Trans. Nonferrous Met. Soc. China 20(2010) s988-s992

Preparation of SiCp/A356 electronic packaging materials and its thixo-forging
WANG Kai-kun(王开坤), KANG Yong-lin(康永林), SONG Pu-guang(宋普光),
XU Feng(徐 峰), LI Xian-hui(黎先辉)
School of Materials Science and Engineering, University of Science and Technology Beijing, Beijing, 100083, China
Received 13 May 2010; accepted 15 July 2010
Abstract: The rapid development of electronic packaging industry has resulted in higher requirement for packaging materials. The packaging material of SiC reinforced A356 aluminum alloy was fabricated by mechanical mixing method, and the SiCp/Al composite billet was formed by thixo-forging to manufacture the electronic packaging shell. The microstructure of the produced part was investigated. Two different thixo-forging procedures for manufacturing electronic packaging shell were analyzed. The results show that after being heated to 600℃ and held for 3 h, SiCp has good compatibility with A356 aluminum alloy and the SiCp/A356 composite billet can meet the requirements of thixo-forging. When the billet was remelted to 580℃, held for 10 min, the homogeneous microstructure with the best thixo-formability can be realized. The thixo-forging of electronic packaging shell is feasible.
Key words: SiCp/Al composite; electronic packaging shell; thixo-forging; microstructure
1 Introduction
The electronic packaging is to integrate various electronic components reasonably and isolate them from surrounding environment, and at the same time dissipate the heat generated in the work of semiconductor chips[1-3]. According to packaging materials, the electronic packaging has many types, such as plastic packaging, ceramic packaging and metal matrix composites packaging[4]. Due to its high mechanical strength, low linear expansion rate and high thermal conductivity, metal matrix composite is widely used in aerospace, automotive and electronics, among which the silicon carbide reinforced aluminum matrix (SiCp/A356) is the most frequently used composite[5].
Conventionally, the SiC electronic packaging shell is produced through powder injection technology. There are four main steps. First, the SiC particles is mixed into the resin completely on a certain condition. Second, the mixture is injected into the forming cavity so that the expected shape of the part can be got. Then, the semi-finished part is sintered and the SiC skeleton is obtained. At last, alitizing, namely on a certain condition,aluminum liquid into the SiC skeleton[6-7]. It can be found that the production line is long, the efficiency is low and the air tightness of the produced part is bad. On the other hand, since the specific property of the metals in semi-solid state is found, many other important advantages, for example low solidification shrinkage, leading to a more precise dimension product; net-shape forming, filling much more complicated shapes with thinner section,have been discovered[8-12]. In this study, an innovative forming method is put forward in producing electronic packaging shell of A356 aluminum alloy reinforced by SiCp[13-14]. The basic theory is separation of solid phase and liquid phase during thixoforming, in which small SiC particles flow with the liquid phase ahead of the solid phase, so the electronic packaging shell with high content of SiC particles an be produced, satisfying the requirements of electronic packaging shell.
Based on the self-made casting mold and thixo-forging die, three processes: preparation of SiCp/A356 composite, reheating and thixotropic forming, were studied. Two different thixo-forging procedures for manufacturing electronic packaging shell were analyzed.
2 SiCp/Al composite preparation
The thixo-forming generally includes three stages: preparation of semi-solid billet, reheating semi-solid billet and thixo-forming. In this experiment, the mechanical mixing method is adopted to prepare the billet of SiCp/A356 composite.
First, the blocks of A356 aluminum alloy was put into porcelain crucible and it was heated to melt by HXR-200 multistage digital control box resistance furnace. After complete smelting, the temperature of the liquid alloy was adjusted to 590 °C, the pretreated SiC particles were added into the liquid and at the same time the slurry was stirred for about 10 min at a speed of 50-80 r/min. During the procedure, the primary dendrite was broken down and semi-solid rheology slurry with ball or globular microstructure was obtained. The experiments proved that, if the stirring speed was below 50 r/min, SiC particles would be liable to be attached to the blade, and could not mix with the liquid aluminum alloy completely, resulting in lamination phenomenon. If the stirring speed was over 80 r/min, due to the large centrifugal force, the SiC particles would tend to flow to the inner surface of the crucible, resulting in insufficient stir, which is also not beneficial to the homogeneity of the composites. Furthermore, high stirring speed could lead to splash of the smelt slurry. After stirring evenly for about 10 min, the slurry was poured into the preheated casting mold and SiCp/A356 composite bar billets (with the dimensions of d 30 mm×45 mm ) were got, as shown in Fig.1. It can be seen from Fig.1 that the surface of the billet is smooth, and SiC particles are distributed well.
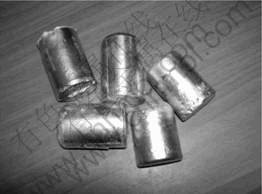
Fig.1 Billets of SiCp/A356 composites
3 Billet reheating process
Among the three stages, reheating acts as the connecting role, which not only makes the slurry have globular microstructure, but also provides the necessary conditions for the successive thixo-forging. Therefore, determination of heat strategy is the most important work during the reheating process. However, heating efficiency and inertia of the heating furnace should also be considered. In this experiment, a HXR-200 the multistage digital control box resistance furnace was used, semi-solid temperatures of 560, 570, 575, 580 and 585 °C were tried, the corresponding microstructures were also analyzed. After optimization, one reheating strategy of 580 °C, 10 min was selected. The heating strategy is shown in Fig.2.
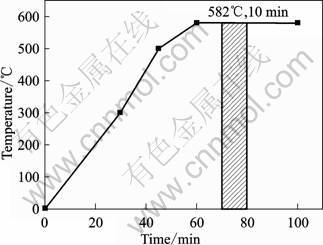
Fig.2 Reheating curve for billet of SiCp / A356 composite
4 Thixo-forging of electronic packaging shell
The after heated billet was transferred quickly into the preheated forging die. The upper forging die was installed on the ram, the lower die and extrusion rod were installed on the platform. The die preheating temperature was 300 °C, the press capacity was 1 960 kN. The schematic diagram of die of thixo-forging of the electronic packaging shell is shown in Fig.3.
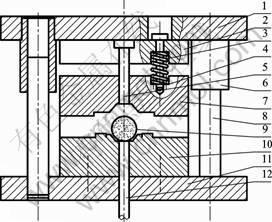
Fig.3 Schematic diagram of die of thixo-forging for electronic packaging shell: 1 Upper plate; 2 Backing plate; 3 Spring; 4 Screw; 5 Upper punch; 6 Guide sleeve; 7 Upper die; 8 Guide pole; 9 Billet; 10 Lower die; 11 Lower plate; 12 Lower punch
Two different thixo-forging processes were designed for fabricating the electronic packaging shell.
Fig.4 shows the thixo-forging of electronic packaging shell with upper punch. The process is that with the downward-running of the ram, the lower surface of the upper die contacts with the upper surface of the lower die, and a closed die cavity is created under the action of the spring in Fig.4(b). At this point, the billet was slightly deformed (upset) and didn’t flow into the die cavity for the electronic packaging shell. As the ram continues to go down, the upper die was pushed by the spring and remained still. However, as the upper punch moves down further along the inner surface of the wall in the upper die, it contacts with the billet surface and gradually squeezes the billet into die cavity for electronic packaging shell, as shown in Fig.4(c). After dwelling for about 20s, the ram withdraws and the backing plate separates from the upper die under spring back pressure, however, the upper die and lower die is still in the state of contact. When the ram’s backward stroke is larger than that of the initial gap between the backing plate and the upper die, the upper die and lower die separates each other, then the formed electronic packaging shell can be taken out from the die cavity.
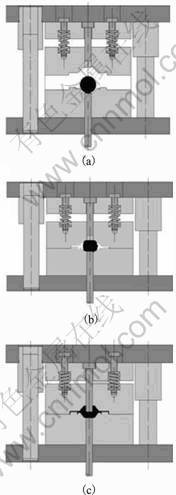
Fig.4 Thixo-forging of electronic package shell with upper punch
The advantage of the thixo-forging process with upper punch is that die closing process and forging process are almost completed at the same time, so the time for the whole thixo-forging process is shortened, the work efficiency is high. Furthermore, the billet temperature decreases only a little, and the thixo-forging process can be accomplished in semi-solid temperature range, so large amounts of SiC particles can flow with the liquid phase to the die cavity, therefore, the produced parts have high SiC volume percentage. The disadvantages are that since the two processes of upsetting and squeezing are finished almost at the same time, no sooner have the die cavity been created than the squeeze process started, which inevitably leads to the existence of burrs, as shown in Fig.5.
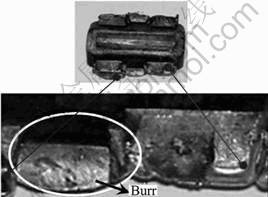
Fig.5 Burr in thixo-forged part during thixo-forging with upper punch
Fig.6 shows the thixo-forging of electronic packaging shell with lower punch. Compared with the die movement in Fig.4, the upper punch is a little short and the squeeze process is accomplished by the lower punch, the squeeze process doesn’t begin until the closed die cavity has been created completely.
The advantages of the thixo-forging of electronic packaging shell with lower punch is that during the whole thixo-forging process, the lower punch works in the closed die cavity, the parts can be produced with high density and no burrs appear. And the closed die cavity can lead to maximum solid-liquid segregation, which allows more SiC particles flow into the die cavity for electronic packaging shell. The disadvantage is that the lower punch needs a reaction time of about 2 s, which can lead to temperature decreasing of the forming billet.
In our present research, some experiments were done during the thixo-forging process in Fig.4. The results show that the burr problem always exists. In order to improve the quality of the thixo-forged part, in our next research plan, the thixo-forging process with lower punch will be adopted.
5 Analysis of first thixo-forged part
Fig.7 shows the schematic diagram of the electronic packaging shell (cross-section). In order to observe the SiCp content in the produced part, the microstructures in three points were analyzed. It can be observed from Fig.8 that, during the thixo-forging process, due to high deformation speed, the solid-liquid separation phenomenon appears. Although the SiCp content in the produced part could not be measured precisely, a comparison of the microstructures between Fig.8(a) and Fig.8(c) shows that the SiCp content in Fig.8(c) is obviously higher than that in Fig.8(a). And it also reveals that the farther the composite slurry flows, the higher the SiCp content is.
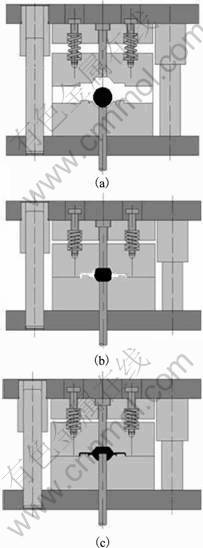
Fig.6 Thixo-forging of electronic package shell with lower punch
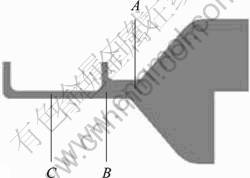
Fig.7 Schematic diagram of electronic packaging shell from thixo-forging (cross-section)
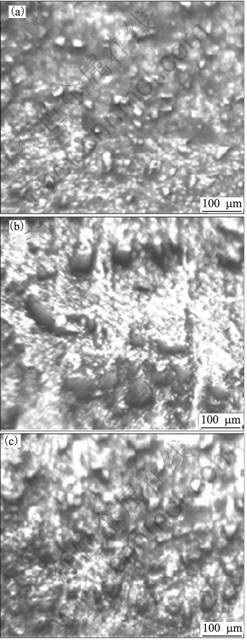
Fig.8 Microstructures of different areas of thixo-forged part in Fig.7: (a) Area A; (b) Area B; (c) Area C
6 Conclusions
1) Based on the analysis of the segregation characteristic in semi-solid forming, an innovative manufacturing technology was put forward for producing electronic packaging shell with SiCp/A356 composite.
2) The SiCp and A356 aluminum alloy have good compatibility when the SiCp particles were heated to 600 °C and held for three hours.
3) An optimized strategy of 580 °C, 10 min was found in reheating SiCp/A356 composite. SiC particles distribute homogeneously in the eutectic area of the microstructure, being favorable for SiC particles flowing with the liquid phase during the successive thixo-forging process.
4) With the aim to fabricate electronic packaging shell with the maximum SiCp content, two different thixo-forging procedures for manufacturing electronic packaging shell were analyzed. The experiments testified the feasibility of the thixo-forging for producing electronic packaging shell.
References
[1] MOORES K A, JOSHI Y K. High performance packaging materials and architectures for improved thermal management of power electronics [J]. Future Circuits Int, 2001 (7): 45-49.
[2] MODIGELL M, HUFSCHMIDT M, PETERA J. Two-phase simulation and visualization of isothermal die filling processes [C]// Proc of the 7th S2P Proceeding. Japan: The Conference Organizer, 2002.
[3] ZWEBEN C. Advanced Materials for Optoelectronic Packaging [J] . Optoelectronics , 2002 (9): 37240.
[4] KHAKBIZ M, SIMCHI A, BAGHERI R. Analysis of the rheological behavior and stability of 316L, stainless steel-TiC powder injection molding feedstock [J]. Materials Science and Engineering A, 2005, 407: 105-113.
[5] KOPP R, KALLWERT J, MOELLER T, SEIDL I. Materials forming and joining of commercial steel grades in the semi-solid state [J]. Processing Technology, 2002,130/131: 562-568.
[6] WENZELBURGER M, AISINA M N, VON Niessen K, GADOW R. Thermal spray manufacturing of semi-finished parts for thixoforming of fiber and particle reinforced metal matrix composites [J]. Diffusion and Defect Data Part B, 2006, 116/117: 375-378.
[7] FLEMINGS M C. Behavior of metal alloys in the semisolid state [J]. Metallurgical Transactions A, 1991, A22: 957-981.
[8] LEE B S, JOO D H, KIM M H. Extrusion behavior of AI-Cu alloys in the Semi-solid state [J]. Materials Science and Engineering A, 2005, 402: 170-176.
[9] HIRT G, BLECK W, SHIMAHARA H, BUHRIG-POLACZEK A, PUTTGEN W. Semi-solid casting and forging of steel [J]. Die Casting Eng, 2006, 49B: 32-8.
[10] WANG Kai-kun. Manufacturing electronic packaging shell of SiC reinforced composites by means of semi-solid forming CN200710119013.0 [P]. 2007-10-14.
[11] MA Chun-mei, WANG Kai-kun, XU Feng. Research on extrusion thixotropic of SiCp/A356 aluminum alloy composite material [J]. Electronic Components and Materials, 2009, 28(6): 63-66.
[12] XU Feng. Investigation on SiCp/A356 alloy composite preparation and its thixo-forging of electronic packaging shell [D]. Beijing: Universitly of Science and Technology of Beijing, 2009.
[13] WANG Kai-kun. Multilayer tube thixo-co-extrusion technology and its equipment. CN2007100644454.5 [P]. 2007-03-16.
[14] WANG Kai-kun, KOPP R, HIRT G. Thixo-forging and thixo-joining of an integrated product [J]. Steel Research International, 2006, 77(5): 349-354.
(Edited by LI Yan-hong)
Foundation item: Project (2007AA03Z119) supported by the National High Technology Research and Development Program of China; projects (2102029, 2072012) supported by Beijing Natural Science Foundation, China
Corresponding author: WANG Kai-kun; Tel: +86-10-62333997; E-mail: kkwang@mater.ustb.edu.cn