J. Cent. South Univ. (2017) 24: 335-340
DOI: 10.1007/s11171-017-3435-2

Dissolution kinetics of copper from multi-metal copper alloy roasted in oxygen
LU Wei-hong(卢伟红), YIN Zhou-lan(尹周澜), DING Zhi-ying(丁治英), LIU Yang(刘洋)
College of Chemistry & Chemical Engineering, Central South University, Changsha 410083, China
Central South University Press and Springer-Verlag Berlin Heidelberg 2017
Abstract: A kinetic study on the sulfuric acid leaching of multi-metal oxide, which is the product of multi-metal copper alloy with iron trioxide roasted in oxygen, was carried out. The effects of leaching time, stirring speed, sulfuric acid concentration, reaction temperature, and particle size of the multi-metal oxide on the kinetics and mechanism of copper extraction were studied. It was found that the reaction kinetic model about the copper extraction from multi-metal oxide follows the mixed kinetic shrinking core mode: 1/3ln(1–X)+(1–X)–1/3–1=680.5C(H2SO4)0.4297dP–0.75115exp(–Ea/RT)t.
Key words: leaching kinetic; multi-metal copper alloy; roasting
1 Introduction
At present, the economical and environmental requirements impel the development of effective and inexpensive methods for the recovery of valuable metals from secondary sources. Significant amounts of copper exist in lead and copper metallurgical wastes. Copper contained in lead minerals is usually separated from lead in the form of copper sulfide and copper-containing multi-metal alloy [1–6]. Copper matte (copper sulfide) is treated by hydrometallurgical processes in acid or ammonia leaching/electrowinning processes which brings some disadvantages such as slow rate of reaction and leaching, or in acid medium in pressure oxidative leaching [7, 8].
The multi-metal copper alloy obtained from the industrial slag is multi-phase materials. The copper- containing multi-metal alloy usually contains copper, lead, silver, antimony, arsenic and other valuable metals [9]. It is always treated by copper pyrometallurgy because of the high content of copper. However, copper pyrometallurgy has many disadvantages, such as low recovery of metals, environmental pollution, high energy consumption because of less sulfur or no sulfur in the alloy and so on. BURZYNSKA et al [10] showed that anodic dissolution in the ammonocial solution could be a suitable method for the separation of Cu-Co-Fe alloys. The high-copper (90%) alloys dissolved spontaneously in Cu2+-ammonia-ammonium sulfate solution, while low- copper (5% Cu) alloys were unaffected by chemical leaching, but did dissolve during electrolysis in ammonia-ammonium chloride solution. PARK et al [11, 12] studied the dissolution behaviour of complex Cu-Ni-Co-Fe matte in CuCl2-NaCl-HCl and FeCl3-HCl leaching medium. REDEMAN et al [13] showed the leaching characteristics of Ni-Cu Matte in the acid-oxygen pressure leaching process at Implasa platiunum. Roasting copper slag with ferric sulfate [14] and sulfuric [15] followed by acidic leaching were also reported in the literatures.
The copper-containing multi-metal alloy cannot be corroded by sulfuric acid or hydrochloric acid solution in ordinary pressure. Although it could be treated by nitric acid, it is not an economical and environmental method for high acid consumption and a great deal of nitric oxide formed. Hydrometallurgical treatment by sulfuric acid or hydrochloric acid was less reported. Therefore, the development of new technique for copper-containing multi-metal alloy with high rate of recovery, low environmental pollution and low cost is very essential.
The present work reports the oxidation of multi-metal copper alloy and the dissolution in the H2SO4 solution of its oxide. The kinetic characteristics are analyzed according to the mixed kinetic shrinking core mode, which is based on the interface transfer and diffusion across the solid layer [16, 17]. An overall mathematical model for copper extraction from multi-metal oxide is developed, which can offer the potential knowledge to optimize copper recovery by controlling the process parameters.
2 Chemical reactions
2.1 Roasting reactions
The roasting process of multi-metal copper alloy
with iron trioxide at 450 °C in oxygen can be described by the following chemical reactions:
Fe2O3+M=FeO+MO (1)
2FeO+1/2O2=Fe2O3 (2)
2M+O2=2MO (M=Cu(II), Fe(III), Pb(II), As(V), Sb(V)) (3)
M1O+M2O=M1O·M2O (M1=Fe(III), Cu(II), Pb(II);
M2=As(V), Sb(V)) (4)
2.2 Leaching reactions
The leaching of the copper multi-metal oxide can be described by the following chemical reactions:
CuO+H2SO4=CuSO4+H2O (5)
PbO+H2SO4=PbSO4+ H2O (6)
CuSb2O6+H2SO4+H2O=CuSO4+Sb2O5·2H2O (7)
2Cu4(AsO4)O+8H2SO4=8CuSO4+5H2O+2H3AsO4 (8)
Fe2O3+H2SO4=Fe2(SO4)3+H2O (9)
3 Methods of analyses
3.1 Chemical analysis of products
Multi-metal copper alloy and leaching solution were assayed for suit of elements by inductively coupled plasma-atomic emission spectroscopy (ICP-AES) using the standard method. The elements included arsenic, copper, iron, silver, lead, gold and antimony. The sulfur analysis was carried out by “Methods for Chemical Analysis of Copper Ores, Lead Ores, Zinc Ores – Part 12: Determination of Sulfur Content”.
3.2 Mineralogical analyses
Multi-metal copper alloy and multi-metal oxide were analyzed using qualitative X-ray diffraction (XRD). Patterns were recorded on a Japan Rigaka 2550 (18 kW) using Cu Kα radiation. The phases present were identified by comparison of the peak positions and intensities with data published by MDI Jade 6.
3.3 Mass analyses
The masses of multi-metal copper alloy and its oxide were analyzed using Shimazu AUY 220 balance.
4 Experimental results
4.1 Change in mass and chemical analysis
The multi-metal copper alloy, which was produced by pyro-refining of lead, was obtained from Hunan Jinwang Bismuth Co. Ltd., China. It was crushed, ball-milled, roasted with iron trioxide in oxygen atmosphere. Table 1 lists that the mass increase after oxidation. But the mass gain rate was not evidently changed and kept at about 18% when the original mass changed. From Table 2, it can be seen that the content of copper, antimony, arsenic and lead decreases after being roasted with iron trioxide in oxygen atmosphere. From the composition of the sample before and after roasting, it can be deduced that arsenic and antimony did not escape in the form of arsenic trioxide and antimony trioxide.
Table 1 Increase percentage in mass of samples with different initial masses
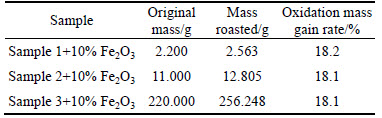
Table 2 Chemical compositions of sample and sample roasted in oxygen (mass fraction, %)
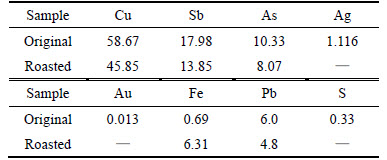
4.2 XRD analysis
XRD pattern of the multi-metal copper alloy is illustrated in Fig. 1. The diffraction peaks are diffused and most of the energy is absorbed by the sample for the test equipment using Cu Kα radiation. It may be inferred that the sample is in amorphous state and contains a lot of copper (Cu).
From Fig. 2, it can be seen that the diffraction peaks of tenorite (CuO), copper diantimony(V) oxide (CuSb2O6) and tetracopper bi(arsenate(V) oxide Cu4(AsO2)4O replace the original diffuse peak, which illustrates that the multi-metal copper alloy was oxidized.
4.3 Leaching experiments
Multi-metal oxide was ball-milled again, and then screened for different particle size with Tyler sieves. The chemical composition of 125-150 μm size fraction is in the form of CuO, CuSb2O6 and Cu4(AsO4)O.
The leaching experiments were conducted in a 400 mL glass beaker. Temperature was controlled automatically in the electric-heated thermostatic water bath. The slurry was agitated by magnetic stirring apparatus. The temperature was recorded from the thermometer, and agitation speed was monitored through the electric-heated water bath. Typically, 200 mL H2SO4
solution was agitated in the glass beaker and heated to the required temperature, and then 2 g sample was added in the H2SO4 solution. The reaction time was counted after the introduction of sample into the glass beaker. In the experiments, about 2 mL of leaching solution was sampled and filtered each time; and then, 1 mL filtered leaching solution was pipetted into 200 mL volumetric and brought to volume before analysis for copper by inductively coupled plasma-atomic emission spectroscopy (ICP-AES).
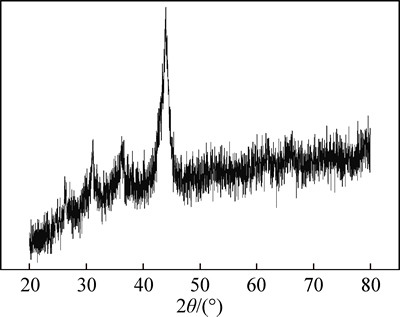
Fig. 1 XRD pattern of multi-metal copper alloy
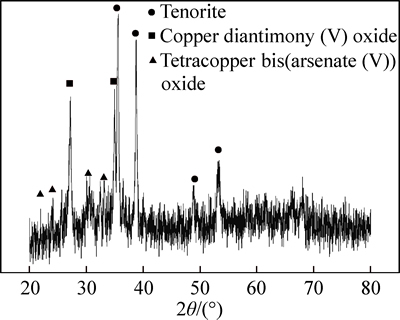
Fig. 2 XRD pattern of multi-metal copper alloy roasted with iron trioxide in oxygen
5 Leaching kinetic discussion
5.1Effect of stirring speed
Figure 3 shows that stirring speed has a significant effect on the leaching of copper. The copper recovery rate stayed the same when the stirring speed was more than 250 r/min and other experimental conditions were kept constant.
5.2 Effect of leaching temperature
The effect of leaching temperature from 30 °C to 60 °C on copper recovery was studied. The results presented in Fig. 4(a) show that the copper recovery increased from 70.65% to 98.72% after 1500 s, when the temperature rose from 30 °C to 60 °C. The solid layer of product, such as lead sulfate and second hydration antimony pentoxide, was produced in the leaching process.
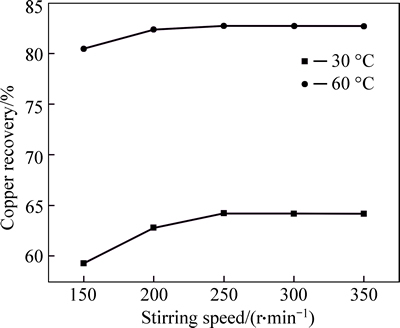
Fig. 3 Effect of stirring speed on recovery of copper from multi-metal copper alloy roasted with iron trioxide in oxygen (Acid concentration, 20 g/L; particle size, 150–125 μm; 2 g; solid to liquid ratio, 1:100 g/mL; time, 15 min)
Assuming that the leaching behavior of copper is controlled by diffusion across the solid layer, leaching behavior of multi-metal oxide can be described by diffusion shrinking model. The kinetic equation can be expressed as follows:
1–3(1–X)2/3+2(1–X)=kexp(–Ea/RT) (1)
Then, taking natural logarithms on both sides of Eq. (1), there is
ln[d(1–3(1–X)2/3+2(1–X)/dt]=lnk′–Ea/RT (2)
The calculated results according to Eq. (2) are plotted in Fig. 4(b). It is shown that the diffusion shrinking model does not fit perfectly the leaching behavior of copper in multi-metal copper alloy with iron trioxide after being roasted in oxygen. The diffusion across the solid layer of product is probably one of the crucial factors in controlling the leaching behavior. Then, by assuming that the leaching behavior of copper is controlled by the interface transfer and diffusion across the solid layer [16], the leaching behavior of multi-metal oxide can be described by the mixed kinetic shrinking core model:
1/3ln(1–X)+(1–X)–1/3–1=K0C(H2SO4)adPbexp(–Ea/RT)t (3)
where C(H2SO4) is the initial concentration of H2SO4, g/L; a is the reaction order; dP is the particle diameter; b is the constant factor. Taking natural logarithms on both sides of Eq. (3) yields
ln[d(1/3ln(1–X)+(1–X)–1/3–1)/dt]=lnk′–Ea/RT (4)
The calculated results according Eq. (4) are plotted in Fig. 4(c). It shows good fits to the experimental data (R>0.985). The relationship between ln[d(1/3ln(1–X)+ (1–X)–1/3–1)/dt] and 1/T in Fig. 4(d) gives a straight line,
from which the activation energy of the reaction can be derived as Ea=47.81 kJ/mol.
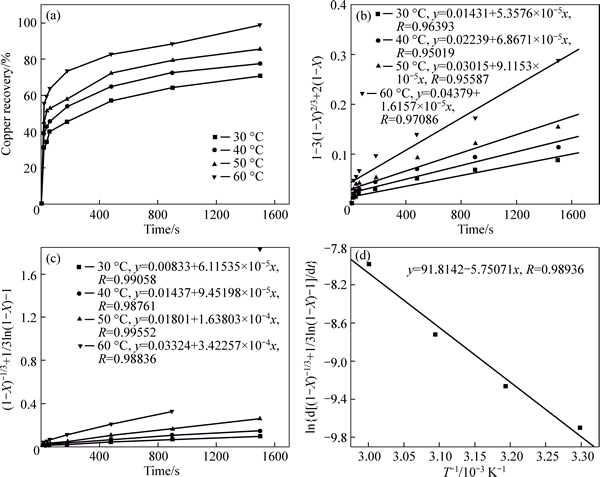
Fig. 4 Effect of leaching temperature on Cu recovery ratio (a) and its relation with time (b–d)
5.3 Effect of particle size
The samples were all leached at 30 °C with sulfuric acid of 20 g/L, agitation speed of 350 r/min and liquid-to-solid ratio of 100. The results are given in Fig. 5. From Fig. 5(a), it is clear that the copper leaching speed is fast at the beginning. If the particle size decreases, the dissolution is faster. The copper extraction ratio increased from 60.9% to 70.1% after 25 min for samples with the particle sizes changing from 0.425– 0.250 mm to 0.150–0.25 mm.
According to the mixed kinetic shrinking core mode, when the temperature and acid concentration keep constant, taking natural logarithms on both sides of Eq. (3) yields
ln[d(1/3ln(1–X)+(1–X)–1/3–1)/dt]=k″+blndp (5)
Equation (5) illustrates a linear relationship between ln[d(1/3ln(1–X)+(1–X)–1/3–1)/dt] and lndp. In order to clarify the quantitative relationship between ln[d(1/3ln(1–X)+(1–X)–1/3–1)/dt] and lndp, the experimental data were analyzed in terms of Eq. (5) as plotted in Fig.5(b). From Fig 5(b), it can be seen that the linear regression equations between ln[d(1/3ln(1–X)+ (1–X)–1/3–1)/dt] and lndp for samples with different particle sizes show good fits to the experimental data (R>0.985). The plot for ln[d(1/3ln(1–X)+(1–X)–1/3–1)/dt] and lndp for the four particle size is an excellent straight line (R=0.998) as shown in Fig. 5(c).
5.4 Effect of acid concentration
Acid concentration is another important factor during the leaching process for the multi-metal copper alloy. The effect of the sulfuric acid concentration from 10 to 40 g/L was studied at 30 °C while the particle size of the sample was 0.150–0.125 mm. The experimental results are presented in Fig. 6(a), which shows that the copper extraction ratio increased from 63.8% to 73.9% at 30 °C after 25 min when the acid concentration was changed from 10 g/L to 40 g/L. According to the mixed kinetic shrinking core mode, when the temperature and particle size keep constant, taking natural logarithms on both sides of Eq. (3) yields
Ln(d(1/3ln(1–X)+(1–X)–1/3–1)/dt)=k″′+alnC(H2SO4) (6)
The linear relationship between ln[d(1/3ln(1–X)+ (1–X)–1/3–1)/dt] and lnC(H2SO4) is illustrated in Fig. 6(b). According to Fig. 6(b), the linear regression equations between ln(d(1/3ln(1–X)+(1–X)–1/3–1)/dt) and lnC(H2SO4) fit the experimental data properly (R>0.995), and the plot for ln[d(1/3ln(1–X)+(1–X)–1/3–1)/dt] and lnC(H2SO4) for the four acid concentrations fits an excellent straight line(R=0.998), as shown in Fig. 6(c).
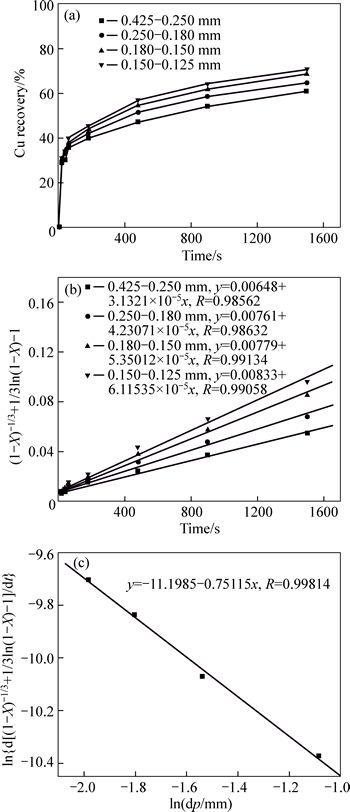
Fig. 5 Effect of particle size on Cu recovery (a) and its relation with time (b–c)
6 Mathematical model of copper leaching
By data statistics of the experiments, the mathematical equation about the kinetic of the copper leaching is as follows:
1/3ln(1–X)+(1–X)–1/3–1=680.5C(H2SO4)dP–0.75115exp(–Ea/RT)t (7)
The predicated value of 1/3ln(1–X)+(1–X)–1/3–1 can be calculated from Eq. (7); and its experiment value can also be calculated from the leaching experiments.Figure 7 shows the predicated and experimental valuesof 1/3ln(1–X)+(1–X)–1/3–1. It is shown that the mathematic equations can excellently describe the process of the copper leaching.

Fig. 6 Effect of acid concentration on Cu recovery (a) and its relation with time (b) and lnC(H2SO4) (c)
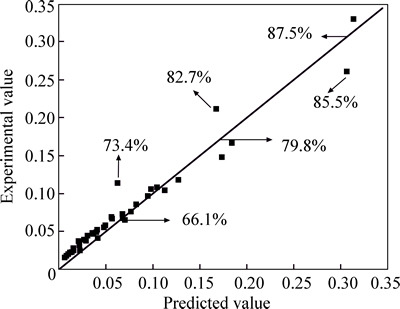
Fig. 7 Comparison of calculated and experimental values of 1/3ln(1-X)+(1-X)-1/3-1 for copper extraction
7 Conclusions
1) The multi-metal copper alloy with iron trioxide was oxidized in oxygen atmosphere at the temperature 450 °C to enhance the extraction of copper.
2) The copper in multi-metal copper alloy, which hardly reacts in sulfuric acid and hydrochloric acid under normal pressure, can dissolve in sulfuric acid under normal pressure after being roasted in oxygen atmosphere with iron trioxide at 450 °C, and the highest copper removal rate can reach 98.7%.
3) Copper extraction increases with the decrease of particle size, the increase of temperature and the increase of sulfuric acid concentration in the range 10–40 g/L.
4) By comparing different dynamic models at different temperatures, the mixed kinetic shrinking core model, controlled by the interface transfer and diffusion across the solid layer, can give a better description of the copper extraction process in sulfuric acid from multi- metal oxide under the normal pressure. The activation energy of the reaction can be derived as Ea=47.81 kJ/mol. The integrated kinetic equation for leaching of copper from multi-metal oxide is
1/3ln(1–X)+(1–X)–1/3–1=680.5C(H2SO4)0.4297dP–0.75115exp(–Ea/RT)t
References
[1] THOMPSON W T, BALE C W, PELTON A D. Facility for theanalysis of chemical thermodynamics (FACTSage) [EB/OL]. Ecole Polytechnique, Montreal. http:www.crct.polymtl.ca, 2012.
[2] CHAIDEZ FELIX A, ROMERO SERRANO A. HERNANDEZ- RAMIREZA A, PEREZ LABEA M, ALMAGUER GUZMAN I, BENAVIDES PEREZ R, FLORES FAVELA M. Effect of copper, sulfur, arsenic and antimony on silver distribution in phases of lead blast furnace [J]. Transactions of Nonferrous Metals Society of China, 2014, 24: 1202–1209.
[3] QU Sheng-li, DONG Zhun-qin, CHEN Tao. Study on gold collection in matte with oxygen enriched bottom blowing smelting process [J]. Nonferrous Metals (Extractive Metallurgy), 2013(6): 40–42.
[4] LIU Liu, YAN Hong-jie, ZHOU Jie-min, GAO Qiang, ZHANG Zhen-yang, LIU Fang-kan, CUI Zhi-xiang. Mechanism of copper smelting process by oxygen bottom blowing and microanalysis of smelting products [J]. The Chinese Journal of Nonferrous Metals, 2012, 22(7): 2116–2124. (in Chinese)
[5] ZHANG Li, LIN Gong-min, BIN Wan-da, LI Yuan-xiang, LI Xiao-bin. Research on oxygen side blow reduction furnace and high lead slag liquid reduction process [C]// The 2nd Bath Smelting Technology and Equipment Symposium. Xi’an: China Nonferrous Metal Society Heavy Metal Metallurgy Academy Committee, 2011: 275-280. (in Chinese)
[6] PEREZ LABRA M, ROMERO SERRANO A, HERNANDEZ RAMIREZA, ALMAGUER GUZMAN I, BENAVIDES PERRZR. Distribution of lead and silver under lead blast furnace conditions [J]. Revista de Metalurgia de Madrid, 2012, 48(3): 213–222.
[7] JIN Bing-jie, YANG Xian-wan, SHEN Qing-feng. Pressure oxidative leaching of lead-containing copper matte [J]. Hydrometallurgy, 2009, 96: 57–61.
[8] JIN Bing-jie, YANG Xian-wan, SHEN Qing-feng. Kinetics of copper dissolution during pressure oxidative leaching of lead-containing copper matte [J]. Hydrometallurgy 2009, 99: 119–123.
[9] RAGHAVAN R, MOHANAN P K. Hydrometallurgical treatment of copper matte generated at a lead smelter for simultaneous recovery of copper, lead and silver [J]. Bull Electrochem, 2000, 16(1): 44–48.
[10] BURZYNSKA L, GUMOWSKA W, RUDNIK E. Influence of the composition of Cu–Co–Fe alloys on their dissolution in ammoniacal solutions [J]. Hydrometallurgy, 2004, 71: 447–455.
[11] PARK K H, MOHAPATRA D, REDDY R. A study on the acidified ferric chloride leaching of a complex (Cu–Ni–Co–Fe) matte [J]. Separation and Purification Technology, 2006, 51: 332–337.
[12] PARK K H, MOHAPATRA D, KIM I H, GUO X Y. Dissolution behaviour of a complex Cu–Ni–Co–Fe matte in CuCl2–NaCl–HCl leaching medium [J]. Separation and Purification Technology, 2007, 56: 303–310.
[13] RADEMAN J A M, LORENZEN L, van DEVENTER J S J. The leaching characteristics of Ni–Cu matte in the acid–oxygen pressure leach process at Impala Platinum [J]. Hydrometallurgy, 1999, 52: 231–252.
[14] ALTUNDOGAN H S, T
MEN F. Metal recovery from copper converter slag byroasting with ferric sulphate [J]. Hydrometallurgy 1997, 44: 261–267.
[15] ARSLAN C, ARSLAN F. Recovery of copper, cobalt and zinc from copper smelter and converter slags [J]. Hydrometallurgy, 2002, 67: 1–7.
[16] DICKINSON C F, HEAL G R. Solid-liquid diffusion controlled rate equations [J]. Thermochimica Acta, 1999, 340(99): 89–103.
[17] LIU Zhi-xiong, YIN Zhou-lan, HU Hui-ping, CHEN Qi-yuan, Leaching kinetics of low-grade copper ore with high-alkality gangues in ammonia-ammonium sulphate solution [J]. Journal of Central South University, 2012, 19(1): 79–84.
(Edited by YANG Bing)
Cite this article as: LU Wei-hong, YIN Zhou-lan, DING Zhi-ying, LIU Yang. Dissolution kinetics of copper from multi-metal copper alloy roasted in oxygen [J]. Journal of Central South University, 2017, 24(2): 335-340. DOI: 10.1007/s11171-017-3435-2.
Foundation item: Project(2011AA061003) supported by Hi-Tech Research and Development Program of China
Received date: 2015-12-14; Accepted date: 2016-05-11
Corresponding author: YIN Zhou-lan, Professor, PhD; Tel: +86–731–88877364; E-mail: xhli@csu.edu.cn