
Bioleaching of low-grade copper sulphides
YIN Sheng-hua(尹升华)1, WU Ai-xiang(吴爱祥)1, QIU Guan-zhou(邱冠周)2
1. School of Civil and Environment Engineering, University of Science and Technology Beijing,Beijing 100083, China;
2. School of Mineral Processing and Bioengineering, Central South University, Changsha 410083, China
Received 28 June 2007; accepted 9 November 2007
Abstract: The bioleaching behavior of low-grade copper sulphides under the condition of preferential solution flow was investigated through experiments. The experiment of bioleaching was conducted within the multifunction autocontrol bioleaching apparatus. The results show that the concentrations of Cu2+ and total Fe increase slowly at the beginning. The recovery rate decreases with the increase of depth of dump. The preferential solution happens within the fine region when the application rate is low, and the recovery rate of the fine region is higher than that of the coarse region. The content of fine ore particles within both fine and coarse regions increases during the leaching period, and the preferential solution flow shifts from fine region to coarse region. The surface of the ores at the top of dump is attacked seriously, and the ores in the middle is attacked slightly. There are plenty of crackles on the surface of bottom ores because of the precipitation layer on the surface.
Key words: preferential solution flow; copper sulphides; bioleaching; leaching ratio; surface morphology
1 Introduction
Low-grade ores, small and complicated ore bodies, waste ores and ores that are hard to be recovered by traditional method can be recovered by bioleaching[1-2]. The comprehensive utilizing rate and utilizing spectrum are enhanced by this technology, which has many advantages, such as economic, energy-efficient, pollution-free process and low capital requirements[3]. So the bioleaching technology shows further application in the exploitation of metal resource[4-6].
The bioleaching process involves the extraction of useful element from ores by bacteria and solution. The soluble metals were carried out by the flow of solution [7-8]. The six steps during bioleaching are outer diffusion, inner diffusion, leaching reaction, process of precipitation and hydrolysis of the element, transport- ation of microorganisms, heating and cooling of the bed.
The transportation of solute, momentum, heat and microorganism is achieved by the solution flow, with which all the processes above have close relationship [9-10]. So the solution flow is one of the most important factors that influence the bioleaching process[11]. Preferential solution flow is a prevailing phenomenon within the dump leaching[12]. The leaching rate and recovery efficiency of the dump are influenced by the preferential solution flow, so the practice of this technology is limited. The formation mechanism of preferential solution flow and its influence on the transportation of solute were discussed[13]. The bioleaching behavior under the condition of preferential solution flow was conducted in library, and metal ion concentration, leaching rate, ore size distribution, preferential solution flow and ore morphology were investigated systematically. The results of this experiment can provide theoretical guideline for the optimization of bioleaching process.
2 Experimental apparatus
The experiment was conducted within the multi- function auto-control bioleaching apparatus as shown in Fig.1. The diameter and depth of the column selected by this experiment were 159 and 1 300 mm, respectively. The volume of raised barrel and collective barrel was 30 L.
This apparatus consisted of circulation of heated water, aerated system, circulation of solution, datum collecting system, controlling cabinet, raised barrel, column and collective barrel. Besides the multi-function auto-control bioleaching apparatus, many other equipments were required for this experiment, such as refrigerator, bacterial counter, rotary shaker in air bath, sterilization machine, distiller and oscillating screen used for testing the ore size distribution of the sample.
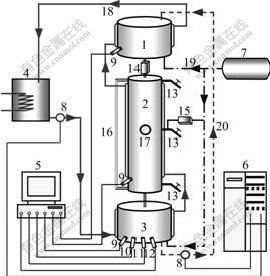
Fig.1 Multi-function auto-control bioleaching apparatus: 1 Raised barrel; 2 Column; 3 Collecting barrel; 4 Electrical bar; 5 Datum collection; 6 Control cabinet; 7 Air compressor; 8 Peristaltic pump; 9 Temperature sensor; 10 pH electrode; 11 Dissolved oxygen sensor; 12 Redox potential sensor; 13 Solution outlet; 14 Flow meter; 15 Gas flow meter; 16 Solution level gauge; 17 View pot; 18 Water circulation; 19 Aerated system; 20 Solution circulation
3 Experimental sample
3.1 Dump leaching of Dexing Copper Mine
The Dexing Copper Mine is a porphyry copper deposit. 1.17 billion tons of low-grade ores will be produced during the open pit mining, and the total copper metal is 1.2 million tons. Based on the good experiment result, a dump leaching plant with annual production of 2 000 t was built[14-15].
The chemical composition of the sample is shown in Tables 1 and 2. The main elements are Si, Al, Ca and Mg, with some Mo and As. The Cu grade is low and less than 1%. Most of the ores are primary sulfide copper, and contain small secondary copper sulfide and copper oxide. And some pyrites coexist within the ores.
Table 1 Chemical composition of ores in Dexing Copper Mine (mass fraction, %)
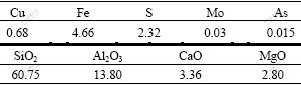
Table 2 Main minerals of ores in Dexing Copper Mine (mass fraction, %)
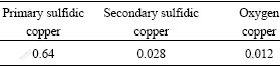
3.2 Size distribution of sample
800 kg samples were fetched from the dump leaching plant of Dexing Copper Mine. The samples were screened into two groups, fine ores and coarse ores. 18 kg ores selected from both groups were used by this experiment. And their size distributions are listed in Table 3.
Table 3 Size distribution of fine and coarse ores
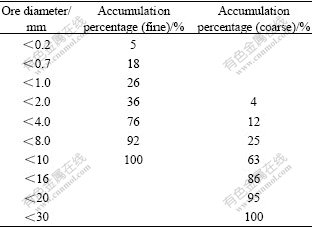
3.3 Surface morphology of samples
The surface morphology of both ore groups was analyzed with Scanning Electron Microscopy before experiment, as shown in Figs.2 and 3. The surface of course ores was compacted, and there were few pores and crackles. The pores and crackles of the fine ores were filled with other minerals, and the surface was little coarse. Main elements of both samples were Si and Al, with little amount part of Fe, Ca, S, Mg and Cu.
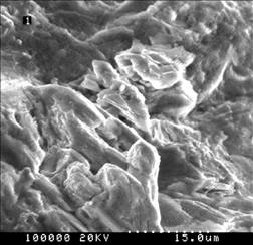
Fig.2 Surface morphology of coarse ores before leaching
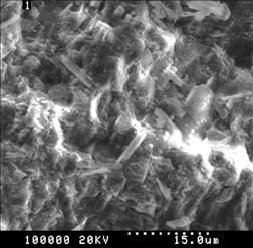
Fig.3 Surface morphology of fine ores before leaching
3.4 Element analysis
The coarse and fine ores were mixed enough respectively before leaching. A small part of coarse and fine samples were ground into 74 μm, then used for element analysis with Plasma-Atomic Emission Spectrometry. Table 4 lists the average content of Cu, Fe and S. This result differs from that in Table 1, because the ores collected from Dexing cannot represent the whole dump of Dexing. After leaching, the ore residence was analyzed in the same way. So the Cu, Fe and S content before and after leaching can be compared.
Table 4 Main chemical composition of sample (mass fraction, %)
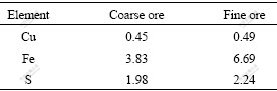
4 Leaching experiment
4.1 Preparation stage
Because there was only one export in the bottom of the column, the preferential solution flow experiment was conducted by the equipment with two exports as shown in Ref.[13]. Distilled-ion exchanged water was put into the raised barrel as shown in Fig.1. The natural mixtures of bacterial types from Dexing Copper Mine were added into it. The volume was fixed at 15 L. The pH value of the solution was adjusted to 2.0 by adding H2SO4.
4.2 Leaching stage
The solution was sprayed into column when the ore sample and solution were prepared. The application rate was adjusted by the flow meter. The solution flowed through the coarse and fine regions respectively, then mixed and flowed out at the bottom of the column. The pH value of the solution was higher than 2.0 at the end of each circulation. So H2SO4 was added into the collective barrel to adjust the pH value to 2.0 again. Then the solution was pumped into the raised barrel, and the next solution circulation began. The temperature was not controlled during the leaching period, so the temperature of the leaching system was the same as room temperature.
The whole leaching process was divided into two isolated stages. There were sixty-three circulations in the first stage. When the first stage was finished, new solution was prepared with distilled-ion exchanged water, mixed bacterial and H2SO4. There were thirty-six circulations in the second leaching stage.
5 Results and discussion
5.1 Concentration of Cu2+ and Fe
The concentrations of Cu2+ and Fe are the important factors that reflect the leaching rate and recovery efficiency and influence the next processions, such as solvent extraction and electrowinning. Experience shows that the concentrations of Cu2+ and Fe in the solution used for electrowinning cannot exceed 34 and 175 g/L, respectively. The concentration of Cu2+ in the solution from dump leaching is usually higher than 1.0 g/L. Although Fe3+ plays an important role during the leaching process, Fe3+ can deoxidize the high value manganese and damage the organic phase. So the proper concentration of Fe is 1.0 g/L. During the electrolysis process, Fe2+ ions near anticathode were oxidized into Fe3+ ions, which were deoxidized into Fe2+ in the cathode area. A large amount of electricity will be consumed when the Fe3+ concentration is high.
The Cu2+ and Fe concentrations of solution during leaching period are shown in Figs.4 and 5. At the beginning of the first leaching stage, Cu2+ and Fe concentration increases slowly even though the acid is consumed rapidly. So much of acid is reacted with the alkali gangues, while little acid accounts for the leaching process. The concentrations of Cu2+ and Fe increase sharply during the later period of first leaching stage and second leaching stage.
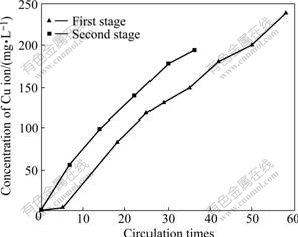
Fig.4 Cu2+ concentration during leaching period
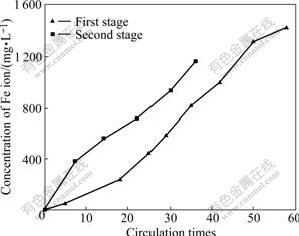
Fig.5 Fe concentration during leaching period
5.2 Recovery efficiency
In order to investigate the recovery efficiency of different parts of column and the influence of preferential solution flow on the recovery efficiency of coarse and fine ore area, 0.1 kg of leaching residues were selected from top, middle and bottom parts of the column in both coarse and fine areas. The leaching residue was ground into 74 μm. As shown in Figs.6 and 7, the constitute element of leaching residue was analyzed by Plasma-Atomic Emission Spectrometry.
The grade of leaching residence selected from both coarse and fine regions increases with the increase of dump depth, while the recovery efficiency decreases with the increasing of dump depth. The acid and other oxidant are consumed gradually when solution flows from the top to bottom of the dump. There is plenty of oxygen
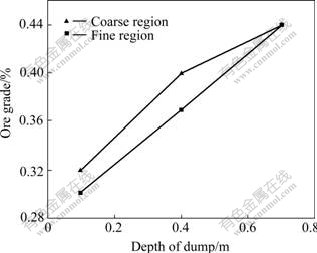
Fig.6 Ore grade of different parts of dump
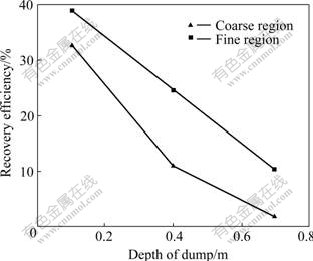
Fig.7 Recovery efficiency of different parts of dump
available for the leaching reaction and bacterial growth at the top of the dump. The concentration of acid, oxidant and bacterial at the bottom is lower than that at the top dump. The pH value is high when it reaches the bottom of the column, and the precipitation of sulfur and jarosite forms. The precipitation covers on the ore surface and prevents the reactant and production from diffusing. So the recovery efficiency at the top dump is larger than that at the bottom dump, and it decreases with the increase of column depth.
5.3 Size distribution of leach residence
The size distribution of leaching residence is shown in Table 5. Compared with Fig.5, the content of fine ores in both regions increases after leaching. Ore particles dissolve into small particles. And the precipitations become small particles when they are dried. So the content of fine ores increases.
Table 5 Size distribution of leaching residence
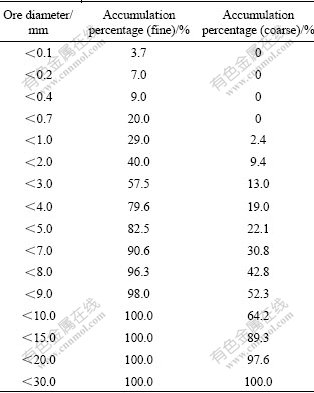
5.4 Preferential solution flow before and after leaching
The preferential solution flow can’t be conducted by the multi-function auto-control bioleaching apparatus because there is only one export at the bottom of the column. So the preferential solution flow of leaching residence was conducted according to Ref.[13]. Twelve groups of application rate were selected. The outflow rates of solution flow from coarse or fine region are shown in Figs.8 and 9.
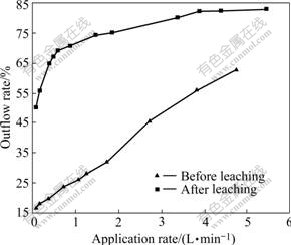
Fig.8 Outflow rate from course region
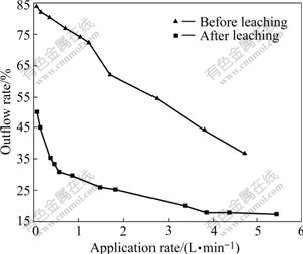
Fig.9 Outflow rate from fine region
Before leaching, the outflow from fine region is larger than that from coarse region. Especially when the application rate is very small, the outflow from fine region is almost five times larger than that from coarse region. So the outflow happens mainly in the fine region. This result is consistent with the research of Ref.[13].
After leaching, the outflow from fine region is smaller than that from coarse regions, and the preferential solution flow happens in the coarse region. Before leaching, the experiment of preferential solution flow was conducted using very high application rate. Part of the fine ores were carried out by water, or entered into the coarse region. During the leaching process, coarse ores are dissolved into fine ores, and precipitation is formed. So the content of fine ores in the coarse region increases. And the preferential solution flow shifts from fine region to coarse region.
5.5 Surface morphology
As shown in Tables 1 and 2, there are oxidant and sulphide of Cu, Fe, Al, Mg and Ca within the ores. The minerals on the ore surface were dissolved or precipitated on the surface under the attack of bacterial acid solution. The surface morphology, specific surface area, pore size and pore volume ratio change a lot during leaching process.
By comparing Fig.2 with Fig.10, the coarse ore surface is smooth and consists of compacted blocks. During leaching process, pores and crackles inside the ores develop. So the surface of leaching residence is loose and lacunaris. The specific surface area increases. The number and volume of the micro-pore increase sharply. And the pores and crackles develop into deep side of the ores. In this instance, the contact of solution and minerals is enhanced.
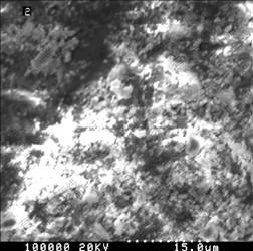
Fig.10 Surface morphology of top coarse residence
In order to investigate erosion degree of ores in different parts of the column, three groups of leaching residence were selected from top, middle and bottom part of the column. The leaching residences from coarse regions are shown in Figs.10, 11 and 12. The coarse ores on the top of the column is eroded seriously, and the erosion degree of middle ores is lighter. There are plenty of crackles on the bottom residence surface. The pH value of solution decreases when the solution flows to the bottom of the column. Precipitation of sulfur and jarosite forms on the ore surface. The precipitation layer crackles when leaching residence is dried. By analyzing the surface surface morphology, we can learn that the erosion grade and recovery efficiency decrease with the increase of dump depth. This result is consistent with that of 5.2.
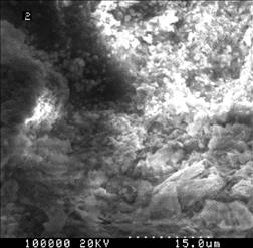
Fig.11 Surface morphology of middle coarse residence
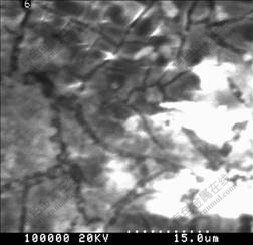
Fig.12 Surface morphology of bottom coarse residence
The surface morphology of fine ores and its residence are shown in Figs.3, 13-15. The surface of residence is eroded differently. The surface of fine ores before leaching is smooth. The surface of the top ores is eroded seriously. Its cracks develop deeply, and the pore diameter becomes larger. The erosion degree of the middle ores is lighter than that of top ores. The bottom ores are eroded slightly. And a small part of the mineral on the surface is dissolved. This phenomenon is consistent with the result of 5.2.
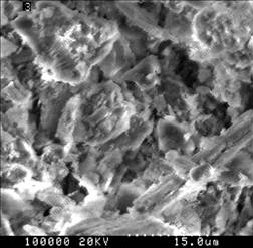
Fig.13 Surface morphology of top fine residence
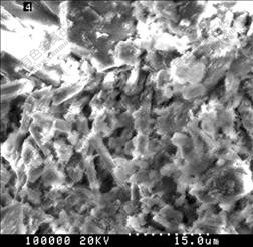
Fig.14 Surface morphology of middle fine residence
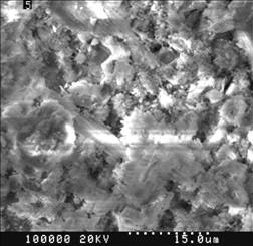
Fig.15 Surface morphology of bottom fine residence
6 Conclusions
1) The pH value increases sharply during the starting period, but the Cu2+ concentration increases slightly. This is because the acid is consumed by the other gangues, while the amount of acid accounting for leaching process is very small.
2) The recovery efficiency decreases with the increase of dump depth. The acid and other oxidant are consumed gradually when solution flows from the top to bottom of the dump. There is plenty of oxygen available for the leaching reaction and bacterial growth at the top of the dump. The concentration of acid, oxidant and bacterial at the bottom is lower than that at the top dump. The precipitation covers on the ore surface and prevents the reactant and production from diffusing.
3) The SEM photograph shows that ores at the top of the column are eroded seriously, and the erosion degree of middle ores is lighter. There are plenty of crackles on the bottom residence surface, because the precipitation layer crackles when leaching residence is dried. By analyzing the surface morphology, we can learn that the erosion grade and recovery efficiency decreasing with the increase of dump depth.
References
[1] GONG Lei, XU Xiao-jun. Research on physical mutation of bacterium T.f and its leaching of low grade chalcopyrite ore [J]. Metal Mine, 2005, 8: 39-41. (in Chinese)
[2] LI Hong-xu, CANG Da-qiang, CHEN Jing-he, QIU Guan-zhou. Effect of biological factors on heap bioleaching kinetics of secondary copper sulfide [J]. The Chinese Journal of Nonferrous Metals, 2007, 17(2): 331-335. (in Chinese)
[3] SHI Shao-yuan, FANG Zhao-heng. Enhancement of bioleaching of marmatite flotation concentrate by metallic ions [J]. The Chinese Journal of Nonferrous Metals, 2005, 15(10): 1623-1628.(in Chinese)
[4] LI Hao-ran, FENG Ya-li. Bioleaching the open stripe nickel ore in Jinchuan Mine of China [J]. Journal of University of Science and Technology Beijing, 2004, 26(6): 584-587. (in Chinese)
[5] XU Xiao-jun, GONG Lei, MENG Yun-sheng, JIANG Jine. Chemical mutation of bacterium T.f and its leaching of low grade chalcopyrite ores [J]. Metal Mine, 2004, 8: 41-43. (in Chinese)
[6] LIU Yuan-yuan. Feasibility study of bioleaching for low-grade ore in Tongkuaangyu Copper Mine [J]. Mining & Metallurgy, 2004, 13(1): 26-29. (in Chinese)
[7] ZHOU Pei-lin, WANG Hui-ying. Solution mining [M]. Changsha: Central South University of Technology Press, 1990. (in Chinese)
[8] YANG Shi-jiao, YANG Jian-ming, LI Guang-yue, LI Chang-shan, LI Qin, ZHANG Xiao-wen, HUANG Yong-zhong, HUANG Xiao-nai. In-place leaching of fragmented uranium ore by blasting [M]. Changsha: Central South University Press, 2003. (in Chinese)
[9] WU Ai-xiang, LIU Jin-zhi. Simulation of coupled flowing- reaction-deformation with mass transfer in heap leaching processes [J]. Applied Mathematics and Mechanics, 2007, 28(3): 297-304. (in Chinese)
[10] WU Ai-xiang, YIN Sheng-hua, WANG Hong-jiang, SU Yong-ding. Solute transport mechanism and model of dump leaching [J]. Journal of Central South University (Science and Technology), 2006, 37(2): 385-389. (in Chinese)
[11] WU Ai-xiang, YIN Sheng-hua, LI Jian-feng. Influential factors of permeability rule of leaching solution in ion-absorbed rare earth deposits with in-situ leaching [J]. Journal of Central South University (Science and Technology), 2005, 36(3): 506-510. (in Chinese)
[12] WU Ai-xiang, YIN Sheng-hua, LIU Jin-zhi, YANG Bao-hua. Formative mechanism of preferential solution flow during dump leaching [J]. Journal of Central South University of Technology, 2006, 13(5): 590-594.
[13] WU Ai-xiang, YIN Sheng-hua, YANG Bao-hua, WANG Jun, QIU Guan-zhou. Study on preferential flow in dump leaching of low-grade ores [J]. Hydrometallurgy, 2007, 87: 124-132.
[14] LIU Jian-she, XIA Hai-bo, WANG Zhao-hui, HU Yue-hua. Bacterial oxidation activity in heap leaching [J]. Journal of Central South University of Technology, 2004, 11(4): 375-379.
[15] YANG Song-rong, XIE Ji-yuan, QIU Guan-zhou, HU Yue-hua. Research and application of bioleaching and biooxidation technologies in China [J]. Minerals Engineering, 2002, 22(5): 361- 363.
Foundation item: Project(2004CB619205) supported by the National Basic Research Program of China; Projects(50325415, 50574099) supported by the National Natural Science Foundation of China; Project(50621063) supported by China Science Fund for Distinguished Group
Corresponding author: YIN Sheng-hua; Tel: +86-13811668481; E-mail: csuysh@yahoo.com.cn
(Edited by LI Xiang-qun)