
Microstructure of reactive sintered Al bonded Si3N4-SiC ceramics
CUI Chong(崔 崇), WANG Yuan-ting(王媛婷), JIANG Jin-guo(江金国), CHEN Guang(陈 光), SUN Qiang-jin(孙强金)
Department of Materials Science and Engineering, Nanjing University of Science and Technology,
Nanjing 210094, China
Received 20 April 2006; accepted 30 June 2006
Abstract: Aluminium nitride-silicon nitride-silicon carbide (AlN-Si3N4-SiC) composite ceramics were prepared to increase the bending strength and improve the phase structure of Si3N4-based ceramics. The ceramics were made by reactive sintering in N2 atmosphere at 1 360 ℃, using Al as sintering additive. The phase composing of ceramics was identified with an X-ray diffractometer and the microstructure of the materials was studied by scanning electron microscopy. The results indicate that the phase structure is affected remarkably and the interface modality is changed. The interface between Si3N4 and SiC becomes blurry and that between SiC and AlN matches more better at the same time. But the liquid-phase appears during the reactive sintering along with the addition of Al by which the melting point of Si is decreased. The appearance of liquid Si decreases the bending strength of the ceramics. Lower temperature nitrification technic was introduced to avoid the appearance of liquid-phase Si. The optimum addition of Al was investigated by XRD and SEM analysis in order to obtain the maximal bending strength of materials.
Key words: Al; Si3N4-SiC; microstructure; bending strength; reactive sintering
1 Introduction
In recent years, reactive sintered Si3N4-SiC ceramic materials with excellent oxidation resistance, high corrosion resistance, high wear resistance, and high temperature resistance etc have been used widely. But it is a common phenomenon that the strength of reactive sintered ceramics is relative low. The interface between Si3N4 and SiC as well as the low volume density are conditionality factors of improving the mechanical properties of the Si3N4-SiC ceramic materials. The interface between Si3N4 and SiC limits the addition of SiC and increases intergranular fracture trend of materials. Reactive sintered Al bonded Si3N4-SiC ceramics improve the mechanical properties and the interface combinative modality of the Si3N4-SiC ceramic materials. So it is hoped to replace current used reactive sintered Si3N4 based ceramics.
In this paper, aluminium nitride-silicon nitride- silicon carbide (AlN-Si3N4-SiC) composite ceramics were made by reactive sintering in N2 atmosphere at 1 360 ℃, using Al, Si and SiC as raw materials[1]. The influence on the phase compose and microstructure along with the addition of Al was also discussed.
2 Experimental
Al, SiC and Si powders were used as raw materials. Eight different systems of sintering additives were used in this study. Kept the proportion of Si to SiC of 7 to 3, and Al from 0 to 8. The starting powders were mixed for 2 h using absolute alcohol solvent in a steel jar, and 1Cr18Ni9Ti balls were used as the milling media. After ball milling, the slurry was dried by using an evaporator. PVA was used as mixed binder. Dry-pressing experiments were carried out under applied pressure of 100 MPa. Lower temperature nitrification sintering were carried out at 700-1 000 ℃ and then reactive sintering were carried out at 1 360 ℃ for 5 h.
The phases of sample were identified by X-ray diffraction analysis(2038-X). Three specimens of 55 mm×10 mm×8 mm in dimension were prepared for flexural tests. The surface between Si3N4 and SiC and fractured surface of specimen were observed by scanning electron microscopy (JEOL JSM-6380LV).
3 Results and discussion
3.1 X-ray and SEM analyses
X-ray diffraction patterns from Si3N4-SiC and AlN-Si3N4-SiC(Al:Si:SiC=4:7:3) ceramic samples are shown in Fig.1 and Fig.2. Major phases of Si3N4-SiC materials are α-Si3N4, β-Si3N4 and SiC. For AlN-Si3N4- SiC samples, α-Si3N4, β-Si3N4, SiC, AlN and Si are major phases. This reveals that Al changes into AlN and Si changes into Si3N4 after the reactive sintering process. But some Si remain in the samples.
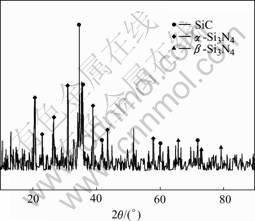
Fig.1 XRD patterns of Si3N4-SiC
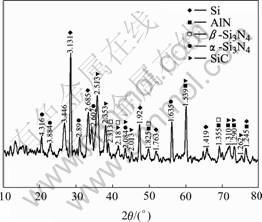
Fig.2 XRD patterns of AlN-Si3N4-SiC(Al:Si:SiC=4:7:3)
SEM micrographs of samples are shown in Figs.3-6. Fig.3 shows the micrograph of Si3N4-SiC ceramic. In Fig.3, the gray bulk substance is micron SiC, the bright substance around is Si3N4 matrix. SiC particles inhomogenously distribute in Si3N4 matrix. The interface between SiC and Si3N4 is clear. The existences of SiC/Si3N4 interface have influence on the strength of materials. The micrograph of AlN- Si3N4-SiC ceramics is shown in Fig.4. In Fig.4, Si3N4 matrix is more close-knit. The pores in the Si3N4 matrix are filled with fibroid AlN crystals. The interface between SiC and Si3N4 is blurry compared to that without the addition of Al. SEM micrograph for fibroid AlN crystal in the low nitride temperature sample is shown in Fig.5. A good number of fibroid AlN crystals forms in the nitride process between 700 ℃ and 1 000 ℃. The formation of AlN can increase the density of the Si3N4 ceramics and decrease the sintering temperature. The addition of Al decreases the melting point of Si which melts in the high temperature nitride process and forms liquid phase Si, as shown in Fig.6. In the picture, the bright retained Si in the samples can be seen very clearly. Fig.7 shows that Al and Si can form liquid phase at the eutectic temperature (577 ℃)[2]. With increasing temperature, more and more Si melts and form liquid colony. The nitrification of Si will be prevented and retained Si still exists in the samples. Liquid phase Si is a brittle phase in the materials. It will decrease the bending strength of ceramics. With increasing Al content, more liquid Si forms at the same
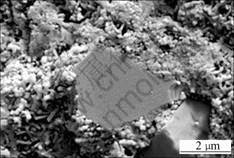
Fig.3 SEM micrograph of interface between SiC and Si3N4 without addition of Al
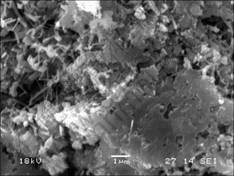
Fig.4 SEM micrograph of interface between SiC and Si3N4 with addition of Al
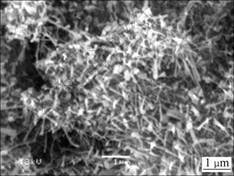
Fig.5 SEM micrograph of fibroid AlN crystal in low nitride temperature sample
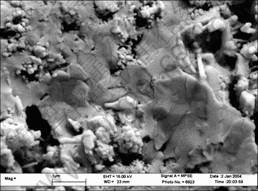
Fig.6 SEM micrograph of melted Si in sample AlN-Si3N4
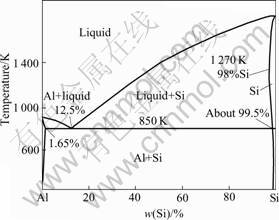
Fig.7 Phase diagram of binary Al-Si
temperature. Lower temperature nitrification technic will be able to avoid these phenomena. Heat preservation at the melting point of Si was carried to make AlN from Al. Si is surrounded by AlN and will not conglomerate into liquid phase Si.
3.2 Bending strength
Bending strength for all samples as a function of Al content is shown in Fig.8. Samples doped with Al exhibit higher strength at room temperature. The sample (Al:Si:SiC=4:7:3) especially shows average strength of 146 MPa and maximum strength of 179 MPa. This scattering of strength in the samples is attributed to the processing defects, such as Si agglomerates, inclusions. Bending strength degradation occurs above Al content being 4. When Al content achieves 6, the effect of strengthening with addition of Al is not obvious because Si prevents from advancing the strength of materials.
3.3 Reaction mechanism
SiC does not participate in the reaction during the formation process of AlN-Si3N4-SiC composite ceramic. With the increasing temperature, Al and Si can transform to AlN and Si3N4 with nitrogen respectively.
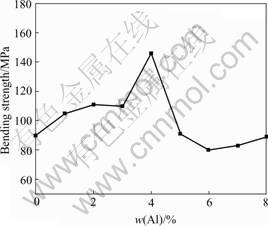
Fig.8 Al content dependence on bending strength for AlN- Si3N4-SiC ceramic material
The reaction of Al and N2 can be shown as
Al+N2→AlN
Actually, the nitridation reaction has already taken place slowly before the melting of Al. A layer of AlN forms on the surface of Al grains in the initial stage of reaction. N2 can diffuse through the nitride film because the AlN grains new formed are very fine and loose. The micro-cracks can form for the great stress caused by thermo expanding mismatching and pressure related with the curvature of nitride films in the nitride films and then the nitridation reaction can further progress[3]. Because the grain sizes are bigger than critical size, the nitridation reaction carries on by nitrogen ions diffusing through the micro-cracks. For the smaller grains, it is by nitrogen diffusing through the macro-cracks in the nitride film.
After the melting of Al, the nitridation speed increases. The pressure in the nitride films increases constantly with the expanding volume of Al melting and nitridation. When the pressure exceeds the strength of the nitride films, melting Al can enter the nearby grain holes through the micro-cracks. These melting Al will be surrounded by N2 and they can surround the Si and SiC grains. At the moment the nitridation reaction of Si has not started. The melting Al outside of Si grains still continues the reaction, but the reaction speed is slow because new phases are formed by gas-liquid diffusion.
With the increasing temperature, Si starts to react with N2 and Si3N4 formed. Since there are water and oxygen in industrial nitrogen, they could react with Si as
Si(s)+1/2O2(g)→SiO(g)
Si(s)+H2O(g)→SiO(g)+H2(g)
3SiO(g)+2N2(g)→Si3N4(s)+3/2O2(g) [4]
The diffusing process of N2 in Si3N4 is controlled by the diffusion speed. α-Si3N4 fibers form on the surface of raw materials by the gas-liquid-solid mechanism and β-Si3N4 phases formed at the same time[5]. H2 in the reacting gases and impurities in the raw materials such as Fe have reductive effects at high temperature and they destroy SiO2 on the surface of Si and SiC particles. Si can react with H2O and O2 brought by industrial N2 and transform to SiO. Adding a small quantity of H2 can increase the SiO concentration and then SiO can react with N2 and α-Si3N4 formed. This process is very slow. At the same time, AlN has bigger diffusion modulus and higher vapor tension, so the transplant rate of AlN to particle SiC is faster than the converse transplant rate. AlN could extend to SiC grain surfaces earlier and grow with SiC particles together[6]. With increasing tempera- ture, plenty of melting Si limits the nitridation of Si. The increasing melting Si exists in the ceramics along with the content of increasing Al at the same temperature. Many β-Si3N4 phases form because of the existence of the liquid phases in Si which takes part in the reaction[7].
4 Conclusions
1) The interface between Si3N4 and SiC is improved effectively by adding Al to the Si3N4-SiC ceramic. The addition of Al eliminates the interface limitation’s influence on the properties of materials and increases the SiC content.
2) Liquid Si content increases with Al content at the same temperature. Liquid Si forms brittle phase in the center of ceramic and decreases mechanical properties of materials. So the Al content should be controlled.
References
[1] CUI Chong, WANG Yuan-ting. Preparation of AlN-Si3N4-SiC Composite Ceramic Materials [P]. CN 200510041261.9, 2005-07- 29.
[2] MONDOLFO L F. Aluminum Alloys [M]. Beijing: Metallurgical Industry Press, 1988.
[3] CAI Ke-feng, NAN Ce-wen. Mechanism of reaction bonding AlN-Al2O3 composite [J]. Journal of the Chinese Ceramic Society, 1996, 2: 216-221.(in Chinese)
[4] ATKINSON A, MOULSON A M. Nitridation of high purity sicicon [J]. Journal of American Ceramic Society, 1976(7-8): 286-289.
[5] JENNINGS H M, RICHMAN M H. Microstructural analysis of reaction-bonded silicon nitride [J]. Metallography, 1976(10): 427-446.
[6] PAN Y B, QIN J H, MORITA M, et al. J Mater Sci, 1998, 33(5): 1238.
[7] SUTTON G P. Rocket Propulision Elements [M]. Beijing: National Defence Industry Press, 1966.
(Edited by LI Xiang-qun)
Corresponding author: CUI Chong; E-mail: cuichong@mail.njust.edu.cn