
Plasma surface alloying of titanium alloy for enhancing burn-resistant property
ZHANG Ping-ze(张平则) 1, XU Zhong(徐 重) 1,2, ZHANG Gao-hui(张高会) 2,
HE Zhi-yong(贺志勇) 2,YAO Zheng-jun(姚正军) 1
1.School of Material Science and Technology,
Nanjing University of Aeronautics and Astronautics, Nanjing 210016, China;
2.Institute of Surface Engineering, Taiyuan University of Technology, Taiyuan 030024,China
Received 28 July 2006; accepted 15 September 2006
Abstract: Conventional titanium alloy may be ignited and burnt under high temperature, high pressure and high gas flow velocity condition. In order to avoid this problem, burn-resistant alloying layers were made on the surface of Ti-6Al-4V and Ti-6.5Al-0.3Mo-1.5Zr-0.25Si titanium alloys by using double glow plasma surface alloying technology (DG Technology). Two typical burn-resistant layers Ti-Cr and Ti-Mo were made by DG plasma chromizing and DG plasma molybdenizing, respectively. Burn-resistant properties were tested by layer ignition method using 2 kW laser machine. Ignition experiments result reveals that the ignition temperature of alloyed layer with Mo and Cr concentration above 10% is about 200℃ higher than ignition temperature of Ti-6Al-4V substrate.
Key words: double glow plasma surface alloying; burn-resistant titanium alloy; plasma molybdenizing; plasma chromizing
1 Introduction
Titanium and its alloys have been extensively used in aeronautics and astronautics industries because of their low specific gravities, high strength, stiffness, good toughness and high corrosion resistance. However, conventional titanium alloys may be ignited and burnt under high temperature, high pressure and high gas flow velocity conditions. Titanium fire took place several times in engines[1-4]. This shortcoming limits the application of titanium alloys. In order to avoid this technical problem, Ti-Cr-V, Ti-Cu-Al and Ti-Nb series burn-resistant titanium alloys have been invented since 1990. Nowadays detailed references about burn-resistant titanium alloys are lacked. Typical burn-resistant titanium include alloy C(Ti-35V-15Cr), Ti-45Nb (USA)[4-6], BTT-1(Ti-13Cu-4Al-4Mo-2Zr) (Russia)[7], Ti-25V-15Cr-2Al-0.2C(Great Britain)[8-11] and Ti-40 (China)[12-15]. Though these alloys have obvious burn-resistant property, their limitations are also evident. The main limitation of current burn-resistant titanium is lower strength-gravity ratio induced by adding large amount of heavy alloying elements into titanium alloys. In order to solve these problems, surface burn-resistant titanium alloys were proposed using double glow plasma surface alloying technology(DG Technology) in this paper. Cr and Mo element was introduced into the surface of Ti-6.5Al-0.3Mo-1.5Zr-0.25Si alloy and Ti-6Al-4V alloy. Ti-Cr and Ti-Mo burn-resistant alloy layer was formed on the surface of this conventional titanium alloy. For the surface burn-resistant titanium alloy, loads are endured by substrate, and surface alloyed layer fulfill the function of burn-resistance.
2 Experimental
Ti-6.5Al-0.3Mo-1.5Zr-0.25Si and Ti-6Al-4V were selected as experimental substrate materials. Ti-Cr surface alloying layer was made by double glow plasma surface chromizing process where pure chromium plate was selected as source cathode. Ti-Mo alloying layer was made by double glow plasma surface molybdenizing process, where pure molybdenium was selected as source cathode. Processing temperature of chromizing and molybdenizing was 800-1 000 ℃, working time was 1-6 h, air pressure was 20-50 Pa and working media was pure argon. The negative voltage of the cathode was distributed from 300 V to 600 V and that of the source electrode from 800 V to 1 300 V. Orthogonal experi- ments results indicate that optimized technique parameters are as follows: negative voltage 450 V, source electrode voltage 950 V, working argon gas pressure 25 Pa, temperature 890 ℃. Working time can be selected according to required thickness of alloyed layer, alloyed layer can reach 50 μm in 4 h. Compositions and distributions of the alloying elements in the surface alloy layers produced by DG technology were analyzed by GDS (Glow Discharge Spectroscopy).
3 Results and discussion
3.1 Microstructure and concentration
After DG plasma chromizing, the microstructure of alloyed layer formed on the surface of Ti-6.5Al- 0.3Mo-1.5Zr-0.25Si is shown in Fig.1. The outer layer is the deposition layer made of Cr with width 1-2 μm, it is compound layer beneath the deposition layer. X-ray diffraction analysis and phase diagram analysis show that it consists of α+β substrate microstructure plus little dispersed Cr2Ti intermetallic. Most of Cr elements are dissolved into β phase, little occurs as Cr2Ti intermetallic. Under compound layer, it is the Cr diffusion layer in substrate. Fig.2 shows the distribution of chromium in the Cr-alloyed layer. Ref.[16] indicates that, when Cr content reaches 14%, Ti-Cr binary alloy could be act as burn-resistant titanium alloy.
After DG plasma molybdenizing, the microstruc- ture of alloyed layer formed on the surface of Ti-6Al-4V is shown in Fig.3. The white outer layer is molybdenium deposition layer. Beneath the deposition layer, it is diffusion layer. There is a obvious interface between deposition layer and diffusion layer. Between diffusion layer and substrate, there also exists a obvious interface. It is owing to different solid phase transformations of substrate and alloyed layer during DG processing. Under DG processing temperature(880 ℃), substrate locates in β phase area and Mo can enlarge and stabilize β phase. After cooling, the microstructure of diffusion layer is single β phase solutioned with Mo.
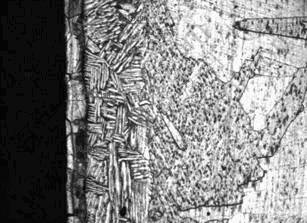
Fig.1 Microstructure of DG plasma chromized layer on Ti- 6.5Al-0.3Mo-1.5Zr-0.25Si surface
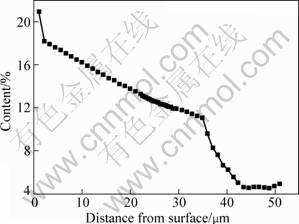
Fig.2 Chromium content in chromized layer
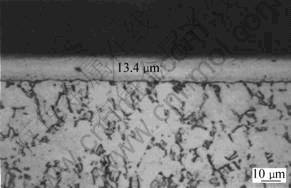
Fig.3 Microstructure of DG plasma molybdenized layer on Ti-6Al-4V surface
Fig.4 shows the distribution of molybdenium in the alloyed layer. Gradually distributed alloying element is beneficial to increasing adhere strength between alloyed layer and substrate. It is noted that Al and V elements are appreciably lower than those in substrate due to ion bombardmen induced surface sputtering.
3.2 Burn-resistance experiments
The burn-resistance experiments are performed using 2 kW laser machine. The surface alloyed samples of titanium alloy were irradiated by laser beam whose diameter was 2.5 mm for 1.5-2.0 s. The laser beam intensity was enlarged gradually until the sample ignition and burn, critical laser intensity function was used as valuable index. Table 1 shows the ignition experiments results.
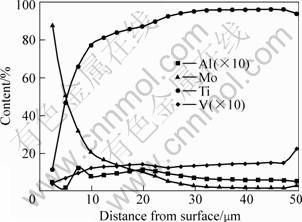
Fig.4 Molybdenium content in molybdenized layer
Table 1 Ignition intensity function of different alloying layers
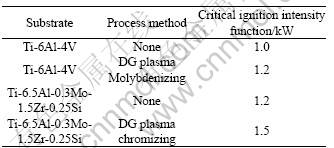
In order to get ignition temperature, a simple model of heat transfer on laser irradiation condition was built. As shown in Fig.5, titanium sample was put on the surface of a infinite carrier block, laser beam with special intensity function irradiated vertically on the sample. For titanium sample, its heat transfer function can be written as
t>0, 0≤x≤d (1)
where d is the thickness of sample.
The initial condition is
Tf(x, 0)=0(Initial temperature is 0 ℃)
The boundary condition is
(2)
where Af is laser absorbent rate(laser intensity function is constant).
For carrier block, heat transfer function, initial condition and boundary condition are as follows:
(t>0, 0≤x≤∞) (3)
Tp(x, 0)=0 (initial temperature is zero) (4)
Tp(∞, t)=0 (temperature in infinite border is zero) (5)
(6)
In interface between sample and block, temperature and heat conductive rate are the same, so,
(7)
(8)
According to above functions and boundary conditions, the temperature distribution form can be gotten as
(9)
where, erfc is error function,
(10)
(11)
Fig.6 shows the temperature distribution near Ti- 6Al-4V surface calculated according to above method and Fig.7 shows the temperature distribution near Ti-6.5Al- 0.3Mo-1.5Zr-0.25Si surface. Obviously, the ignition temperature of both Ti-6Al-4V and Ti-6.5Al-0.3Mo- 1.5Zr-0.25Si increases above 200 ℃ after DG plasma processing.
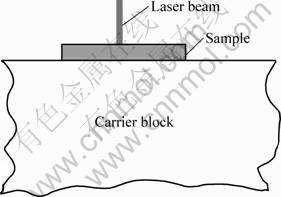
Fig. 5 Laser Ignition model
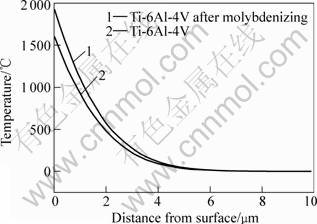
Fig. 6 Temperature distribution near surface of Ti-6Al-4V after DG plasma molybdenizing during laser irradiation
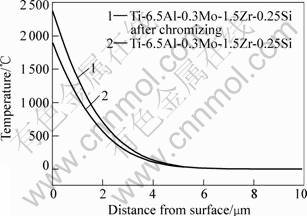
Fig.7 Temperature distribution near surface of Ti-6.5Al-0.3Mo- 1.5Zr-0.25Si after DG plasma chromizing during laser irradiation
4 Conclusions
1) Burn-resistant titanium alloys are successfully made by the DG plasma surface alloying technology upon the surface of conventional titanium alloys. This unique technology is a very powerful means of transforming the ordinary material surface into an exotic alloy layer.
2) The surface alloy produced by this process is a gradient material. Composition in the alloyed surface layer changes gradually in the depth direction of the substrate. Therefore, there exists no distinct boundary between the surface alloy and matrix, and risk of delamination is greatly reduced.
3) After DG plasma molybdenizing and chromizing, laser ignition temperature of Ti-6Al-4V and Ti-6.5Al- 0.3Mo-1.5Zr-0.25Si increases above 200 ℃.
References
[1] GUNAJI, MOHAN V, SIRCAR, SUBHASISH, BEESON, HAROLD D. Ignition and combustion of titanium and titanium alloys[J]. ASTM Special Technical Publication, 1995, 1267(12): 81-85.
[2] WILSON D B, STOLTZFUS J M. Fundamentals of metals in oxygen[J]. ASTM Special Technical Publication, 1997, 1319(10): 272-282.
[3] BOLOBOV V I. Mechanism of self-ignition of titanium alloys in oxygen[J]. Combustion, Explosion and Shock Waves, 2002, 38(6): 639-645.
[4] ROSENBAND V. Thermo-mechanical aspects of the heterogeneous ignition of metals[J]. Combustion and Flame, 2004, 137(3): 366-375.
[5] EYLON D. Issues in the development of beta titanium alloys[J]. Journal of Materials, 1994, 26(6): 14-15.
[6] HEMSON R. New titanium-niobium alloy solves autoclave problem[J]. Advanced Materials and Processes, 1995, 14(5): 27-28.
[7] Hansen J O, Novotnak D, Welter M F, Wood J R. Properties and processing of a high strength beta titanium alloy[C]//Titanium’95: Science and technology. London, 1995: 675-682.
[8] LI Y G, BLENKINSOP P A, LORETTO M H, RUGG D, VOICE W. Effect of carbon and oxygen on microstructure and mechnical properties of Ti-25V-15Cr-2Al(wt%) alloys[J]. Acta Mater, 1999, 47(10): 2889-2905.
[9] LI Y G, LORETTO M H, RUGG D, VOICE W. Effect of heat treatment and exposure on microstructure and mechanical properties of Ti-25V015Cr-2Al-0.2C(wt%) alloys[J]. Acta Mater, 2001, 49(3): 3011-3017.
[10] WU X, SHARMAN R, MEI J, VOICE W. Direct laser fabrication and microstructure of a burn-resistant Ti alloy[J]. Materials and Design, 2002, 23(3): 239-247.
[11] WU X, SHARMAN R, MEI J, VOICE W. Microstructure and properties of a laser fabricated burn-resistant Ti alloy[J]. Materials and Design, 2004, 25(2): 103-109.
[12] ZHAO Yong-qing, ZHOU Lian, DENG Ju. Effects of the alloying element Cr on the burning behavior of titanium alloys[J]. Journal of Alloys and Compounds, 1999, 284(1/2): 190-193.
[13] ZHU K Y, ZHHAO Y Q, QU H L, WU Z L, ZHAO X M. Microstructure and properties of burn-resistant Ti-Al-Cu alloys[J]. Journal of materials science, 2000, 35(22): 5609-5612.
[14] ZHAO Y Q, WU W L, MA X D, et al. Semi-solid oxidation and deformation behavior of Ti14 alloy[J]. Materials Science and Engineering A, 2004, 373(1/2): 315-319.
[15] ZHAO Y Q, QU H L, WANG M M, WU H, ZHU K Y. Thermal stability and creep behavior of Ti-V-Cr burn-resistant alloys[J]. Journal of Alloys and Compounds, 2006, 407(1/2): 118-124.
(Edited by CHEN Can-hua)
Foundation item: Project(50271045) supported by the National Natural Science Foundation of China
Corresponding author: ZHANG Ping-ze; Tel: +86-25-52112904-83132; E-mail: pzzhang@nuaa.edu.cn