
Effects of calcium addition on as-cast microstructure and mechanical properties of Mg-5Zn-5Sn alloy
YANG Ming-bo(杨明波)1, 2, CHENG Liang(程 亮)1, PAN Fu-sheng(潘复生)2
1. Materials Science and Engineering College, Chongqing University of Technology, Chongqing 400050, China;
2. National Engineering Research Center for Magnesium Alloys, Chongqing University, Chongqing 400030, China
Received 3 April 2009; accepted 24 July 2009
Abstract: The effects of Ca addition on the as-cast microstructure and mechanical properties of the Mg-5Zn-5Sn (mass fraction, %) alloy were investigated. The results indicate that an addition of 0.5%-1.5% (mass fraction) Ca to the Mg-5Zn-5Sn alloy not only refines the as-cast microstructure of the alloy but also causes the formation of the primary and/or eutectic CaMgSn phases with high thermal stability; an increase in Ca amount from 0.5% to 1.5% (mass fraction) increases the amount and size of the CaMgSn phase. In addition, Ca addition to the Mg-5Zn-5Sn alloy improves not only the tensile properties at room temperature and 150 ℃ but also the creep properties. Among the Ca-containing Mg-5Zn-5Sn alloys, the one added 0.5% (mass fraction) Ca obtains the optimum ultimate tensile strength and elongation at room temperature and 150 ℃, however, the alloy added 1.5% (mass fraction) Ca exhibits the optimum yield strength and creep properties.
Key words: magnesium alloy; Mg-5Zn-5Sn alloy; microstructure and properties; Ca addition
1 Introduction
Low density of magnesium alloys makes them attractive materials for weight-saving components in the automotive industry. Currently, the most widely used magnesium alloys contain Al as a major alloying element. However, the application of commercially available Mg-Al based alloys is limited at elevated temperatures due to their poor creep behaviour caused by the grain boundary phase β-Mg17Al12 which softens at temperatures exceeding 120 ℃. Therefore, improving the properties at elevated temperatures becomes a critical issue for possible application of magnesium alloys in hot components[1]. At present, efforts are made to develop new creep-resistant magnesium alloys based on the Mg-Zn-Sn system due to the following reasons[2-4]: 1) Zn can enhance the age hardening response, improve the castability and form several stable intermetallics with Mg; 2) Sn can go into solid solution with Mg, impart corrosion resistance and form a stable Mg2Sn compound with Mg.
According to the previous investigations[5-6], the Mg-5Zn-5Sn alloy whose strengthening mechanism is mainly connected with the formation of two precipitates MgZn and Mg2Sn, is considered as one of the promising Mg-Zn-Sn alloys. However, previous works on Mg-5Zn-5Sn alloy mainly focus on the age-hardening behaviour[4-5, 7]. Investigation on the effects of alloying and microalloying on the microstructure and mechanical properties of Mg-5Zn-5Sn alloy is very limited. Up to now, only GORNY et al[2] preliminarily investigated the effect of Y addition on the microstructure of Mg-5Zn-5Sn alloy, and found that Y addition can improve the structural stability of the alloy due to the formation of high temperature ternary phase MgSnY. Because the cost of yttrium (Y) is relatively high, it is necessary to introduce other cheap alloying and/or microalloying elements in order to improve the mechanical properties of the Mg-5Zn-5Sn alloy. It is well known that Ca can behave as a grain refiner of magnesium alloys and form a stable Mg2Ca compound with Mg[8-10]. Furthermore, Ca and Zn together with Mg may form the stable intermetallic compound Ca2Mg6Zn3[11-12]. In addition, Ca and Sn together with Mg may also form the stable intermetallic compound CaMgSn[13-16]. Therefore, it is expected that Ca addition to Mg-5Zn-5Sn alloy would result in additional precipitation and hence improve the mechanical properties. Based on the reasons mentioned above, the present work investigated the effects of Ca addition on the as-cast microstructure and mechanical properties of Mg-5Zn-5Sn magnesium alloy.
2 Experimental
The Ca-containing Mg-5Zn-5Sn alloys used in this study were prepared from Mg, Zn and Sn (99.9% purity), Ca was added in the form of Mg-19%Ca (mass fraction) master alloy. The experimental alloys were melted in a crucible resistance furnace and protected by flux addition. After the Mg-Ca master alloy was added to the melt at 740 ℃, the melt was homogenized by mechanical stirring and held at 740 ℃ for 20 min, then it was poured into a preheated permanent mould in order to obtain a casting. The specimens whose size was previously reported in Ref.[17] were fabricated from the casting for tensile and creep tests. Furthermore, the samples of the experimental alloys were subjected to a solution heat treatment (heated at 300 ℃ for 48 h, and then heated at 450 ℃ for additional 12 h, followed by water quenching) in order to examine the microstructural stability at high temperatures. For comparison, Mg-5Zn-5Sn alloy without the addition of Ca was also cast and machined into the same size, and tested under the same conditions as the above samples. The chemical compositions of the experimental alloys are listed in Table 1.
Table 1 Chemical compositions of experimental alloys (mass fraction, %)
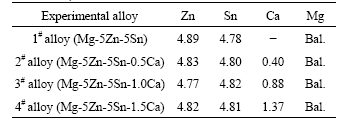
The samples were etched in an 8% nitric acid distilled water solution, and then examined by using an Olympus optical microscope and JEOL/JSM-6460LV type scanning electron microscope (SEM) equipped with an Oxford energy dispersive spectrometer (EDS) at an operating voltage of 20 kV. The phases in the experimental alloys were analyzed by D/Max-1200X type X-ray diffractometer (XRD) operated at 40 kV and 30 mA. The tensile properties of the experimental alloys at room temperature and 150 °C were determined from a complete stress—strain curve. The ultimate tensile strength (UTS), 0.2 % yield strength (YS) and elongation to failure (Elong.) were obtained based on the average value of three tests. The constant-load tensile creep tests were performed at 150 ℃ and 50 MPa for 100 h. The total creep strain and minimum creep rates of the experimental alloys were respectively measured from each elongation—time curve and averaged over three tests.
3 Results and discussion
3.1 Effect of Ca on as-cast microstructure
Fig.1 shows the XRD patterns of the as-cast experimental alloys. At present, two main phases in the Mg-5Zn-5Sn alloy were reported[6], one is identified as MgZn phase, and the other is Mg2Sn phase. Similar to the previous results, the as-cast experimental alloys are mainly composed of α-Mg, MgZn and Mg2Sn phases according to the information from Fig.1. Moreover, it is found in Fig.1 that the addition of 0.5%-1.5% Ca (mass fraction) to the Mg-5Zn-5Sn alloy results in the formation of CaMgSn phase rather than Mg2Ca or Ca2Mg6Zn3 phase. In general, the difficulty level in forming the intermetallics can be estimated by the electronegative difference between different elements. The higher the electronegative difference is, the more easily the intermetallics forms. The electronegative values of Mg, Zn, Sn and Ca are 1.31, 1.65, 1.96 and 1.00[18], respectively. Obviously, the CaMgSn intermetallics is more easily formed due to the higher electronegative difference value between Ca and Sn elements, while the Mg2Ca intermetallics is less easily formed due to the lower electronegative difference value between Mg and Ca elements. Similarly, the Ca2Mg6Zn3 intermetallics is not easily formed due to the relatively low electronegative difference value between Ca and Zn elements. In spite of the above analysis, the reason for the formation of the secondary phases in the Ca-containing Mg-5Zn-5Sn alloys is not completely clear, further investigations need to be considered.
Figs.2 and 3 show the microstructures of the as-cast
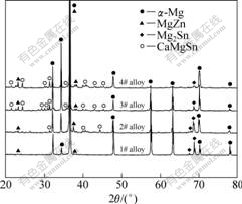
Fig.1 XRD patterns of as-cast experimental alloys
alloys. It can be observed from Fig.2 that the primary α-Mg phases in the as-cast experimental alloys mainly exhibit a dendrite configuration, and the dendritic arm spacing and grain size of the 1# alloy are relatively bigger than those of the 2#-4# alloys, indicating that adding 0.5%-1.5% (mass fraction) Ca to the Mg-5Zn-5Sn alloy can effectively refine the as-cast microstructure of the alloy. Furthermore, it is found from Fig.3 that the Mg2Sn and MgZn phases in the Mg-5Sn-5Zn alloy are also refined by Ca addition. Some black second phases with short rod-like and coarse needle-like morphologies are observed in the 3# and 4# alloys (Figs.2(c)-(d) and Figs.3(c)-(d)). According to the XRD and EDS results (Table 2), these black second phases in the 3# and 4# alloys are identified as primary CaMgSn phase which were described in details in Refs.[13-15]. Some feather-like eutectic CaMgSn phases previously reported by KOZLOV et al[13-15] are also
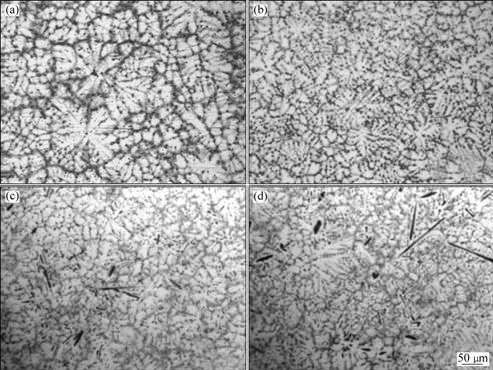
Fig.2 Optical microstructures of as-cast experimental alloys: (a) 1# alloy; (b) 2# alloy; (c) 3# alloy; (d) 4# alloy
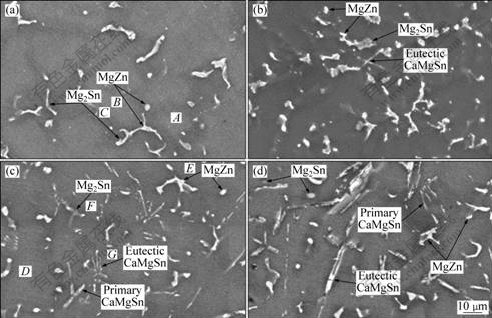
Fig.3 SEM images of as-cast experimental alloys: (a) 1# alloy; (b) 2# alloy; (c) 3# alloy; (d) 4# alloy
Table 2 EDS results of as-cast experimental alloys (molar fraction, %)
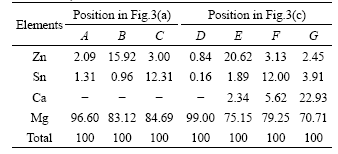
observed in the 2#-4# alloys as shown in Figs.3(b)-(d). It is found from Fig.3 that the increase in Ca amount from 0.5% to 1.5% (mass fraction) causes the amount and size of the CaMgSn phase to increase. According to the previous investigations on the microstructures of the Mg-Sn-Ca ternary alloys with different composition[13-15], it is inferred that the formation of primary and/or eutectic CaMgSn phases with different morphologies in the 2#-4# alloys is possibly related to the different amount of Ca.
3.2 Effect of Ca on mechanical properties
The tensile properties including ultimate tensile strength (UTS), 0.2% yield strength (YS), elongation (Elong.) and creep properties of the as-cast experimental alloys are listed in Table 3. It is observed that with the Ca amount increasing from 0.5% to 1.5% (mass fraction), the ultimate tensile strength and elongation of the experimental alloys first increase and then decrease; the maximum ultimate tensile strength and elongation in the Mg-5Zn-5Sn alloy with addition of 0.5% Ca are achieved at room temperature and 150 ℃. This is possibly ascribed to the microstructural refinement of the Mg-5Zn-5Sn alloy added with 0.5% Ca. However, as shown in Figs.2(c) and (d) and Figs.3(c) and (d), the excess Ca causes the formation of coarse primary CaMgSn phase. The presence of these coarse primary CaMgSn phases possibly promotes the initiation and propagation of cracks and leads to an adverse effect on the ultimate tensile strength and ductility. This can be further confirmed by Figs.4 and 5 which show the SEM tensile fractographs and optical microstructures of longitudinal sections of the as-cast experimental alloys failed in tensile test at room temperature, respectively. As shown in Fig.4, a number of cleavage planes and steps are present, some river patterns can also be observed in the tensile fracture surfaces of the experimental alloys, which indicates that all the tensile fracture surfaces of the experimental alloys exhibit mixed characteristics of cleavage and quasi-cleavage fractures. Therefore, it is inferred that Ca addition to the Mg-5Zn-5Sn alloy does not significantly change the fracture mode of the alloy. However, some relatively large cleavage-type facets are observed in the fracture surface of the 1# alloy (arrow A in Fig.4(a)) whereas the cleavage-type facets in the fracture surfaces of the 2#-4# alloys are relatively fine. In addition, it is observed from Fig.5 that, the tensile rupture of the experimental alloys occurs along inter-granular boundary, but the cracks seem to extend easily along the interfaces between the coarse primary CaMgSn particle and α-Mg matrix (arrow A in Fig.5(c)), which possibly results in the relatively poor mechanical properties of the 3# and 4# alloys.
The Ca-containing Mg-5Zn-5Sn alloys exhibit relatively higher yield strength and creep properties than
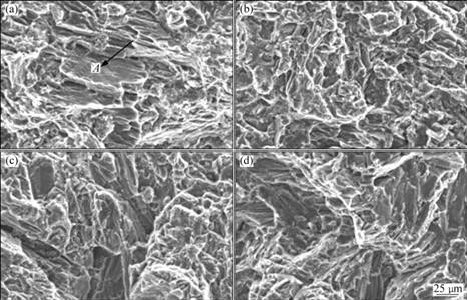
Fig.4 SEM tensile fractographs of as-cast experimental alloys tested at room temperature: (a) 1# alloy; (b) 2# alloy; (c)3# alloy; (d) 4# alloy
Fig.5 Optical microstructures of longitudinal sections of as-cast experimental alloys failed in tensile test at room temperature: (a)1# alloy; (b) 2# alloy; (c) 4# alloy
Table 3 Tensile and creep properties of as-cast experimental alloys

the Mg-5Zn-5Sn alloy without adding Ca, and with the Ca amount increasing from 0.5% to 1.5% (mass fraction), the yield strength and creep properties of the Ca-containing Mg-5Zn-5Sn alloys gradually increase (Table 3). Since the creep properties of magnesium alloys are mainly related to the structure stability at high temperatures, the solutionized microstructures of the experimental alloys are examined (Fig.6). Furthermore, the secondary phases in the solutionized alloys are also identified based on the EDS results (Table 4). Compared with Figs.2, 3 and 6, it is found that the remanent Mg2Sn phases are observed only in the 1# solutionized alloy, and the MgZn phase dissolves into the a-Mg matrix. However, it is found from Figs.6(c) and (d) that besides the remanent Mg2Sn phase, the CaMgSn phase is also observed in the 3# solutionized alloy, indicating that the CaMgSn phase has a high thermal stability. Obviously, the higher creep properties of the Ca-containing Mg-5Zn-5Sn alloys are possibly related to the CaMgSn phase in the alloys, and the finer microstructures of the Ca-containing Mg-5Zn-5Sn alloys
are one of the possible reasons.
Table 4 EDS results of solutionized experimental alloys (molar fraction, %)
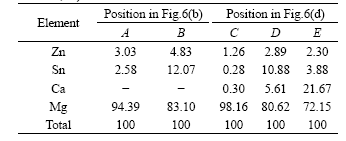
3.3 Discussion
The above results indicate that Ca addition to the Mg-5Zn-5Sn alloy can result in the microstructural refinement of the alloy. It is well known that the Ca atom has a larger atomic radius than the Zn and Sn atoms (Ca: 0.197 nm; Zn: 0.131 nm; Sn: 0.141 nm), with the Ca addition to the Mg-5Zn-5Sn alloy, the Ca element is mainly rich in the solid-liquid interface during solidification. Fig.7 shows the X-ray mapping results of different elements in the 2# as-cast experimental alloy. It is observed that the Ca, Zn and Sn elements mainly distribute at the grain boundaries. Moreover, it is found from Table 2 that the concentrations of Zn and Sn elements in the α-Mg matrix of the 3# as-cast alloy are lower than those of the 1# as-cast alloy. Therefore, it is preliminarily inferred that the above observed microstructural refinement of the Ca-containing Mg-5Zn-5Sn alloys is possibly related to the Ca enrichment, which hinders the diffusion of Sn and Zn atoms and induces the constitution undercooling at the solidification interface front. It is inferred that the CaMgSn compound which has a high thermal stability, can possibly restrain the growth of α-Mg primary phase and secondary solidification phases during solidification. Consequently, the Ca-containing Mg-5Zn-5Sn alloys obtain finer microstructures than the Mg-5Zn-5Sn alloy without Ca addition.
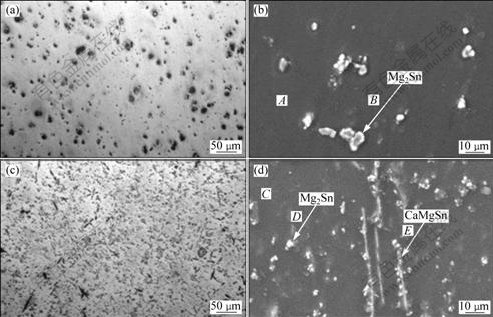
Fig.6 Optical (a, c) and SEM (b, d) images of 1# and 3# solutionized alloys: (a) and (b) 1# alloy; (c) and (d) 3# alloy
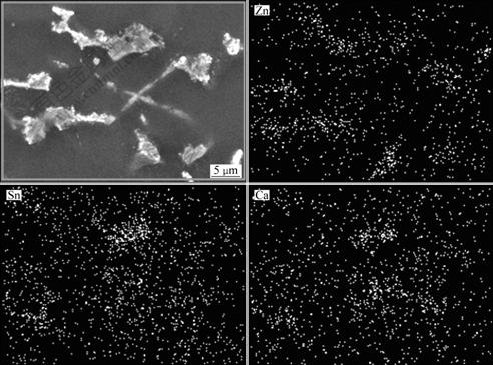
Fig.7 X-ray mapping results of different elements in 2# as-cast experimental alloy
Although the results above indicate that Ca addition to the Mg-5Zn-5Sn alloy can improve the mechanical properties of the as-cast alloy, the question that whether Ca addition influences the age-hardening response of the alloy remains, since the Mg-Zn-Sn based alloys belong to a typical age hardenable system. Therefore, further research is needed to understand the effect of Ca addition on the age-hardening behaviour of the Mg-5Zn-5Sn alloy.
4 Conclusions
1) Adding 0.5%-1.5% (mass fraction) Ca to the Mg-5Zn-5Sn alloy not only refines the as-cast microstructure of the alloy, but also causes the formation of eutectic and/or primary CaMgSn phase with high thermal stability. With the Ca amount increasing from 0.5% to 1.5%, the amount and size of the CaMgSn phase increase.
2) Ca addition to the Mg-5Zn-5Sn alloy improves the tensile properties both at room temperature and 150 ℃, which is beneficial to the creep properties. Among the Ca-containing Mg-5Zn-5Sn alloys, the alloy added 1.5% Ca exhibits the optimum yield strength and creep properties, however, the maximum ultimate tensile strength and elongation are achieved in the alloy added 0.5% Ca at room temperature and 150 ℃. The strengthening mechanism of Ca-containing Mg-5Sn-5Zn alloys is mainly attributed to the microstructural refinement and/or the formation of the CaMgSn phase.
References
[1] YANG M B, PAN F S, ZHANG J, ZHANG J. An analysis of the development and applications of current and new Mg-Al based elevated temperature magnesium alloys [J]. Mater Sci Forum, 2005, 488/489: 923-926.
[2] GORNY A, BAMBERGER M, KATSMAN A. High temperature phase stabilized microstructure in Mg-Zn-Sn alloys with Y and Sb additions [J]. J Mater Sci, 2007, 42: 10014-10022.
[3] RASHKOVA B, PRANTLB W, GORGL R, KECKES J, COHEN S, BAMBERGER M, DEHMA G. Precipitation processes in a Mg-Zn-Sn alloy studied by TEM and SAXS [J]. Mater Sci Eng A, 2008, 494: 158-165.
[4] MENDIS C L, BETTLES C J, GIBSON M A, HUTCHINSON C R. An enhanced age hardening response in Mg-Sn based alloys containing Zn [J]. Mater Sci Eng A, 2006, 435/436: 163-171.
[5] COHEN S, GOREN-MUGINSTEIN G R, AVRAHAM S, DEHM G, BAMBERGER M. Phase formation, precipitation and strengthening mechanisms in Mg-Zn-Sn alloys [C]//KAINER K U. Magnesium: Proceedings of the 6th International Conference on Magnesium Alloys and Their Applications. Germany: WILEY-VCH Verlag GambH & Co.KGaA, Weinheim, 2004: 24-30.
[6] BAMBERGER M. Phase formation in Mg-Sn-Zn alloys—Thermodynamic calculations vs experimental verification [J]. J Mater Sci, 2006, 41: 2821-2829.
[7] SASAKI T T, OH-ISHI K, OHKUBO T, HONO K. Enhanced age hardening response by the addition of Zn in Mg-Sn alloys [J]. Scripta Mater, 2006, 55: 251-254.
[8] LI S S, TANG B, ZENG D B. Effects and mechanism of Ca on refinement of AZ91D alloy [J]. J Alloys Compds, 2007, 437: 317-321.
[9] BEN-HAMU G, ELIEZER D, SHIN K S. The role of Si and Ca on new wrought Mg-Zn-Mn based alloy [J]. Mater Sci Eng A, 2007, 447: 35-43.
[10] QIAN B G, GENG H R, TAO Z D, ZHAO P, TIAN X F. Effects of Ca addition on microstructure and properties of AZ63 magnesium alloy [J]. Transactions of Nonferrous Metals Society of China, 2004, 14(5): 987-991.
[11] LEVI G, AVRAHAM S, ZILBEROV A, Bamberger M. Solidification, solution treatment and age hardening of a Mg-1.6 wt.% Ca-3.2 wt.% Zn alloy [J]. Acta Mater, 2006, 54: 523-530.
[12] OH J C, OHKUBO T, MUKAI T, HONO K. TEM and 3DAP characterization of an age-hardened Mg-Ca-Zn alloy [J]. Scripta Mater, 2005, 53: 675-679.
[13] KOZLOV A, OHNO M, ARROYAVE R, LIU Z K, SCHMID-FETZER R. Phase equilibria, thermodynamics and solidification microstructures of Mg-Sn-Ca alloys, Part 1: Experimental investigation and thermodynamic modeling of the ternary Mg-Sn-Ca system [J]. Intermetallics, 2008, 16: 299-315.
[14] KOZLOV A, OHNO M, ABULEIL T, HORT N, KAINER KU, SCHMID-FETZER R. Phase equilibria, thermodynamics and solidification microstructures of Mg-Sn-Ca alloys, Part 2: Prediction of phase formation in Mg-rich Mg-Sn-Ca cast alloys [J]. Intermetallics, 2008, 16: 316-321.
[15] KIM D H, LEE J Y, LIM H K, KYEONG J S, KIM W T, KIM D H. The effect of microstructure evolution on the elevated temperature mechanical properties in Mg-Sn-Ca system [J]. Mater Trans, 2008, 49(10): 2405-2413.
[16] YANG M B, MA Y L, PAN F S. Effects of little Ce addition on as-cast microstructure and creep properties of Mg-3Sn-2Ca magnesium alloy [J]. Transactions of Nonferrous Metals Society of China, 2009, 19(5): 1087-1092.
[17] YANG M B, PAN F S, CHENG R J, SHEN J. Comparison about effects of Sb, Sn and Sr on as-cast microstructure and mechanical properties of AZ61-0.7Si magnesium alloy [J]. Mater Sci Eng A, 2008, 489: 413-418.
[18] XIAO W L, JIA S S, WANG J, WU Y M, WANG L M. Effects of cerium on the microstructure and mechanical properties of Mg-20Zn-8Al alloy [J]. Mater Sci Eng A, 2008, 474: 317-322.
(Edited by FANG Jing-hua)
Foundation item: Project(50725413) supported by the National Natural Science Foundation of China; Project (2007CB613704) supported by the National Basic Research Program of China; Projects(2006AA4012-9-6, 2007BB4400) supported by Chongqing Science and Technology Commission, China
Corresponding author: YANG Ming-bo; Tel: +86-23-68667455; E-mail: yangmingbo@cqut.edu.cn
DOI: 10.1016/S1003-6326(09)60212-0