
Low-temperature sintering method for NiCuZn ferrite and effect of Mn addition on electromagnetic properties
JU Dong-ying(巨东英)1, 2, BIAN Pei(边 培)2
1. Research Center of High Technology, Anshan University of Science and Technology, Anshan 114044, China;
2. Advanced Science Research Center, Saitama Institute of Technology, Fusaiji 1690, Okabe,
Saitama, Japan 369-0293
Received 10 April 2006; accepted 25 April 2006
Abstract: Low temperature sintering NiCuZn ferrite was employed at most cases due to its co-firability with Ag (below 960 ℃). The NiCuZn ferrite sintered body with high-strength and high-frequency magnetic properties was fabricated. Firstly, NiCuZn ferrite powder was synthesized under CO2 atmosphere at 500 ℃ from the mixed doxalate synthesized by liquid phase precipitation method. Then a small amount of boric acid (H3BO3) was added to the powder, and the NiCuZn ferrite powder compact was prepared with Newton press and CIP methods. Finally, NiCuZn ferrite sintered body was fabricated by sintering at 900 ℃ under CO2 atmosphere. The minimum sintering temperature (800 ℃) was determined by the study of high temperature shrinkage. By this method, NiCuZn ferrite sintered body with 0.5% (mass fraction) boric acid was obtained, which has the bending strength of 340 MPa. The effect of various Mn addition on electromagnetic properties were studied.
Key words: ferrite; NiCuZn; boric acid; electromagnetic properties; Mn addition
1 Introduction
Recently, the surface mounting devices (SMD) have been rapidly developed for miniaturisation of electronic applications such as cellular phones, cameras, computers. Low temperature sintering NiCuZn ferrite is important due to its co-firability with Ag[1]. Ultrafine NiCuZn ferrite with uniform composition, small grain size, and narrow size distribution is expected to realize low temperature sintering and attain ideal magnetic property at the same time [2, 3].
The conventional fabrication process is as the following: reagent-grade materials of NiO, CuO, ZnO and Fe2O3 were mixed to yield a composition. The mixture was ball-milled for 10 to 20 h and then dried and calcinated at 900℃ to form spinel structure. After calcination, the mixture was ground and pressed into pellets with small amount addition of sintering binders, which were sintered in air at 950 ℃ [4, 5]. There are some disadvantages for the processes: the particles were easy cohesive because of poor liquidity, the particle sizes’ distribution was wide and the particles would grow abnormally, the mechanical ground method was low efficiency and high cost.
In this paper, the liquid phase precipitation method was used to produce ultrafine NiCuZn ferrite particles with a composition of (Ni0.2-xMnxCu0.2Zn0.6O)(Fe2O3)0.99 (x=0-0.1). Boric acid was added as binder and at CO2 protection atmosphere NiCuZn ferrite was sintered. The effects of boric acid additives on growth of particle and sintering temperature were studied. The minimum sintering temperature (800 ℃) was determined by the study of high temperature shrinkage. The density and bending strength of the NiCuZn sintered magnet with various adding of H3BO3 as well as at various sintered temperatures were evaluated by TMA (Thermo- Mechanical Analyzer), TEM (Transmission Electronic Microscopy) and 3-point bending test. The effect of various Mn addition on electromagnetic properties was evaluated by impedance analyzer.
2 Experimental
2.1 Preparation of NiCuZn ferrite powder
The liquid phase precipitation method was employed to produce fine Ni(Mn)CuZn ferrite powders. The superfine NiCuZn ferrite particle was derived (Ni0.2-xMnxCu0.2Zn0.6O)(Fe2O3)0.99, (x=0, 0.02, 0.04, 0.06, 0.08, 0.1) from mixture oxalate by decomposition reaction and rapid cooling in turn. The precipitation process in the study to get mixture oxalate from raw materials of mixture chloride and ammonium oxalate are showed in the following reaction, where Me is Ni, Mn, Cu, Zn and Fe ion.

By stirring mixture chlorides (FeCl2·4H2O, NiCl2·6H2O, MnCl2·4H2O, CuCl2·2H2O, ZnCl2) and ammonium oxalate ((NH4)C2O4) in aqueous solution for 1h and then filtrate them through the absorption filtration, as first step, we can get the fine mixture oxalate powder. The next step was to dissolve the mixture oxalate powder into ethanol followed by vacuum distillation and recrystallization. Then the refined mixture oxalate was achieved [6].
(2)
(3)
In the next procedure, the mixture oxalate powder was put into a quartz tube where the flowing volume of CO2 was controlled as 200 mL/min. Here, the temperature (10 ℃/min) was raised until the most suitable temperature then kept it for 60 min. After this, draw the quartz tube out of the heating system and quench it into water. Due to good conductivity of quartz material, the magnetic particles were rapidly cooled and then fine powers were obtained.
In order to determine the optimum synthesis temperature, the thermal analysis of mixture oxalate with TG-DTA in the protection atmosphere of CO2 gas(200 mL/min) from room temperature to 800 ℃, the two mass reductions around 200 and 400 ℃ at 10 ℃/min heating speed was carried out. Fig.1 shows accompanying the decalescence phenomenon. The reduced mass percent (59%) is in accordance with the reduction of decomposing mixture oxalate into FeO in which gases are released, at 200 ℃, H2O, small amount of CO and CO2, 400 ℃, CO and CO2, however, no mass change is observed above 450 ℃.
The decomposition of mixture oxalate at the protection of inert gases during producing FeO is given in the reactions (1) and (2). And the change of the protective gases into O2 and CO2 in the reaction is shown in reaction (3), in which the equilibrium trends toward right by controlling the oxygen partial pressure with the product of NiCuZn ferrite. It is possible to synthesize NiCuZn ferrite at low temperature.
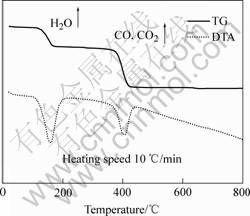
Fig.1 TG-DTA curves of NiCuZn oxalate
To find the best maintaining time, the mixture oxalate was heated to 500 ℃ for a certain time of 60 min at the protection of CO2. Comparing the measured XRD profile with JCPDS cards, it is confirmed that high purified NiCuZn ferrite is obtained by the above method. Then the NiCuZn ferrite particles of NiCuZn ferrite prepared by this method were observed by transmission electron microscope. From the TEM micrograph as shown in Fig.2, it is found that there two different particle sizes exist, the small size is about 6 nm and the larger one is about 100 nm. It is possible to sinter at low temperature by means of small crystal particle, large surface area and high surface free energy.
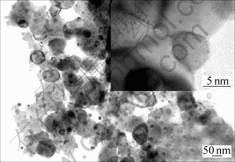
Fig.2 TEM micrographs of NiCuZn powder
2.2 Molded body of NiCuZn ferrite
By carefully mixing the superfine NiCuZn ferrite powder with suitable amount of H3BO3 addition, the NiCuZn ferrite powder was prepared finally. Fill 1.5 g fine NiCuZn ferrite powder into the mould and then apply pressure to the system with 0.5 t for 10min by Newton press, thus the molded bodies (5 mm×5 mm×20 mm used for measuring mechanical strength and d3.5 mm×d8 mm×3 mm used for high frequency magnetic property) were formed. After that, the molded body was put into the vacuum film followed by preserving the body for 1min at the pressure of 50, 100 and 150 MPa by CIP, the high-density compact comes out.
2.3 Low temperature sintering of NiCuZn ferrite with high frequency permeability
The molded bodies with different amount of H3BO3 (0, 0.5, 1.0, 2.0 %) were sintered. The sintering processes were performed at the surrounding of CO2 and the heating schedules were: heatd from room temperature to the setting temperature (800, 850, 900, 950 ℃) at 10 ℃/min; then held for 3 h; finally cooled to room temperature at 10 ℃/min. The proper H3BO3 addition was determined based on the density measurements and 3-points bending tests. The lowest sintering temperature was obtained by TMA based on different sintering temperature with 0.5%.
In order to improve the high frequency permeability, Mn was added and molded bodies were sintered with the same processes described above. The electromagnetic properties of sintered bodies were evaluated by impedance analyzer [7-9].
3 Results and discussion
3.1 Effects of boron amount on sintering condition
The relationship between density and sintering temperature is shown in Fig.3. The relationship between 3-point bending strength and sintering temperature of NiCuZn sintered bodies is shown in Fig.4. The density and strength are increased with the increasing of sintering temperature and the maximum density and strength are obtained at 0.5% H3BO3 addition and 950 ℃[10-12].
Fig.5 shows the relationship among temperatures, shrinkage and time of sintering process with 0.5 % H3BO3 addition by TMA. The sintering body will expand with temperature increasing from room temperature to 580 ℃. From 580 to 800 ℃ the sintering body will shrink for a small amount because H3BO3 will be thermally decomposed to B2O3 at 180 ℃, and the melting point of B2O3 is 577 ℃. It is the phase transformation of B2O3 Resulting in the small amount
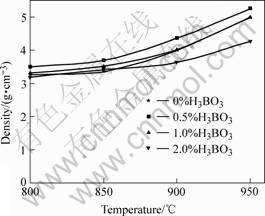
Fig.3 Relationship between density and sintering temperature
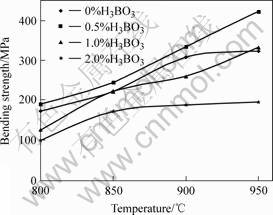
Fig.4 Relationship between 3-point bending strength and temperature of NiCuZn sintered bodies
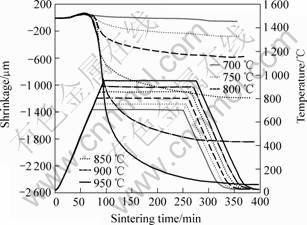
Fig.5 Relationship among temperature, shrinkage and sintering time by TMA
of shrinkage. Above 800 ℃, the sintering body shrinks rapidly because the molten B2O3 promotes the growth of ferrite particles and reduces the pores. Therefore the minimum sintering temperature should be above 800 ℃.
3.2 Effect of Mn content on NiCuZn ferrite electromagnetic properties
The high frequency of permeability for the sample with various Mn content is shown in Fig.6. The permeability is increased with the increasing of sintering temperature and Mn addition. From 0 to 2 % Mn (mole fraction) addition the permeability increases obviously and above 2% Mn addition it changes slowly. High Mn content will decrease the scope of high frequency [13, 14]. The permeability achieves 300 and the high frequency scope is 10 MHz at 900 ℃ and 2% Mn addition. The Q-value decreases according to the increase of frequency, as shown in Fig.7. The lowered Q-value caused by the change of frequency can be explained by Eqn.(4) which shows the relation between Q and the initial permeability[15]. Q-value is not sensitive to Mn content. The Q-value is 25 at 1 MHz, 900 ℃ and 2% Mn addition.
(4)
where
(5)
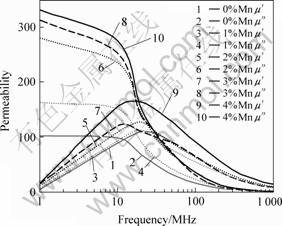
Fig.6 High frequency of initial permeability for sample with various Mn content
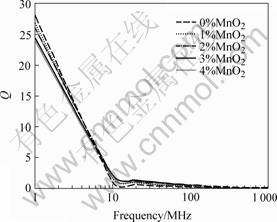
Fig.7 Relationship between quality factor and various Mn content
4 Conclusions
Ultrafine powder and H3BO3 addition are the keys for low temperature sintering of NiCuZn ferrite. As a new manufacturing method, Ni(Mn)CuZn ferrite powder can be obtained after being heated to 500 ℃ for 60 min at the protection of CO2 and then being quenched into water. At the pressure of 150MPa by CIP the molded bodies are fabricated. The lowest sintering temperature is 800 ℃. With 0.5% H3BO3 and 2% Mn additions at 900 ℃ the permeability is 300, the high frequency scope is 10MHz and Q-value is 25.
Acknowledgements
The support provided by High Technology Research Center in Saitama Institute of Technology for this work is gratefully acknowledged.
References
[1] MURTHY S R. Low temperature sintering of MgCuZn ferrite and its electrical and magnetic properties [J]. Bull Mater Sci, 2001, 24: 379-383.
[2] NAKAHATA I, MURASE T, NAKANO A. The study of low temperature sisntering MgCuZn ferrites [J]. J Jpn Soc Powder Powder Metallurgy, 2001, 48: 126-130.
[3] HSU W C, CHEN S C, KUO P C, LIE C T, TSAI W S. Preparation of NiCuZn ferrite nanoparticles from chemical co-precipitation method and the magnetic properties after sintering [J]. Mater Sci Eng B, 2004, B111: 142-149.
[4] OI A, NAKANO A, NOMURA T. Enhancement initial permeability of low temperature sintered NiCuZn ferrites [J]. J Jpn Soc Powder Powder Metallurgy, 2000, 47: 779-783.
[5] KOBAYASHI H, IKEDA T, MITAMURA T, KAKIZAKI K, HIRATSUKA N. Preparation of magnetic particles by the pyrolysis of ferrous oxalate in various atmospheres [J]. J Jpn Soc Powder Powder Metallurgy, 1996, 42: 89-94.
[6] SUZUKI Y, BIAN P, JU D Y, MITAMURA T, KOBAYASHI H. Effect of additives on the microstructure of ferrite sintered body and its characteristic evaluation [J]. J Jpn Soc Powder Powder Metallurgy, 2001, 48: 801-805.
[7] WANG X H, QU W G, GUI Z L. The influence of Mn dopant on the electromagnetic properties of NiCuZn ferrite [J]. Ceramics International, 2004, 30: 1615-1618.
[8] LI B, YUE Z X, QI X W, ZHOU J, GUI Z L, LI L T. High Mn content NiCuZn ferrite for multiplayer chip inductor application [J]. Mater Sci Eng B, 2003, B99: 252-254.
[9] YUE Z X, GUO W Y, ZHOU J, GUI Z L, LI L T. Synthesis of nanocrystilline ferrites by sol-gel combustion process: the influence of pH value of solution [J]. J Magn Magn Mater, 2004, 270 216-223.
[10] KIM C W, KOH J G. A study of synthesis of NiCuZn-ferrite sintering in low temperature by metal nitrates and its electromagnetic property [J]. J Magn Magn Mater, 2003,257 355-368.
[11] SU H, ZHANG H W, TANG X L. Effects of Bi2O3–WO3 additives on sintering behaviors and magnetic properties of NiCuZn ferrites [J]. Mater Sci Eng B, 2005, B117: 231-234.
[12] BABA F, KAKIZAKI K, HIRATSUKA N. Effects of Pr6O11 additives on magnetic properties and microstructure of Mn-Zn ferrites [J]. J Jpn Soc Powder Powder Metallurgy, 2002, 49: 666-670.
[13] NAKANO A, SUZUKI T, MOMOI H. Development of low temperature NiCuZn ferrites and study of high performance for multilayer chip ferrites [J]. J Jpn Soc Powder Powder Metallurgy, 2001, 49: 77-86.
[14] LOW K O, SALE F R. Electromagnetic properties of gel-derived NiCuZn ferrites [J]. J Magn Magn Mater, 2002, 246: 30-35.
[15] REDDY N R, RAMANA M V, RAJITHA G, RAJAGOPAL E, SICAKUMAR K V, MURTHY V R K. Stress sensitivity of inductance in NiCuZn ferrites [J]. J Magn Magn Mater, 2005, 292: 159-163.
(Edited by YUAN Sai-qian)
Corresponding author: JU Dong-ying; Tel: +81-48-5956826; Fax: +81-48-5855928; E-mail: dyju@sit.ac.jp