
Tensile properties and microstructure of AZ31B magnesium alloy sheet processed by repeated unidirectional bending
HUANG Guang-sheng(黄光胜)1,2, LI Hong-cheng(李红成)1,2, SONG Bo(宋 波)1,2, ZHANG Lei(张 雷)1,2
1. College of Materials Science and Engineering, Chongqing University, Chongqing 400045, China;
2. National Engineering Research Center for Magnesium Alloys, Chongqing University, Chongqing 400044, China
Received 3 February 2009; accepted 13 July 2009
Abstract: The mechanical properties of the AZ31B magnesium alloy sheet processed by repeated unidirectional bending (RUB) with a basal pole tilted in the rolling direction were systematically investigated at different temperatures. Compared with the as-received sheet exhibiting approximately the same average grain size, the fracture elongation increased while the proof stress decreased at room temperature. The initial texture had a significant influence on the mechanical properties at room temperature, while it showed a much weaker effect on the mechanical properties because of the activation of non-basal slips and initiation of dynamic recrystallization during deformation at elevated temperature.
Key words: repeated unidirectional bending; magnesium alloys; texture; mechanical properties; microstructure
1 Introduction
Magnesium alloys, the lightest metallic construction materials with high strength, good thermal conductivity and shock-absorbing characteristics, are considered one of green materials in the 21st Century[1]. For magnesium alloys with hexagonal closed-packed crystal structure, critical resolved shear stress (CRSS) of the non-basal slips is much higher than that of the basal slip at room temperature, thus the formability is limited at room temperature[2-3]. In addition, rolled magnesium alloy sheets have poor cold forming properties due to strong basal texture[4-5]. Therefore, it is very important to improve or weaken the basal texture for enhancing room temperature forming properties.
The texture of magnesium alloy sheets can be controlled by cross-rolling and different-speed-rolling (DSR). CHINO et al[6-8] and ZHANG et al[9] studied the cross-rolled AZ31 magnesium alloy sheets and found that cross-rolling could reduce the intensity of basal texture and increase the elongation, but the texture component has no significant change. WATANABE et al[10-11] and HUANG et al[12] investigated the mechanical properties of the AZ31 alloy sheets processed by DSR and reported that the basal pole tilted in the rolling direction. However, inclination angles with 5-15? to c-axis were limited.
Previous researches[13-14] showed that the basal texture of magnesium alloy sheets could be weakened by repeated unidirectional bending (RUB). In this study, the tensile properties of the sheet that underwent RUB were investigated and the texture evolution during tensile deformation was analyzed by electron-backscattered diffraction (EBSD) method.
2 Experimental
The as-received AZ31B rolled sheets with 0.8 mm in thickness were processed by RUB, and the schematic diagram of the RUB process is shown in Fig.1. The radius of the cylindrical support is 1 mm and the bending angle is 90?. The RUB process used in this experiment was six-pass bending at two orientations. This meant that after each bending pass, the sheet was turned over and the bending orientation was also changed in the next pass.
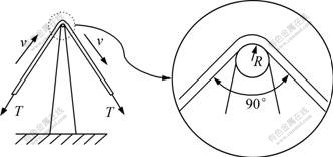
Fig.1 Schematic diagram of RUB
The sheets that underwent RUB were annealed at 533 K for 60 min. Tensile specimens with gauge size of 20 mm×10 mm were cut on the plate along the direction parallel to the rolling direction (RD) by wire-cutting. Uniaxial loading tests were carried out on HT91-02B computer- controlled experimental material servo drive at the temperatures ranging from 298 K to 673 K, and at strain rates ranging from 1×10-4 s-1 to 1×10-1 s-1.
The longitudinal section fracture microstructures of tensile specimens were observed by Nikon 200 metallurgical microscope and the texture evolution at 10% tensile deformation and 1×10-2 s-1 initial strain rate was analyzed by EBSD. The vertical profiles of the tensile specimens were observed by FEI-FEG Nova400 field emission scanning electron microscope (SEM) with equipment for Channel 5.0 HKL EBSD probe. The tensile specimens were polished by commercial AC-II electrolyte, and scanning step was 1 μm.
3 Results and discussion
3.1 Effect of RUB on crystal orientation
The pole figures of as-received sample shown in the Fig.2(a) indicated that a strong basal texture existed in magnesium alloy sheets. Strong pole intensity existed within 10? which was the angle between normal direction (ND) of sheet and c-axis of grain. Texture components of the sample that underwent RUB (Fig.2(b)) became more dispersive with more pole peaks appearing, and basal texture was weakened because c-axis became inclined from the ND towards the RD.
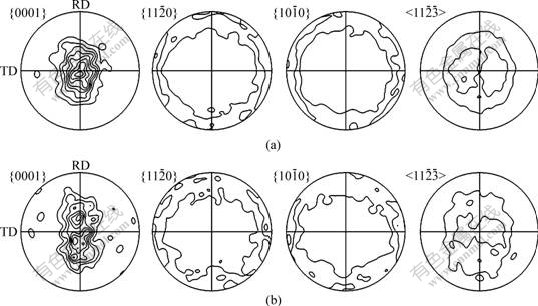
Fig.2 Pole figures of as-received sample and RUB sample: (a) as-received sample, max=8.55; (b) RUB sample, max=7.31. Levels= 1, 2, 3,… (RD: Rolling direction; TD: Transverse direction)
Fig.3 shows an EBSD map obtained by orientation-imaging microscopy (OIM) of the as-received sample and the sample that underwent RUB.The grains appeared in gray according to their different basal Schmid factor when the tensile stress was applied in the RD. Basal Schmid factor of as-received sample with strong basal texture was smaller, thus it was more difficult to activate the basal slip during deformation. However, for the sample that underwent RUB, soft-oriented grains of basal slip were obviously increased and average Schmid factor had an increase from 0.25 to 0.30. The strong basal texture of AZ31B magnesium alloy sheet was effectively improved by RUB. Compared with the as-received sample, a part of grains grew up slightly in the sample that underwent RUB, and average grain sizes of the as-received sample and the sample that underwent RUB measured by EBSD system were about 5.8 μm and 6.2 μm, respectively. Thus, the effect of grain size on the mechanical properties could be neglected.
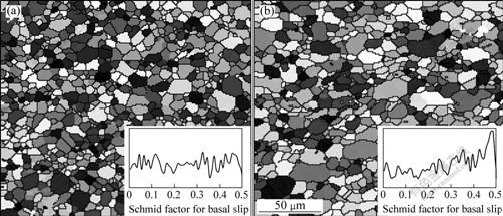
Fig.3 OIM images and distributions of basal Schmid factor: (a) As-received sample; (b) RUB sample
3.2 Microstructures and tensile properties
By the observation of the tensile fracture microstructures of the as-received samples and the samples that underwent RUB at different temperatures and strain rates, it was found that basal slip was the main deformation mechanism and a small number of twins appeared during the tensile deformation at the temperature of 298 K and 373 K. The fracture microstructure of tensile deformation at 473 K is shown in Fig.4 and the twins were not found. The microstructure of the sheet that underwent RUB was composed of equiaxed crystal at strain rate of 1×10-1 s-1. With a reduction of the strain rate, a large number of small grains were formed, especially at the strain rate of 1×10-4 s-1, because there is enough time for completely dynamic recrystallization. When samples were deformed at the temperatures of 573 K and 673 K, recrystallization grains grew up and new equiaxed structure was formed.
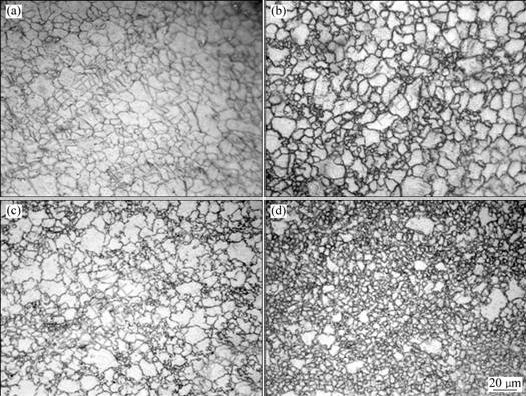
Fig.4 Fracture microstructures of RUB samples processed at 473K: (a)
=1×10-1 s-1; (b)
=1×10-2 s-1; (c)
=1×10-3 s-1; (d)
=1×10-4 s-1
Tensile tests of as-received sheets and the sheets that underwent RUB were performed. Fig.5 shows the fracture elongations of the sheets that underwent RUB. At room temperature, the fracture elongation of the sheets that underwent RUB was increased to about 25% from about 20%, which was not greatly influenced by the strain rate. With the increase of tensile temperature, the plasticity of AZ31B magnesium alloy sheets was improved obviously and the elongation increased significantly. At the same temperature, the elongation reduced with an increase of strain rate. The true tensile stress—strain curves of the magnesium alloy sheets that underwent RUB shown in Fig.6 indicated that dynamic recrystallization had obvious softening effect during deformation with an increase of deformation temperature. As a result, the peak stresses and work-hardening rates were decreased significantly with an increase of tensile temperature and the 0.2% proof strengths tended to increase at the same deformation temperature with an increase of strain rate. Thus, the sheets that underwent RUB showed low-strain-rate superplasticity at low temperature and high-strain-rate superplasticity at high temperature. Similar results of mechanical properties of as-received sheets were also obtained. The superplasticity mainly thanks to dynamic recrystallization and non-basal slips activated[15-16]. When tensile temperature was higher than 473 K, the fracture elongations of as-received sheets were higher than those of the RUB sheets, especially at lower strain rate. The exact reason is unclear, and further research is needed.
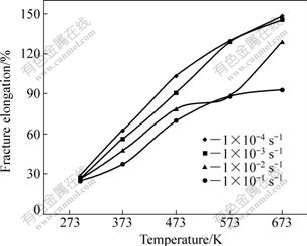
Fig.5 Fracture elongations of sheets that underwent RUB at different temperatures and strain rates
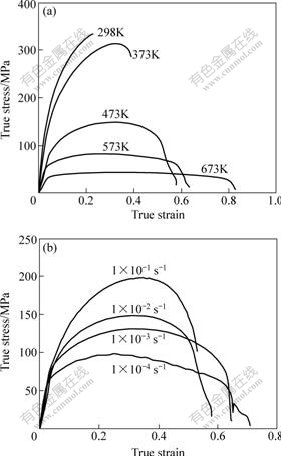
Fig.6 True stress—strain curves of RUB samples: (a) At strain rate of 1×10-2 s-1; (b) At temperature of 473 K
With an increase of tensile temperature, AZ31B magnesium alloy sheets were softened obviously and the proof strength tended to decrease. Fig.7 shows the proof strength at a strain rate of 1×10-2 s-1. When magnesium alloy sheets were tension deformed at room temperature, for the sheets that underwent RUB, proof strength showed a large decrease of about 40 MPa. For the sheets that underwent RUB, the c-axis orientation distribution became more dispersive and the basal texture was weakened so that average basal Schmid factor was increased. Thus, the basal plane slip can be more easily activated during plastic deformation. And Erichsen value of the sheets that underwent RUB was increased from 3.53 mm to 5.90 mm at room temperature[13]. However, with an increase of deformation temperature, differences of proof strength between as-received sheets and sheets that underwent RUB tended to decrease. According to the reported data[15], the CRSS of basal slip at room temperature is approximately 1/55 that of non-basal slip, and becomes 1/12 at 523 K. Thus, the contribution of basal slip tended to decrease with an increase of deformation temperature.
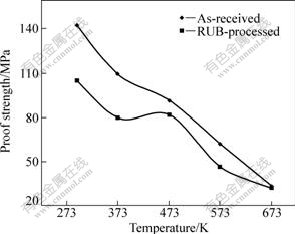
Fig.7 0.2% proof strength at strain rate of 1×10-2 s-1 for as-received sheet and RUB processed sheets in tensile directions of RD
3.3 Texture evolution of sheets underwent RUB during tensile deformation
Fig.8 shows the pole figures of tensile deformation with 10% elongation at 1×10-2 s-1. Pole figures of tensile deformation at 298 K shown in Fig.8(a) indicated that c-axes of grains mainly distributed along the RD. Compared with the pole figures of the sheet that underwent RUB, the c-axes of some grains tended to rotate toward the directions perpendicular to the tensile direction. Figs.8(b)-(d) showed that the tendency became more obvious with an increase of tensile temperatures. The c-axes of more grains would rotate towards the directions perpendicular to the tensile direction with an increase of elongation[17]. For tensile deformation at 573 K, the texture gradually evolved into the more concentrated type. The texture components were more concentrated to
and this trend became more apparent at 573 K (referring to the arrows in the pole figures). The reason can be the activation of multiple slip and preferred orientations of recrystallization grains.
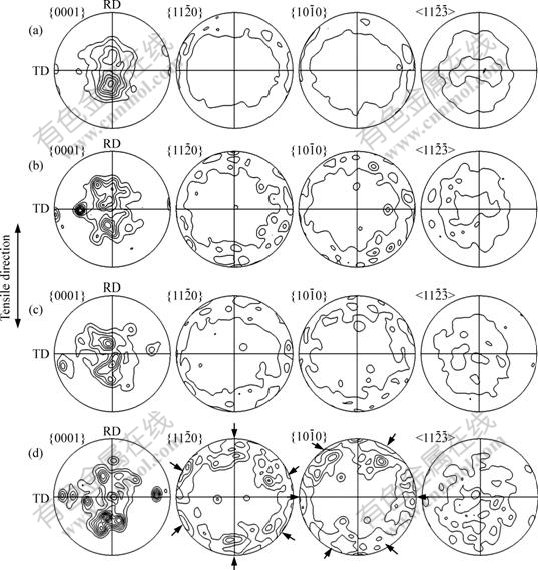
Fig.8 Pole figures of RUB samples with 10 % elongation at 1×10-2 s-1 corresponding to different temperatures: (a) 298 K, max=7.35; (b) 373 K, max=7.81; (c) 473 K, max=6.70; (d) 573 K, max=10.34. Levels=1,2,3,…
According to above discussion, for the magnesium alloy with strong basal texture, c-axis tended to distribute along the directions perpendicular to the tensile direction during uniaxial tension[17]. This indicated the c-axis could still be parallel to the ND or distribute along the TD. In other words, the grains were still the hard-oriented grains of basal slip during uniaxial tension. For the magnesium alloy with inclined texture, at the beginning stage of tension, the soft-oriented grains of basal slip can lead to a decrease of proof strength, especially at room temperature. With an increase of elongation, the c-axis tended to rotate towards the direction perpendicular to the tension direction; thus, the contribution of basal slip tended to decrease. Of course, the effect of texture evolution during tension on the mechanical properties was not a prime factor at room temperature. First, the tendency of texture evolution was not very obvious, and fracture elongation was very low at room temperature. Second, the work-hardening was a very important factor for the mechanical properties at room temperature. With an increase of deformation temperature, the c-axis rotated more easily to the directions perpendicular to the tensile direction during uniaxial tension, and with the activation of non-basal slip systems and initiation of dynamic recrystallization, the initial texture on mechanical properties of magnesium alloy sheets became weak.
4 Conclusions
1) The mechanical properties of the AZ31B magnesium alloy sheet underwent RUB with c-axes inclining towards the RD were improved at room temperature due to the increase of the average Schmid factor for basal slip system.
2) The influence of initial texture was weaker at elevated temperature on mechanical properties of magnesium alloy sheets because of the activation of non-basal slip systems and initiation of dynamic recrystallization.
3) With an increase of elongation, the c-axis tended to rotate towards the direction perpendicular to the tension direction. With an increase of tensile temperature, the trend became more obvious.
References
[1] MORDIKE B L, EBERT T. Magnesium properties- applications-potential [J]. Materials Science and Engineering A, 2001, 302: 37-45.
[2] STAROSELSKY A, ANAND L. A constitutive model for hcp materials deforming by slip and twinning: Application to magnesium alloy AZ31B [J]. International Journal of Plasticity, 2003, 19: 1843-1864.
[3] JEONG H T, HA T K. Texture development in a warm rolled AZ31 magnesium alloy [J]. Journal of Materials Processing Technology, 2007, 187/188: 559-561.
[4] BARNETT M R, NAVE M D, BETTLES C J. Deformation microstructures and textures of some cold rolled Mg alloys [J]. Materials Science and Engineering A, 2004, 386: 205-211.
[5] STANFORD N, BARNETT M R. Fine grained AZ31 produced by conventional thermo-mechanical processing [J]. Journal of Alloys and Compounds, 2008, 466: 182-188.
[6] CHINO Y, SASSA K, KAMIYA A, MABUCHIM. Enhanced formability at elevated temperature of a cross-rolled magnesium alloy sheet [J]. Materials Science and Engineering A, 2006, 441: 349-356.
[7] CHINO Y, SASSA K, KAMIYA A, MABUCHI M. Microstructure and press formability of a cross-rolled magnesium alloy sheet [J]. Materials Letters, 2007, 61: 1504-1506.
[8] CHINO Y, SASSA K, KAMIYA A, MABUCHI M. Stretch formability at elevated temperature of a cross-rolled AZ31 Mg alloy sheet with different rolling routes [J]. Materials Science and Engineering A, 2008, 473: 195-200.
[9] ZHANG Qing-lai, LU Chen, ZHU Yan-ping, DING Wen-jiang, HE Ji-hong. Effect of rolling method on microstructure and properties of AZ31 magnesium alloy thin sheet [J]. The Chinese Journal of Nonferrous Metals, 2004, 14(3): 391-397. (in Chinese)
[10] WATANABE H, MUKAI T, ISHIKAWA K. Differential speed rolling of an AZ31 magnesium alloy and the resulting mechanical properties [J]. Journal of Materials Science, 2004, 39: 1477-1480.
[11] WATANABE H, MUKAI T, ISHIKAWA K. Effect of temperature of differential speed rolling on room temperature mechanical properties and texture in an AZ31 magnesium alloy [J]. Journal of Materials Processing Technology, 2007, 182: 644-647.
[12] HUANG Xin-sheng, SUZUKI K, WATAZU A, SHIGEMATSU I, SAITO N. Improvement of formability of Mg-Al-Zn alloy sheet at low temperatures using differential speed rolling [J]. Journal of Alloys and Compounds, 2009, 479: 726-731.
[13] HUANG Guang-sheng, XU Wei, HUANG Guang-jie, LI Hong-cheng, PAN Fu-sheng. New method for improving formability of AZ31B magnesium alloy sheets [J]. Materials Science Forum, 2009, 610/613: 737-741.
[14] HUANG Guang-sheng, XU Wei, HUANG Guang-jie, LI Hong-cheng, SONG Bo. Textural evolution of AZ31B magnesium alloy sheets undergoing repeated unidirectional bending at room temperature [J]. Journal of Materials Sciences and Technology, 2009, 25(3): 365-369.
[15] SUZUKI M, SATO H, MARUYAMA K, OIKAWA H. Creep deformation behavior and dislocation substructures of Mg-Y binary alloys [J]. Materials Science and Engineering A, 2001, 319/321: 751-755.
[16] WATANABE H, TAKARA A, SOMEKAWA H, MUKAI T, HIGASHI K. Effect of texture on tensile properties at elevated temperatures in an AZ31 magnesium alloy [J]. Scripta Materialia, 2005, 52: 449-454.
[17] LIU Yi, WU Xin. An electron-backscattered diffraction study of the texture evolution in a coarse-grained AZ31 magnesium alloy deformed in tension at elevated temperatures [J]. Metallurgical and Materials Transactions A, 2006, 37: 7-17.
Foundation item: Project(50504019) supported by the National Natural Science Foundation of China; Project(2008BB4040) supported by the Natural Science Foundation of Chongqing Science and Technology Commission, China; Project(2008AA4028) supported by the Scientific and Technological Program of Chongqing Science and Technology Commission, China
Corresponding author: HUANG Guang-sheng; Tel: +86-23-65112239; E-mail: gshuang@cqu.edu.cn
DOI: 10.1016/S1003-6326(09)60092-3
(Edited by YANG Bing)