J. Cent. South Univ. (2017) 24: 766-772
DOI: 10.1007/s11771-017-3478-9

Deep drawing of cup shell by powder cavity flexible forming technology
XUE Ya-hong(薛亚红)1, CHEN Ke(陈科)1, FAN Cun-jie(范存杰)1, LUO Jun-ting(骆俊廷)1, 2
1. Education Ministry Key Laboratory of Advanced Forging and Stamping Technology and Science,
Yanshan University, Qinhuangdao 066004, China;
2. State Key Laboratory of Metastable Materials Science and Technology, Yanshan University,Qinhuangdao 066004, China
Central South University Press and Springer-Verlag Berlin Heidelberg 2017
Abstract: A forming method named powder cavity flexible forming was proposed. It is a forming technology which uses powder medium instead of rigid punch or die to form sheet metals. Cup shells were successfully obtained by this technology. The theoretical calculation equation of forming load was obtained through mechanical analysis and the stress state in cup shells was analyzed by finite element simulation. The results show that powder cavity flexible forming technology can improve the forming limit of sheet metal. Compared with rigid die forming process, the thickness reduction in the punch fillet area significantly decreases and the drawing ratio increases from 1.8 to 2.2. The thinning compressive stress in the bottom of cup shell emerges, which makes the bottom of the cup shell in three-dimensional stress state and the stress in punch fillet region decrease due to powder reaction force, which can effectively inhibit the sever thinning of the sheet and prevent the generation of fracture defects.
Key words: cup shell; powder; cavity flexible forming; drawing; finite element simulation
1 Introduction
Sheet metal stamping forming plays an important role in the fields of automotive, aviation, aerospace, electronics and other industries. There is an increasingly high demand for stamping products of dimensional accuracy, lightweight, surface quality, shape complexity and forming limit. The new process which can improve the performance of the sheet metal forming and overcome the defect of conventional process needs to be researched and the characteristics of the new process are simple mold, short cycle and low cost [1-3]. As a result, research on special forming process of sheet metal has become one of the primary development directions in the field of metal forming [4-7].
Sheet forming process which uses special pressure-transfer medium instead of punch or cavity is called soft mold forming [8]. Sheet metal is shaped as the rigid mould shape under the effect of special pressure-transfer medium. Soft mold forming technology, such as hydro-forming [9, 10] and viscous pressure forming [11, 12] has promoted the development of sheet metal forming technology, but there also exist shortcomings. For hydro-forming, a lager drawing force and blank holder force are required, which can increase the cost of equipment [13]. In addition, hydro-forming and viscous pressure forming greatly limit the increase of heating temperature. Although solid granules medium forming can solve the problems of traditional soft mold forming technologies, it will inevitably produce tiny pints which will influence the appearance and precision of the parts [14, 15].
Sheet forming process using powder medium as the pressure-transfer medium is called powder die flexible forming. In 1986, WAKAI et al [16] first proposed powder punch flexible bulging forming. The 3Y-TZP ceramic tube bulging was formed by adding SiC and BN powder between the punch and sheet metal. In 2002, powder punch flexible forming technology used for sheet forming was proposed by WANG et al [17]. When superplastic deep drawing was preceded in the vacuum sintering furnace, BN powder was placed between the punch and the plate, and the superplastic deep drawing of ceramic part was succeeding. These reports are only some simple applications of powder punch flexible forming process. When parts are formed by the punch, the powder and the sheet are both taken out, and then the powder needs to be added before the next process. And thus, the production cycle and the labor intensity increase, which can not meet the requirement of automation production. The cavity flexible forming can overcome these defects and no additional complex molds is required, which is available for the application in industrial production.
In this work, the formulas for forming load powder cavity flexible forming were derived by mechanical analysis and the stress state of forming parts was analyzed through finite element simulation. In order to verify that the new method can improve the forming limit and inhibit the generation of micro cracks, the experiments of powder cavity flexible forming were performed.
2 Powder cavity flexible forming technology and forming load analysis
The principle diagram of powder cavity flexible forming is shown in Fig. 1. The principle of this process is similar to that of hydro-mechanical deep drawing forming. In the forming process, the reaction force between the powder and the sheet increases as the powder is compressed gradually, which makes the stress in the deformation zone of parts decrease and excessive thinning in the dangerous zone be avoided, and then the forming limit is increased.
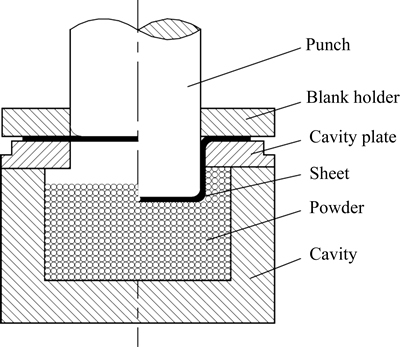
Fig. 1 Principle diagram of powder cavity flexible forming
The force diagram of powder cavity flexible drawing for cup shell is shown in Fig. 2. From Fig. 2, the balance equation can be obtained as follows
(1)
where FZ is the total forming force on cup shell; FB is the forming force formed by rigid die; FP is the reaction load provided by powder; FC is the side load of cup shell provided by powder; μ is the friction coefficient between the powder and the cup shell.
The equilibrium equation for powder is given as
(2)
where PX is the pressure provided by lower plate; SX is the contact area between powder and lower plate; PP is the pressure provided by powder in the punch projectionarea; SP is the cross-sectional area of the punch; PR is the pressure in the annular region except for the punch projection area provided by powder in the axial direction; SR is the surface area of the annular region of cavity except for the punch projection area.
Assuming that PP is directly proportional to PR as
(3)
where K is defined as thrust ratio and K≤1. The value of K can be obtained by experimental testing or calculation.
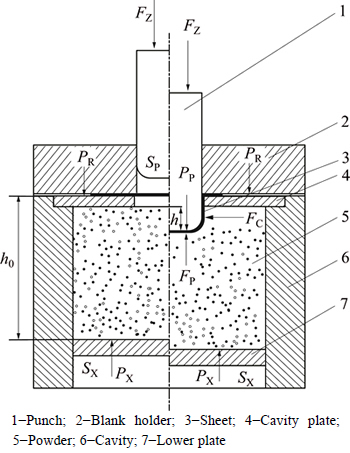
Fig. 2 Force diagram of powder cavity flexible drawing for cup shell:
The value of K is calculated as
(4)
where h is the punch stroke; h0 is the initial height of the powder. At the initial time of deep drawing, h=0, K=1 and PP=PR. With increasing punch stroke, the value of K decreases gradually.
Putting Eq. (3) into Eq. (2)
(5)
The following can be obtained by
(6)
(7)
It is assumed that the pressure in the annular region except for the punch projection area provided by powder in the axial direction is equal to side pressure of cup shell provide by powder, so
(8)
where PC is the side pressure of cup shell provide by powder.
The total forming force can be obtained by:
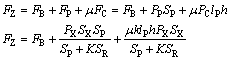
(9)
where lp is the cross section perimeter of punch.
3 Finite element simulation
3.1 Finite element model
436 stainless steel plates with diameter of 80 mm and the thickness of 1 mm are used as the forming blanks. The diameter of the punch is 36 mm. BN is selected as the powder for the cavity flexible forming process. The relative density-pressure curve obtained by the powder compressing experiment is shown in Fig. 3. The powder can provide a compression force of more than 10 MPa when the relative density exceeds 0.5, and the initial relative density of powder is 0.37, the elastic modulus is 30 GPa. Simplified 1/4 axial symmetry finite element model is established by the powder module of Marc software to simulate the powder cavity flexible forming process. For comparison, the finite element simulation of the rigid die deep drawing process is conducted under the same condition. The geometry model and the deformation result for powder cavity flexible forming are shown in Fig. 4.
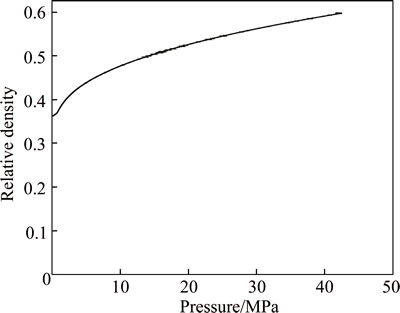
Fig. 3 Relative density-pressure curve of BN powder
3.2 Analysis of simulation results
The equivalent strain contours of cup shell for powder cavity flexible forming are shown in Fig. 5. We can know that the maxmum equivalent strain apears inthe puch fillt area and die corner area which is the dangerousous region.
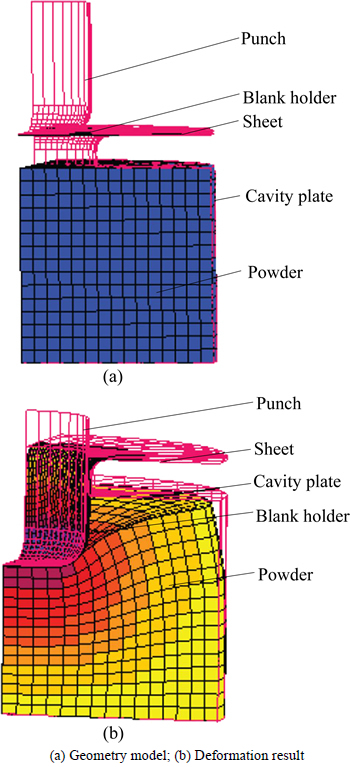
Fig. 4 Finite element model of powder cavity flexible forming:
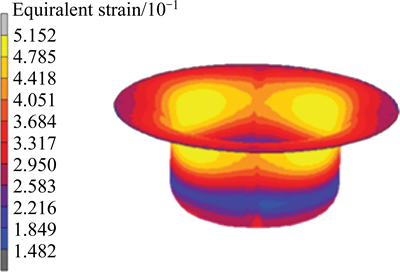
Fig. 5 Equivalent strain contours of cup shell for powder cavity flexible forming
To obtain the stress-punch stroke contrast curve of powder cavity flexible forming and rigid die deep drawing, 2 nodes are selected from the part bottom and punch fillet area. The locations of selected nodes are shown in Fig. 6. The stress-punch stroke contrast curves in part bottom and punch fillet areas are shown in Figs. 7 and 8, respectively.
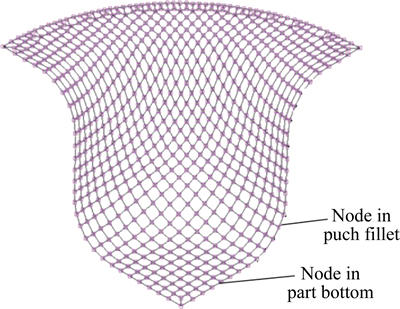
Fig. 6 Locations of selected nodes
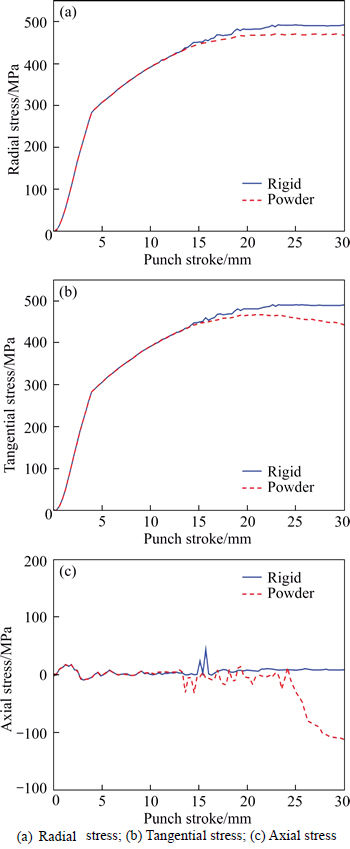
Fig. 7 Stress-punch stroke curves of part bottom:
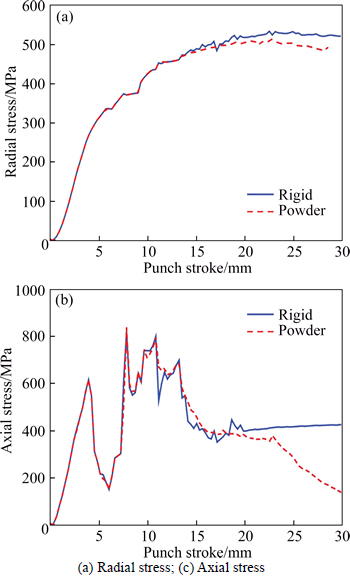
Fig. 8 Stress-punch stroke curves of punch fillet area:
Compared with traditional rigid die deep drawing, the tress-strain state of sheet metal in the process of powder cavity forming is changed. The thinning compressive stress in the bottom of cup shell emerges when the drawing stroke reaches a certain height, which makes the bottom of the cup shell in three-dimensional stress state.
As can be seen in Figs. 7(a), 7(b) and Fig. 8, the radial stress and tangential stress of powder cavity flexible forming and rigid die deep drawing are basically the same in the first half stage, because the sheet has not yet come into contact with the powder or just touch it, and there is no or just a little reaction force provided by the powder. Difference emerges when the deep drawing process carries on to a certain stage and the difference increases with the increase of the punch stroke. That is because as the punch stroke continues to increase, the relative density of the powder gets progressively bigger and bigger and the reaction force provided by the powder will be increased.
Figure 8 shows that the racial and axial stress in the punch fillet region of parts formed by powder cavity flexible forming is smaller than that of rigid die deep drawing, which is conducive to prevent the generation of fracture defects and improve the forming limit of sheet metal.
4 Experimental researches
4.1 Experimental die and procedures
The sketch of the powder cavity flexible forming die is shown in Fig. 9. The experimental procedure and specific content are as follows: 1) Select the blank and punch; 2) Calculate the initial theoretical drawing ratio and drawing limit of the blank; 3) Conduct the rigid die drawing test without powder and the cavity flexible drawing test with the powder filled in the cavity; 4) Measure the thicknesses of the parts formed by two kinds of drawing processes with three coordinates measuring instrument; 5) Compare the forming limit and the surface quality of the parts formed by two kinds of forming processes. The blank holder force is controlled in the forming process by using a torque wrench.
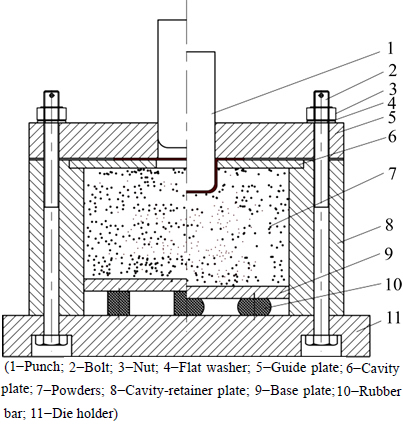
Fig. 9 Sketch of powder cavity flexible forming die
4.2 Preparation of blank and powder
BN is selected as the powder for the cavity flexible forming process. The average diameter of the powder is 80-100 μm. 436 stainless steel plates prepared by wire-electrode cutting are used as the forming blanks. 436 stainless steel is a modified form of 434 stainless steel, which is used in automotive inner decoration board and other products as the good corrosion resistance property. However, the elongation rate and the plastic process performance are poor because of high content of Cr and Mo. The chemical composition of 436 stainless steel is shown in Table 1.
4.3 Selection and calculation of drawing ratio
Choose a blank with diameter D of 80 mm and the thickness t of 1 mm. With these parameters, the relative thickness of the blank is: t/D=1.25×10-2. The limit drawing coefficient m of the rigid mold is 0.53, and thenthe drawing ratio can be calculated as K=1/m≈1.887. In order to reflect the advantages of the powder cavity flexible forming technology, the drawing coefficient is chosen as 0.45, which is smaller than that of conventional rigid drawing, and then the corresponding drawing ratio K is 2.2.
Table 1 Chemical composition of 436 stainless steel (mass fraction, %)

4.4 Experimental results
4.4.1 Forming parts and macro profiles
The cup shells formed by different forming technologies are shown in Fig. 10. The cup shells break when the drawing height is less than 20 mm for rigid die drawing. However, the height of cup shells can be up to 37 mm for powder cavity flexible drawing process. Moreover, the quality of the cup shells is also very good.
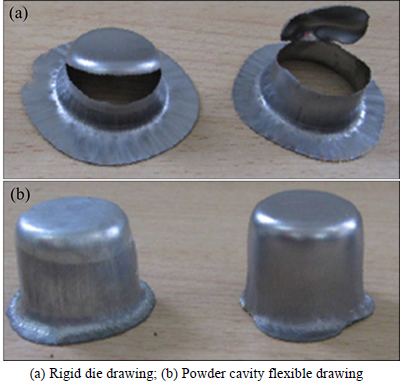
Fig. 10 Cup shells formed by different forming technologies:
The fractured parts and macro profiles after rigid die drawing are shown in Fig. 11. Figures 11(a) and (b) show the fractured part and the vertical cracks, respectively. Figures 11(c) and (d) show the fractured part and the transverse cracks, respectively. Both the vertical cracks and sharp corners of the transverse cracks show that the plasticity of the experimental material is poor. The characteristics of the brittle fracture also can be seen on the fracture surface.
4.4.2 Analysis of wall thickness
The wall thickness distribution of parts is measured by three coordinate measuring instruments. When both sides of the same generatrix of the cylinder are scanned by the front probe of three coordinates measuring instrument, two spline curves are obtained. The distance of the two curves is measured by Unigraphics software, which represents the thickness of this place. The thicknesses at the same place of parts that formed by the powder cavity flexible forming and rigid die forming are measured. As shown in Fig. 12, 11 points are selected from the bottom of the cylinder to the cylinder wall. Points 1-3 are at the part bottom, points 4-7 are at the punch fillet area of the part, and points 8-11 are at cylinder wall of the part. The wall thickness distribution curves for parts under different forming technologies are shown in Fig. 13.
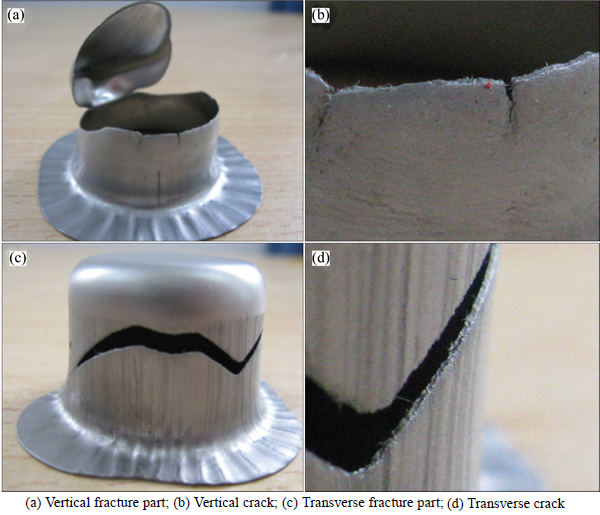
Fig. 11 Fracture parts and cracks for rigid die deep drawing:
As shown in Fig. 13, the thickness tendency of part formed by powder cavity flexible drawing is consistent with that of rigid die drawing. There is a large thickness reduction in the bottom of cup shell, but the maximum value appears in the punch fillet, which is the rupture risk area. Thickness reduction in the punch fillet area for parts formed by powder cavity flexible drawing is smaller than that of rigid die deep drawing due to the powder reaction force, which can effectively inhibit the sever thinning of the plate. The thickness in the side wall and punch fillet area for cup shell formed by two different forming technologies are basically the same due to the powder force is small here.
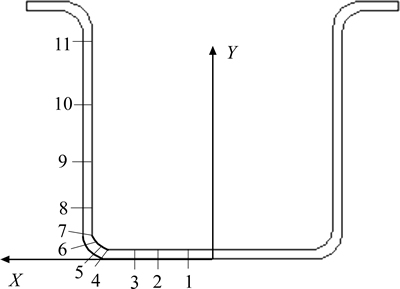
Fig. 12 Positions of measuring points
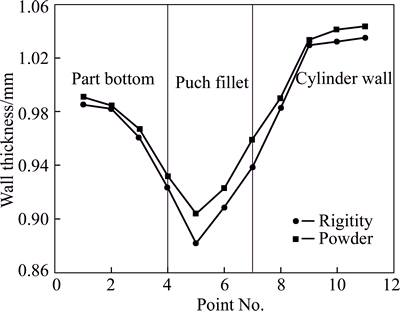
Fig. 13 Contrast curves of wall thickness distribution
4.4.3 Analysis of forming load
Contrast curves of the forming force for rigid die deep drawing and powder cavity flexible drawing are shown in Fig. 14.
The forming forces of the rigid die drawing and powder cavity flexible drawing are basically equal at the initial stage of drawing, because the relative density of powder is small, and it does not play any role during the initial stage of drawing. When the part is drawn to a certain height, the powder is gradually compressed and the relative density sharply increases. At the same time, the reaction force provided by the powder gradually increases. As a result, the forming force of the sheet increases. Comparing this with the rigid die forming process, Fig. 14 indicates that the forming force for powder cavity flexible forming has a rise of 10%.
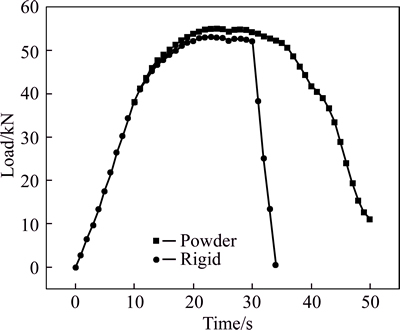
Fig. 14 Contrast curves of forming load
5 Conclusions
1) Compared with rigid die cavity forming process, the forming limit of the sheet that formed by powder cavity flexible forming process is improved. The drawing ratio increases from 1.8 to 2.2.
2) Compared with the rigid die forming process, the wall thickness reduction of the cup shells formed by powder cavity flexible forming process is reduced in the punch fillet, and thus can effectively suppress the generation of micro cracks in the fracture risk area.
References
[1] LANG L, DANCKERT J, NIELSEN K B. Investigation into hydrodynamic deep drawing assisted by radial pressure: Part II. Numerical analysis of the drawing mechanism and the process parameters [J]. Journal of Materials Processing Technology, 2005, 166(1): 150-161.
[2] YAGHOOBI A, BASERI H, BAKHSHI-JOOYBARI M, GORIJI A. Pressure path optimization of hydrodynamic deep drawing of cylindrical-conical parts [J]. International Journal of Precision Engineering & Manufacturing, 2013, 14(12): 2095-2100.
[3] KIM J T, JEON Y P, KIM B M, KANG C G. Die design for a center pillar part by process analysis of hot stamping and its experimental verification [J]. International Journal of Precision Engineering & Manufacturing, 2012, 13(9): 1501-1507.
[4] ZHANG Qing-fang, CAI Zhong-yi, ZHANG Yan, LI Ming-zhe. Springback compensation method for doubly curved plate in multi-point forming [J]. Materials & Design, 2013, 47(9): 377-385.
[5] SATO H, MANABE K, ITO K, WEI D, JIANG Z. Development of servo-type micro-hydromechanical deep-drawing apparatus and micro deep-drawing experiments of circular cups [J]. Journal of Materials Processing Technology, 2015, 224: 233-239.
[6] SIEGERT K, HAUSSERMANN M, LOSCH B, RIEGER R. Recent developments in hydroforming technology [J]. Journal of Materials Processing Technology, 2000, 98(2): 251-258.
[7] LIU Jian-guang, WANG Zhong-jin, WANG Zhong-ren. Numerical simulation of influence of viscous adhesive stress on viscous pressure bulging process of hemispherical sphere [J]. Transactions of Nonferrous Metals Society of China, 2003, 13(6): 1354-1359.
[8] DONG Guo-jiang, ZHAO Chang-cai, CAO Miao-yan. Process of back pressure deep drawing with solid granule medium on sheet metal [J]. Journal of Central South University, 2014, 21(7): 2617-2626.
[9] LIU Bao-sheng, LANG Li-hui, ZENG Yuan-song, LIN Jian-guo. Forming characteristic of sheet hydroforming under the influence of through-thickness normal stress [J]. Journal of Materials Processing Technology, 2012, 212(9): 1875-1884.
[10] DONG Guo-jiang, ZHAO Chang-cai, CAO Miao-yan, HAO Hai-bin. Experimental research on physical properties of pressure-transfer medium in SGMF of plates and pipes [J]. Journal of Plasticity Engineering, 2010, 17(4): 71-75. (in chinese)
[11] LIU Jian-guang, WANG Zhong-jin. Prediction of wrinkling and fracturing in viscous pressure forming (VPF) by using the coupled deformation sectional finite element method [J]. Computational Materials Science, 2010, 48(2): 381-389.
[12] WANG Zhong-jin, WANG Peng-yi, SONG Hui. Research on sheet-metal flexible-die forming using a magnetorheological fluid [J]. Journal of Materials Processing Technology, 2014, 214(11): 2200- 2211.
[13] GRUNER M, MERKLEIN M. Numerical simulation of hydro forming at elevated temperatures with granular material used as medium compared to the real part geometry [J]. International Journal of Material Forming, 2010, 3(S1): 279-282.
[14] DONG Guo-jiang, ZHAO Chang-cai, CAO Miao-yan. Flexible-die forming process with solid granule medium on sheet metal [J]. Transactions of Nonferrous Metals Society of China, 2013, 23(9): 2666-2677.
[15] ZHAO Chang-cai, CAO Miao-yan, XIAO Hong, DONG Guo-jiang, HAO Hai-bin. Solid granular medium drawing process parameters of magnesium alloy sheet [J]. The Chinese Journal of Nonferrous Metals, 2012, 22(4): 991-999. (in Chinese)
[16] WAKAI F, SAKAGGUCHI S, KANYAMA K. Ceramic Materials and Components for Engines [C]// Proc of the Second International Symposium, Luebeck-Travemuende: VDKG, 1986: 1205-1207.
[17] WANG Guo-feng, ZHANG Kai-feng, CHEN Feng, HAN Wen-bo. Study on superplastic forming for nano 3Y-TZP sheet [J]. Forging & Stamping Technology, 2002, 3: 31-33. (in Chinese)
(Edited by FANG Jing-hua)
Cite this article as: XUE Ya-hong, CHEN Ke, FAN Cun-jie, LUO Jun-ting. Deep drawing of cup shell by powder cavity flexible forming technology [J]. Journal of Central South University, 2017, 24(4): 766-772. DOI: 10.1007/s11771-017-3478-9.
Foundation item: Project(E2017203046) supported by the Natural Science Foundation of Hebei Province, China
Received date: 2016-01-13; Accepted date: 2016-06-12
Corresponding author: LUO Jun-ting, Professor, PhD; Tel/Fax: +86-335-8052253; E-mail: luojunting@ysu.edu.cn