J. Cent. South Univ. Technol. (2010) 17: 881-887
DOI: 10.1007/s11771-010-0571-8

Deformation simulation of low-temperature high-speed extrusion for 6063 Al alloy
WANG Meng-jun(王孟君)1, 2, HE Zhao(何钊)1, WU Xing-xing(武星星)1,
LI Cai-wen(李彩文)1, LI Guang-yao(李光耀)2
1. Key Laboratory of Nonferrous Metal Materials Science and Engineering of Ministry of Education,
Central South University, Changsha 410083, China;
2. State Key Laboratory of Advanced Design and Manufacture for Vehicle Body, Hunan University,
Changsha 410082, China
? Central South University Press and Springer-Verlag Berlin Heidelberg 2010
Abstract: The hot compression test of 6063 Al alloy was performed on a Gleeble-1500 thermo-simulation machine, and the forming of 6063 rod extrudate in low-temperature high-speed extrusion was simulated with extrusion ratio of 25 on the platform of DEFORM 2D successfully. From the compression experimental results, the flow stress model of this Al alloy is obtained which could be the constitutive equation in the simulation of low-temperature high-speed extrusion process. From the numerical simulation results, there is a higher strain concentration at the entrance of the die and the exit temperature reaches up to 522 ℃ in low-temperature high-speed extrusion, which approaches to the quenching temperature of the 6063 Al alloy. The results show that the low-temperature high-speed extrusion method as a promsing one can reduce energy consumption effectively.
Key words: 6063 Al alloy; hot deformation; low-temperature high-speed extrusion; constitutive equation; numerical simulation
1 Introduction
Aluminum extrusion is one of the conventional metal forming processes, mostly used to produce long, straight semi-finished products in the forms of solid and hollow sections with various complexities [1]. In recent years, extrusion methods and processes have been constantly improved and perfected. Except for studying the forward and backward extrusion deeply, there are many new extrusion methods, such as equal channel angular pressing [2-4], isothermal extrusion [5], and twist extrusion [6-7]. But because of the complicated plastic deformation, the complexity of the boundary conditions and the difficulty of mathematic modeling, many researchers utilize the finite element method (FEM) to analyze the extrusion process. AJIBOYE and ADEYEMI [8] analyzed the temperature distribution in axisymmetric extrusion process. ZHI and TERRY [9] discussed material flow in isothermal extrusion with the help of FEM simulations, obtained the ‘unsteady’ character of the extrusion process. In addition, other researchers performed some FEM-based analyses to determine the deformation behavior of materials and to investigate the stress-strain evolution in the extrusion process [10-13], and made considerable progresses.
With the energy shortage in the world, a new type of extrusion technology called low-temperature high-speed extrusion has attracted more and more interest, which means that the billet temperature is lower than that in traditional extrusion methods, and during the whole extrusion process, temperature rises by increasing ram speed. Apparently, this technology meets the need of the society development and will be very promising. However, now low-temperature high-speed extrusion technology is seldom reported deeply [14].
The purpose of this work is to study the deformation behavior of 6063 Al alloy during low-temperature high-speed extrusion using the thermal simulation and numerical simulation technology, so as to carefully control the processing variables in low-temperature high-speed extrusion of aluminum alloys.
2 Experimental
2.1 Compression experiment
A commercial 6063 Al alloy was used for hot compression experiment. The chemical composition isgiven in Table 1. The samples were machined to cylinders of d 10 mm×14 mm. In order to minimize the friction between the samples and die during hot deformation, the flat ends of the samples were recessed to a depth of 0.2 mm to entrap the colloidal graphite, as shown in Fig.1. The hot compression tests were carried out at five different temperatures (473, 573, 623, 673 and 723 K) and four different strain rates (5, 10, 20 and 30 s-1) on a Gleeble-1500 thermo-mechanical simulator. Each sample was heated at heating rate of 100 ℃/min and insulated for 1 min before deformation. The reduction in height was 50% at the end of the compression tests.
Table 1 Chemical composition of tested 6063 alloy (mass fraction, %)

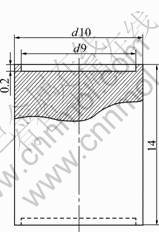
Fig.1 Schematic diagram of sample for compression test (Unit: mm)
2.2 Numerical simulation
The DEFORM 2D software package was used for simulation, which has been applied to the simulation of extrusion processes in recent years. In this numerical experiment, a flat-faced die was designed to produce a rod profile, as shown in Fig.2. By taking advantage of its symmetry, only 1/2 of the billet, extrudate and extrusion die were modeled, which obviously reduced the calculation time. The materials used for the billet and die were 6063 Al alloy and H13 hot-work tool steel, respectively. For the die, a rigid material formulation coupled with a heat transfer formulation [15] was used. The number of the mesh reached 8 000 by the Lagrangian description, and the time step was set as 0.01 s. The friction at the workpiece-tooling interfaces was assumed to shear type. The extrusion speeds were 10, 12, 15 and 20 mm/s, respectively. And other process parameters are given in Table 2.
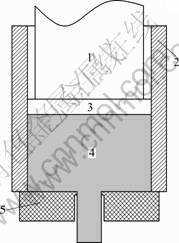
Fig.2 Schematic diagram of model of bar extrusion: 1—Extrusion ram; 2—Extrusion container; 3—Backpad; 4—Billet; 5—Die
Table 2 Process parameters used in simulation
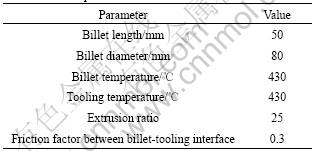
3 Results and discussion
3.1 Constitutive equations of flow stress for 6063 Al alloy
The stress-strain data obtained from compression tests under different strain rate and temperature conditions can be used to determine the material constant of the constitutive equation [16-17]. The relationship between true stress and true strain of the hot-compression of 6063 Al alloy is shown in Fig.3.
The Arrhenius equation is widely used to describe the relationship among the strain rate, the flow stress and the temperature, especially at high temperatures. Also, the effects of the temperatures and strain rates on the deformation behaviors can be represented by Zener–Hollomon parameter in an exponent-type equation. The hyperbolic law in Arrhenius type equation gives better approximations between Zener–Hollomon parameter and flow stress.
(1)
where
is the strain rate (s-1); Q is the deformation activation
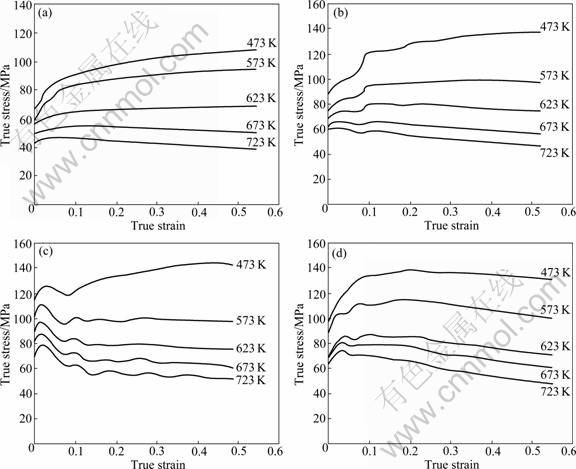
Fig.3 True stress-strain curves for 6063 Al alloy at different temperatures and strain rates: (a) 5 s-1; (b) 10 s-1; (c) 20 s-1; (d) 30 s-1
energy (kJ/mol); R is the universal gas constant (8.31 J/(mol·K)); T is the thermodynamic temperature (K); σ is the flow stress (MPa) for a given strain; A, α and n are material constants, α=β/n.
The relationship among peak stress, deformation rate and deformation temperature is shown in Fig.4. It is obvious that the flow stress obtained from the compression tests can be approximated by a group of parallel and straight lines in the hot deformation conditions. The values of n and β can be obtained from the slope of the lines in σ-ln
and ln σ-ln
plots, respectively. Because the slope of the lines is approximately the same, the values of n and β can be obtained for different deformation temperatures by linear fitting method, and mean values of n and β can be computed as 8.47 and 0.142 MPa-1, respectively. Then, α=β/n=0.016 8 MPa-1. The value of Q can be derived from the slope in a plot of ln[sinh(ασ)] as a function of 1/T, evaluated to be 171.68 kJ/mol. A is attained from the relationship between ln[sinh(ασ)] and ln
, whose value is 1.904×1013 s-1. So, the flow stress model of high temperature compression deformation for 6063 Al alloy is given as:
σ=59.5 ln{[Z/(1.904×1013)]1/8.47+{[Z/(1.904×1013)]2/8.47+1}1/2} (2)
where Z is defined by the expression: Z=
exp[171.68/ (RT)]. In the simulation surrounding, through interpolation method, this flow stress can describe the constitutive equation during low-temperature high-speed extrusion.
3.2 Temperature distribution
The temperature management is a key to aluminum extrusion. The varieties of extrusion temperature decide the product quality and die life. For the products, the exit temperature affects the microstructure, and the shape and dimensional tolerances are also affected in the subsequently cooling process. For the die, the exit temperature can lead to the change of the bearing length and die abrasion, thus in turn makes impact on the shape and dimensional tolerances. In practice, higher billet temperature is conducive to the metal flow, but if too high, it also brings the overburning phenomenon and decreases the maximum extrusion speed. So it is important to analyze the extrudate temperature in the extrusion process for aluminum profiles.
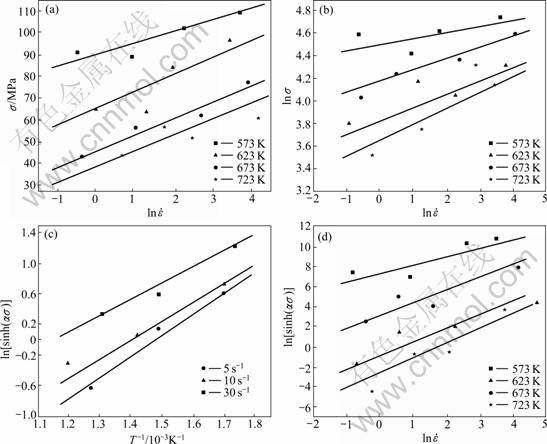
Fig.4 Relationship among peak stress, temperature and strain rate of 6063 Al alloy: (a) σ-ln
; (b) ln σ-ln
; (c) ln[sinh(ασ)]-1/T; (d) ln[sinh(ασ)]-ln
In the extrusion process, the hot billet is forced to pass through the bearing land, in which a part of energy worked on materials is consumed to overcome deformation resistance, and some are used to overcome the friction between the die and the material. The heat energy generated by deformation and friction retains in deformed material partly; some are transferred to the extrusion container and die; and some are delivered to the undeformed billet. So there is heating exchange balance among the billet, extrusion container and surroundings. When the deformation heat and friction heat exceed the heat loss the temperature of extrudate increases.
The development of the maximum extrudate
temperature is of the greatest interest. Fig.5 shows the maximum extrudate temperature with stroke at different extrusion speeds in numerical simulation process. It is obvious that the maximum temperature of the extrudate becomes higher as the extrusion speed increases. The faster the extrusion speed, the larger the temperature rise. The mainly reason is ascribed to that the higher extrusion speed leads to the more heat energy generated in deformation zone; on the other hand, the higher the extrusion speed is, the less the time needs for heat
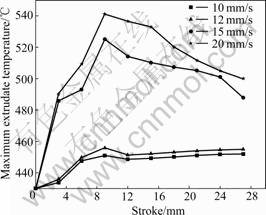
Fig.5 Maximum temperature of extrudate with stroke at different extrusion speeds
exchange, which leads to difficulty for a lot of deformation heat to diffuse, and then the extrudate temperature rises. After a gradual temperature increase, the workpiece temperature decreases and then keeps steady. It might be caused by the following three factors: (1) the decrease of heat from the mechanical work due to the softening of the billet under the condition of the onset of dynamic restoration, (2) the less frictional heat caused by the decrease of the billet length, and (3) the decrease of liquidity due to the heat loss to the surrounding. So the low-temperature high-speed extrusion is possible to decrease the energy consumption.
Fig.6 shows the temperature distribution of the extrudate at the extrusion speed of 15 mm/s. From Fig.6, it can be seen that the highest temperature occurs at the center of the workpiece. The total magnitude of temperature rise over the whole ram stroke is over 95 ℃. This implies that the exit temperature attains 525 ℃, which approaches to the quenching temperature for 6063 Al alloy. This is mainly ascribed to the continuous heat generation due to deformation energy and friction, especially near the die core where there exists dramatic shear deformation.
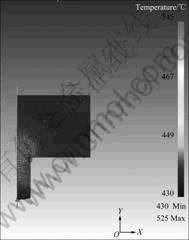
Fig.6 Temperature distribution of extrudate at extrusion speed of 15 mm/s
3.3 Metal flow pattern of high-speed extrusion
Fig.7 shows the metal flow pattern at the extrusion speed of 15 mm/s, in which the central zone, the coextrusion zone and the dead zone can be observed. The technique is based on comparing the deformed grid pattern with the original underformed pattern introduced into the billet. It has been used in previous experiments [9]. Presently, with the development of FEM, the technology can be used in a more precise and economic way, and it indeed gives a pertinent description of the metal flow and deformation in simulation of the extrusion process. From the change of the elements shape, the overall deformation can be estimated. The reference grid is deformed heavily in the central area and the coextrusion area, especially at the exit of the die, and in the dead zone the reference grid remains unchanged. In Fig.7, the deformation is observed to increase from the centre of the extrudate towards the surface of the rod. Because the material flow at the interface of the billet and the container is influenced strongly by the friction, the metal close to the surface of the rod is deformed heavily in shear during extrusion. But in Fig.7, it can be seen that the height of the dead zone is large, which makes the material flow inhomogeneous. The area of the dead zone is influenced strongly by the extrusion ram speed and friction. It is proved that the area of the dead zone becomes larger with the increase of the extrusion speed [9] and the friction force [18]. In this work, the dead zone is larger due to the higher extrusion speed. And in further study, the interaction between the extrusion speed and friction will be investigated to optimize the extrusion process. By choosing extrusion speed and friction condition, the inhomogeneity can be reduced.
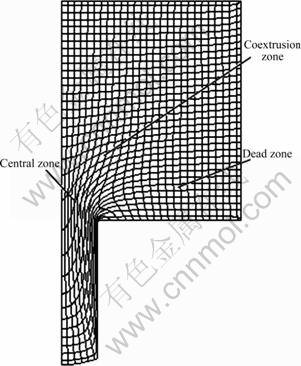
Fig.7 Figure of material flow
The velocity distribution at different extrusion speeds is shown in Fig.8. The farther the distance from the billet center, the smaller the velocity. As a result, there is a resulting conclusion that the velocity reaches the largest value at the exit of the die. All these may be ascribed to the effect of the friction, that is, when the area between the die and the billet is considered, the area close to the center is smaller than that away from the center, and hence the friction will be smaller. This is consistent with the metal flow. From Fig.8, it can be seen that with increasing the extrusion speed, the metal velocity in y direction increases obviously, and the inhomogeneity of the flow also increases accordingly. But the influence of the extrusion speed on inhomogeneity is not great.
3.4 Effective strain distribution
Fig.9 shows the effective strain distribution in
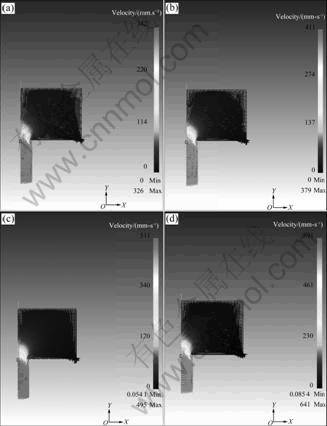
Fig.8 Velocity distribution at different extrusion speeds: (a) 10 mm/s; (b) 12 mm/s; (c) 15 mm/s; (d) 20 mm/s
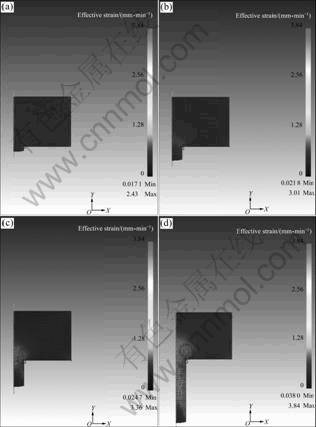
Fig.9 Distribution of effective strain at extrusion speed of 15 mm/s during extrusion at different time steps: (a) Step 72; (b) Step 78; (c) Step 83; (d) Step 100
different strokes of the low-temperature high-speed extrusion. Larger strain gradient is presented at the entrance of the die. The maximum effective strain gradually increases during the extrusion process, which is much larger than that of the conventional extrusion [19-20]. The possible mechanism is that the metal flow is blocked at the entrance of the die during the high-speed extrusion, which results in large shear deformation and high strain concentration. It is also the reason why die wearing failure happens mostly at the entrance of the die. In the actual production, the material used at the entrance of the die should be local hardening heat treatment to improve the wear resistance of die.
4 Conclusions
(1) The flow stress of 6063 Al alloy during hot compression test can be described by the Zener-Hollomon parameter model. And the constitutive equation in low-temperature high-speed extrusion is given as: σ=59.5 ln{[Z/(1.904×1013)]1/8.47+{[Z/(1.904×1013)]2/8.47+1}1/2}, where Z is defined by the expression: Z=
exp[171.68/(RT)].
(2) The area of the dead zone is relatively large, and high strain concentration is presented at the entrance of the die during the low-temperature high-speed extrusion. This can affect the product quality. By optimizing the relationship between the extrusion speed and the friction, the inhomogeneity can be reduced.
(3) Most of the temperature rise occurs at the initial stage of the extrusion, and then the temperature tends to be stable as the ram travels further. The exit temperature reaches up to 525 ℃ at an extrusion ratio of 25 and a extrusion speed of 15 mm/s, which approaches to the quenching temperature. The low-temperature high-speed extrusion is therefore possible to decrease the energy consumption.
References
[1] ZHOU J, LI L, DUSZCZYK J. 3D FEM simulation of the whole cycle of aluminum extrusion throughout the transient state and the steady state using the updated Lagrangian approach [J]. Journal of Materials Processing Technology, 2003, 134(3): 383-397.
[2] BALASUNDAR I, RAO M S, RAGHU T. Equal channel angular pressing die to extrude a variety of materials [J]. Materials & Design, 2009, 30(4):1051-1059.
[3] SIVARAMAN A, CHAKKINGAL U. Flow properties of an aluminum alloy processed by equal channel angular pressing [J]. Journal of Materials Science, 2008, 43(23/24): 7432-7437.
[4] MOGUCHEVA A A, KAIBYSHEV R O. Structure and properties of aluminum alloy 1421 after equal-channel angular pressing and isothermal rolling [J]. Physics of Metals and Metallography, 2008, 106(4): 424-433.
[5] YANG H, ZHANG J, HE Y M, HAN B T. Effect of temperature and ram speed on isothermal extrusion for large-size tube with piece-wing [J]. Journal of Materials Science and Technology, 2005, 21(4): 499-504.
[6] BEYGELZIMER Y, VARYUKHIN V, SYNKOV S, ORLOV D. Useful properties of twist extrusion [J]. Materials Science and Engineering A, 2009, 503(1/2): 14-17.
[7] ORLOV D, BEYGELZIMER Y, SYNKOV S, VARYUKHIN V, HORITA Z. Evolution of microstructure and hardness in pure Al by twist extrusion [J]. Materials Transactions, 2008, 49(1): 2-6.
[8] AJIBOYE J S, ADEYEMI M B. Effects of extrusion variables on temperature distribution in axisymmetric extrusion process [J]. International Journal of Mechanical Sciences, 2008, 50(3): 522-537.
[9] ZHI P, TERRY S. A study on material flow in isothermal extrusion by FEM simulation [J]. Modelling Simul Mater Sci Eng, 2004, 12(5): 745-763.
[10] BASAVARAJ V P, CHAKKINGAL U, KUMAR T S P. Study of channel angle influence on material flow and strain inhomogeneity in equal channel angular pressing using 3D finite element simulation [J]. Journal of Materials Processing Technology, 2009, 209(1): 89-95.
[11] LI L, ZHOU J, DUSZCZYK J. A 3D FEM simulation study on the isothermal extrusion of a 7075 aluminum billet with a predeterminded non-linear temperature distribution [J]. Modelling Simul Mater Sci Eng, 2003, 11(3): 401-416.
[12] YANG F Q, SARAN A, OKAZAKI K. Finite Element simulation of equal channel angular extrusion [J]. Journal of Materials Processing Technology, 2005, 166(1): 71-78.
[13] ZHI P, TERRY S. Simulation of multi-hole die extrusion [J]. Materials Science and Engineering A, 2004, 367(1/2): 329-342.
[14] WANG Meng-jun, GAN Chun-lei, LIU Xin-yu. Deformation behavior of 6063 aluminum alloy during high-speed compression [J]. Journal of Wuhan University of Technology: Mater Sci Ed, 2005, 20(3): 40-43.
[15] KOBAYASHI S, ALTAN T. Metal forming and the finite element method [M]. New York: Oxford University Press, 1989: 12-49.
[16] LIN Y C, CHEN M S, ZHONG J. Constitutive modeling for elevated temperature flow behavior of 42CrMo steel [J]. Computational Materials Science, 2008, 42(3): 470-477.
[17] SHENG Z Q, SHIVPURI R. Modeling flow stress of magnesium alloys at elevated temperature [J]. Materials Science and Engineering A, 2006, 419(1/2): 202-208.
[18] YUAN Shi-jian, LI Feng, LIU Gang. Research of metal flow during extrusion process under different friction conditions by deforming area division [J]. Acta Metallurgica Sinica, 2007, 43(2): 199-204.
[19] LIN Gao-yong, ZHOU Jia, ZHENG Xiao-yan, FENG Di, HUANG Guang-fa, PENG Da-shu. Numerical simulation of extrusion process of X5214 aluminum alloy profile [J]. Journal of Central South University: Science and Technology, 2008, 39(4): 748-754. (in Chinese)
[20] CHENG Lei, XIE Shui-sheng, HUANG Guo-jie, WU Peng-yue, HE You-feng. Numerical simulation in porthole dies extrusion of aluminum harmonica-shaped tube [J]. Journal of Plasticity Engineering, 2008, 4(15): 131-135. (in Chinese)
(Edited by YANG You-ping)
Foundation item: Project(2008A09030004) supported by the Major Science and Technology Project of Guangdong Province, China; Project(30815009) supported by the Foundation of State Key Laboratory of Advanced Design and Manufacture for Vehicle Body
Received date: 2009-11-03; Accepted date: 2010-03-26
Corresponding author: WANG Meng-jun, PhD, Professor; Tel: +86-731-88836408; E-mail: wmj1965@yahoo.com.cn