
Effect of spinning deformation on microstructure evolution and
mechanical property of TA15 titanium alloy
XU Wen-chen(徐文臣)1, SHAN De-bin(单德彬)1, WANG Zhen-long(王振龙)2,
YANG Guo-ping(杨国平)1, L? Yan(吕 炎)1, KANG Da-chang(康达昌)1
1. School of Materials Science and Engineering, Harbin Institute of Technology, Harbin 150001, China;
2. School of Mechatronics Engineering, Harbin Institute of Technology, Harbin 150001, China
Received 15 July 2007; accepted 10 September 2007
Abstract: Hot spinning of tubular workpiece of TA15 alloy was conducted on a CNC spinning machine, and the microstructure evolution during hot spinning and annealing was observed and mechanical properties of spun tubes were tested. The results show that with the increase of spinning pass, the fiber microstructure comes into being gradually in axial direction and the circumferential microstructure also stretches obviously along circumferential direction. At the same time, the tensile strength increases and elongation decreases not only in axial direction but also in circumferential direction. When the reduction ratio of wall thickness rises close to or over 40%, tensile strength increases and elongation decreases more rapidly, which means that tubular workpiece of titanium alloy can be strengthened bi-directionally by power spinning. The ductility of spun workpiece of TA15 alloy could be improved by annealing at the temperature no higher than recrystallization temperature with slight decrease of tensile strength.
Key words: TA15 alloy; hot spinning; microstructure evolution; mechanical property; annealing
1 Introduction
With the development of aviation and aerospace industry, there is an increasing demand for structural components of high strength and low mass, such as large thin-walled rotary workpieces of titanium alloy having high specific strength, excellent corrosion resistance and moderate thermal stability[1-4]. Nowadays those workpieces are mainly produced by roll welding of sheet blanks, in which weld seams existing in axial direction may decrease circumferential strength of tubular workpieces. Tube spinning is one of the most effective techniques to produce large tubular workpiece, by which the forming precision is not less than that of machining and the material utilization and mechanical property of tubular workpiece are superior to machining[5-8]. In addition, as the metal is subjected to rolling deformation during tube spinning, the microstructure and mechanical property of titanium alloy can be improved obviously[9-13]. CHANG et al[9-10] studied the microstructure evolution of 2024 and 7075 aluminum alloy during spinning and the effect of microstructure on microspinnability, and obtained the reasonable process scheme including spinning and heat treatment to fabricate thin-walled tube with high strength and ductility. RAJAN et al[11] conducted the experiment of tube spinning of AISI 4130 steel and established the relationship among mechanical property of spun workpiece, initial tube blank and spinning process parameters, and enhanced the mechanical property of pressure container evidently by means of controlling initial microstructure of tube blank. However, there is no systematic study on microstructure and mechanical property of titanium alloy during hot spinning of tubular workpieces.
In the present work, hot spinning experiment of tubular workpiece of TA15 alloy was conducted on a CNC spinning machine, and the microstructure and mechanical property of spun tube during hot spinning and annealing were studied. The effect of spinning deformation on microstructure and mechanical property of spun workpiece was revealed, and the proper method of heat treatment of spun workpiece of TA15 alloy was obtained. The research could contribute to the application of thin-walled tubular workpieces of titanium alloy working under the condition of complicated stress and large inner pressure.
2 Experimental
2.1 Experimental material
As-rolled bar of TA15 titanium alloy was used in the hot spinning experiments, which was produced by Baoji nonferrous metal works, China, with a diameter of 120 mm. TA15 is a near α alloy containing high aluminium content similar to BT20 alloy in Russia, whose chemical composition is listed in Table 1. TA15 alloy serves as an important structural material in aviation and aerospace industry because of its high strength, good corrosion and creep resistance, and excellent weldability[14]. However, the alloy has low plasticity at ambient temperature and high thermal sensitivity at elevated temperature, which leads to the poor forgeability and narrow forging temperature range of TA15 alloy.
Table 1 Chemical composition of TA15 titanium alloy (mass fraction, %)

2.2 Experimental procedure
Hot spinning experiment of TA15 alloy was conducted on a CNC spinning machine, and the trajectory of the rollers can be programmed flexibly by CAD system of the equipment. The tube blank for spinning experiment was machined from hot rolled bar of TA15 alloy, as shown in Fig.1. According to Ref.[15], it is feasible to deform TA15 titanium alloy in lower temperature range of 600-700 ℃ for some local plastic forming processes with small plastic deformation or strong confined deformation, such as sheet bending and flow forming, so the spinning temperature of tube workpiece was controlled in the range of 600-700 ℃ during tube spinning. Before the spinning experiment started, the mandrel and tube blank were preheated to
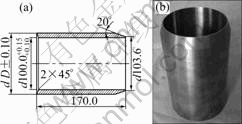
Fig.1 Tube blank of TA15 alloy for hot spinning (D=119.7 mm): (a) Dimension; (b) Macroscopic image
350 ℃ and 650 ℃, respectively. In the process of tube spinning, tube blank was heated by torch to maintain the required temperature range of TA15 alloy that was monitored by infrared thermometer.
In addition, annealing of spun workpiece of TA15 alloy was carried out in order to study the effect of annealing treatment on the microstructure and mechanical property of spun workpieces of TA15 alloy and obtain the proper annealing process scheme.
2.3 Experimental method of microstructure analysis and mechanical property test
The spun workpieces were sectioned in axial and circumferential direction to observe the microstructure of TA15 alloy during hot spinning and annealing. Specimens for optical metallography were etched with a solution consisting of 3%HF-10%HNO3-H2O.
The specimens for tensile test were spark machined from spun tubular workpieces, as illustrated in Fig.2. The axial specimens were directly stretched on INSTRON5569 testing machine. Due to surface shape of tensile specimens, the end of axial specimens should be flattened so that the specimens could be gripped tightly.

Fig.2 Schematic diagram of tension specimen cut from spun workpiece
In order to test circumferential mechanical property of tubular workpieces more exactly, the testing method from Chinese criterion of tension experiment GB/T 17104—1997 was improved in the present work, as indicated in Fig.3. Fig.3(a) shows the schematic diagram of tensile experiment of circular specimen (GB/T 17104—1997), in which circular specimens would be stretched into racetrack shape and severe plastic deformation would take place beside the zone of gage length of circular specimens. Therefore, two semicircle blocks were designed to substitute for the tension rods that exert opposite tensile load on circular workpiece (Fig.3(b)). In this case, plastic deformation was concentrated on the zone of gage length of circular workpiece, beside which little plastic deformation occurred, so the testing result could be improved effectively. Fig.4 shows the schematic diagram of axial and circumferential tension specimens, whose dimensions are listed in Table 2.
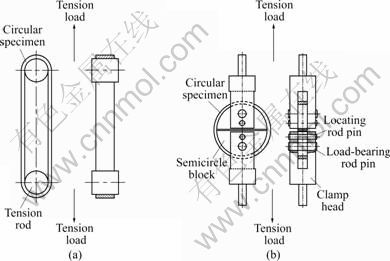
Fig.3 Schematic diagram of tension experiment: (a) GB/T 17104—1997; (b) Improved tension method
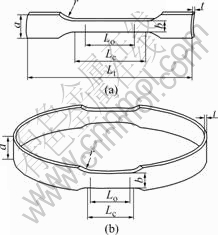
Fig.4 Schematic diagram of tension specimen: (a) Axial specimen; (b) Circular specimen
Table 2 Dimension of tension specimen
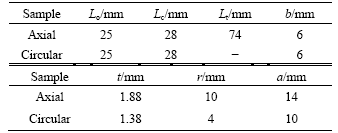
3 Results and discussion
The whole process of tube spinning was completed in five passes and the cumulative reduction ratio reaches 80.9%. The scheme of pass distribution is listed in Table 3. After hot spinning, tubular workpieces were annealed at 700 ℃ and 830 ℃, respectively, for 60 min.
Table 3 Distribution of reduction ratio of spun workpiece
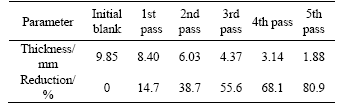
3.1 Microstructure evolution of TA15 alloy during hot spinning and annealing
Fig.5 shows the initial microstructure of as-rolled bar of TA15 alloy. The axial microstructural morphology contains bar-shaped grains that stretches mainly along axial direction under the action of rolling deformation (Fig.5(a)), but the transversal microstructure distributes more randomly(Fig.5(b)).
With the progress of tube spinning process, the reduction ratio of wall thickness increases and the microstructure is refined gradually. After the second spinning pass at the reduction ratio close to 40%, the microstructure starts to refine obviously, but not uniformly along the direction of wall thickness(Fig.6). Subjected to big plastic deformation, the microstructure in outer layer contacting rollers transforms into axial fiber morphology (Fig.6(a)). Despite elongated along axial direction, the microstructure in inner layer contacting mandrel is still coarse because of small deformation (Fig.6(b)). However, there is no microstructure change distinctly along circumferential direction on cross section (Figs.6(c) and (d)). When spinning process proceeds into the 5th pass at the reduction ratio over 80%, the microstructure is refined uniformly all over the deformed region of spun workpiece due to severe plastic deformation (Fig.7). Not
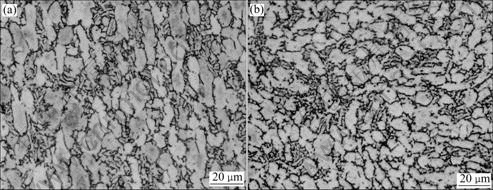
Fig.5 Initial microstructures of tube billet: (a) Axial section; (b) Cross section

Fig.6 Microstructures after 2nd pass of spinning: (a) Outer layer of axial section; (b) Inner layer of axial section; (c) Outer layer of cross section; (d) Inner layer of cross section
only the axial fiber microstructure becomes more fine and homogeneous, but also the transverse microstructure has certain orientation in circumferential direction. The result shows that the rollers have an effect of bi-directional rolling on deformation zone during tube spinning, and the rolling effect in axial direction is more remarkable than that in circumferential direction.
After hot spinning, annealing is conducted to control the microstructure and mechanical property of spun workpiece. Fig.8 displays the different microstructures of spun workpiece of TA15 alloy at the annealing temperature of 700 and 830 ℃ for 60 min. As illustrated in Fig.8, there is no obvious change in the morphology of spun microstructure of TA15 alloy, whether in axial direction or circumferential direction, at 700 ℃ (Figs.8(a) and (b)). When annealed at 830 ℃, the fiber microstructure breaks into large quantities of small grains, clearly shown in the optical photographs of axial and cross section (Figs.8(c) and (d)). As a result, static recovery is the main evolution mechanism of spun microstructure of TA15 alloy at the annealing temperature of 700 ℃, and static recrystallization leads to the breakup of fiber microstructure at the temperature of 830 ℃.
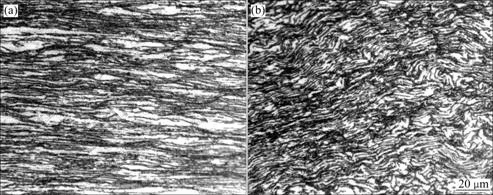
Fig.7 Microstructures after 5th pass of spinning: (a) Axial section; (b) Cross section
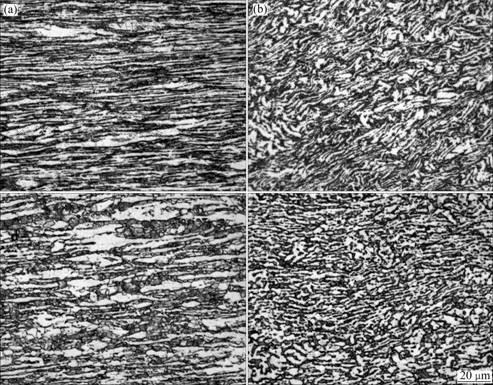
Fig.8 Microstructures at different annealing temperatures: (a) Axial section, 700 ℃; (b) Cross section, 700 ℃; (c) Axial section, 830 ℃; (d) Cross section, 830 ℃
3.2 Mechanical property of TA15 alloy during hot spinning and annealing
In the process of tube spinning, the evolution of microstructure will cause the change of mechanical property of TA15 alloy, which may influence the service performance of spun workpiece. Therefore, it is necessary to study the variation of mechanical property of spun workpiece during tube spinning and annealing. Fig.9 shows the variation of circumferential tensile strength σb and elongation δ of spun workpiece as the spinning pass rises. As can be seen from Fig.9, the circumferential tensile strength increases and elongation decreases with the increase of reduction ratio of wall thickness. When the reduction ratio grows close to or over 40%, tensile strength increases and elongation decreases more rapidly owing to the obvious refinement of spun microstructure.
Fig.10 shows the testing result of tensile strength and elongation of TA15 alloy at different microstructure states. Compared with those of initial specimens cut from tube blank, the axial tensile strength σb of final spun workpiece grows by 22.2% and the elongation δ reduces by 18.0%, while the circumferential tensile strength σb grows by 14.9% and the elongation percentage δ reduces by 53.5%. Therefore, spinning deformation can strengthen bi-directionally the mechanical property of

Fig.9 Circumferential tensile strength and elongation at various reduction ratio of wall thickness
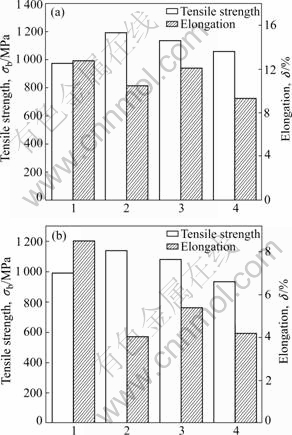
Fig.10 Tensile strength and elongation of TA15 alloy under condition of spinning and annealing: 1 Initial bar; 2 Final spun workpiece; 3 Annealing at 700 ℃; 4 Annealing at 830 ℃; (a) Axial tensile strength and elongation; (b) Circumferential tensile strength and elongation
tubular workpiece owing to the effect of bi-directional rolling, which is more remarkable in axial direction than in circumferential direction. At the same time, material plasticity reduces both in axial and circumferential directions, but the plasticity in axial direction decreases more slowly. After annealing at 700 ℃, the elongation of final spun workpiece grows by 15.3% from 10.49% to 12.1% in axial direction and by 33.4% from 4.04% to 5.39% in circumferential direction. The tensile strength of spun workpiece only decreases by 4.7% from 1 192 MPa to 1 136 MPa in axial direction and by 5.0% from 1 140 MPa to 1 083 MPa in circumferential direction. However, not only the tensile strength but also elongation of spun workpiece at annealing temperature of 830 ℃ reduces more obviously than those at 700 ℃.
Therefore, the annealing temperature has important influence on mechanical property of spun workpiece of TA15 alloy. When annealed at 700℃, static recovery of spun microstructure can release residual stress in spun workpiece and improve the plasticity of spun workpiece effectively, and only slightly reduces the tensile strength. However, static recrystallization of TA15 alloy can cause fiber microstructure to break into small equiaxed grains at 830℃, which may lead to the decrease of tensile strength as well as elongation. Consequently, spun workpiece of TA15 alloy should be annealed at the temperature lower than recrystallization temperature to gain high strength and ductility.
4 Conclusions
1) The tension experiment scheme of circular specimen is improved by two semicircle blocks substituting for the tension rods that could relieve the influence of severe plastic deformation beside the zone of gage length of circular specimens on testing results.
2) With the increase of spinning pass, the fiber microstructure comes into being gradually in axial direction and the circumferential microstructure also stretches along circumferential direction. At the same time, the tensile strength grows and elongation decreases not only in axial direction but also in circumferential direction. When the reduction ratio of wall thickness grows close to or over 40%, tensile strength increases and elongation decreases more rapidly owing to the obvious refinement of spun microstructure. This means that tubular workpiece of titanium alloy could be strengthened biaxially by power spinning due to the effect of bi-directional rolling.
3) The ductility of spun workpiece of TA15 alloy could be improved by annealing treatment at the temperature no higher than recrystallization temperature with slight decrease of tensile strength.
References
[1] BOYER R R. An overview on the use of titanium in the aerospace industry [J]. Mater Sci Eng A, 1996, 213: 103-114.
[2] GORYNIN I V. Titanium alloys for marine application [J]. Mater Sci Eng A, 1999, 263: 112-116.
[3] GURAPPA I. Protection of titanium alloy components against high temperature corrosion [J]. Mater Sci Eng A, 2003, 356(1/2): 372-380.
[4] LI L X, LOU Y, YANG L B. Flow stress behavior and deformation characteristics of Ti-3Al-5V-5Mo compressed at elevated temperatures [J]. Materials and Design, 2002, 33: 451-457.
[5] CHEN Shi-xian, JIA Wen-duo, CAO Geng-shun, ZHAO Hong-wen. Power spinning technology and machine [M]. Beijing: National Defense Industry Press, 1986: 55-114. (in Chinese)
[6] XU Y, ZHANG S H, LU Y. 3D rigid-plastic FEM numerical simulation on tube spinning [J]. J Mater Process Technol, 2001, 113: 710-713.
[7] WONG C C, DEAN T A, LIN J. A review of spinning, shear forming and flow forming processes [J]. Inter J Mach Tool Manu, 2003, 43: 1419-1435.
[8] KALPAKJIAN S, RAJAGOPAL S. Spinning of tubes: A review [J]. J Applied Metal Working, 1982, 2(3): 211-223.
[9] CHANG S C, HUANG C A, YU S Y. Tubes pinnability of AA 2024 and 7075 aluminum alloys [J]. J Mater Process Technol, 1998, 80/81: 676-682.
[10] CHANG S C, WANG C C, HUANG C A. Fabrication of 2024 aluminum spun tube using a thermo-mechanical treatment process [J]. J Mater Process Technol, 2001, 108: 294-299.
[11] RAJAN R M, DESHPANDE P U, NARASIMHAN K. Effects of heat treatment of perform on the mechanical properties of flow formed AISI 4130 tube [J]. J Mater Process Technol, 2002, 125/126: 503-511.
[12] JAHAZI M, ERAHIMI G. The influence of flow-forming parameters and microstructure on the quality of a D6ac steel [J]. J Mater Process Technol, 2000, 103: 362-366.
[13] BRANDON D G., ARI-GUR P, BRATT Z, GUR M. Texture inhomogeneity and the strain distribution in shear-spun steel tubes [J]. Mater Sci Eng A, 1980, 44: 185-194.
[14] HONG Quan, ZHANG Zhen-qi. Hot deformation behavior of Ti-6Al-2Zr-1Mo-1V alloy [J]. Journal of Aeronautical Materials, 2001, 21(1): 10-12. (in Chinese)
[15] XU W C, SHAN D B, YANG G P, LU Y. Flow behavior and microstructure evolution during hot compression of TA15 titanium alloy [J]. Trans Nonferrous Met Soc China, 2006, 16(S3): 2066-2071.
(Edited by YANG Bing)
Corresponding author: XU Wen-chen; Tel: +86-451-86416221; E-mail: xuwc_76@hit.edu.cn