
Mechanical behaviour of Al/Al2O3 composite in pseudo-semi-solid state during isothermal compression
CHENG Yuan-sheng(程远胜), LUO Shou-jing(罗守靖)
School of Materials Science and Engineering, Harbin Institute of Technology, Harbin 150001, China
Received 10 June 2009; accepted 15 August 2009
Abstract: To gain a better understanding of thixoforging for the Al2O3-37%Al composite, its mechanical behavior in the pseudo-semi-solid state was studied by isothermal compression tests. The results show that the values of peak stress obviously decrease with increasing temperature and decreasing strain rate. The compressive true stress—strain curves of the Al2O3-37%Al composite can be divided into four stages. They are rapidly ascending, decreasing, steady and slowly ascending. Moreover, the main deformation mechanism controlling deformation of the composite in the pseudo-semi-solid state is the sliding or rotary movement between solid particles.
Key words: composite; pseudo-semi-solid state; mechanical behaviour; stress—strain curve
1 Introduction
Compact billets were prepared under certain pressure with ceramic powders and metal powders by the powder metallurgy technology[1-3]. Then billets were reheated into the temperature interval—pseudo-semi- solid temperature, at which the ceramic was in the solid state and the metal was in the liquid state based on the characteristics of semi-solid metal processing[4-5]. Finally, the parts were prepared by forging. Based on power metallurgy and semi-solid processing[6-7], a new technology, thixoforging in the pseudo-semi-solid state, was proposed.
It is important to grasp this technology and select the processing parameters reasonably by studying the mechanical behavior of the composite in the pseudo-semi-solid state. In this paper, the research of mechanical behaviors of Al/Al2O3 composite by pseudo-semi-solid state isothermal compression was presented. Moreover, the sketch of Al/Al2O3 composite structure changing during upsetting in the pseudo semi-solid state was also proposed.
2 Experimental
Raw materials were Al metal powders with an average size of 40 mm and nearly spherical α-Al2O3 withan average size of 120 nm. The composition of α-Al2O3 is listed in Table 1.
Table 1 Composition of Al2O3 (mass fraction, %)

The interface wettability and compatibility of common metal/ceramic composites were poor[8-10]. To improve the interface wettability between metal and ceramic, two methods were adopted during the study as follows[11-12]: adding Mg and pre-heat treatment of ceramic powders. The optimum heat treatment technology was heating ceramic powders to 900 ℃ and keeping this temperature for 2 h. The powders were mixed by ball-milling with KQM-4 for about 5 h. The charge ratio was about 5?1. The billets with the size of d56 mm×60 mm were prepared by compression under 1 000 kN hydraulic press. To reduce internal pores and avoid metal oxidation [13-16], the cold compacted billets must be compacted further by hot compression. The temperatures of mould and billets were about 350 and 550 ℃, respectively.
The compression samples with the size of d8 mm×12 mm were cut from billets obtained by hot compression. The isothermal compression was carried out on Instron-1186. The device is shown in Fig.1. The
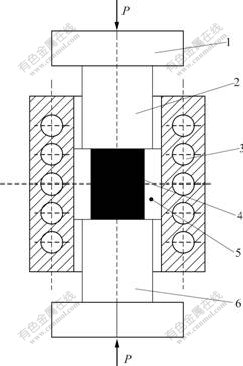
Fig.1 Schematic diagram of isothermal compression test of Al/Al2O3 composite: 1-Sensor; 2-Upper punch; 3-Heating apparatus; 4-Sample; 5-Thermocouple; 6-Under punch
temperatures are 700, 750, 800 and 850 ℃, respectively. The strain rates are 1×10-1, 5×10-2, 5×10-3 and 2.5×10-3s-1, respectively. The samples were placed into cold water after compression quickly. Microstructures were observed under SEM (S570).
3 Results and discussion
3.1 Isothermal deformation characteristics
Fig.2 shows the true strain—true stress curves of Al2O3-37%Al in the pseudo-semi-solid state. The shape of the curves indicates that firstly the stress increases with increasing strain. The true stress decreases with increasing strain after the stress reaches the value of peak flow stress. With further increasing true strain, the true stress increases. But the amplitude is small. It could be said that it is in a stable stage. Finally, the stress increases when the true strain reaches a certain degree again.
The compression process of Al2O3-37%Al composite can be divided into four stages. The first stage is the increasing rapidly one. The liquid metal is flowed into these micro zones whose iso-pressings are low when the samples are compressed under pressure. But the liquid metal mainly surrounds the solid grains because the

Fig.2 True strain—true stress curves of Al/Al2O3 composite during isothermal upsetting in pseudo-semi-solid state at different temperatures and different strain rates: (a) 700 ℃; (b) 750 ℃; (c) 800 ℃; (d) 850 ℃
deformation is small. More and more solid grains are deviated from equilibrium position with increasing the deformation. The attractive power between solid grains decrease to zero when the distance between these grains reaches a certain numeric value and the three- dimensional net structure in the interior tissue is broken without recovery. So, the first stage is the elasticity and plasticity stage or the further densification one (see Fig.3(a)).
The second stage is the decreasing one. The liquid metal flows into the interior extended zones of samples with the true strain further increasing because of pressure. The iso-pressing between surface of samples and contact site of dies is high, which in the central site is high and in the outer site is low. So, the liquid phase flows into the outer from central area. Solid grains begin to rotate and slide greatly and micro flaws begin to appear too, for example the pores and crackles. So, the internal friction and apparent viscosity decrease because the distance between solid grains increases and the flow stress decreases. It displays that the true stress decreases with the true strain increasing (see Fig.3(b)).
The third stage is the stable flowage stage. During this stage most of the Al2O3 solid grains in the samples begin to slide and rotate. The inner pores and cracks increase and the true stress decreases gradually. But the metal in the central area is little because it flows to the outer area. So, the central solid grains rotate and slide difficultly under external force. It displays that the true stress increases. In addition, the friction on the two end surfaces increases because the contact area of the samples increases during upsetting. This curve in this stage is relatively stable because of combining effects of the both actions above (see Fig.3(c)).
During the fourth stage the true stress increases with increasing the true strain. In this stage the liquid metal in the central area is relatively little because of extruding. At the same time the inner flaws and distances between solid grains increase because the flaws generated in the third stage extend sequentially, for example, the cracks and the inner stress condition change. All of these make the true stress increase. It displays that the true stress increases with the strain increasing (see Fig.3(d)).
3.2 Influences of strain rate on mechanical behavior
Fig.4 shows the strain rate sensitivity of Al2O3-37%Al composite in the high temperature stage. Under the conditions of the same strain capacity, the true stress increases evidently and the true stress—true strain curves shift up with decreasing the strain rate. The shapes of the curves change, the peak flow stress begins to decrease and the radiuses of curvature increase with decreasing the strain rate. The reason is that with increasing the strain rate some solid grains or aggregations can not rotate or slide immediately, the aggregations can not break easily and the inner frictions of the samples increase.
The peak flow stress—strain rate curves and steady flow stress—strain rate curves at different pseudo- semi-solid temperatures are shown in Fig.4. As shown in Fig.4, the peak flow stresses and steady flow stresses of the materials increase with decreasing the temperature and increasing the strain rate.
During the compression the micro flaws increase
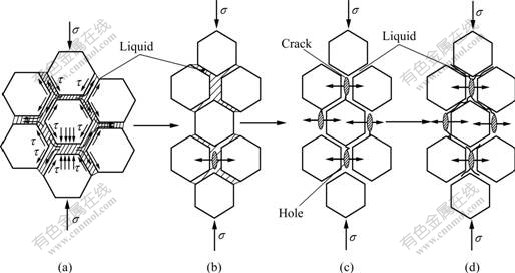
Fig.3 Sketch of Al2O3-37%Al composite structure changing during upsetting in pseudo semi-solid state: (a) First stage; (b) Second stage; (c) Third stage; (d) Fourth stage
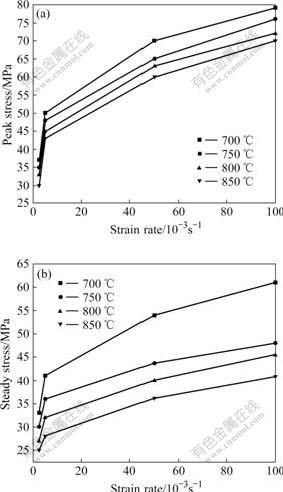
Fig.4 Relationship between stress and strain rate of Al2O3-37%Al composite during isothermal upsetting in pseudo-semi-solid state at different temperatures: (a) Peak flow stress—strain rate; (b) Steady flow stress—strain rate
gradually because of most solid grains deformed difficultly in the samples. Of course not all these solid grains rotate or slide immediately under the action of external force but are more ordered. The poor connection grains begin to break firstly. Under the conditions of low strain rates, more and more solid grains begin to rotate and slide until the whole sample is broken. But if the strain rate is too high some solid grains or aggregations cannot rotate and slide immediately, only the poor connections break and pores generate. It displays that the peak flow stresses increase with increasing strain rates. So, the strain rate has a great influence on Al2O3-37%Al composite during high temperature deformation stage.
3.3 Influences of temperature on mechanical behavior
The steady flow stress—deformation temperature curves of composite are shown in Fig.5. As shown in Fig.5, the steady flow stresses decrease gradually with increasing deformation temperatures.
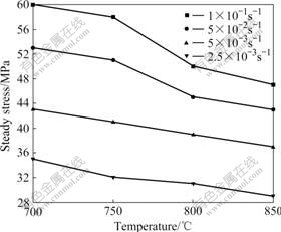
Fig.5 Relationship between steady stress and deformation temperature of Al2O3-37%Al composite during isothermal upsetting in pseudo-semi-solid state at different temperatures and different strain rates
With increasing temperature the energy of flow units of sample increases, the ordering degree decreases but the disordering degree increases; the interfacial force of liquid metal and the inner friction of samples decrease; the solid grains or aggregations rotate and slide easily; and the coordinability of each phase and the deformability in the composite and the wettability between interfaces improve. It displays that the true stresses decrease. So, the flow stress with appropriate addition of deformation temperature is decreased during thixiforging at pseudo-semi-solid temperature. At the same time it explains the deformation temperature sensitivity of Al2O3-37%Al composite.
3.4 Microstructures of isothermal compression in pseudo-semi-solid state
As shown in Fig.6, the samples break more and more heavily with increasing compression degrees (?h). When ?h=0.5 mm (see Fig.6(a)), the inner of whole sample is not broken basically but few zones are with pores. This is just the first stage (increasing rapidly) of true stress—true strain curves during isothermal compression. The sample is much compact under pressure. When the compression decrement increases more and more the micro flaws generate and extend (see Fig.6(b) and (c)). When ?h=3 mm (see Fig.6(d)), the compressing decrement is large, the shearing crushing and some pores extending greatly appear in the inner of sample because of interfaces separating. The distances between solid grains increase, the apparent viscosity and the flow stress decrease. All of these factors benefit to the filling during die forming.
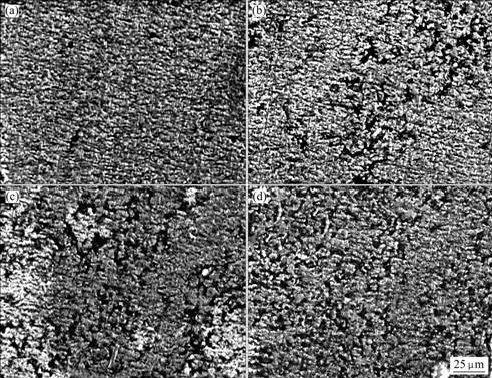
Fig.6 Microstructures of Al2O3-37%Al composite isothermal compression samples under different compression degrees: (a) ?h=0.5mm; (b) ?h=1.5 mm; (c) ?h=2 mm; (d) ?h=3 mm
4 Conclusions
1) There are four stages in the true stress—true strain curves during isothermal compressing of Al2O3-37%Al composite in pseudo-semi-solid state.
2) The steady flow stresses and peak flow stresses decrease evidently with increasing the deforming temperature and strain rate. It indicates that Al2O3-37%Al composite is with the characters of deforming temperature and strain rate sensitivities.
3) The mechanical behavior depends on the fluxion of liquid metal, rotation and sliding of solid grains or aggregations.
References
[1] JIA Cheng-chang. Introduction of composites [J]. Beijing: Metallurgical Industry Press, 2002. (in Chinese)
[2] DU Zhi-ming, CHENG Yuan-sheng, LUO Shou-jing. High volume fraction Al2O3/Al composites thixoforming in pseudo-semi-solid state [J]. Solid State Phenomena, 2006, 116/117: 725-729.
[3] LUO Shou-jing, CHENG Yuan-sheng, WANG Peng-xiang. Pseudo-semi-solid thixoforging of cup shell with Al/Al2O3 [J]. Trans Nonferrous Met Soc China, 2006, 16(4): 772-775.
[4] RAMANATHAN S, KARTHIKEYAN R, GANASEN G. Development of processing maps for 2124Al/SiCp composites [J]. Mater Sci Eng A, 2006, 441: 321-325.
[5] ZENG Yuan-song, HUANG Xia. Forming technologies of large integral panel [J]. Acta Aeronautica et Astronautica Sinica, 2008, 29(3): 721-727.
[6] ZHAO Zu-de, CHEN Qiang, WANG Yan-bin, SHU Da-yu. Microstructural evolution of an ECAE-formed ZK60-RE magnesium alloy in the semi-solid state [J]. Mater Sci Eng A, 2009, 506 (1/2): 8-15.
[7] ZHAO Zu-de, CHEN Qiang, KANG Feng, SHU Da-yu. Microstructural evolution and tensile mechanical properties of thixoformed AZ91D magnesium alloy with the addition of yttrium [J]. Journal of Alloys and Compounds, 2009, 482(1/2): 455-467.
[8] LUO Shou-jing, CHENG Yuan-sheng, DU Zhi-ming. Thixoforming of SiC ceramic matrix composites in pseudo-semi-solid state [J]. Trans Nonferrous Met Soc China, 2005, 15(5): 1062-1066.
[9] CHEN Ti-jun, HAO Yuan, SUN Jun. Compressive deformation of semi-solid SiCp/ZA27 composites [J]. Trans Nonferrous Met Soc China, 2003, 13(5): 1164-1170.
[10] GAN Wei-ping, WANG Yi-ren, CHEN Tie-ping, YANG Fu-liang, LIU Hong. Research of hot deformation behavior of 6013 aluminum alloy [J]. Materials Review, 2006, 20(5): 111-113.
[11] VEDANI M, ERRICO F D, GARIBOLDI E. Mechanical and fracture behaviour of aluminium-based discontinuously reinforced composites at hot working temperatures [J]. Composites Science and Technology, 2006, 66: 343-349.
[12] LIU T Y, ATKINSON H V, KAPRANOS P, KIRKWOOD D H, HOGG S C. Rapid compression of aluminum alloys and its relationship to thixoformability [J]. Metallurgical Transactions: A, 2003, 34: 1545-1554.
[13] UGGOWITZER P J, KAUFMANN H. Evolution of globular microstructure in new rheocasting and super rheocasting semi-solid slurries [J]. Steel Research International, 2004, 75(8/9): 525-530.
[14] BAI Qian, YANG He, ZHAN Mei. Finite element modeling of power spinning of thin-walled shell with hoop inner rib [J]. Trans Nonferrous Met Soc China, 2008, 18(1): 6-13.
[15] FLINN B, RUHLE M, EVANS A G. Toughening in composites of Al2O3 reinforced with Al [J]. Acta Metall, 2004, 37(4): 3001-3006.
[16] WAGONER R H, LIB M. Simulation of springback: Through-thickness integration [J]. International Journal of Plasticity, 2007, 23: 345-360.
(Edited by HE Xue-feng)
Foundation item: Project (50705018) supported by the National Natural Science Foundation of China; Project(20070420847) supported by the Postdoctor Foundation of China; Project(LBH-Z07140) supported by the Postdoctor Foundation of Heilongjiang
Corresponding author: CHENG Yuan-sheng; Tel: +86-451-86415464; E-mail: dasheng21cn@gmail.com