J. Cent. South Univ. Technol. (2011) 18: 1349-1353
DOI: 10.1007/s11771-011-0844-x
Influence of thermomechanical aging on microstructure and mechanical properties of 2519A aluminum alloy
WANG Hui-min(王会敏), XIA Chang-qing(夏长清), LEI Pan(雷攀), WANG Zhi-wei(王志伟)
School of Materials Science and Engineering, Central South University, Changsha 410083, China
? Central South University Press and Springer-Verlag Berlin Heidelberg 2011
Abstract: The influence of thermomechanical aging on microstructure and mechanical properties of 2519A aluminum alloy was investigated by means of microhardness test, tensile test, optical microscopy (OM) and transmission electron microscopy (TEM). The results show that 50% cold rolling deformation prior to aging is beneficial since it promotes a more homogeneous distribution of the precipitation phase and reduces the number of precipitation phase on the grain boundaries, and thus shrinks the total volume of precipitation-free zones at grain and sub-grain boundaries. As a result, the tensile properties of 2519A aluminum alloy have been significantly improved.
Key words: pre-aging deformation; precipitation hardening; tensile properties; aluminum alloys
1 Introduction
Aluminum alloys have been the primary materials for structural components of military aircrafts, helicopters, amphibians, etc. for several decades. This is because of the low density of aluminum which favors the selection of aluminum alloys in weight-critical applications [1]. 2519 aluminum alloys used as armor plates have good weldability, acceptable ballistic resistance and mechanica1 properties as wel1 as resistance to stress corrosion cracking [2-4].
To meet all these requirements, an improved understanding of the relationship between composition, processing, microstructure and properties is required. In particular importance, microstructural features for control are: size, coherence, volume fraction and distribution of strengthening precipitates, degree of recrystallization, grain size and shape, crystallographic texture as well as the presence of intermetallic constituent particles. By thermo-mechanical aging (TMA) treatments, it is possible to develop a dislocation substructure which can control the coarsening of second-phase precipitate particles even after long exposures at elevated temperature and such dislocation arrangement is responsible for improvement in the overall properties of aluminum alloys [5-7]. The reasons suggested for improvement in tensile properties are: 1) introducing a particular type of dislocation substructure [6]; 2) optimizing the precipitate size and shape [8]; 3) producing a homogeneous distribution of dislocations and precipitated particles [9].
Quantitative determination of the precipitate size is a key aspect for understanding the precipitate size effect. Once these data are known, the mechanical properties of 2519A aluminum alloy can be easily estimated. Moreover, an understanding of the precipitate size evolution favors better microstructural design in terms of the stability of microstructure corresponding to different deformation or aging temperature. This work was attempted to find microstructural reasons (if any) of improvement in tensile properties.
2 Experimental
The experimental 2519A aluminum alloy plate was prepared by melting intermediate alloys and homogenizing at 510 °C for 20 h. Subsequently, the plate was solution-treated for 1 h at 525 °C and then water quenched. At last, the plate was cold rolled by different deformation ratios (0%, 15%, 50%) before artificial aging at 165 °C for various time. The chemical composition of the experimental alloy is given in Table 1.
Vickers hardness measurement was carried out on all aged samples. The samples with the highest hardness were selected for TEM investigation. The disks were subsequently ground down to about 0.08-0.1 mm and electro-polished in a solution of 70% ethanol and 30% nitric acid solution at about -25 °C, using double-jet equipment operated at a voltage of 15 V. The mechanical test was performed on an universal tensile testing machine of CSS-44100 type at room temperature. OM and TEM were applied to characterize the microstructure of the peak-aged alloys with different deformation ratios.
Table 1 Measured composition of 2519A (mass fraction, %)

3 Results and discussion
3.1 Aging curve
Figure 1 shows the Vickers hardness (HV) curves of the experimental 2519A aluminum alloys. All the alloys show the same trend of hardness variation with aging time. That is, the micro-hardness increases when the aging time increases and then decreases after the hardness reaches the peak value. For the aging alloy at 165 °C, aging hardening rate and the Vickers hardness increase with the deformation ratio increasing. The peak hardness of the alloy with 15% cold deformation is HV 142 at 165 °C, which is increased by HV15 compared with that of alloy without deformation. Accordingly, the time reaching the peak value is shortened from 12 h to 9 h. When the deformation is further increased to 50%, the peak hardness reaches HV 166. Meanwhile, the peak- aging time is only 6 h.
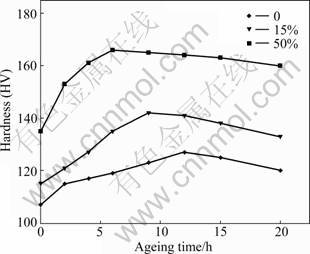
Fig.1 Hardening curves of alloy aged at 165 °C
3.2 Tensile properties
Tensile properties of different deformation alloys after peak aging are listed in Table 2. The tensile strength increases from 437 MPa to 496 MPa and yield strength increases from 375 MPa to 454 MPa at room temperature when the deformation is increased up to 15%. When the deformation is further increased to 50%, the tensile strength and yield strength increases to 547 MPa and 515 MPa, respectively. With increasing deformation in the alloys, the elongation is gradually reduced from 15% to 9%. It could be concluded that increasing deformation can increase the room temperature strength but decrease the elongation of 2519A aluminum alloy.
Table 2 Tensile properties of experimental alloy
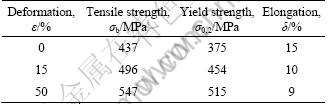
3.3 Optical microscopy observation
Figure 2 shows typical grain structure of the peak- aging alloys. The grain structure of the experimental alloys is mainly modified by pre-deformation while subsequent aging exerts little effect. From Fig.2, it is clear that complete recrystallization occurs in the alloys. The recrystallized grains without deformation are larger than those of the deformed alloys. Furthermore, because the alloys are cold rolled again with different strains after quenching (called T8 treatment), some areas of the alloys appear obvious fine second phase particles. According to these results, it can be concluded that the size of recrystallized grains could be controlled by the cold rolling reduction.
3.4 TEM observation
The TEM microstructures of the experimental alloys peak aged are shown in Fig.3. Regardless of the differences in deformation prior to aging, the microstructures in all examined samples are similar. Figure 3 shows a microstructure characterization of semi-coherent θ′ precipitates. These Cu-rich θ′ precipitates lie on {100} planes of Al matrix, having a perpendicular needle morphology, and homogeneously distribute in the matrix. Compared with those of alloy without deformation, the alloy with 50% deformation treatment yields finer θ′ precipitates (Fig.3(b)). The average diameter of θ′ phase after various treatments have been estimated from TEM. The average diameter of the peak aged alloy without deformation is 80 nm, and that of the 50% deformation is 30 nm. The presence of fine θ' particles in the deformed structure is considered to be conducive to the enhancement of the tensile properties. It is believed that more complex deformation mode prior to the aging in such samples is beneficial to more homogeneous distribution of Cu-rich precipitates.
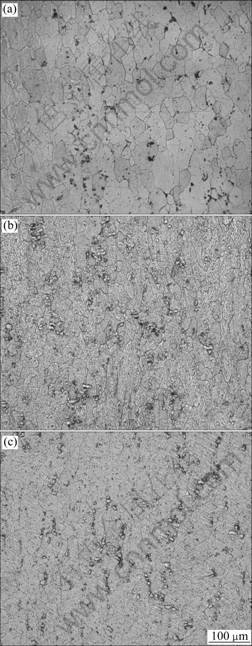
Fig.2 Optical micrographs of 2519A aluminum alloy deformed at 0% (a), 15% (b) and 50% (c)
Samples of experimental alloys exhibit precipitates on grain boundaries and sub-grain boundaries. These precipitates are usually Cu-rich (probably semi- coherent θ′ or incoherent θ (Al2Cu) phase). A typical feature of such a microstructure is the presence of precipitation-free zones (PFZ) along the grain boundaries and grain boundaries precipitate (GBP), as shown in Fig.4. By comparing Fig.4(a) with Fig.4(b), PFZ are narrower in the 50% deformation treatment alloy. The width of PFZ reduces sharply from 80 nm to 40 nm. The precipitates and high-density dislocations are observed near the grain boundaries (see Fig.4(b)). Meanwhile, the number of θ'(θ) phase decreases on the grain boundaries, the θ'(θ) phase distributes in a more discrete manner and the total volume of precipitation free zones at grain boundaries is shrinked.
4 Discussion
The present study shows that the deformation greatly affects the microstructure and properties of the 25l9A aluminum alloy. With the increase of deformation, the size and density of the predominant hardening phase of θ′ phase are changed after peak-aging at 165 °C. For example, both the microhardness and tensile strength are improved with the increase of deformation. It is obvious that the density of θ′ phase in the experimental alloy increases. These fine phases hinder dislocation movement, increasing the tensile strength of the experimental alloy. However, with the increase of strength, the elongation decreases gradually.
2519A aluminum alloy is a typical age-hardenable alloy which is strengthened by the semi-coherent fine θ′ phase (Al2Cu). A new interpretation of the precipitation behavior is established in an Al-Cu alloy as: supersaturated solid solution (SSSS)→quenched clusters →GP zone (I)→GP zone (II)→θ" (independent of GP zone (II))→θ′→stable θ [10]. In the previous work [11], θ′, θ and GP zone precipitate reflections and typical double diffraction relative to the aluminum matrix in 2519A aluminum alloy were successfully summarized. The appearance of θ′ precipitates promotes greater strengthening and promising mechanical properties at ambient temperature because of the deformation resistance. At the same time, the degree of θ′ precipitation strengthening depends on their size, mean interparticle spacing, volume fraction and their distribution in the matrix. All these factors are interrelated. Pre-aging deformation promotes a more homogeneous distribution and reduces the number of the precipitate phase on the grain boundaries and thus shrinks the total volume of precipitation-free zone at grain and sub-grain boundaries. Moreover, the Cu content within the PFZ is lower than that in the surrounding matrix and does not exceed 2% (mass fraction). According to the literature, the difference in electro-chemical potentials between the Cu-depleted zone and the Cu-rich matrix forms a strong galvanic cell with a potential difference of about 0.12 V [12]. Compared with the area of the cathodic matrix, the anodic Cu-depleted zone is small in area, thus leading to a high driving force for rapid intergranular corrosion. Stress is likely to be concentrated in the zones because they are relatively soft. It is believed that the resistance to the corrosion cracking is inversely proportional to the total volume of precipitation-free zones. The tensile test shows that the tensile strength of the experimental alloys increases from 437 MPa (without deformation) to 547 MPa (50% TMA treatment). The results also demonstrate that the TMA is beneficial for strength.
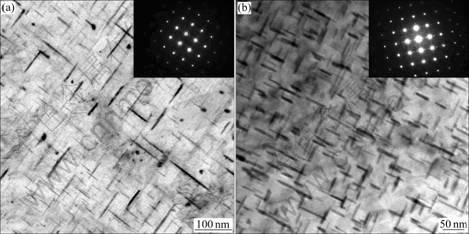
Fig.3 Morphologies of θ′ precipitates in experimental alloys deformed at 0% (a) and 50% (b)
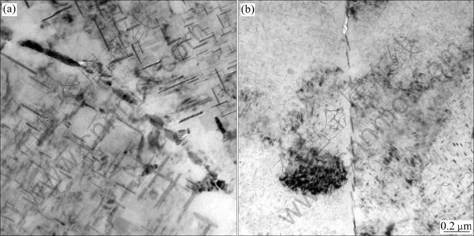
Fig.4 Precipitates-free zones at grain boundary of 2519A aluminum alloy deformed at 0% (a) and 50% (b)
In the 50% TMA treatments samples, the peak hardness is associated only with θ′ as no evidence of θ″ precipitates is observed in these samples. Because the diameter of θ' precipitates in all the aged samples is less than 80 nm, it appears that the strengthening after TMA treatments would be significantly governed by the nature of dislocation substructures. This is in agreement with the observations of DOHERTY and MARTIN [13] that recrystallization in A1-Cu alloys containing
phase is slowed down when the inter-particle spacing is less than 1 μm. Neither Mn-rich nor Mg-rich precipitates are found at grain boundaries. This means that the anticipated roles of Mg and Mn to modify the precipitation process of the precipitate phase, thus resulting in a greater age-hardening effect, come up to expectations.
In light of the above discussion and on the basis of TEM observations, it is concluded that the TMA treatment not only provides maximum strengthening to 2519A aluminum alloy but also provides a more homogeneous distribution of the θ′ precipitates which is effective in strengthening the tensile strength at room temperature.
5 Conclusions
1) The general strengthening of the alloy is attributed mainly to the existence of
and dislocation precipitate tangles. In the peak-aged material, the hardening occurs predominantly due to
precipitates, whereas TMA treatment promotes a more homogeneous distribution of
precipitate and yields finer
precipitates.
2) TMA treatment is effective in strengthening the tensile properties at room temperatures. Moreover, TMA treatment reduces the number of precipitates on the grain boundaries and thus shrinks the total volume of precipitation-free zones at grain and sub-grain boundaries. Meanwhile, the deformation prior to aging can speed up the aging hardening and improve the tensile properties of 2519A aluminum alloy.
References
[1] STARKE E A, Jr STALEY J T. Application of modern aluminum alloys to aircraft [J]. Progress in Aerospace Sciences, 1996, 32(2/3): 131-172.
[2] DYMEK S, DOLLAR M. TEM investigation of age hardenable Al 2519 alloy subjected to stress corrosion cracking tests [J]. Materials Chemistry and Physics, 2003, 8l(2/3): 286-288.
[3] KRAMER L S, BLAIR T, BLOUGH S D. Stress-corosion cracking susceptibility of various product forms of aluminum alloy 2519 [J]. Journal of Materials Engineering and Performance, 2002, 11(6): 645-650.
[4] FISHER J, JAMES J. Aluminum alloy 2519 in military vehicles [J]. Advance Materials and Processes, 2002, 160(9): 43-46.
[5] SINGH S, GOEL D B. Influence of thermomechanical aging on tensile properties of 2014 aluminum alloy [J]. Materials Science, 1990, 25(1): 3894-3900.
[6] PATTANAIK S, SRINIVASAN V, BHATIA M L. Thermomechanical treatment of 2024 aluminum alloy [J]. Scripta Metallurgica, 1972, 6(3): 191-196.
[7] CHUNG D W, CHATURVEDI M C. Studies of the effect of thermomechanical treatments on the superaturation content of strip-cast aluminum alloy 3004 [J]. Materials Science and Engineering, 1981, 48(1): 27-34.
[8] DI RUSSO E, CONSERVA M, BURATTI M, GATTOA F. A new thermo-mechanical procedure for improving the ductility and toughness of Al-Zn-Mg-Cu alloys in the transeveerse directions [J]. Materials Science and Engineering, 1974, 14 (1): 23-26.
[9] PATON N E, SOMMER A W. Influence of thermomechanical processing treatments on properties of aluminum alloys [C]// Proceedings of the 3rd International Conference on Strength of Metals and Alloys. Cambridge, UK, 1973, 1(2): 101-105.
[10] SON S K, TAKEDA M, MITOME M, BANDO T E. Precipitation behavior of an Al-Cu alloy during isothermal aging at low temperatures [J]. Materials Letters, 2005, 59(6): 629-632.
[11] WANG S C, STARINK M J, GAO N. Precipitation hardening in Al-Cu-Mg alloys revisited [J]. Scripta Materialia, 2006(54): 287-291.
[12] KRAMER L S, BLAIR T P, BLOUGH S D, FISHER J J, PICKENS J R. Stress-corrosion cracking susceptibility of various product forms of aluminium alloy 2519 [J]. Journal of Materials Engineering and Performance, 2002, 11(6): 645-650.
[13] DOHERTY R D, MARTIN J W. The effect of dispersed second phase on the recrystallization of aluminum-copper alloys [J]. The Institute of Metals, 1962, 63(91): 332-338.
(Edited by HE Yun-bin)
Foundation item: Project(2005CB623706) supported by the National Basic Research Program of China
Received date: 2010-06-18; Accepted date: 2010-11-09
Corresponding author: XIA Chang-qing, Professor; Tel: +86-731-88830267; E-mail: xia_gro@mail.csu.edu.cn