
Dehydriding reaction kinetic mechanism of MgH2-Nb2O5 by Chou model
LIU Yang(刘 杨)1, LI Qian(李 谦)1, CHOU Kuo-chih(周国治)1, 2
1. Shanghai Key Laboratory of Modern Metallurgy and Materials Processing, Shanghai University,
Shanghai 200072, China;
2. School of Metallurgical and Ecological Engineering, University of Science and Technology Beijing,
Beijing 100083, China
Received 12 June 2008; accepted 5 September 2008
Abstract: Chou model was used to investigate the dehydriding reaction kinetic mechanism of MgH2-Nb2O5 hydrogen storage materials at 573 K. A new conception, “characteristic absorption/desorption time (tc)” was introduced to characterize the reaction rate. The fitting results show that for the hydrogen desorbing mechanism, the surface penetration is the rate-controlling step. The mechanism remains the same even when the original particle size of Nb2O5 is before ball milling (BM) or when the BM time changes. And tc indicates that the desorption rate of MgH2-Nb2O5 will be faster than that of MgH2-Nb2O5 by BM. The dehydriding reaction rate of MgH2-Nb2O5 (micro particle) BMed for 50 h is 4.76 times faster than that of the MgH2-Nb2O5 (micro particle) BMed for 0.25 h, while the dehydriding reaction rate of MgH2-Nb2O5 (nano particle) BMed for 50 h is only 1.18 times as that of the MgH2-Nb2O5 (nano particle) BMed for 0.25 h. The dehydriding reaction rate of the BMed MgH2-Nb2O5 (nano particle) is 1-9 times faster than that of the BMed MgH2-Nb2O5 (micro particle).
Key words: MgH2 composite; Chou model; hydrogen desorbing mechanism
1 Introduction
Magnesium hydride is considered one of the most interesting alternatives for the reversible storage of hydrogen because of its high gravimetric hydrogen storage capacity of 7.6%(mass fraction). Magnesium is environmentally benign, abundant, inexpensive and easy to handle. Its limitation for practical applications, however, lies in the poor hydrogen sorption kinetics and high thermodynamic stability[1]. A hydrogen storage alloy requires not only a large hydrogen capacity but also a fast hydriding/dehydriding reaction rate. By using magnesium hydride in nanocrystalline form obtained by BM[2] in combination with transition metal oxide as BM additives[3-4], large improvements in the sorption kinetics have been achieved. Nb2O5 was regarded as one of the best additives[5]. Amongst these mechanisms are the catalysis of hydrogen sorption in magnesium by reduction of activation barrier of hydriding/dehydriding reactions[6-7], facilitation of hydrogen diffusion in the matrix due to changes in the microstructure[8-9] or even a particle size reduction effect and formation of nanoparticles of MgH2 by BM[10] with the additive.
Up to the present, most measurements of hydrogen sorption of MgH2 intermetallic are simply presented as plots of reacted fraction or percentage of reacted amount versus time[11]. Model fitting method is extensively used to study the kinetic mechanism of gas-solid reaction including hydriding/dehydriding reactions in hydrogen storage alloys. Many studies on the kinetic mechanisms of hydriding reaction performed by different investigators got different conclusions, such as the Shrinking Core model[12], Jander model[13] and the First Order Kinetics[14]. Since the hydriding/ dehydriding reaction is involved in a complex heterogeneous solid-gas reaction, the calculation is difficult to get an analytic solution. Therefore, the theoretical investigation on the hydrogen absorption and desorption of kinetics in MgH2-based alloys is still not satisfactory in comparison with the experimental study.
In this paper, the experimental kinetic data of MgH2 intermetallic are summarized from Refs.[15-16]. A new kinetic model proposed in our lab recently[17-18] is applied to analyze the hydrogen desorption kinetic mechanism. From the point of view of practical application, it is desirable to have a simpler and more explicit analytic expression with physical meaning, which is convenient for use and can also give a good prediction under an acceptable simplified assumption. Investigations on the influence of the particle size and the BM time of the composition on the kinetic mechanism are presented.
2 Reference kinetics model
A general mechanism of dehydriding reaction for a particle can be described as the following five steps, they are: 1) hydride decomposition; 2) diffusion of hydrogen atoms in the solid solution; 3) surface penetration of hydrogen atoms; 4) hydrogen molecules formation at the surface of alloy particle; 5) hydrogen in the surface of alloy particle transfer to the bulk gas phase.
Chou model involves a series of analytic equations for various kinds of rate-controlling steps. These formulae express the reacted fraction ξ of hydriding/dehydriding reaction as an explicit function of time t, temperature T, hydrogen partial pressure
p(H2) and particle size R0. Among them, the reacted fraction (or transformation fraction) ξ is a key parameter to describe the kinetic behavior. Besides, the new conception tc is also a very important and useful parameter. The physical meaning of the tc is the required time that the whole particle is completely hydrogenated. The smaller the tc, the faster the hydriding reaction. tc indicating the kinetic ability of storage materials is comparable. Otherwise, since this method gives all possible formulae for calculating the ξ at different processing times for different kinds of assuming controlling steps, the rate-controlling step for any hydriding/dehydriding reaction can be determined by comparing the experimental results with the theoretical equations.
The formulae are deduced by an assumption that all particles of the metal or alloy could be regarded as spherical balls with the same density and radius. The whole particle is a ball of radius R0.
In most cases, the first step is very fast and steps (2) and (3) could be the rate-controlling steps. It is because the diffusion of hydrogen atoms in the solid solution and surface penetration of hydrogen atoms are slower. Sometimes, the process may include a couple of different controlling steps at different stages of the process. When the rate-controlling step is the surface penetration, the relation of the dehydriding reacted fraction ξ and time t is given by
(1)
And when the rate-controlling step is the diffusion of hydrogen atoms in the solid solution, the experiment data will satisfy
(2)
where tc(sp) and tc(d) are tc of the dehydriding reaction which are controlled by surface penetration of hydrogen atoms and diffusion of hydrogen atoms in the solid solution, respectively.
In addition, if we know the value of tc, the kinetics of the hydriding/dehydriding reaction can be described conveniently. However, in most cases, tc is not easy to measured accurately. Therefore, in this paper, linear regression method is used to deduce tc. Eqns.(1) and (2) give us two expressions of the transferred fraction ξ versus t. After a series of mathematical treatments, Eqn.(1) can also be expressed as
(3)
and Eqn.(2) can be expressed as
(4)
Obviously, for a surface penetration step, there is a linear relationship existing between [1-(1-ξ)1/3] and t. And for a diffusion step, the linear relationship is between [1-(1-ξ)1/3]2 and t. A scatter plot can be used to describe the relationship between the variables. At the same time, the relationship between these two variables can be modeled by fitting a linear equation to experimental data. And the slope of the line is the reciprocal of tc(sp) or tc(d).
3 Results and discussion
3.1 Effects of particle size on dehydriding kinetic mechanism of MgH2-Nb2O5
FRIEDRICHS et al[15] investigated the dehydriding property of MgH2-10% Nb2O5(mass fraction) composite. The composite material was synthesized by ball milling the MgH2 and Nb2O5 with the proper stoichiometric ratios in a Fritsch P5 planetary mill with 100 g zirconium oxide balls (d = 10 mm) in a ceramic vial and with a ball to powder mass ratio of 10/1 for 0.25 h. Fig.1 shows the hydrogen desorption kinetics of MgH2 milled with 10% Nb2O5 (nano and micro particles) for 0.25 h at 573 K.

Fig.1 Kinetic curves of MgH2 milled with 10% Nb2O5 (nano and micro particles) for 0.25 h with calculated curves
Based on the experimental data in Fig.1, the plot of [1-(1-ξ)1/3]2 and [1-(1-ξ)1/3] vs t for the materials can be shown in Fig.2.

Fig.2 Plots of [1-(1-ξ)1/3]2 and 1-(1-ξ)1/3 vs t together with regression lines for MgH2 milled with 10% nano and micro Nb2O5 particles for 0.25 h
We model the relationship between these variables by fitting linear equations and list the results in Table 1. It can be known from Table 1 that, for the surface penetration step, the corresponding R2 of the linear regression equations are 0.974 2 and 0.991 4 for nano and micro Nb2O5 particles, respectively.
In contrast to the linear regression result of the surface penetration step, the experimental data can not be fitted by the model with the rate determining step of diffusion. Therefore, the rate-controlling step is surface penetration. For MgH2-10% Nb2O5 (nano and micro particles), a linear relationship exists between 1-(1-ξ)1/3 and t at 573 K as shown in Fig.2. Then, the values of tc(sp) can be calculated from the reciprocal value of slope of the straight line for each material and are listed in Table 1. Substituting theses values into Eqn.(1), three equations are yielded, and the formulae can be expressed as where ξm, ξn, tm and tn are the reaction fractions and reaction time at 573 K for MgH2-10% Nb2O5 (nano and micro particles), respectively.
(5)
(6)
Based on Eqns.(5) and (6), a series of theoretical curves are drawn in Fig.1 together with all experimental data. It can be seen from Fig.1 that there is a good agreement between experimental data and the calculated results. It can be seen from Table 1 that tc(sp)n>tc(sp)m, where tc(sp)n and tc(sp)m are the tc of the nano-particle and micro-particle in the dehydriding reaction which are controlled by surface penetration, respectively. After short milling time, the particle size does not have a significant reduction. Nonetheless the MgH2/Nb2O5-nano sample already achieves very fast desorption kinetics after additional milling time of 0.25 h. Using the nanocrystalline form of Nb2O5 the milling time can be reduced 200 times, displaying a kinetic behavior at the short milling time about 10 times faster than that for the MgH2/Nb2O5-micro sample[15]. Indeed, for the MgH2- 10% Nb2O5 materials synthesized by BM for 0.25 h, the dehydriding reaction rate of the BMed MgH2-Nb2O5 (nano particles) is 9 times faster than that of the BMed MgH2-Nb2O5 (micro particles) compared with their tc directly.
Since the particle size reduction by the milling process can be neglected for the short milling time, this result points to a catalytic effect of the additive[3]. This conclusion is also supported by the fact that the MgH2/Nb2O5-micro sample shows better kinetics than the MgH2/Al2O3-nano sample at shorter milling time[15].
Table 1 Linear regression results of MgH2 milled with 10% nano and micro Nb2O5 particles for 0.25 h
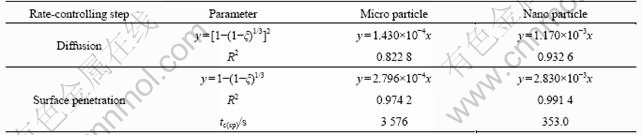
Friedrichs also used the same method to investigate the dehydriding property of the same composite under longer BM time, 50 h. Fig.3 shows the hydrogen desorption kinetics of MgH2 milled with 10% Nb2O5 (nano and micro particles) for 50 h at 573 K.
Based on the experimental data in Fig.3, Fig.4 and Table 2 can be given as below with the same method mentioned in Fig.2 and Table 1.
The relationship between these variables was modeled by fitting linear equations and the results are listed in Table 2.
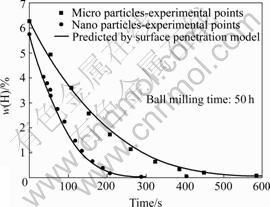
Fig.3 Kinetic curves of MgH2 milled with 10% nano and micro Nb2O5 particles for 50 h

Fig.4 Plots of [1-(1-ξ)1/3]2 and 1-(1-ξ)1/3 vs t together with regression lines for MgH2 milled with 10% nano and micro Nb2O5 particles for 50 h
It can be seen from Table 2 that, for the surface penetration step, the corresponding R2 of the linear regression equations are 0.989 2 and 0.997 0 for nano and micro Nb2O5 particles, respectively. In contrast to the linear regression results of the surface penetration step, the experimental data can not be fitted by the model with the rate determining step of diffusion. Therefore, the rate-controlling step is surface penetration. For MgH2- 10% Nb2O5 (nano and micro particles), a linear relationship exists between 1-(1-ξ)1/3 and t at 573 K as shown in Fig.4. Then, the value of tc(sp) can be calculated from the reciprocal value of slope of the straight line for each material and listed in Table 2. Substituting these values into Eqn.(1) three equations are yielded, the formulae can be expressed as
(7)
(8)
where ξm, ξn and tm, tn are the reaction fractions and reaction time at 573 K for MgH2-10% Nb2O5 (nano and micro particles), respectively.
Based on Eqns.(7) and (8), a series of theoretical curves are drawn in Fig.3 together with all experimental data. It can be seen from Fig.3 that there exists a good agreement between experimental data and the calculated results.
For long BM time, MgH2 milled with 10% Nb2O5 (nano and micro particles) shows similar kinetics, which is strongly enhanced. This result indicates a particle size reduction effect[10] rather than a catalytic one. The generation of higher surface area for the hydrogen uptake and release is then responsible for the kinetic desorption improvement. From Table 2 it can be seen that the tc(sp)n>tc(sp)m. Therefore, for the MgH2-10% Nb2O5 materials synthesized by BM for 50 h, the dehydriding reactions rate of the BMed MgH2-Nb2O5 (nano particle) is twice as fast as that of the BMed MgH2-Nb2O5 (micro particle). And the mechanism also remains the same even the BM time changes.
Table 2 Linear regression results of MgH2 milled with 10% nano and micro Nb2O5 particles for 50 h
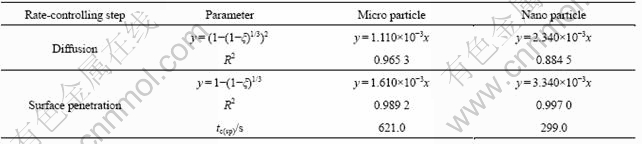
3.2 Effects of BM time on dehydriding kinetic mechanism of MgH2-Nb2O5
FRIEDRICHS et al[15] also investigated the dehydriding property of MgH2-10% Nb2O5 (micro particle) system composites formed by BM. They measured the dehydriding kinetics at 573K for the samples of MgH2 BMed with 10% Nb2O5 (micro particle) for 0.25, 1, 5 and 50 h. Fig.5 gives a plot of the dehydriding kinetic curve corresponding to different samples mentioned above.
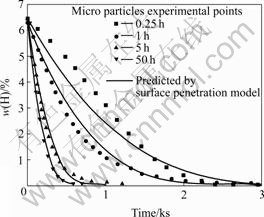
Fig.5 Kinetic curves of MgH2 BMed with 10% Nb2O5 (micro particle) for different times
We model the relationship between [1-(1-ξ)1/3]2 and [1-(1-ξ)1/3] vs t of the materials fitting linear equations and list the results in Table 3.
From Table 3 we know that, for the surface penetration step, the corresponding R2 of the linear regression equations are 0.974 2, 0.982 1, 0.983 7 and 0.989 2 for MgH2 BMed with 10% Nb2O5 (micro particle) for 0.25, 1, 5 and 50 h, respectively. In contrast to the linear regression result of the surface penetration step, the experimental data can not be fitted by the model with the rate determining step of diffusion. Therefore, the rate-controlling step is surface penetration. For MgH2 BMed with 10% Nb2O5 (micro particle) for 0.25, 1, 5 and 50 h the values of tc(sp) can be calculated for each material and listed in Table 3. Substituting theses values into Eqn.(1) four equations are yielded, and the formulae can be expressed as
(9)
(10)
(11)
(12)
where ξm and tm are the reaction fractions and reaction time at 573 K for MgH2 BMed with 10% Nb2O5 (micro particle) for 0.25, 1, 5 and 50 h, respectively.
Based on Eqns.(9)-(12), a series of theoretical curves are drawn in Fig.5 together with all experimental data. It can be seen from Fig.5 that there is a good agreement between the experimental data and the calculated results. With increasing of BM time, the impact on micro-particles changes from catalytic effect to particle size reduction effect. With the BM time increasing further, the particle size will get smaller obviously and much fresher surface will exist. And the micro particles present good properties with more characteristics of nano-particles, which is beneficial to the reaction. It can be seen from Table 3 there exists the sequence as: tc(sp), 0.25 h>tc(sp), 1 h>tc(sp), 5 h>tc(sp), 50 h. Therefore, for the MgH2-10% Nb2O5 materials synthesized by BM, the dehydriding reaction rate of MgH2-Nb2O5 (micro particle) BMed for 50 h is 4.76 times faster than that of the MgH2-Nb2O5 (micro particle) BMed for 0.25 h. The rate-controlling step is the surface penetration, and the mechanism, also remains the same even the BM time changes.
Similarly, FRIEDRICHS et al[15] investigated the dehydriding kinetics at 573 K for the samples of MgH2 BMed with 10% Nb2O5 nanopowder for the same time (0.25, 1, 5 or 50 h). Fig.6 shows the plots of the dehydriding kinetic curve corresponding to different samples mentioned above.
The relationship was modeled between [1-(1-ξ)1/3]2 and [1-(1-ξ)1/3] vs t for the materials fitting linear equations and the results are listed in Table 4.
Table 3 Linear regression results of MgH2 BMed with 10% Nb2O5 (micro particle) for different times

Table 4 Linear regression results of MgH2 BMed with 10% of Nb2O5 (nano particle) for different times
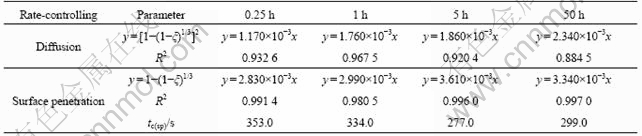
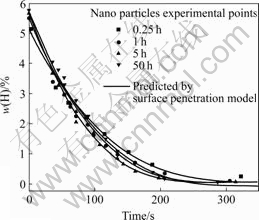
Fig.6 Kinetic curves of MgH2 BMed with 10% Nb2O5 (nano particle) for different times
It can be seen from Table 4 that, for the surface penetration step, the corresponding R2 of the linear regression equations are 0.991 4, 0.980 5, 0.996 0 and 0.997 0 for MgH2 BMed with 10% Nb2O5 (nano particle) for 0.25, 1, 5 and 50 h, respectively. In contrast to the linear regression result of the surface penetration step, the experimental data can not be fitted by the model with the rate determining step of diffusion. Therefore, the rate-controlling step is surface penetration. For MgH2 BMed with 10% Nb2O5 (nano particle) for 0.25, 1, 5 and 50 h, the values of tc(sp) can be calculated for each material as listed in Table 4. Substituting theses values into Eqn.(1) four equations are yielded, and the formulae can be expressed as
(13)
(14)
(15)
(16)
where ξm and tm are the reaction fractions and reaction time at 573 K for MgH2 BMed with 10% Nb2O5 (nano particle) for 0.25 h, 1 h, 5 h and 50 h, respectively.
Based on Eqns.(13)-(16), a series of theoretical curves are drawn in Fig.6 together with all experimental data. It can be seen from Fig. 6 that there exists a good agreement between the experimental data and the calculated results. It can be seen from Table 4 that, for the MgH2-10% Nb2O5 materials synthesized by BM, the dehydriding reaction rate of MgH2-Nb2O5 (nano particle) BMed for 50 h is only 1.18 times as that of MgH2- Nb2O5 (nano particle) BMed for 0.25 h. And the mechanism, the rate-controlling step is the surface penetration, also remains the same even when the BM time changes. Table 4 shows the sequence as: tc(sp), 0.25 h>tc(sp), 1 h>tc(sp), 5 h<tc(sp), 50 h when compared with their characteristic desorption time directly.
With increasing BM time, the impact on nano-particles changes from catalytic effect to particle size reduction effect. Milling with Nb2O5-nanopowder for not a very long time is necessary to improve the hydrogen sorption kinetics significantly, which could be explained by achieving a good contact between the Nb2O5 particles and the MgH2 phase with a high dispersion of the niobium oxide particles in the sample. With the BM time increases further, it is very difficult for nano-particles to refine and the agglomeration of the nano-particles tended to occur because of the high surface activity. After the agglomeration to some extent, the particle becomes larger, which makes the desorption kinetic property worse. But the rate-controlling step is always surface penetration.
4 Conclusions
1) Chou model is used to investigate the hydrogen desorption kinetic mechanism of MgH2-Nb2O5. The results indicate that the rate-controlling step is the surface penetration of hydrogen atoms and can not be changed with original particle size of Nb2O5 before BM. And the mechanism also remains the same even when the BM time changes. It is feasible to apply Chou model to the MgH2 intermetallic system to analyze the hydrogen desorption mechanism.
2) With the linear regression method, the tc value is deduced and the relation of ξ and t is given. The dehydriding reaction rate of the BMed MgH2-Nb2O5 (nano particle) is 1-9 times faster than that of the BMed MgH2-Nb2O5 (micro particle). The dehydriding reaction rate of MgH2-Nb2O5 (nano particle) BMed for 50 h is only 1.18 times as that of the MgH2-Nb2O5 (nano particle) BMed for 0.25 h while the dehydriding reaction rate of MgH2-Nb2O5 (micro particle) BMed for 50 h is 4.76 times faster than that of the MgH2-Nb2O5 (micro particle) BMed for 0.25 h.
References
[1] BOGDANOVI? B, HARTWIG T H, SPLIETHOFF B. The development, testing and optimization of energy storage materials based on the MgH2-Mg system[J]. International Journal of Hydrogen Energy, 1993, 18(7): 575-589.
[2] HU L X, WANG E D. Hydrogen generation via hydrolysis of nanocrystalline MgH2 and MgH2-based composites[J]. Trans Nonferrous Met Soc China, 2005, 15(5): 965-970.
[3] CASTRO F J, BOBET J. L. Hydrogen sorption properties of an Mg+WO3 mixture made by reactive mechanical alloying[J]. Journal of Alloys and Compounds, 2004, 366(1/2): 303-308.
[4] LIANG G, HUOT J, BOILY S, VAN NESTE A, SCHULZ R. Catalytic effect of transition metals on hydrogen sorption in nanocrystalline ball milled MgH-Tm (Tm5Ti, V, Mn, Fe and Ni) systems[J]. Journal of Alloys and Compounds, 1999, 292(1/2): 247-252.
[5] BARKHORDARIAN G, KLASSEN T, BORMANN R. Effect of Nb2O5 content on hydrogen reaction kinetics of Mg[J]. Journal of Alloys and Compounds, 2004, 364(1/2): 242-246.
[6] HUOT J, PELLETIER J F, LIANG G, SUTTON M, SCHULZ R. Structure of nanocomposite metal hydrides[J]. Journal of Alloys and Compounds, 2002, 330/332(2): 727-731.
[7] OELERICH W, KLASSEN T, BORMANN R. Metal oxides as catalysts for improved hydrogen sorption in nanocrystalline Mg-based materials[J]. Journal of Alloys and Compounds, 2001, 315(1/2): 237-242.
[8] STUHR U, STRIFFLER T, WIPF H, NATTER H, WETTMANN B, JANSSEN S, HEMPELMANN R, HAHN H. An investigation of hydrogen diffusion in nanocrystalline Pd by neutron spectroscopy[J]. Journal of Alloys and Compounds, 1997, 253/254: 393-396.
[9] BRASS A M, CHANFREAU A. Accelerated diffusion of hydrogen along grain boundaries in nickel[J]. Acta Materialia, 1996, 44(9): 3823-3831.
[10] KWON I H, BOBET J L, BAE J S, SONG M Y. Improvement of hydrogen-storage properties of Mg by reactive mechanical grinding with Fe2O3[J]. Journal of Alloys and Compounds, 2005, 396(1/2): 264-268.
[11] AGUEY-ZINSOU K F, ARES FERNANDEZ J R, KLASSEN T, BORMANN R. Using MgO to improve the (de)hydriding properties of magnesium[J]. Materials Research Bulletin 2006, 41(6): 1118-1126.
[12] BEREZNITSKY M, JACOB I, BLOCH J, MINTZ M H. Hydriding kinetic properties in massive Zr(AlxCo1-x)2 samples as a function of the Al content[J]. Journal of Alloys and Compounds, 2003, 349(1/2): 316-320.
[13] CUI X Y, LI Q, CHOU K C, CHEN S L, LIN G W, XU K D. A comparative study on the hydriding kinetics of Zr-based AB2 hydrogen storage alloys[J]. Intermetallics, 2008, 16(5): 662-667.
[14] BERNAUER O, T?PLER J, NOR?US D, HEMPELMANN R, RICHTER D. Fundamentals and properties of some Ti/Mn based Laves phase hydrides[J]. International Journal of Hydrogen Energy, 1989, 14(2): 187-200.
[15] FRIEDRICHS O, KLASSEN T, S?NCHEZ-L?PEZ J C, BORMANN R, FERN?NDEZ A. Hydrogen sorption improvement of nanocrystalline MgH2 by Nb2O5 nanoparticles[J]. Scripta Materialia, 2006, 54(7): 1293-1297.
[16] FRIEDRICHS O, S?NCHEZ-L?PEZ J C, L?PEZ -CARTES C, KLASSEN T, BORMANN R, FERN?NDEZ A. Nb2O5 “Pathway Effect” on Hydrogen Sorption in Mg[J]. Journal of Physical Chemistry B, 2006, 110(15): 7845-7850.
[17] CHOU K C, XU K D. A new model for hydriding and dehydriding reaction in intermetallics[J]. Intermetallics, 2007, 15(5/6): 767-777.
[18] CHOU K C, LI Q, LIN Q, JIANG L J, XU K D. Kinetics of absorption and desorption of hydrogen in alloy powder[J]. International Journal of Hydrogen Energy, 2005, 30(3): 301-309.
(Edited by LONG Huai-zhong)
Foundation item: Project(2006AZ001) supported by the Shanghai Municipal Education Commission, China; Project(06JC14031) supported by the Science and Technology Commission of Shanghai Municipality, China; Project(06QA14021) supported by the Shanghai Rising-Star Program (A type), China; Project(200746) supported by the Foundation for the Author of National Excellent Doctoral Dissertation of China; Project supported by the Innovation Fund for Graduate Student of Shanghai University, China
Corresponding author: LI Qian; Tel: +86-21-56338065; Fax: +86-21-56338065; E-mail: shuliqian@shu.edu.cn