
Numerical simulation of temperature field during gas preheating and start-up of drained aluminum reduction cell
ZHOU Ping(周 萍)1, WANG Zhi-qi(王志奇)2, ZHOU Nai-jun(周乃君)1
1. School of Energy and Power Engineering, Central South University, Changsha 410083, China;
2. School of Mechanical Engineering, Xiangtan University, Xiangtan 411105, China
Received 9 September 2005; accepted 6 March 2006
Abstract: The method of numerical simulation was applied to investigate gas preheating and start-up process in a drained aluminum reduction cell. The transient temperature and velocity fields of a 156 kA drained aluminum reduction cell were numerically calculated. The results show that the method of gas preheating and bake-out can basically meet the technical requirements of the start-up process for the drained cell. If the same distributing scheme of gas nozzle as that in the general cells is used, there are problems of great temperature gradients and low temperature zone at the top of cathode near the side of nozzles. In order to promote the effect of gas preheating and baking the drained cell, the jetting angle of end nozzle is adjusted and the temperature distribution in the drained cell is obviously improved. By means of simulating the temperature field in the case that jetting angle varies from 0? to 30?, it is concluded that better temperature distribution can be obtained if the jetting angle of end nozzle is approximately 15?.
Key words: drained cell; aluminum reduction cell; gas preheating; start-up; temperature field; numerical simulation
1 Introduction
The drained aluminum reduction cell is a new type cell and it is predicted that it can reduce the voltage of the cell 0.6 V and save the consumption of direct current 2400 kW×h/t, compared with the general cells[1,2]. Therefore, more and more attention is devoted to the study of drained aluminum reduction cell in recent years [3-7].
As for the general cells, the method of preheating and bake-out in a drained cell plays a significant role in the cell life. Among all factors influencing the cell life, its contribution to the total cell life is about 25%[8, 9]. The effects of preheating cathode lie in avoiding flash pyrolysis and rapid gas evolution from ramming paste, avoiding uneven current distribution because of bath freezing in the anode-cathode interspace. Bottom failure due to improper cell preheating practices may happen as early as on the stage of baking or during start-up of the cell.
There are two basically different methods that are commonly used to preheat aluminum cells, flue gas heating by combusting oil or gas, or ohmic heating by passing electrical current through the cell (such as coke preheating, graphite powder preheating)[10,11]. At present, since the equipment for flue gas preheating is too complicated, its application is limited, and the method of coke preheating and bake-out is employed more widely in the general cells. The latter demands that the surface of cathode and the undersurface of the anode are fairly flat[12]. However, in the drained cell, the surface of cathode is made into slope shape and some depositing grooves are cut on it. If the method of coke preheating and bake-out is used, it is difficult to make coke or graphite powder distribute evenly on the surface of the cathode and in the depositing grooves. These will result in early failure of cells easily and reduce the cell life. So, it is predictable that the gas preheating method is more suitable for the drained aluminum reduction cell.
The drained cell wasn’t put forward until 1980s. A lot of investigations on the drained cell are still needed for its industrial production and one of these is preheating and bake-out during its start-up. In this paper,based on the studying experiences in general cells[13,14], the method of mathematical simulation is employed to research into the preheating and bake-out in the drained cell. By means of analyzing its temperature distribution, the feasibility of gas preheating and bake-out is estimated and the angle of nozzles is optimized, which will offer theory foundation for the industrialization of the drained cell.
2 Physical and mathematical model, initial and boundary conditions
2.1 Physical model
Take the 156 kA drained aluminum reduction cell as study object. A wider depositing groove is cut at the middle of cathode in the long axial direction, four narrower grooves are evenly cut in the cathode in the short axial direction, and four narrower grooves are cut around the cathode. Their cross sections have the shape of rectangle. If the whole cell is simulated, too much grids are needed and a lot of calculating time is cost because of its quite large volume and quite complicated construction. Considering the symmetry of the cell structure and the nozzle position, a half of the cell in the long axial direction is taken to be simulating model. The sketch of the drained cell is shown as Fig.1.
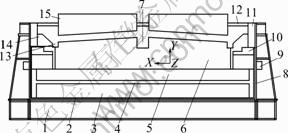
Fig.1 Schematic structure of 156 kA drained cell in short axis direction (vertical section): 1 Cradle and shell; 2 Calciumsili- cate plate; 3 Thermal insulating brick; 4 Alumina; 5 Impervious material; 6 Carbon cathode with TiB2 coat; 7 Middle depositing groove; 8 Steelshell; 9 Cathode steel bar; 10 Refractory; 11 Sidewall carbon; 12 Electrolyte crust; 13 Side depositing groove; 14 Ramming paste; 15 Carbon anode
In order to make the temperature field in the cell more real, the following characteristics are taken into account during developing physical model.
1) Real geometrical model. The cell is made of over 10 types of materials and their sizes are very different.
2) Nonlinear and anisotropic thermo-physical properties of material. During preheating and baking process, the temperature of the cell changes greatly with the increasing of preheating time. Meanwhile the thermo-physical properties of material change with temperature. Moreover, the thermo-physical properties of the material made of carbon are often anisotropic.
2.2 Mathematical model
In the gas preheating system, oil or natural gas is burnt in compact combusting equipment, the flue gas with high temperature is gotten and its temperature is controlled according to the preheating technical demand. The flue gas is jetted to the cell between the anode and cathode. So, there are mainly heat and momentum transfer during the preheating process, which can be described by the following general equation:
(1)
where ρ is the density, U is the velocity vector, and Γφ is the diffusive coefficient. In the above equation, the replacement of
with value of 1 gives the continuity equation, while for
and H, the momentum and enthalpy equations are obtained respectively.
denotes the source terms and in enthalpy equation, it is the source terms caused by radiative heat transfer or the sink terms caused by the vaporization of water in ramming paste. k-ε turbulent model is applied in the calculation[15].
2.3 Boundary conditions
The inlet velocity and temperature of the flue gas are determined by the preheating and bake-out technique. At the initial time, the inlet velocity and temperature of the gas flue are 5 m/s and 773 K, respectively. After preheating 72 h, they are 30.2 m/s and 1 493 K. The varying function as preheating time is as following[16].
(2)
where Tin and uin are the inlet temperature and velocity, t is the preheating time.
The heat transfer of the cell surfaces, the electrolyte crust and anodes are treated as the third boundary condition. The total coefficient of the heat transfer is calculated in terms of the following formula[17]:
(3)
where αWA denotes the total coefficient of the heat transfer, TW the surface temperature, TA the environmental temperature, σ0 Stefan-Boltzmann constant and εW the emissivity. α is the heat transfer coefficient of the natural convection between the surface and environment, and it has different calculating formula with different direction of the surface.
Top surface:
α=1.52(TW-TA)1/3 (4)
Vertical surface:
α=1.31(TW-TA)1/3 (5)
Bottom surface:
α=0.58[(TW-TA)1/3/L]1/3 (6)
where L is the length of shorter side on the surface.
2.4 Initial conditions
The initial temperature is assumed to be the environmental temperature, i.e. 30 ℃.
3 Simulating results and discussion
Uneven multi-block structural grids are taken and the whole computational region consists of 185 000 meshes. ANSYS software is applied to simulate the velocity and temperature fields during gas preheating and start-up process in a drained aluminum reduction cell.
3.1 Results of cells with same nozzles distribution as general cells
The major results of mathematical simulation are shown in Figs.2-5.
It is known from Fig.2 that the average temperature at the top and bottom surfaces of the cathode is approximately in direct proportion to preheating time. With the increase of preheating time, the rate of temperature rising decrease a little because of the non-linear increase of the heat flux loss.
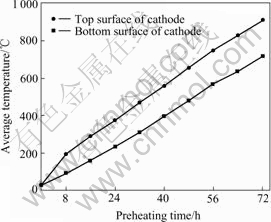
Fig.2 Average temperature vs preheating time
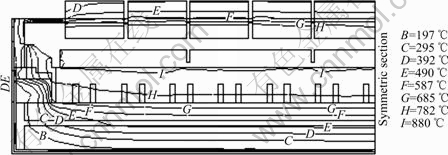
Fig.3 Temperature contours at vertical section of cell after preheating 72 h
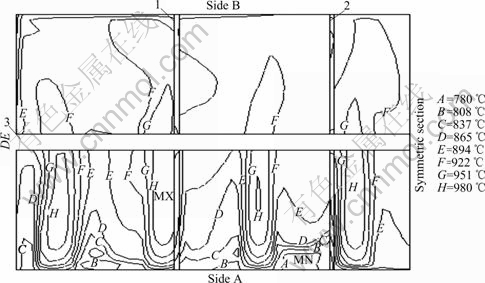
Fig.4 Temperature contours at top of cathode after preheating 72 h (1,2 and 3 are depositing grooves)
Fig.2 and Fig.3 show that, after preheating 72 h, the average temperature at the top and bottom of the cathode are over 900 ℃ and 700 ℃, respectively, and the average temperature at the bottom steel shell is about 65℃. The results indicate that the method of gas preheating and baking cell is able to meet the technical demand[18]. Moreover, the average temperature of ramming paste in the side of the cell is 722.3 ℃, which illuminates the ramming paste is baked fully and this is also one of the important characteristics of the gas preheating method.
It is found from Fig.4 and Fig.5 that, after preheating 72h, the temperature distribution at the bottom of cathode is evener than that at the top of the cathode and the greatest temperature gradient appears at the top of the cathode. Meanwhile, the temperature distribution in the nozzle side in the drained cell is not even as that in the general cells because of the effects of the depositing grooves.
3.2 Optimization of nozzles angle
To improve the temperature distribution at the top of cathode, the angle of nozzle near duct end is adjusted, that is, it leans slightly to duct end from paralleling duct end. Part of gas can flow into the depositing groove at the nozzle side and raise the temperature at this part. So, the angle between the end nozzle and the short axis is assumed to be 0? (that is the case of 3.1), 10?, 15?, 20? and 30?. The temperature field simulation in the cell with different angle was carried out and the main results are show in Table 1.
It is obvious that the maximum of temperature difference at the top of cathode is lowered,and the average temperature of top cathode, bottom cathode, the depositing grooves and the ramming paste are increased, when the angle of end nozzle varies from 0? to 30?. But when the angle is 15?, the maximum of temperature difference at the top of cathode is the least, which indicates that this case is more beneficial to the preheating and baking of the drained cell. The reason is that with increasing the angle of the end nozzle slowly, part of gas flows into the depositing groove at the side of the nozzle from the end depositing groove, which is help for enhancing the temperature distribution, and with increasing the angle of the end nozzle continuously, part of gas is jetted towards the side carbon and rebounded, in this way, less gas can flow into the depositing groove and towards the other side of nozzle side, which is disadvantageous to improving the temperature distribu- tion further.
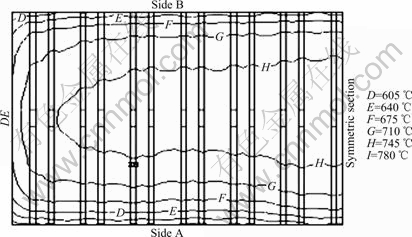
Fig.5 Temperature contours at bottom of cathode after preheating 72 h
Table 1 Main simulating results with different angle of end nozzle
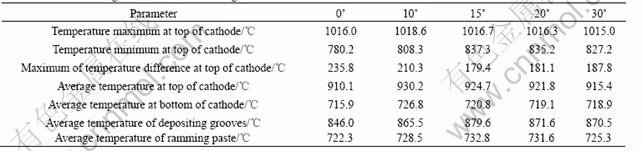
4 Conclusions
1) The method of gas flue preheating and baking the drained aluminum reduction cell can meet the technical requirement.
2) Compared with the method of coke preheating and baking the cell, the ramming paste is baked better by using the method of gas flue preheating and baking.
3) The gas flow in the drained cell with the depositing grooves is more complicated than that in the general cell. To obtain better baking quality of the drained cell, the distributing scheme of the nozzles should be optimized further on the base of that used in the general cell.
References
[1] BROWN G D, HARDIE G J, SHAW R W, et al. TiB2 coated aluminum reduction cells: Status and future direction of coated in Comalco [A]. Welch B. Aluminium Smelting Conference[C]. New Zealand: Queenstown, 1998. 529-538.
[2] ZHOU Nai-jun, LI Jie. The technology advance and application research of the drained aluminum reduction cells [J]. Light Metals, 2000(9): 29-31. (in Chinese)
[3] VITTORIO D N, NASSAU. B, JAINAGESH A S. Method for production of aluminum using protected carbon-containing components [P]. US Patent: 5651874. 1997.
[4] GEORGES B, SIERRE C H. Aluminum Production Cell and Cathode[P]. US Patent: 6358393. 2002.
[5] LIU Ye-xiang, LI Xiang-peng, LI Jie, LAI Yan-qing. Calculation of thermal stress distribution in drained aluminum reduction cell cathode and its structural optimization [J]. J Cent South Univ Technol, 2004, 35(6): 869-874. (in Chinese)
[6] LIU Ye-xiang, LI Xiang-peng, LAI Yan-qing, LI Jie, ZHOU Xiang-yang, ZHAO Heng-qin. Heat balance simulation of drained aluminum reduction cell [J]. Trans Nonferrous Met Soc China, 2003, 13(5): 1119-1202.
[7] ZHOU Nai-jun, MEI Chi, JIANG Chang-wei, LI Jie. A method of determining and designing the drained slope in drained aluminum reduction cells [J]. J Cent South Univ Technol, 2003, 10(1): 74-77.
[8] DESILETS M, MARCEAU D, FAFARD M. Start-curve: Thermo-electro-mechanical transient simulation applied to electrical preheating of a Hall-Heroult cell [A]. Crepeau P N. Proceedings of the Technical Sessions (132th TMS Annual Meeting, Light Metals) [C]. Warrendale: AIME, 2003. 247-253.
[9] CHEN Zhu, LI Qian-yu, LAI Yan-qing. Effects of preheating and start up procedure on potlife of prebaked anode aluminum reduction cell [J]. Mining and Metallurgical Engineering, 2002, 22(4): 76-78. (in Chinese)
[10] BENTZEN H, HVISTENDAHL J, JENSEN M. Gas preheating and start of soderberg cells [A]. Rooy E L. Proceedings of the Technical Sessions (120th TMS Annual Meeting, Light Metals) [C]. Warrendale: AIME, 1991: 741-747.
[11] LIU Yong-gang, TANG Qian, LIANG Tao. Comparison among four preheating methods in large prebaked aluminum reduction cells [J]. Light Metals, 2000(4): 32-35. (in Chinese)
[12] GAN Yi-ren. The technical keys and operating method on the coke preheating in aluminum reduction cells [J]. Light Metals, 2001(9): 40-43. (in Chinese)
[13] SUN Yang, WANG Qian-pu, RYE K A, SORLIE M, OYE H A. Modeling of thermal and sodium expansion in prebaked aluminum reduction cells [A]. Crepeau P N. Proceedings of the Technical Sessions (132th TMS Annual Meeting, Light Metals) [C]. Warrendale: AIME, 2003. 603-610.
[14] GOULET P, LABERGE C, LACROIX R, KISS L I, PERRON J. Modeling of the coke bed used in the electrical preheat of an aluminum reduction cell [A]. Crepeau P N. Proceedings of the Technical Sessions (132th TMS Annual Meeting, Light Metals) [C]. Warrendale: AIME, 2003. 263-268.
[15] QIN Ke-fa, FAN Jian-ren. Theory and Calculation of Gas-Solid Multi-Phase Flow in Engineering [M]. Hangzhou: Zhejiang University Press, 1990. (in Chinese)
[16] WU Cheng-bo, YIN En-sheng, ZHANG Li, LIU Yang-gang, ZHANG Bing-huai, TANG Qian. Numerical simulation of three-dimensional temperature field of gas start up method for aluminum electrolysis cell [J]. The Chinese Journal of Nonferrous Metals, 2003, 13(6): 1534-1539. (in Chinese)
[17] LUO Hai-yan, LU Ji-dong, HUANG Lai, WU Jun-qi. 3D thermo-electric analysis of the aluminum reduction cell [J]. J Huazhong Univ of Sci & Tech, 2002, 30(7): 4-7. (in Chinese)
[18] GONG Chun-lei, LI Xiao-bo, LIU Gang. On the technical scheme and practice for prolonging the life of aluminum reduction cell [J]. Non-ferrous Smelting, 2003, 32(6): 13-16. (in Chinese)
(Edited by YUAN Sai-qian)
Foundation item: Project(G1999064903) supported by the National Basic Research Program of China
Corresponding author: ZHOU Ping; Tel: +86-731-8830897; Fax: +86-731-8879863; E-mail: zhoup@mail.csu.edu.cn