J. Cent. South Univ. (2017) 24: 2605-2612
DOI: https://doi.org/10.1007/s11771-017-3674-7

Transmission loss simulation based on rectangular-pulse method and experimental evaluation of acoustic performance of perforated intake pipe
LI Heng(李恒), HAO Zhi-yong(郝志勇), ZHENG Xu(郑旭), LIU Lian-yun(刘联鋆)
College of Energy Engineering, Zhejiang University, Hangzhou 310027, China
Central South University Press and Springer-Verlag GmbH Germany, part of Springer Nature 2017
Abstract: Exact simulation of the acoustic performance is essential to the engineering application for a vehicle intake system. The rectangular-pulse method based on the computational fluid dynamics approach was employed for calculating the transmission loss. Firstly, the transmission loss of the single-cavity element was simulated without any airflow, and the effects of different structural parameters on the acoustic performance were investigated comprehensively. Secondly, the static transmission loss of the perforated intake pipe was obtained by the rectangular-pulse method, which is proved to be accurate enough compared with the result by finite element method. Thirdly, under the different conditions of the mean airflow and the operating temperature, the specific transmission loss was acquired respectively. In general, the peaks of the transmission loss are shifted to the lower frequency range because of the reverse airflow, but the amplitudes are irregularly changed. Besides, when the operating temperature increases, the peaks are shifted to the higher frequencies. Finally, with the designed perforated pipe installed to the intake system, the road tests were proceeded to evaluate the actual acoustic performance, and the result indicates that the intake sound pressure level is greatly attenuated. Typically in the range of 600–1500 Hz, the insertion loss of the intake noise at the decelerating moment is almost 20 dB(A), and the overall noise is reduced more than 14.2 dB(A). In conclusion, the perforated intake pipe has been proved excellent in improving the acoustic performance of intake system and could provide the guidance for the automotive engineering application.
Key words: perforated intake pipe; rectangular-pulse method; transmission loss; mean flow; temperature; road test
1 Introduction
The vehicle turbocharger runs in a high speed and generates the high-frequency noises heard as abnormal sound, which seriously influences the sound quality and the riding comfort inside the vehicle [1, 2]. The turbocharger consists of the turbo and the compressor in general. The noises generated by the turbo could be attenuated by the exhaust muffler, but the compressor-induced noises would be radiated to the engine compartment straightly through the intake nozzle, especially shown as the high-frequency noises. So, it is particularly essential to improve the acoustic performance of the intake system [1]. The most important work should be done in two fields: design of an effective muffler and acoustic performance analysis.
A variety of mufflers are widely used in the intake system, e.g., expansion chamber and side branch silencer. In the area of attenuating the turbocharger-induced noise, some typical mufflers were presented in Refs. [3, 4]. The Helmholtz resonator constituted of multiple cavities was designed by LEE [5], which was proved excellent in acoustic performance. However, those mufflers were all used at the outlet of the compressor to reduce the radiation noise of the connecting pipe. LIU [6] proposed the perforated muffler with the sound absorbing material inside. The filled material might probably be washed by the airflow, which would lead to the different acoustic performance. Besides, the shape size of the muffler is a little large, so it could not be the best choice for engineering. Therefore, we aim to design a smaller silencer in the intake system to meet the demand of specific noise attenuation.
In the other field, the acoustic performance of the intake system has widely been investigated on the noise reduction (NR), transmission loss (TL) and insertion loss (IL). As the structure of the acoustical element is increasingly complex, the plane-wave theory [7] is not appropriate for acoustical analysis. Considering the mean airflow, the heat transfer and the viscous dissipation in a duct, the computational fluid dynamics (CFD) approach was proposed. BROATCH et al [8] employed the CFD approach to simulate the TL of various mufflers with mean airflow and the results were validated by experiment. From then on, the CFD approach was developed in the field of acoustic performance simulation. XU et al [9], SHI et al [10] and LIU et al [11] simulated the acoustic performance of the perforated exhaust muffler by CFD approach. Nevertheless, they had not evaluated the actual performance through the road test or the bench test. LIU et al [12] analyzed the TL with mean flow of a certain muffler used at the outlet of the compressor. Accordingly, the bench test was proceeded with the muffler attached to an engine. During the measurement, the pipe connecting the compressor and the intercooler was cut off so that the noise could be measured easily. Undoubtedly, the working condition of the engine was different from the reality, so the acoustical evaluation would not be accurate at all. So we put forward the road test for evaluating the actual acoustic performance of the perforated intake pipe.
In this work, the rectangular-pulse method based on the CFD approach is employed for simulating the acoustic performance. The acoustical effects of different structural parameters are investigated. Then, the perforated intake pipe is designed and the TL is obtained validated by the finite element method (FEM). Subsequently, the TL with mean airflow is analyzed numerically, as well as that with different operating temperatures. Finally, the road test is proceeded to evaluate the actual acoustic performance, and the results of several working conditions are acquired and analyzed comprehensively.
2 Rectangular-pulse method in transmission loss simulation
TL is widely employed as the evaluation of acoustic performance not considering the sound source and the acoustical termination [13]. So, TL could be the parameter showing the acoustic performance of a certain element itself, and it is modeled as
(1)
where LWi represents the incident sound pressure level (SPL), and LWt represents the transmitted SPL; pi+ denotes the incident sound pressure of the inlet, and pt denotes the transmitted sound pressure of the outlet; Si is the cross-section area of the inlet, and St is the cross-section area of the outlet.
The structure of single-cavity perforated element is shown in Fig. 1. The equivalent diameter of the main duct is 76 mm, the thickness of the wall is 2.5 mm, and the volume of the cavity is 296 mL. There are totally 25 holes evenly located in the contact area, and the diameter of the holes is 6 mm. The cavity performs as a side branch silencer connecting to the main duct through the perforation. And the sound wave inside would be attenuated at the specific frequencies once the air is resonated in the cavity.
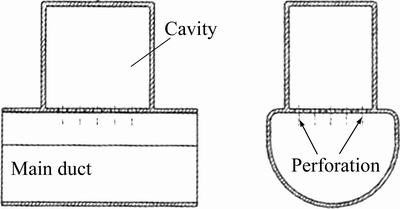
Fig. 1 Structure of single-cavity perforated element
2.1 CFD model and boundary condition setup
Based on the 3-dimensional CFD approach, the second-order discrete format is adopted in numerical simulation, and the time step size is set up as 5 μs. As the Nyquist sampling theorem [9, 11] showed, the maximum analysis frequency could reach 10 kHz, meeting the demand of spectral analysis. The CFD model of the single-cavity perforated element is shown in Fig. 2. The average size of the discrete elements is about 6 mm. During the simulation, the ideal gas is preferred as the medium inside, and the energy transfer between the medium is considered as well. Actually, the laminar model is employed in calculating the fluctuating pressure of the measuring section in the condition of no airflow.
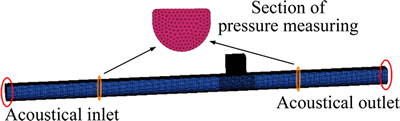
Fig. 2 TL calculating CFD model of single-cavity perforated element
To prevent the reflected wave disturbing the transmitted wave on the outlet [14], the outlet duct is extended to 0.6 m along the normal direction of the cross section with the measuring section being positioned at 0.4 m away from the outlet panel. Accordingly, the inlet duct is extended to 0.9 m with the measuring section being positioned at 0.4 m away from the inlet panel as well. And both of the inlet and outlet panel are set up as anechoic terminations. In many literatures [9–12], only one measuring point was adopted to obtain the fluctuating pressure, which would of course enlarge the calculation error. So in this work, the area-average pressure of the measuring section is used as the inlet or outlet fluctuating pressure. The inlet boundary condition (BC) is set up as the rectangular pulse signal of the transient Mach (Ma). Especially, the pulse amplitude of inlet Ma is 0.04 lasting 160 μs, and the Ma keeps zero at other moments. Besides, the wall is set up as adiabatic and no-slip with the constant temperature at 300 K.
2.2 Acoustic performance on structural parameters
To gain the effects of different structural parameters on the acoustic performance, the cavity, the diameter of the holes, and the number of the holes of are changed respectively. In different cases, the specific parameters of the single-cavity perforated element are listed in Table 1. Accordingly, the TL in each case would be obtained, and the specific change would be proved to provide the engineering guidance of designing and optimizing the perforated intake pipe following.
Table 1 Structural parameters of single-cavity perforated element in different cases
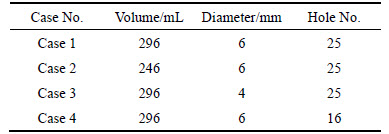
2.3 Result and analysis of TL
When the simulation is converged, the area-average fluctuating pressures of both inlet and outlet measuring sections could be obtained in time domain. Then the incident and the transmitted sound pressure could be achieved by fast Fourier transform (FFT) in frequency domain. Finally, based on Eq. (1), the TL in each case mentioned above is shown in Fig. 3. It indicates that with the decreasing of the cavity volume, the frequency of TL peak is moved to higher range, but the TL peak is slightly lower. When the diameter of the holes is smaller or the number of the holes is reduced, the frequency of TL peak is moved to lower range. Apparently, the TL peak is a little bit lower as well, and the frequency range of noise attenuating is evidently narrower. In conclusion, the different structural parameters could lead to different acoustic performance, which could be the guidance of designing the perforated intake pipe.
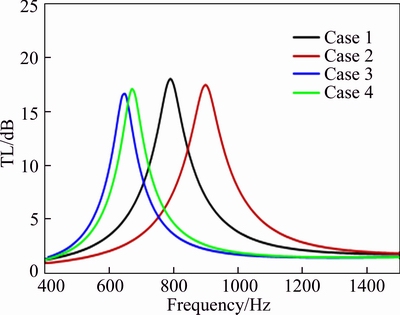
Fig. 3 TL of single-cavity perforated element with different structural parameters
3 Perforated intake pipe design and TL calculation
According to the results from Section 2.3, the optimum diameter of the holes, the number of holes, and the volume of each resonant cavity are confirmed. The designed perforated intake pipe is shown in Fig. 4. The four resonant cavities are set apart by the baffles inside, and each resonant cavity is defined from Cav.1# to Cav.4#, respectively along the direction of the intake airflow. The structural parameters of the four cavities are listed in Table 2.
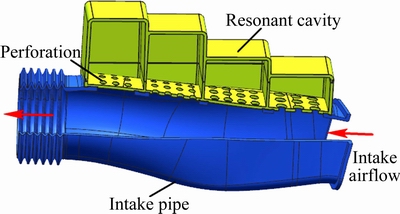
Fig. 4 Structure of perforated intake pipe
Table 2 Structural parameters of four resonant cavities of perforated intake pipe
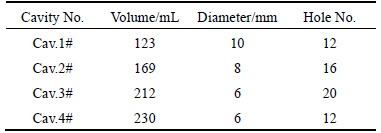
3.1 CFD model and boundary condition setup
Actually, the airflow could not be neglected in working condition of an engine, so the standard k–ε model is employed to simulate the TL of the perforated intake pipe with mean flow. Two main steps are included during simulating. Firstly, the constant Ma is set up both on the inlet and the outlet panels to complete the steady state simulation. And it is essential that the actual propagating directions of the sound wave and the intake airflow are opposite, so the acoustical inlet equals the airflow outlet. Secondly, when the steady state simulation is converged, the inlet BC is set up as the rectangular pulse on the basis of the constant Ma. During the transient state simulation, the area-average fluctuating pressures of both inlet and outlet measuring sections could be obtained accordingly. The TL calculating model of the perforated intake pipe is shown in Fig. 5.
As to study the influences of the operating temperature on the acoustic performance, an additional investigation is proceeded. The laminar model is adopted in simulating but without the airflow. During simulating, various cases of different temperatures are proposed regardless of the temperature gradient change. And the wall is set up as adiabatic and no-slip.
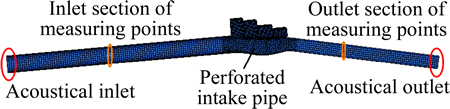
Fig.5 TL calculating CFD model of perforated intake pipe
3.2 Result and analysis of TL
The simulated TL by CFD approach without airflow is shown in Fig. 6. And in comparison with the TL by finite element method (FEM), the results fit well in trend. Furthermore, the four peaks are shown at several frequencies, i.e., 590, 770, 950, and 1190 Hz, respectively. Clearly, with the analysis in Section 2.3, the TL peak is corresponded with each single cavity individually. In the frequency range of 600 Hz to 1300 Hz, the average TL is about 12 dB, and some peaks reach as high as 25 dB, e.g. at 950 Hz and 1190 Hz. Actually, the designed perforated intake pipe matches the initial goal of noise attenuating well. However, the CFD results are always slightly lower than the FEM results nearly in the whole frequency range. And the frequency of the 3rd peak is shifted a little bit lower than that of FEM approach. In detail, the exact frequency of CFD approach is 950 Hz, but it is 980 Hz of FEM approach. The deviations might be mainly attributed to the neglect of the viscous dissipation by FEM [15], but it is considered in simulation by CFD approach. In conclusion, the simulated TL by rectangular-pulse method based on CFD approach is precise enough with the validation by FEM approach.
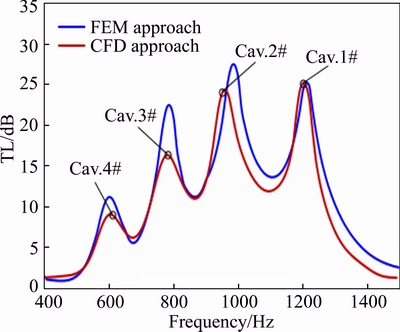
Fig. 6 TL without mean flow of perforated intake pipe
Three mean flow cases are analyzed in this study, and Ma is defined as follows, i.e. 0.05, 0.10, and 0.15, respectively. The TL of each case is shown in Fig. 7. As a whole, the TL curve is moved a lot under the influence of mean flow. Due to the reverse flow function, each TL peak is shifted to the lower frequency range. Furthermore, the higher the frequency is, the more it is moved. As the Doppler effect showed [7], the speed of sound waves is reduced by the reverse flow existed in the duct. So, the TL peak of an element would be shifted to the lower frequency area according to one-dimensional (1-D) plane wave propagation theory [7]. In general, the average TL is higher in amplitude with mean flow, which is mainly caused by the enhancing dissipation effect of the perforated structure. On the other hand, the air-induced broadband noise would appear with the airflow existing in the intake pipe, and it would lead to the differences irregularly. Of course, the spectral changing trend of the TL peaks should be provided as the guidance of determining the attenuated frequency band.
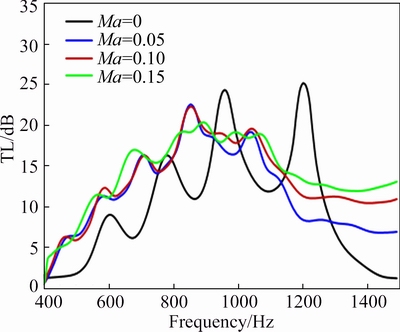
Fig. 7 TL with mean flow of perforated intake pipe
Considering the influence of different operating temperatures, the TL is analyzed accordingly without mean flow. And it contains four cases with the temperature from 300 K to 345 K, every 15 K a step. The TL curves are shown in Fig. 8. Apparently, as the operating temperature increases, the TL peaks are shifted to the higher frequency range. However, little is changed in amplitude, which indicates that the temperature may not be the positive factor in noise attenuating. As known to us, the state equation would be obeyed when the sound wave transmits in the ideal gas. And the square of the sound speed is proportional to the absolute temperature of the operating environment [12]. So, when the temperature is increased, the sound speed is faster, and in result, the TL peaks of the perforated pipe would be shifted to the higher frequency.
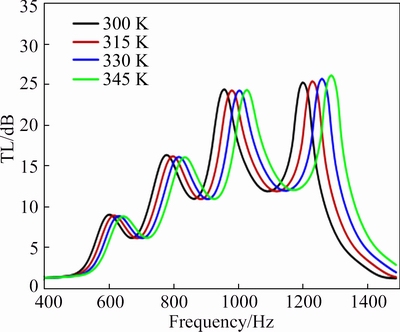
Fig. 8 TL with different temperatures of perforated intake pipe
4 Road test and acoustical evaluation
The perforated intake pipe is equipped in the correct position of the intake system. Then the road tests are proceeded with and without the perforated pipe. In the following, the case without the perforated pipe is defined as original case, and the case with this pipe is defined as optimized case. During the road tests, all the intake noise are obtained accordingly, and the two total working conditions are chosen, i.e., the acceleration with mid-high load, and the acc.-deceleration with high load.
4.1 Intake noise of accelerating condition
A certain turbocharged gasoline vehicle is adopted for the road test, and the intake noise spectrum of the specific accelerating condition is shown in Fig. 9. Compared with that in the original case, the intake noise is shown lower in almost the whole frequency range. When the engine speed is accelerated from 1000 r/min to 3800 r/min, the SPL is reduced heavily at each frequency from 600 Hz to 3000 Hz. Especially when the engine speed is under 2100 r/min, the intake noise is mostly obviously attenuated. And in the range from 600 Hz to 1500 Hz, the highest SPL is reduced from 73 dB(A) to 62 dB(A), which is consistent with the acoustic performance of the perforated intake pipe itself. Actually, in the frequency range of higher than 1500 Hz, the intake noise is slightly attenuated as well. In fact, when analyzing the TL of the pipe, the cut-off frequency is set up as 1500 Hz, but there would be some more peaks in the higher area called order peaks. So in other range, the intake noise is also well smoothed. Besides, the narrow band noise signed in Fig. 9(a) should be the squeaking noise related to the operating of the turbocharger.
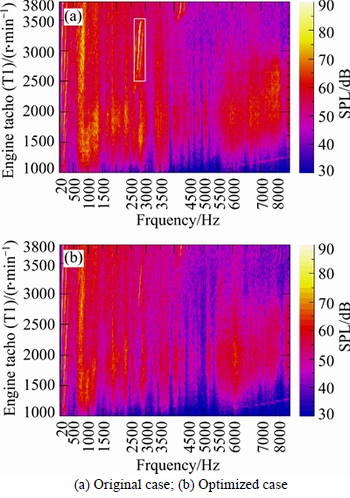
Fig. 9 Intake noise spectrum of accelerating condition:
Based on the intake noise spectrum, the A-weighted overall of SPL is achieved accordingly. Actually, the insertion loss (IL) is always used to evaluate the real acoustic performance of a muffler [7], which indicates the difference between the original and the optimized SPL of the intake noise. The overall and the IL are shown in Fig. 10. In the whole range of engine speed from 1000 r/min to 3800 r/min, the intake noise has been greatly attenuated compared with the original one. With the help of the perforated intake pipe, the average IL could reach as high as 3.5 dB(A). Especially when the engine speed is 3200 r/min, the IL is as high as 7 dB(A). As a result, the designed perforated pipe is proved effective in practical application through the road test. However, the optimized overall is fluctuated slightly at the specific speed range, i.e., 1300–1600 r/min. It might be mainly attributed to the environment factors, e.g. the uneven ground in the road test.
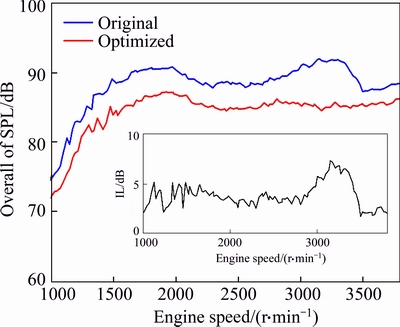
Fig. 10 Overall of intake noise of accelerating condition
4.2 Intake noise of acc.-decelerating condition
When the accelerator is suddenly loosed during the accelerating condition of a vehicle, the opening of the throttle would be smaller because the airflow is dropped sharply in demand. Actually, the turbocharger is still working in high speed due to the effect of inertia. At that moment, it is essential to reduce the pressure in the chamber of the turbocharger, so the electromagnetic relief valve is used. When the valve is instantaneously opened, the air flows from the turbocharger to the intake pipe with high velocity, which could lead to the broadband noise called aerodynamic noise [16]. As it appears in the transient conditions, e.g., the sudden deceleration, the broadband noise is terribly annoying so that it would greatly affect the interior sound quality of the vehicle in general. So, the road test is proposed with/without the perforation intake pipe installed, and the intake noise is typically obtained. The spectra of the intake noise with the specific engine speeds, e.g.,2000 r/min and 2500 r/min, are respectively shown in Fig. 11 and Fig. 12. The 2000 r/min denotes that the accelerator is loosed suddenly when the engine speed is accelerated to 2000 r/min, so does the 2500 r/min.
As seen both in Figs. 11 and 12, the broadband noise of the turbocharger obviously exists in the frequency range, i.e., 600–1500 Hz. The SPL peak reaches 93.5 dB(A) in the original case of 2000 r/min, and the peak of 2500 r/min is 91.8 dB(A). Actually when the frequency is lower than 600 Hz or higher than 1500 Hz, there are pieces of broadband noise as well. Especially in the case of 2500 r/min, the noise is shown apparent in the additional range, i.e., 1500–3000 Hz compared with that of 2000 r/min. The most possible reason is that the engine noise is highlighted with the higher speed of 2500 r/min, which covers up the aerodynamic noise. So in Fig. 13(a), the broadband noise is shown smoother than that in Fig. 12(a). However, in the optimized cases with the perforated intake pipe installed, the intake noises are obviously attenuated. In the range of 600–1500 Hz, the SPL peaks are dropped to 79.5 dB(A), and 79.2 dB(A) in the cases of 2000 r/min and 2500 r/min, respectively. Besides, a few pieces of broadband noise are still left in the range of 600–1500 Hz, as well as in area of the higher frequency. The remaining noise might be part of the tire noise, wind noise, and some other environmental noises.
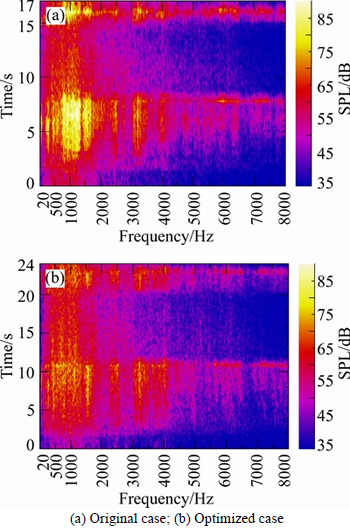
Fig. 11 Intake noise spectrum of acc.-decelerating condition (2000 r/min):
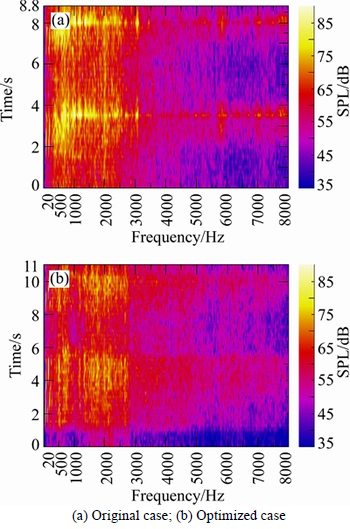
Fig. 12 Intake noise spectrum of acc.-decelerating condition (2500 r/min):
Focusing on the moment of the sudden deceleration, the spectra of the intake SPL are shown in Figs. 13 and 14, respectively, of 2000 r/min and 2500 r/min. With the perforated intake pipe installed, the optimized intake noise is attenuated in general. Especially, the original intake SPL is shown highest in the frequency range of 600–1600 Hz, which should be the broadband noise mentioned previously. When the engine speed is 2000 r/min, the highest SPL reaches 85.4 dB(A), but the peak value drops to 69.7 dB(A) in the optimized case. The average IL is 19.2 dB(A) in the specific frequency band. Also when the engine speed is 2500 r/min, the highest SPL reaches 88.2 dB(A), but the optimized peak drops to 76.8 dB(A). And the average IL is 17.9 dB(A) in the specific frequency band. So the perforated intake pipe has been proved excellent in acoustic performance and the main frequency range corresponds to the analyzed TL in Section 3.2. Besides, the designed pipe is also effective in noise attenuating at other frequencies. However, the acoustic performance is not so good but worse in few frequency ranges, e.g., 4200–4300 Hz of 2000 r/min, 1950–2320 Hz of 2500 r/min and 5980–6350 Hz of 2500 r/min. It might be attributed to the subtle change in the positions of the microphone and the other objective factors like the different operation of the driver in the two tests. Moreover, a local peak appears at 138 Hz of 2000 r/min, similarly the other appears at about 172 Hz of 2500 r/min. The two frequencies are in accordance with the 4th order of the engine firing [17], which proved the validity of the road test. In conclusion, the perforated intake pipe is proved excellent in improving the acoustic performance through the experimental evaluation of the road test, and the acoustical characteristic is consistent with the TL analysis by CFD approach. So the rectangular-pulse method is proved accurate enough in acoustical simulation.
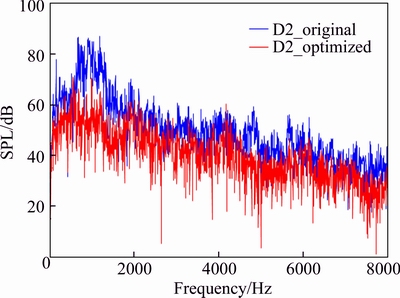
Fig. 13 Intake SPL of acc.-decelerating condition (2000 r/min)
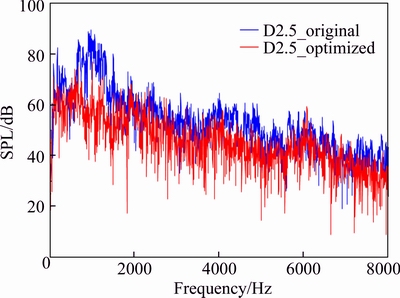
Fig. 14 Intake SPL of acc.-decelerating condition (2500 r/min)
Moreover, the IL of the intake noise is shown in Fig. 15 viewed in 1/3 octave spectrum. In general, the IL of 2000 r/min is slightly higher than that of 2500 r/min, the same as that has been analyzed in Figs. 11 and 12. The IL curves both show that the perforated intake pipe performed most excellently in the frequency range of 630–1600 Hz. The highest IL is 22.9 dB(A) at 800 Hz (the center frequency) of 2000 r/min, and the one of 2500 r/min is 20 dB(A) at 1000 Hz. However, in the low frequency range of 2500 r/min, e.g., 50 Hz, 63 Hz,125 Hz and 500 Hz, the acoustic performance of the pipe is not so good because the most highlight noise should be the structure-induced noise of the engine itself.
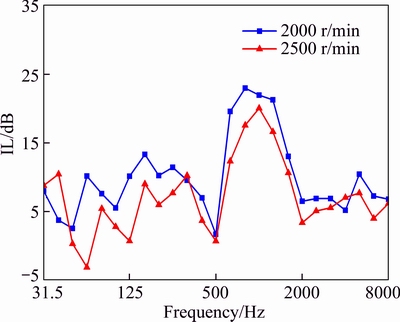
Fig. 15 IL of intake noise at decelerating moment
In practical application of automotive engineering, the overall and the order noise are acquired to straightly evaluate the acoustic performance of the perforated intake pipe, and the noise values at the decelerating moment are listed in Table 3. Obviously, both the overall and the order noise are greatly attenuated. Typically, the IL of the overall noise is 18.2 dB(A) of 2000 r/min, and 14.2 dB(A) of 2500 r/min. However, the 2nd order noise is not well-performed at all. Even when the engine speed is 2500 r/min, the intake SPL is a little bit increased. Since the 2nd order noise is mainly attributed to the engine noise itself, the intake noise is not most distinguished in general. From Table 3, the perforated pipe has been proved excellent in noise attenuating, which should be provided for engineering application.
Table 3 Overall and order noise of intake SPL of acc.- decelerating condition
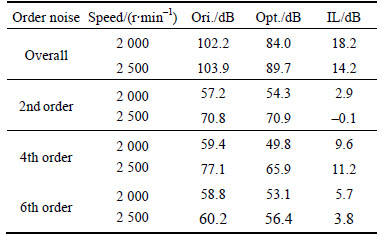
5 Conclusions
The perforated intake pipe has been designed for improving the acoustic performance of the intake system, which is more space-saving compared with the widely used side branch silencers so far. It has been analyzed numerically and experimentally, and the conclusions of the current work can be summarized as follows:
1) Methodologies, i.e., the rectangular-pulse method based on CFD approach, are employed to simulate the TL. And the TL shows good agreement with the result by FEM approach in general, which proves the accuracy of the CFD approach in TL simulation.
2) The frequency of the TL peak is related to the volume of the cavity, the diameter and the number of the holes. The reasonable selection of such parameters would help to provide guidance for improving the acoustic performance. Moreover, with the reverse airflow, the TL peaks are shifted to the lower frequency, and the higher the frequency it is located, the farther the interval it is moved. Besides, when the operating temperature increases, the TL peaks are shifted to the higher frequency range.
3) The road test is proceeded in order to evaluate the acoustic performance of the perforated pipe. The test result shows that the intake noise has been well attenuated, especially in the frequency range of 600– 1500 Hz corresponding to the target frequency range of design.
4) To sum up, the designed perforated intake pipe has been proved excellent in improving acoustic performance. And it remains further studies on the experimental TL with the mean airflow, as well as the treatment of the objective factors in the road test.
References
[1] PEAT K S, TORREGROSA A J, BROATCH A, FERNANDEI T. An investigation into the passive acoustic effect of the turbine in an automotive turbocharger [J]. Journal of Sound and Vibration, 2006, 295: 738–756.
[2] VIVEK K, VEERAMANI K, PAWAN T, TIWARI A, MANOJ P N. Optimization of an air intake system to reduce multiple whoosh noises from an engine [C]// SAE, 2013-01-1714, 2013.
[3] TROCHON E P. A new type of silencers for turbo charger noise control [C]// SAE, 2001-01-1436, 2001.
[4] GRAEFENSTEIN A J, WENZEL W. “Herschel-quincke spiral” a new interference silencer [C]// SAE, 2003-01-1722, 2003.
[5] LEE I J, SELAMET A, KIM H. Design of a multi-chamber silencer for turbocharger noise [C]// SAE, 2009-01-2048, 2009.
[6] LIU Li-yuan, JI Zhen-lin. Design of turbocharged engine intake silencers and numerical analysis for their acoustic performance [J]. Journal of Vibration and Shock, 2011, 30(10): 193–196. (in Chinese)
[7] MUNJAL M L. Acoustics of ducts and mufflers with application to exhaust and ventilation system design [M]. New York: Wiley, 1987.
[8] BROATCH A, MARGOT X, GIL A. A CFD approach to the computation of the acoustic response of exhaust mufflers [J]. Journal of Computational Acoustics, 2005, 13(2): 301–316.
[9] XU Hang-shou, JI Zhen-lin, KANG Zhong-xu. Three-dimensional time-domain computation method of resistant muffler transmission loss [J]. Journal of Vibration and Shock, 2010, 29(4): 107–110. (in Chinese)
[10] SHI Yan, SHU Ge-qun, BI Feng-rong. Acoustic characteristics simulation of engine exhaust muffler based on CFD [J]. Journal of Vibration Engineering, 2011, 24(2): 205–209. (in Chinese)
[11] LIU Che, JI Zhen-lin, XU Hang-shou. Three-dimensional Time-domain Computation and Analysis of Acoustic Attenuation Performance of Perforated Tube Silencers [J]. Journal of Mechanical Engineering, 2012, 48(10): 7–13. (in Chinese)
[12] LIU Lian-yun, HAO Zhi-yong, QIAN Xin-yi, HU Xian-feng. Prediction and evaluation of acoustic performance of silencer for turbocharger compressor outlet [J]. Journal of Harbin Engineering University, 2013, 34(2): 197–201. (in Chinese)
[13] LIU Chi, HAO Zhi-yong, CHEN Xin-rui. Optimal design of acoustic performance for automotive air-cleaner [J]. Applied Acoustics, 2010, 71: 431–438.
[14] LIU Lian-yun, HAO Zhi-yong, LIU Chi. CFD analysis of a transfer matrix of exhaust muffler with mean flow and prediction of exhaust noise [J]. Journal of Zhejiang University: Science A (Applied Physics & Engineering), 2012, 13(9): 709–716.
[15] MIDDELBERG J M, BARBER T J, LEONG S S, BYRNE K P, LEONARODI E. CFD analysis of the acoustic and mean flow performance of simple expansion chamber mufflers [J]. ASME Conference Proceedings, 2004, 47152: 151–156.
[16] TOUSSAINT L, MARQUES M, MORAND N, DAVIES P, GROVES C, TOMANEC F, ZATKO M, VLACHY D, MRAZEK R. Improvement of a turbocharger by-pass valve and impact on performance, controllability, noise and durability [C]// 11th International Conference on Turbochargers and Turbocharging. Oxford: Woodhead Publishing, 2014: 137–146.
[17] LIU Lian-yun. Acoustic analysis of ICE intake and exhaust systems by a 3D time-domain pulse method [D]. Hangzhou: Zhejiang University, 2013. (in Chinese)
(Edited by YANG Hua)
Cite this article as: LI Heng, HAO Zhi-yong, ZHENG Xu, LIU Lian-yun. Transmission loss simulation based on rectangular-pulse method and experimental evaluation of acoustic performance of perforated intake pipe [J]. Journal of Central South University, 2017, 24(11): 2605–2612. DOI:https://doi.org/10.1007/s11771-017-3674-7.
Foundation item: Project(51705454) supported by the National Natural Science Foundation of China
Received date: 2016-02-22; Accepted date: 2016-05-23
Corresponding author: ZHENG Xu, PhD; Tel/Fax: +86–571–87953286; E-mail: zhengxu@zju.edu.cn