
Effect of additive on corrosion resistance of NiFe2O4 ceramics as inert anodes
XI Jin-hui(席锦会)1, XIE Ying-jie(谢英杰)2, YAO Guang-chun(姚广春)2, LIU Yi-han(刘宜汉)2
1. School of Materials Science and Engineering, China University of Mining and Technology,
Xuzhou 221008, China;
2. School of Materials and Metallurgy, Northeastern University, Shenyang 110004, China
Received 4 September 2007; accepted 7 January 2008
Abstract: In order to improve the corrosion resistance of NiFe2O4 ceramics as inert anode, additive V2O5 was added to raw materials NiO and Fe2O3. The inert anodes of nickel-ferrite ceramics were prepared by powder metallurgic method and the static corrosion rate in Na3AlF6-Al2O3 was determined by mass loss measurement. The effect of V2O5 on sintering property and corrosion resistance was studied. The results show that V2O5 can promote the grain to develop completely and improve sintering property. EDS results show the reaction product Ni2FeVO6 distributes along the grain boundary. The corrosion tests show that V2O5 is beneficial to improving corrosion resistance remarkably. The reasons that V2O5 can improve the corrosion resistance must be V2O5 promoting the gains to develop completely and Ni2FeVO6 distributes along the grain boundary. The stable structure can control the chemical dissolution of ceramics anode and the reinforced grain boundary can control the grain-boundary corrosion rate.
Key words: NiFe2O4; inert anode; additive; corrosion resistance
1 Introduction
In conventional aluminium electrolysis, the major cell reaction is
1/2Al2O3+3/4C=Al+3/4CO2 (1)
Thus, using carbon anodes has many disadvantage,such as the consumption of anode carbon and the emission of carbon dioxide and fluorocarbon. With an inert anode, the reaction[1] is
1/2Al2O3=Al+3/4O2 (2)
The introduction of inert anodes will evolve oxygen [2-3], being friendlily to environment, which makes the use of inert anode commercially attractive. Re- searches have been done in order to find the appropriate material for inert anodes in aluminum production.
However, the inert anode must meet some basic requirements[4]: to exhibit a low corrosion rate in the high-temperature melts and environment of high oxidizability; not to contaminate the produced metal Al; to be economically feasible and to be a good electric conductor. A lot of research work has been carried out,which can be divided into three classes, namely, metals [5-6], ceramic oxides[7-8], and cermets[9-10] , but no material has been found to satisfy all these requirements. One of the formidable challenges is the corrosion property.
The major corrosion mechanisms of inert anodes in electrolyte are chemical dissolution, electrolyte penetration as well as electrochemical dissolution.
As discussed by RAY[11], the cermets anode material may be corroded via several mechanisms such as oxidation, chemical dissolution (fluorination), electrochemical dissolution, reduction by dissolved metal Al, electrolyte penetration, and grain boundary attack. Under conventional electrolysis conditions, chemical dissolution and electrolyte penetration serve as two major corrosion mechanisms[12-13].
For the chemical dissolution, the reasons are the dissociation of NiFe2O4 ceramics and the following reactions with electrolyte[14]:
2AlF3(s)+3FeO(s)=3FeF2(s)+3/2O2(g)+2Al(l) (3)
2AlF3(s)+Fe2O3(s)=2FeF3(s)+3/2O2(g)+2Al(l) (4)
2AlF3(s)+3NiO(s)=3NiF2(s)+3/2O2(g)+2Al(l) (5)
As for the electrolyte penetration, LI et al[14] thought it may result from two reasons. The first one is due to pores left by the electrochemical dissolution of metal phase when anodes are polarized, or by the metal phase oxidation and the following preferential chemical dissolution. Bath penetrates into these pores by capillary effects. The second one is the selective dissolution of Fe. In the ceramic phase of the NiFe2O4-based anode, Fe has a fairly high solubility in cryolite, compared with Ni. So improving the density of ceramics matrix and strengthening the grain boundary are very important.
In this work, the NiFe2O4 ceramics with little amounts of V2O5 (0-2.0%, mass fraction) were prepared. By determining the density and corrosion rate of anodes and analyzing anode by EDS connected to the SEM, we expected to see how V2O5 affects the sintering property and corrosion resistance.
2 Experimental
2.1 Preparation of NiFe2O4 ceramics
The raw materials, NiO, Fe2O3 and V2O5 were all in reagent grade. NiFe2O4 ceramics samples with V2O5 were prepared by cold pressing-sintering process. NiO and Fe2O3 and a proper amount of V2O5 (0%, 0.5%, 1.0%, 1.5%, 2.0%, respectively) were mixed by ball milling and then the mixed powders were cold pressed into rectangular blocks (70 mm×18 mm×(10-11) mm) at the pressure of 100 GPa and sintered at 1 200 ℃ for 6 h.
2.2 Performance tests
The density was tested by Archimedes draining method. Samples with V2O5 were prepared for characterization by DSC (SDT Q600), DTA (SDT22960) and X-ray diffraction (XRD) (RigakuD/max-RB) to investigate if there are foreign phases produce.
The samples were immerged in molten cryolite, with temperature maintained at 960 ℃ for 10 h, to determine the static state corrosion rate. The electrolyte was made up of reagent grade CaF2 and AlF3, technical grade NaF and Al2O3. The CR (molar ratio of NaF to AlF3) was kept to be 2.2, and the concentrations of CaF2 and Al2O3 were both kept to be 5% (mass fraction). The eroded samples were washed in 30%AlCl3 solution at 100 ℃ to remove the adhering melt. The corrosion rate was determined by mass loss measurement.
Some anodes were analyzed by scanning electron microscope(SEM) (SSM550) and energy dispersive spectrometer(EDS) connected to the SEM.
3 Results and analysis
3.1 Effect of V2O5 content on ceramics density
The changes of density and volume shrinkage with the content of V2O5 are shown in Fig.1. From Fig.1, it can be found that in the range of 0-2.0% V2O5, the higher the V2O5 content, the higher the density and the larger the volume shrinkage, especially when the content of V2O5 is more than 1%. The fact shows that V2O5 can promote sintering property.
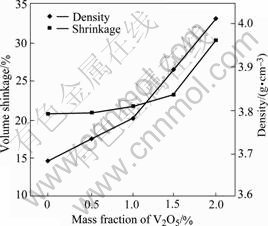
Fig.1 Effect of V2O5 on density and volume shrinkage
The microstructures of samples without V2O5 and with 1.5%V2O5 are shown in Fig.2(a) and Fig.2(b) respectively. The grain size in the sample without V2O5 is small and uniform, being 2-4 μm commonly, and the grains are granulose. But when 1.5%V2O5 is added, the grain size accretes obviously. Furthermore, the grain size is non-uniform, being 2-8 μm, and big grain is octahedron. This shows that V2O5 can promote the grain to grow and develop completely.
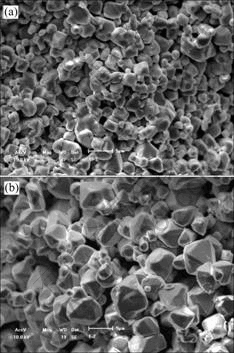
Fig.2 SEM photographs of samples: (a) Without additive; (b) With 2.0%V2O5
In order to analyze the effect of V2O5 on sintering, the distribution of elements such as Ni, Fe, V and O on the polished surface of NiFe2O4 with 2.0% V2O5 was analyzed by scanning electron microscopy, as shown in Fig.3. It can be seen that the element V distributes along the grain boundary.
Fig.3 SEM micrograph (a) and distribution of Ni (b), Fe (c), V (d) and O (e) on polished surface of NiFe2O4 with 2.0%V2O5
Ternary phase diagram of the system NiO-V2O5- Fe2O3[15] is shown in Fig.4. The reaction products of the compositions of NiO-Fe2O3-2%V2O5 in this work lies in the XI section. The phase compositions in this section are Ni2FeVO6, NiO and NiFe2O4.
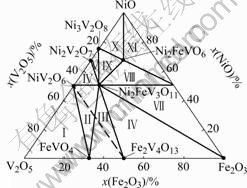
Fig.4 Ternary phase diagram of NiO-V2O5-Fe2O3
In order to study if there are new phases produce, the DSC was carried out on the Fe2O3-NiO-2%V2O5 system, and the curve is shown in Fig.5(a). There is a small exothermic peak at 625-650 ℃. It can be determined that a chemical reaction arises at 625-650 ℃. Due to the fact that the amount of V2O5 is too little, the exothermic peak is not obvious. Then the DTA was carried out on the Fe2O3-NiO-30%V2O5 system, and the curve is shown in Fig.5(b). A exothermic peak exists from 625.07 ℃ to 651.64 ℃. It is same as the former. In order to study the new phase, XRD analysis was carried out. Fig.6 shows the XRD pattern of sample with 2.0%V2O5. It can be seen that the new phase is Ni2FeVO6. The peak is probably associated with the produce of Ni2FeVO6. Combining with Fig.3, we can know Ni2FeVO6 concentrates at the grain boundary. According to Ref.[15], the melting point of Ni2FeVO6 is low. At the sintering temperature adopted in this work, Ni2FeVO6 becomes liquid. The sintering of the system (Fe2O3-NiO-2%V2O5) is liquid-phase sintering, so in this process, the densification was gotten through mass transfer of liquid phase. The small grains dissolve, and the big grains grow bigger, so the grain sizes are non-uniform. And the liquid can promote the grains to grow and develop completely with the regular octahedron shape. With the amount of V2O5 increasing, the amount of liquid increases, so the character of liquid improving sintering is more obvious.
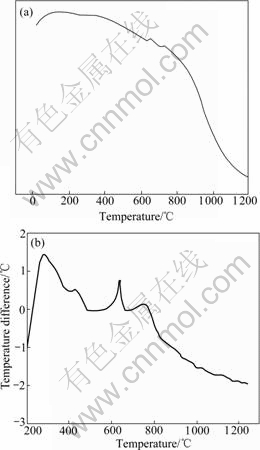
Fig.5 DSC curve of Fe2O3-NiO-2%V2O3 (a) and DTA curve of Fe2O3-NiO-30%V2O5 system (b)
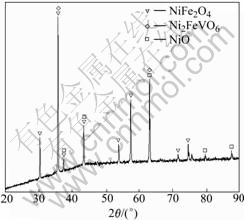
Fig.6 XRD pattern of sample with 2.0%V2O5
3.2 Effect of V2O5 content on corrosion resistance
The effect of V2O5 content on corrosion rate is shown in Fig.7, from which it is obvious that adding V2O5 can dramatically lower the corrosion rate. Corrosion rate of sample without V2O5 is 0.048 2 g·cm-2·h-1. The corrosion rate of sample with 0.5%V2O5 is 0.011 g·cm-2·h-1, 1/4 of that of sample without V2O5. The corrosion rate of sample with 1.5%V2O5 is the lowest, being 0.001 05 g·cm-2·h-1, 1/46 of that of sample without additive.
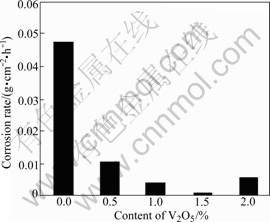
Fig.7 Corrosion rate of samples with different contents of V2O5
After being eroded in molten salt, the two samples are all in good condition, no crack or tumescence. But the sample without V2O5 is not smooth, many visible pits on it. On the contrary, the sample with 1.5%V2O5 is smooth and no visible pits appear.
The eroded surfaces were characterized by SEM, as shown in Fig.8. From Fig.8(a), it can be found that many big holes on the grains and the grains become loosen because the grain boundary is attacked by molten cryolite. From Fig.8(b), it can be seen that the sample is eroded slightly then its surface is flat. There are only the fewer and smaller holes on the grains and grains bind closely. So the grain and grain boundary all have good corrosion resistance to melt and could effectively hold back the melt penetration.
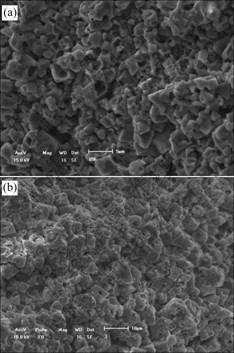
Fig.8 SEM photographs of samples eroded by molten cryolite: (a) Without additive; (b) With 1.5%V2O5
The surface of sample with V2O5 is eroded slightly, which is coincident with the result of the samples’ corrosion rate.
The reasons that V2O5 can improve the corrosion resistance must be V2O5 promoting the gains to develop completely with the octahedron shape and Ni2FeVO6 concentrating at grain boundary. The stable structure could control the chemical dissolution of ceramics anode, which is beneficial to improving the corrosion resistance of sample in molten cryolite. Moreover the reaction product Ni2FeVO6 concentrates at grain boundary and it has good corrosion resistance, so can reinforce the corrosion resistance of the grain boundary. As the candidate materials of inert anodes, the requirement to corrosion rate is rigorous. Improving the corrosion resistance is the key problem that researchers are making great efforts to solve. In this work, adding V2O5 can increase the corrosion resistance of sample remarkably, so V2O5 is an interesting additive for NiFe2O4 ceramics.
4 Conclusions
1) When V2O5 is added to NiO, Fe2O3 and Ni2FeVO6 are produced, which has lower melting-point. During sintering, it becomes liquid and then promotes sintering property.
2) V2O5 can improve the corrosion resistance of samples in molten cryolite remarkably. After being eroded for 10 h, the sample with 1.5%V2O5 is in good condition and the corrosion rate of the sample is 1/46 of that of sample without additive.
3) The reasons that V2O5 can improve the corrosion resistance are that liquid promotes the grain to develop completely and Ni2FeVO6 concentrates at grain boundary. The stable structure could control the chemical dissolution of ceramics anode. Ni2FeVO6 has better corrosion resistance than NiFe2O4, so Ni2FeVO6 controls the grain-boundary corrosion rate.
References
[1] PETERSON R D, RICHARDS N E, TABEREAUX A T, KOSKI O H, MORGAN L G, STRACHAN D M. Results of 100 h electrolysis test of a cermet anode: Operational results and industry perspective [C]// CHRISTIAN M B. Light Metals. Warrendale PA: TMS, 1990: 385-393.
[2] PAWLEK R P. Inert anodes: An update [C]// SCHNEIDER W. Light Metals. Warrendale, PA: TMS, 2002: 449-456.
[3] SADOWY D R. Inert anode for the Hall-Héroult cell: The ultimate materials challenge [J]. JOM, 2001, 53(5): 34-35.
[4] OLSEN E, THONSTAD J. Nickel ferrite as inert anodes in aluminium electrolysis (Part I): Material fabrication and preliminary testing [J]. Journal of Applied Electrochemistry, 1999, 29(3): 293-299.
[5] SHI Zhong-ning, XU Jun-li, QIU Zhu-xian, GAO Bing-liang, WANG Zhao-wen. Copper-nickel superalloys as inert alloy anodes for aluminum electrolysis [J]. JOM, 2003, 55(11): 63-65.
[6] GLUCINA M, HYLAND M. Laboratory-scale performance of a binary Cu-Al alloy as an anode for aluminium electrowinning [J]. Corrosion Science, 2006, 48(9): 2457-2469.
[7] YANG Jian-hong, LIU Ye-xiang, WANG Hua-zhang. Behaviour and improvement of SnO2-based inert anodes in aluminium electrolysis [C]// DAS S K. Light Metals. Warrendale, PA: TMS, 1993: 493-495.
[8] ZHANG Lei, JIAO Wan-li, YAO Guang-chun. Preparation of NiFe2O4 inert anode and its electrolysis corrosion mechanism [J]. Journal of the Chinese Ceramic Society, 2005, 33(12): 1431-1436.
[9] LAI Yan-qing, SUN Xiao-gang, LI Jie, DUAN Hua-nan, LI Xin-zheng, ZHANG Gang, TIAN Zhong-liang. Densification of Ni-NiFe2O4 cermets for aluminum electrolysis [J]. Trans Nonferrous Met Soc China, 2005, 15(3): 666-670.
[10] TIAN Zhong-liang, LAI Yan-qing, LI Jie, ZHANG Gang, LIU Ye-xiang. Electrical resistivity of NiFe2O4 ceramic and NiFe2O4 based cermets [J]. Trans Nonferrous Met Soc China, 2004, 14(3): 421-425.
[11] RAY S R. Inert anodes for Hall cells [C]// MILLER R E. Light Metals. Warrendale, PA: TMS, 1986: 287-298.
[12] LAI Yan-qing, TIAN Zhong-liang, LI Jie, YE Shao-long, LI Xin-zheng, LIU Ye-xiang. Results from 100 h electrolysis testing of NiFe2O4 based cermet as inert anode in aluminum reduction [J]. Trans Nonferrous Met Soc China, 2006, 16(4): 970-974.
[13] LUO Tao, WANG Zhao-wen, GAO Bing-liang, YU Xu-guang, SHI Zhong-ning, QIU Zhu-xian. Study on corrosion of cermet inert anode based on nickel ferrite spinel [C]// TRAVIS J G. Light Metals. Warrendale PA: TMS, 2006: 491-493.
[14] LI Jie, DUAN Hua-nan, LAI Yan-qing, TIAN Zhong-liang, LIU Ye-xiang. Effect of NiO content on corrosion behaviour of Ni-xNiO-NiFe2O4 cermets in Na3AlF6-Al2O3 melts [J]. Trans Nonferrous Met Soc China, 2004, 14(3): 421-425.
[15] MARIAK K, ANNA B T. Phase equilibria in the system NiO-V2O5-Fe2O3 in subsolidus area [J]. Therm Anal Calorim, 2004, 77: 65-73.
Foundation item: Project(2006A050) supported by Science and Technology Foundation of China University of Mining and Technology, China; Project (0702058C) supported by Postdoctoral Scientific Research Foundation of Jiangsu Province, China
Corresponding author: XI Jin-hui; Tel: +86-516-83591880; E-mail: xjh825@163.com
(Edited by LI Xiang-qun)