
Desiliconisation of alkaline leaching solution of roasted stone coal with carbonation method
LONG Si-si(龙思思), ZHANG Guo-fan(张国范), FENG Qi-ming(冯其明),
OU Le-ming(欧乐明), LU Yi-ping(卢毅屏)
School of Resources Processing and Bioengineering, Central South University, Changsha 410083, China
Received 6 July 2009; accepted 30 December 2009
____________________________________________________________________________________________
Abstract: The effects of reaction time, reaction temperature, stirring speed and flowrate of CO2 gas on desilication rate and loss rate of vanadium were studied. The results indicated that desilication rate increases with the increase of flowrate of CO2 gas and reaction time. Reaction temperature and stirring speed have little effect on desilication rate, while influence the loss rate of vanadium significantly. Under the condition of reaction time of 2 h, reaction temperature of 95 ℃, stirring speed of 180 r/min, flowrate of CO2 gas of 60 mL/min and aging time of 2 h, desilication rate is more than 96% and the loss rate of vanadium is about 4.24%. The residue of desilication process can be processed for silicon materials, such as high-grade hydrated silica, which commonly known as white carbon black. In addition, with this carbonation method, leaching regents NaOH can be recycled by simple treatments.
Key words: separation of vanadium and silicon; carbonation method; stone coal; vanadium
____________________________________________________________________________________________
1 Introduction
Stone coal ore is a kind of vanadium-contained carbonaceous shale[1]. During the past decades, technical progress on leaching vanadium from stone coal mainly focuses on the diversity of roasting additives and selection of suitable leaching reagents[2-5]. Compared with acid (H2SO4 or HCl) leaching technology, alkali (NaOH, Na2CO3 or NaHCO3) leaching technology has lots of advantages, such as little impurity in leaching solution, which is beneficial to the follow-up processes, lower anticorrosion requirement for equipments and the wastewater and solid residue can be directly discharged after simple treatments[6]. Brief flowsheet about the technology of leaching vanadium from roasted stone coal with NaOH solution includes oxidation roasting, alkaline leaching, purification, enrichment of vanadium and preparation[1]. In the process of leaching vanadium from roasted stone coal with NaOH solution, vanadium will be leached into the solution and a large number of impurities such as Si, Al, As and K will also be leached out. To insure the purity of the final product, these impurities should be removed through purification process. The frequently-used method to remove Si from leaching solution is adjusting solution pH with H2SO4, which is called acid method[7]. The main problems of this method are large consumption of H2SO4, large loss rate of vanadium, high cost and especially the leaching reagent NaOH cannot be recycled. The aim of this work is to investigate an innovative method to remove impurities especially Si from leaching solution, which is called carbonation method[8]. Compared with acid method, carbonation method has obvious advantages. On one hand, Si separated from alkaline leaching solution can be recovered and processed into amorphous silica (silicic acid, well-known as white carbon black), which can be used as rubber filler[9]; on the other hand, leaching reagent NaOH can be recovered and reused, which can greatly reduce the cost. The main aim of this work is to remove Si from alkaline leaching solution of roasted stone coal with carbonation method.
2 Experimental
2.1 Sample preparation
The raw material used in this study was prepared as follows: after being crushed and ground, the raw stone coal was put in a furnace and roasted at 850 ℃ for 3 h, and then the roasted stone coal was leached in NaOH solution at 90 ℃ for 2 h and followed by filtration. The filtrate, leaching solution of stone coal, was used as the experimental sample for this study. The mass concen- trations of ions in filtrate were measured by Inductively Coupled Plasma spectrometry (ICP) and the results are presented in Table 1. From Table 1, it can be found that the main elements in the sample are Si, V, Al, K and S. The pH value of the leaching solution is about 13.85.
Table 1 ICP analysis results of alkaline leaching solution of roasted stone coal
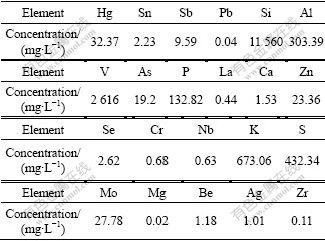
2.2 Experimental principle and method
2.2.1 Experimental principle
ICP analysis results of alkaline leaching solution indicated that concentration of Si in the solution was more than 11 g/L. Silicon with the form of NaSiO3 (Na2O?mSiO2) existed in the alkaline solution. When CO2 gas is put into the solution, the dissolution of CO2 can reduce the pH value of solution. With the continuously dissolution of CO2, hydrated silica is formed according to the equations[10-12]:
Na2O?mSiO2+nH2O+CO2=mSiO2?nH2O↓+Na2CO3 (1)
SiO2?nH2O=SiO2?n′H2O+(n-n′)H2O (2)
Na2CO3+CO2+H2O=2NaHCO3 (3)
Experimental parameters such as reaction time, reaction temperature, stirring time and flowrate of CO2 have remarkable effect on the quality of hydrated silica. The aim of this study is to remove the overwhelming majority of Si from alkaline leaching solution. As a result, high desiliconisation rate will be reached. At the same time, the residue resulted from desiliconisation process can be obtained as junior product of white carbon black. With further treatments, the junior white carbon black can be processed for qualified production, which is the aim of our further research. It is worth noting that in desiliconisation process a certain amount of vanadium will be lost. Thus, loss rate of vanadium should be controlled in a certain range.
2.2.2 Experimental method
The reaction was performed in a 250 mL three- necked-flask equipped with a condenser and mechanical stirrer, and heated directly by water bath. CO2 gas was sent into the flask from pressure tank through rubber tube which attached a glass tube at the end. CO2 gas flow was adjusted and measured by particular valves and flowmeters. Experiments were carried out at certain temperature and for certain time. Then, the CO2 gas and stirring were stopped, and the sample was aged at certain temperature for certain time. Next the solution was filtered and the residue was washed with 100 mL hot water. The filtrate and wash-water were gathered, diluted and analyzed by ICP. The dried and weighed filter residue (junior product) was analyzed to determine the content of SiO2 and V, which was used to calculate the desiliconisation rate and loss rate of vanadium.
3 Results and discussion
3.1 Effect of reaction time
Effects of carbonation time on desilication rate and loss rate of vanadium are shown in Fig.1. It can be seen that the reaction time had significant effect on desilication rate. As the reaction time increased from 30 min to 60 min, the desilication rate increased from 11.52% to 92.61%. When reaction time increased from 60 min to 120 min, desilication rate showed an minor increase, namely from 92.61% to 96.54%. Once the reaction time exceeded 120 min, further increase of reaction time had little effect on desilication rate. At the reaction beginning of Eq.(1), silicon concentration in solution was high; thus, the reaction speed was the fastest[12]. With the reaction carrying on, the silicon concentration sharply reduced. When reaction time reached 60 min, there was little silicon in solution, thus, reaction speed was very slow, which resulted in only slight increase in desilication rate. In addition, Fig.1 also indicates that with the increase of reaction time, loss rate of vanadium gradually reduced. When reaction time was 120 min, the loss rate of vanadium was the least of about 5.69%. Thus, to control the loss rate of vanadium, reaction time of 120 min was preferable. To investigate the effects of other factors, reaction time of 60 min was also chosen in next experiments.
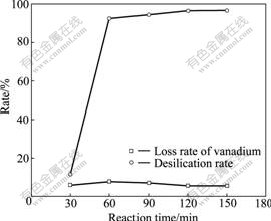
Fig.1 Effects of reaction time on desilication rate and loss rate of vanadium with reaction parameters of reaction temperature of 80 ℃, stirring speed of 180 r/min, flowrate of CO2 gas of 60 mL/min and aging time of 2 h
3.2 Effect of reaction temperature
Experiments under various temperatures were carried out, and the results are shown in Fig.2. It can be known that reaction temperature had a slight effect on desilication rate but significant effect on loss rate of vanadium. With the increase of reaction temperature, loss rate of vanadium rapidly reduced and desilication rate changed little. Reaction temperature increasing from 25 ℃ to 95 ℃ resulted in the decrease of loss rate of vanadium from 23.96% to 4.51%. Temperature had complicated effect on the formation of hydrated silica [13]. Under lower temperature such as ambient temperature, it was easy to form gelatinous precipitate [12, 14]. This was attributed to a layer of dense sodium carbonate film on the surface of gelatinous precipitate formed from the reaction between CO2 and sodium silicate, which prohibited CO2 entering the inside of sodium silicate[12] and formed coagel. In this process, vanadium was encapsulated in gelatinous precipitate. It was the reason that there was higher loss rate of vanadium under lower temperature. With the increase of reaction temperature, the native size of hydrated silica particle reduced and its structure became looser [11-13]. These changes could prevent the encapsulation of vanadium, which induced the decrease of loss rate of vanadium with the increase of reaction temperature. The lowest loss rate of vanadium was obtained at 95 ℃. As a result, the optimum reaction temperature was chosen as 95 ℃ in later experiments.
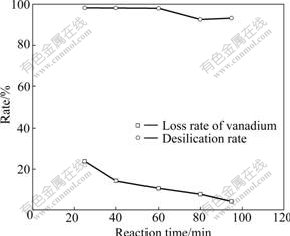
Fig.2 Effect of reaction temperature on desilication rate and loss rate of vanadium with reaction parameters of reaction time of 1 h, stirring speed of 180 r/min, flowrate of CO2 gas of 60 mL/min and aging time of 2 h
3.3 Effect of stirring speed
Effects of stirring speed on desilication rate and loss rate of vanadium are shown in Fig.3. Fig.3 shows that stirring speed had a certain effect on desilication rate and affected the loss rate of vanadium. With the increase of stirring speed from 80 r/min to 180 r/min, the loss rate of vanadium reduced from 11.41% to 4.51%. When the stirring speed continued to increase from 180 r/min to 280 r/min, contrarily, the loss rate of vanadium increased from 4.51% to 5.46%. In general, when stripping speed exceeded 180 r/min, further increase of stirring speed increased the loss rate of vanadium. At the stirring speed of 180 r/min, the loss rate of vanadium was the lowest. In the formation process of hydrated silica, macroscopic physical force such as mechanical stirring and movement of liquid flow had important effects on nucleation, crystal aggregation and crystal growth[15]. Appropriate stirring speed should ensure that gas phase, liquid phase and solid phase were uniformly mixed. Higher stirring speed was not conducive to the nucleation and physical flocculation. It is indicated from Fig.3 that suitable stirring speed was 180 r/min.
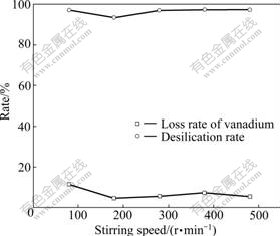
Fig.3 Effect of stirring speed on desilication rate and loss rate of vanadium with reaction parameters of reaction time of 1 h, reaction temperature of 95 ℃, flowrate of CO2 gas of 60 mL/min and aging time of 2 h
3.4 Effect of flowrate of CO2 gas
Fig.4 shows the effect of flowrate of CO2 gas on desilication rate and loss rate of vanadium. It can be seen that when flowrate of CO2 gas was 20 mL/min, desilication rate was only about 58.18%. When flowrate of CO2 gas increased from 20 mL/min to 40 mL/min, desilication rate increased from 58.18% to 96.29%. Further increase of flowrate of CO2 gas had no impact on desilication rate. The reaction of liquid sodium silicate with CO2 gas was controlled by interfacial liquid-film resistance[13, 15]. That was to say, mass transfer rate was dominated by the concentration gradient of CO2 gas. Thus, higher concentration of CO2 gas led to faster reaction and higher desilication rate. The other reactant sodium silicate also influenced the reaction significantly. When the desilication rate reached about 96% (flowrate of CO2 of 40 mL/min), the concentration of the rest sodium silicate in solution was very low. Further increase of CO2 concentration had slight effect on disilication rate, which was indicated in Fig.4. Meanwhile, flowrate of CO2 gas also had obvious effect on the loss rate of vanadium. When flowrate of CO2 gas was 60 mL/min, the loss rate of vanadium was the lowest. Thus, the optimal flowrate of CO2 gas was 60 mL/min.
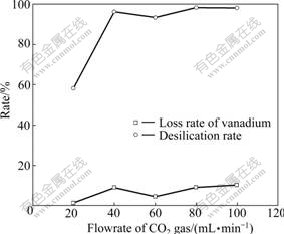
Fig.4 Effect of flowrate of CO2 on desilication rate and loss rate of vanadium with reaction parameters of reaction time of 1 h, reaction temperature of 95 ℃, stirring speed of 180 r/min and aging time of 2 h
From the results above, it can be known that the optimum parameters for carbonation reaction were: reaction time of 2 h, reaction temperature of 95 ℃, stirring speed of 180 r/min and flowrate of CO2 gas of 60 mL/min. With above-mentioned parameters and additional aging time of 2 h, a series of experiments were carried out, from which the average desilication rate of 96% and average loss rate of vanadium of 4.24% were obtained. The content of SiO2 in silicon residue (hydrated silica) was more than 91%.
4 Conclusions
1) Carbonation method is a kind of effective way to remove silicon from alkaline leaching solution of roasted stone coal and to separate the silicon and vanadium. The loss rate of vanadium in this method is equivalent with that of acid method.
2) Reaction time, reaction temperature, stirring speed and flowrate of CO2 gas are main influencing factors. The optimum parameters for carbonation reaction are reaction time of 2 h, reaction temperature of 95 ℃, stirring speed of 180 r/min and flowrate of CO2 gas of 60 mL/min. With the optimum parameters, the average desilication rate can reach 96%, and average loss rate of vanadium is about 4.24%.
3) Loss rate of vanadium can be further reduced to a lower value and the residue can be processed for qualified silicon product.
4) This carbonation method can provide guidance for the treatment of other silicon-contained alkaline solution.
References
[1] HE Dong-sheng, FENG Qi-ming, ZHANG Guo-fan, OU Le-ming, LU Yi-ping. An environmentally-friendly technology of vanadium extraction from stone coal [J]. Minerals Engineering, 2007, 20(12): 1184-1186.
[2] HE Dong-sheng, FENG Qi-ming, ZHANG Guo-fan, LUO Wei, OU Le-ming. Study on leaching vanadium from roasting residue of stone coal [J]. Minerals and Metallurgical Processing, 2008, 25(4): 181-184.
[3] LAN Yao-zhong, LIU Jin. Review of vanadium processing in China [J]. Engineering Science, 2005, 3(3): 58-62.
[4] ZHOU Xiang-yang, LI Chang-lin, LI Jie, LIU Hong-zhuan, WU Shang-yuan. Leaching of vanadium from carbonaceous shale [J]. Hydrometallurgy, 2009, 99(1/2): 97-99.
[5] WANG Ming-yu, XIAO Lian-sheng, LI Qing-gang, WANG Xue-wen, XIANG Xiao-yan. Leaching of vanadium from stone coal with sulfuric acid [J]. Rare Metals, 2009, 28(1): 1-4.
[6] HE Dong-sheng, FENG Qi-ming, ZHANG Guo-fan, OU Le-ming, LU Yi-ping, SHAO Yan-hai. The study on leaching vanadium from stone coal with alkali [J]. Nonferrous Metals (Extractive Metallurgy), 2007, 4: 17-19. (in Chinese)
[7] LI Min-ting, WEI Chang, FAN Gang, LI Cun-xiong, DENG Zhi-gan, LI Xing-bin. Extraction of vanadium from black shale using pressure acid leaching [J]. Hydrometallurgy, 2009, 98(3/4): 308-313.
[8] ZHAO Zhi-ying. Application of deep carbonization precipitation technology in production [J]. Light Metals, 2008(4): 23-25. (in Chinese)
[9] WANG Bao-jun, ZHANG Pei-ping, LI Shu-fa, MA Li-yan, TIAN Li-yu. Application and preparation of amorphous silica [J]. Global Geology, 2006, 25(1): 100-104. (in Chinese)
[10] ADEOGUN M J, HAY J N. Synthesis of mesoporous amorphous silica via silica-polyviologen hybrids prepared by the sol-gel route [J]. Chemistry of Material, 2000, 12(3): 767-775.
[11] YAO Ying. Study of the influence about surface active agent to carbonation white carbon [J]. Tianjin Chemical Industry, 2006, 20(4): 36-37. (in Chinese)
[12] YAO Ying, HE Kai. Preparation of SiO2 using limekiln gas [J]. Journal of Taiyuan University of Technology, 2004, 35(2): 199-211. (in Chinese)
[13] TU Hua, ZHOU Yong-hua, YU Jia-geng, MAN Rui-lin. Preparation of white carbon black with carbonization method and its reaction kinetics [J]. Inorganic Chemicals Industry, 2001, 33(6): 8-11. (in Chinese)
[14] LEE Y K, YOON Y R, RHEE H K. Preparation of colloidal silica using peptization method [J]. Colloids and Surfaces A: Physicochemical and Engineering Aspects, 2000, 173(1/3): 109-116.
[15] YAO Ying. Study of carbonization preparation and surface modification of inorganic active filler white carbon [D]. Taiyuan: Taiyuan University of Technology, 2004: 36-46. (in Chinese)
___________________________
Foundation item: Project(50974133) supported by the National Natural Science Foundation of China
Corresponding author: ZHANG Guo-fan; Tel: +86-731-88830913; E-mail: zhangguofan2002@163.com
(Edited by FANG Jing-hua)