
Effect of pre-strain on fatigue crack growth of 2E12 aluminum alloy
YI Dan-qing(易丹青)1, 2, YANG Sheng(杨胜)1, 2, DENG Bin(邓斌)1, ZHOU Ming-zhe(周明哲)1
1. School of Materials Science and Engineering, Central South University, Changsha 410083, China;
2. Key Laboratory of Non-Ferrous Metals, Material Science and engineering,
Ministry of Education, Changsha 410083, China
Received 15 July 2007; accepted 10 September 2007
Abstract: The influences of pre-strain on the mechanical property and fatigue crack growth of 2E12 aluminum alloy were evaluated by SEM, TEM, mechanical property and fatigue tests. The axial fatigue tests were conducted under a constant amplitude sinusoidal wave loading at stress ratio of 0.1 in laboratory air and salt fog at room temperature. The results show that the yield stress of pre strain material is higher than that of the material without undergoing pre-strain, but pre-strain can not make the increase of the growth rate of fatigue crack. Fatigue crack growth rates of the alloy in salt fog are higher than those in air. The increased fatigue crack growth of the alloy in a given environment and more brittle striations can be observed in salt fog.
Key words: 2E12 aluminum alloy; pre-strain; fatigue crack growth; salt fog
1 Introduction
With the development of civil and military aircraft, the increasing emphasizes is about the ability of the aircraft’s structure to maintain damage tolerance and fatigue property in different environments. 2524 aluminum alloy is the relatively new aluminum alloy as a fuselage skin replacement for 2024 skin sheet and is currently used in the Boeing 777 aircraft[1-4]. 2E12 aluminum alloy is the newest anti-fatigue damage aluminum alloy of China, which is developed based on 2524 aluminum alloy.
Pre-strain is an important method to improve the mechanical property of aluminum alloy[2-3]. Though pre-strain can improve the yield stress and tensile stress of alloy, the growth rate of fatigue crack can increase for the smaller plastic zone size and less crack closures[5]. Aluminum aircraft structures are susceptible to corrosion and fatigue damage. Interaction between corrosion and fatigue may represent a serious threat for integrity of the air craft become older[6-7].
In this study, the influence of pre-strain on cyclic stress amplitude-controlled fatigue crack growth of 2E12 aluminum alloy in air and salt fog was investigated. The fatigue crack growth mechanism and corrosion fatigue mechanism were discussed.
2 Experimental
The samples were rolled plates with 2 mm in thickness. The specimens were machined according to the ASTME 647-93 for the fatigue crack growth, all specimens were cut in longitudinal orientation relative to the rolling direction.
Table 1 Chemical composition of 2E12 alloy (mass fraction%)

Fatigue tests were conducted at 10 Hz in air of 40%-60% relative humidity and at 5 Hz in salt fog (3.5% NaCl solution) at 25 ℃ in MTS servohydraulic mechanical test machine. Fatigue loading was in stroke control and tension-tension (R=0.1). Cracks on the specimens were initiated and separated by using drops of ink to the surface, crack lengths were measured at intervals in fatigue test by optical microscopy. TEM observation was carried out with Philips F-20 TECNAI G2, 200 kV transmission electron microscope.
3 Results and discussion
3.1 Microstructure
The TEM images are shown in Fig.1. The T (Al20Cu2Mn3) phases with size from 0.2 to 0.6 μm were found in the grains (Fig.1(a)), with a few decorated at the grain boundaries(Fig.1(b)). There are some round second-phase iron-rich intermetallics. The coarse second-phase particles serve as potential sites for void nucleation during fatigue deformation. After pre-strain in Fig.1(b), more dislocations are observed within the grain interior.
3.2 Fatigue crack growth
Fig.2(a) shows the effect of pre-strain compared with T4 condition on da/dN in the applied stress intensity factor range. The results show that the pre-strain increase the crack growth mainly at the early propagation stage. When the stress intensity factor is less than 15 MPa?m1/2, the crack growth rates of alloys after pre-strain are faster than that those in T4 condition. When the ΔK is higher than 15 MPa?m1/2, the crack growth rates of all samples are similar. That is, at the high stress intensity factor, the effect of pre-strain is weaker.
From Fig.2(b) it can be seen that, the fatigue crack growth in salt fog is faster than that in air, crack growth rates of pre-strain and T4 condition in salt fog are very similar.
The fracture surfaces were studied by scanning electron microscopy. Fig.3(a) shows the fracture after fatigue at ΔK=7 MPa?m1/2 in air, the fracture mode is rough and ductile with cracking along crystallographic plate. With the growth of fatigue crack, the stable crack growth (Fig.3(b)) is comprised of pockets of striations and fine microscopic cracks along the crystallized grain boundaries. The even striations (Fig.3(c)) shows the stable growth of the crack. The overload region (Fig.3(d)) is comprised of cracked particles, isolated pockets of voids with variable size and shape[8-9].
The fracture surfaces of alloys after pre-strain (shown in Fig.4) are very similar to those of samples undergoing T4 condition. Striations and fine microscopic crack are observed.
The fracture surface morphology of alloy (shown in Fig.5) in salt fog differs substantially from specimens tested in air. The striations in corrosion fatigue are rough and jagged. These brittle striations and corrosive pits are typically observed on fatigue crack surfaces[10-11].
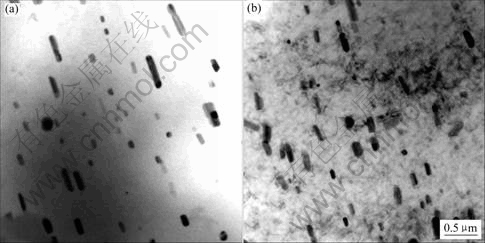
Fig.1 TEM images of 2E12 alloy: (a) T4 condition; (b)10% pre-strain
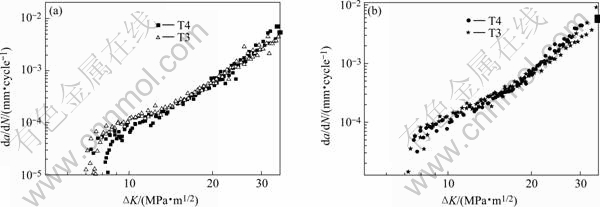
Fig.2 Fatigue crack propagation rates of samples after T4 and T3 treatments in different environments: (a) Air; (b) Salt fog
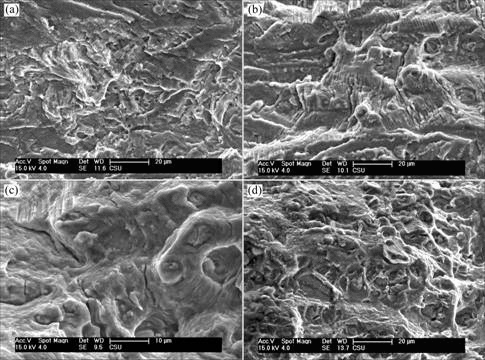
Fig.3 SEM images showing fracture surface of 2E12 specimen at different stress intensity factors: (a) ΔK=7 MPa?m1/2; (b) ΔK=20 MPa?m1/2, low magnification; (c) ΔK=20 MPa?m1/2, Higher magnification; (d) Shear zone
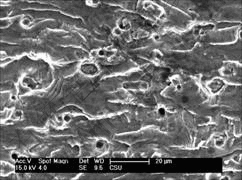
Fig.4 Fracture surface morphology of 2E12 specimen after pre-strain at ΔK=20 MPa?m1/2 in air
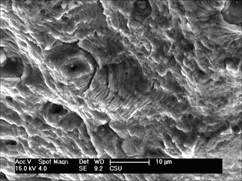
Fig.5 Fracture surface morphology of 2E12 specimen at ΔK=20 MPa?m1/2 in salt fog
3.3 Fatigue crack growth mechanics
The yield strength after pre-strain is from 329 to 375 MPa. The higher yield strength of pre-strained materials has a smaller monotonic plastic zone size(rp)[5]:
(1)
According to Eqn.(1), the plastic zone size should be about 20% smaller in the pre-strained material. In view of the smaller plastic zones in the pres-trained materials, less plastic deformation would be left in the wake of crack tip, then the crack growth rates could be increased. According to the results of experiments, the fatigue crack growth of the specimen after pre-strain is similar to that of specimen after T4 treatment.
The strain energy density factor was proposed in the early 1970 s; the theory has been employed successfully to analyze numerous problems in many fields. Based on the strain energy density the sequence of fatigue crack growth in structure can be illustrated in Fig.6[12]. Strain energy density of pre-strain was similar to that of T4 condition, so the energy of fatigue crack growth was similar to that under T3 and T4 conditions.
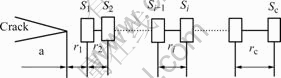
Fig.6 Illustration of fatigue crack propagation
3.4 Fatigue crack growth mechanics in salt fog
The proposed explanation of fatigue crack growth in salt fog is based on the sequential embrittlement process, which is shown in Fig.7. When the gaseous phase responsible for the corrosion fatigue in salt fog reaches the crack tip, gaseous hydrogen arising from reaction is adsorbed on the metallic surface and chemically dissociated in atomic hydrogen. Subsequently, hydrogen entered the material and caused the embrittlement by dislocation movement. At the same time, corrosion environment accelerates the anodic dissolution, these corrosion pits increase the growth rates of fatigue crack[13, 15]. So the hydrogen embrittlement and anodic dissolution are the key factors that affect fatigue crack growth in salt fog.
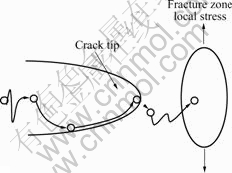
Fig.7 Illustration of hydrogen embrittlement[13-14]
4 Conclusions
1) The yield stress of pre-strain material is higher than that of the material without pre-strain. But pre-strain does not increase the growth rate of fatigue crack.
2) Fatigue crack growth rates in salt fog are faster than that in lab air. Furthermore, the fractographic features, such as small crystallographic face of micro-crack growth, fatigue striation of macro-crack growth and microstructure of shear zone reflect the fatigue crack growth behaviors of alloy in a given environment, more brittle striations are observed in salt fog than in air.
3) The increased crack growth rates in salt fog are due to a combination of hydrogen embrittlement and anodic dissolution at the crack tip.
References
[1] WILLIAM C, JOHN L, JAMES T. Aluminum alloys for aircraft structure[J]. Advanced Materials Processes, 2002, 160(12): 27-29.
[2] MANABU N, TAKEHIKO E. New aspects of development of high strength aluminum alloys for aerospace applications[J]. Materials Science and Engineering A, 2000, A285(1): 62-68.
[3] STARKE E A, STALEYT J T. Application of modern aluminum alloys to aircraft[J]. Prog Aerospace Sci, 1996, 32(2/3): 131-172.
[4] HOFFMAN M E, HOFFMAN P C. Corrosion and fatigue research structural issues and relevance to naval aviation[J]. International Journal of Fatigue, 2001, 23(1): 1-10.
[5] SCHIJCE J. The effect of pre-strain on fatigue crack growth and crack closure[J]. Engineering Fracture Mechanics, 1976, 8: 575-581.
[6] ZHANG W L, RUAN SH L, WOLFE D A, et al. Statistical model for intergranular corrosion growth kinetic[J]. Corrosion Science, 2003, 45: 353-370.
[7] VALERIE G L, GEORGES M K. Localized corrosion of 2024-T351 aluminium alloy in chloride media corrosion[J]. Corrosion Science, 1999, 41: 421-438.
[8] MERATZI A. A study of nucleation and fatigue behavior of an aerospace aluminum alloy 2024-T3[J]. International Journal of Fatigue, 2005, 27: 34-44.
[9] PEDRO M G P, PAULO F P, PAULO M S T. Fatigue striation spacing and equivalent initial flaw size in Al 2024-T3 riveted specimens[J]. Theoretical and Applied Fracture Mechanics, 2005, 43(1): 89-99.
[10] RUIZ J, ELICES M. Effect of water vapour pressure and frequency on fatigue behavior in 7017-T651 aluminum alloy plate[J]. Acta Mater, 1996, 45(1): 281-293.
[11] TANGUY D, BAYLE B, DIF R. Hydrogen effects during IGSCC of pure Al-Mg alloy in NaCl media[J]. Corrosion Science, 2002, 44: 1163-1175.
[12] ZUO J Z, KERMANIDIS Al. Th, PANTELAKIS Sp G. Energy density prediction of fatigue crack growth from hole of aging aircraft structure[J]. Theoretical and Applied Fracture Mechanics, 2002, 38: 37-51.
[13] KERMANIDIS A T, PETROYIANNIS P V, PANTELAKIS S G. Fatigue and damage tolerance behavior of corroded 2024 T351 aircraft aluminum alloy[J]. Theoretical and Applied Fracture Mechanics, 2005, 43: 121-132.
[14] THAKUR A, RAMAN R, MALLHOTRA S N. Hydrogen embrittlement studies of aged and retrogressed-reaged Al-Zn-Mg alloy[J]. Materials Chemistry and Physics, 2007, 101: 441-447.
[15] KIMBERLI J, DAVID W. Prior corrosion and fatigue of 2024-T3 aluminum alloy[J]. Corrosion Science,2006, 48(10): 3109-3122.
Foundation item: Projects(2005CB623705) supported by the National Basic Research Foundation of China
Corresponding author: YANG Sheng; Tel: +86-731-8830092; E-mail: csuyangsh@yahoo.com.cn
(Edited by CHEN Wei-ping)