Trans. Nonferrous Met. Soc. China 26(2016) 2561-2566
Effect of Mg on nucleation process of recrystallization in Al-Mg-Si/SiCp composite
Bin LI1, Bing-hui LUO1, Ke-jian HE2, Wen-li FAN1
1. School of Materials science and Engineering, Central South University, Changsha 410083, China;
2. Advanced Research Centre, Central South University, Changsha 410083, China
Received 11 May 2015; accepted 28 August 2016
Abstract: The recrystallization nucleation processes of two cold-rolled Al-Mg-Si/SiCp composites with different contents of Mg are investigated mainly by dynamic mechanical analyzer (DMA) and electron microscopy including high angle annular dark field scanning transmission electron microscopy (HAADF-STEM) and high-resolution transmission electron microscopy (HRTEM). Internal friction and electron microscopy results show that solute atom clusters are present in association with dislocations in supersaturated cold-rolled composites. During recrystallization process, the internal friction peak position of Al-Mg-Si/3SiCp/2Mg (volume fraction, %) is higher than that of Al-Mg-Si/3SiCp (volume fraction, %) due to more solute atom clusters formed in association with the dislocations in the cold-rolled composite with a much higher Mg content, indicating a stronger resistance for the recrystallization nucleation.
Key words: aluminum matrix composites; recrystallization; internal friction; dislocation; microstructures;transmission electron microscopy;
1 Introduction
Al-Mg-Si alloys (6000 series) have received considerable attention for automotive and aerospace applications on account of their low density with good mechanical properties [1,2]. Furthermore, the addition of SiC reinforcement phase can raise the performance limits of Al-Mg-Si alloys. Aluminum matrix composites (AMCs) are designed to have the required toughness of alloy matrix along with the desired hardness, stiffness and strength of hard ceramic reinforcements [3,4]. The purpose of Mg addition is manifold, because it can promote the formation of spinel (MgAl2O4) or MgO at the oxidized SiCp/Al interface, as well as enhance the wetting behavior of the SiC particles with the matrix [5]. The bonding strength between MgAl2O4 and Al is higher than that between Al4C3 and Al [6,7]. According to some researches [8,9], it is found that the main reaction product is MgAl2O4 for AMCs with a Mg content less than 4% while it is MgO for AMCs with a Mg concentration higher than 4%. In previous studies [10], we found that a MgAl2O4 phase becomes the main reaction product at the SiCp/Al interface and the bonding strength of SiCp/Al interface is improved in Al-Mg-Si/ 3SiCp/2Mg (volume fraction, %) composite. A significant amount of works have been made in studying the effect of Mg at the SiCp/Al interface in AMCs, but much less has been done in researching the effect on the recrystallization process of AMCs.
The aluminum alloys may exhibit complex behavior of recrystallization and precipitation,especially when recrystallization of a deformed supersaturated solid solution is not completed and precipitation is still ongoing. There is a strong interest in the recrystallization-precipitation interaction in aluminum alloys in order to optimize their properties [11,12]. Great efforts have been made in studying the recrystallization- precipitation interaction mechanisms and microstructural evolutions in the deformed and annealed aluminum alloys so far [13-15], but much less has been done in AMCs, especially at the early-stage of recrystallization- precipitation interaction.
Compared with other techniques such as the hardness measurement, the internal friction technique can well detect the microstructural evolution taking place in high resolution [16-20]. In our research, internal friction technology is applied as a new characterization method to research the nucleation process of recrystallization and the interactions between solute atom clusters and dislocations. The aim of the present work is to investigate the effect of Mg addition on the recrystallization nucleation in the cold-rolled Al-Mg-Si/3SiCp (volume fraction, %) composites using internal friction and electron microscopy.
2 Experimental
The Al-Mg-Si/3SiCp and Al-Mg-Si/3SiCp/2Mg composites were produced by powder metallurgy technique. The chemical composition of the metal matrix was Al-1.3Mg-1.1Si-0.7Cu (mass fraction, %). The samples were hot-rolled at 450 °C to a plate of 4 mm in thickness, solution treated at 520 °C for 2 h and quenched into water at room temperature. Then, the sheets were cold-rolled along the hot-rolled direction to a thickness of 2 mm with a total reduction of 50%.
STEM and HRTEM were conducted using a Titan G2 60-300 TEM with an image corrector and a Super-X detector operated at 300 kV. The specimens for microscopy were prepared by mechanically grinding, polishing, dimpling and finally ion-milling using a Gatan PIPS 691.
Both measurements of temperature dependent internal friction (TDIF) and strain amplitude dependent internal friction (ADIF) were carried out with a dynamic mechanical analyzer (DMA) Q800 Ta instrument in a dual cantilever mode. The specimens for internal friction test were cut off to sizes of 35 mm × 2 mm × 10 mm. The TDIF measurements were carried out at a strain amplitude 2×10-6,in a temperature range between room temperature and 400 °C at the frequencies of 0.5, 1 and 3 Hz, respectively. The rate used for both the heating and the cooling was 2 K/min. The ADIF measurements were carried out at strain amplitude between 1×10-6 and 1×10-3 with a frequency of 1 Hz.
3 Results and discussion
3.1 microstructures
Figure 1 shows the precipitates of the two cold-rolled supersaturated composites after annealing at 200 °C for 3 h. As for Al-Mg-Si alloys, the complex decomposition sequence in metal matrix is generally considered to be as follows [21,22]: super-saturated solid solution (SSSS)→clusters/co-cluster of Mg and Si→Guinier-Preston (GP) zones→β″→β′→Q′→β+Q. The nucleation, growth and coarsening rates of Mg2Si precipitates are largely dependent on the element Mg [23]. As seen from the micrographs in Figs. 1(a) and (b), the addition of Mg can also promote the precipitation of spherical phase and improve its dispersive distribution in cold-work supersaturated composites after annealing treatment. To investigate the dislocation evolution during heating, internal friction technique was employed in the following experiment.
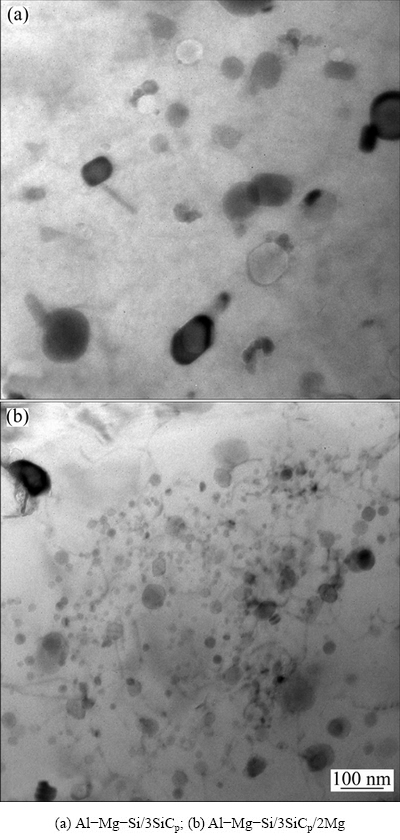
Fig. 1 TEM BF images of phase present in cold-rolled supersaturated composites after annealing treatment at 200 °C for 3 h
3.2 TDIF measurements
Figure 2 shows the internal friction curves upon heating and cooling for the two cold-rolled supersaturated composites. Because the recrystallization nucleation is formed by the movement of dislocation, the increase or decrease of internal friction value Q-1 could be interpreted as an increase or decrease in the dislocation motion for recrystallization nucleation. The internal friction peak appeared during heating can be denoted as PR (recrystallization) peak, and PR peak disappears at cooling or second heating because the irreversible transition of recrystallization nucleation. The PR peak can be clearly observed at a starting point about 100 °C (Fig. 2(a)) upon heating, implying that the dislocation motion of recrystallization is activated at about 100 °C in Al-Mg-Si/SiCp, while the PR peak can be clearly seen at a starting point about 200 °C in Al-Mg-Si/SiCp/2Mg (Fig. 2(b)) upon heating, indicating that dislocation motion is activated at about 200 °C in Al-Mg-Si/SiCp/2Mg. The dislocation motion of Al-Mg-Si/SiCp/2Mg is more difficult to be activated with a higher content of Mg.
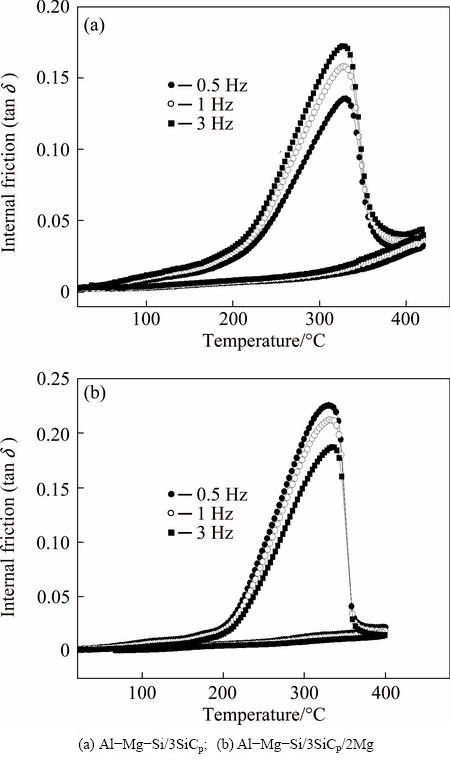
Fig. 2 Temperature dependent internal friction measurements for cold-rolled supersaturated composites
The PR peak position of Al-Mg-Si/3SiCp/2Mg (see Fig. 2(b)) is about 3.8 °C higher than that of Al-Mg-Si/ 3SiCp (see Fig. 2(a)), which indicates that the recrystallization nucleation process becomes harder due to the effect of Mg addition. As the recrystallization nucleation is completed and the newly formed grains grow up, the PR peak decreases sharply due to the reduction of dislocation density [9].
The PR peaks of both composites occur in the temperature range 100-350 °C in which the precipitates will precipitate and would not be dissolved [24]. Hence, these precipitates will have an effect of pinning the dislocation movement and thus impeding recrystallization nucleation throughout the entire process of recrystallization nucleation. In this way, the dislocation motion could be deeply modified by precipitation [25].
3.3 ADIF measurements
As seen from the ADIF curves in Fig. 3, the slopes of the lower amplitude strain part in both Figs. 3(a) and (b) are almost approaching zero and they are not related to the amplitude strain, which is because the dislocation relaxation is restricted under low strain. In previous
research [26], the solute Si atoms have a strong interaction with the dislocations and thus act as hard pining points where the dislocations cannot break away under low strain. The solute Mg atoms act as weak pinning points where the dislocations can break away under low strain, but the dislocations unpinned away from some Mg atoms are pinned down immediately by other Mg atoms concentrated around the dislocations.
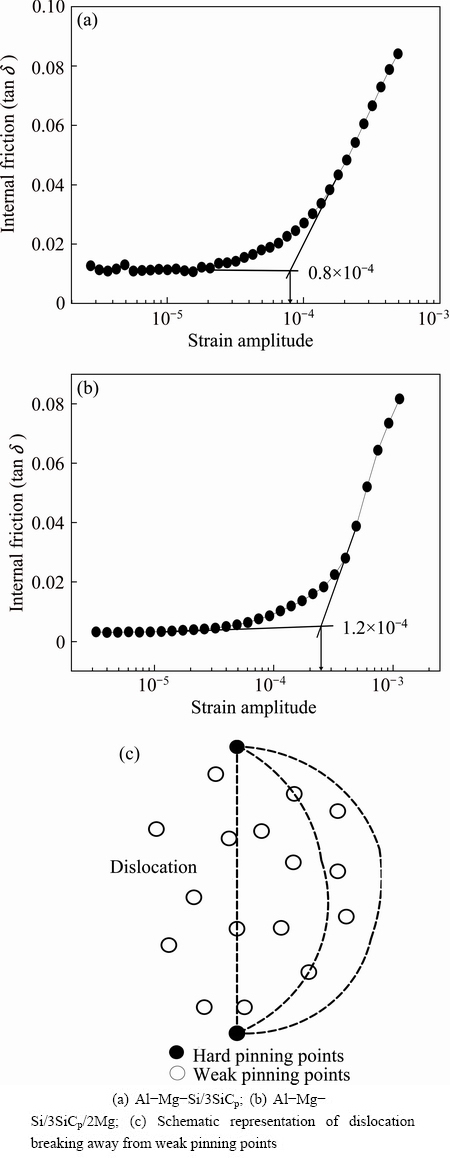
Fig. 3 ADIF measurements at room temperature for cold-rolled supersaturated composites
The well-defined critical amplitude εcr corresponds to the dislocation unpinning from the pinning points under high strain [24,26-28]. In Figs. 3(a) and (b), the critical amplitude is the cross point of two lines which are obtained by fitting two different slopes of ADIF curves using least squares principle. The process of dislocations breaking from solute atom clusters is illustrated in Fig. 3(c).
According to the equation in Ref. [17]: εcr∝
, where
is the average length between pinning points which pin a dislocation. The more the solute atoms interacting with dislocation, the higher the value of εcr needed for dislocation to unpinning from pinning, due to the reduction of the weak pinning point distance
. The εcr of Al-Mg-Si/3SiCp/2Mg is 1.2×10-4 in contrast to 0.8×10-4 of Al-Mg-Si/3SiCp, which is a 50% increase. This substantial increase of εcr reveals that more amount of solute atom clusters associated with dislocations make a greater obstruction effect on the dislocation motion due to the addition Mg.
3.4 HRTEM and HADDF-STEM characterizations
To confirm the validity of cluster-dislocation associations in 50% cold-work supersaturated composites, HRTEM and HADDF-STEM characteriza- tions have been conducted and the results are further analyzed by the Fourier masking method. Figure 4(a) indicates the dislocation pile ups in the Al matrix close to the SiCp/Al interfaces due to the obstruction effect of SiC particles on the dislocation motion during cold work. These dislocations are aligning along the SiCp/Al interface. As shown in Figs. 4(b) and (c), the elongated clusters appear after cold work, with a length of about 5 nm and a width of about 2 nm. The slight lattice distortions in Figs. 4(b) and (c) are due to the segregation of solute atoms, because no second phase diffraction can be observed in fast Fourier transformation (FFT) but only the lattice structure of Al matrix, implying that some of Al atoms are replaced by solute atoms. The inserted FFT patterns of these clusters also reveal some diffraction streaks on the Al-rich matrix reflections in a direction perpendicular to their elongated orientations. This is an indication that the lattice parameter of cluster deviates slightly from that of Al-rich matrix linked to the compositional deviation from the average matrix composition. The inverse fast Fourier transformation (iFFT) images of both HRTEM and HADDF-STEM reveal that the clusters are indeed surrounded by dislocations, which is in good agreement with the results of ADIF measurements.
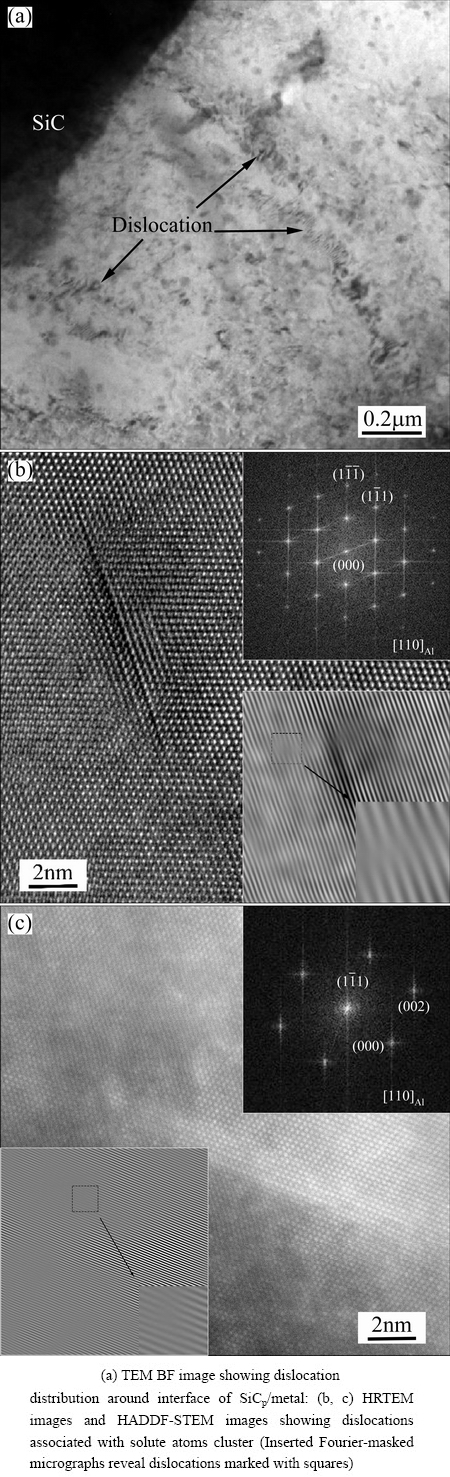
Fig. 4 TEM micrographs of cold-rolled supersaturated Al-Mg-Si/3SiCp/2Mg
The early-stage precipitation in Al-Mg-Si alloys was simulated by FALLAH et al [29], in which the Si-rich clusters appeared in the supersaturated matrix, some of Si-rich clusters then attracted a higher proportion of Mg and became Mg-rich clusters. The dislocations in a supersaturated solid solution could effectively reduce the energy of precipitation nucleation [30,31]. Our results also indicate that the solute atoms Mg and Si prefer to concentrate in and around the line defects such as dislocations. With a much higher content of Mg, the εcr value of the Al-Mg-Si/ 3SiCp/2Mg composite is substantially increased (Figs. 3(a) and (b)), indicating that more Mg-Si atom clusters are formed. More Mg-Si atom clusters make a greater obstruction effect on the dislocation motion by pinning dislocations during recrystallization.
During heating, the precipitates based on the Mg-Si atom clusters are nucleated and then coarsened [29]. That more Mg-Si atom clusters in Al-Mg-Si/3SiCp/ 2Mg result in that more precipitates evolved from these clusters are formed with a more dispersive and homogenous distribution (Figs. 1(a) and (b)). Some researchers have reported that precipitates could strongly affect recrystallization behavior, severely inhibit the recrystallization [32,33]. Therefore, the motion of dislocations in Mg-added composite should become more difficult due to the greater precipitate pining effect on dislocations.
On the whole, the recrystallization nucleation of Al-Mg-Si/3SiCp/2Mg (see Fig. 2(b)) is harder to proceed than that of Al-Mg-Si/3SiCp (see Fig. 2(a)), due to a more effective effect in pinning the motion of dislocations by a larger number of Mg-Si solute atoms and precipitates,
4 Conclusions
1) Mg-Si atom clusters are found associated with dislocations in supersaturated composites after cold work.
2) With a much higher content of Mg, more Mg-Si atom clusters are formed due to the substantial increase of εcr value of the Al-Mg-Si/3SiCp/2Mg composite after cold work.
3) The recrystallization nucleation of Al-Mg-Si/ 3SiCp/2Mg is harder to proceed than that of Al-Mg-Si/ 3SiCp/2Mg because a more effective effect in pinning the motion of dislocations by a larger number of Mg-Si solute atoms and precipitates.
References
[1] Miller W S, Zhuang L, Bottema J, Wittebrood A J, Smet P D, Haszler A, Vieregge A. Recent development in aluminium alloys for the automotive industry [J]. Materials Science and Engineering A, 2000, 280: 37-49.
[2] WILLIAMS J C, STARKE E A. Progress in structural materials for aerospace systems [J]. Acta Materialia, 2003, 51: 5775-5799.
[3] MAZAHERY A, SHABANI M O. Microstructural and abrasive wear properties of SiC reinforced aluminum-based composite produced by compocasting [J]. Transactions of Nonferrous Metals Society of China, 2013, 23: 1905-1914.
[4] KHOSRAVI H, AKHLAGHI F. Comparison of microstructure and wear resistance of A356-SiCp composites processed via compocasting and vibrating cooling slope [J]. Transactions of Nonferrous Metals Society of China, 2015, 25: 2490-2498.
[5] PECH-CANUL M I, KATZ R N, MAKHLOUF M M. Optimum conditions for pressureless infiltration of SiCp preforms by aluminum alloys [J]. Journal of Materials Processing Technology, 2000, 108: 68-77.
[6] LEE J C, LEE H I, AHN J P, SHI Z L, KIM Y. Modification of the interface in SiC/Al composites [J]. Metallurgical and Materials Transactions A, 2000, 31: 2361-2368.
[7] KIM Y, LEE J C. Processing and interfacial bonding strength of 2014 Al matrix composites reinforced with oxidized SiC particles [J] Materials Science and Engineering A, 2006, 420: 8-12.
[8] LEVI C G, ABBASCHIAN G J, MEHRABIAN R. Interface interactions during fabrication of aluminum alloy–alumina fiber composites [J]. Metallurgical Transactions A, 1978, 9: 697-711.
[9] PAI B C, RAY S. Fabrication of aluminium–alumina (magnesia) particulate composites in foundries using magnesium additions to the melts [J]. Materials Science and Engineering, 1976, 24: 31-44.
[10] LI Bin, LUO Bing-hui, HE Ke-jian, ZENG Li-zhou, FAN Wen-li, BAI Zhen-hai. Effect of aging on interface characteristics of Al-Mg-Si/SiC composites [J]. Journal of Alloys and Compounds, 2015, 649: 495-499.
[11] LEE Y S, KIM W K, JO D A, LIM C Y, KIM H W. Recrystallization behavior of cold rolled Al-Zn-Mg-Cu fabricated by twin roll casting [J]. Transactions of Nonferrous Metals Society of China, 2014, 24: 2226-2231.
[12] RAMESH C S, KESHAVAMURTHY R, KOPPAD P G, KASHYAP K T. Role of particle stimulated nucleation in recrystallization of hot extruded Al6061/SiCp composites [J]. Transactions of Nonferrous Metals Society of China, 2013, 23: 53-58.
[13] YANG W, YAN D S, RONG L J. The separation of recrystallization and precipitation processes in a cold-rolled Al-Mg-Sc solid solution [J]. Scripta Materialia, 2013, 68: 587-590.
[14] LI H Y, GAO Z H, YIN H, JIANG H F, SU X J, BIN J. Effects of Er and Zr additions on precipitation and recrystallization of pure aluminum [J]. Scripta Materialia, 2013, 68: 59-62.
[15]
C, MOHLES V, GOTTSTEIN G. Modeling of non-isothermal annealing: Interaction of recrystallization, recovery, and precipitation [J]. Acta Materialia, 2011, 59: 6574-6587.
[16] BLANTER M S, GOLOVIN I S,
H, SINNING H R. Internal Friction in Metallic Materials [M]. 1st ed. Berlin: Springer, 2007.
[17] SCHALLER R, FANTOZZI G, GREMAUD G. Mechanical spectroscopy Q-1 2001 with applications to materials science [M]. 1st ed. Switzerland: Trans Tech Publications, 2001.
[18] KEJIAN H, HENDRY A. The early stages of the precipitation sequence in nitride dilute Fe-Ti alloys [J]. Philosophical Magazine A, 1992, 66: 797-810.
[19] ZHOU Hai, WANG Jing-feng, PAN Fu-sheng, XU Dan-dan, TANG Ai-tao, LIANG Hao. Influence of rolling on internal friction peak of Mg-3Cu-1Mn alloy [J]. Transactions of Nonferrous Metals Society of China, 2013, 23: 1610-1616.
[20] LIU Shu-wei, JIANG Hai-chang, LI Xiu-yan, RONG Li-jian. Effect of precipitation on internal friction of AZ91 magnesium alloy [J]. Transactions of Nonferrous Metals Society of China, 2010, 20: 453-457.
[21] BUHA J, LUMLEY R N, CROSKY A G, HONO K. Secondary precipitation in an Al-Mg-Si-Cu alloy [J]. Acta Materialia, 2007, 55: 3015-3024.
[22] CHAKRABARTI D J, LAUGHLIN D E. Phase relations and precipitation in Al-Mg-Si alloys with Cu additions [J]. Progress in Materials Science, 2004, 49: 389-410.
[23] HASS M D, HOSSON J T. Grain boundary segregation and precipitation in aluminium alloys [J]. Scripta Materialia, 2001, 44: 281-286.
[24]
E, SEIFEDDINE S. Artificial ageing of Al-Si-Cu-Mg casting alloys [J]. Materials Science and Engineering A, 2011, 528: 7402-7409.
[25] YANG Wen, YAN De-sheng, RONG Li-jian. The separation of recrystallization and precipitation processes in a cold-rolled Al-Mg-Sc solid solution [J]. Scripta Materialia, 2013, 68: 587-590.
[26] GOLOVIN I S, MIKHAYLOVSKAYA A V, SINNING H R. Role of the β-phase in grain boundary and dislocation anelasticity in binary Al-Mg alloys [J]. Journal of Alloys and Compounds, 2013, 577: 622-632.
[27] GRANATO A,
K. Temperature dependence of amplitude- dependent dislocation damping [J]. Journal of Applied Physics, 2011, 52: 7136-7142.
[28] GAVRILJUK V G, SHIVANYUKA V N, SHANINA B D. Change in the electron structure caused by C, N and H atoms in iron and its effect on their interaction with dislocations [J]. Acta Materialia, 2005, 53: 5017-5024.
[29] FALLAH V, KORINEK A, OFORI-OPOKU N, RAEISINIA B, GALLERNEAULT M, PROVATASAND N, ESMAEILI S. Atomic-scale pathway of early-stage precipitation in Al-Mg-Si alloys [J]. Acta Materialia, 2015, 82: 457-467.
[30] FALLAH V, KORINEK A, OFORI-OPOKU N, PROVATAS N, ESMAEILI S. Atomistic investigation of clustering phenomenon in the Al-Cu system: Three-dimensional phase-field crystal simulation and HRTEM/HRSTEM characterization [J]. Acta Materialia, 2013, 61: 6372-6386.
[31] FALLAH V, OFORI-OPOKU N, STOLLE J, PROVATAS N, ESMAEILI S. Simulation of early-stage clustering in ternary metal alloys using the phase-field crystal method [J]. Acta Materialia, 2013, 61: 3653-3666.
[32] LIU W C, RADHAKRISHNAN B. Recrystallization behavior of a supersaturated Al-Mn alloy [J]. Materials Letters, 2010, 64: 1829-1832.
[33] WANG Ying, PAN Qing-lin, SONG Yan-fang, LI Chen, LI Zhi-feng, CHEN Qin, YIN Zhi-min. Recrystallization of Al-5.8Mg-Mn-Sc- Zr alloy [J]. Transactions of Nonferrous Metals Society of China, 2013, 23: 3235-3241.
Mg元素对Al-Mg-Si/SiCp复合材料再结晶形核过程的影响
李 彬1,罗兵辉1,何克坚2,范文丽1
1. 中南大学 材料科学与工程学院,长沙 410083;
2. 中南大学 高等研究中心,长沙 410083
摘 要:通过内耗、高角环形暗场像扫描透射电子显微镜(HADDF-STEM)和高分辨透射电子显微镜(HRTEM)等技术手段,研究两种不同Mg含量的冷变形Al-Mg-Si/SiCp复合材料的再结晶形核过程。实验结果表明,固溶态冷变形Al-Mg-Si/SiCp复合材料中溶质原子与位错相联,形成溶质原子气团。在再结晶过程中,Mg含量较高的复合材料中与位错相联的溶质原子气团的数量更多,对复合材料再结晶形核过程有更大的阻碍作用,因而Al-Mg-Si/3SiCp/2Mg复合材料的再结晶内耗峰峰温高于Al-Mg-Si/3SiCp复合材料的再结晶内耗峰峰温。
关键词:铝基复合材料;再结晶;内耗;位错;显微组织;透射电镜
(Edited by Yun-bin HE)
Foundation item: Project (LH201236) supported by the Pre-research Project of Equipment Development Department of China
Corresponding author: Bing-hui LUO; Tel: +86-731-88830333; E-mail: lbh@csu.edu.cn
DOI: 10.1016/S1003-6326(16)64382-0