
Wetting between molten iron and prereduced ilmenite with carbon
WANG Yu-ming(王玉明)1, 2, YUAN Zhang-fu(袁章福)1, ZHAO Hong-xin(赵宏欣)3,
XIONG Shao-feng(熊绍锋)3, JIANG Wei-zhong(姜伟忠)2, LI Zhao-yi(李肇毅)2
1. Department of Energy and Resources Engineering, College of Engineering,
Peking University, Beijing 100871, China;
2. Institute of Ironmaking Research, Baoshan Iron and Steel Co., Ltd, Shanghai 201900, China
3. State Key Laboratory of Multi-Phase Complex System, Institute of Process Engineering,
Chinese Academy of Sciences, Beijing 100190, China
Received 11 May 2009; accepted 23 July 2009
Abstract: An interfacial study between molten iron and the prereduced ilmenite with carbon was conducted at different melting temperatures by the sessile droplet method. The wetting characteristics between molten iron and the prereduced ilmenites with carbon were investigated by measuring contact angle of the droplet of molten iron on the prereduced ilmenite substrate. The images of the interface were also examined by the optical microscope and SEM equipped with EDS. The volume of molten iron increased with the melting temperature increasing when titania or high-content titania slag was used as the substrate. The contact angle decreased with the melting temperature increasing and it was independent on time at constant temperature. The contact angle was positively correlated with the reduction degree of the ilmenite, but the work of adhesion was negatively correlated with it. Higher smelting temperature was beneficial to the separation of iron and Ti oxides. The permeability of molten iron into the prereduced ilmenite with carbon was more obvious with reduction degree increasing owing to the high porosity of prereduced ilmenite.
Key words: molten iron; prereduced ilmenite; wetting; interfacial permeability; contact angle; carbon reduction
1 Introduction
The minerals, rutile (TiO2) and ilmenite (FeTiO3), are used as raw materials in the production of titanium dioxide pigments. The two main routes for pigment production are the sulfate process and the chloride process[1-4]. Ilmenite is used as feed material for the sulfate process and rutile is used as feed material for the chloride process. However, declining of rutile supplies requests alternative feed materials such as titania slag[5-9]. In industrial process, ilmenite is traditionally smelted in electric arc furnace for the coproduction of pig iron and titania slag. New smelting processes, such as plasma and melt circulation technology, are being developed for saving energy and protecting environment[10-11]. No matter what means are used, oxides in ilmenite feed may react with carbon. Dependent on difference of the density of the products, pig iron and titania-rich slag can be separated at higher temperature. The separation has great effect on the quality of the products, also on downstream production process. Therefore, investigation on the separation of pig iron and titania slag is very important. This work focuses on investigating wetting and interfacial permeability of molten iron and prereduced ilmenite pellet systems, so as to clarify the separation process of iron and titania slag.
Wettability is essentially a spontaneous response at the interface when a liquid is brought into contact with a solid surface. Often, wetting is measured in terms of contact angle, θ, a characteristic angle forming at the solid/liquid/gas interface, as a result of the intermolecular forces acting on the liquid drop[12-18]. The equilibrium contact angle is characterized by classical Young’s equation[19], and is related to surface energies as shown in the following equation:
cos θ=(γSG-γLS)/γLG (1)
where γSG, γLS and γLG are the surface and interfacial tensions at solid/gas, solid/liquid and liquid/gas interfaces, respectively. In this work, the wetting phenomenon between molten iron and the prereduced ilmenite with carbon (CPI) at the melting temperature larger than 1 373 K are studied.
2 Experimental
2.1 Raw materials
The pig iron (chemical composition: 95.50% Fe; 4.30% C; 0.159% Si; 0.008% Mn; 0.027% P; 0.006% S) from Beijing Iron and Steel Co. was machined into a column (about 0.7 g, diameter of 8 mm and height of 8 mm).
2.2 Ilmenite prereduced with carbon
The ilmenite was ground and screened to particle size from 71 to 150 μm. For carbon prereduction, total 10 g ilmenite and graphite were weighed precisely in which the molar ratio of carbon to oxygen from iron oxides (nC/nO) kept constant in all experiments, corresponding to the complete carbon conversion to carbon monoxide. The raw materials were thoroughly mixed by stirring over 30 min with the addition of adhesive, and then pressed into the cylindrical discs (diameter of 16 mm, length of 8 mm) in a steel die under 15 MPa. The sample was placed into a vertical SiC furnace, and preheated for 20 min to ensure that the adhesive and moisture were volatilized fully. The preheated temperature was 823 K. Argon with the flow rate of 1.00 L/min was purged to the tube to provide inert ambience. The reaction temperatures were varied from 1 373 to 1 673 K.
More detailed procedure on the preparation of ilmenite discs prereduced with carbon was described elsewhere[4-5].
2.3 Wetting measurement
Contact angle was measured by using sessile drop equipment, which composed of a horizontal furnace, a digital camera for the image manipulation and observation of the contact angle, a deoxidation furnace and a gas manometer system for controlling the atmosphere.
The pig iron was polished, rinsed in acetone by an ultrasonic cleaner and dried afterward. The iron and the substrate were put into the middle of corundum tube and then sealed. Argon which was purified firstly to high purity (99.999 %) was introduced into the tube to purge oxygen at a flow rate of 400 mL/min. The specimen was heated to prescribed temperature at a rate of 5 K/min. More than five photographs of droplets were captured at each desired experimental temperature as a function of time. The contact angles were calculated by analyzing these photos with self-made software. The mean value of those data at the same temperature was considered as the contact angle at this temperature. The contact angle was measured by the sessile droplet of molten pig iron on the prereduced ilmenite substrate, and the measurement error was estimated to be less than 2%. Details for the apparatus and procedure are described elsewhere[20].
The interfacial topography was observed by optical microscope (Leitz Wetzlar-307) and JSM scanning electron microscopy equipped with energy dispersive spectroscopy (EDS) to observe the distribution of elements. The phases in prereduced ilmenite were investigated by XRD (Philips 1140, Cu Kα, 40 mA and 30 kV).
3 Results
3.1 Wetting between molten iron and prereduced ilmenite
Fig.1 shows a typical morphological evolution of molten iron on the ilmenite substrate prereduced with carbon at experimental temperatures from 1 465 to 1 553 K. Prereduced temperature was 1 573 K and the remaining carbon in the substrate was 0.63% of total mass of the ilmenite substrate. The ilmenite substrates were reduced uniformly and the reduction degree was 93.18%. The cylindrical iron specimen began to collapse at 1 467 K, indicating the melting commenced at this temperature. As shown in Fig.1(d), an intact wetting couple was formed roughly at 1 473 K, from which contact angle became measurable. Molten iron is nonwettable with the ilmenite prereduced with carbon even at the temperature up to 1 553 K, as well as slight decrease in contact angle with temperature could also be observed, as shown in Figs.1(d)-(f).
Fig.2 indicates the variation of contact angle between molten iron and ilmenite prereduced with carbon at different temperatures. The experimental temperature was 1 553 K. Increment of the prereduced temperature caused increment of the contact angle between molten iron and the prereduced ilmenite. Therefore, the wetting between molten iron and the substrate was negatively correlated with the prereduced temperature. All contact angles were more than 90?. The results suggested the reduction at higher temperature was beneficial to the separation of pig iron and titanium oxides. Therefore, in industry process, the smelting reduction temperature was more than 1 873 K.
3.2 Variation of volume of molten iron with experimental temperature
The images of molten iron recorded by a digital camera were processed with the Photoshop software, then the volume of molten iron could be calculated by self-made software. The details of the experimental calculating procedure can be found elsewhere[20].
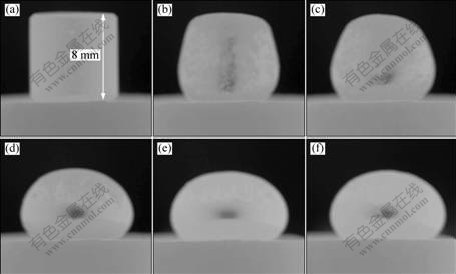
Fig.1 Morphological evolution of wetting couples at different experimental temperatures between molten iron and ilmenite prereduced with carbon at 1 573 K: (a) 1 465 K; (b) 1 467 K; (c) 1 468 K; (d) 1 473 K; (e) 1 513 K; (f) 1 553 K
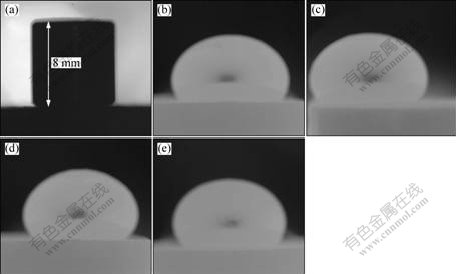
Fig.2 Morphologies of wetting couples at experimental temperature of 1 553 K between molten iron and ilmenite prereduced with carbon at different prereduced temperatures: (a) Original; (b) 1 373 K; (c) 1 473 K; (d) 1 573 K; (e) 1 673 K
The calculating results of the volume with the software are shown as a function of the melting temperature in Fig.3. The high-content titania slag and titania were used as the substrates in the experiment, respectively. The results showed the volume of molten iron increased with the melting temperature increasing; but the relationship between the volume and the temperature was not linear, which agreed with the opinion that with the temperature increasing the density of metal reduced. The increasing rate of volume of molten iron with titania as substrate was less than that of molten iron with high-content titania slag as substrate. This may be due to the diversity of surface roughness for different substrates.
Based on the experimental results, it can be deduced that low temperature leads to more slight difference of density of molten iron with high-content titania slag.
3.3 Variation of contact angle
The contact angle between molten iron and the substrate as a function of experimental temperature is shown in Fig.4(a). The contact angle decreased with the experimental temperature increasing; and the variation of the contact angle was more obvious at lower experimental temperature. All contact angles were much larger than 90?, indicating the poor wettability between molten iron and prereduced products. The contact angle increased significantly with increasing the prereduced temperature of ilmenite with carbon. It was indicated that the complete separation of molten iron from ilmenite in carbon thermal reduction process could be achieved at higher reduction temperature.
Fig.4(b) shows the variation of contact angle with time when ilmenite substrates prereduced with carbon
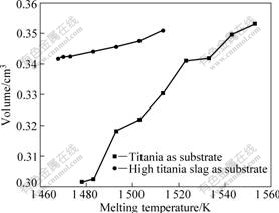
Fig.3 Effect of melting temperature on volume of molten iron with different substrates
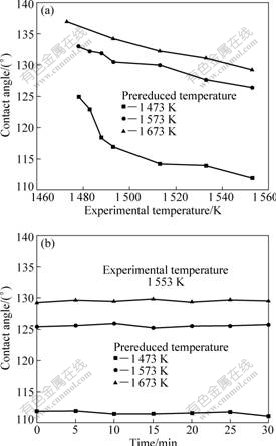
Fig.4 Variation of contact angle between molten iron and ilmenite prereduced with carbon at different reaction temperatures: (a) With various experimental temperatures; (b) With different time at 1 553 K
were used at the experimental temperature of 1553 K. It was seen clearly that the contact angle of molten iron with prereduced ilmenites is time-independent, indicating the wetting is a nonreactive process.
3.4 Interfacial permeability of molten iron and prereduced ilmenite
The morphologies of interfacial permeability between molten iron and ilmenite prereduced with carbon at different prereduced temperatures were observed with optical microscope. As shown in Fig.5, the interfacial permeability was found in these specimens, obviously for the ilmenite substrates prereduced at 1 573 and 1 673 K. It could be seen that the permeable layer thickness increased with increasing prereduced temperature.
High prereduced temperature would result in the increase of carbon consumption, and high porosity of prereduced ilmenite[4]. Molten iron would penetrate more easily into prereduced porous ilmenite discs to form permeability layer. In fact, molten iron was non-wetted with titanium oxides. However, since the pores in prereduced ilmenite were big enough, the penetration force of molten iron into the pores depending on its gravity could overcome the surface tensile between molten iron and Ti oxides. Therefore, large amount of titanium oxides were surrounded by molten iron.
Line scanning analysis of Fe, Ti, O and Si elements by EDS at interface of molten iron and the ilmenite prereduced with carbon is presented in Fig.6. The result showed that molten iron permeated into the substrate to form the layer of permeation of molten iron and the prereduced ilmenite, and the thickness of the interfacial layer was about 300 μm. During the process of permeation, molten iron penetrated into substrate and coalesced with a little amount of reduction iron in the pellet; therefore, the titanium oxides were surrounded by iron to form the layer of permeation.
4 Discussion
From Figs.2 and 4, it can be summarized that the separation between pig iron and reduced product of ilmenite was improved at higher prereduced temperature. Table 1 shows the influence of prereduced temperature on the phase composition of prereduced product by carbon. The sample reduced at 1 473 K contained iron, rutile, reduced rutiles, Ti3O5, carbon and pseudobrookite. At 1 573 K, rutile phase became invisible, which suggested that the reduction reaction was enhanced. Carbon phase disappeared at 1 673 K, which suggested that the pseudobrookite was reduced and decomposed and the reduction reaction was enhanced further. These results show that high temperature is beneficial to
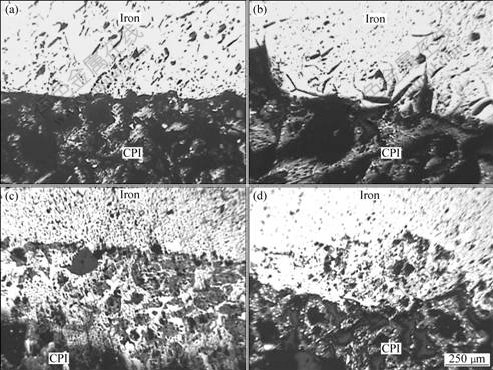
Fig.5 Morphologies of interfaces between solidified iron and ilmenite prereduced with carbon at different prereduced temperatures (Experimental conditions: 1 553 K, 30 min): (a) 1 373 K; (b) 1 473 K; (c) 1 573 K; (d) 1 673 K
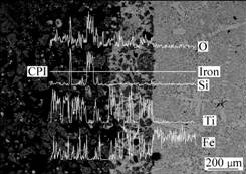
Fig.6 Line scanning micrographs of Fe, Ti, Si and O at interface of molten iron and ilmenite prereduced with carbon
Table 1 X-Ray diffraction analysis result of prereduced ilmenite samples
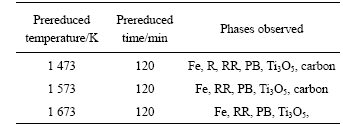
Fe, metallic iron; R, rutile; RR, reduced rutiles; PB, pseudobrookite.
producing Ti oxides by reduction. It was reported that Ti oxides have the poor wettability with most transition metals[20-22]. This might be associated with the increase of contact angles with increasing prereduced temperature for the ilmenites prereduced with carbon.
The reduction degrees of ilmenites prereduced with carbon have been measured at different temperatures in our previous research[4]. Fig.7 shows the relationship between contact angle and reduction degree measured at the experimental temperature of 1 553 K. It can be seen that the contact angle increases when reduction degree increases. However, the increment of reduction temperature was beneficial to the reduction of ilmenite concentrate; therefore, higher reduction temperature was in favor of better separation of pig iron and titanium oxides.
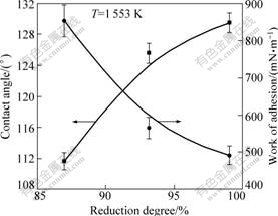
Fig.7 Variations of contact angle and work of adhesion with reduction degree at 1 553 K
Energy balance at the triple line is considered to explain wetting of liquid metal on a solid substrate[16]. The work of adhesion (energy needed to separate liquid iron from the substrate, or vice versa) at static state can be expressed as
W=γLG(1+cosθ) (2)
where W, γLG and θ are work of adhesion, surface tension and contact angle, respectively. Work of adhesion between molten iron and the prereduced ilmenite as a function of reduction degree of the ilmenite is also shown in Fig.7. Work of adhesion between molten iron and the substrate decreased with reduction degree of the ilmenite increasing, which suggested the separation of the molten iron and the prereduced ilmenite turned easier. Reduction degree and the content of titanium oxides in the substrate were positively correlated with reduction temperature. Therefore, complete separation of molten iron and titanium oxides can be achieved at higher reduction temperature in carbon thermal reduction process. The results are in agreement with above results.
5 Conclusions
1) The contact angle between molten iron and the substrate was positively correlated with the reduction temperature. Therefore, higher reduction temperature is beneficial to the separation of pig iron and titanium oxides.
2) The contact angle decreased with melting temperature increasing, and the contact angle was independent with time at constant temperature. With the reduction degree of the ilmenite increasing, the contact angle increased, and the work of adhesion decreased.
3) High prereduced temperature resulted in high porosity of prereduced ilmenite. Therefore, the permeability of molten iron into the substrate was more obvious with reduction degree increasing.
References
[1] WANG Z, YUAN Z F, ZHOU E. Influence of temperature schedules on particle size and crystallinity of titania synthesized by vapor-phase oxidation route [J]. Powder Technology, 2006, 170(3): 135-142.
[2] VIJAY P L, VENUGOPALAN R, SATHIYAMOORTHY D. Preoxidation and hydrogen reduction of ilmenite in a fluidized bed reactor [J]. Metallurgical and Materials Transactions B, 1996, 27: 731-738.
[3] YUAN Z F, WANG X Q, XU C. A new process for comprehensive utilization of complex titania ore [J]. Minerals Engineering, 2006, 19(9): 975-978.
[4] WANG Y M, YUAN Z F. Reductive kinetics of the reaction between a natural ilmenite and carbon [J]. International Journal of Mineral Processing, 2006, 81(3): 133-140.
[5] WANG Y M, YUAN Z F, GUO Z C. Reduction mechanism of natural ilmenite with graphite [J]. Transactions of Nonferrous Metals Society of China, 2008, 18(4): 962-968.
[6] COETSEE T, PISTORIUS C. Preliminary observations on phase relations in the “V2O3-FeO” and V2O3-TiO2 systems from 1400 to 1600℃ in reducing atmospheres [J]. Journal of the American Ceramic Society, 2000, 83(6): 1485-1488.
[7] MORRIS A J, JENSEN R F. Fluidized-bed chlorination rates of Australian rutile [J]. Metallurgical Transactions B, 1975, 7: 1976-1989.
[8] YANG F, HLAVACEK V. Recycling titanium from Ti-waste by a low-temperature extraction process [J]. AIChE Journal, 2000, 46(12): 2499-2503.
[9] YANG F, HLAVACEK V. Effect extraction of titanium from rutile by a low-temperature chloride process [J]. AIChE Journal, 2000, 46(2): 355-360.
[10] GALGALI R K, RAY H S, CHAKRABARTI A K. A study on carbothermic reduction of ilmenite ore in a plasma reactor [J]. Metallurgical and Materials Transactions B, 1998, 29: 1175-1180.
[11] MA N, WARNER N A. Smelting reduction of ilmenite by carbon in molten pig iron [J]. Canadian Metallurgical Quarterly, 1999, 38(4): 165-173.
[12] KANG T W, GUPTA S, SAHA-CHAUDHURY N, SAHAJWALLA V. Wetting and interfacial reaction investigations of coke/slag systems and associated liquid permeability of blast furnaces [J]. ISIJ International, 2005, 45(11): 1526-1535.
[13] LEE J, MORITA K. Dynamic interfacial phenomena between gas, liquid iron and solid CaO during desulfurization [J]. ISIJ International, 2004, 44(2): 235-242.
[14] LEE J, MORITA K. Evaluation of surface tension and adsorption for liquid Fe-S alloys [J]. ISIJ International, 2002, 42(6): 588-594.
[15] LI J, YUAN Z F, QIAO Z, FAN J F, XU Y, KE J J. Measurement and calculation of surface tension of molten Sn-Bi alloy [J]. Journal of Colloid and Interface Science, 2006, 297(1): 261-265.
[16] POIRIER D R, YIN H, SUZUKI M, EMI T. Interfacial properties of dilute Fe-O smelts on alumina substrates [J]. ISIJ International, 1998, 38(3): 229-238.
[17] LEE J, AKIHITO K, TANAKA M. Surface tension of liquid Fe-Ti alloys at 1823K [J]. ISIJ International, 2006, 46(4): 467-471.
[18] MILLS K C, SU Y C. Review of surface tension data for metallic elements and alloys: Part 1—pure metals [J]. International Materials Reviews, 2006, 51: 329-351.
[19] YOUNG T. An essay on the cohesion of fluids [M]. London: Philosophical Transactions of the Royal Society, 1805, 95: 65-87.
[20] MUKAI K, YUAN Z F. Wettability of ceramics with molten silicon at temperatures ranging from 1 693 to 1 773 K [J]. Materials Transactions JIM, 2000, 41(2): 338-345.
[21] YUAN Z F, MUKAI K. Effect of boron on the surface tension of molten silicon and its temperature coefficient [J]. Journal of Colloid and Interface Science, 2004, 270(1): 140-145.
[22] SHINOZAKI N, SONODA M, MUKAI K. Wettability, surface tension and reactivity of the molten manganese/zirconia-yttria ceramic system [J]. Metallurgical and Materials Transactions A, 1998, 29(3): 1121-1125.
(Edited by YANG Bing)
Foundation item: Project(2008AA06Z1071) supported by the National High-tech Research and Development Program of China; Project(50474043) supported by the National Natural Science Foundation of China
Corresponding author: YUAN Zhang-fu; Tel/Fax: +86-10-82529077; E-mail: afuyuan@coe.pku.edu.cn
DOI: 10.1016/S1003-6326(09)60237-5