
Inter-granular liquid phase aiding grain boundary sliding in superplastic deformation of fine-grained ZK60 Mg alloy
LEE Shyong1, CHIANG Chih-te1, CHU Chun-lin1, HSU Chang-chuan2
1. Department of Mechanical Engineering, National Central University, Jhong-li, Taiwan, China;
2. Chun-Shan Institute of Science, Lung-tan, Taiwan, China
Received 23 September 2009; accepted 30 January 2010
Abstract: For 7475 Al alloy, there were micrographs showing filaments or whiskers formation during the separation stage of superplastic elongation. This indicates the presence of liquid phase which accommodates grain boundary sliding to reach superplasticity. On the other hand, there is no such phenomenon reported regarding Mg alloy in literatures. Scanning electron microscopic (SEM) fractography exceptionally exhibits a mark of grain boundary sliding and its accommodating mechanism of inter-granular liquid phase. Under the testing conditions of 350 ?C and 1×10-4 s-1, the initially fine-grained structure (3.7 μm) yields 642% superplastic elongation and exhibits fluffy appearance on the fractured surface. For other specimens showing less superplasticity, their fractured surfaces exhibit partial fluffy appearance.
Key words: Mg alloy; inter-granular phase; grain boundary sliding; superplastic deformation
1 Introduction
The microscopic mechanism responsible for superplastic deformation is still not thoroughly understood. However, there is almost no doubt that grain boundary sliding (GBS) is involved such that fine and equiaxed grain structure is a requisite. It also needs to be aided by an accommodation mechanism in order to achieve strain compatibility and relieve any stress concentration resulting from GBS. A relatively recent model is “liquid phase aided GBS”, as first proposed by NIEH and WADSWORTH[1] on aluminum matrix composite. Thereafter, the role of liquid phase associated with Al alloys or Al-based composites has been discussed[2-14]. CAO et al[15] presented fractography of superplastically elongated AA7475, claiming whisker formation. However, some of SEM micro-graphs appeared more fluffy-like patterns. TAKAYAMA et al[16] continued the investigation and showed filament morphology on fracture surfaces of the broken specimens tested with AA7475. MUKAI et al[17] thought there is no need for the presence of a liquid phase for Mg alloys and composites. In this work, the above mentioned mechanism, GBS accommodated by a liquid phase, is studied by investigating a fine-grained Mg alloy, ZK60. This work is based on the tensile behavior characteristic of some superplastic specimens, especially the fracture modes.
2 Experimental
The ZK60 magnesium alloy used has a chemical composition of Mg-5.29%Zn-0.59%Zr (mass fraction). The alloy was prepared by chill casting it into an 200 mm (8”) ingot. Using this casting method avoids potential macro-segregation. It was then extruded at 380 ?C to obtain a sheet of 1 000 mm×90 mm×6 mm, which corresponds to a reduction ratio of 60:1. This extrusion was an intermediate process to facilitate the subsequent rolling work. This as-extruded sheet was first annealed at 265 ?C for 3 h, and then rolled at 350 ?C with 80% thickness reduction. The final recrystallization treatment to result in fine grain size of 3.7 μm, as displayed in Fig.1, was achieved by annealing at 265 ?C for 16 h. Specimens of this grain structure were superplastically elongated at specific temperature and strain rate combination. Their post-test metallography and fracture mode were examined with optical and scanning electron microscopes.
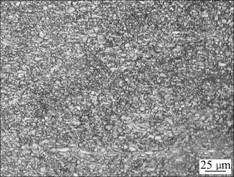
Fig.1 SEM image of specimen with fine grain structure of 3.7 μm obtained by rolling at 350 ?C with 80% reduction and subsequent annealing at 265 ?C for 16 h
3 Results and discussion
3.1 Effects of testing temperature and strain rate on superplastic elongation
The first specimen was tested at 350 ?C under 10-4 s-1 strain rate, and its elongation reaches 642.4% (Fig.2). The second and third ones were tested at 300 ?C under 10-3 s-1 and 10-2 s-1, respectively. Their corresponding elongations are 429% and 240% (Fig.3). Obviously, temperature and strain rate are decisive regarding superplastic behavior. Their suitable combination dictates the degree of operation of grain boundary sliding (GBS) mechanism. If inter-granular liquid phase plays an accommodating role, its viscosity at 350 ?C should be much just right than that at 300 ?C.
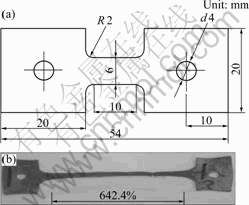
Fig.2 Sketch map (a) and specimen after being tested under 350 ?C and 10-4 s-1 showing elongation of 642.4% (b)
3.2 SEM showing inter-granular fracture mode and mark of liquid phase
The elongated and broken specimen No.1 exhibits a distinct inter-granular fracture mode (Fig.4), with grain size of about 10 μm. This growth of grain from the initial 3.7 μm is resulted from long period of tensile testing, as it lasts for about 18 h (corresponding to 10-4 s-1 of strain rate) at 350 ?C. This SEM stereographic description is consistent with the planar observation through optical metallography (Fig.5). Higher magnification SEM image of the fracture surface (Fig.6) shows the surface morphology of individual grain, exhibiting fluffy appearance that is neither cleavage like nor ordinary inter-granular. A reasonable inference is that highly viscous liquid phase exists between grains, which glues grains and facilitates grain boundary sliding during deformation. When grains are separated, the adhesive
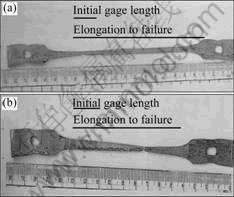
Fig.3 Second and third specimens tested at 300 ?C under 10-3 s-1 and 10-2 s-1 respectively, showing corresponding elongations of 429% (a) and 240% (b)
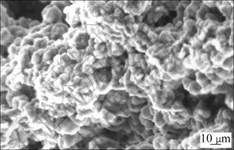
Fig.4 Specimen No.1 exhibiting distinct inter-granular fracture mode with grain size of about 10 μm
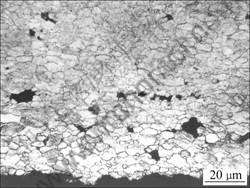
Fig.5 Optical micro-graph of post-tested specimen No.1 showing significant grain growth at 350 ?C and 10-4 s-1
liquid leaves fluff-like mark. When partial liquid phase works because of lower testing temperature (300 ?C and 350 ?C) as for specimens 2 and 3 (Fig.7), superplastic elongation capabilities also decrease.
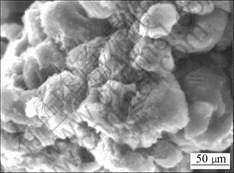
Fig.6 Higher SEM magnification image of fracture surface showing fluffy grain surfaces
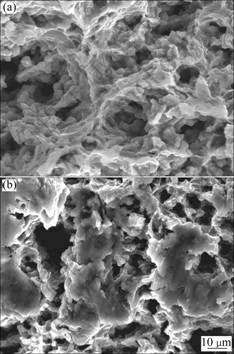
Fig.7 Partial inter-granular fracture mode at lower testing temperature (300 ?C) and higher strain rate, as demonstrated in post-tested specimens 2 (a) and 3 (b)
3.3 Observation of grain growth and cavitation
As stated above, running tensile test at 350 ?C for a long period leads to significant grain growth. It is compared with the condition of 300 ?C and shorter periods as applied to specimens 2 and 3. It is seen that grain growth is minimal as compared with the initial grain size (Fig.8 vs Fig.1). However, elongation of specimens 2 or 3 is much lower than that of specimen 1. The difference should be attributed to how well liquid phase aids GBS process, which is a function of temperature dependent viscosity. For specimen 1, its final breaking should be related to growth and coalescence of cavities, as shown in Fig.9.
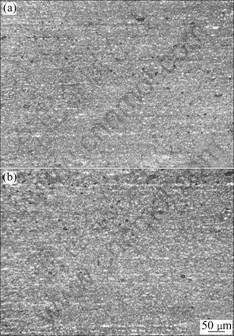
Fig.8 Grain growth for specimens 2 (a) and 3 (b) tested at 300 ?C for shorter periods
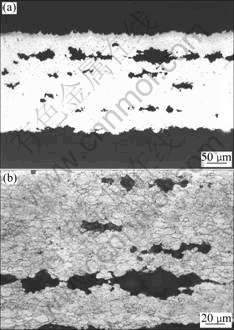
Fig.9 Cavitation appearance of specimen No.1 (a) and near fracture site (b)
4 Conclusions
1) A relatively common Mg alloy, ZK60, can be processed by rolling plus annealing to be fine-grain structured, thus possesses superplasticity.
2) A suitable testing temperature may be essential for a proper viscosity of inter-granular liquid phase to facilitate grain boundary sliding. However, this temperature may also negatively cause grain growth inhibiting GBS when being exposed sufficiently long.
3) If low strain rate prolongs during superplastic elongation, grain growth may occur so that the amount of superplasticity will be reduced.
References
[1] NIEH T G, WADSWORTH J. High-strain-rate superplasticity in aluminum matrix composites [J]. Mater Sci Eng A, 1991, 147: 129-142.
[2] CAO W D, LU X P, SPRECHER A F, CONRAD H. Superplastic deformation behavior of 7475 aluminum alloy in an electric field [J]. Mater Sci Eng A, 1990, 129: 157-166.
[3] SATOH T, OKIMOTO K, NISHIDA S, MATSUKI K. Superplastic-like behavior of rapid-solidification-processed hyper-eutectic Al-Si P/M alloys [J]. Scripta Materialia, 1995, 33(5): 819-824.
[4] LIM S W, NISHIDA Y. Superplasticity of whisker reinforced 2024 aluminum alloy composites fabricated by squeeze casting [J]. Scripta Metall, 1995, 32(12): 1911-1915.
[5] LI X J, TAN M J. A study of the strength of P/M 6061Al and composites during high strain rate superplastic deformation [J]. J Mater Sci, 2003, 38: 2505-2510.
[6] ZELIN M G. On micro-superplasticity [J]. Acta Mater, 1997, 45(9): 3533-3542.
[7] KAIBYSHEV R, MUSIN F, GROMOV D, NIEH T G, LESUER D R. Effect of liquid phase on superplastic behavior of a modified 6061 aluminum alloy [J]. Scr Mater, 2002, 47: 569-575.
[8] KOIKE J, MIKI K, TAKAHASHI H, MARUYAMA K. Effects of the liquid phase on tensile elongation of Al-Bi alloy [J]. Mater Sci Eng A, 2000, 285: 158-164.
[9] IWASAKI H, MABUCHI M, HIGASHI K. The role of liquid phase in cavitation in a Si3N4p/Al-Mg-Si composite exhibiting high- strain-rate superplasticity [J]. Acta Mater, 1997, 45: 2759-2764.
[10] KOIKE J, MABUCIHE M, HIGASHI K. In situ observation of partial melting in superplastic aluminum alloy composites at high temperatures [J]. Acta Mater, 1995, 43(1): 199-206.
[11] HIGASHI K, NIEH T G, MABUCHI M, WADSWORTH J. Effect of liquid phases on the tensile elongation of superplastic aluminum alloys and composites [J]. Scr Metall Mater, 1995, 32(7): 1079-1084.
[12] MAKHERJEE A K, MISHRA R S, BIELER T R. Some critical aspects of high strain rate superplasticity [J]. Mater Sci Forum, 1997, 233/234: 217-234.
[13] CHEN C L, TAN M J. Cavity growth and filament formation of superplastically deformed Al 7475 alloy [J]. Mater Sci Eng A, 2001, 298: 235-244.
[14] KOIKE J. Microstructure and superplasticity in Al-Mg alloy composites reinforced with silicon nitride particles [J]. Mater Sci Forum, 1997, 243/245: 277-286.
[15] CAO W D, LU X P, CONRAD H. Whisker formation and the mechanism of superplastic deformation [J]. Acta Mater, 1996, 44(2): 697-706.
[16] TAKAYAMA Y, TOZAWA T, KATO H. Superplasticity and thickness of liquid phase in the vicinity of solidus temperature in a 7475 aluminum alloy [J]. Acta Mater, 1999, 47(4): 1263-1270.
[17] MUKAI T, WATANABE H, NEIH T G, HIGASHI K. Routes to develop fine-grained magnesium alloys and composites for high strain rate superplasticity [J]. Mat Res Soc, 1999, 601: 291-302.
(Edited by YANG Hua)
Corresponding author: CHU Chun-lin; Tel: +88-63-4267377; Fax: +88-63-4254501; E-mail: jenlen.boy@msa.hinet.net