
Preparation and oxidation property of ZrB2-MoSi2/SiC coating on carbon/carbon composites
ZHANG Wu-zhuang, ZENG Yi, GBOLOGAH Lemuel, XIONG Xiang, HUANG Bai-yun
State Key Laboratory of Powder Metallurgy, Central South University, Changsha 410083, China
Received 10 November 2010; accepted 16 February 2011
Abstract: To improve the oxidation resistance of carbon/carbon composites, ZrB2-MoSi2/SiC coating on the carbon/carbon substrate was prepared. The inner coating of SiC was prepared by pack cementation and the outer coating of ZrB2-MoSi2 was prepared by slurry painting. The phase compositions and microstructures of the coating were characterized by XRD and SEM, respectively. The preparation and the high temperature oxidation property of the coated composites were investigated. The results show that the outer coating of carbon/carbon composites is composed of ZrB2, MoSi2 and SiC phases. The mass losses of the ZrB2-MoSi2/SiC coated samples with SiC nano-whiskers after 30 h and 10 h of oxidation at 1 273 K and 1 773 K were, respectively, 5.3% and 3.0%. The ZrB2-MoSi2/SiC coated samples exhibit self-sealing performance and good oxidation resistance at high temperature.
Key words: carbon/carbon composites; ZrB2-MoSi2; SiC; coating; oxidation
1 Introduction
Carbon/carbon (C/C) composites have many advantages over traditional materials, such as low density, high specific strength and retention of mechanical properties at high temperatures. However, C/C composites oxidize rapidly when they are exposed to an oxidizing atmosphere at high temperatures. Therefore, much attention has been given to the development of methods for oxidation protection of carbon materials [1]. One of such approaches most widely used is to apply coatings to the article surface [2], such as SiC [3], MoSi2 [4] and ZrSiO4 [5]. The oxidation protection properties of these coatings are different from the fabrication technologies such as pack cementation, chemical vapor deposition (CVD) and slurry painting. Slurry painting has a lot of advantages including its easy processes, low costs, etc. MoSi2 is promising candidate material for high-temperature applications because of the self-sealing performance at high-temperature [6]. ZrB2 has excellent anti-oxidation property due to B2O3 glaze which is one kind of oxides of ZrB2 at 1 273 K [7]. The SiC ceramic also has outstanding anti-oxidation properties because of the self-sealing performance of SiO2 formed from oxidation of SiC. However, not much literature has been reported for the oxidation performance of ZrB2-MoSi2 coating prepared by slurry painting. In the present work, the preparation and the oxidation property of ZrB2-MoSi2 coating on the C/C composites were investigated. In order to relieve the thermal expansion mismatch between the outer coating and C/C composites, the inter SiC transition layer was prepared by pack cementation.
2 Experimental
The C/C composites used were three-dimensional materials with a density of 1.78 g/cm3. The specimens were polished using a SiC paper, cleaned with ethanol and oven dried at 393 K. The inner coating of SiC was prepared by pack cementation. The sintering temperature and holding time were 2 073 K and 2 h, respectively. The pack chemistry was as follows: 60%-80% (mass fraction) Si, 10%-20% carbon, and 1%-5% Al2O3. The ZrB2-MoSi2 layer was prepared by painting the slurry mixture comprising of 50%Si, 25%ZrB2, 25%Mo powders and silica sol on the surface of SiC coated substrates, and then dried. Since Si element would evaporate in the sintering procedure, two methods were taken to control the Si content. The first one was to control the mole ratio of Si to Mo in the mixture larger than that of MoSi2 (2:1). The second one was to decrease the evaporation of Si from the coating by wrapping substrates in a parchment paper on which the Si and silica sol were painted. The samples treated by the first and second methods were labeled A and B, respectively. Then the two kinds of samples were placed in a graphite crucible with a graphite lid and heated in an argon atmosphere at 1 773 K for 15 min to obtain ZrB2-MoSi2 coating. The phase composition of the prepared coatings was determined with X-ray diffractometer (XRD). The morphologies of the coatings were analyzed using scanning electronic microscope (SEM). The balance with an accuracy of 0.1 mg was used to study the mass changes of samples after oxidation.
3 Results and discussion
3.1 Phase composition and micro-structure of coating
Figure 1 shows the XRD patterns of the ZrB2-MoSi2/SiC coating. It is observed that ZrB2, MoSi2 and SiC are the main phases. The peak intensity of SiC in Fig. 1(b) is stronger than that of SiC in Fig. 1(a), suggesting that more SiC phases were formed in the coating after wrapping with painted parchment paper. The SiO2 phases came from the silica sol.
Figure 2 shows the surface and cross-section SEM micrographs of ZrB2-MoSi2/SiC coatings. Figure 2(a) shows the surface SEM image of ZrB2-MoSi2/SiC coating of sample A. It is observed that there are a lot of cracks on the surface of the coating, which is due to the silica sol shrinkage and the crystal volume change when Si reacts with Mo [8]. Figure 2(b) shows the surface SEM image of ZrB2-MoSi2/SiC coating of sample B. It is noted that the coating is denser than that on sample A due to the formation of the whiskers and particles, as shown in Fig. 2(e). Figures 2(c) and (d) show the cross-section micrographs of SiC coating and ZrB2-MoSi2 coating, respectively. From Fig. 2(c), it is observed that there is good combination between the SiC coating and carbon substrate due to the infiltration of SiC into the fibers of the substrate which can enhance the thermal shock resistance. There is also no obvious interface between SiC coating and ZB2-MoSi2 coating (Fig. 2(d)), inferring that there is good physical compatibility between the inner and outer coatings. From Fig. 2(f), the nano- whiskers on ZrB2-MoSi2 coating on sample B can be observed. Results obtained from Fig. 3 indicate that the composition of the nano whisker is SiC.
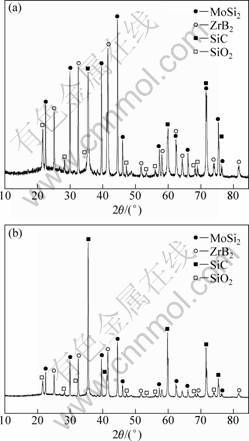
Fig. 1 XRD patterns of ZrB2-MoSi2/SiC coatings: (a) Sample A; (b) Sample B
Ca and Al in Fig. 3 may be impurities in the Si powder. The diameters of the whiskers are 25-63 nm. Some cracks on the surface of the coating are full of SiC whiskers which can enhance the oxidation resistance of the coated C/C composites. The mechanism of crystal growth of the SiC nano-whisker can be attributed to the reactions [9]:
SiO2(s)+Si(l)=2SiO(g) (1)
SiO(g)+2C(s)=SiC(s)+CO(g) (2)
SiO(g)+3CO(s)=SiC(s)+2CO2(g) (3)
SiO is obtained by the reaction between SiO2 and Si on the parchment paper (reaction 1), and SiO reacts with the carbon to form SiC whiskers because of the high carbon potential in graphite crucible.
As noted in Fig. 2(e), not only the SiC whiskers were observed, but also the SiC particles were found, which is related to the different growth velocities of SiC crystals. The velocity of crystal growth of SiC can be attributed to the following equation [10]:
(4)
where A is equilibrium constant of reaction; T is thermodynamic temperature; pco is partial pressure of CO; Δε is activation energy. Reaction (4) shows that high partial pressure of CO is beneficial to the growth of SiC crystal. The SiC whiskers almost form from reaction (3) and the SiC particles form from reaction (2) [11-12]. Therefore, the higher partial pressure of CO accelerates the reaction of reaction (3), which, in turn, results in formation of more SiC whiskers. Formation of some SiC particles is due to the higher equilibrium constant of reaction (2) than reaction (3).
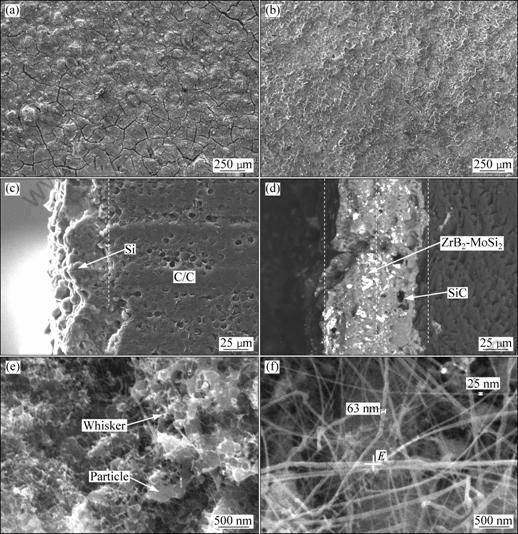
Fig. 2 Surface and cross-section SEM micrographs of ZrB2-MoSi2/SiC coating: (a) Surface micrograph of sample A; (b) Surface micrograph of sample B; (c) Cross-section micrograph of SiC coating; (d) Cross-section micrograph of ZrB2-MoSi2/SiC coating; (e) Particles and whisker of SiC; (f) SiC nano-whiskers
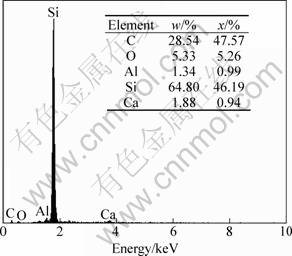
Fig. 3 EDS analysis of surface spot E in Fig. 2(f)
3.2 Oxidation properties analysis
3.2.1 Oxidation properties of coated samples at 1 273 K
Figure 4 shows the isothermal oxidation curves of the C/C composites with coatings in air at 1 273 K. Figure 5 shows the surface SEM micrographs of the ZrB2-MoSi2/SiC coating after oxidation at 1 273 K for 30 h. Figure 6 shows XRD patterns of ZrB2-MoSi2/SiC coating after oxidation at 1 273 K.
From Fig. 4, it can be observed that the mass losses of ZrB2-MoSi2/SiC coated samples A and B after 30 h of oxidation at 1 273 K are 30.2% and 5.3%, respectively. This suggests that the oxidation protection for sample B is superior to that for sample A. The single SiC coated sample has a mass loss of 11.0% after oxidation for 5.5 h. Figure 5(b) shows that a ceramic glaze is formed on the surface of the coating.
There is new phase of ZrO2 since the oxidation of ZrB2 can form ZrO2 and B2O3. However, the B2O3 phase is not detected. It is believed that the samples were quenched in air in the course of drawing the samples rapidly out of the furnace and that the liquid B2O3 was not able to crystallize before solidification. So the ceramic glaze on the coating can be considered B2O3 (Fig. 5(b)) [13]. The B2O3 glaze seals the holes and cracks due to the liquidity on the coating [7], which can enhance the oxidation resistance of the coated C/C composites. However, obvious cracks can be found in Fig. 5(a). The original cracks on the coating without SiC whiskers and particles covering was too wide for limited B2O3 glaze to be sealed. This may be the reason why the oxidation protection for sample B is superior to that for sample A.
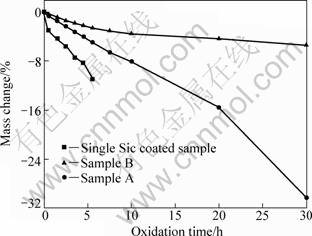
Fig. 4 Isothermal oxidation curves of C/C composites with coatings in air at 1 273 K
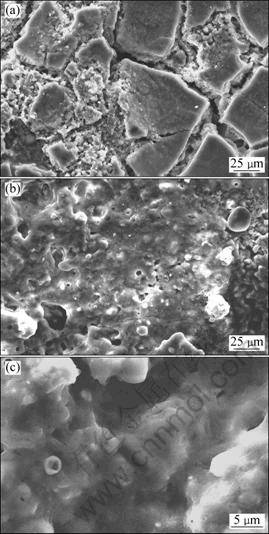
Fig. 5 Surface SEM micrographs of coatings after oxidation at 1 273 K for 30 h: (a) Sample A; (b), (c) Sample B
From Fig. 6 and Fig. 1(b), the peaks of MoSi2 decreased and that of SiO2 increased after oxidation, which indicates that MoSi2 was oxidized, producing SiO2 and MoO3 at 1 273 K [14]. However, the MoO3 phase is not detected due to MoO3 (melting point: 1 068 K) evaporation at this temperature which results in some minor holes on the coating (Fig. 5(b)). The evolution of CO2 and CO from the SiC and substrate oxidation may result in the other holes. The whiskers disappeared and the coating became smooth (Fig. 5(c)), also suggesting that the SiC phase was oxidized. Hence, all of these reactions can be described as follows:
2ZrB2(s) +5O2(g)=2ZrO2(s)+2B2O3(g) (5)
2MoSi2(s)+7O2(g)=2MoO3(g)+4SiO2(s) (6)
SiC(s)+2O2(g)=SiO2(s)+CO2(g) (7)
2SiC(s)+3O2(g)=2SiO2(s)+2CO(g) (8)
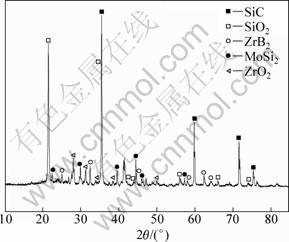
Fig. 6 XRD pattern ZrB2-MoSi2/SiC coating after oxidation at 1 273 K
3.2.2 Oxidation properties of coated samples at 1 773 K
Figure 7 shows isothermal oxidation curves of the coated C/C composites in air at 1 773 K. Figure 8 shows the surface and cross-section SEM micrographs of ZrB2-MoSi2/SiC coating after oxidation at 1 773 K for 10 h.
From Fig. 7, the mass loss of the single SiC coated samples is 9.2% after oxidation for 3 h, which suggests that the sample with a single coating of SiC has limited protection for substrates. It is also found that the mass losses of the samples A and B after 10 h of oxidation at 1 773 K are 3.6% and 3.0%, respectively. This suggests that ZrB2-MoSi2/SiC coated samples have excellent oxidation resistance due to the formation of a glassy layer which seals the original cracks and the coating becomes more smoother (Fig. 8(a)). In Fig. 8 (b), there are still good combination between the carbon substrate and coatings and there is no obvious interface between SiC coating and ZrB2-MoSi2 coating, which is the reason why the coated samples possess good thermal shock resistance during oxidation at 1 773 K. From Figs. 8(c) and (d), the samples A and B have similar micrographs after oxidation at 1 773 K, which results in the excellent anti-oxidation performance of the two samples.
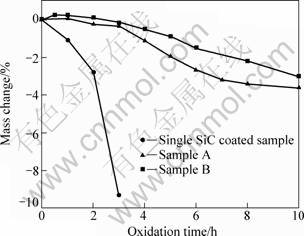
Fig. 7 Isothermal oxidation curves of coated C/C composites in air at 1 773 K for 10 h
Figure 9 shows XRD patterns of ZrB2-MoSi2/SiC coating after oxidation at 1 773 K. Figure 10 shows the phase distribution of the coating and EDS analysis of the corresponding surface spots.
From Fig. 9, ZrSiO4 phase formed was due to the reaction between ZrO2 and SiO2. In Fig. 10, there are two kinds of textures (shown as grey 1, white 2) on the coating after oxidation. By spot EDS analysis, the elements composing of grey 1 and white 2 are mainly Si, O and Si, O, Zr, respectively. Based on this fact together with the X-ray diffraction analysis in Fig. 9, it is believed that the grey phase 1 is composed of SiO2, whereas the white phase 2 is composed of ZrSiO4. From Fig10(a), it is observed that the ZrSiO4 phase spreads around the glassy SiO2, which can enhance the anti-oxidation performance based on the following facts: 1) glassy SiO2 possesses low oxygen diffusion coefficient (10-13 g/(cm?s) at 1 473 K) which can decline/reduce the velocity of oxygen through the coating [15]; 2) thermal expansion coefficient of ZrSiO4 is close to that of SiC, which can eliminate the thermal expansion mismatch between the outer and inner coating. The ZrSiO4 phase also has pining effect on the melting-point (2 550 °C) [5] in the case of the fact that the SiO2 glaze vaporized fast.
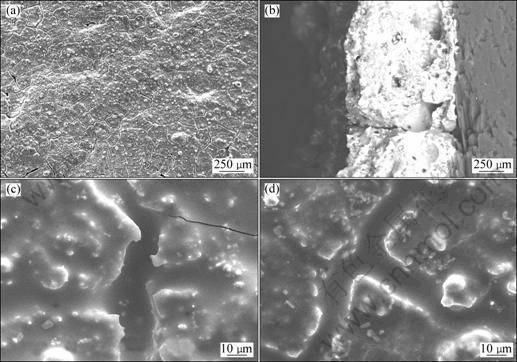
Fig. 8 Surface (a, b) and cross-section (c, d) SEM micrographs of ZrB2-MoSi2/SiC coating after oxidation at 1 773 K for 10 h: (a), (c) Sample A; (b), (d) Sample B
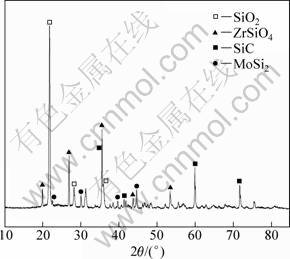
Fig. 9 XRD pattern of ZrB2-MoSi2/SiC coating after oxidation
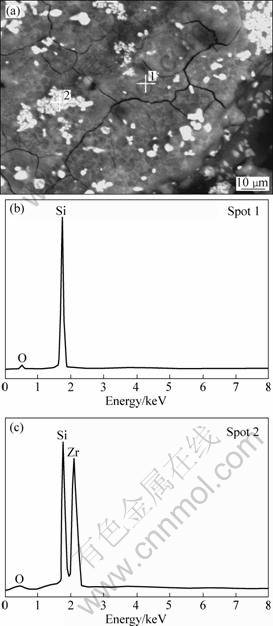
Fig. 10 Phase distribution of ZrB2-MoSi2/SiC coating (a) and EDS analyses (b, c) of corresponding surface spots
4 Conclusions
1) ZrB2-MoSi2/SiC coating on the carbon/carbon substrate was prepared successfully. The outer coating is composed of ZrB2, MoSi2, and SiC phases. There are lots of SiC nano-whiskers on ZrB2-MoSi2/SiC coating for sample B.
2) Single SiC coating has limited protection for carbon/carbon substrates. The ZrB2-MoSi2/SiC coated samples B shows good anti-oxidation ability at 1 273 K due to the SiC nano-whiskers covering the original cracks and the formation of B2O3 glaze after oxidation. The ZrB2-MoSi2/SiC coated samples exhibits self-sealing performance and oxidation resistance due to the formation of ZrSiO4 and SiO2 glaze at 1 773 K.
References
[1] DZYADIKENICHY V, OLEJNIK V E. The ways of protection of the graphite materials against oxidation [J]. Poroshkovaya Metallurgiya, 1996, 3-4: 7-41.
[2] XU Y D, CHENG L F, ZHANG L T. Oxidation behavior and mechanical properties of C/SiC composites with Si-MoSi2 oxidation propetion coating [J]. J Mat Sci, 1999, 34(24): 6009-6014.
[3] HUANG Jian-feng, ZENG Xie-rong, LI He-jun. Influence of the preparation temperature on the phase, microstructure and anti-oxidation property of a SiC coating for C/C composites [J]. Carbon, 2004, 42(9): 1517-1521.
[4] YAN Zhi-qiao, XIONG Xiang, XIAO Pen, CHEN Feng, ZHANG Hong-bo, HUANG Bai-yun. Oxidation behavior of Mo-Si coated C/SiC composites [J]. Technique Aerospace Materials and Technology, 2007, 10(6): 39-43.
[5] ZHU Hui-chao, LI Fu-hai, WANG Feng. Study on properties of ZrSiO4 ceramic coatings by plasma spray [J]. Journal of Guangdong Non-ferrous Metals, 2005, 15(1): 30-32. (in Chinese)
[6] LIU Rong-jun, ZHOU Xin-gui, ZHANG Chang-rui, ZHOU An-chen. The oxidation resistant MoSi2-SiC-Si coating for Cf/SiC ceramic matrix composites prepared by cementation [J]. Technique Aerospace Materials and Technology,2000, 2(3): 45-48.
[7] SCHUBERT T. Effects of high energy milling on densification behavior of Mo-Si powder mixtures during pressureless sintering [J]. Intermetallics, 2002, 10(9): 873-878.
[8] LIU Xing-fang, HUANG Qi-zhong, SU Zhe-an, JIAN Jian-xian. Preparation of SiC coating by chemical vapor reaction [J]. Journal of the Chinese Ceramic Societ, 2004, 32(7): 906-910. (in Chinese)
[9] WANG Long, LI De-yi, LIU Wen-chao, WEI Kun, TANG Shao-qun. Influence of temperature on the synthetic whisker SiC by carbon thermal reduction method [J]. Journal of Ceramics, 2001, 22(4): 220-222.
[10] LIU K, LIU L, ZHANG Y X, SHEN S D, GE S, LING L C. Synthesis of nanometre silicon carbide whiskers from binary carbonaceous silica aerogels [J]. Carbon, 2001, 39(2): 159-165.
[11] CHEYSANTHOU A, GRIEVESON P, JHA A. Formation of silicocarbide whiskers and their microstructure [J]. J Mater Sci, 1991, 26(10): 3463-3465.
[12] GAO Rui-lan, MIN Guang-hui, YU Hua-shun, ZHENG Shu-qi, LU Qing-liang, HAN Jian-de, WANG Wei-ti. Fabrication and oxidation behavior of LaB6-ZrB2 composites [J]. Ceramics International, 2005, 31(1): 15-19.
[13] TRIPP W C, GRAHAM H C. Thermogravimetric study of the oxidation of ZrB2 in the temperature range of 800 °C to 1 500 °C [J]. Electrochem Soc, 1971, 118(16): 1195-1199.
[14] HOU Dang-she, LI Ke-zhi, LI He-jun. SiC/W-Mo-Si composite anti-oxidation coating for carbon/carbon composites [J]. Materials Protection, 2008, 41(2): 43-46.
[15] HUANG Jian-feng. The investigation of coating of SiC by pack cementation [D]. Xi’an: Key Laboratory of Thermostructure Composite Materials for National Defense Science and Technology, Northwestern Polytechnical University, 2004. (in Chinese)
ZrB2-MoSi2/SiC涂层C/C复合材料的制备及氧化性能
张武装,曾 毅,GBOLOGAH Lemuel,熊 翔,黄伯云
中南大学 粉末冶金国家重点实验室,长沙 410083
摘 要:为了提高C/C复合材料的抗氧化性,在C/C复合材料基体上制备了ZrB2-MoSi2/SiC涂层。采用包埋法制备SiC中间层,采用喷涂法制备ZrB2-MoSi2外涂层。用XRD和SEM分别分析、测试所制备涂层的物相组成和显微结构,研究涂层复合材料的高温抗氧化性能。结果表明:C/C复合材料的外涂层由ZrB2、MoSi2 和SiC三相组成;在1 273 K和1 773 K下分别氧化30 h和10 h后ZrB2-MoSi2/SiC涂层试样的质量损失分别为5.3%和3.0%,涂层表面长有纳米SiC晶须。C/C复合材料ZrB2-MoSi2/SiC涂层具有自愈合特性和良好的高温抗氧化性能。
关键词:C/C复合材料;ZrB2-MoSi2;SiC;涂层;氧化
(Edited by YANG Hua)
Foundation item: Project (50721003) supported by the Innovation Community Foundation of National Natural Science of China; Project (2011CB605805) supported by the National Basic Research Program of China
Corresponding author: XIONG Xiang; Tel/Fax: +86-731-88836079; E-mail: Xiong228@sina.com
DOI: 10.1016/S1003-6326(11)60893-5