
Effects of electrolyte components on properties of Al alloy anode
MA Zheng-qing(马正青), ZUO Lie(左 列), PANG Xu(庞 旭), ZENG Su-min(曾苏民)
School of Materials Science and Engineering, Central South University, Changsha 410083, China
Received 12 December 2007; accepted 11 July 2008
Abstract: The effects of Na2SnO3, In(OH)3 and Na2SnO3+In(OH)3 on the properties of Al alloy anode were studied in alkaline medium at 25 ℃. The self-corrosion rate of Al alloy anode was studied by method of H2 immersed in aqueous medium, and the electrochemical properties of Al alloy anode were tested via galvanostatic discharge and dynamic potential methods. The results show that the self-corrosion rate of Al alloy anode in 4 mol/L NaOH+3 mol/L NaAlO2 medium can be minimized by adding Na2SnO3, In(OH)3 and Na2SnO3+ In(OH)3. Na2SnO3, In(OH)3 and Na2SnO3+In(OH)3 make Al anodic potential shift positively in galvanostatic discharging. The most effective additive of Al alloy anode in 4 mol/L NaOH+3 mol/L NaAlO2 medium is 0.075 mol/L Na2SnO3+0.005 mol/L In(OH)3, integrating self-corrosion rate and electrochemical properties.
Key words: aluminum alloy anode; electrode potential; self-corrosion rate; alkaline medium
1 Introduction
Aluminum is an attractive choice for galvanic anode in primary alkaline batteries due to its attractive properties such as high specific energy and high current density in alkaline medium as well as its abundance, low cost and light mass[1-4].
The main properties of power batteries and specific capacities of anode materials are listed in Table 1. It can be seen from Table 1 that the gravimetric specific capacity of aluminum anode is just lower than that of Li, which is 2.98 A?h/g. However, its volumetric specific capacity is four times higher than that of Li, which is 8.10 A?h/cm3. And the specific energy of Al/AgO battery containing aluminum as anode is 1 090 W?h/kg, which is close to that of Li-ion battery[5].
Al anode battery can be applied in the power source of unmanned underwater vehicle(UUVs) propulsion system, such as the utilization of emergency power sources and fieldwork electrical sources. Al anode may be developed to the power sources of electrical automobile due to its merit of pollution-free[6-7]. However, the drawbacks of the Al anode such as high self-corrosion rate, gassing, and high polarization will restrict its development and application. To solve these problems and enhance the properties of Al anode, one reliable way is to incorporate different alloying elements like indium, gallium, tin and magnesium into aluminum[8-12]. The other reliable approach is to add some corrosion inhibitors and compound agents[13].
A number of corrosion inhibitors and compound agents have been developed to minimize the self-corrosion of aluminum anode in alkaline mediums. MACDONALD and ENGLISH[14] investigated the corrosion inhibition of aluminum anode by adding K2MnO4 in 4 mol/L KOH. They concluded that K2MnO4 is an effective corrosion inhibitor, particularly at high discharge rate (400 mA/cm2). But at low discharge rate, only manganate offers a significant advantage in coulombic efficiency over that of the uninhibited solution. Some organic compounds are also used as corrosion inhibitors. ZHANG and SONG[15] investigated the corrosion inhibition of aluminum anode by adding O-aminophenol in 4 mol/L KOH. Their results show that O-aminophenol decreases the absorption quantity of OH- on the surface of Al anode and the volume of hydrogen evolution. However, to our knowledge, the work taking In(OH)3 and Na2SnO3+In(OH)3 binary combination as corrosion inhibitors of aluminum anode in alkaline mediums has not yet been reported so far.
The aim of the current work is to investigate the effects of Na2SnO3, In(OH)3 and Na2SnO3+In(OH)3 compounds on the properties of aluminum anode in 4 mol/L NaOH+3 mol/L NaAlO2 medium, and to find out the most effective additive to improve the performances of Al anode applied in underwater propulsion battery system.
Table 1 Main properties of power batteries and specific capacities of anode materials
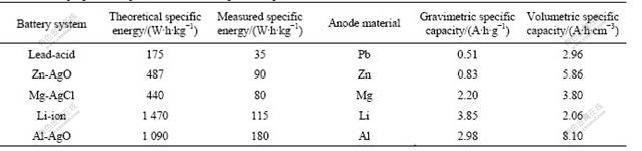
2 Experimental
2.1 Material
Al alloy anode was prepared by adding the alloying elements Ga (purity: 99.99%), Sn (purity: 99.999%) and Mg (purity: 99.99%) into the high pure aluminum solution (purity: 99.999%) (nominal composition: 0.1% Ga, 0.2% Sn, 0.8% Mg, balance Al). The high pure graphite crucible was used and the melt was cast into flat ingot in a water-cooled model. After annealing and face milling, the flat ingot Al alloy was cold-rolled into 0.5 mm-thick planar Al alloy anode materials.
All other reagents were of analytical grade and were used without further purification. Distilled water was used in all experiments.
2.2 Self-corrosion rate and electrochemical measure- ment
The self-corrosion rate of Al alloy anode was studied by methods of immersing in aqueous medium[16], while the electrochemical properties of aluminum alloy anode were tested using a Solartron SI 1287 (Solartron Analytical, UK) electrochemistry test machine. A three- electrode configuration was employed. Aluminum alloy anode was used as a working electrode, Hg/HgO (1 mol/L NaOH) was applied as a reference electrode and graphite (S=4.0 cm2) was served as an auxiliary electrode. The area of working electrode was 10 mm×10 mm. All potentials were reported with respect to the reference electrode. The galvanostatic discharge was measured for 300 s (current density: 50 mA/cm2) and dynamic potential measurement was performed from -2.0 V to -1.5 V. Both of self-corrosion studies and electrochemical property tests of Al alloy anode were carried out at 25 ℃.
2.3 Surface analysis
The micrographs of the surface of Al anode reacted in alkaline media with or without additives were examined using Sirion200(FEI.,USA) Field Emission SEM coupled with GENESIS 60E EDS (EDAX Inc.,USA).
3 Results and discussion
3.1 Effects of additives on self-corrosion rate of Al alloy anode in alkaline medium
The self-corrosion rate of Al anode in different media is shown in Fig.1. Fig.1(a) shows that the self-corrosion rate of Al alloy anode decreases when the concentration of Na2SnO3 increases. But it tends to be a constant of 0.09 mL/(cm2·min) when the concentration of Na2SnO3 is up to 0.05 mol/L. In Fig.1(b), the self- corrosion rate of Al alloy anode treated by 4 mol/L NaOH+3 mol/L NaAlO2 without In(OH)3 is 0.21 mL/(cm2·min), which is much faster than that of Al alloy anode treated by 4 mol/L NaOH+3 mol/L NaAlO2+In(OH)3 medium. Furthermore, the self- corrosion rate retains at about 0.03 mL/(cm2·min) when the concentration of In(OH)3 is up to 0.003 mol/L.
The self-corrosion rate of Al alloy anode in 4 mol/L NaOH+3 mol/L NaAlO2 together with the 0.005 mol/L In(OH)3+x mol/L Na2SnO3 compound is shown in Fig.1(c). The self-corrosion rate retains at about 0.03 mL/(cm2·min) in 4 mol/L NaOH+3 mol/L NaAlO2 added with a mixture of 0.005 mol/L In(OH)3+x mol/L Na2SnO3. This obviously indicates that the increasing concentration of Na2SnO3 has almost no effect on the self-corrosion rate.
Fig.1(d) gives the self-corrosion rate of the Al alloy anode in 4 mol/L NaOH+3 mol/L NaAlO2 added with 0.075 mol/L Na2SnO3+y mol/L In(OH)3 compound. It can be seen from Fig.1(d) that the self-corrosion rate of the Al alloy anode almost sustains at about 0.03 mL/(cm2·min) when the concentration of In(OH)3 is higher than 0.003 mol/L, which is much less than that of the Al alloy anode in 4 mol/L NaOH+3 mol/L NaAlO2 added with 0.075 mol/L Na2SnO3.
3.2 Effects of additives on electrochemical properties of Al alloy anode in alkaline medium
Fig.2(a) and 2(b) show the Tafel and galvanostatic discharge curves of the Al alloy anode treated by different alkaline media, respectively. The corresponding self-corrosion potential(φcorr) and corrosion current density(Jcorr) are listed in Table 2. As shown in Fig.2(a) and Table 2, the corrosion potentials of Al alloy anode treated by different alkaline media, which are labeled as 2, 3 and 4, is -1.70, -1.69 and -1.63 V, respectively. Compared with that in medium labeled number 1, the self-corrosion potential has shifted positive notably. In Table 3, the corrosion current densities of Al alloy anode in number 2, 3 and 4 are 2.903, 6.21 and 0.735 mA/cm2, respectively, which reduce very much than those of Al alloy anode in number 1 (Jcorr=58.203 mA/cm2) medium. The experimental results reveal that the self-corrosion potential of Al alloy anode notably shifts positively, the corrosion current density of Al alloy anode reduces sharply and self-corrosion decreases while anodic efficiency increases when Na2SnO3, In(OH)3 and Na2SnO3+ In(OH)3 compound are added to alkaline medium.
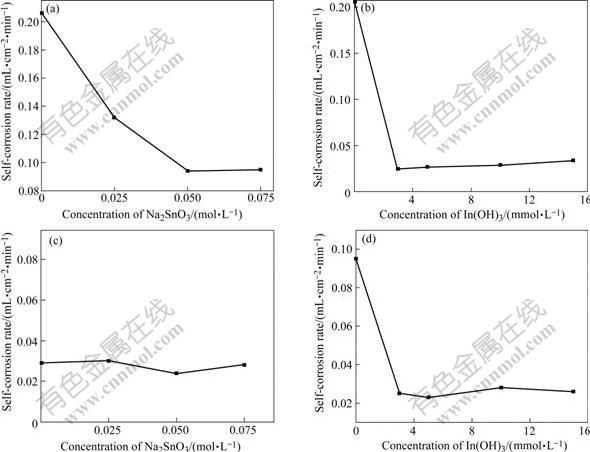
Fig.1 Self-corrosion rate of Al anode in different alkaline mediums at 25 ℃: (a) 4 mol/L NaOH+3 mol/L NaAlO2+Na2SnO3; (b) 4 mol/L NaOH+3 mol/L NaAlO2+ In(OH)3; (c) 4 mol/L NaOH+3 mol/L NaAlO2+ 0.005 mol/L In(OH)3+x mol/L Na2SnO3; (d) 4 mol/L NaOH+3 mol/L NaAlO2+0.075 mol/L Na2SnO3+y mol/L In(OH)3
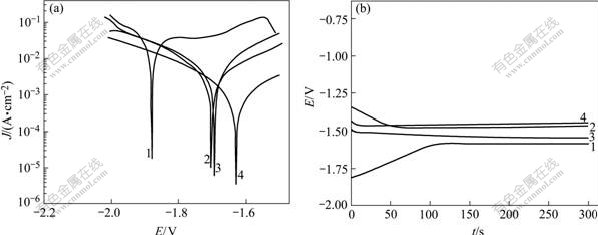
Fig.2 Tafal (a) and galvanostatic (b) curves for Al anode in different media at 25 ℃: 1—4 mol/L NaOH+3 mol/L NaAlO2; 2—4 mol/L NaOH+3 mol/L NaAlO2+0.075 mol/L Na2SnO3+0.005 mol/L In(OH)3; 3—4 mol/L NaOH+3 mol/L NaAlO2 +0.075 mol/L Na2SnO3; 4—4 mol/L NaOH+3 mol/L NaAlO2 +0.005 mol/L In(OH)3
Table 2 φcorr and Jcorr of Al anode in different media
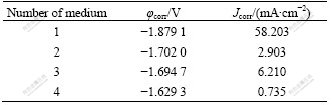
In Fig.2(b), the steady galvanostatic polarization potentials (current density: 50 mA/cm2) of Al alloy anode in medium 1, 2, 3 and 4 are -1.59, -1.495, -1.53 and -1.48 V, respectively. Compared with the Al alloy anode treated in medium 1, the potential of Al alloy anode treated in the latter is positively shifted to 0.095, 0.06 and 0.11 V, respectively. This obviously indicates that in galvanostatic polarization, Na2SnO3, In(OH)3 and Na2SnO3+In(OH)3 compound can make the Al anodic potential shift positively in alkaline medium. Compared with the curves shown in Fig.2(b), the voltage delay phenomenon can be improved by adding Na2SnO3, In(OH)3 and Na2SnO3+ In(OH)3 compound into alkaline medium.
3.3 SEM and EDS of surface of Al anode reacted in alkaline medium
Fig.3 exhibits the image of uniform surface corrosion without pitting and intercrystalline corrosion of Al alloy anode surface in 4 mol/L NaOH + 3 mol/L NaAlO2. Figs.4, 5 and 6 show the SEM and EDS results of corroded Al anode surface in 4 mol/L NaOH+3 mol/L NaAlO2 added with Na2SnO3, In(OH)3 and Na2SnO3+In(OH)3, respectively. Fig.4 indicates that Al alloy anode in 4 mol/L NaOH+3 mol/L NaAlO2+Na2SnO3 medium forms a uniform, porous and adherent tin coating on its surface. Fig.5 reveals that the Al alloy anode treated by 4 mol/L NaOH+3 mol/L NaAlO2+In(OH)3 medium, forms an irregular granular and adherent indium coating on its surface. As shown in Fig.6, the surface of Al alloy anode is coated by a porous and adherent tin layer or by an irregular granular indium layer.
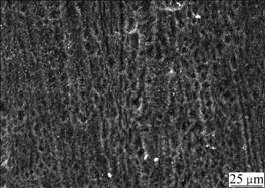
Fig.3 SEM image of surface of Al anode reacted in 4 mol/L NaOH+3 mol/L NaAlO2 at 25 ℃
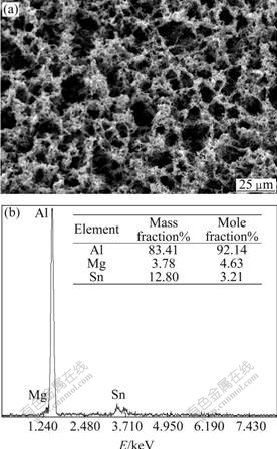
Fig.4 SEM image and EDS pattern of surface of Al anode reacted in 4 mol/L NaOH+3 mol/L NaAlO2+Na2SnO3 at 25 ℃
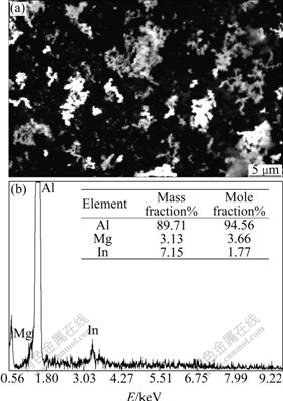
Fig.5 SEM image and EDS pattern of surface of Al anode reacted in 4 mol/L NaOH+3 mol/L NaAlO2+In(OH)3 at 25 ℃
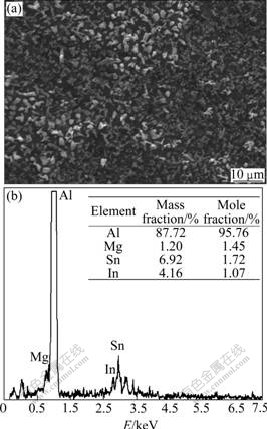
Fig.6 SEM image and EDS pattern of surface of Al anode reacted in 4 mol/L NaOH+3 mol/L NaAlO2+Na2SnO3+In(OH)3 at 25 ℃
3.4 Discussion
As mentioned above, Na2SnO3, In(OH)3 and Na2SnO3+In(OH)3 could be respectively deoxidized to elemental Sn, In and Sn+In (Eqs.(3) and (4)) by aluminum substrate or alloying elements on its surface in alkaline medium (see Figs.4, 5 and 6):
InO2-+2H2O+6e→In+4OH- (
=0.146 V) (3)
SnO32-+2H2O+6e→Sn+4OH- (
=-1.750 V) (4)
These chemical reactions not only destroy the denseness of aluminum oxide membranes, which makes Al alloy anode discharge well at high negative potential, but also reduce the self-corrosion of Al alloy anode. The electrode kinetics parameters of Sn and In in Table 3 indicate that both of them are high hydrogen evolution over-potential elements.
According to the Tafel’s law, η=a+blogJ, where η is the hydrogen evolution overpotential, a and b are two Tafel constants, and J represents the current density. Hence, η is the function of the Tafel constants when the current density J is a constant[17]. Hence, the elemental Sn and In scattering on the surface of Al alloy anode can raise the hydrogen evolution over-potential and reduce the reaction area of Al substrate, which makes the potential of Al alloy anode shift positively, increases the cathodic polarization of electrochemical corrosion, restrains the depolarization reaction (2H++2e→H2), reduces the self-corrosion rate and enhances the anodic current efficiency of the Al alloy anode.
Table 3 Electrode kinetics parameters[18]
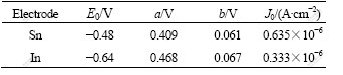
Both of cathodic and anodic current densities in 4 mol/L NaOH +3 mol/L NaAlO2 solution with Na2SnO3, In(OH)3 and Na2SnO3+In(OH)3 are much lower than those in 4 mol/L NaOH+3 mol/L NaAlO2 solution. Firstly, the oxygen reduction and alloy substrate dissolution process are limited by Na2SnO3, In(OH)3 and Na2SnO3+In(OH)3, which shows they can act as a mixed type inhibitor to inhibit the corrosion of aluminum alloy anode by blocking the active sites of the metal surface[19]. Secondly, the existence of Na2SnO3, In(OH)3 and Na2SnO3+In(OH)3 can accelerate the activation of Al alloy anode in 4 mol/L NaOH+3 mol/L NaAlO2 solution. Lastly, along with the deposition of elemental Sn and In on surface of Al anode, the galvanostatic discharging potential and self-corrosion potential of Al anode shift positively.
4 Conclusions
1) Adding Na2SnO3, In(OH)3 and Na2SnO3+ In(OH)3 mixture into alkaline medium can form coated layers on Al surface due to the deoxidation reaction of the compounds. The coatings of Sn and In can reduce the self-corrosion rate and enhance the anodic current efficiency of the Al alloy anode.
2) When adding Na2SnO3, In(OH)3 and Na2SnO3+ In(OH)3 compound in alkaline medium, the self- corrosion potential of Al alloy anode shifts positively; the corrosion current of Al alloy anode will be greatly reduced; and the voltage delay phenomenon of Al alloy anode can be improved. In galvanostatic discharging, Al anodic potential shifts positively in the alkaline medium.
3) Among three additives of Na2SnO3, In(OH)3 and Na2SnO3+In(OH)3, the most effective additive of Al alloy anode in 4 mol/L NaOH+3 mol/L NaAlO2 medium is 0.075 mol/L Na2SnO3+0.005 mol/L In(OH)3, integrating self-corrosion rate and electrochemical properties.
References
[1] ANDREY Z Z, ALEXANDER E S, BORIS V K, EUGENE I S, MARAT Y L. Use of low-cost aluminum in electric energy production [J]. Journal of Power Sources, 2006, 157: 921-926.
[2] ANDERSON G E, MIDDLETOWN R I. Al-AgO primary battery: US3953239 [P]. 1976.
[3] WANG Zhen-wen, LI Yan-xiang. Advances in development and application of aluminum anode materials [J]. Nonferrous Metals, 2002, 54(1): 1-2. (in Chinese)
[4] SHU Fang-xia, WANG Zhen-wen, GAO Bing-liang. Research progress in Al alloy anodes for alkaline Al/air battery [J]. Battery Bimonthly, 2005, 35(2): 158-159. (in Chinese)
[5] LI Qing-feng, BJERRUM N J. Aluminum as anode for energy storage and conversion: A review [J]. Journal of Power Sources, 2002, 110: 1-10.
[6] ?ISTEIN HASVOLD, NILS J. ST?RKERSEN. Electrochemical power sources for unmanned underwater vehicles used in deep sea survaer operations [J]. Journal of Power Sources, 2001(96): 252-258.
[7] YANG Shao-hua, KNICKLE H. Design and analysis of aluminum/air battery system for electric vehicles [J]. Journal of Power Sources, 2002, 17: 162-173.
[8] THOMPSON D S, SCOTT D H. Aluminum battery alloys: US4554131 [P]. 1985.
[9] TARCY G P, PITTSBURGH P. Aluminum alloy and anode and battery: US4950560 [P]. 1990.
[10] MODEN J R, PERKONS G. Aluminum anode alloy for primary high power density alkaline fuel cells and batteries: US4150204 [P]. 1979.
[11] HUNTER J A. Aluminium batteries: US5032474 [P]. 1991.
[12] MA Zheng-qing, ZENG Su-min, LI Wen-xian. Study on electrochemical performance of aluminum alloys anode materials [J]. Surface Technology, 2005, 34(1): 25-26. (in Chinese)
[13] PARAMASIVAM M, JAYACHANDRAN M, VENKATAKRISHNA I S. Influence of alloying additives on the performance of commercial grade aluminum as galvanic anode in alkaline zincate solution for use in primary alkaline batteries [J]. Journal of Applied Electrochemical, 2003, 33: 303-309.
[14] MACDONALD D D, ENGLISH C. Development of anodes for aluminium/air batteries-solution phase inhibition of corrosion [J]. Journal of Applied Electrochemistry, 1990, 20: 405-417.
[15] ZHANG Yan, SONG Yu-su. Inhibiting H2-evolution for O-aminophenolon in the system of Al-Ga-Sn-Mg/KOH [J]. Journal of Chinese Society for Corrosion and Protection, 2005, 25(6): 369-373. (in Chinese)
[16] MA Zheng-qing, LI Wen-xian, XIAO Yu-de, YU Kun. Microstructure and electrochemistry properties of new aluminum alloy anodes [J]. Materials Protection, 2002, 26(5): 365-368. (in Chinese)
[17] CAO Chu-nan. Electrochemical corrosion [M]. Beijing: Chemical Industry Press, 2004: 45-68. (in Chinese)
[18] LI Jun-hua, FEI Xi-ming, XIANG Cui-li. Electrochemical properties of copper electrode coated with Sn-In alloy electrochemical plating in KOH solution [J]. Materials Protection, 2005, 38(12): 8-10. (in Chinese)
[19] LI Song-mei, ZHANG Hong-rui, LIU Jian-hua. Corrosion behavior of aluminum alloy 2024-T3 by 8-hydroxy-quinoline and its derivative in 3.5% chloride solution [J]. The Chinese Journal of Nonferrous Metals, 2007, 17(2): 318-325. (in Chinese)
Corresponding author: MA Zheng-qing, Tel: +86-731-8876010; E-mail: alanode@163.com
DOI: 10.1016/S1003-6326(08)60245-9
(Edited by LI Xiang-qun)