J. Cent. South Univ. (2012) 19: 682-687
DOI: 10.1007/s11771-012-1057-7
Experimental assessment of a new salt aerosol generator for
measuring efficiency of automotive air filters
ZHOU Bin(周斌)1, 2, ZHANG Xiao-song(张小松)1, P. Tronville3,HUI Mu-xian(惠慕贤)4, HUI Lü-feng(惠旅锋)4
1. School of Energy and Environment, Southeast University, Nanjing 210096, China;
2. Key Laboratory of Environmental Medicine Engineering of Ministry of Education,Southeast University, Nanjing 210009, China;
3. Politecnico di Torino, Corso Duca degli Abruzzi 24, Torino 10129, Italy;
4. Suxin Cleanroom Equipment Factory, Suzhou 215031, China
? Central South University Press and Springer-Verlag Berlin Heidelberg 2012
Abstract: Generation of polydisperse KCl aerosol with a new salt aerosol generator was investigated. Special attention was paid on particles with diameters between 3 and 10 μm. The main improvement consists of the different routes of KCl solution droplets. In traditional generators, the solution droplets travel through one cylinder; while in the case analyzed here, after spray atomization, the droplets travel through two cylinders in series. The first cylinder was fed with warm air and the second one with cold air. In such way, the complete evaporation of the water from the droplets can be ensured. The influencing factors of the generated aerosol size distribution were investigated. The data measured show that the concentration of generated aerosol becomes higher both increasing the flow rate of the KCl solution injected in the first cylinder and increasing the concentration in the solution. The temperature of solution influences mainly the generation of smaller KCl particles (0.3-3 μm). The amount of hot air used in the generation process increases the concentration of larger KCl particles (>3 μm) while cold air does not have the same effect. The aerosol generator is able to generate KCl aerosol stably. This instrument can be used effectively for testing air filters for automotive.
Key words: aerosol generation; potassium chloride aerosol; droplet-to-particle conversion; air filter testing
1 Introduction
Air filters for automotive applications are used to provide clean air for both engine and occupants inside the cabins. The development and implementation of widely accepted international standards (e.g. ISO standards) have become necessary due to the increasingly expanding market for vehicular air filters and the globalization of the industry [1-2]. These air filters face quite high concentrations of relatively coarse dusts and, especially in urban areas they are also challenged by a high amount of fine carbon particles produced by combustion process. Therefore, the fractional efficiency is used to assess their performance and potassium chloride (KCl) aerosol with optical diameters between 0.3 μm and 10 μm is used as the test aerosol. Hence, it is useful to develop a KCl generator specifically aiming at this type of test.
One aerosol generation method is the droplet-to- particle conversion, which includes droplet generation, evaporation of solvent from droplets, crystallization of solute in the droplet, and formation of a dried particle [3]. In the complex physical and chemical processes of aerosol generation, many parameters will influence the particle size distribution of the generated KCl aerosol. The most important parameters affecting the droplet diameter distribution include liquid properties, atomizer type and configuration, and fluid flow field in the drying chambers. The process of droplet-to-particle conversion process is complex because of the combined effect of flow fields, heat and mass transfer and morphological changes. Both experimental and numerical studies have been performed to investigate this process [4-11]. The classification and characteristics of the preparation method of fine particles are described in terms of gas-to-particle and droplet-to-particle conversion [7]. LEONG [6] examined the morphology of particles generated from the evaporation of solution droplets. ESLAMIAN et al [8] proposed a mathematical model for the entire process of micro- and nano-particle formation, and three physical stages for drying of solution droplets, including shrinkage, induction and constant-diameter periods, were identified. Final particle size, shape, surface state and structure were found to be affected by thermal decomposition temperature, rate of evaporation of the solution droplet and mass of solute present [6-7]. The evolution of droplet size distribution in two-phase flows was modeled when droplet collision and coalescence, evaporation and cooling, gravitational settling, and turbulent dispersion of dispersed phase were considered [4]. A model for the drying of droplets containing suspended solids was published, where the population is evolved using a moment method with an interpolative closure employed in the case of a size dependent solids diffusion coefficient [5]. However, there are few studies related to KCl aerosol generation process. One of them was carried out by MAEDA et al [9] who found that when ethanol was mixed with KCl, the solubility of KCl decreased and the KCl particle size decreased [9].
The aim of this work is to present a new KCl aerosol generator with two sequential cylinders. The characteristics of aerosol generation are investigated with special attention on larger particles and their concentrations.
2 Experimental
Pure water and KCl powder (according to GB/T 646 [12]) were mixed to form the KCl solution. The KCl solution was used in the droplet-to-particle conversion process, which generated droplets with homogeneous concentration and particles with homogeneous chemical composition. Ambient air was used after filtration with three main functions: 1) The kinetic energy of the spray was provided; 2) It was heated to increase the evaporation rate of solution droplets; 3) It was cooled to provide a favorable environment in the condensing cylinder with low relative humidity.
The schematic layout of the aerosol generator is shown in Fig. 1. There are three main parts:
1) Atomization part including compressed air, KCl solution, HEPA filter, and atomizing nozzle;
2) Drying part including atomizing chamber for droplet evaporation and condensing cylinder for condensation;
3) Controlling and adjusting parts including atomizing pressure controller, KCl solution/conditioned air flow meter control valve, compressed air valve after oil-water separation device (pressure ≥ 800 kPa).
A Met One 2400? portable air particle counter (Hach Ultra Analytics, Inc.) was used to measure the particle size distribution and concentration of the generated KCl aerosol. The particle concentrations were measured in the following size ranges: 0.3-0.5, 0.5-1.0, 1.0-3.0, 3.0-5.0, 5.0-10.0 and >10.0 μm. Since high KCl aerosol concentration was the focus of this work, attention was paid on the corresponding concentration. During the experiment, a DS1052E? digital oscilloscope (RIGOL Technologies Inc.) was utilized to track the KCl diameter distribution. The pulse signal displaying on the digital oscilloscope could be used to determine if enough KCl particles had been generated with the required concentration.
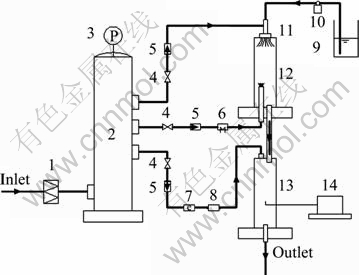
Fig. 1 Schematic diagram of KCl aerosol generator: 1-HEPA filter; 2-Air reservoir; 3-Pressure gauge; 4-Control valve; 5-Air flow meter; 6-Air heater; 7-Air cooler; 8-Air dryer; 9-KCl solution; 10-Solution pump; 11-Nozzle; 12-Atomizing cylinder; 13-Condensing cylinder; 14-Sampling monitor
3 Results
3.1 Relationship between solution pump speed and flow rate
The quantitative relationship between the KCl solution pump speed and the flow rate injected through the nozzle was measured, as illustrated in Fig. 2. At the beginning and the end of each test, a stop watch was used to calculate the time period, and the volume change of the solution was measured with a graduated cylinder. Three measurements were performed for each pump speed and the average value was calculated. In the interval between 14 and 18 r/min of the solution pump speed, the flow rate increases by 0.000 5 L/min when increasing the speed value by 2 r/min.
3.2 Effect of KCl solution injection flow rate
A comparative study was performed with different KCl solution intake flow rates when the pressure of compressed air was fixed at 10 kPa, as shown in Fig. 3. For each condition, three measurements were performed with φmax<5% when the relative difference parameter φ isφ=[max{ni}-navg]/navg.
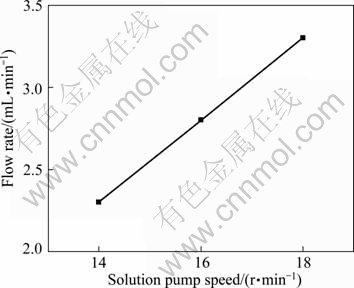
Fig. 2 Correlation between pump speed and KCl solution flow rate
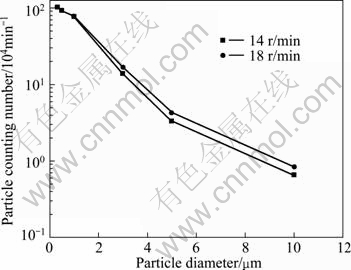
Fig. 3 Measured particle size distributions and concentrations at different pump speeds
The generated KCl aerosols were polydisperse with the diameter range covering the size range from 0.3 μm to 10 μm. The generated particle concentration increased with the KCl solution injection flow rate. The concentration of KCl with diameter of 0.3 μm decreased slightly when the solution injection speed increased from 14 to 18 r/min. As it could be seen from Fig. 3, the larger the generated KCl particle size, the higher the increase of particle concentration, due to the increased injection speed.
3.3 Effect of KCl solution temperature
The temperature of KCl solution is usually the same as the ambient temperature. However, the ambient temperature changes with different locations and seasons. In order to investigate the response of the new KCl generator, the effect of KCl solution temperature on generated KCl concentration, especially in the larger size ranges, was studied. The results obtained are illustrated in Fig. 4. And φmax in this case was <8%.
The influence of KCl solution temperature is stronger for smaller KCl particles (0.3-3 μm). The concentration of small KCl particles is maximum when the solution temperature is 30 ?C. However, the corresponding concentration of 10 μm KCl particles is not the highest. The optimal solution temperature for generating as many 10 μm KCl particles as possible is 25 °C.
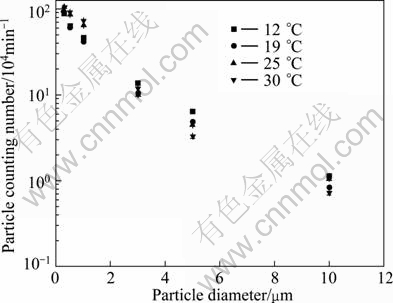
Fig. 4 Measured particle size distributions and concentrations under different KCl solution temperatures
3.4 Effect of KCl solution mass concentration
The test results are shown in Fig. 5 in the case that φmax was <8%. As expected, by increasing the mass concentration of KCl solution from 10% to 20%, the concentration of the generated KCl aerosol after nozzle spraying, heating and cooling became higher. This result is similar as that of MAEDA et al [9] when KCl alcoholic solution was used. In their study, when the mass concentration of KCl in ethanol solution increased, the KCl crystal size increased too.
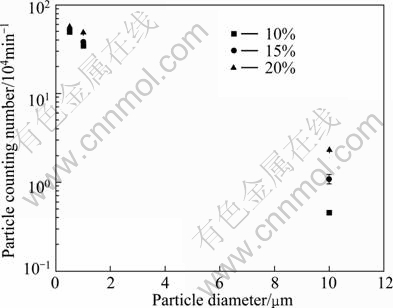
Fig. 5 Measured particle size distributions and concentrations at different KCl solution concentrations
3.5 Effect of hot air and cold air flow rate
The hot air is used in the atomization cylinder while the cold air is passing through the condensing cylinder. The effect of flow rates of hot and cold air was investigated. The results are shown in Fig. 6.
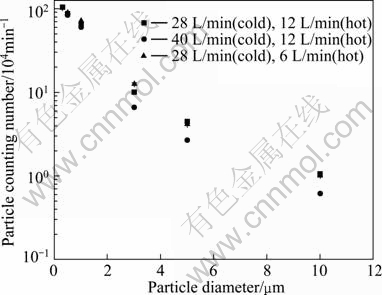
Fig. 6 Measured particle size distributions and concentrations with different hot/cold air flow rates
Three cases with different flow rates of heating/cold air were studied: 1) 28 L/min (467 cm3/s) of cold air with 12 L/min (200 cm3/s) of hot air; 2) 40 L/min (667 cm3/s) of cold air with 12 L/min (200 cm3/s) of hot air; 3) 28 L/min (467 cm3/s) of cold air with 6 L/min (100 cm3/s) of hot air. The results are shown in Fig. 6. The 10 μm KCl particle concentration decreased by 42% when the flow rate of cold air increased from 28 L/min to 40 L/min. Therefore, in order to increase the amount of large particles, it is not useful to increase the cold air flow rate. Cases 1) and 3) showed that 10 μm KCl particle concentration increased by 4.5% when the flow rate of hot air increased from 6 L/min to 12 L/min. Hence, by the increase of the flow rate of hot air, it is likely to generate more 10 μm KCl particles. However, at the same time, the concentration of KCl particle below 3 μm will decrease with larger hot air flow rate, even if it will be still high enough for using the aerosol for testing purpose.
The hot air promotes the heating rate, so that rapid vaporization near the surface takes place and the droplet concentration increases rapidly to produce super- saturated state. At the surface of droplet, the nuclei are generated while the center of the particle remains in a liquid state. This can explain why the concentration of large KCl particles increases by increasing the amount of hot air.
3.6 Stability of KCl aerosol generator
A test was performed to check the stability of this aerosol generator with solution intake speed of 18 r/min and solution concentration of 15%. The test was carried out by analyzing six samples, with each one taken after another during 0.5 h operation time. In Fig. 7, results show that the generated KCl concentrations were (73.93±0.67)×104 min-1 and (0.46±0.01)×104 min-1 for the 1 and 10 μm particle size, respectively. The resulting standard deviations of the concentrations are 0.9% and 1.1% of their average values.
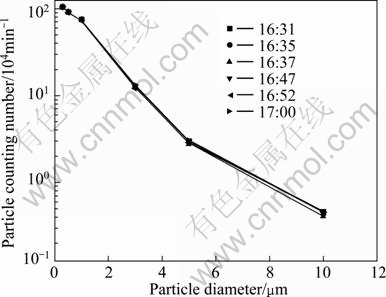
Fig. 7 Measured particle size distributions and concentrations during 30 min operation
4 Discussion
4.1 Particle concentration
Larger particles (i.e. ≥3 μm) were harder to be generated, sampled and measured in comparison with smaller particles (i.e. 0.3-1 μm). This may result in comparatively high concentration for small particles while still obtaining too low concentration for large particles. If the number of large particles is not high enough, the uncertainty of the efficiency measurement in that size range would increase. Ultimately, the efficiency data may become meaningless due to the very high uncertainty associated. This is why the test methods set minimum aerosol concentrations in the test duct.
4.2 Properties of KCl solution
The most relevant properties of a liquid are surface tension, viscosity and density [3]. Figure 8 shows the relationship between solubility of KCl solution, temperature and the corresponding mass concentration.
It can be noted from Fig. 8 that the solubility of KCl increases proportionally with temperature. Such trend is also valid for the relationship between mass concentration and temperature. The temperature range (12-30 ?C) during the experiments and the mass concentrations used in the tests were below the maximum values of mass concentration, i.e. the solution was unsaturated. According to MAEDA et al, the increase of solubility of KCl in ethanol solution because of less ethanol fraction in the solution will result in larger KCl diameters [9]. These findings are confirmed by our results shown in Fig. 4 but with a limitation to the temperature range between 12 and 19 °C. When the solution temperature is between 19 and 30 ?C, the results do not agree with such behavior and this needs further investigation.
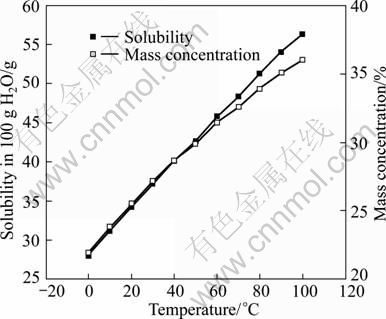
Fig. 8 Relationship among solubility, mass concentration and solution temperature
The characteristic of the surface tension of KCl aqueous solution is shown in Fig. 9. The surface tension decreases as temperature increases, if the mass concentration does not change.
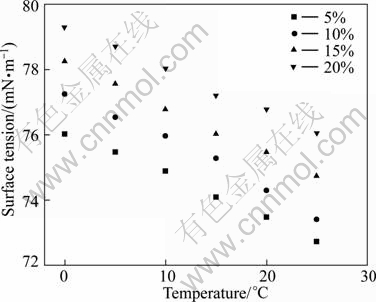
Fig. 9 Effect of mass concentration and temperature on surface tension of KCl aqueous solution [13]
For a fixed mass concentration in the solution, the surface tension of solution droplet decreases with temperature. Moreover, the solubility increases with temperature, which is favorable to form solid particles [6]. This explains why the concentration of small KCl increases with temperature in the experiment. However, it is not clear why the concentration of KCl with 10 μm particles is not the highest when the temperature is 30 °C.
At the same temperature, the surface tension of the solution droplet increases with mass concentration. Droplets with less surface tension are likely to disintegrate into small droplets. This may be the reason why the concentration of generated large KCl aerosol becomes higher when the mass concentration of the KCl solution increases, as shown in Fig. 5.
4.3 Features of KCl generator
A KCl generator with only one evaporating cylinder as the one specified by ANSI/ASHRAE Standard 52.2-2007 was built too. The relative humidity measured inside the cylinder was higher than 70%. This may lead to the generation of wet particles, i.e. still including some water. In ANSI/ASHRAE Standard 52.2-2007, the height of evaporating cylinder is very large for giving more time to the droplets to dry inside the cylinder. The diameter of evaporating cylinder is 305 mm and the height is 1 300 mm. The aerosol generator studied in this work consists of two separate cylinders placed in series. The diameter of each cylinder is 100 mm and the height is 500 mm. The upper cylinder was used as the atomizing cylinder and the lower cylinder as the condensing cylinder for aerosol stream and cold air.
In the upper atomizing cylinder, the water is evaporated to form KCl crystal with the interaction between hot air and the droplets. During this process, smaller droplets will be dried earlier than larger ones [14]. In the lower condensing cylinder, the droplets temperature decreases while they move ahead with cold air. This helps the crystallization of KCl.
The relative humidity measured in the lower cylinder was lower than 70%. The droplets containing KCl could be dried completely to form solid particles [15] and the particle diameter distribution obtained from the particle counter represents the real size distribution of the KCl aerosol. Our experiment shows that, after the KCl generation process, some water droplets got stuck on the interior surface of the upper cylinder, while the surface of the lower cylinder was kept clean.
5 Conclusions
1) A new KCl aerosol generator able to provide large particles in adequate concentration has been engineered and assessed. Particles generated were polydisperse with diameters covering 0.3-10 μm.
2) The higher the KCl solution injected flow rate is, the higher the KCl aerosol concentration is.
3) The KCl solution temperature influences mainly the generation of smaller KCl particles (0.3-3 μm).
4) The flow rate increase of hot air helps generate large (>3 μm) KCl particles while cold air does not.
5) The concentration of generated KCl aerosol is lower when decreasing the solution concentration.
6) The aerosol generator is stable during the aerosol generation process.
References
[1] TRONVILLE P, RIVERS R. International standards: Filters for vehicular applications [J]. Filtration & Separation, 2005, 42(9): 24-27.
[2] ISO/TS 19713-1:2010. Road vehicles-inlet air cleaning equipment for internal combustion engines and compressors-Part 1: Fractional efficiency testing with fine particles (0.3 μm to 5 μm optical diameter) [S]. 2010.
[3] BARON P A, WILLEKE K. Aerosol measurement: Principles, techniques, and applications. 2nd Edition [M]. New York: John Wiley & Sons, 2005: 936-938.
[4] KOLLAR L E, FARZANEH M. Modeling the evolution of droplet size distribution in two-phase flows [J]. International Journal of Multiphase Flow, 2007, 33(11): 1255-1270.
[5] HANDSCOMB C S, KRAFT M, BAYLY A E. A new model for the drying of droplets containing suspended solids [J]. Chemical Engineering Science, 2009, 64(2): 628-637.
[6] LEONG K H. Morphology of aerosol particles generated from the evaporation of solution drops [J]. Journal of Aerosol Science, 1981, 12(5): 417-435.
[7] OKUYAMA K. Preparation of micro-controlled particles using aerosol process [J]. Journal of Aerosol Science. 1991, 22(S1): S7-S10.
[8] ESLAMIAN M, AHMED M, ASHGRIZ N. Modeling of solution droplet evaporation and particle evolution in droplet-to-particle spray methods [J]. Drying Technology: An International Journal, 2009, 27(1): 3-13.
[9] MAEDA K, TOHARA A, ASAKUMA Y, FUKUI K. Formation of fine crystals of potassium chloride dissolved in aqueous ethanol solution by spray evaporation [J]. Chemical Engineering Science, 2009, 48(7): 1270-1273.
[10] VEHRING R, FOSS W R, LECHUGA-BALLESTEROS D. Particle formation in spray drying [J]. Journal of Aerosol Science, 2007, 38(7): 728-746.
[11] LIM E W C, KOH S H, LIM L K, ORE SH, TAY B K, MA Yi-fei, WANG C H. Experimental and computational studies of liquid aerosol evaporation [J]. Journal of Aerosol Science, 2008, 39(7): 618-634.
[12] GB/T 646—1993. Chemical reagent-potassium chloride [S]. 1993.
[13] YAMADA M, FUKUSAKI S, KAWANAMI T, SAWADA I, HORIBE A. Surface tension of aqueous binary solutions [J]. International Journal of Thermophysics, 1997, 18(6): 1483-1493.
[14] MASTERS K. Spray drying handbook. 4th Edition [M]. London: George Godwin Limited, 1985: 185.
[15] ANSI/ASHRAE Standard 52.2-2007. Method of testing general ventilation air-cleaning devices for removal efficiency by particle size [S]. 2007.
(Edited by YANG Bing)
Foundation item: Project(2010EME006) supported by Open Fund of the Key Laboratory of Environmental Medicine Engineering of Ministry of Education of China; Project(51008063) supported by the National Natural Science Foundation of China; Project(3203000601) supported by the Postdoctoral Key Research Program from Southeast University, China; Project(2011BAJ03B05) supported by the National Science and Technology Pillar Program during the 12th Five-Year Plan Period of China
Received date: 2011-07-26; Accepted date: 2011-11-14
Corresponding author: ZHOU Bin, PhD; Tel: +86-13404144095; E-mail: zhoubinwx@hotmail.com