J. Cent. South Univ. Technol. (2010) 17: 765-769
DOI: 10.1007/s11771-010-0554-9
Extraction of valuable metals from low-grade nickeliferous laterite ore by reduction roasting-ammonia leaching method
CHEN Sheng-li(陈胜利)1,2, GUO Xue-yi(郭学益)1, SHI Wen-tang(石文堂)1, LI Dong(李栋)1
1. School of Metallurgical Science and Engineering, Central South University, Changsha 410083, China;
2. Jinchuan Nonferrous Metals Company, Jinchang 737100, China;
? Central South University Press and Springer-Verlag Berlin Heidelberg 2010
Abstract: Nickel and cobalt were extracted from low-grade nickeliferous laterite ore using a reduction roasting-ammonia leaching method. The reduction roasting-ammonia leaching experimental tests were chiefly introduced, by which fine coal was used as a reductant. The results show that the optimum process conditions are confirmed as follows: in reduction roasting process, the mass fraction of reductant in the ore is 10%, roasting time is 120 min, roasting temperature is 1 023-1 073 K; in ammonia leaching process, the liquid-to-solid ratio is 4:1(mL/g), leaching temperature is 313 K, leaching time is 120 min, and concentration ratio of NH3 to CO2 is 90 g/L:60 g/L. Under the optimum conditions, leaching efficiencies of nickel and cobalt are 86.25% and 60.84%, respectively. Therefore, nickel and cobalt can be effectively reclaimed, and the leaching agent can be also recycled at room temperature and normal pressure.
Key words: low-grade nickeliferous laterite ore; nickel; cobalt; reduction roasting; ammonia leaching; extraction
1 Introduction
There is about 4.7×108 t nickel reserved in the world [1], in which nickeliferous laterite ore takes about 60% and magnetic Cu-Ni sulfide occupies about 40% [2]. Currently, the resource of nickel industry mostly comes from sulfide nickel ores, which occupies 60%-65% in the total output, the other comes from nickel oxide ores [3]. It is anticipated that about half primary nickel will be produced from nickeliferous laterite ores after 2012 [4-5].
At present, hydrometallurgical processes are more applicable to the nickeliferous laterite ores [6-9]. In consideration of the composition difference of ores, different methods and flowsheets are adopted in hydrometallurgical processes. For instance, high- temperature ammonia leaching, high pressure acid leaching, atmospheric pressure leaching, and dump leaching [10-22] are the alternative processes to extract nickel and cobalt from nickeliferous laterite ores. However, these conventional technologies cannot release some disadvantages, such as large energy consumption in recovering valuable metals, ineffective recovery of nickel and cobalt and secondary environmental pollution. Autoclaves are expensive and difficultly operated. In comparison, ammonia leaching at normal temperature is favorable to nickelferrous laterite ore treatment. Consequently, reduction roasting-low temperature ammonia leaching process was carried out to extract nickel and cobalt from low-grade nickeliferous laterite ore.
2 Experimental
2.1 Raw materials
Low-grade nickeliferous laterite ore used in this work belongs to ferruginous ore with high content of iron. The main chemical composition is shown in Table 1. The main minerals are limonite, goethite, serpentine ore, hard chromium spinel, and gangue. The XRD pattern of raw material is shown in Fig.1.
Table 1 Chemical composition of low-grade nickeliferous laterite ore (mass fraction, %)
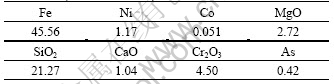
2.2 Apparatuses and reagents
The main experimental apparatuses are as follows: shake stick mill, muffle furnace, acidimeter, round bottom flask, temperature water-bath cauldron with electrothermal constant, electric agitator, air compressor, gas flowmeter, filtrator and dry oven.
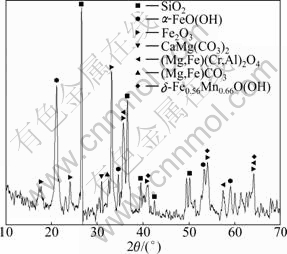
Fig.1 XRD pattern of low-grade nickeliferous laterite ore
The main reagents are as follows: industrial bituminous coal (48.81% of fixed carbon and 22.86% of volatile part), industrial NH4HCO3 (N, ≥17.1%; H2O, ≤3.5%, mass fraction), NH3·H2O (NH3, 25%-28%).
2.3 Experimental method
The raw material was screened to the required particle size (≤10 mm), and then heated in dry oven. 100 g of sample was mixed with a certain amount of fine coal ground to 177 μm, and then the mixture was put in a special container with a sealed cover. The container was put in muffle furnace and heated at a certain temperature for a certain time. Thereafter, the sample was cooled by water quenching with (NH4)2CO3 solution. Afterwards, nearly 80% of abrasive materials were ground to 75 μm and then stirred slowly in NH3-(NH4)2CO3 solution in air at a certain liquid-to-solid ratio for a period of time. Finally, after filtration and washing, the contents of Ni and Co in the solution and residue were analyzed, respectively.
2.4 Theoretical fundamental
2.4.1 Reduction roasting process
Coal can be used as a reductant, which consists of the fixed coal and volatile part. The reduction reaction of fixed coal was regarded as the combination of indirect reduction reaction (carbon monoxide was used as reductant) and Boudol reaction. The chemical reactions are as follows:
MeO+CO=Me+CO2↑ (1)
C+CO2=2CO↑ (2)
When the equilibrium partial pressure of carbon dioxide (CO2) in Boudol reaction exceeds the partial pressure of CO2 produced in reduction reaction of MeO, carbon monoxide (CO) is produced through Boudol reaction with carbon and CO2 in the system, and then CO reacts with MeO. CO2 is consumed and reactant CO is produced constantly by Boudol reaction, so that the reaction may continue until the fixed coal runs out or all of the metal oxide is reduced.
Volatile part is considered to be reductant of CH4, which is only concerned as interacting matter. The main reduction reactions are as follows:
NiO+CH4=Ni+2H2↑+CO↑ (3)
3Fe2O3+CH4=2Fe3O4+2H2↑+CO↑ (4)
CoO+CH4=Co+2H2↑+CO↑ (5)
2.4.2 Ammonia leaching process
Ni and Co in the calcine exist in the form of metal. The main leaching reactions occur when air is insufflated into NH3-(NH4)2CO3 solution:
2Ni+O2+2(n-2)NH3+2(NH4)2CO3=
2[Ni(NH3)n]CO3+2H2O (6)
2Co+O2+2(n-2)NH3+2(NH4)2CO3=
2[Co(NH3)n]CO3+2H2O (7)
4[Co(NH3)n]CO3+O2+2(NH4)2CO3=
2[Co(NH3)n]2(CO3)3+4NH3+2H2O (8)
The form of iron in the calcine is mainly Fe3O4, and the others are FeO and Fe. The main reactions are as follows:
Fe+1/2O2+(n-2)NH3+(NH4)2CO3=
[Fe(NH3)n]CO3+H2O (9)
FeO+(n-2)NH3+(NH4)2CO3=[Fe(NH3)n]CO3+H2O (10)
However, [Fe(NH3)n]CO3 is not stable, it is precipitated as Fe(OH)3 and enters into the residue in the oxygen atmosphere. The reaction is as follows:
4[Fe(NH3)n]CO3+10H2O+O2=
4Fe(OH)3+4(n-2)NH3+4(NH4)2CO3 (11)
3 Results and discussion
3.1 Effect of roasting temperature
The effect of roasting temperature on leaching efficiency of Ni and Co was investigated under the following conditions: 10% for the mass fraction of coal in ore, 120 min for roasting time, 120 min for leaching time, 4:1 for the liquid-to-solid ratio, 313 K for leaching temperature, and 90 g/L:60 g/L for the concentration ratio of NH3 to CO2. The results are shown in Fig.2.
It can be seen from Fig.2 that while the roasting temperature is between 973 and 1 173 K, the leaching efficiencies of Ni and Co keep almost the same. When the roasting temperature is over 1 173 K, the leaching efficiencies of Ni and Co tend to decrease, which is mainly due to the agglomeration of calcine and the decreases of material porosity at high temperature, so the leaching solution can hardly contact the materials. In the meantime, considering energy saving, the optimum roasting temperature is fixed at 1 023-1 073 K.
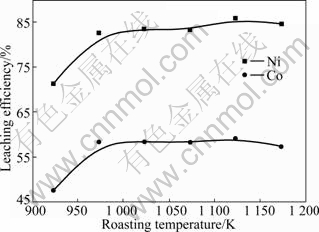
Fig.2 Effect of roasting temperature on leaching efficiencies of Ni and Co
3.2 Effect of mass fraction of coal
The effect of mass fraction of coal on leaching efficiencies of Ni and Co was studied under the following conditions: 1 073 K for roasting temperature, 120 min for roasting time, 120 min for leaching time, 4:1 for the liquid-to-solid ratio, 313 K for leaching temperature, and 90 g/L:60 g/L for the concentration ratio of NH3 to CO2. The results are shown in Fig.3.

Fig.3 Effect of mass fraction of coal on leaching efficiencies of Ni and Co
It can be seen from Fig.3 that while the mass fraction of coal is below 10%, the leaching efficiency increases with the increase of mass fraction of coal. When the mass fraction of coal keeps increasing, the leaching efficiency tends to decrease. It may be due to that Ni and Co are not reduced completely when the coal addition is insufficient, and Fe or FeO form is obtained in the reduction process. The Fe or FeO form enters into the solution in ammonia leaching process and then easily oxidized to be Fe(OH)3 colloid, which has strong adsorptions of Ni and Co [23-24]. So, the mass fraction of coal was controlled as 10%.
3.3 Effect of roasting time
The effect of roasting time on leaching efficiencies of Ni and Co was studied under the following conditions: 1 073 K for roasting temperature, 10% for the mass fraction of coal, 120 min for leaching time, 4:1 for the liquid-to-solid ratio, 313 K for leaching temperature, and 90 g/L: 60 g/L for the concentration ratio of NH3 to CO2. The results are shown in Fig.4.
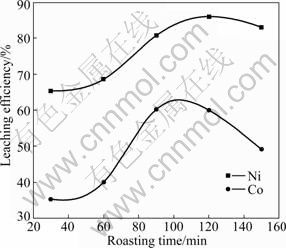
Fig.4 Effect of roasting time on leaching efficiencies of Ni and Co
The results in Fig.4 reveal that while the roasting time is less than 120 min, the leaching efficiencies of Ni and Co increase remarkably with extension of roasting time. When the roasting time is over 120 min, the leaching efficiency tends to decrease. This is maybe because when the roasting time is too long, the excessive iron is reduced and then easily transformed to Fe(OH)3 colloid in leaching process. Moreover, Fe(OH)3 colloid has strong adsorptions of Ni and Co, resulting in the decrease of leaching efficiencies of Ni and Co. With the increase of the roasting time, the color of ammonia leaching residue changes from black to brown and then to yellow, indicating that the amount of Fe(OH)3 increases step by step. Therefore, the best roasting time is 120 min.
3.4 Effect of leaching time
The effect of leaching time on leaching efficiencies of Ni and Co was investigated under the following conditions: 1 073 K for roasting temperature, 120 min for roasting time, 10% for the mass fraction of coal, 4:1 for the liquid-to-solid ratio, 313 K for leaching temperature, and 90 g/L:60 g/L for the concentration ratio of NH3 to CO2. The results are shown in Fig.5.
It can be seen from Fig.5 that the leaching efficiency of Co increases rapidly with the extension of leaching time. But it tends to decrease with the increase of leaching time over 120 min. The leaching efficiency of Ni increases remarkably and almost shows linear relationship with the leaching time. It is maybe because Co can be dissolved rapidly in ammonia solution in the form of Co(NH3)n2+. With the increase of leaching time, some cobalt complex can be easily absorbed by Fe(OH)3 formed in ammonia leaching process. The results also indicate that the adsorption capacity of Co by Fe(OH)3 is stronger than that of Ni. Therefore, according to the results, the optimum leaching time is 120 min.
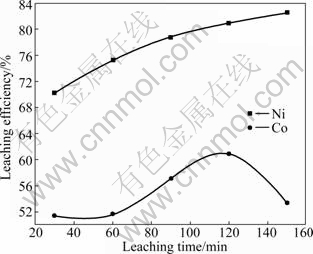
Fig.5 Effect of leaching time on leaching efficiencies of Ni and Co
3.5 Effect of liquid-to-solid ratio
The effect of liquid-to-solid ratio on leaching efficiencies of Ni and Co was investigated under the following conditions: 1 073 K for roasting temperature, 120 min for roasting time, 10% for the mass fraction of coal, 313 K for leaching temperature, 120 min for leaching time, and 90 g/L:60 g/L for the concentration ratio of NH3 to CO2. The results are shown in Table 2.
Table 2 Effect of liquid-to-solid ratio on leaching efficiencies of Ni and Co

The results in Table 2 show that the leaching efficiencies of Ni and Co increase with the increase of the liquid-to-solid ratio. This is because the reduced calcine can contact more ammonia and ammonium in a limited time as the liquid-to-solid ratio increases. However, to increase the leaching efficiencies of Ni and Co by increase of liquid-to-solid ratio is based on the decrease of the utilization efficiency of leaching equipment. So, considering the leaching efficiency and production capacity simultaneously, the liquid-to-solid ratio is chosen to be 4:1.
3.6 Effect of leaching temperature
The effect of leaching temperature on leaching efficiencies of Ni and Co was investigated. The experimental conditions were the same as above except the change of the leaching temperature. The results are shown in Fig.6.

Fig.6 Effect of leaching temperature on leaching efficiencies of Ni and Co
The results in Fig.6 indicate that the leaching efficiencies of Ni and Co keep changeless basically with the increase of leaching temperature. However, it can be seen that the leaching efficiencies of Ni and Co decrease slowly when the leaching temperature is higher than 313 K.
It is maybe because NH3 can be easily volatilized from the leaching solution when the leaching temperature gets high, resulting in a negative effect on leaching of Ni and Co. Therefore, the optimum leaching temperature is chosen as 313 K.
3.7 Effect of concentration ratio of NH3 to CO2
The effect of concentration of NH3 to CO2 on leaching efficiencies of Ni and Co was investigated under the following conditions: 1 073 K for roasting temperature, 120 min for roasting time, 10% for the mass fraction of coal, 4:1 for the liquid-to-solid ratio, 120 min for leaching time, and 313 K for leaching temperature. The results are shown in Table 3.
According to Table 3, leaching efficiencies of Ni and Co increase with the increase of concentration of NH3. It is maybe because more Ni and Co are dissolved in ammonia solution in the form of Ni(NH3)n2+ and Co(NH3)n2+ with the increase of NH3 and CO2, respectively. While the concentration of NH3 is higher, the ammonia volatilization loss gets higher in the ammonia leaching. Thus, the leaching efficiencies of Ni and Co and the consumption of NH3 should be considered simultaneously. To ensure the high leaching efficiency, the concentrations of NH3 and CO2 should be lowered as soon as possible. Based on the results of the experiment, the best concentration ratio of NH3 to CO2 is 90 g/L: 60 g/L.
Table 3 Effect of concentration ratio of NH3 to CO2 on leaching efficiencies of Ni and Co

4 Conclusions
(1) The process of reduction roasting-ammonia leaching is adopted to extract nickel and cobalt from low-grade nickeliferous laterite ore. Nickel and cobalt can be effectively recovered with fine coal as a reductant and the leaching agent can be recycled at room temperature and normal pressure.
(2) In the reduction roasting process, nickel and cobalt are reduced by CO, and iron in calcine mainly exists in the form of Fe3O4. The optimum conditions for the process are as follows: the mass fraction of coal is 10%, roasting time is 120 min, and roasting temperature is 1 073 K.
(3) In the ammonia leaching process, nickel and cobalt can be leached effectively. The optimum conditions of the process are as follows: leaching time is 120 min, the liquid-to-solid ratio is 4:1, leaching temperature is 313 K, and concentration ratio of NH3 to CO2 is 90 g/L:60 g/L.
(4) Under the optimum conditions, the leaching efficiencies of nickel and cobalt are 86.25% and 60.84%, respectively.
References
[1] LI Jian-hua, CHENG Wei, XIAO Zhi-hai. Review on process technologies of laterite-nickel ore [J]. Hydrometallurgy of China, 2004, 23(4): 191-194. (in Chinese)
[2] CAO Yi-sheng. The status quo and prospects of nickel industry at home and abroad [J]. World Nonferrous Metal, 2005(10): 67-71. (in Chinese)
[3] HE Huan-hua. Present situation and development trend of world nickel industry [J]. Nonferrous Smelting, 2001, 12(6): 1-3. (in Chinese)
[4] LAN Xing-hua. The survey of world’s nickel laterite smelter[J]. World Nonferrous Metal, 2006(11): 65-70. (in Chinese)
[5] CUI He-tao, XUE Ping, XU You-sheng. China’s nickel metallurgical process development and technological progress [J]. Mining and Metallurgy, 1997, 6(2): 43-55. (in Chinese)
[6] BCRGRNAN R A. Nickel production from low-iron laterite ores: process descriptions [J]. CIM Bulletin, 2003, 1072: 127-138.
[7] LIU Yan, ZHAI Yu-chun, WANG Hong. Research on production process of nickel [J]. Materials Review, 2006, 20(3): 79-81.
[8] LI Xiao-ming, TANG Lin, LIU Shi-liang. Technology of treating nickel-bearing laterite [J]. Ferro-alloys, 2007, 38(4): 24-28. (in Chinese)
[9] KING M G. Nickel laterite technology—Finally a new dawn? [J]. JOM, 2005, 57(7): 35-39.
[10] POWER L F, GEIGER G H. The application of the reduction roast-ammoniacal ammonium carbonate leach to nickel laterites [J]. Minerals Science, 1997, 9(1): 32-50.
[11] WHITTINGTON B, MUIR D M. Pressure acid leaching of nickel laterites: A review [J]. Mineral Processing and Extractive Metallurgy Review, 2000, 21(6): 527-600.
[12] WHITTINGTON B I, MCDONALD R G, JOHNSON J A, MUIR D M. Pressure acid leaching of Bulong nickel laterite ore. Part I: Effect of water quality [J]. Hydrometallurgy, 2003, 70(1/3): 31-46.
[13] GEORGIOU D, PAPANGELAKIS V G. Sulphuric acid pressure leaching of a limonitic laterite: Chemistry and kinetics [J]. Hydrometallurgy, 1998, 49(1/2): 23-46.
[14] COTO O, GALIZIA F, HERNADEZ I, MARRERO J, DONATI E. Cobalt and nickel recoveries from laterite tailings by organic and inorgnic bio-acids [J]. Hydrometallurgy, 2008, 94(1/4): 18-22.
[15] KAR B B, SWAMY Y V, MURTHY B V R. Design of experiments to study the extraction of nickel from lateritic ore by sulphatization using sulphuric acid [J]. Hydrometallurgy, 2000, 56(3): 387-394.
[16] XU Yan-bin, XIE Yan-ting, YAN Lan, YANG Ru-dong. A new method for recovering valuable metals from low-grade nickeliferous oxide ores [J]. Hydrometallurgy, 2005, 80(4): 280-285.
[17] VALIX M, TANG J Y, CHEUNG W H. The effects of mineralogy on the biological leaching of nickel laterite ore [J]. Mineral Engineering, 2001, 14(12): 1629-1635.
[18] AGATZINI LEONARDOU S, ZAFIRATOS I G. Beneficiation of a Greek serpentinic nickeliferous ore. Part II: Sulphuric acid heap and agitation leaching [J]. Hydrometallurgy, 2004, 74(3/4): 267-275.
[19] PURWANTO H, SHIMADA T, TAKAHASHI R, YAGI J I. Recovery of nickel from selectively reduced laterite ore by sulphuric acid leaching[J]. ISIJ International, 2003, 43(2): 181-186
[20] FU Fang-ming, HU Qi-yang, LI Xin-hai, WANG Zhi-xing, LI Jin-hui, LI Ling-jun. Reduction leaching of lateritic nickel by dilute hydrochloric acid solution [J]. Mining and Metallurgical Engineering, 2009, 29(4): 74-76, 84. (in Chinese)
[21] CHANG Yong-feng, ZHAI Xiu-jing, FU Yan, LI Bin-chuan, ZHANG Ting-an. Sulphuric acid leaching kinetics of pre-reduced laterite ores [J]. Journal of Molecular Science, 2008, 24(4): 241-245. (in Chinese)
[22] MOHAPATRA S, PRADHAN N, MOHANTY S, SUKLA L B. Recovery of nickel from lateritic nickel ore using Aspergillus Niger and optimization of parameters [J]. Minerals Engineering, 2009, 22(3): 311-313.
[23] CARON M H. Fundamental and practical factors in ammonia leaching of nickel and cobalt ores [J]. Metals, 1950, 188: 67-90.
[24] KASHERININOV G O. Behaviour of iron in ammonia solutions during leaching of cobalt from its ores [J]. J Appl Chem VSSR, 1960, 33(6): 1225-1236.
Foundation item: Project(50674014) supported by the National Natural Science Foundation of China
Received date: 2009-09-29; Accepted date: 2010-01-26
Corresponding author: GUO Xue-yi, PhD, Professor; Tel: +86-731-88877863; E-mail: xyguo@mail.csu.edu.cn
(Edited by YANG You-ping)