20 g。单个球的碰撞频率(
)由下式可得:

单个球每次碰撞转移到单位质量粉末的能量为[16]

式中 ?E为单个球每次碰撞转移到粉末的能量;mmax为碰撞过程中捕获的粉末的最大质量;Rp为球磨机的盘子的半径,本实验中Rp=0.115 m;ρb、E和db分别是磨球的密度、弹性模量和直径,对于硬质合金磨球,ρb和E分别为15.55×106 g/m3和5.5×1011 N/m2。面密度σ通过测量最初几个小时球磨后球的质量增量后取平均值,为0.25 kg/m2。值得注意的是,这里的能量是单个球在一次碰撞过程中捕获的少量粉末所吸收的能量,并不是整个系统的碰撞能。在考虑球料比的影响时,还须考查多个球间的相互作用,则单位质量粉末单位时间内获得的总能量为

式中 nb为磨球的个数;φb为与填充量有关的阻碍因子,当粉末的填充量低于1/3,φb接近1[16],本实验中由于粉末的填充量都小于1/3,所以φb取值为1。有效强度因子Eb可表示为

在假设能量全部转移给粉末的情况下,需要考虑一定时间内的能量积累,于是得到球磨总能量Et为[17]

表1列出了不同球磨条件下的各参数,并根据有效强度因子的计算结果绘制了高能球磨合成WC-MgO的球磨能量图,如图5所示。图中比较了球磨速度和球料比对有效强度因子的影响。通过有效强度因子可以界定两种反应模式产生的球磨能量条件:在一定的球磨条件下,若有效强度因子大于38.24 kJ/(g·s),则合成WC-MgO的反应模式为自蔓延反应;若有效强度因子小于22.12 kJ/(g·s),不能合成WC-MgO复合粉末;只有当有效强度因子为22.12~38.24 kJ/(g·s)时,可以通过扩散反应机理合成WC-MgO复合粉末。
表1 不同球磨条件下的参数
Table 1 Parameters under different milling conditions

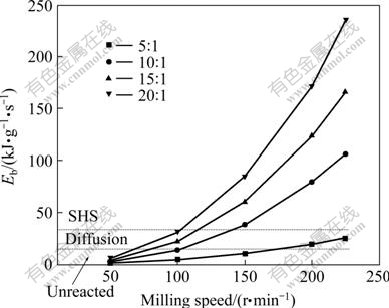
图5 不同球磨条件下合成WC-MgO的球磨能量曲线
Fig.5 Milling curves of WC-MgO under different milling conditions
图6所示为自蔓延和扩散反应合成WC-MgO的能量图。由图可以看出,自蔓延反应和扩散反应机理合成WC-MgO所需要的总球磨能量不同。对于自蔓延反应合成WC-MgO,所需总能量为21.51×109~ 61.82×109 J/g;而对于扩散反应合成WC-MgO,所需最小总能量为112.83×109 J/g,几乎为自蔓延反应的5倍,因而其所需要的球磨时间远超过前者。产生上述差别可归因于:1) 对于自蔓延反应机理而言,磨球间少量粉末在短时间内获得足够能量,可以越过反应的能量势垒,优先生成WC-MgO,同时,释放的热能有利于附近粉末继续反应,故所需总球磨能量少;2) 对于扩散反应机理而言,扩散反应是吸热过程,消耗了大量的球磨能量,需要的球磨反应时间也较长,热量损失也大,所以WC-MgO的合成需要较大的球磨能量。
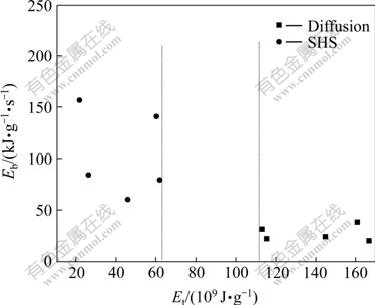
图6 自蔓延和扩散反应合成WC-MgO的能量图
Fig.6 Energy map of WC/MgO synthesized by SHS and diffusion
由上述分析可知,通过自蔓延反应和扩散反应都可以获得纳米WC-MgO复合粉末。对于自蔓延反应合成WC-MgO,反应在极短的时间内完成,但放出的大量燃烧热常常会引起很危险的爆炸现象,可控性差,从而限制了这种工艺的实际应用。而对于扩散反应合成WC-MgO,由于其反应速率较低,放出的反应热不足以引起爆炸现象,较安全可控。本文作者结合Magini和杨君友模型讨论了上述关于WC-MgO的球磨能量的讨论,较系统地考虑了球磨过程中的多个参数,但是也存在一定的不足,例如未考虑球磨过程碰撞能的损失问题,因而其计算值偏大,与实际情况有差距,但基于同等假设球撞击能量全部为粉末所吸收的前提下,对实际球磨工艺参数的选择仍具有较好的指导意义。
4 结论
1) 建立了高能球磨制备纳米WC-MgO复合粉末过程的工艺参数关系曲线、球磨能量曲线和反应能量图,并通过所得能量图阐明了球磨工艺条件对合金化反应模式的影响。
2) 确定了扩散反应和自蔓延反应两种反应模式的能量区域:当有效强度因子大于38.24 kJ/(g·s)时, WC-MgO的反应模式为自蔓延反应;当有效强度因子小于22.12 kJ/(g·s)时,无法合成WC-MgO复合粉末;仅当有效强度因子为22.12~38.24 kJ/(g·s),可以通过扩散反应机理合成WC-MgO复合粉末。
3) 通过自蔓延反应合成WC-MgO,所需总能量为21.51×109~61.82×109 J/g;通过扩散反应逐渐合成WC-MgO,所需最小总能量为112.83×109 J/g。
REFERENCES
[1] EL-ESKANDARANY M S. Fabrication and characterizations of new nanocomposite WC/Al2O3 materials by room temperature ball milling and subsequent consolidation[J]. Journal of Alloys and Compounds, 2005, 391: 228?235.
[2] IVANOV E Y, SURYANARAYANA C, BRYSKIN B D. Synthesis of a nanocrystalline W-25wt.% Re alloy by mechanical alloying[J]. Mater Sci Eng A, 1998, 251: 255?261.
[3] KIM J W, CHUNG H S, LEE S H, OH K H, SHIM J H, CHO Y W. Mechanochemical synthesis of TiN/TiB2/Ti-silicide nanocomposite powders and their thermal stability[J]. Intermetallics, 2007, 15: 206?210.
[4] LU L, LAI M O, NG C W. Enhanced mechanical properties of an Al based metal matrix composite prepared using mechanical alloying[J]. Mater Sci Eng A, 1998, 252(2): 203?211.
[5] JOARDAR J, PABI S K, MURTY B S. Milling criteria for the synthesis of nanocrystalline NiAl by mechanical alloying[J]. Journal of Alloys and Compounds, 2007, 429: 204?210.
[6] WOO K D, ZHANG D L. Fabrication of Al-7wt%Si-0.4wt%Mg/ SiC nanocomposite powders and bulk nanocomposites by high energy ball milling and powder metallurgy[J]. Current Applied Physics, 2004, 4(4): 175?178.
[7] EL-ESKANDARANY M S. Fabrication of nanocrystalline WC and nanocomposite WC-MgO refractory materials at room temperature[J]. Journal of Alloys and Compounds, 2000, 296(1/2): 175?182.
[8] EL-ESKANDARANY M S, OMORI M, KONNO T J, SUMIYAMA K, HIRAI T, SUZUKI K. Synthesizing of nanocomposite WC/MgO powders by mechanical solid-state reduction and subsequent plasma-activated sintering[J]. Metall Mater Trans A, 2001, 32: 157?164.
[9] ZHANG H A, LIU X Y. Analysis of milling energy in synthesis and formation mechanisms of molybdenum disilicide by mechanical alloying[J]. International Journal of Refractory Metals and Hard Materials, 2001, 19: 203?208.
[10] YEN B K, AIZAWA T, KIHARA J. Synthesis and formation mechanisms of molybdenum silicides by mechanical alloying[J]. Mater Sci Eng A, 1996, 220: 8?14.
[11] ATZMON M. In situ thermal observation of explosive compound-formation reaction during mechanical alloying[J]. Physical Review Letter, 1990, 64: 487?490.
[12] KIRAKOSYAN KH G, MANUKYAN KH V, KHARATYAN S L, MNATSAKANYAN R A. Synthesis of tungsten carbide- carbon nanomaterials by combustion reaction[J]. Materials Chemistry and Physics,2008, 110 (2/3): 454?456.
[13] SURYANARAYANA C. Mechanical alloying and milling[J]. Progress in Materials Science, 2001, 46: 127?128.
[14] MAGINI M, BASILI N, BURGIO N, ENNAS G, MARTELLI S, PADELLA F. Mechanical alloying of the Fe-Zr system. Correlation between input energy and end products[J]. Il Nuovo Cimento, 1991, 13D: 459.
[15] BURGIO N, IASONNA A, MAGINI M, PADELLA F. Mechanical alloying of the Fe-Zr system in different milling conditions[J]. Le Journal de Physique Colloques, 1990, 51: C4-265?C4-271.
[16] MAGINI M, IASONNA A, PADELLA F. Ball milling: An experimental support to the energy transfer evaluated by the collision model[J]. Scripta Material, 1996, 34(1): 13?19.
[17] MURTY B S, MOHAN RAO M, RANGANATHAN S. Milling maps and amorphization during mechanical alloying[J]. Acta Metallurgica et Materilia, 1995, 43(6): 2443?2450.
[18] ROJAC T, KOSEC M, MALI? B, HOLC J. The application of a milling map in the mechanochemical synthesis of ceramic oxides[J]. Journal of the European Ceramic Society,2006, 26(16): 3711?3716.
[19] 杨君友, 张同俊, 崔 崑, 胡镇华. 球磨过程中的碰撞行为分析[J]. 金属学报, 1997, 33(4): 381?385.
YANG Jun-you, ZHANG Tong-jun, CUI Kun, HU Zheng-hua. Analysis of impact behavior during ball milling[J]. Acta Metallurgica Sinica, 1997, 33(4): 381?385.
基金项目:上海市纳米科技专项基金资助项目(05nm05031)
收稿日期:2008-05-26;修订日期:2008-10-10
通讯作者:朱世根,教授;电话:021-67792006;E-mail: sgzhu@dhu.edu.cn
(编辑 李向群)