
Tensile properties and microstructure of Ti14 alloy after semi-solid forging
CHEN Yong-nan1, WEI Jian-feng2, ZHAO Yong-qing3, ZHANG Xue-min1
1. Engineering Research Center of Transportation Materials of Ministry of Education,
School of Materials Science and Engineering, Chang’an University, Xi’an 710064, China;
2. State Key Laboratory for Mechanical Behavior of Materials, Xi’an Jiaotong University, Xi’an 710049, China;
3. Northwest Institute for Nonferrous Metal Research, Xi’an 710016, China
Received 14 December 2010; accepted 15 May 2011
Abstract: Tensile properties of a new α+Ti2Cu alloy after solid forging at 950 ℃ and semi-solid forging at 1 000 ℃ and 1 050 ℃ were investigated over the temperature range of 20-600 ℃. The results reveal that high strength and low ductility are obtained in all semi-solid forged alloys. Tensile properties decrease as the semi-solid forging temperature increases, and cleavage fractures are observed after semi-solid forging at 1 050 ℃. The variations in tensile properties are attributed to the coarse microstructures obtained in the semi-solid alloys. It is found that the elevated semi-solid temperatures lead to more liquid precipitates along the prior grain boundaries, which increases the peritectic precipitation and formation of Ti2Cu precipitation zones during re-solidification. Recrystallization heat treatment leads to fine microstructure of semi-solid forged alloys, resulting in improvement of tensile properties.
Key words: Ti14 alloy; semi-solid forging; microstructure; tensile properties; heat treatment
1 Introduction
Titanium alloys are very attractive in the navigation and aerospace industries from the ecological point of view because of their good creep performance, high strength and toughness as well as excellent corrosion resistance [1]. One of the technical challenges for the widespread use of the titanium alloys in structural applications is improvement of formability and reduction of processing cost. Fruitful achievements on improving formability as well as reducing the processing cost have been obtained in the main titanium industrial countries such as Ti62S and Ti-LCB [2] in USA, Ti12LC [3] and Ti8LC [4] in China. Some famous manufacture technologies to improve formability and reduce the cost have already been found, in which semi-solid processing is known as one of the most promising high-tech manufacturing methods for materials in the 21st century.
Several investigations of the deformation and forging behavior on semi-solid of Al, Mg alloy [5-10] and steel [11-12] showed that the alloy in a semi-solid state can be processed more easily with a lower deformation resistance than in a solid state due to the presence of a small volume of liquid. Most recently, some of present authors [13] reported that the semi-solid deformation behavior and microstructure of Ti14 alloys (α+Ti2Cu) were quite different from the conventional one, but there was not further investigation on tensile properties and microstructure of Ti14 alloy after semi-solid forging, which is considered to be an very important property for burn resistant alloy. The objective of the present work was therefore to comprehensively study the tensile properties of Ti14 alloy after semi-solid forging at different temperatures, as compared with that after conventional forging. Furthermore, the effect of heat treatment on tensile properties was also reported.
2 Experimental
The Ti14 alloy used in this work was a new α+Ti2Cu type burn-resistant Ti alloy (Ti-1Al-13Cu-0.2Si) [4-5]. The solidus temperature of Ti2Cu is 990 ℃. If the deformation temperature rises above 990 ℃, Ti14 alloy changes to a semi-solid state. The Ti14 alloy used was a 25 kg ingot. After conventional ingot alloy was forged to bars with diameter of 40 mm, two processing ways were used: 1) semi-solid (1 000 and 1 050 ℃) forging to bars with diameter of 25 mm, respectively, and 2) solid (950 ℃) forging to bars with diameter of 25 mm. Room temperature and high temperature tensile specimens of cylindrical geomertry with a diameter of 4 mm and a gauge length of 45 mm were cut from the forging billets, and tensile tests were performed using an Instron system at the temperatures of 20, 200, 400 and 600 ℃ under a nominal strain rate of 4.2×10-3 s-1. During all the testing, the specimens were kept at the given temperature within ±5 ℃. The results of tensile tests were based on the average of three specimens on each test condition. Moreover, the tensile properties were examined before and after recrystalliza- tion heat treatment, i.e., solution at 810 ℃ for 30 min water quenching (WQ) followed by aging at 450 ℃ for 8 h air cooling (AC). Phases were determined by X-ray diffraction technique (XRD, XRD-1700) and confirmed by energy dispersive X-ray spectrometer (EDS). Optical microscopy (OM, OLYMPUS GX71), and scanning electron microscopy (SEM, JSM-6700) were used for study on the microstructures and tensile fractographs.
3 Results
3.1 Tensile properties
Results of room temperature (RT) tensile test of Ti14 after solid forging and semi-solid forging are shown in Table 1. The strengths of all semi-solid forged specimens increased obviously compared with the solid forged ones. The specimen after semi-solid forging at 1 000 ℃ exhibits the highest strength with the ultimate tensile strengths (UTS) almost 990 MPa. However,the specimen after semi-solid forging at 1 050 ℃ presents the lowest ductility with the elongation (El) of 8.5% in all tests and reduction in area of 18.5%, which decreased by 43.0% and 51.3%, respectively, compared with the solid forged one.
Table 2 lists the tensile properties of Ti14 alloy with heat treatment for the semi-solid and solid forging at RT. Similar to the forging condition, the semi-solid forged alloy also presents high strength and low ductility, namely, the tensile strength of semi-solid (1 050 ℃) forged alloy increased by 20.9%, the yield strength increased by 28.3%, while the elongation decreased by 19.0% and reduction in area decreased by 29.3%, respectively, compared with the solid forged specimen.
By comparison of the values before and after heat treatment, the strength of the semi-solid forged specimen after heat treatment increases slightly, but the ductility increases greatly, which increases elongation from 9% to 19% after forging at 1 000 ℃ and from 8.5% to 17% after forging at 1 050 ℃. These results reveal that the heat treatment could improve ductility of semi-solid forged alloy.
The relationships between tensile properties and tensile temperature of Ti14 alloy at different forging temperatures are shown in Fig. 1. It is evident that the strength of all forged alloys decreases and the ductility increases with increase of tensile temperature, which is similar to the conventional laws. Compared with the solid forging, the higher strength and lower plasticity are obtained under 300 ℃ in all semi-solid specimens, while tensile at 400 ℃, the strength and the ductility of the both forging ways are very close.
3.2 Microstructure of solid forged alloy and semi-solid forged alloy
Figure 2 shows the results of XRD and Fig. 3 shows the optical micrographs of the Ti14 alloy forged at different temperatures. It is found all forged alloys mainly consisted of α-Ti matrix and Ti2Cu precipitate phase, irrespective of the temperature. The alloy after solid forging represents a typical microstructure of Ti14 (Fig. 3(a)), which consists of fine and homogeneous Ti2Cu precipitates [14]. Ti2Cu precipitation occurred both within grains and on grain boundaries in samples forged at 1 000 ℃ (Fig. 3(b)), and more Ti2Cu tended to precipitate on grain boundaries in sample forged at 1 050 ℃ (Fig. 3(c)). As a result, the segregation of Ti2Cu on grain boundaries increased with the semi-solid forging temperatures, which resulted in the formation of a coarse grain boundary structure.
Table 1 Room temperature tensile properties of Ti14 alloy bar after different processings

Table 2 Tensile properties of Ti14 alloy after heat treatment of (810 ℃, 30 min, WQ)+(450 ℃, 8 h, AC)

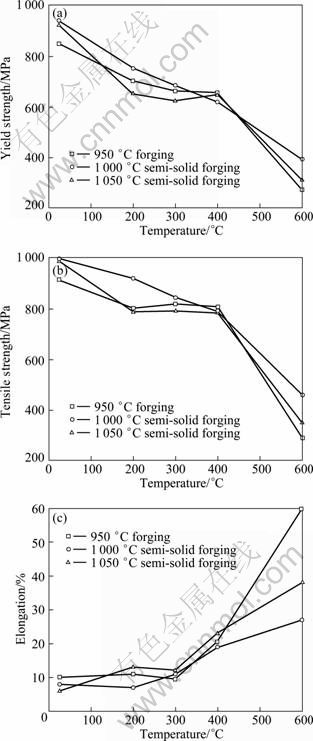
Fig. 1 Tensile properties of Ti14 alloy after heat treatment at different temperatures: (a) Yield strength; (b) Tensile strength; (c) Elongation
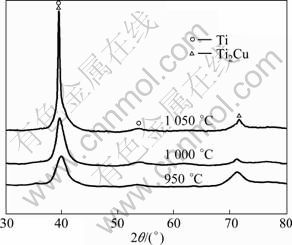
Fig. 2 X-ray diffraction patterns of Ti14 alloy after forging at different temperatures
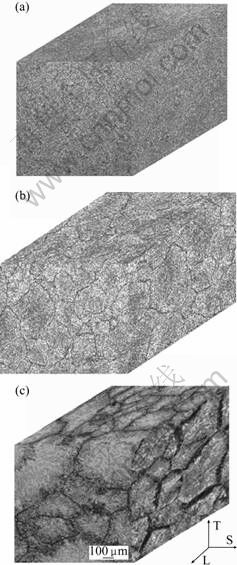
Fig. 3 Tri-planner collage of optical micrograph of Ti14 alloy without heat treatment: (a) Solid forging; (b) Semi-solid forging at 1 000 ℃; (c) Semi-solid forging at 1 050 ℃
Figure 4 illustrates the optical micrographs of forged Ti14 alloys after heat treatment. Compared with Fig. 3, it is seen that the semi-solid forged coarse microstructure is refined, which indicates that heat treatment can improve the microstructure of semi-solid alloy, resulting in improvement of mechanical properties.
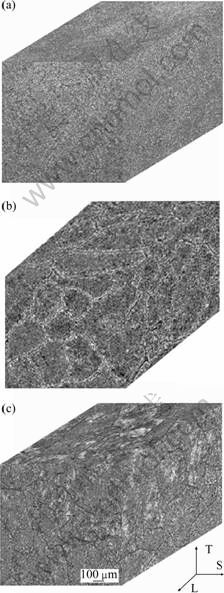
Fig. 4 Tri-planner collage of optical micrograph of Ti14 alloy after heat treatment: (a) Solid forging; (b) Semi-solid forging at 1 000 ℃; (c) Semi-solid forging at 1 050 ℃
3.3 Precipitates characteristics of forged alloy
SEM images and EDS analysis of the grain boundaries of the Ti14 alloy after forging at 950 ℃, 1 000 ℃ and 1 050 ℃ are shown in Fig. 5. The grain boundaries of solid forged alloy mainly consist of fine-particle Ti2Cu (Fig. 5(a)). A plate-shaped Ti2Cu phase was observed after semi-solid forging at 1 000 ℃, as shown by arrows in Fig. 5(b). As the forging temperature increased, more plate-shaped Ti2Cu precipitates were observed on the grain boundaries, which formed gross precipitated zones adjacent to grain boundaries and led to coarse grain boundaries, as shown by arrows in Fig. 5(c). Furthermore, EDS analysis showed that the average contents of Cu element at the grain boundaries after forging at 950, 1 000 and 1 050 ℃ are 19.93%, 31.34% and 36.94% (mass fraction), respectively. By comparison of the precipitates in the semi-solid forged alloys, it is found that the volume fraction of the plate-shaped precipitates increased with increasing forging temperature, which suggested that more precipitation occurred on grain boundaries at higher semi-solid temperature.
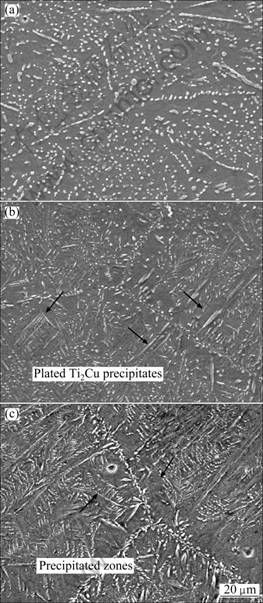
Fig. 5 SEM images of precipitates on grain boundaries after solid forging (a), semi-solid forging at 1 000 ℃ (b) and semi-solid forging at 1 050 ℃ (without heat treatment) (c)
3.4 Tensile fractographs
The tensile fractographs of semi-solid and solid forged alloys are listed in Fig. 6. It is clearly evident that ductile failure occurs due to the nucleation, growth, and coalescence of microvoids, after solid forging, which is well fine dimple fracture (Fig. 6(a)), resulting in high ductility. The fracture surfaces of these samples represent a mixed mode of failure involving both cleavage and dimple fracture after semi-solid forging at 1 000 ℃ (Fig. 6(b)), even though the specimen exhibits a tensile elongation of 10%. The fracture surface topography is indicative for the limited ductility. Fracture morphology of specimens after semi-solid forging exhibits a cleavage fracture (Fig.6 (b)). Typical cleavage fracture is observed clearly after forging at 1 050 ℃ (Fig. 6(c)), where the delaminating of precipitates and matrix is the principal mechanism for the nucleation of microcracks within the grains.
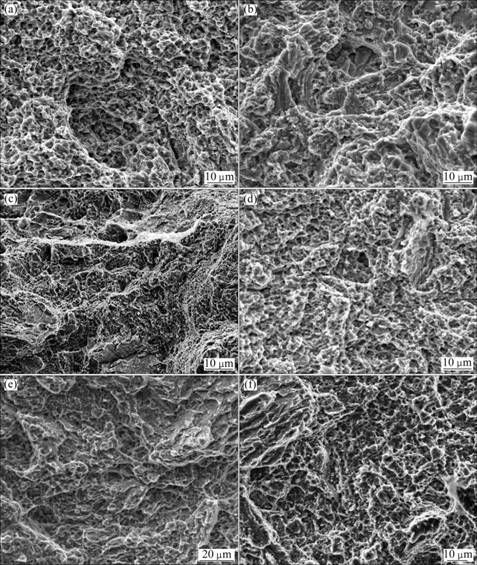
Fig. 6 Tensile fractographs of Ti14 alloys after forging (a, b, c) then heat treatment (d, e, f): (a) Solid forging; (b) Semi-solid forging at 1 000 ℃; (c) Semi-solid forging at 1 050 ℃; (d) Solid forging and heat treatment; (e) Semi-solid forging at 1 000 ℃ and heat treatment; (f) Semi-solid forging at 1 050 ℃ and heat treatment
The tensile fractographs of the specimens after heat treatment for all forged alloys are shown in Figs. 6(d)-(f). The fracture of solid forged alloy is inter-grain failure with fine dimple existed on surface (Fig. 6(d)). The fracture of semi-solid forged alloy exhibits a mixture of ductile fracture as well as cleavage fracture, with fine dimple and second cracks (Figs. 6(e) and (f)). Compared with the fractographs and tensile elongation of semi-solid forged alloys before and after heat treatment, it is found that elongation increases from 8.5% to17%, and ductile fracture characterization is observed after semi-solid forging at 1 050 ℃, which suggests that heat treatment can obviously improve the ductility of semi-solid forged alloys.
4 Discussion
The original researches on the deformation behaviour of Ti alloys are all in solid state, and general results show that hot deformation is controlled by slip, twinning or climbing of dislocations. While in semi-solid state, the existence of liquid makes the grain boundary and grain a mixture of solid and liquid state, which leads to low deformation stress during deformation. The high temperature solid deformation of Ti alloy can form fine grains through the breakdown of grains, while the semi-solid deformation cannot produce fine grains, instead of coarse grain boundaries (Figs. 3 and 4). The coarse grain boundaries microstructures are associated to the precipitation behaviors of the Ti2Cu during the solidification. In our tests, solidification and phase transformation path way for the alloy is as follows: L+β (990 ℃)→Ti2Cu (peritectic)+β→α+Ti2Cu(eutectoid)+Ti2Cu (peritectic). It is found that the precipitation and growth of Ti2Cu significantly depends on the distribution and the volume fraction of liquids. In this work, more liquids segregate to the grain boundary with increase of forging temperature during forging [15]. This leads to more plated-Ti2Cu precipitate and grow on grain boundaries to form precipitated zones, which is the main reason for coarse grain boundaries.
Difference in tensile properties of alloy in the two forging states can be related to the change of microstructure caused by semi-solid forging. The increase of strength is attributed to hardening effects caused by Ti2Cu precipitates [16-17]. Low ductility is attributed to the grain boundaries precipitates zones consisted of plated-Ti2Cu precipitates, which is considered to be the principal mechanism for the nucleation, extend of microcracks. It is found that deformation incompatibility of precipitated zones and matrix could induce microcracks between their interfaces, causing the cleavage fracture.
After recrystallization heat treatment (810 ℃) [14], the microstructures of alloy in the two forging states are similar (Figs. 3 and 4). The only difference is that Ti2Cu is fine and well distribution in the solid forged samples (Figs. 3 and 4), while the Ti2Cu is coarse after semi-solid forging, which leads to low ductility and high strength (Table 2). Ti2Cu is a low melting point phase. With the increase of testing temperature, the influence of Ti2Cu phase on ductility is slight, and upper than 400 ℃, the high temperature tensile properties of two forging state are very close, which suggests that heat treatment could improve the mechanical properties of semi-solid forged alloys.
Summarily, the semi-solid forged alloy exhibited high strength and low ductility during tensile tests, even at high temperature. The low ductility is mainly due to the coarse grain boundaries caused by peritectic reaction. The heat treatment at recrystallization temperature (810 ℃) could refine the microstructure of grain boundaries and improve the ductility.
5 Conclusions
1) The semi-solid forging enhances the tensile strength and reduces the ductility compared with solid forging. RT tensile fractography of specimens reveals evidence of ductile failure mechanisms for solid forged alloy and cleavage fracture mechanisms for the alloy after semi-solid forging at 1 050 ℃. The relative contributions of tensile properties and the fracture attribute to the grain boundary microstructure obtained by semi-solid forging.
2) Coarse grain boundaries with plated-Ti2Cu precipitates were obtained in all semi-solid forged alloys, especially after SSF at 1 050 ℃. The elevated semi-solid temperatures lead to more liquid precipitates along the grain boundaries, which increase the peritectic precipitation and form precipitation zones during re-solidification.
3) Recrystallization heat treatment causes fine microstructure, which is similar to solid forging, improving its mechanical properties.
References
[1] DOMACHIE M J. Titanium—A technical guide [M]. OH, Materials Park: ASM International, 2000: 22.
[2] FLEMINGS M C. Solidification processing [M]. New York: McGraw Hill, 1974: 160.
[3] CHEN G Z, FRAY D J, FARTHING T W. Direct electrochemical reduction of titanium dioxide to titanium in molten calcium chloride [J]. Nature, 2000, 407: 361-363.
[4] ZHAO Y Q, ZHU K Y, LI Y. A low cost Ti alloy: Chinese Patent, 02101189.3 [P]. 2003-12-7. (in Chinese)
[5] RAMADAN M, TAKITA M, NOMURA H. Effect of semi-solid processing on solidification microstructure and mechanical properties of gray cast iron [J]. Mater Sci Eng A, 2006, 417(1): 166-173.
[6] ESKIN D G, SUYTINO, KATGERMAN L. Mechanical properties in the semi-solid state and hot tearing of aluminum alloys [J]. Prog Mater Sci, 2004, 49: 629-712.
[7] PHILLION A B, THOMPSON S, COCKCROF S L, WELLS M A. Tensile properties of as-cast aluminum alloys AA3104, AA6111 and CA31218 at above solidus temperatures [J]. Mater Sci Eng A, 2008, 497: 388-393.
[8] TZIMAS E, ZAVAKLIANGOS A. Mechanical behavior of alloys with equiaxed microstructure in the semisolid state at high solid content [J]. Acta Mater, 1999, 47: 517-526.
[9] LEWANDOWSKI M S, OVERFELT R A. High temperature deformation behavior of solid and semi-solid alloy 718 [J]. Acta Mater, 1999, 47: 4695-4703.
[10] HU K, PHILLION A B, MAIJER D M, COCKCROF S L. Constitutive behavior of as-cast magnesium alloy Mg-Al3-Zn1 in the semi-solid state [J]. Scripta Mater, 2009, 60: 427-433.
[11] PU¨TTGEN W, HALLSTEDT B, BLECK W. On the microstructure and properties of 100Cr6 steel processed in the semi-solid state [J]. Acta Mater, 2007, 55: 6553-6560.
[12] PU¨TTGEN W, HALLSTEDT B, BLECK W. On the microstructure formation in chromium steels rapidly cooled from the semi-solid state [J]. Acta Mater, 2007, 55: 1033-1041.
[13] ZHA Y Q, WU W L, MA X D. Semi-solid oxidation and deformation behavior of Ti14 alloy [J]. Mater Sci Eng A, 2004, 373: 315-321.
[14] ZHU K Y, ZHAO Y Q. Microstructures of a burn resistant highly stabilized β-titanium alloy [J].J Mater Sci, 2000, 35: 5609-5614.
[15] CHEN Y N, WEI J F, ZHAO Y Q. Effect of semi-solid forging temperature on microstructure and mechanical properties of Ti14 alloy [J]. Journal of Alloys and Compounds, 2009, 487: 314-320.
[16] NAGARJUNA S, SARMA D S. The grain size dependence of flow stress in a Cu-26Ni-17Zn alloy [J].Acta Mater, 2000, 48: 1807-1813.
[17] SUN Q Y, YU Z T, ZHU R H. Mechanical behavior and deformation mechanisms of Ti-2.5 Cu alloy reinforced by nano-scale precipitates at 293 and 77 K [J]. Mater Sci Eng A, 2004, 364: 159-165.
半固态锻造Ti14合金的拉伸性能和组织演变特征
陈永楠1, 魏建锋2, 赵永庆3, 张学敏1
1. 长安大学 材料科学与工程学院,西安 710064;
2. 西安交通大学 金属材料强度国家重点实验室,西安 710049;
3. 西北有色金属研究院,西安 710016
摘 要:通过室温和高温拉伸性能测试,对比研究了Ti14合金经常规锻造(950 ℃)和半固态锻造(1 000 ℃和1 050 ℃)后试样在不同温度区间的宏观力学行为,分析了微观组织演变规律、断口微观形貌及断裂特征。结果表明:合金经半固态锻造后表现出高强度、低塑性的力学特征,随着半固态锻造温度的升高,合金力学性能下降。半固态锻造过程中组织的变化是引起力学性能差异的主要原因,而组织演变的主要特征是Ti2Cu析出相形态和分布的变化。随着半固态温度的升高,更多的液相在晶界析出,并在凝固过程中析出大量板条状Ti2Cu相,最终在晶界上形成偏析带组织。这种带状组织在拉伸过程中引发了解离断裂, 导致了低塑性。此外,通过再结晶退火可以有效地细化半固态组织,改善强度性能。
关键词:Ti14合金;半固态锻造;微观组织;拉伸性能;热处理
(Edited by LI Xiang-qun)
Foundation item: Projects (2005CCA06400, 2007CB613807) supported by the National Basic Research Program of China; Project (CHD2012JC078) supported by the Special Fund for Basic Scientific Research of Central Colleges, China; Project (0111201) supported by the State Key Laboratory for Machanical Behavior of Materials; Project (20110474) supported by Natural Science Basic Research Plan in Shaanxi Province of China
Corresponding author: CHEN Yong-nan; Tel: +86-29-82664764; E-mail: frank_cyn@163.com
DOI: 10.1016/S1003-6326(11)61099-6