
Mechanism of influence of ferric ion on electrogenerative leaching of
sulfide minerals with FeCl3
WANG Shao-fen(王少芬)1, 2, FANG Zheng(方 正)2
1. Department of Chemistry and Environmental Engineering, Changsha University of Science and Technology, Changsha 410077, China;
2. School of Chemistry and Chemical Engineering, Central South University, Changsha 410083, China
Received 27 September 2005; accepted 13 January 2006
Abstract: A dual cell system was used to study the influence of ferric ion on the electrogenerative leaching of sulfide minerals. Reaction mechanisms for the ferric chloride electrogenerative leaching of a series of sulfide minerals were proposed based on the data collected from the dual cell experiments. The influences of ferric ion on the electrogenerative leaching of sulfide minerals are similar. Ferric ion plays an important role on limiting the electrogenerative leaching rate at a relatively low concentration of FeCl3 (about less than 0.15 mol/L). The mathematical models based on the Butler-Volmer relation were delineated, and kinetic equations with respect to ferric ions for each sulfide mineral were obtained. The kinetic equations show that when the concentration of ferric ion is relatively low, the electrogenerative leaching rates are predicted to be proportional to 6/7, 4/5, 2/3 and 2/3 order of ferric ion for nickel concentrate, chalcopyrite concentrate, sphalerite and galena respectively. As the concentration of ferric ion increase, the correlative dependence between electrogenerative leaching rate and concentration of ferric ion becomes weak. The above conclusions are in agreement with the experimental results.
Key words: ferric ion; sulfide minerals; electrogenerative leaching; leaching rate; mechanism
1 Introduction
Electrogenerative leaching process is a newly- developed technique in hydrometallurgy. Although its principle has developed since the late 1960s[1], this technique has been overlooked in metallurgy until ZHANG et al[2] introduced it to the leaching of synthetic Ni3S2 with FeCl3. In order to utilize the chemical energy in leaching process reasonably and simplify the purification process, WANG et al[3-8] completed experimental studies of electrogenerative leaching a series of sulfide minerals through a dual cell system technique with FeCl3 and acidic MnO2 as oxidant respectively. It was indicated that a slight increase of [FeCl3] resulted in a sharp increase of the output current and power at a relatively low [FeCl3] (<0.15 mol/L). Over this value, the output current and power become independent of [FeCl3]. The similar influence of [FeCl3] was found in some traditional leaching experiments [9-15]. In order to elucidate the role of [FeCl3] in electrogenerative leaching process, a reaction mechanism was proposed in this study.
2 Experimental
A dual cell system technique was used to study the influence of [Fe3+]. Nickel concentrate (Ni3S2, Ni 55.2%, mass fraction), chalcopyrite concentrate (CuFeS2, Cu 22.3%), sphalerite (Zn 61.39%), galena (Pb 60.1%), were taken as the anodic materials respectively.
An ion-selective membrane connected the separated anolyte and catholyte compartments so that the effect of solution variables on each half cell can be independently evaluated. Solutions used in the experiments were prepared with analytical-grade chemicals and distilled water. Two mini-stirrers were used for agitating and water bath thermostat was used for heating. Each of half-cell potentials(φ) was measured versus the saturated calomel electrode(SCE), and the output voltages(V) of the leaching cell were measured with a digital voltmeter. The current(I) was measured with a low resistance milliammeter.
3 Results
3.1 Influence of [Fe3+] on electrogenerative leaching rate
The anolyte of the electrogenerative leaching system was NaCl (3.0 mol/L), and the catholyte was HCl (2.0 mol/L) plus a certain concentration of FeCl3. Under mild stirring (rate: 1 100 r/min), all the output currents along with the increase of the FeCl3 concentration were measured at 298.8 K for the electrogenerative leaching process of the four sulfide minerals systems. For the galena system, the relation of the logarithm of the maximum output current (lgImax) versus the logarithm of the ferric ion concentration (lg[Fe3+]) is plotted in Fig.1.
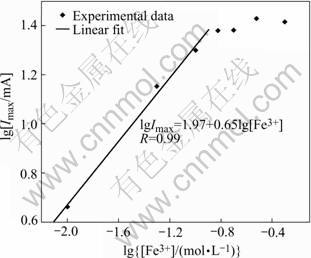
Fig.1 lgImax—lg[Fe3+] relation in electrogenerative leaching galena with FeCl3 system
From Fig.1, the influence of the [Fe3+] on the electrogenerative leaching rate is illustrated, that is the increase of [Fe3+] can raise the electrogenerative leaching rate at a relatively low [Fe3+] concentration (<0.15 mol/L). Above that concentration, the output current and power become relatively independent of concentration. All the other three sulfide minerals systems show the same phenomenon. From the data collected from the four systems, the mathematical equations are used to express the linear relation of lgImax and lg[Fe3+], which are listed in Table 1.
In conclusion, the electrogenerative leaching rate of sulfide minerals is directly proportional to [Fe3+]B at relatively lower concentration and deviate from this order at higher [Fe3+].
3.2 Influence mechanisms
In order to describe mechanism of the influence of ferric ion concentration on the electrogenerative leaching rate, an electrochemical model was introduced. In this model, it is assumed that the electrogenerative leaching occured through a redox couple between sulfide minerals and ferric ion. The rate controlling step is the electrochemical charge transfer process on the electrode surface, so an electrochemical charge transfer mechanism was used in this analysis.
Table 1 Relation between Imax and lg[Fe3+] (0.01-0.1 mol/L)
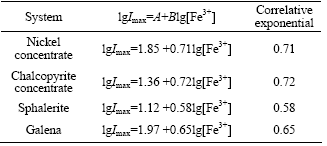
1) Fe3+ was adsorbed on Pt electrode:
Pt+Fe3+(aq)=[Pt ·Fe3+]ads (1)
According to Langmuir isothermal adsorption equation, the following relation is obtained:
(2)
where θ represents the fraction of total available surface sites occupied by Fe3+, K1 represents the equilibrium constant of Eqn.(1).
2) As the external resistance is varied from an infinitely high value (open circuit) down to a very low value, sulfide minerals are oxidized as shown in Eqns.(3)-(6) and Fe3+ is reduced in cathode as shown in reaction(7):
Ni3S2(s)=3Ni2+(aq)+2S0(s)+6e (3)
CuFeS2(s)=Cu2+(aq)+Fe2+(aq)+2S0(s)+4e (4)
ZnS(s)=Zn2+(aq)+S0(s)+2e (5)
PbS(s)=Pb2+(aq)+S0(s)+2e (6)
[Pt·Fe3+]ads+e=[Pt·Fe2+]ads (7)
θ
For the cathodic reaction (7), the Butler-Volmer equation is
(8)
where n is the number of electron in reaction (7) and n=1; α and β represent transfer coefficients and the values are 0.5, respectively. α+β=1, commonly; ε is the polarization potential; Ac is the surface area of Pt electrode; K7 and
represent equilibrium constants of reaction (7) and reverse reaction of reaction (7). Eqn.(8) can be simplified as Eqn.(9) owning to that there is no external Fe2+ existed in solution and the reverse reaction of reaction (7) can be ignored:
(9)
For Eqns.(3)-(6), the Butler-Volmer equations are as follows:
(10)
(11)
(12)
(13)
where Aa is the surface area of mineral electrodes; K3-K6 and
represent the equilibrium constants of reactions (3)-(6) and reverse reactions of (3)-(6). Owning to that there are no external sulfide mineral mental ions exist in solution and the reverse reactions of (3)-(6) can be ignored. The Butler-Volmer Eqns.(10)- (13) can be simplified as
(14)
(15)
(16)
(17)
Considering i7=i3, i7=i4, i7=i5, i7=i6 when the electrogenerative leaching is ongoing, Eqn.(9) is combined with Eqns.(14)-(17) respectively, the following equations are obtained:
(18)
(19)
(20)
(21)
exp[Fε/RT] for each system can be expressed as follows, respectively:
(22)
(23)
(24)
(25)
The overall electrogenerative leaching rates, expressed as the rates disappearance of sulfide minerals, are related to the anodic current through the following equations which are essentially the statement of Faraday’ Law:
(26)
(27)
(28)
(29)
Combining Eqns.(14)-(17) yields
(30)
(31)
(32)
(33)
When concentration of Fe3+ is relatively lower, 1+K1[Fe3+]≈1 in Eqns.(30)-(33) and the electrogenerative leaching rate of nickel concentrate, chalcopyrite concentrate, sphalerite and galena predict 6/7, 4/5, 2/3 and 2/3 order dependence on Fe3+, respectively. K1[Fe3+] in Eqns.(30)-(33) can not be ignored as concentration of Fe3+ increases, which results in the correlative dependence between electrogenerative leaching rate and [Fe3+] become weak. The results are in agreement with the experiment study: the rate of electrogenerative leaching of nickel concentrate, chalcopyrite concentrate, sphalerite and galena is directly proportional to [Fe3+] 0.71, [Fe3+]0.72, [Fe3+]0.58, [Fe3+]0.65 at relatively lower concentration and deviate from this order at higher [Fe3+].
4 Conclusions
The influence of [Fe3+] on the electrogenerative leaching system was investigated through a dual cell system technique. Fe3+ was involved in the electrogenerative leaching process of sulfide minerals directly. The output power increases as [Fe3+] increases. There has weaker influence on the electrogenerative leaching rate when the [Fe3+] reaches a certain value.
The mechanism of cathodic reaction was deduced under reasonable hypothesis and kinetic equations with respect to [Fe3+] for each sulfide mineral were obtained as follows:
The above conclusions are in agreement with the experimental results: the rate of electrogenerative leaching of nickel concentrate, chalcopyrite concentrate, sphalerite and galena is directly proportional to [Fe3+] 0.71, [Fe3+]0.72, [Fe3+]0.58, [Fe3+]0.65 at relatively lower concentration and deviate from this order at higher [Fe3+].
References
[1] Langer S H, Yurchak S. Electrochemical reduction of the benzene ring by electrogenerative hydrogenation[J]. J Electrochem Soc, 1969, 116((9): 1228-1230.
[2] Zhang H Z, Fang Z, Zhang P M. An investigation on electrogenerative leaching of Ni3S2[A]. Proc of ICHM’92[C]. Beijing: Inter Academic Pub, 1992. 286-289.
[3] Wang S F, Fang Z, Chen Y G, Long S. Exploration of electrogenerative leaching of PbS with FeCl3[J]. The Chinese Journal of Process Engineering, 2002, 2(3): 235-240.(in Chinese)
[4] WANG S F, FANG Z, CHEN Y G. An investigation on electrogenerative leaching of galena with FeCl3[J]. Journal of the Chinese Rare Earth Society, 2002, 20(S): 234-236.
[5] WANG S F, FANG Z, CHEN Y G. Application of mechanical activation on the electrogenerative leaching process of galena[J]. The Chinese Journal of Hydrometallurgy, 2003, 22(2): 93-96.
[6] WANG S F, FANG Z, WANG Y Y, CHEN Y G. Electrogenerative leaching of galena with ferric chloride[J]. Minerals Engineering, 2003, 16(9): 869-872.
[7] WANG S F, FANG Z, LONG S. Exploration of electrogenerative leaching sulfide minerals and MnO2 simultaneously[J]. Nonferrous Metals, 2004, 56(1): 56-59. (in Chinese)
[8] WANG S F, FANG Z, WANG Y Y. Electrogenerative leaching of nickel concentrates with ferric chloride[J]. Journal of Central South University of Technology, 2004, 11(4): 405-409.
[9] Bobeck G E, Su H. Kinetics of dissolution of sphalerite in ferric chloride solution[J]. Metallurgical Transactions B, 1985, 16B(3): 413-424.
[10] Morin D, Gaunand A, Renon H. Representation of kinetics of leaching of galena by ferric chloride in sodium chloride solutions by a modified mixed kinetics model[J]. Metallurgical Transactions B, 1985, 16B(1): 31-39.
[11] Dutrizac J E. The dissolution of galena in ferric chloride media[J]. Met Trans, 1986, 17B: 5-17.
[12] Fuerstenau M C, Chen C C, Han K N, Palmer B R. Kinetics of galena dissolution in ferric chloride solution[J]. Met Trans, 1986, 17B: 415-423.
[13] Suni J, Henein H, Warren G W, Reddy D. Modelling the leaching kinetics of a sphalerite concentrate size distribution in ferric chloride solution[J]. Hydrometallurgy, 1989, 1: 25-38.
[14] Kobayashi M, Dutrizac J E, Toguri J M. Critical review of the ferric chloride leaching of galena[J]. Canadian Metallurgical Quarterly, 1990, 29(3): 201-211.
[15] chen a a, dreisiger d b. The ferric fluosilicate leaching of lead concentrates(part 1): Kinetic studies[J]. Metallurgical and Materials Transactions B, 1994, 25B: 473-480.
Foundation item: Project(50374077) supported by the National Natural Science Foundation of China
Corresponding author: WANG Shao-fen; Tel: +86-731-5128112; E-mail: wangsf711117@163.com
(Edited by LI Xiang-qun)