Ta-7.5%W在退火过程中的组织和织构演变
左波,汪明朴,夏福中,王珊,陈畅,金鹏
(中南大学 材料科学与工程学院,湖南 长沙,410083)
摘要:通过金相组织观察、透射电子显微镜(TEM)及显微硬度测试,研究冷轧变形量为95%的Ta-7.5%W合金箔材在1 050,1 200和1 360 ℃退火时的组织和性能变化,并采用取向密度函数(ODF)分析在此过程中其织构演变规律。对其实验结果进行研究发现:冷轧态Ta-7.5%W合金硬度为HV 300,经1 360 ℃退火后硬度迅速减小,说明此时合金已发生回复再结晶。轧制后的Ta-7.5%W合金箔材具有各向异性,在轧面//{111}取向上形成位错胞亚结构,在轧面//{100}取向上形成了形变带,冷轧态的主要织构为{001}
,{112}
和{110}
织构;在1 200 ℃退火时,在轧面//{111}取向上,再结晶通过亚晶界迁移、亚晶长大形核,而在轧面//{100}取向上,主要是通过亚晶转动、聚合形核;{001}
织构增强,{112}
织构减弱;在1 360 ℃退火时,{001}
织构急剧减弱,{111}
织构增强。
关键词:Ta-W合金;退火;再结晶;织构
中图分类号:TG146.2 文献标志码:A 文章编号:1672-7207(2012)03-0883-07
Microstructures and textures evolution of Ta-7.5%W during annealing process
ZUO Bo, WANG Ming-pu, XIA Fu-zhong, WANG Shan, CHEN Chang, JIN Peng
(School of Materials Science and Engineering, Central South University, Changsha 410083, China)
Abstract: The organization and performance evolution of Ta-7.5%W at 1 050, 1 200 and 1 360 ℃ were investigated by microstructure observation, transmission electron microscope (TEM) and hardness tests, and the texture evolution was investigated by orientation density function (ODF). It was found that after 1 360 ℃ annealing the hardness decreases rapidly from HV 300 to HV 240, and the recovery recrystallization occurs. Ta-7.5%W is anisotropic; the dislocation substructure appears in {111} orientation and the deformation zone appears in {100} orientation. The main textures of cold-rolled Ta-W alloy are {001}
, {112}
and {110}
. As the annealing temperature is 1 200 ℃, the recrystallization nucleation is mainly through the migration of the subgrain boundary and the growth of the subgrain in {111} orientation, while the recrystallization nucleation is mainly through the rotation and polymerization of the subgrain in {100} orientation; the texture of {001}
increases and the texture of {112}
decreases. While annealing at 1 360 ℃, the texture of {001}
decreases rapidly, and the texture of {111}
increases.
Key words: Ta-W alloy; annealing; recrystallization; textures
钽及钽钨合金具有力学性能好、耐高温、高密度、化学性能稳定、抗腐蚀能力强和塑性加工性能好等特点, 被广泛用于化工[1-2]、电子[3-4]、通讯[5]和航天[6]等领域。作为体心立方过渡族难熔金属,如钒、铌、钼、钽和钨,其中除了钽,都显示出了塑脆转变现象,在低温变形时显示出脆性,这使得体心立方金属的加工变得困难。钽钨合金适合进行体心立方金属变形规律研究是因为其在变形和退火过程中不会发生结构转变和相变,因此研究钽钨合金的变形行为对体心立方金属的变形规律研究具有重要意义。体心立方金属的层错能均很高,为400~1 000 mJ/m2。因此,体心立方金属的塑性变形基本上是通过位错的滑移与交滑移实现的。钽钨合金板在轧制过程中,由于在轧制过程中金属表层和心部的受力条件不同,其轧制织构的类型和组分也存在着一定的差异,沿轧板的厚度方向上,织构存在一定的不均匀性[7],这些织构的形成,使钽钨合金板在不同方向上的强度和伸长率都产生很大的差异[8]。因此,研究钽钨合金箔材在轧制以及退火过程中组织和性能的变化规律,不仅对钽钨合金箔材的生产具有指导意义,而且对体心立方金属的塑性变形行为具有重要意义。
1 实验
本文采用粉末冶金法制备获得了Ta-7.5W合金坯锭,通过对合金锭坯经过中间退火,退火工艺为1 200 ℃保温40 min,轧制最终得到了厚度为100 μm的Ta-7.5W合金箔材。轧制道次变形量控制在5%~10%,每次冷轧的总变形量控制在50%左右。对冷轧获得的100 μm Ta-7.5W合金箔材分别在1 050,1 200和1 350 ℃温度下真空退火1 h。
金相显微组织采用LeicaEC3显微镜观察。显微硬度测量在HV-5型小负荷维氏硬度计上进行,载荷为0.2 N,加载15 s,每个试样测量5次,去掉最大值和最小值,然后取其平均值。极图测量采用反射法,在D8 Discover2500型号的X线衍射仪上进行测试,箔材样品尺寸为15 mm×15 mm×0.1 mm。对所得的X线衍射谱,使用MDI Jade 5.0软件进行分析,从而得式(1)中的I标HKL和IHKL,利用式(1)计算可以得到轴密度参量PHKL:
(1)
式中:HKL为晶面指数;n为测量{HKL}衍射线的数目;IHKL为{HKL}衍射的强度;
为板材无织构时{HKL}的衍射强度。
本实验通过测定棒材横截面的{110},{200}和{211} 3个不完整极图(极图测量范围α=0°~75°,β=0°~360°)。由实测值算得极密度
,进行归一化处理后得到真实极密度
。极图数据经修正和对称(立方正交对称性)处理后,采用Bunge球谐函数分析与级数展开法[9]即可计算相应的取向分布函数(ODF),并将Clmn系数表示至lmax=22。透射电镜观察在JEOL 2010上进行,操作电压为200 kV。电镜样品减薄在MTP-1双喷减薄仪上进行,电解液用 V(氢氟酸):V(硫酸):V(甲醇)=1:5:94,电流为200 mA。
2 结果与分析
2.1 退火温度对Ta-7.5%W合金硬度的影响
图1所示为Ta-7.5%W合金箔材显微硬度随着退火温度升高的变化。由图1可以看出:冷轧态Ta-7.5%W合金的显微硬度达到了300 HV,硬度相比于纯钽冷轧加工态(197 HV)得到了较大提高。 这是由于溶质元素W添加后,其与位错之间会发生弹性交互作用、电交互作用以及化学交互作用,这不仅会钉扎位错运动,而且还会增加位错运动的摩擦阻力[10],因此,溶质元素W的添加使得Ta-W合金强度得到了大幅度提高,起到了很大的固溶强化效果。
从图1还可以看出:随着退火温度的升高,Ta- 7.5%W合金箔材的显微硬度逐渐下降。冷轧态Ta- 7.5%W合金的显微硬度为300 HV,经1 050 ℃退火,合金的硬度下降为265 HV,经1 200 ℃退火,合金的硬度下降为248 HV,而经1 360 ℃退火,合金的硬度仅为212 HV。合金显微硬度下降很快,说明合金此时发生了再结晶。
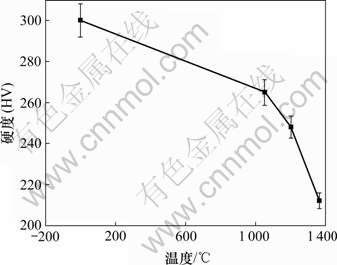
图1 Ta-7.5%W合金显微硬度随着退火温度的变化
Fig.1 Dependence of micro-hardness of Ta-7.5%W alloy on annealing temperature
2.2 退火温度对Ta-7.5%W合金箔材组织的影响
图2所示为轧制厚度为0.100 mm的Ta-7.5%W合金箔材在不同退火状态下的侧面金相显微组织照片。
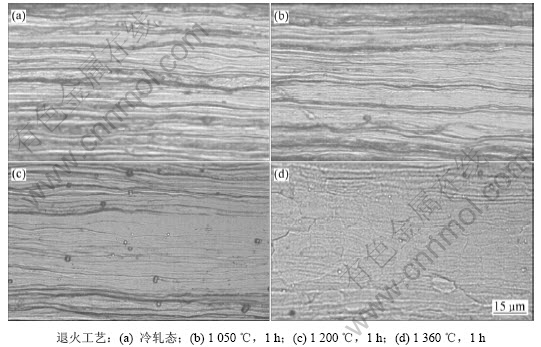
图2 Ta-7.5%W合金箔材侧面的显微组织
Fig.2 Microstructures of lateral surface of Ta-7.5%W alloy foils
从图2可以看出:Ta-7.5%W合金经冷轧变形后,基体内的晶粒沿轧制方向被拉长,晶界变得模糊不清,呈现纤维状,是明显的高度变形的纤维组织(如图2(a)所示)。经1 050和1 200 ℃退火1 h后,合金基体仍然是明显的纤维组织(如图2(b)和(c)所示),金相观察看不出明显变化。但经1 360 ℃退火1 h后,由图2(d)可以看出:该合金基体内已出现了明显的细小再结晶晶粒,尺寸为5 μm左右,大的再结晶晶粒为20 μm左右,纤维组织部分断裂,这说明轧制厚度为0.100 mm Ta-7.5%W合金箔材在此温度下发生了再结晶。
2.3 退火温度对Ta-7.5%W合金箔材织构的影响
图3所示为不同状态的Ta-7.5%W合金箔材轧面的X线衍射谱[11]。由图3可以看出:冷轧态轧面上各个晶面对应的衍射峰的强度均明显不同于无织构样(对照样),这说明了Ta-7.5%W合金箔材在冷轧变形过程中晶粒出现了择优取向,形成了织构[12]。经不同的温度退火1 h后,各衍射峰的相对强度发生不同程度的变化,说明冷轧态Ta-7.5%W合金箔材在退火过程中织构发生了演变。
表1列出了经X线衍射谱测量并通过轴密度计算式(1)计算得到的各晶面的轴密度,通过轴密度分析可以得出冷轧态Ta-7.5%W合金箔材织构主要有{001}
,{111}
和{211}
3种织构组分(
为晶向指数)。经1 200 ℃退火1 h后,(001)晶面轴密度增强,由冷轧态7.08增加到14.13,(112) 晶面轴密度稍有增强,由0.78增加到1.00,而(111)晶面轴密度减小。经1 360 ℃退火1 h后,(001)晶面轴密度减小到12.89,(112)晶面轴密度由1.00增加到1.27,(111)晶面轴密度继续减小到0.40。
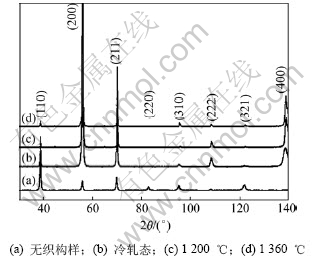
图3 Ta-7.5%W合金轧面的X线衍射谱
Fig.3 XRD patterns of Ta-7.5%W alloy on rolled surface
表1 Ta-7.5%W合金轧面轴密度
Table 1 Axis density of Ta-7.5%W alloy on rolled surface
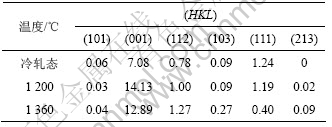
上述研究结果表明:退火温度会对Ta-7.5%W合金箔材的织构产生影响,随着退火温度由1 200 ℃升高到1 360 ℃,冷轧态{001}
织构先增强后减弱,{112}
织构逐渐增强,而{111}
织构逐渐减弱。
为了更加准确地确定Ta-7.5%W合金箔材中的织构组分,本研究利用ODF对该合金的织构进行了进一步分析,图4所示为厚度为0.100 mm的Ta-7.5%W合金箔材冷轧态和退火态恒φ1=0?的ODF截面图。由图4(a)可以看出:在边缘区尤拉角为φ1=0?,Φ=0?,φ2=45?的位置上取向密度最高,这表明冷轧态合金中的主要织构组分是{001}
。此外还存在其他的织构组分,譬如在尤拉角(0?,30?,45?)处的{112}
织构。经1 200 ℃退火1 h(图4(b))后,在尤拉角(0?,0?,45?)处的{001}
织构增强,Φ=30?处的{112}
织构减弱,其余织构组分变化并不十分明显,主要织构组分还是{001}
和{112}
。经1 360 ℃退火1 h后(图4(c)),取向密度最高点仍处于尤拉角为φ1=0?,Φ=0?,φ2=45?的位置,但是取向密度相对减弱,这表明1 360 ℃退火1 h会减弱{001}
织构组分。
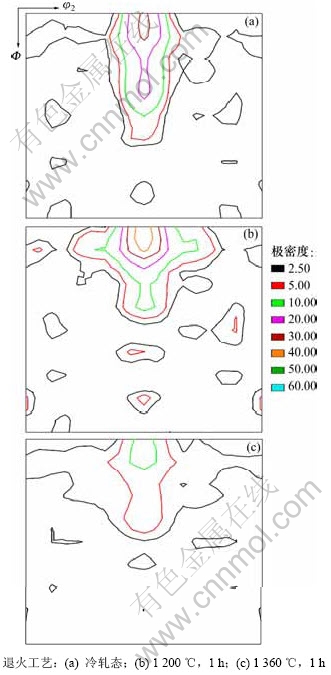
图4 Ta-7.5%W合金恒φ1=0?的ODF截面图
Fig.4 ODF section of Ta-7.5%W alloy when φ1=0?
图5所示为不同状态的Ta-7.5%W合金箔材在退火过程中晶粒取向变化的取向线分析[11]。从图5可以看出:冷轧态Ta-7.5%W合金箔材沿α取向线在Φ=0?,35?,90?处出现了3个峰值,分别对应的织构组分为{001}
,{112}
和{110}
。经1 200 ℃退火1 h后,{001}
织构组分增强,{112}
织构组分减弱,而{110}
织构略有减小。经1 360 ℃退火1 h后,{001}
织构组分急剧减弱;而{112}
织构也略有减小。冷轧态合金中{111}
织构取向密度也较高,经1 200 ℃退火1 h后,{111}
织构取向密度减小;经1 360 ℃退火 1 h后,{111}
和{111}
织构取向密度略有 增加。
2.4 TEM组织观察
图6所示为冷轧态Ta-7.5%W合金箔材的TEM像。由图6可以看出:在轧面//{111}晶面取向的晶粒中,基体中的变形组织以胞状组织为主,位错胞的胞壁较厚,胞壁中缠结的位错密度很高,在这种大的位错胞的内部还可以看到少量相互缠结的位错线。在轧面//{100}晶面取向的晶粒中形成了形变带组织,形变带中有大量拉长的位错胞组织,这些拉长的位错胞平行分布,拉长的位错胞边界为平行分布的长的高密度位错边界,称为几何必须位错边界。由对应的衍射斑分布可以看出:这些GNBS延着{100}晶面平行分布。可见,在此取向的晶粒中,大量位错在{100}晶面上发生了滑移。另外在这些拉长的位错胞中,还存在着大量细小的位错胞,这些位错胞的边界称为附加位错边界(IDBS)。一般来说,几何必须位错边界是用来协调各相邻位错胞块之间的取向差,即晶格的旋转,含有大量多余的净位错柏矢,位错差大。而附加位错边界中缠结的位错的净柏矢几乎为零,位错胞向的取向差小。
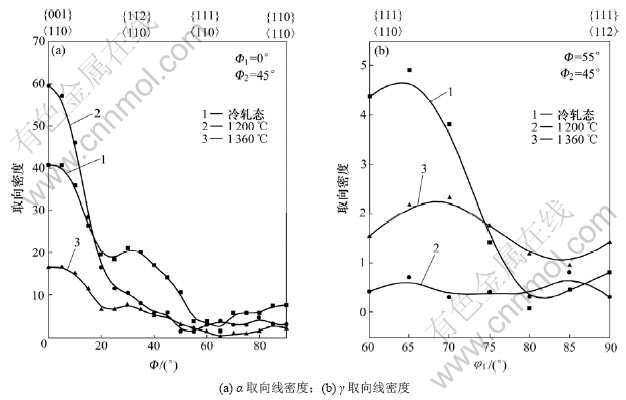
图5 Ta-7.5%W合金箔材退火过程晶粒取向变化的取向线分析[11]
Fig.5 Orientation line analysis results of Ta-7.5%W in annealing process
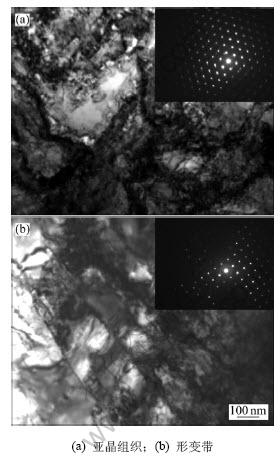
图6 冷轧态Ta-7.5%W合金箔材的TEM像
Fig.6 TEM images of cold-rolled state Ta-7.5%W
图7所示为Ta-7.5%W合金箔材1 200 ℃退火1 h的TEM像。由图7可以看出:与冷轧态Ta-7.5%W合金箔材的TEM显微组织相比,大量位错消失,位错胞壁已经变薄,胞壁中缠结的位错数量有所减少,这是因为在退火过程中,位错线会向胞壁迁移并与胞壁中的异号位错相互抵消,降低了胞壁处的位错密度。在轧面//{111}晶面取向上的晶粒中形成了大量的亚晶结构,此时亚晶边界开始迁移形成再结晶晶核(图7(a))。而在轧面//{100}晶面取向上的晶粒中,形变带中位错密度也减小,开始形成亚晶结构。由此可以看出在轧面//{111}晶面取向上的晶粒,其再结晶进程要比轧面//{100}晶面取向上的晶粒缓慢。
图8所示为Ta-7.5%W合金箔材1 360 ℃退火1 h的TEM像,由图8可以看出:合金经1 360 ℃退火 1 h后合金中形成了平直的大角度晶界,说明此时合金中发生了再结晶。相邻亚晶粒某些公共边界上的位错通过攀移和滑移,转移到周围晶界或角度较大的亚晶界上,由于大角亚晶界上吸收了更多的位错,使相邻亚晶粒的位向差增大,小角晶界逐渐转化为大角晶界,它比小角晶界具有更高的迁移率, 可迅速移动, 清除其移动路程中存在的位错, 最终在它后面留下无畸变的组织。
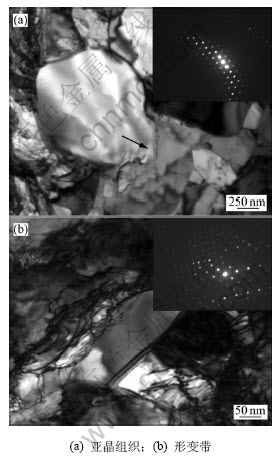
图7 Ta-7.5%W合金箔材1 200 ℃退火1 h的TEM像
Fig.7 TEM images of Ta-7.5%W alloy after annealing at 1 200 ℃ for 1 h
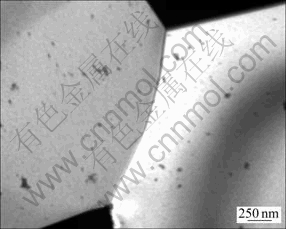
图8 Ta-7.5%W合金箔材1 360 ℃退火1 h的TEM像
Fig.8 TEM image of Ta-7.5%W alloy after annealing at 1 360 ℃ for 1 h
3 讨论
Ta-7.5%W合金在冷轧过程中形成了强烈的{001}
和{112}
织构。图9(a)所示为冷轧{001}
织构形成机理。钽钨合金属于体心立方晶粒,滑移往往会沿着最密排面上的密排方向
进行滑移,{110}
,{112}
和{123}
都是其潜在的滑移系。为了简单起见,只考虑(211)
和
[111] 2个滑移,由这2个滑移系对称滑移即可形成{001}
织构,如图9(a)所示。在{211}和
晶面上分布了两组位错平行于
,柏氏矢量分别平行于[111]和
的刃型位错[13-14],同时位错在(211)和
面上并不是均匀分布。由Lee的关于bcc金属的再结晶模型理论[15]可知(图9(b)):当钽钨合金的最大应力方向[111]转动到与最小弹性模量方向[100]一致时,退火过程中储能的释放最大,再结晶进行速度达到最快,导致了{111}
再结晶织构的形成[16]。
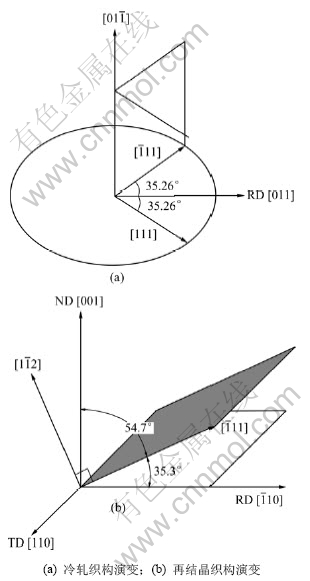
图9 冷轧、再结晶织构形成示意图
Fig.9 Formation diagram of cold-rolled and recrystallization texture
另外根据近代再结晶形核理论[17],不同的变形组织,其再结晶的形核机制也不同。通过透射电镜观察,发现冷轧态Ta-7.5%W合金箔材在轧面//{111}晶面取向上形成了大量的位错胞亚结构,再结晶过程中,由于变形大,位错密度高,亚晶界曲率大,易于迁移。亚晶界迁移中清除并吸收其扫过区相邻亚晶的位错,使亚晶界获得更多位错,与相邻亚晶取向差增大变为大角晶界,当大角界面达到临界曲率半径,便成为稳定再结晶核心。这种亚结构主要通过亚晶界迁移、亚晶长大形核。而在轧面//{100}晶面方向上形成了形变带,形变带中取向差梯度比较大,亚晶界的位错主要是通过攀移和交滑移而迁出,使亚晶界消失,相邻亚晶转动。这种形核机制相对亚晶界迁移、长大机制较慢,这与织构测量所得结果相一致。
4 结论
(1) 冷轧变形的Ta-7.5%W合金箔材经1 360 ℃退火时硬度减小速度明显大于经1 200 ℃退火时硬度减小速度,说明此时已发生再结晶。
(2) Ta-7.5%W合金冷轧态的主要织构为{001}
和{112}
,回复再结晶之后形成典型的{111}
再结晶织构。
(3) 经95%冷轧变形的Ta-7.5%W合金箔材具有各向异性,在轧面//{111}晶面取向上形成位错胞亚结构,在再结晶过程中通过亚晶界迁移、亚晶长大形核;而在轧面//{100}晶面取向上形成了形变带,主要是通过亚晶转动、聚合形核;这种组织上的差异,使再结晶形核机制不同,影响再结晶织构。
参考文献:
[1] Ensinger W. Ion-beam sputter coating of tantalum tube inner walls for protection against hydrogen embrittlement[J]. Surface and Coatings Technology, 1996, 84(1/2/3): 434-438.
[2] Cardarelli F, Taxil P, Savall A. Tantalum protective thin coating techniques for the chemical process industry: Molten salts electrocoating as a new alternative[J]. International Journal of Refractory Metals and Hard Materials, 1996, 14(5/6): 365-381.
[3] Laurila T, Zeng K, Kivilahti J K, et al. Tantalum carbide and nitride diffusion barriers for Cu metallization[J]. Microelectronic Engineering, 2002, 60(1/2): 71-80.
[4] Li S, Park H S, Liang M H, et al. Effects of Cu diffusion behaviors on electronic property of Cu/Ta/SiO2/Si structure[J]. Thin Solid Films, 2004, 462/463: 192-196.
[5] Balaji T, Govindaiah R, Sharma M K, et al. Sintering and electrical properties of tantalum anodes for capacitor applications[J]. Materials Letters, 2002, 56(4): 560-563.
[6] Delplanque J P, Cai W D, Rangel R H, et al. Spray atomization and deposition of tantalum alloys[J]. Acta Materialia, 1997, 45(12): 5233-5243.
[7] Sandim H R Z, Martins J P, Pinto A L, et al. Recrystallization of oligocrystalline tantalum deformed by cold rolling[J]. Materials Science and Engineering, 2005, 392(1/2): 209-221.
[8] Hosseini E, Kazeminezhad M. Dislocation structure and strength evolution of heavily deformed tantalum[J]. International Journal of Refractory Metals and Hard Materials, 2009, 27(3): 605-610.
[9] Bunge H J. Texture analysis in materials science[M]. London: Butterworths, 1982: 10-19.
[10] Nasser S N, Kapoor R. Deformation behavior of tantalum and a tantalum tungsten alloy[J]. International Journal of Plasticity, 2001, 17(10): 1351-1366.
[11] 金鹏. 钽钨合金箔材组织结构及性能的研究[D]. 长沙: 中南大学材料科学与工程学院, 2009: 22-36.
JIN Peng. The structure and properties of Ta-W alloy[D]. Changsha: Central South University. School of Materials Science and Engineering, 2009: 22-36.
[12] Azushima A, Kopp R, Korhonen A, et al. Severe plastic deformation (SPD) processes for metals[J]. CIRP Annals- Manufacturing Technology, 2008, 57(2): 716-735.
[13] Park Y B, Lee D N, Gottstein G. A model of the development of recrystallization textures in body centered cubic metals[J]. Materials Sciences and Engineering A, 1998, 257(1): 178-184.
[14] Lee M G, Wang J, Anderson P M. Texture evolution maps for upset deformation of body-centered cubic metals[J]. Materials Science and Engineering A, 2007, 463(1/2): 263-270.
[15] Kumar B R, Ghosh M. Surface and mid-plane texture evolution in austenite phase of cold rolled austenitic stainless steels[J]. Materials Science and Engineering A, 2007, 457(1/2): 236-245.
[16] Lee D N. The evolution of recrystallization textures from deformation textures[J]. Scripta Metallurgica et Materialia, 1995, 32(10): 1689-1694.
[17] 郑子樵. 材料科学基础[M]. 长沙: 中南大学出版社, 2005: 371-372.
ZHENG Zi-qiao. Journal of materials science[M]. Changsha: Central South University Press, 2005: 371-372.
(编辑 陈爱华)
收稿日期:2011-04-06;修回日期:2011-07-15
基金项目:国家高技术研究发展计划(“863”计划)项目(2006AA03Z517);湖南省自然科学基金资助项目(05JJ30095)
通信作者:汪明朴(1952-),男,湖北安徽人,教授,博士生导师,从事有色金属材料研究;电话:0731-88830264;E-mail: wangmp@csu.edu.cn