J. Cent. South Univ. (2012) 19: 1808-1812
DOI: 10.1007/s11771-012-1212-1
Extraction of metals from a zinc smelting slag using two-step procedure combining acid and ethylene diaminetetraacetic acid disodium
JIANG Kai-qi(蒋凯琦), GUO Zhao-hui(郭朝晖), XIAO Xi-yuan(肖细元), ZHANG Long(张珑)
School of Metallurgical Science and Engineering, Central South University, Changsha 410083, China
? Central South University Press and Springer-Verlag Berlin Heidelberg 2012
Abstract: A two-step leaching method in combination of acid and ethylene diaminetetraacetic acid disodium (EDTA-Na2) was applied to extract metals such as Cd, Cu, Fe, Pb and Zn from a zinc smelting slag. The results show that the extraction rates of Cd, Cu, Fe and Zn in slag reach 88.3%, 54.1%, 69.6% and 54.7%, respectively, while the extraction rate of Pb is only 0.05% leached with 1.25 mol/L sulfuric acid under the conditions of the ratio of slag to liquid of 100 g/L, 65 ℃ and 120 r/min for 2 h. However, Pb extraction rate from 1.25 mol/L sulfuric acid leached residue reaches as high as 66.5% by using 0.1 mol/L EDTA-Na2 solution. The results indicate that two-step sequential extraction procedure combining 1.25 mol/L sulfuric acid and 0.1 mol/L EDTA-Na2 solution can extensively extract Cd, Cu, Fe, Pb and Zn from zinc smelting slag.
Key words: zinc smelting slag; metal values; two-step sequential extraction; sulfuric acid; EDTA-Na2
1 Introduction
Smelting slag contains heavy metals, such as Ag, As, Cd, Cu, Pb and Zn, which poses potential environment risk due to the solubilization of these elements [1-3]. Hydrometallurgical extraction of metal values from smelting slag has been deeply applied with the extensive increase of the slag produced by metallurgical processing. Generally speaking, extraction using sulfuric acid (H2SO4) is a conventional leaching method due to its easy and fast dissolution kinetics of the residue in solution [4]. The research has been reported that Cu extraction rate could be arrived up to 88% when copper slag was roasted with sulfuric acid at 150 ℃, and 87% of Co, 93% of Zn and 83% of Fe were also obtained [5]. Extraction rates of Cd and Zn from a Cd-Ni residue were more than 90%, while those of Ni and Pb were less than 10%, when being leached by 0.82 mol/L sulfuric acid at ratio of slag to liquid 250 g/L, 45 ℃ and 400 r/min for 60 min [6]. Therefore, sulfuric acid has been considered to be an effective reagent for selective extraction of metals from different smelting wastes [7-9]. However, Pb was slightly extracted. Besides, the result showed that extraction rates of Zn and Cd from the Waelz sintering waste slag leached by hydrochloric acid were 97% and 91%, respectively, but the extraction rate of Pb was also only 0.052% [10]. High extraction rate of Pb could be attained in HNO3 system due to avoiding the formation of Pb compound precipitation, and about 90% of Ag and 80% of Pb from a Pb-Ag concentrate were extracted by 0.65 mol/L HNO3 at 130 ℃ for 90 min [11]. Hydrochloric acid or nitric acid, however, has been limited due to non-selective leaching and costly material consumption. Furthermore, they are not suitable for industrialization due to their volatility [12].
Brine leaching with chloride solutions, such as NaCl, CaCl2 and FeCl3, is widely used in order to improve the extraction efficiency of Pb from the slag [13-14]. About 89% of Pb in a zinc plant residue was dissolved, which was blended with H2SO4 and subjected to roasting, water leaching, and finally 200 g/L NaCl leaching at a pulp density of 20 g/L and 25 ℃ for 10 min [15]. Moreover, Pb extraction rate reached 98.9% in 300 g/L NaCl and 30 mL/L HCl solution when the temperature increased to 95 ℃ [16]. Though Pb in slag can be efficiently extracted by chloride solution, second contamination and wasted leachant will be produced by excessive chloride remained in residue [17]. Ethylene diaminetetraacetic acid disodium (EDTA-Na2), which can be recycled [18-19], could effectively extract Pb from the metal-containing sulfide oxidation products, such as galena, lead hydroxide, lead carbonate, lead sulfate and lead hydroxyl-carbonate [20-21]. Therefore, EDTA extraction should be an alternative method based upon the strong ability to form complexes with metal ions [22].
A two-step sequential extraction, for example sulfuric acid and NaCl, has been testified to leach metal values including Pb, Zn, Cu in solids [7, 23]. In this work, two-step procedure combining acid with EDTA-Na2 was conducted to extract metal values from a zinc smelting slag. The aims of this work were: 1) to choose a suitable acid system to leach Cd, Cu, Fe and Zn from original zinc smelting slag, and 2) to optimize the concentration of EDTA-Na2 for leaching acid leached residue at the following step.
2 Experimental
2.1 Slag
Zinc smelting slag, a historical solid waste, was collected from an abandoned pile in Hengyang district, Hunan Province, China. The slag was dried at 60 ℃ and crushed using ball mill and then passed through a 0.25 mm sieve. Element contents of the slag are listed in Table 1.
Table 1 Chemical compositions of zinc smelting slag (mass fraction, %)

2.2 Experimental design
The experiment was conducted with two steps. Firstly, different agents including HNO3, HCl, H2SO4 and EDTA-Na2 solution with two levels were used to leach the slag (Table 2). HNO3 and HCl were set as two levels of 1.0 and 2.5 mol/L, while H2SO4 was 0.5 and 1.25 mol/L, respectively. The 0.25 mol/L EDTA-Na2 leaching system existed as a control treatment to compare with the two-step procedure. Secondly, the acid leached residues were extracted by 0.25 mol/L EDTA-Na2 solution. Finally, the H2SO4 leached residue was leached with 0.025, 0.05, 0.1 and 0.25 mol/L EDTA-Na2, respectively.
Table 2 Leachant concentrations (mol/L) for experimental design
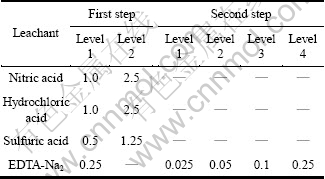
The leaching experiments were carried out in a 250 mL erlenmeyer flasks with 100 mL leachant, which submerged in a thermostatic bathoscillator with digital temperature control (within ±2 ℃). The slag samples were mixed with four different leaching agents at the ratio of slag to liquid of 100 g/L, 65 ℃ and 120 r/min for 2 h. Each treatment was four reduplicated.
2.3 Sample analysis and statistical treatment
The zinc smelting slag was digested with a mixture of HNO3-HClO4. Concentrations of Cd, Cu, Fe, Pb and Zn in digested and leached solution were determined by inductively coupled plasma atomic emission spectrometry (ICP-OES, Intrepid II XSP, USA). The main crystalline compounds in the slag and leached residues were identified by X-ray powder diffractometer (XRD, SIMENS2500X model, Germany).
3 Results and discussion
3.1 Metals leached with different agents
Metal values including Cd, Cu, Fe, Pb and Zn from the slag could be mostly extracted in HNO3 leaching system (Fig. 1). Cd extraction rate from the slag reached as high as 91.8% with 2.5 mol/L HNO3, and 80.7% of Cu, 63.6% of Fe, 79.6% of Pb and 75.4% of Zn were also obtained, respectively. The results might be due to the oxidative of HNO3 that could promote the dissolution of metals present in solid materials to some extent. The extraction rates of metals, except for Cd, extracted by 1.0 mol/L HNO3 were slightly lower than those by 2.5 mol/L HNO3, indicating that metal values extraction could be enhanced by increasing HNO3 concentration. High HCl concentration (2.5 mol/L) also showed high metal extraction rates, in which 90.4% of Cd, 62.8% of Cu, 73.8% of Fe and 60.2% of Zn were obtained, respectively (Fig. 1). The enhancement of Cd extraction was probably due to the formation of a certain amount of species such as [CdOH(H2O)x]+ in HCl leaching system, and the strength of O—H bonds was weakened in acid solution while some complex ions such as [CdCl4]2- were formed due to abundant Cl- existing in solution, and then Cd dissolution increased [10]. Pb extraction rate with 2.5 mol/L HCl was only 54.6%, while that of Pb leached with 1.0 mol/L HCl reached 72.1%.
The extraction rates of Cd in the slag in 1.0 mol/L H2SO4 leaching system was also reached up to 88.3% (Fig. 1). The extraction rates of Cu (56.1%), Fe (69.6%) and Zn (54.7%) leached with 1.25 mol/L H2SO4 were higher than those extracted with 0.5 mol/L, respectively. Pb, however, could not almost be extracted by H2SO4, and the extraction rate was as low as 0.05%, which was mainly owing to the formation of PbSO4 in H2SO4 solution (Fig. 2). Globally, the extraction rates of Cd and Fe from zinc smelting slag showed no obvious difference in HNO3, HCl and H2SO4 leaching system. H2SO4 was chosen for this work because of the limited usage of HNO3 and HCl in industrial processes. The extraction rates of Cu, Fe and Zn with EDTA-Na2 solution were slightly less than those with to acid leaching, and the Cd and Pb extraction rates reached up to 87.2% and 71.6%, while 20.5% of Cu, 40.3% of Fe and 26.5% of Zn were obtained, respectively (Fig. 1). The result was consistent with other research that metals could not be efficiently dissolved in pure EDTA-Na2 system even at high chelant-to-metal ratios [24], and a higher Pb extraction rate in comparison to Zn could be explained by the lower stability of Zn–EDTA complexes compared to Pb–EDTA complexes (lgK=16.5 and lgK=18.0, respectively, at 25 ℃ and ionic strength of 0.1) [25]. Furthermore, Fe and Ca may compete with heavy metals to form complexes with EDTA [26]. The results showed that H2SO4 could be used for extracting Cd, Cu, Fe and Zn, while EDTA-Na2 solution could extract most of Pb in the zinc smelting slag. If H2SO4 was combined with EDTA-Na2 to be an integral system for leaching, Cd, Cu, Fe, Pb and Zn present in slag would be extensively leached.
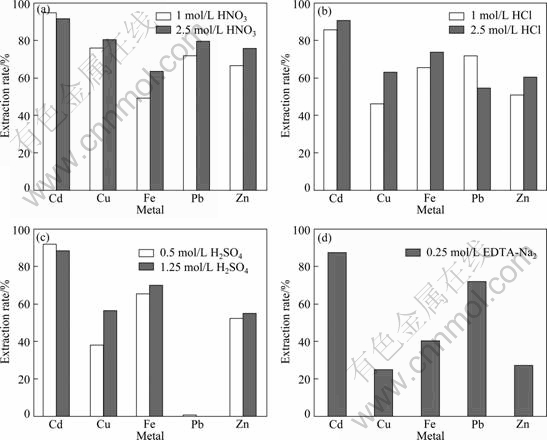
Fig. 1 Extraction rates of metals from zinc smelting slag leached by different leachants: (a) HNO3; (b) HCl; (c) H2SO4; (d) EDTA-Na2

Fig. 2 XRD patterns of original slag and leached residue: (a) Original slag; (b) Sulfuric acid leached residue; (c) Residue leached with combined sulfuric acid and EDTA-Na2
3.2 Metals extraction from acid leached residue by EDTA-Na2 solution
As shown in Fig. 3, the metal extraction rates with 0.25 mol/L EDTA-Na2 solution for 2.5 mol/L HNO3 leached residues were obviously higher than that for 1.0 mol/L HNO3 leached residues, but slight differences in metal extraction rate between 1.0 mol/L and 2.5 mol/L HCl leached residues were found. The extraction rates of Cd, Cu, Fe, Pb and Zn from the HNO3 or HCl leached residues were only about 10%, respectively. The extraction rates of Cd, Cu, Fe and Zn from H2SO4 leached residue slightly increased with increasing EDTA-Na2 solution concentration, however, the extraction rate of Pb significantly increased to 63.6%, which was in agreement with the investigation that EDTA played a vital role in solubilization of lead oxides, lead sulfate, lead hydroxide and lead carbonate [21].
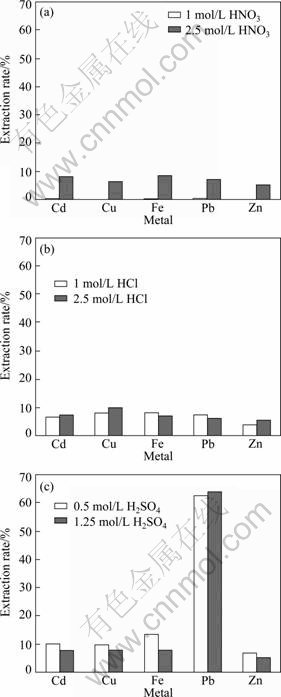
Fig. 3 Extraction rates of metals from different acid leached residues leached by EDTA-Na2: (a) HNO3; (b) HCl; (c) H2SO4
Soluble PbEDTA complex could be formed at pH of 0-14, however, di-anion PbEDTA2- was stable in acid at pH of 3 [27]. Final pH of the leachate of H2SO4 leached residue by EDTA-Na2 was 6.76, showing that PbEDTA and PbEDTA2- should be present. The reaction mechanism between EDTA and sulfides and oxides of metal values may exist in system of H2SO4 leached residue leached by EDTA-Na2:

(1)
EDTA-Na2 could be immediately combined with Pb2+ when it was produced in solution. The reaction occurred as the following equation:
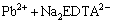

(2)


(3)
The Eqs. (2) and (3) could enhance the formation of the PbEDTA2- and PbEDTA, then accelerate to break up PbSO4 formation. The XRD patterns for the EDTA-Na2 leached residue indicated that Pb compounds were out of determination, which suggested that most of Pb compounds had been extracted from the acid leached residue (Fig. 2).
3.3 Pb extraction with different levels of EDTA-Na2 solution
Pb extraction rate from H2SO4 leached residue increased significantly with increasing EDTA-Na2 concentrations in the range of 0.025-0.25 mol/L (Fig. 4). About 66.5% of Pb would be extracted using 0.1 mol/L EDTA-Na2, while pronounced increase in extraction rate leached by 0.25 mol/L EDTA-Na2 was not found. It was suggested that low concentration of EDTA-Na2 could availably leach Pb from the residue. This result agreed with the investigation that low EDTA-Na2 concentration could be efficiently used for metal extraction [25-26]. In other words, the two-step sequential extraction procedure with H2SO4 then followed by EDTA-Na2 solution should be an efficient way to extract Cd, Cu, Fe, Pb and Zn from zinc smelting slag and detoxify the slag.
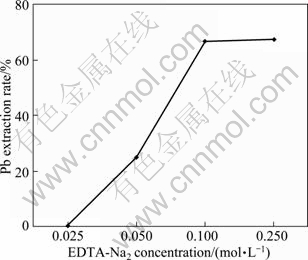
Fig. 4 Effect of EDTA-Na2 concentration on Pb extraction rate present in sulfuric acid leached residue
4 Conclusions
1) The extraction rates of Cd, Cu, Fe, Pb and Zn from the slag exceed 50% by acid leaching. The extraction rates of Cd, Cu, Fe and Zn in 1.25 mol/L H2SO4 leaching system reach 88.3%, 54.1%, 69.6% and 54.7%, respectively, while that of Pb is slightly extracted and the extraction rate is only about 0.05%.
2) Pb extraction rate from H2SO4 leached residue with 0.1 mol/L EDTA-Na2 solution reach 66.5%, indicating that EDTA-Na2 is a potential leachant to leach Pb in zinc smelting slag.
3) Two-step sequential extraction procedure combined with sulfuric acid and EDTA-Na2 solution could recover Cd, Cu, Fe, Pb and Zn from zinc smelting slag.
References
[1] PIATAK N M, SEAL R R. Mineralogy and the release of trace elements from slag from the Hegeler Zinc smelter, Illinois (USA) [J]. Applied Geochemistry, 2010, 25(2): 302-320.
[2] SONKE J E, SIVERY Y, VIERS J, FREYDIER R, DEIONGHE L, ANDR? L, AGGARWAL J K, FONTAN F, DUPR? B. Historical variations in the isotopic composition of atmospheric zinc deposition from a zinc smelter [J]. Chemical Geology, 2008, 252(3/4): 145-157.
[3] KUL M, TOPKAYA Y. Recovery of germanium and other valuable metals from zinc plant residues [J]. Hydrometallurgy, 2008, 92(3/4): 87-94.
[4] SAFARZADEH M S, MORADKHANI D, ILKHCHI M O. Kinetics of sulfuric acid leaching of cadmium from Cd–Ni zinc plant residues [J]. Journal of Hazardous Materials, 2009, 163(2/3): 880-890.
[5] ARSLANA C, ARSLANB F. Recovery of copper, cobalt, and zinc from copper smelter and converter slags [J]. Hydrometallurgy, 2002, 67(1/2/3): 1-7.
[6] SAFARZADEH M S, MORADKHANI D, ILKHCHI M O, GOLSHAN N H. Determination of the optimum conditions for the leaching of Cd–Ni residues from electrolytic zinc plant using statistical design of experiments [J]. Separation Purification Technology, 2008, 58(3): 367-376.
[7] GOUVEA L R, MORAIS C A. Recovery of zinc and cadmium from industrial waste by leaching/cementation [J]. Minerals Engineering, 2007, 20(9): 956-958.
[8] ZHANG Yang, MAN Rui-lin, NI Wang-dong, WANG Hui. Selective leaching of base metals from copper smelter slag [J]. Hydrometallurgy, 2010, 103(1/2/3/4): 25-29.
[9] MORALES A, CRUELLS M, ROCA A, BERG? R. Treatment of copper flash smelter flue dusts for copper and zinc extraction and arsenic stabilization [J]. Hydrometallurgy, 2010, 105(1/2): 148-154.
[10] BESE A V, BORULU N, COPUR M, COLAK S, ATA O N. Optimization of dissolution of metals from Waelz sintering waste (WSW) by hydrochloric acid solutions [J]. Chemical Engineering Journal, 2010, 162(2): 718-722.
[11] GUTI?RREZ R Z, LAPIDUS G T, MORALES R D. Pressure leaching of a lead–zinc–silver concentrate with nitric acid at moderate temperatures between 130 and 170 ℃ [J]. Hydrometallurgy, 2010, 104(1): 8-13.
[12] JHA M K, KUMAR V, SINGH R J. Review of hydrometallurgical recovery of zinc from industrial wastes [J]. Resource, Conservation and Recycling, 2001, 33(1): 1-22.
[13] FARAHMAND F, MORADKHANI D, SAFARZADEH M S, ASHCHI F R. Brine leaching of lead-bearing zinc plant residues: Process optimization using orthogonal array design methodology [J]. Hydrometallurgy, 2009, 95(3/4): 316-324.
[14] SENANAYAKEI G. Review of theory and practice of measuring proton activity and pH in concentrated chloride solutions and application to oxide leaching [J]. Minerals Engineering, 2007, 20(7): 634-645.
[15] TURAN M D, ALTUNDOGAN H S, TQMEN F. Recovery of zinc and lead from zinc plant residue [J]. Hydrometallurgy, 2004, 75(1/2/3/4): 169-176.
[16] RUSEN A, SUNKAR A S, TOPKAYA Y A. Zinc and lead extraction from ?inkur leach residues by using hydrometallurgical method [J]. Hydrometallurgy, 2008, 93(1/2): 45-50.
[17] PARK Y J. Stabilization of a chlorine-rich fly ash by colloidal silica solution [J]. Journal of Hazardous Materials, 2009, 162(2/3): 819-822.
[18] PALMA L D, FERRANTELLI MERLI P, BIANCIFIORI C F. Recovery of EDTA and metal precipitation from soil flushing solutions [J]. Journal of Hazardous Materials B, 2003, 103(1/2): 153-168.
[19] ZENG Q R, SAUVE S, ALLEN H E, HENDERSHOT W H. Recycling EDTA solutions used to remediate metal-polluted soils [J]. Environmental Pollution, 2005, 133(2): 225-231.
[20] RUMBALL J A, RICHMOND G D. Measurement of oxidation in a base metal flotation circuit by selective leaching with EDTA [J]. International Journal of Mineral Processing, 1996, 48(1/2): 1-20.
[21] GREET C, SMART R S C. Diagnostic leaching of galena and its oxidation products with EDTA [J]. Minerals Engineering, 2002, 15(7): 515-522.
[22] FEDIE K K, EKBERG C, SKARNEMARK G, STEENARI B M. Removal of hazardous metals from MSW fly ash—An evaluation of ash leaching methods [J]. Journal Hazardous Materials, 2010, 173(1/2/3): 310-317.
[23] GUO Zhao-hui, PAN Feng-kai, XIAO Xi-yuan, ZHANG Long, JIANG Kai-qi. Optimization of brine leaching of metals from hydrometallurgical residue [J]. Transactions of Nonferrous Metals Society of China, 2010, 20(10): 1-6.
[24] NOWACK B, SCHULIN R, ROBINSON B H. Critical assessment of chelant-enhanced metal phytoextraction [J]. Environmental Science Technology, 2006, 40(17): 5225-5232.
[25] FIN?GAR N, LE?TAN D. Heap leaching of Pb and Zn contaminated soil using ozone/UV treatment of EDTA extractants [J]. Chemosphere, 2006, 63(10): 1736–1743.
[26] FIN?GAR N, LE?TAN D. Multi-step leaching of Pb and Zn contaminated soils with EDTA [J]. Chemosphere, 2007, 66(5): 824-832.
[27] N??EZ-L?PEZ R A, MEAS Y, GAMA S C, BORGES R O, OLGU?N E J. Leaching of lead by ammonium salts and EDTA from Salvinia minima biomass produced during aquatic phytoremediation [J]. Journal Hazardous Materials, 2008, 154(1/2/3): 623-632.
(Edited by YANG Bing)
Foundation item: Project(2011SK3262) supported by Science and Technology Program of Hunan Province, China
Received date: 2011-04-27; Accepted date: 2011-05-21
Corresponding author: XIAO Xi-yuan, PhD; Tel: +86-731-88836442; E-mail: xiaoxy@csu.edu.cn