
Electroless copper plating on microcellular polyurethane foam
TIAN Qing-hua(田庆华), GUO Xue-yi(郭学益)
School of Metallurgical Science and Engineering, Central South University, Changsha 410083, China
Received 6 July 2009; accepted 30 December 2009
_____________________________________________________________________________________________________
Abstract: In order to obtain substrates with good conductive foam for high porosity foam metal materials used in the metal electrodes, the technique of electroless copper plating on the microcellular polyurethane foam with pore size of 0.3 mm was investigated. The main factors affecting the deposition rate such as the solution composition, temperature, pH value and adding ultrasonic were explored. The results show that the optimum process conditions are CuSO4 16 g/L, HCHO 5 mL/L, NaKC4H4O6 30 g/L, Na2EDTA 20 g/L, K4Fe(CN)6 25 mg/L, pH value of 12.5-13.0 and temperature of 40-50 ℃. Under these technical conditions, the process has excellent bath stability. Adding ultrasonic on the process can elevate the deposition rate of copper by 20%-30%. The foam metal material with a porosity of 92.2% and a three-dimensional network structure, was fabricated by electro-deposition after the electroless copper plating.
Key words: electroless copper plating; microcellular; polyurethane foam; deposition rate; foam metal material
_____________________________________________________________________________________________________
1 Introduction
Foam metal materials have received a great deal of attention because of their special structure and extreme lightness with relatively high strength and stiffness, and have been mostly used in several fields including impact energy absorbers, silencers, filters, flame arresters, heaters and heat exchangers[1-3]. Recently, new interest in the thin metallic foams with high specific surface area increases, along with its potential applications to such electrochemical devices as porous electrodes, catalyst and sensors. There are many ways available to manufacture foam metal materials, but electro-deposition is the most popular method to prepare the foam metal materials for metal electrodes[4]. Electro-deposition on polyurethane foam requires some electrical conductivity of the initial polymer foam. Then, a three-dimensional reticular structure with high porosity can be obtained by electro-deposition. The pore size of such foam metal material has been found to be virtually dependent on the average pore size of the polyurethane foam. It is found that the polyurethane foam with pore size ranging in 0.2-0.4 mm as substrate can get excellent electrochemical performance [5].
As a nonconductor, polyurethane foam cannot be electrodeposited directly. The most important procedure of electro-deposition methods is conductive treatment, which is also known as surface metallization, playing a key role in controlling the coating quality of the following process. The main methods of the conductive treatments include vacuum evaporation, arc ion plating, cathode sputtering, electroless plating and coating with electrically conductive slurry[6-7]. The first three methods require high costs and expensive apparatuses, and the last one is difficult to batch coating. Also the adsorption type between the deposited layers and the surfaces of the conductor in all of these four methods are physical adsorption, which is less conglutination to base, and easy to disconnect[8-9]. Among these techniques, electroless plating has widely been employed as a method to form metallic thin film on the surface of electrically nonconductive three-dimensional substrates, typically polymers. There were several advantages of electroless plating, such as low cost, easy formation of continuous and uniform coating on the surface of substrate with complex shape, and capability of depositing on either conductive or nonconductive parts[10-11]. In this paper, electroless plating method was applied to depositing a layer of copper on the surface of polyurethane foam. The main factors affecting the deposition rate such as the solution composition, temperature, pH value and adding ultrasonic were investigated comprehensively. The purpose of this work is to optimize the conditions of electroless copper plating in order to establish more stable and higher deposition rate bath to produce higher quality deposit.
2 Experimental
2.1 Chemicals
Polyurethane foam with an average pore size of 0.3 mm, an average porosity of 96% from the Bridgestone Corp. (Japan) was used as the substrate.
The electroless copper plating bath contained CuSO4, HCHO, NaKC4H4O6, Na2EDTA and K4Fe(CN)6. All chemicals used in the present work were of analytical purity.
2.2 Procedure
The electroless plating was carried out by multi-step processes which included degreasing, rinsing, roughening, rinsing, sensitization, rinsing, activation and electroless copper plating. The specimens were cleaned, degreased and polished with ethanol (C2H5OH) for 1 min, and then scoured in solution (35 g/L NaOH, 25 g/L Na2CO3, 10 g/L Na3PO4) at 70 ℃ for 5 min to remove the dirt and release agent on the surface of polyurethane foam firstly. The samples were rinsed then in distilled water and etched in a mixture of 1 g/L KMnO4 and 0.5 mL/L H2SO4 solution at 45 ℃ for 5 min. The surface sensitization was conducted by immersion of the samples into an aqueous solution containing 50 g/L SnCl2 and 1 mol/L HCl at 30 ℃ for 5 min. The specimens were then rinsed in distilled water and immersed in an activator containing 0.5 g/L PdCl2 and 1 mol/L HCl at 40 ℃ for 5 min. The specimens were then rinsed in a large volume of deionized water for more than 5 min to prevent contamination of the plating bath. The specimens were then immersed in the electroless copper plating bath.
The most important reaction, occurring in the electroless copper plating when formaldehyde was used as reducing agent, is as follows[12]:
Cu2++2HCHO+4OH- = Cu↓+ 2HCOO-+2H2O+ H2↑ (1)
The foam metal materials can be obtained by electro-deposition after electroless plating.
2.3 Deposition rate testing
It is difficult to calculate the surface area of the foam materials because of the complex surface. In this study, the deposition rate is defined as the mass gain of unit mass foam substrate and unit time. The deposition rate was calculated by the following equation:
ν=(m2-ml)/(m1t) (2)
where ml and m2 are the masses of the specimen before and after electroless plating procedure, respectively; t is the stabilizing time of electroless plating bath.
2.4 Porosity testing
The porosity of foam materials (ε) was calculated by the following equation:
ε=(V0-V1-V2-V3)/V0=[V0-(V0-ε1V0)-m′2/ρ2-m′3/ρ3]/V0=ε1-m′2/ρ2V0-m′3/ρ3V0 (3)
where V0 is the volume of all the foam materials including the void; V1 is the volume of polyurethane foam; V2 and V3 are the volumes of electroless coatings and electrodeposits, respectively; m′2 and m′3 are the masses of electroless coatings and electrodeposits, respectively; ρ2 and ρ3 are the densities of electroless coatings and electrodeposits, respectively; ε1 is the porosity of polyurethane foam.
3 Results and discussion
3.1 Effect of content of CuSO4
The effect of CuSO4 content on the deposition rate is shown in Fig.1. It can be seen from Fig.1 that increasing the content of CuSO4 in the bath may rapidly enhance the deposition rate. In this study, when the content of CuSO4 is more than 20 g/L, the satability of the bath is very poor, and the electroless coating is rough. But if the content of CuSO4 is less than 12 g/L, the deposition rate is low, with the electroless coating becoming gray, presenting dull color and uneven luster. When the content of CuSO4 is around 16 g/L, the deposition rate is fast, and the coating is full bright. The results show that the best content of CuSO4 is around 16 g/L.
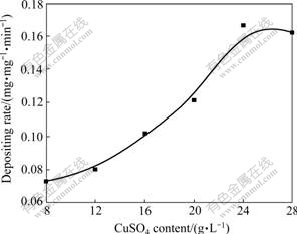
Fig.1 Effect of CuSO4 content in bath on deposition rate
3.2 Effect of content of HCHO
Fig.2 shows that the deposition rate increases with increasing the content of HCHO. When the content of HCHO is 2 mL/L, the deposition rate is low, and the surface of coating has some dark crinkles. When the content of HCHO is 5 mL/L, the deposition rate is fast, and the coating is full bright. When the content of HCHO is over 6 mL/L, the deposition rate increases, but the satability of bath is very poor. A content of 5 mL/L was used in this experiment.

Fig.2 Effect of HCHO content on deposition rate
3.3 Effect of pH value
The effect of pH value on the deposition rate is shown in Fig.3 (pH value was changed by the addition of NaOH concentrated solution to the electroless baths). The results indicate that the deposition rate increases markedly with increasing pH value. The formaldehyde has the capability of reducing Cu(Ⅱ) only under basic conditions(pH>11.0), so, no copper deposited when the pH value was below 11.0[12]. When the pH value was beyond 13.5, it was observed that the bath decomposed easily and produced some Cu2O powder; and the copper coatings were also rough. As the pH value ranges in range of 12.5-13.0, the deposition rate is very fast, and the coating has excellent brightness. Therefore, the pH value at 12.5-13.0 is the best choice of this experiment.
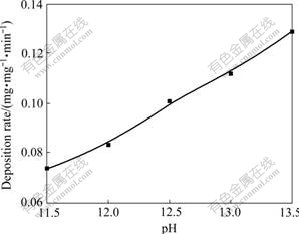
Fig.3 Effect of bath pH value on deposition rate
3.4 Effect of bath temperature
The effect of bath temperature on the deposition rate is shown in Fig.4. The results clearly indicate that the deposition rate increases with increasing the bath temperature. According to the experimental results, the deposition rate is low, and the surface of coating is grey at 20-30 ℃. It is found that the bath decomposes easily and produces a lot of Cu2O powder in the bath beyond 50 ℃. As the bath temperature ranges in 40-50 ℃, the bath is stable, with the coating bright, compact and well-adherent. To sum up, the optimal bath temperature ranges in 40-50 ℃.
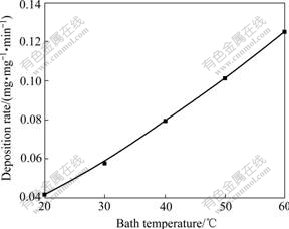
Fig.4 Effect of bath temperature on deposition rate
3.5 Effect of double complexing agents
Complexing agent is one of the most important components of electroless plating bath, which can improve the stability of bath. The good grain refining effect can also be obtained by complexing agents addition[13]. In this work, disodium ethylenediamine tetraacetate (Na2EDTA) and potassium sodium tartrate(NaKC4H4O6)were used as double complexing agents. The effects of changing concentrations of the complexing agents are shown in Figs.5 and 6, respectively. It can be seen from these two figures that the deposition rate decreases obviously with increasing concentrations of complexing agents. According to the experimental results, the optimum conditions are the concentrations of Na2EDTA and NaKC4H4O6 of 20 and 30 g/L, respectively. The baths have poor stability, and coatings are rough and dark-brown when the concentrations are below the optimum ones. The dark appearance usually indicates poor electronic properties. And the deposition rate is very low when the concentrations are beyond the optimum ones.
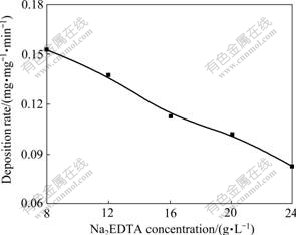
Fig.5 Effect of Na2EDTA concentration on deposition rate
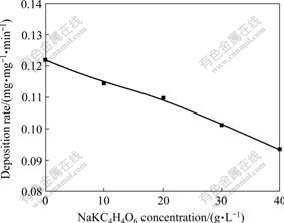
Fig.6 Effect of NaKC4H4O6 concentration on deposition rate
3.6 Effect of additives
A persistent problem in the use of electroless copper plating baths has been a tendency to decompose spontaneously. For the reason, many additives have been proposed to serve as stabilizers. In this work, the addition of K4Fe(CN)4 with concentration of 25 mg/L to the bath was investigated. The color of the deposits had a corresponding improvement, changing from dark-brown to copper-bright with the addition of K4Fe(CN)4 to the plating bath.
3.7 Effect of adding ultrasonic
From Eq.(1), a lot of hydrogen was produced in the electroless copper plating reaction. The average pore size of this polyurethane foam is only 0.3 mm, so it is difficult to discharge the excessive hydrogen timely. A dense packing of the gas bubbles in a small amount of polyurethane foam will reduce the deposition rate and make bad effect on the plating results, causing the non-integrity of coatings inside[14]. Adding ultrasonic in the process was study. The use of ultrasonic during the electroless copper plating affects the deposition rate and the deposits properties. Cooperating with mid- frequency (40 kHz) and power (400 W) ultrasonic after 3 min pre-plating can shorten the inducing time and elevate the speed of the reaction, with the deposition rate increased by 20%-30%.
3.8 Electro-deposition
Foam nickel, foam plumbum and foam zinc are the most common kinds of the foam metal materials for metal electrodes. Taking foam zinc as the study object, the present work selects the sulphate plating bath for electrodepositing of the conductive foam substrate. The bath contains 250 g/L ZnSO4, 20 g/L Al2(SO4)3, 45 g/L KAl(SO4)2, 30 g/L Na2SO4, 10 mL/L sulphur zinc-30 (an additive for bright). Using zinc as anode and conductive foam substrate as cathode, electrodeposited zinc in this bath was studied at 30 ℃, pH=3.5, with cathode current density of 0.03-0.06 A/dm2, electrodes distance of 30-50 mm.
The SEM images of the polyurethane foam and foam zinc after electroless copper plating and zinc electro-deposition are shown in Fig.7. It can be seen from Fig.7 that the microstructure of the foam zinc material still keeps the same three-dimensional network as polyurethane foam substrate with an average pore size of 0.3-0.4 mm. Based on Eq.(3), the porosity of foam zinc materials is about 92.2%.
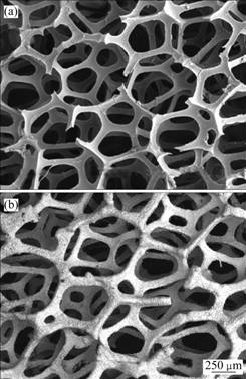
Fig.7 SEM images of foam materials on different phases: (a) Polyurethane foam; (b) Foam zinc material
4 Conclusions
1) The deposition rate increases with increasing temperature, pH value, concentrations of CuSO4 and HCHO, and decreases with increasing concentrations of NaKC4H4O6 and Na2EDTA. And high deposition rate results in loose copper deposits and the surface of the deposits is rough. The addition of K4Fe(CN)4 to the bath can reduce the deposition rate and make the deposits more compact.
2) The obtained optimum process conditions are 16 g/L CuSO4, 5 mL/L HCHO, 30 g/L NaKC4H4O6, 20 g/L Na2EDTA, pH value 12.5-13.0 and reaction temperature 40-50 ℃. In these technical conditions, the process is stable.
3) Adding ultrasonic after pre-plating can increase the deposition rate by 20%-30%. Foam zinc material with porosity of 92.2% was fabricated by electro- deposition after the electroless copper plating.
References
[1] CAO Xiao-qing, WANG Zhi-hua, MA Hong-wei, ZHAO Long-mao, YANG Gui-tong. Effects of cell size on compressive properties of aluminum foam [J]. Trans Nonferrous Met Soc China, 2006, 16(2): 351-356.
[2] TIAN Qing-hua, GUO Xue-yi, XUE Ping, SONG Yu, DUAN Lian, Electro-deposition for foamed zinc material from zinc sulfate solution [J]. Materials Science Forum, 2007, 561/565(3): 1669-1672.
[3] AFSANEH R, LAKSHMI V, NICK R, NOAH Y, BRIAN P N. Processing and characterization of a new composite metal foam [J]. Materials Transactions, 2006, 47(9): 2148-2153.
[4] WANG Dian-long, DAI Chang-song, JIANG Zhao-hua, HU Xin-guo, WU Ning. Current density control for preparation of metal foam by electrodeposition [J]. Journal of Harbin Institute of Technology, 2003, 35(2): 230-233. (in Chinese)
[5] TIAN Qing-hua. Electrodeposition for manufacturing foamed zinc material [D]. Changsha: Central South University, 2007. (in Chinese)
[6] ZHU Ruo-ying, HUA Jun-kai, HUANG Gu. Research on metallic finishing of polyester textiles by vacuum evaporation [J]. Journal of Tianjin Polytechnic University, 2005, 24(6): 3-26. (in Chinese)
[7] LUO Rui-xue, LI Zheng-xian. Investigation of titanium film deposited by arc ion processing on Al2O3 ceramics [J]. Rare Metals Letters, 2005, 25(7): 25-27. (in Chinese)
[8] HARI-KRISHNAN K, JOHN S, SRINIVASAN K N, PRAVEEN J, GANESAN M, KAVIMANI P M. An overall aspect of electroless Ni-P depositions—A review article [J]. Metall Mater Trans A, 2006, 37(6): 1917-1926.
[9] LI Kai-hua, LUO Jiang-shan, LIU Ying, TANG Yong-jian. Electroless plating in synthesizing nickel foams [J]. High Power Laser and Particle Beams, 2007, 19(7): 1158-1162. (in Chinese)
[10] XU Zhi-mou, ZHENG Jia-shen, LIU Hong-fang, ZHANG Lian-meng. Investigation of production of functionally gradient material by electroless platings [J]. Acta Materiae Compositae Sinica, 2000, 17(4): 66-70. (in Chinese)
[11] KHOPERIA T N. Investigation of the substrate activation mechanism and electroless Ni-P coating ductility and adhesion [J]. Microelectronic Engineering, 2003, 69(2/4): 391-398.
[12] LI Ning. Practical electroless plating technology [M]. Beijing: Chemical Industry Press, 2004: 252-262. (in Chinese)
[13] ZHENG Ya-jie, ZOU Wei-hong, YI Dan-qing, GONG Zhu-qing, LI Xin-hai. Electroless copper plating system of potassium sodium tartrate and EDTA·2Na [J]. Journal of Central South University: Science and Technology, 2005, 36(6): 971-976. (in Chinese)
[14] ZHAO Peng, PU Yu-ping, HUANG Chun-hui, LU Guang-shu. Effect of adding ultrasonic on copper electroless plating of polyurethane foam [J]. Journal of Materials Engineering, 2008(4): 43-46. (in Chinese)
_______________________
Corresponding author: GUO Xue-yi; Tel: +86-731-88877863; E-mail: xyguo@mail.csu.edu.cn
(Edited by LONG Huai-zhong)