
Thermal stability and oil absorption of aluminum hydroxide treated by dry modification with different modifiers
ZHOU Xiang-yang(周向阳)1, LI Chang-lin(李昌林)1, HUO Deng-wei(霍登伟)1, 2,
LI Jie(李 劼)1, WU Shang-yuan(伍上元)1
1. School of Metallurgical Science and Engineering, Central South University, Changsha 410083, China;
2. Shandong Branch, China Aluminum Corporation, Zibo 255052, China
Received 31 July 2007; accepted 25 October 2007
Abstract: The thermal stability, particle size and morphology and oil absorption of aluminum hydroxide(ATH) treated by dry modification with three different modifiers were investigated. The experimental results show that the thermal stability of ATH powder is markedly improved by dry modification technology with the following modifiers such as phosphoric acid, polyacrylic acid and the mixture of phosphoric acid and polyacrylic acid. The best effect comes from pure phosphoric acid, and the initial temperature for the loss of crystal water of ATH powder modified with pure polyacrylic acid can reach about 202 ℃ that is approximately 10 ℃ higher than that of ATH powder before modification. The phenomena of agglomeration and macro-aggregate badly exist in ATH powder modified with the modifiers containing phosphoric acid. The growth of particles and agglomerations of powders are not evident in ATH powder modified with pure polyacrylic acid. The oil absorption of ATH powder modified with the modifiers containing phosphoric acid is apparently larger than that of original ATH powder and ATH powder modified with pure polyacrylic acid. The oil absorption of the ATH powder modified with pure polyacrylic acid is slightly smaller than that of original ATH powder.
Key words: aluminum hydroxide; dry modification; polyacrylic acid; thermal stability; oil absorption
1 Introduction
Aluminum hydroxide (ATH) is found to be an increasing consumption in high polymers as flame retardants due to its excellent performances such as flame retardance, smoke suppression, filling, low price and non- toxicity[1-2]. However, ATH’s drawbacks such as lower shaping temperature, higher oil absorption and worse compatibility between ATH and high polymers limit its extensive application in fire resistance fields[3-4].
Many methods are employed to improve the universal flame retardant performances of ATH such as raising thermal stability and reducing oil absorption. The essence of partial dehydration[5] is lowering the apparent molecule quantities of crystal water in ATH to 1.8-2.9 so as to raise the thermal stability of ATH, but the removal of partial crystal water will depress the universal flame retardance performances of ATH. Ultramicronization can availably increase the specific surface area of powder so that the water vapour fractional pressure on the surface of ATH powder decreases and flame retardance efficiency increases. In addition, ultramicronization is an effective way to improve the mechanical property of high polymer products. High purification is usually used to lower the content of ion insoluble substances (especially Na2O) in ATH powder so that the conductivity of ATH powder falls. Nevertheless, ultramicronization and high purification will result in the increase of production cost of ATH powder[6]. Recombination with other synergistic flame retardant agents[7-9] is an available method to improve the universal flame retardant performances of ATH, whereas this method goes against the control of production cost due to the fact that some synergistic agents are more expensive and some recombination technologies are correspondingly complex. Surface modification[10-11] is an effective and simple method to improve the thermal stability of ATH and reduce its oil absorption, which is achieved by the formation of coatings on the surface of ATH particles. Especially, dry surface modification attracts more and more researching interests on account of its advantages such as fewer working steps and almost no emission of three major polluting wastes.
For dry modification of ATH, organic substances such as silicacane, titanate and stearic acid or stearate are accustomed modifiers, which are only effective to improve the compatibility between ATH and high polymers but not evident to enhance the thermal stability of ATH powder[6,10-12]. So, it is necessary to research novel modifiers which can not only increase the thermal stability of ATH powder but also reduce its oil absorption. Some literatures showed that phosphoric acid (H3PO4) can react with aluminum hydroxide and generate phosphate of aluminum such as Al(H2PO4)3 and AlPO4 which have higher thermal stability. As a result, the thermal stability of ATH modified with H3PO4 is improved[13-14]. Additional studies showed that polyacrylic acid (PAA) is available to reform the surface performances of inorganic powder[15,16]. So, H3PO4, PAA and the mixture of H3PO4 and PAA were chosen as modifiers during dry modification process of ATH, and the performances such as thermal stability and oli absorption of modified ATH powder were also investigated in this work.
2 Experimental
2.1 Samples preparation
Main materials used in this study were ATH powder (industrial product from Shangdong Aluminum Co., Shandong Province, China), H3PO4 (concentration of 85%, analytical grade), PAA (concentration of 30%, analytical grade) and deionized water. Main apparatus used in this study were a mixer (maximal rotary speed of 20000 r/min, FW100, Tianjin Taisite Instrument Co. Ltd) and a controlled temperature drier with a maximal temperature of 300 ℃.
The preparation of modified ATH samples can be described as follows. 1) Making up three different modification solutions of 12.5 mL by introducing 2.5 g pure H3PO4, mixture of H3PO4 and PAA(mass ratio of 1?1), pure PAA into deionized water, respectively; 2) Dispersing in batches each modification solution into ATH powder of 50 g by an injector, high speed mixing for 10 min after each injection, and the times of solution injection was 5; 3) Drying the modified powder samples overnight at 120 ℃.
2.2 Testing methods
The initial temperature for the loss of crystal water was used as an indication of thermal stability of powder samples, which was gotten by TGA-DSC on a TA instrument SDT Q600 thermobalance. The testing temperature interval was 25-800 ℃, and the diagrams were obtained with 5 ℃/min heating rate and 100 mL/min linear gas flow rate in air atmosphere.
The oil absorption of powder sample was measured by the following procedure. 1) Drying powder samples at 105 ℃ for 1 h, 2) Taking 5 g dried sample onto the glass board, then adding castor oil into the sample with a burette, meanwhile mixing the oil and powders with glass rod, 3) Stopping the titration of castor oil when the mixture turned to strips and bits, and the mixture could be rolled onto the glass rod with no oil trace on the board. The castor oil absorption per 100 g aluminum hydroxide powders was defined as the oil absorption.
In addition, scanning electron microscopy (SEM, JEOL, JSM5600) was employed to investigate the grain morphology of samples. The structure characteristics of samples were verified by X-ray diffractometer(XRD), with Cu Kα radiation.
3 Results and discussion
3.1 Phase characteristics and thermal stability of powder samples before and after modification
The XRD patterns of samples before and after modification are shown in Fig.1. Obviously, the modification does not change the crystal structure of trihydrate alumina. However, the diffracted intensity of the main diffraction peaks of samples after modification reduces to some extent. For the samples treated with modifiers containing H3PO4, the changes of diffracted intensity may be mainly due to the fact that the surface of ATH particles is closely coated by phosphates of aluminum such as Al(H2PO4)3 and AlPO4 from the reaction between H3PO4 and ATH[14]. On the other hand, there are complicated interactions between PAA and ATH since PAA is an organic weak acid with large steric hindrance groups. PAA is likely to be directly absorbed on the surface of ATH particles to be a coating layer, which is possibly similar to the absorption of PAA on the surface of TiO2 particles[16]. Perhaps, PAA is bonded on the surface of ATH particles by coordinate bond to be surface coat just like the interaction between PAA and Fe3O4[17]. The formation of surface coat may directly lead to the weakening of the diffracted intensity of sample modified with PAA. Thus, it can be concluded that the dry modification is available to form the surface coat which leads to the weakening of the diffracted intensity of modified sample.
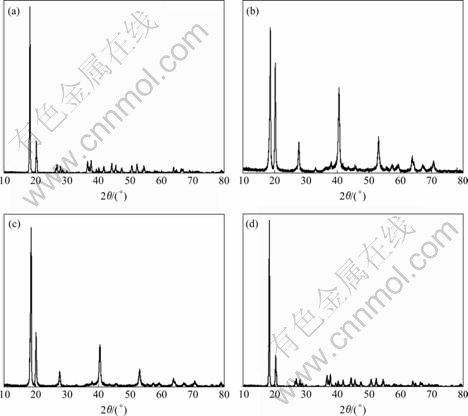
Fig.1 XRD patterns of ATH powder before and after modification: (a) Before modification; (b) Modified with phosphoric acid; (c) Modified with mixture of phosphoric acid and polyacrylic acid; (d) Modified with polyacrylic acid
Fig.2 shows the DSC-TGA curves of the samples before and after modification. The followings can be seen: 1) The shapes of all DSC-TGA curves are almost similar, nevertheless the initial temperature for the loss of crystal water of the all modified samples rises compared with 192 ℃ of the original sample, that is to say, the dry modification used in this study can effectively improve the thermal stability of ATH. This may be attributed to the formation of surface coat. 2) The initial temperature for the loss of crystal water of sample gradually falls with the decrease of H3PO4 content in modifier. For example, the sample modified with pure phosphoric acid has the highest initial loss temperature of 208 ℃ that is higher than 205 ℃ of sample modified with the mixture of H3PO4 and PAA as well as 202 ℃of sample modified with pure PAA. After analyzing the changes of temperature, it can be seen that H3PO4 is more helpful to raising the initial temperature for the loss of crystal water of ATH, which may result from the existence of high thermal stability phosphates of aluminum such as Al(H2PO4)3 and AlPO4 in surface coat.
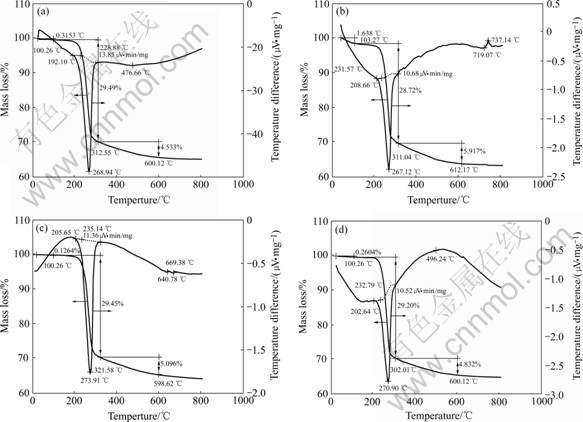
Fig.2 DSC-TGA curves of ATH powder before and after modification: (a) Before modification; (b) Modified with phosphoric acid; (c) Modified with mixture of phosphoric acid and polyacrylic acid; (d) Modified with polyacrylic acid
3.2 Particle size and morphology of powder samples before and after modification
Fig.3 represents the SEM images of powder samples before and after modification. Obviously, agglomeration and macro-aggregate badly exist in ATH powder samples modified with the modifiers containing H3PO4. This may be attributed to the reaction between H3PO4 and ATH. The reaction leads to the formation of phosphates of aluminum which coats on the surface of ATH, as a result, the particle size grows. In addition, the reaction also produces viscous compounds such as Al(H2PO4)3 that can easily connects ATH particles together. Consequently agglomeration and macro- aggregate come into being after powder samples are dried[14].
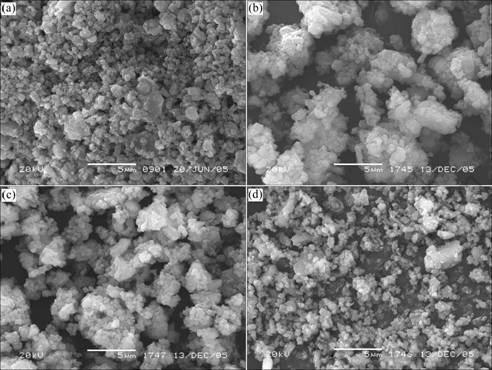
Fig.3 SEM images of ATH powder: (a) Before modification; (b) Modified with phosphoric acid; (c) Modified with mixture of phosphoric acid and polyacrylic acid;(d) Modified with polyacrylic acid
It can be also found that the particle size of ATH powder modified with pure PAA changes very little; and when modifiers contain PAA, the agglomeration is relatively slighter than that in sample modified with pure H3PO4. This may be due to the existence of large steric hindrance groups in surface coat, which can availably prevent the agglomeration during drying process[18-19].
3.3 Oil absorption of powder samples before and after modification
Oil absorption is one of the main factors influencing the application of ATH as flame retardant. The larger oil absorption results in not only higher viscosity in the high polymer slurry but also larger cost[20]. The oil absorption of powder samples before and after modification is given in Table 1.
Table 1 Oil absorption of Al(OH)3 powder before and after modification
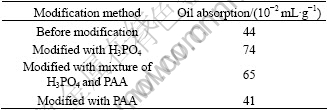
Testing results indicate that the oil absorption of ATH powder modified with the modifiers containing H3PO4 is apparently larger than that of original ATH powder and samples modified with pure PAA. Ref.[21] showed that the dimension of pores existing in powder congeries and surface morphology of powders are the decisive factors to oil absorption of powders. SEM images of samples (Fig.3) show that agglomeration and macroaggregate appear in modified sample when the modifiers contain H3PO4, and the surface of macro- aggregates is very coarse and rugged, even some acuminate protuberances appear as well. And the dimension of pores existing in powder congeries increases with raising the mass of H3PO4 in the modifying agent. These may be main reasons why higher oil absorption exists in powder samples modified with modifiers containing H3PO4.
While being modified with PAA, the oil absorption of sample is slightly smaller than that of original ATH powder. This may be due to the fact that the surface of the sample is relatively lubricous, and the growth of particle and agglomerates of powder are not evident. In addition, the fact that PAA is organic matter may be another reason why the modified sample has smaller oil absorption.
4 Conclusions
1) The thermal stability of ATH powder is markedly improved by dry modification technology with the following modifiers such as H3PO4, PAA and the mixture of H3PO4 and PAA, and modifiers containing H3PO4 are more effective to raise the thermal stability than modifiers without H3PO4.
2) The phenomena of agglomeration and macroaggregate badly exist in ATH powder modified with the modifiers containing H3PO4, but the growth of particles and agglomerates of powder are not evident in ATH powder modified with pure PAA.
3) The oil absorption of ATH powder modified with the modifiers containing H3PO4 is apparently larger than that of original ATH powder. However, the oil absorption of sample modified with pure PAA is slightly smaller than that of original ATH powder.
References
[1] WANG Jian-li, HE Feng-zhi, CHEN Qi-yuan. Preparation, application and development of superfine Al(OH)3 retarder [J]. China Powder Science and Technology, 2007(1): 38-42. (in Chinese)
[2] OU Yu-xiang, FANG Xiao-min. Status and development trends of metal hydroxides based flame retardants [J]. Fine and Specialty Chemicals, 2007, 15(2): 1-4. (in Chinese)
[3] LAURENT C, LAURENT F, ERIC L, JOS?-MARIE L C. Influence of talc physical properties on the fire retarding behavior of (ethylenevinyl acetate copolymer/magnesium hydroxide/talc) composites [J]. Polymer Degradation and Stability, 2005, 88: 504-511.
[4] HUANG Dong, NAN Hai, WU He. Flame retardancy property and application of Al(OH)3 [J]. Development and Application of Materials, 2004, 19(3): 33-37. (in Chinese)
[5] BROWN N, AGGLETON M. Nonhygroscopic thermally stable aluminum hydroxide. US 6280839 B1 [P]. 1999-08-28.
[6] JIA Xiu-wei. Nano flame retardant materials [M]. Beijing: Chemistry Industry Press, 2005: 250-273. (in Chinese)
[7] CROSS M S, CUSACK P A, HORNSBY P R. Effects of tin additives on the flammability and smoke emission characteristics of halogen-free ethylene-vinyl acetate copolymer [J]. Polymer Degradation and Stability, 2004, 79: 309-318.
[8] HAURIE L, FERN?NDEZ A I, VELASCO J I, MARIA C J, JOSE-MARIE L C, FERRAN E. Thermal stability and flame retardancy of LDPE/EVA blends filled with synthetic hydromagnesite/aluminium hydroxide/montmorillonite and magnesium hydroxide/aluminium hydroxide/montmorillonite mixtures [J]. Polymer Degradation and Stability, 2007, 92: 1082- 1087.
[9] HIPPI U, MATTILA J, KORHONEN M, SEPP?L? J. Compatibilization of polyethylene/aluminum hydroxide (PE/ATH) and polyethylene/magnesium hydroxide (PE/MH) composites with functionalized polyethylenes [J]. Polymer, 2003, 44(4): 1193-1201.
[10] NACHTIGALL S M B, MIOTTO M, SCHNEIDER E E, MAULER R S, FORTE M M C. Macromolecular coupling agents for flame retardant materials [J]. European Polymer Journal, 2006, 42(5): 990-999.
[11] SI Ji-chun, ZHENG Shui-lin, LU Mai-xi. Surface modifying and applied research of aluminum hydroxide [J]. China Powder Science and Technology, 2005, 2: 17-20. (in Chinese)
[12] ZHANG Xin-gui, GUO Fen, CHEN Jian-feng, ZHANG Yun-liang CHEN Guo-shu. Dry-modification of nano-Al(OH)3 and its application in EVA [J]. Journal of Beijing University of Chemical Technology, 2005, 32(2): 17-20. (in Chinese)
[13] QIN Wen-qing, LI Feng. Flame retardant technology of material surface coating [M]. Beijing: Chemistry Industry Press, 2004: 39. (in Chinese)
[14] ZHOU Xiang-yang, LI Chang-lin, HUO Deng-wei, LI Jie, WU Shang-yuan. Thermal stability of aluminum hydrate modified by phosphoric acid [J]. The Chinese Journal of Nonferrous metals, 2006, 16(12): 2115-2119. (in Chinese)
[15] SHUI M. Polymer surface modification and characterization of particlate calcium carbonate fillers [J]. Applied Surface Science, 2003, 12: 359-366.
[16] LIUFU Sheng-cong, XIAO Han-ning, LI Yu-ping. Adsorption behavior of poly(acrylic acid) on the surface of nanoparticulate titanium dioxide [J]. Chemical Research In Chinese Universities, 2005, 4: 742-746. (in Chinese)
[17] WEI Shan-shan, ZHANG Yi, XU Jia-rui. Preparation and properties characterization of PAA/Fe3O4 nanocomposite [J]. Journal of Sun Yatsen University, 2006, 45(5): 47-50. (in Chinese)
[18] LI Zhen, LIU Jin, ZHOU Jia-yong, ZHANG Zhi-man. Synthesis and characterization of water-soluble polyacrylic acid series superplasticizer[J]. New Building Materials, 2007, (2): 50-53. (in Chinese)
[19] WANG Y H, LIU X Q, MENG G Y. Dispersion and stability of 8 mol% yttria stabilized zirconia suspensions for dip-coating filtration membranes [J]. Ceramics International, 2007, 33, 1025–1031.
[20] GAO Jian-yang. Physical and chemical properties of AH filler on its use and the products’ performance [J]. Chemical Engineer, 2006(1): 62-64. (in Chinese)
[21] PARK J K, KIM J K, KIM H K. TiO2–SiO2 composite filler for thin paper [J]. Journal of Materials Processing Technology, 2007, 186: 367–369.
Foundation item: Project(06SK2011) supported by the Science and Technology Program of Hunan Province, China
Corresponding author: ZHOU Xiang-yang; Tel: +86-731-8836329; E-mail: xyzhou@mail.csu.edu.cn
(Edited by YANG Bing)