Trans. Nonferrous Met. Soc. China 28(2018) 177-185
Dissolution kinetics of molybdite in KOH media at different temperatures
A. ARACENA1, A. SANINO1, O. JEREZ2
1. Escuela de Ingenieria Quimica, Pontificia Universidad Catolica de Valparaiso, Avenida Brasil 2162, Cod. Postal 2362854, Valparaíso, Chile;
2. Instituto de Geologia Economica Aplicada (GEA), Universidad de Concepcion, Casilla 160-C, Concepcion, Chile
Received 28 November 2016; accepted 18 April 2017
Abstract: The dissolution kinetics of synthetic molybdite (MoO3) in a potassium hydroxide (KOH) medium was studied by varying the system temperature, KOH concentration, and particle size. Additionally, the effects of the stirring rate and different reagents such as barium hydroxide (Ba(OH)2), calcium hydroxide (Ca(OH)2), and sodium hydroxide (NaOH) were also evaluated. The experiments were performed in a reactor with controlled temperature and agitation. The results indicated that the dissolution reaction mechanism of molybdite generates potassium molybdate (K2MoO4) without intermediate compounds. Temperature (6-80 °C), KOH concentration (0.0005-0.025 mol/L), and particle size (5-40 μm) positively affected the dissolution of molybdite. The maximum Mo recovery was 67.5% in 0.25 h for 80 °C and 0.01 mol/L KOH. At the lowest temperature (6 °C), which is near the freezing point of water (0 °C), a substantial amount of Mo was recovered (17.8% in 45 min). The kinetics equation describing the molybdite dissolution in a KOH environment indicated that diffusion occurs through the porous layer. The activation energy was calculated to be 47.81 kJ/mol. A reaction order of 1.0 with respect to KOH concentration was obtained and was found to be inversely proportional to the squared particle size. The kinetics equation was obtained. The dissolution of molybdite resulting from the oxidation of a molybdenite concentrate (MoS2) led to a low molybdenum recovery, which was primarily caused by the consumption of KOH by impurities such as CaCO3 and Cr(MO4)3.
Key words: molybdite dissolution; kinetics; potassium hydroxide
1 Introduction
Alloyed molybdenum (Mo) is mainly used in the electric power, electronics, metallurgy, missile, airline, nuclear energy, chemical, and glass industries [1]. Clearly, molybdenum is a versatile and valuable metal because of its numerous uses. However, using molybdenum for such applications requires that its primary source as molybdenite (MoS2) first be transformed to obtain products commonly used to fabricate salts, such as molybdenum salts, and to ferrous molybdenum and molybdenum trioxide (MoO3), also called molybdite. In general, molybdenite is transformed via pyrometallurgical processing or via roasting at high temperatures. However, roasting molybdenite concentrate results in the oxidation of other species. The maximum content of MoS2 in the concentrate is 49%; the remaining portion includes chalcopyrite (CuFeS2), pyrite (FeS2), and insoluble compounds (SiO2, Al2O3), among other species. Thus, the resulting calcine contains molybdenum trioxide as well as other oxides and impurities such as copper and iron oxides. For this reason, molybdenum trioxide must be treated to eliminate impurities and to recover the molybdenum present in the roasted product. An economical and environmentally friendly alternative is a treatment via hydrometallurgical processes in basic systems. Several studies on molybdite leaching following molybdenite roasting have been performed. For example, JUNEGAR et al [2] roasted a low-grade molybdenum concentrate (20%-45% Mo, 0.35% Cu, 0.17% Ni, and 1.62% Fe) with slaked lime or sodium carbonate at 550-650 °C, followed by leaching in water or sulfuric acid; a 99% Mo dissolution was obtained. The dissolved molybdenum was recovered with activated carbon (>98%) and then precipitated at pH 2 as an oxide. The generated product of MoO3 contained less than 200 mg/kg of the total 11 quantified impurities. Another study performed by SHARIAT et al [3] consisted of processing a calcine mainly consisting of MoO3 (60.9% Mo, 1.3% Cu, 2.9% Fe, 0.16% S, and 1.2% SiO2) by dissolution in ammonium hydroxide. The leaching solution was later treated with ammonium sulfide to remove Cu and other common metals via the sequential precipitation of molybdic acid (H2MoO4) at pH 2. The precipitate was then dissolved in ammonium hydroxide, and ammonium molybdate recrystallized at 60 °C. The final product contained less than 1 mg/kg of several elements (i.e., Ca, Fe, Cu, and As) and 10 mg/kg of Sb. A subsequent study proposed leaching with sulfuric acid and cementation with iron [4] to treat molybdenum oxide and recover copper. The molybdenum oxide contained 70% MoO3, 2.49% Cu2O, 1.97% Fe2O3, and 11.22% SiO2 and was obtained after roasting a molybdenite concentrate. Impurities such as copper and iron were leached from the molybdenum oxide using 1.5% H2SO4 while maintaining a solid:liquid ratio of 1:1 at room temperature (22 °C). SENANAYAKE et al [5] used a mixture of HCl and NH4Cl to remove Cu, Fe, and other impurities from a calcine of MoO3 produced by roasting molybdenite. An increase in the HCl concentration improved the dissolution of Cu and Fe but resulted in a greater loss of molybdenum. At room temperature, a lixiviant of 0.7 mol/L HCl and 0.6 mol/L NH4Cl removed over 80% Cu and 50% Fe from the MoO3 calcine containing 1.04% Cu and 1.45% Fe within 2 h. The loss of Mo was limited to less than 0.5% under these conditions. A temperature increasing to 70 °C promoted a more rapid precipitation of ammonium molybdate and dissolution of Fe, yet no effect on the removal of Cu was observed.
WANG et al [6] proposed a new technology for the recovery of molybdenum from low-grade Ni-Mo minerals using a leaching process that recovered 92.32% of the molybdenum. First, the Ni-Mo compound was roasted at 650 °C for 4 h, followed by leaching the molybdenum with a mixture of Na2CO3 and NaOH. Finally, tailings of a molybdenite concentrate associated with galena were floated subsequent to roasting and then leached in a basic medium with NaOH [7]. In this case, the following optimal conditions were identified: prior roasting at 600 °C for 1 h, alkaline leaching at 130 °C for 1 h with an alkali:total calcined mass ratio of 2:1, initial concentration of 30% NaOH, and a stirring velocity of 600 r/min. Under these conditions, 98% lead and 98% molybdenum present in the floated tailings were extracted.
Although much insight has been gained from these previous studies, none of them have determined their associated kinetic models or parameters such as the activation energy or orders of reaction that would describe the dissolution mechanisms of molybdite. In the present study, these parameters were evaluated for the dissolution of molybdite in a potassium hydroxide medium under different experimental conditions. On the basis of these results, a kinetics model and its associated parameters were then determined.
Electrochemical phase diagrams (φ-pH diagrams) are frequently used to predict the stability of minerals in aqueous solutions. A φh-pH diagram was constructed for a Mo-H2O system at 6, 25, and 80 °C in a solution of 0.025 mol/L KOH and 0.0035 mol/L molybdenum species (Fig. 1). The thermodynamic data used to construct the equilibrium diagram were primarily obtained from the HSC chemistry database [8].
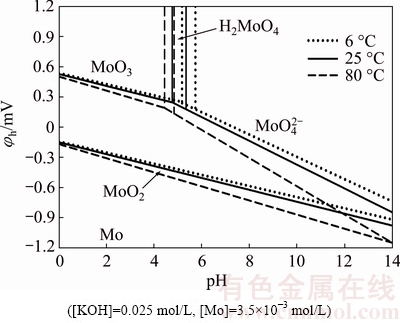
Fig. 1 Potential versus pH as function of temperature in Mo-H2O system
As seen in Fig. 1, an extensive area corresponds to the molybdate anion
at pH of 5.4-14 with potential of -0.9 V at a temperature of 25 °C. At more acidic pH values (4.8-5.4), molybdic acid
forms, and molybdenum trioxide (MoO3) with potential of 0.3 V is present across a wide area at lower pH values (4-4.8).
At the lowest temperature investigated (6 °C), less molybdate is prevalent relative to that at higher temperatures (25 and 80 °C). The equilibrium line of H2MoO3-
corresponds to pH 5.2 and 25 °C. Notably, the pH lowers to 4.8 at 80 °C and increases to 5.6 at 6 °C. Thus, temperature significantly affects the prevalence of the involved species; at elevated temperatures, the prevalence of molybdate increases, whereas the opposite occurs at lower temperatures.
The resulting diagram indicates that leaching molybdite in KOH is thermodynamically possible at pH values above 4.8. The reaction of molybdate with potassium hydroxide is reflected as
MoO3+2KOH=K2MoO4+H2O (1)
The main objective of this study is to describe the dissolution mechanism of molybdate samples in KOH under different experimental conditions involving the following variables: stirring speed, temperature, KOH concentration, particle size, and different reagents. From these data, a kinetics model that represents the dissolution of MoO3 in KOH was obtained, which then permitted the calculation of the activation energy and the orders of the reaction.
In addition, the dissolution of molybdite generated from the oxidation of a molybdenite concentrate (MoS2) was evaluated.
2 Experimental
The synthetic molybdite (Sigma Aldrich) used for the present experiments is a fine powder (under 5 μm) with a purity of 99%. The pelletization method was used to form particles of different sizes; particles were agglomerated by controlled pressure forces to obtain spheres of 10, 20, and 40 μm. The molybdite sample was analyzed by X-ray diffraction (XRD), and the results are shown in Fig. 2(a). The molybdite peaks are observed without interference from other compounds or the molybdenum element.
Experiments were also performed using molybdite from roasted molybdenite concentrates (MoS2). The grade of the concentrate was 82.6% MoS2 and a mixture of impurities. The roasting process was performed at a temperature of 650 °C in a 21% O2 atmosphere with particle size of 123.5 μm. Figure 2(b) shows the XRD data of the molybdenite concentrate relative to a sample of a pure molybdenite concentrate.
Figure 2(c) shows the XRD pattern of the molybdite sample produced by roasting MoS2. The main peaks of molybdite can be identified without interference from any other element or compound. Impurities are not observed, mostly likely because of their low concentration in the concentrate. Subsequently, chemical analyses of the sample of molybdenite were carried out to obtain a degree near 96% of MoO3.
Batch leaching experiments were performed in a 2 L glass reactor equipped with a mechanical agitator, a heating blanket, a thermocouple, a porous tube for liquid samples, and a water-cooled condenser to minimize solution loss by evaporation.
The reactor was filled with 1 L KOH leaching solution. The solution was then heated to the desired temperature, and 1 g of solid material was introduced. As the reaction progressed, liquid samples were extracted at several time intervals to determine the molybdenum content by atomic absorption spectroscopy (AAS). At the end of each experiment, the solution was filtered. The residues were washed and dried before being subjected to XRD analysis.
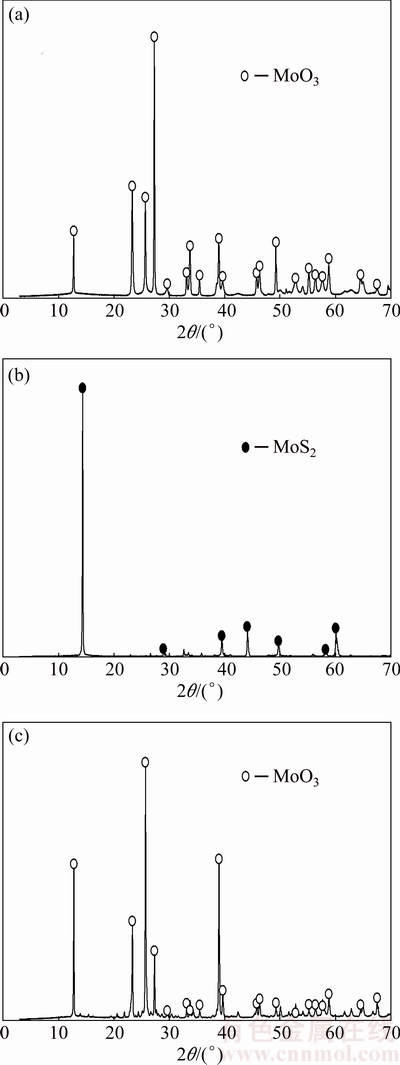
Fig. 2 XRD patterns of original synthetic molybdenite (a), molybdenite concentrate (b) and toasted molybdenite (c)
3 Results and discussion
3.1 Effect of stirring speed
To analyze the effect of stirring speed, several experiments were performed to evaluate the agitation velocities from 200 to 800 r/min. Furthermore, a treatment without agitation was examined. A solution of 0.01 mol/L KOH at 20 °C and a solid:liquid ratio of 1:143 were used as the standard conditions. Figure 3 shows the results of molybdenum recovery as a function of time.
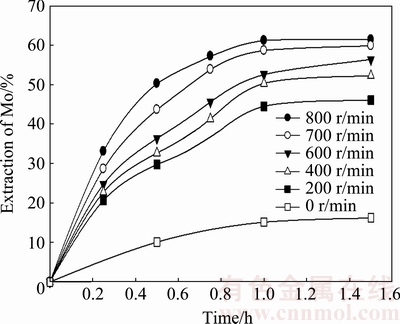
Fig. 3 Effect of stirring speed on leaching velocity of molybdite
Overall, stirring speed plays an important role in the extraction of molybdenum from molybdite. A dissolution of 50.2% molybdite was obtained at 800 r/min after 30 min; reducing the agitation speed to half (400 r/min) decreased dissolution by 17.5%, resulting in 32.7% extraction in the same time. These results indicate that mass transference plays a vital role in the leaching velocity of MoO3. For this reason, a stirring speed of 800 r/min was applied in the subsequent experiments.
Figure 3 also shows that the treatment without agitation (0 r/min) recovered 16.2% molybdenum in 90 min.
3.2 Effect of temperature
Several treatments were performed in a range of temperatures (6-80 °C). A constant agitation at 800 r/min was maintained in a solution of 0.01 mol/L KOH with a solid:liquid ratio of 1:143.
As seen in Fig. 4, a greater quantity of MoO3 is leached and the dissolution velocity increases as the temperature increases. Nearly 60% of Mo is recovered at 20 °C for 1 h; at 60 °C, the same rate of recovery is obtained in just 6 min.
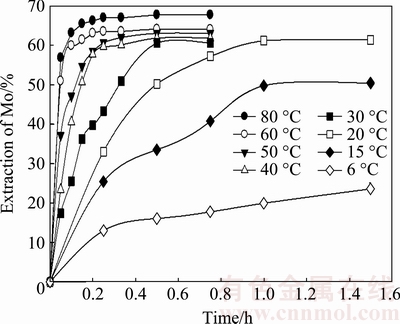
Fig. 4 Extraction of molybdenum at different temperatures as function of time
At the lowest temperature (6 °C), which is near the freezing point of water (0 °C), a substantial amount of Mo (17.8%) was recovered in 45 min.
3.3 Effect of KOH concentration
The effect of the leaching agent concentration on the dissolution velocity of MoO3 was evaluated by testing a range of KOH concentrations between 0.0005 and 0.025 mol/L. Based on Reaction 1 and its stoichiometry, the minimum KOH concentration required to leach molybdenum from molybdite was determined to be 0.01 mol/L. Figure 5 shows the recovery of Mo as a function of time with different KOH concentrations.
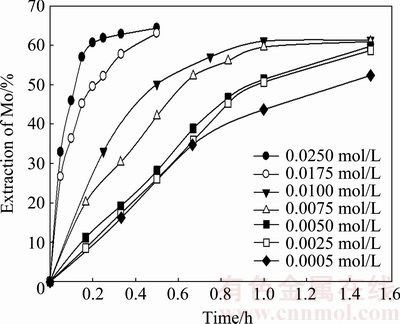
Fig. 5 Effect of KOH concentration on dissolution velocity of MoO3
The KOH concentration impacted the dissolution of MoO3; at 0.005 mol/L KOH, 58.4% recovery was obtained in 1.5 h. Increasing the KOH concentration to 0.025 mol/L resulted in 60.7% recovery in 0.2 h. In other words, the leaching time can be reduced by 1.3 h if the concentration of the KOH solution is increased 10-fold.
Figure 5 shows that the recovery curve of the 0.0005 mol/L KOH solution has a similar behavior to the 0.0050 mol/L KOH solution. In addition, according to the stoichiometric calculations (0.01 mol/L KOH), a notable recovery up to 55% of molybdite, which was dissolved in the solution after 1 h, was obtained.
The dissolution of molybdite is given by Reaction 1. To validate the dissolution reaction of MoO3, an experiment using a 0.01 mol/L KOH solution was performed at 20 °C for 30 min. The resulting Mo extraction curve as a function of time is similar to that shown in Fig. 5. The leached solid sample of molybdite was analyzed by X-ray diffraction (Fig. 6).
As seen, only the molybdite peaks are observed and there is no interference from any other compounds that may have formed. Accordingly, the dissolution mechanism of MoO3 in KOH is represented by Reaction (1).
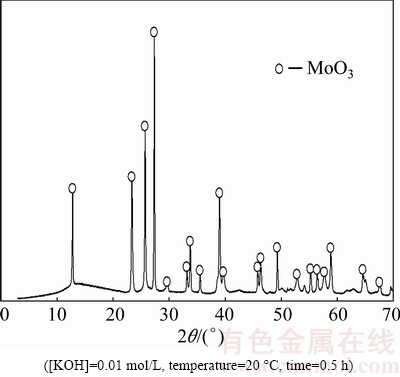
Fig. 6 XRD pattern of leached synthetic molybdite sample
3.4 Effect of particle size
Experiments were performed using several particle sizes (5, 10, 20, and 40 μm) in the 0.01 mol/L KOH solution at 20 °C at a stirring speed of 800 rev/min (Fig. 7). It is found that the dissolution of molybdite decreases with increasing particle size. A dissolution rate of 32% MoO3 was obtained at 1 h for a particle size of 40 μm; the same rate was obtained at 0.5 h for a particle size of 10 μm. The decreasing dissolution velocity of larger particles of molybdite could be caused by a decrease in the interfacial area of the reaction.
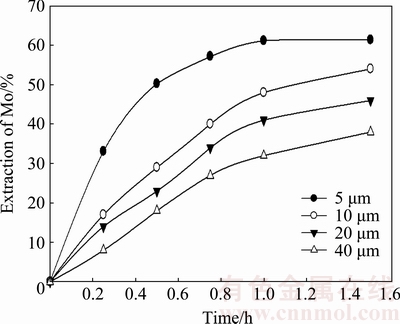
Fig. 7 Effect of particle size on dissolution of MoO3
3.5 Effect of different leaching reagents
The behavior of molybdite dissolution in the presence of different reagents such as barium hydroxide (Ba(OH)2), calcium hydroxide (Ca(OH)2), and sodium hydroxide (NaOH) was studied. The concentration of the leaching agent was maintained constant at 0.01 mol/L as a function of the available OH- for each of the utilized reagents. Experiments were performed at 20 °C with a solid:liquid ratio of 1:143. Figure 8 shows the results for the different reagents.
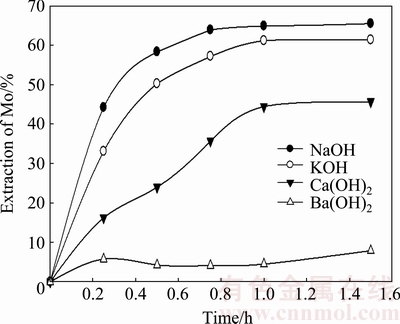
Fig. 8 Effect of different reagents on dissolution of MoO3
At 0.5 h, Ba(OH)2 elicited the lowest molybdenum extraction rate of only 4.2%. Meanwhile, Ca(OH)2 had a higher rate of extraction than Ba(OH)2, reaching 24%, although it was less than that for KOH and NaOH. The comparatively better performances of KOH and NaOH are clear, having extraction rates of 50.2% and 58.3%, respectively, after 0.5 h.
These results reveal that KOH is one of the most suitable reagents for the dissolution of molybdenum trioxide. Notably, NaOH has a molybdenum extraction rate nearly 4% higher than KOH. Thus, this reagent is a good candidate to use to obtain a high dissolution of MoO3.
3.6 Dissolution of roasted molybdite
The roasted molybdite obtained from the roasting of the molybdenite concentrate was used to develop an additional set of experiments under conditions similar to those used for the analysis of synthetic MoO3. The first experiment was performed in 0.01 mol/L KOH solution at 20 °C with a stirring speed of 800 r/min and a solid:liquid ratio of 1:143.
Subsequently, an experimental test was performed under the same conditions with the exception of the KOH concentration, which was raised to 0.025 mol/L. A final leaching experiment was performed under the same initial conditions (0.01 mol/L) but increasing the temperature to 80 °C. The toasted material possessed an average particle size of 124 μm. The experimental results, comparing the dissolution of synthetic and toasted MoO3, are shown in Fig. 9.
For the 0.01 mol/L solution at 80 °C, 52.4% of the roasted material and 67.7% of the synthetic material were recovered; the recovery using the toasted material was 15.4% lower than the synthetic material. In addition, a greater molybdenum recovery from the toasted material was obtained for the same solution (0.01 mol/L) at 80 °C compared with that at 20 °C, resulting in a 6.3% difference. Similar results were obtained at different temperatures and KOH concentrations.
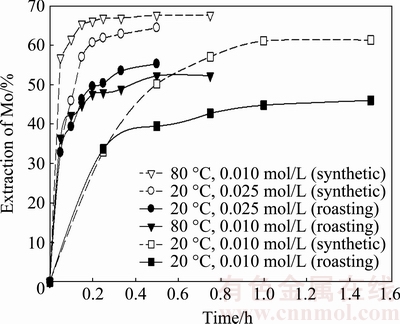
Fig. 9 Dissolution of molybdite resulting from roasting MoS2 and synthetic MoO3 under different conditions
The lower recovery rate from the leached, roasted material compared with the synthetic MoO3 could be caused by the distinct species present in the roasted material, which may be consuming the leached reagent (KOH). Figure 10 depicts the XRD pattern showing the presence of these species, mainly Cr(MoO4)3 and CaCO3. The principal reactions that describe the consumption of KOH are as follows:
CaCO3+KOH→Ca(OH)2+K2CO2 (2)
Cr(MoO4)3+6KOH→3K2MoO4+Cr(OH)6 (3)
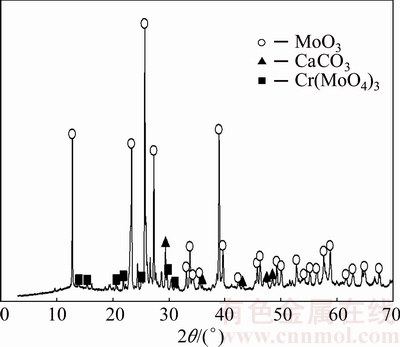
Fig. 10 XRD pattern of leached sample of molybdite produced by roasting molybdenite concentrate
Accordingly, CaCO3 and Cr(MoO4)3 would consume 1 mol and 6 mol KOH, respectively, representing a consumption 3.5 times greater than that observed in Reaction 1.
3.7 Dissolution kinetics of synthetic MoO3
As seen in Fig. 4, temperature does not significantly affect the extraction of molybdenum from molybdite. This behavior suggests that the process is controlled by diffusion via the outer porous layer of the mineral. In this case, the reaction velocity would follow a recessive nucleus model in which diffusion is controlled by the porous layer of radius for a constant concentration of reagents, expressed as the following equation [9]:
1-(2/3)X-(1-X)2/3=kt (4)
where X is the reacted fraction of molybdite, t is the time of reaction, and k is the apparent kinetics constant given by the following general expression:
(5)
where k1 is the intrinsic velocity constant, CKOH is the KOH concentration, and b is a stoichiometric constant. Lastly, m is the order of reaction with respect to the concentration of potassium hydroxide, and r0 is the initial radius of the particle.
Figure 11 shows the graph of 1-(2/3)X-(1-X)2/3 as a function of time using the experimental data highlighted in Fig. 4, at temperatures ranging from 6-80 °C for the dissolution of 5 μm samples of molybdite. As seen, the good linear fit of the kinetics data with the regression model (R2) from 0.94 to 0.99 over the given temperature range indicates the suitability of Eq. (5). The kinetics constants at various temperatures were obtained from the slopes of the straight lines and are shown in Table 1.
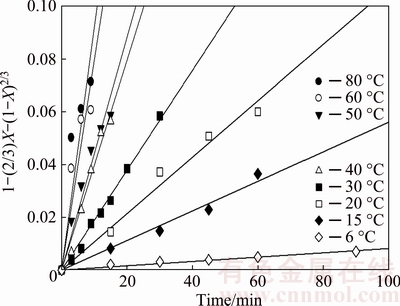
Fig. 11 Dissolution kinetics of molybdite for average particle size of 5 μm in KOH-H2O system under same conditions as Fig. 4
Table 1 Velocity constants for dissolution of molybdite with potassium hydroxide
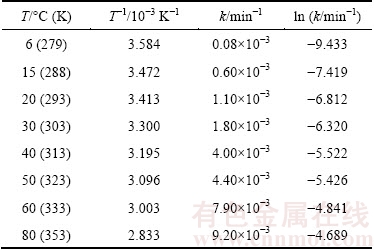
The order of reaction, m, was calculated from the kinetic data on the effect of the KOH solution concentration. Figure 12 shows the experimental data for several KOH concentrations according to Eq. (4); the k values were used to graph ln k versus ln CKOH, as shown in Fig. 13. As seen, a linear relationship is obtained with R2 value equal to 0.87. The slope indicates an order of reaction of 1.0 with respect to the KOH solution concentration.
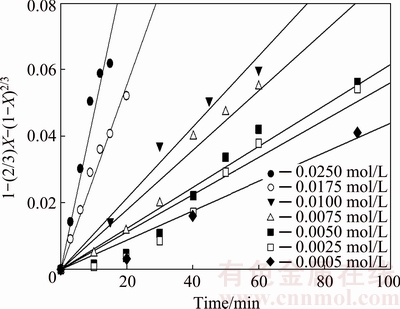
Fig. 12 Dissolution kinetics of molybdite samples at different KOH concentrations with average particle size of 5 μm under same leaching conditions as Fig. 5
Because the kinetics are controlled by diffusion via the outer porous layer, k should vary linearly with the inverse of the initial squared radius of the particle, as indicated in Eq. (5). To verify this dependence, the data related to the particle size (Fig. 7) were adjusted to Eq. (4), giving the results shown in Fig. 14.
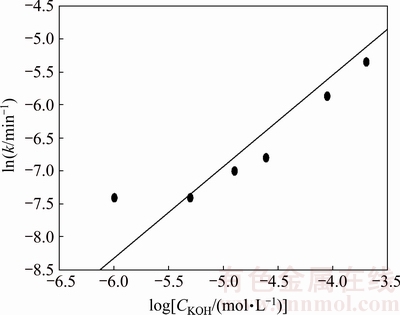
Fig. 13 Order of reaction with respect to KOH concentration
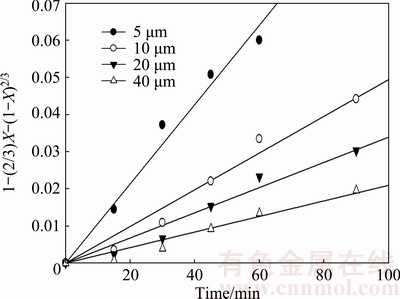
Fig. 14 Dissolution kinetics of molybdite samples with different particle sizes under same leaching conditions as Fig. 7
The resulting k values were plotted as a function of the inverse of the initial particle radius to the second power (Fig. 15). The adequate linear dependence of the data in Fig. 15 (R2>0.89) supports the kinetics model employed.
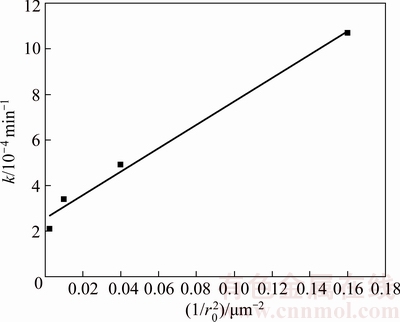
Fig. 15 Dependence of velocity constant on squared inverse of initial particle size on leaching of molybdite
Consequently, the intrinsic oxidation velocity constant, k1, at different temperatures can be calculated using the values of the kinetic constants obtained in Fig. 11, using the m value of 1.0 and particle radius of 2.5 μm. The b value is equal to 1/2 according to the stoichiometry of Reaction 1. Table 2 shows both the apparent and intrinsic constants for the temperature ranges examined in this study.
Table 2 Velocity constants for dissolution of molybdite in temperature range of 6-80 °C
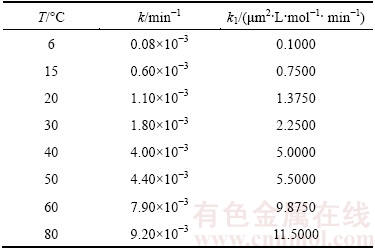
The values calculated for the intrinsic velocity constants, k1, were used to construct the Arrhenius plot shown in Fig. 16. As seen, a good linear fit is obtained (R2>0.86) with the apparent kinetics constants corresponding to each temperature. The calculated activation energy is 47.81 kJ/mol in the temperature range of 6-80 °C, which is typical for a reaction controlled by diffusion via a porous layer.
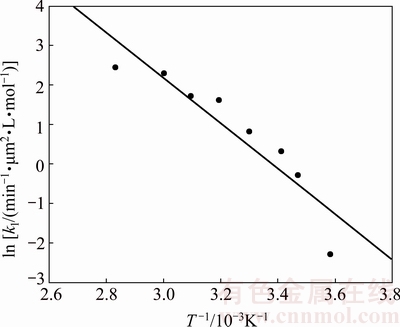
Fig. 16 Arrhenius graph for dissolution of molybdite in KOH-H2O media
The dissolution kinetics of molybdite in a KOH system can be represented by the following equation:

(6)
where k1=2.77×108 μm2·L·mol-1· min-1.
4 Conclusions
1) The dissolution mechanism of molybdite in the presence of KOH results in the production of potassium molybdate without intermediate compounds.
2) Temperature, KOH concentration, and particle size affect the velocity of molybdite dissolution.
3) The kinetics equation that represents the dissolution of molybdite is controlled by diffusion through the porous layer, given as 1-(2/3)X-(1-X)2/3=kt.
4) The calculated activation energy is 47.81 kJ/mol, which is typical for diffusion controlled through a porous layer.
5) The dissolution velocity of MoO3 is 1.0 with respect to the KOH concentration and is inversely proportional to the particle size squared.
6) The dissolution of molybdite resulting from roasting molybdenite results in low rates of recovery, primarily because of the consumption of KOH by impurities such as CaCO3 and Cr(MO4)3.
References
[1] GUPTA C K. Extractive metallurgy of molybdenum [M]. Florida: CRC Press, 2000.
[2] JUNEGAR J M, SINGH S, BOSE D K. Investigations on the extraction of Mo and Re values from low grade molybdenite concentrate [J]. Hydrometallurgy, 1996, 41: 201-209.
[3] SHARIAT M H, SETOODEH, DEHGHAN A. Optimising conditions for hydrometallurgical production of purified molybdenum trioxide from roasted molybdenite of Sarcheshmeh [J]. Minerals Engineering, 2001, 14: 815-820.
[4] KIM B S, JHA M K, JEONG J, LEE J C. Leaching of impurities for the up-gradation of molybdenum oxide and cementation of copper by scrap iron [J]. International Journal of Mineral Processing, 2008, 88: 7-12.
[5] NAM Y I, SEO S Y, KANG Y C, KIM M J, SENANAYAKE G, TRAN T. Purification of molybdenum trioxide calcine by selective leaching of copper with HCl-NH4Cl [J]. Hydrometallurgy, 2011, 109: 9-17.
[6] WANG M, WANG X, LIU W. A novel technology of molybdenum extraction from low grade Ni-Mo ore [J]. Hydrometallurgy, 2009, 97: 126-130.
[7] LIU Y, ZHANG Y, CHEN F, ZHANG Y. The alkaline leaching of molybdenite flotation tailings associated with galena [J]. Hydrometallurgy, 2012, 129: 30-34.
[8] ROINE A. HSC Chemistry 6.0 [M]. Pori, Finlandia: OutoKumpu Research Py, 1999.
[9] SHON H Y, WADSWORTH M E. Rate processes of extractive metallurgy [M]. New York: Plenum Press, 1979.
不同温度下MoO3在KOH介质中的溶解动力学
A. ARACENA1, A. SANINO1, O. JEREZ2
1. Escuela de Ingenieria Quimica, Pontificia Universidad Catolica de Valparaiso, Avenida Brasil 2162, Cod. Postal 2362854, Valparaiso, Chile;
2. Instituto de Geologia Economica Aplicada (GEA), Universidad de Concepcion, Casilla 160-C, Concepcion, Chile
摘 要:通过改变体系的温度、KOH浓度和粒径,研究合成的MoO3在氢氧化钾(KOH)介质中的溶解动力学,考察搅拌速率和和反应剂种类(如氢氧化钡、氢氧化钙和氢氧化钠等)的影响。实验是在一个可以控制温度和搅拌速率的反应器中进行的。结果表明,钼华的溶解反应生成了钼酸钾(K2MoO4),而没有中间化合物生成。温度(6~80 °C)、KOH浓度(0.0005~0.025 mol/L)和粒径(5~40 mm)对MoO3的溶解影响显著。在温度80 °C、KOH浓度0.01 mol/L、反应时间0.25 h的条件下,钼的回收率最大,达67.5%。在接近水的冰点的最低温度(6 °C)下,反应45 min后,钼的回收率为17.8%。建立了KOH环境中MoO3溶解的动力学方程,表明扩散是通过多孔层进行的。计算得到活化能为47.81 kJ/mol,KOH 浓度的反应级数为1.0,与粒径的平方成反比,并得到了动力学方程。MoO3是辉钼矿精矿(MoS2)氧化的产物,它的溶解导致钼的回收率低,这主要是因为CaCO3和Cr(Mo4)3等杂质消耗了KOH。
关键词:MoO3溶解;动力学;氢氧化钾
(Edited by Xiang-qun LI)
Corresponding author: A. ARACENA; E-mail: alvaro.aracena@pucv.cl
DOI: 10.1016/S1003-6326(18)64651-5