Trans. Nonferrous Met. Soc. China 24(2014) 854-860
Preparation of Na specific absorbent and application of sodium removal from ammonium tungstate solution
Zhong-wei ZHAO1,2, Mao-feng YANG1,2, Li-hua HE1,2, Jia-liang ZHANG1,2, Xing-yu CHEN1,2, Xu-heng LIU1,2
1. School of Metallurgy and Environment, Central South University, Changsha 410083, China;
2. Hunan Key Laboratory for Metallurgy and Material Processing of Rare Metals, Changsha 410083, China
Received 27 March 2013; accepted 26 November 2013
Abstract: An adsorbent, Na1.6Al0.6Ti1.4(PO4)3 (or NATP), was prepared by controlled crystallization of glasses in the Na2O-Al2O3- CaO-TiO2-P2O5 system. The crystalline phases characterized by X-ray diffraction (XRD) show that the sample glasses crystallizes into two phases, i.e. NATP and Ca9Al(PO4)7, while the Ca9Al(PO4)7 phase can be leached selectively with HCl, leaving a massive number of pores in the material. Through the experimental research, the effects of contact time, solution pH, and the initial concentration of Na+ on the cation exchange properties were investigated. The batch sorption kinetics and equilibria can be described by Pseudo-second-order kinetic equations and Langmuir isotherm equations respectively. Furthermore, the experiments with an industrial solution show that the removal rate of sodium from industrial (NH4)2WO4 is higher than 97%. Cycle experiment also shows that the NATP has a good cyclic performance.
Key words: Na specific adsorbent; sodium removal; ammonium tungstate; purification
1 Introduction
Ammonium paratungstate (APT), as an intermediate product of tungsten metallurgy and tungsten chemical [1-3][1], is used to manufacture many terminal products, such as cemented carbide, tungsten metal material, ammonium metatungstate. Generally, almost all the tungsten raw materials should be firstly converted to sodium tungstate for recovering tungsten [4,5]. To transform from sodium tungstate to ammonium tungstate, ion-exchange and/or solvent extraction methods is frequently used in industrial (NH4)2WO4 production [6,7]. But in practice it is found that timely trace sodium still contaminates the (NH4)2WO4 owing to physical entrainment, misoperation, which leads to exceeding level of sodium content in APT, and makes it unable to meet higher application requirements.
In order to obtain products of APT-0 grade (as per Chinese standard GB 10116-88), the Na+ concentration in (NH4)2WO4 solutions must be lower than 10 mg/L [8]. In factories, to control the sodium content in APT some measures have to be adopted. Firstly, a large volume of pure water should be used to wash off most of the entrained sodium impurities. Secondly, purified desorption reagents should be used to avoid bringing extra sodium in (NH4)2WO4 solution. These processing steps are generally labor intensive and complicated, and produce substantial volume of waste water with low concentrations of tungstate, which is difficult to recover. The removal of Na+ is more difficult compared with other harmful elements in the (NH4)2WO4 solution, and has become a difficult problem in tungsten metallurgy industry. In (NH4)2WO4 solution, the predominant monovalent cation is NH4+, and the separating method employed should show a high selectivity for Na+ in order to remove Na+ efficiently. Methods for Na+ removal are precipitation [9], adsorption and ion exchange. The selectivity of precipitation and adsorption obtained is generally low, and therefore its application is limited to a few particular cases [10].
It was reported that NASICON-type materials have stable skeleton structure, in which PO4 tetrahedron share their corners with TiO6 octahedra to form a 3D network structure [11], and sodium ion can transfer through the channels freely. There has been some research about the cation exchange properties of some NASICON-type materials [12-15], which has shed some light on Na+ removal from (NH4)2WO4 solution.
In the present study, we prepared NASICON-type Na1.6Al0.6Ti1.4(PO4)3 (NATP) as a Na+ ion-sieve, and the exchange properties of this material were studied.
2 Experimental
2.1 Preparation of porous NATP
All reagents used in the experiment were in analytical grade and the solutions were prepared with distilled water. The base glass in the system Na1.6Al0.6Ti1.4(PO4)3+0.5Ca3(PO4)2 (molar ratio) was prepared with Na2CO3, Al2O3, TiO2, CaCO3 and H3PO4(85%) as starting materials. Stoichiometric starting materials were placed in a Teflon beaker and stirred completely, and a slurry was obtained. Then the slurry was dried at 240 °C for 10 h, and the resulting cake was ground to powders. The powders were then melted in a corundum crucibles at 1300 °C for 1 h. The melts were poured into a stainless steel mold to form glass. The mold was removed and the glass was annealed at 620 °C. The glass was heated up to 690 °C and maintained at the same temperature for 24 h. Subsequently, the specimens were heated at 800 °C without cooling down to room temperature and kept for 20 h. The resulting dense glass ceramics were crushed to produce a certain particle size distribution. Then the particles were leached with 1 mol/L HCl with stirring for 6 h and then filtered, washed, and dried. In this way, the soluble phase was selectively leached while the NATP phase was converted into the H+-form.
The crystal structures of samples were characterized with a Rigaku D/max TTRIII X-ray diffractometer (XRD) at room temperature. The morphologies of the samples were observed with a JEOL JSM-6360LV SEM.
2.2 Ion-exchange properties of NATP
2.2.1 pH experiments
In order to study the influence of the pH on the Na+-H+ exchange, 100 mL of 50 mg/L Na+ solution was placed in a sealed polyethylene bottle. The pH was then adjusted to 0.5-12.0 with HCl or NH3·H2O solutions and 1.0000 g of the dry prepared NATP in H+-form was added to the solution. The experiments were carried out at 298 K, and the final pH was measured after reaction for 24 h. The Na+ concentrations in solution were determined by AAS (atomic absorption spectrometry, Persee of Beijing, China).
2.2.2 Adsorption dynamics and isotherm experiments
Kinetic and isotherm experiments were conducted at a constant temperature of 298 K. The NATP particles used in the kinetic experiments are 38-50 μm. For each experiment, 1.0 g prepared exchanger was added to 1000 mL Na+ simulant solution (pH=11.0), and samples were taken from the reactor at regular time intervals. Na+ solutions (50 mL) of different concentrations with increments of 50 mg/L (50-350 mg/L) were equilibrated for a specific period of time with 0.1 g of exchanger in conical flasks with stopper. The chemical compositions of the solutions were carried out via atomic absorption spectroscopy (WFX-120, Thermo Electron Corporation). The Na+ concentration adsorbed into the exchanger was calculated by the mass balance relationship shown in Eq. (1).
q =(ρo-ρt)V/m (1)
where q is the Na+ concentration in the ion exchanger phase (mg/g); ρ0 and ρt are the initial Na+ concentration in the solution and one at time t, respectively; V is the solution volume (L); m is the ion exchanger mass in dry form (g).
3 Results and discussion
3.1 Characterization of porous NATP
Figure 1 shows the XRD patterns of the glass- ceramics before and after the acid leaching treatment. It can be observed that the sample crystallizes into NATP and Ca9Al(PO4)7 phase. The acid dissolves Ca9Al(PO4)7 phase selectively, leaving NATP with a number of pores which are distributed uniformly in the sample. It is obvious that the material is essentially composed of dense glass (Fig. 2(a)) before leaching, and a massive number of pores are left (Fig. 2(b)) after the Ca9Al(PO4)7 phase being leached out with HCl. The schematic of the formation process of porous NATP glass-ceramics can be seen from Fig. 3.
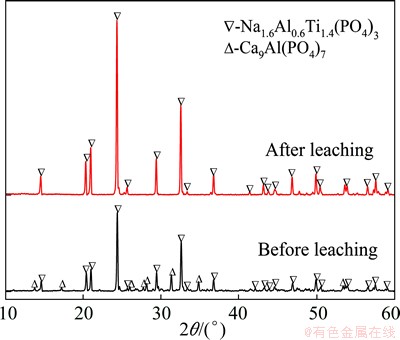
Fig. 1 XRD patterns of glass-ceramics before and after leaching
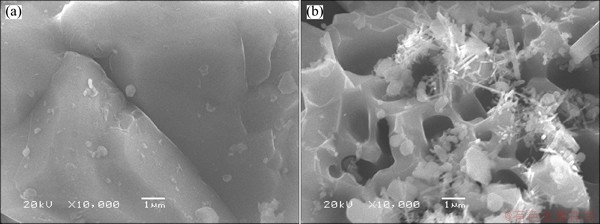
Fig. 2 SEM images of sample before (a) and after (b) HCl leaching
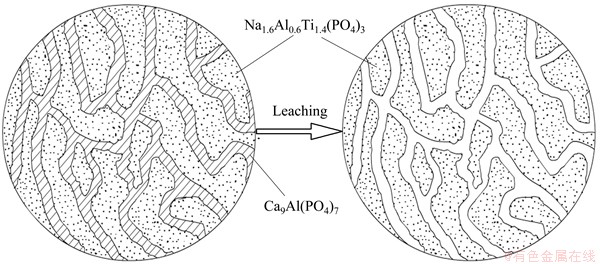
Fig. 3 Schematic of formation process of porous NATP glass-ceramics
Figure 4 shows the ion-exchange properties of the prepared porous NATP glass-ceramics under different pH conditions. It can be seen from Fig. 4, the exchange rate increases with an increase in solution pH, which shows an S-shape. According to report by ZHANG and LIU [16], the exchange process is cation ion exchange, i.e. H+-Na+ exchange mechanism. Furthermore, the sorption is practically zero under acidic conditions pH<1.5, while the exchange rate during sorption can reach higher than 97% at pH>5.5. This means that Na+ uptake cannot be performed completely in solutions with pH<5.5 due to the strong association of hydrogen ions with the active sites of the ion sieves under acidic conditions.
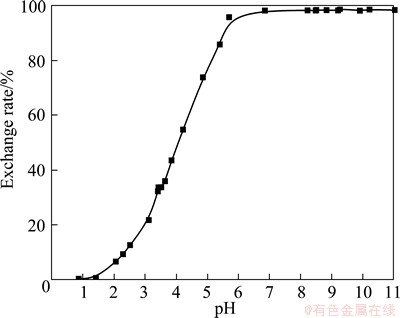
Fig. 4 Exchange rate-pH graph
3.2 Adsorption isotherms
In this work, the uptake equilibrium data can be described by the Langmuir isotherm model [17]. The isothermal equation can be expressed as follows:
(2)
where ρe is the equilibrium concentration (mg/L); qe is the uptake amount at equilibrium (mg/g); qm is the theoretical maximum of adsorption capacity (mg/g); KL is the Langmuir empirical constants.
The relationship between ρe/qe and ρe is illustrated in Fig. 5. The results show that the plot has a good linear relation with a correlation coefficient of 0.998, which demonstrates that a monolayer coverage of Na was adsorbed on the surface of NATP adsorbent. The values of qm and KL are calculated to be 24.82 mg/g and 0.1124 L/mg, respectively. However, the equilibrium exchange capacity of Na+-H+ does not reach its theoretical value (90.89 mg/g). This can be attributed to the structure of the material, namely, in NATP there are two different sites running throughout the lattice structure for the sodium ion, in which the M1 site is fully occupied and the M2 site is partially occupied (Fig. 6) [14]. But the sodium in the M1 site is not fully exchanged, which will result in incomplete exchange of the sodium in NATP.

Fig. 5 Langmuir isotherms for Na+ uptake by NATP
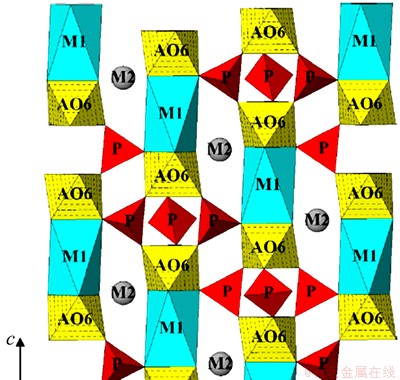
Fig. 6 Crystal structure of NATP
3.3 Adsorption kinetics
The study on ion-exchange kinetics is also important because it demonstrates the solute uptake rate. And the uptake rate in turn will control the residence time of ion exchange at the solid–solution interface, and represent the exchange efficiency of the NATP, thereby determining the potential applications. As shown in Fig. 7, the equilibrium uptake capacity increases with increasing the Na+ concentration. And the maximum amount of adsorption reaches after 10 min, which shows that equilibrium time is independent on initial adsorbate concentration. Therefore, the time mentioned above is sufficient to attain equilibrium at the maximum removal rate of sodium from aqueous solutions of (NH4)2WO4.
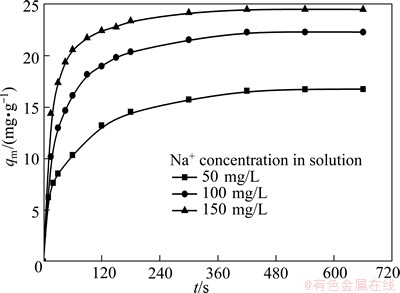
Fig. 7 Effect of contact time on Na+ uptake by NATP at various initial Na+ concentrations
In order to investigate the sorption rate law of ion exchange, the kinetic data obtained from batch experiments were analyzed using the pseudo-second order equation [18,19]. The kinetic rate law can be rewritten as follows:
(3)
where k is the rate constant of sorption (g/(mg×s)); qe is the amount of metal adsorbed at equilibrium (mg/g); qt is the amount of metal adsorbed on the surface of the sorbent at a certain time t (mg/g).
The straight-line plots of t/qt vs t for all cases were obtained by introducing the experimental data into Eq. (3) and shown in Fig. 8. Based on the equations and the obtained linear plots, the qe, k and R2 were calculated and listed in Table 1. The correlation coefficients of the pseudo-second-order rate model for the linear plots are very close to 1, indicating that the process essentially follows the pseudo-second order rate equation. HO and MCKAY [18] reported that the exchange may be the rate-limiting step involving valence forces through exchange of electrons between sorbent and sorbate.
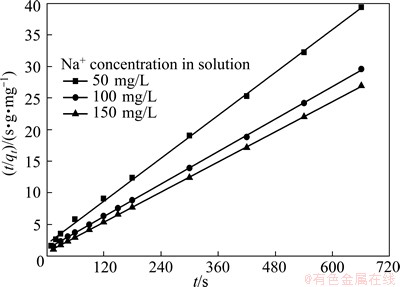
Fig. 8 Pseudo-second order kinetic plots for Na+ uptake by NATP at various initial Na+ concentrations
Table 1 Kinetic parameters of pseudo-second order model for Na+ uptake by NATP at different concentrations
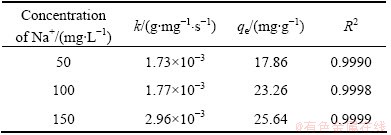
For the investigation of the Na+-H+ exchange mechanism, the intraparticle diffusion model [20] was used and fitted with the experimental data. The equation can be written as follows:
(4)
where qt (mg/g) is the amount adsorbed at time t (s), and kid (mg/(g×s)) is the rate constant of intraparticle diffusion. Figure 9 presents the plots of qt vs t1/2 obtained for the Na+-H+ exchange at different Na+ concentrations, 50, 100 and 150 mg/L. The plots show two stages of sorption, and the first plot was linear but did not pass through the origin. It is concluded that the double stage of the curves were attributed to the fact that the adsorption in the initial stages was due to the boundary layer diffusion whereas in the later stages adsorption was due to the intraparticle diffusion [21,22][Allen, 1989 #50;Bhattacharya, 1984 #52]. On the other hand, the increased sorption rate with the increase of initial concentration can be ascribed to the improved chances of contact between Na+ and the surface of the NATP with increasing Na+ concentration, which results in a larger amount of Na+ diffusion through the boundary layer in unit time [23].

Fig. 9 Intraparticle diffusion plots for Na+ uptake by NATP at different Na+ concentrations
3.4 Na+ removal from (NH4)2WO4 solution
In order to verify the effect of Na+ removal with the prepared NATP materials, a series of experiments were practiced by adding certain amount of the NATP to the industrial (NH4)2WO4 solution (WO3 275 g/L, pH 9.6) with stirring. After about 10 min of contact, the (NH4)2WO4 solution was separated from the ion exchanger by filtering and the ion sieve was recovered for regeneration and reuse. The APT products were obtained by evaporation of filtrate. The recycle tests for ion sieve were conducted with 1 mol/L HCl solution to immerse the Na+-loaded NATP for 10 min.
The removal results are listed in Table 2. The (NH4)2WO4 solution can act as a NH3-NH4Cl buffer solution, and the pH is not changed after exchange reaction. In all cases the removal rate was higher than 97% and the results were consistent with the above. Generally, in order to prepare a APT which can meet the APT-0 (GB/T10116-2007) grade, the mNa/mWO3 in (NH4)2WO4 solution should be lower than 5×10-4 before crystallization [24]. According to the experimental results in this work, the wNa/wWO3 is much lower than the requirement and the spectrographic analysis of sodium concentrations shows that all the products meet the APT-0 grade.
Table 2 Results of deep removing sodium from commercial (NH4)2WO4 solution
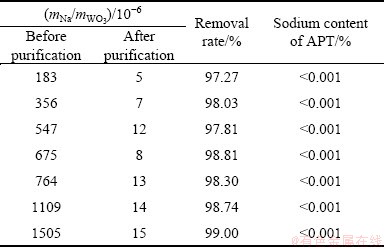
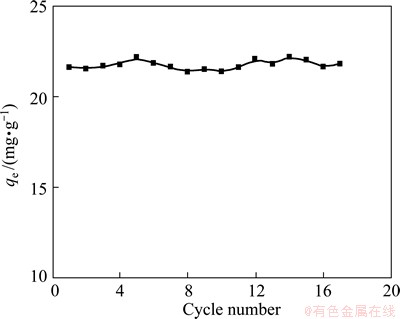
Fig. 10 Cycle performance of NATP
Figure 10 shows the cycling performance of the Na+ removal by NATP materials. The results indicate that the adsorbent could be regenerated easily with 1 mol/L HCl solution and its capacity and activity remain after 17 cycles, indicating an excellent cyclic performance of the adsorbent for Na+ removal from (NH4)2WO4 solution.
4 Conclusions
1) The adsorbent Na1.6Al0.6Ti1.4(PO4)3 can be partially exchanged and the primary exchange mechanism can be described as H+-Na+ exchange.
2) The exchange rate during sorption can reach higher than 97% at pH>5.5, while practically zero at pH<1.5.
3) The adsorbent exhibits a high efficiency for removing sodium from the (NH4)2WO4 solution, and the removal rate of sodium is higher than 97% under optimum conditions. Meanwhile the NATP maintains a good cyclic performance for application.
References
[1] BASU A K, SALE F R. Characterization of various commercial forms of ammonium paratungstate powder [J]. Journal of Materials Science, 1975, 10(4): 571-577.
[2] SUN Pei-mei, CHEN Zou-xi, LI Hong-gui, LI Yun-jiao, LIU Mao-sheng. A new technology for production of high purity paratungstate ammonium from low grade tungsten concentrate [J]. Journal of Central South University of Technology, 1996, 3(2): 171-176.
[3] LI Hong-gui. Production of high purity APT from scheelite and complex tungsten raw material with high Mo content [J]. Transactions of Nonferrous Metals Society of China, 2004, 14(2): 366-369.
[4] LASSNER E. From tungsten concentrates and scrap to highly pure ammonium paratungstate (APT) [J]. International Journal of Refractory Metals and Hard Materials, 1995, 13(1): 35-44.
[5] LI Yun-jiao, LI Hong-gui, LIU Mao-sheng, SUN Pei-mei. Mechanical activation of alkaline leaching of scheelite concentrate [J]. Chinese Journal of Rare Metals, 1998, 17(4): 308-311. (in Chinese)
[6] KHOLMOGOROV A G, KONONOVA O N, KACHIN S V, KALYAKINA O P, PASHKOV G L, KYRILLOVA V P. Ion exchange hydrometallurgy of tungsten using anion exchangers with long-chained cross-linking agents [J]. Hydrometallurgy, 1999, 53(2): 177-187.
[7] LI Hong-gui, LI Bo, ZHAO Zhong-wei. Development of new ion-exchange process in tungsten metallurgy [J]. Rare Metals and Cemented Carbides, 2007, 35(1): 1-4. (in Chinese)
[8] HABASHI F. Handbook of extractive metallurgy [M]. Germany: Wiley-VCH, 1997: 1339.
[9] DEBERITZ J, BELE K K, SCHADE K. Method of separating NaCl from a LiCl solution: WIPO Patent, 1998019966[P]. 1998-05-15.
[10] GIRARDI F, SABBIONI E. Selective removal of radio-sodium from neutron-activated materials by retention on hydrated antimony pentoxide [J]. Journal of Radioanalytical and Nuclear Chemistry, 1968, 1(2): 169-178.
[11] ESSEHLI R, BALI B E, BENMOKHTAR S, BOUZIANEC K, MANOUND B, ABDALSLAME M A, EHRENBERGF H. Crystal structures and magnetic properties of iron(III)-based phosphates: Na4NiFe(PO4)3 and Na2Ni2Fe(PO4)3 [J]. Journal of Alloys and Compounds, 2011, 509(4): 1163-1171.
[12] HOSONO H, IMAI K, ABE Y. Cation exchange properties of LiTi2(PO4)3 and synthesis of its microporous materials via glass [J]. Journal of the Electrochemical Society, 1993, 140(1): L7-L9.
[13] HOSONO H, TSUCHITANI F, IMAI K, ABE Y, MAEDA M. Porous glass-ceramics cation exchangers: Cation exchange properties of porous glass-ceramics with skeleton of fast Li ion-conducting LiTi2(PO4)3 crystal [J]. Journal of Materials Research, 1994, 9(3): 755-761.
[14] MOUAHID F E, ZAHIR M, MALDONADO-MANSO P, BRUQUE S, LOSILLA E R, ARANDA M A G, RIVERA A, LEON C, SANTAMARIA J. Na-Li exchange of Na1+xTi2-xAlx(PO4)3 (0.6≤x≤ 0.9) NASICON series: A rietveld and impedance study [J]. Journal of Materials Chemistry, 2001, 11(12): 3258-3263.
[15] SUN Jian-zhi, DENG Xiao-chuan, WEI Shu-bin, LI Fa-qiang, MA Pei-hua. Synthesis and absorption properties of new Na specific adsorbent Li1+xAlxTi2-x(PO4)3 [J]. Chinese Chemical Letters, 2005, 16(10): 1401-1404.
[16] ZHANG Zheng-bin, LIU Lian-sheng. A study of the theory of stepwise equilibrium of inorganic ion exchange in seawater [J]. Sci Sin, 1974, 17: 486-503.
[17] SHI Xi-chang, ZHANG Zhi-bing, ZHOU Ding-fang, ZHANG Li-fen, CHEN Bai-zhen, YU Liang-liang. Synthesis of Li+ adsorbent (H2TiO3) and its adsorption properties [J]. Transactions of Nonferrous Metals Society of China, 2013, 23(1): 253-259.
[18] HO Y S, MCKAY G. Pseudo-second order model for sorption processes [J]. Process Biochemistry, 1999, 34(5): 451-465.
[19] CHAI Li-yuan, CHEN Yun-nen, SHU Yu-de, CHANG Hao, LI Qing-zhu. Adsorption and removal of cadmium (II) from aqueous solutions by bio-formulation [J]. Transactions of Nonferrous Metals Society of China, 2007, 17(5): 1057-1062.
[20] HUANG C P, HAO O J. Removal of some heavy metals by mordenite [J]. Environmental Technology, 1989, 10 (10): 863-874.
[21] CHEUNG W H, SZETO Y S, MCKAY G. Intraparticle diffusion processes during acid dye adsorption onto chitosan [J]. Bioresource Technology, 2007, 98(15): 2897-2904.
[22] SINGH K K, RASTOGI R, HASAN S H. Removal of cadmium from wastewater using agricultural waste ‘rice polish’ [J]. Journal of Hazardous Materials, 2005, 121(1): 51-58.
[23] WANG Lu, MENG Chang-gong, HAN Mei, MA Wei. Lithium uptake in fixed-pH solution by ion sieves [J]. Journal of Colloid and Interface Science, 2008, 325(1): 31-40.
[24] LI Hong-gui, YANG Gao-jian, LI Kun. Tungsten metallurgy [M]. Changsha: Central South University Press, 2010: 237. (in Chinese).
特性Na离子吸附剂的制备及其从钨酸铵溶液深度除钠
赵中伟1,2,杨茂峰1,2,何利华1,2,张家靓1,2,陈星宇1,2,刘旭恒1,2
1. 中南大学 冶金与环境学院,长沙 410083;
2. 稀有金属冶金及材料制备湖南省重点实验室,长沙 410083
摘 要:在Na2O-Al2O3-CaO-TiO2-P2O5体系中通过控制结晶合成了多孔吸附剂Na1.6Al0.6Ti1.4(PO4)3(NATP)。XRD分析表明,合成的玻璃体会弥散结晶为NATP和Ca9Al(PO4)7两相;通过酸浸可将Ca9Al(PO4)7相溶出,从而使主相NATP中留下大量孔道。实验研究了平衡时间、溶液pH和Na+浓度对吸附剂离子交换性能的影响。吸附动力学和平衡热力学研究表明,吸附过程可以很好地用准二级动力学方程和Langmuir等温方程进行描述。此外,在工业钨酸铵溶液中深度除钠的实验表明,除钠率高于97%,且循环实验表明该吸附剂具备良好的循环性能。
关键词:特性Na吸附剂;除钠;钨酸铵;净化
(Edited by Hua YANG)
Foundation item: Project (2012AA063205) supported by the High-tech Research and Development Program of China
Corresponding author: Zhong-wei ZHAO; Tel: +86-731-88830476; Fax: +86-731-88830477; E-mail: zhaozw@csu.edu.cn
DOI: 10.1016/S1003-6326(14)63135-6